Addressing the Multiplicity of Solutions in Optical Lens Design As a Niching Evolutionary Algorithms Computational Challenge
Total Page:16
File Type:pdf, Size:1020Kb
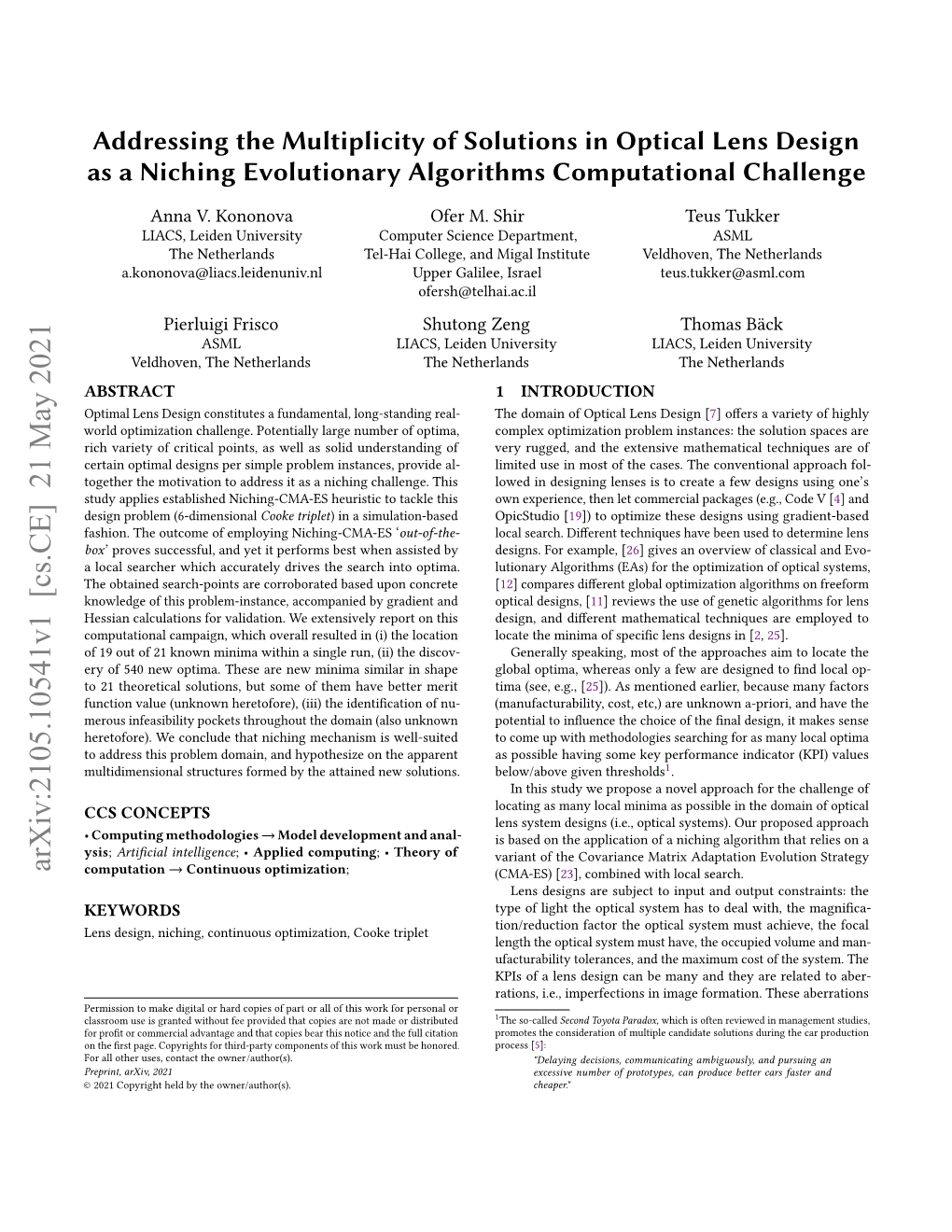
Load more
Recommended publications
-
(12) Patent Application Publication (10) Pub. No.: US 2015/0055085A1 Fonte Et Al
US 2015.0055085A1 (19) United States (12) Patent Application Publication (10) Pub. No.: US 2015/0055085A1 Fonte et al. (43) Pub. Date: Feb. 26, 2015 (54) METHOD AND SYSTEM TO CREATE (52) U.S. Cl. PRODUCTS CPC .......... G02C 13/001 (2013.01); G06F 19/3456 (2013.01); G06F 17/50 (2013.01) (71) Applicant: Bespoke, Inc., San Francisco, CA (US) USPC ............................................. 351/178; 700/98 (72) Inventors: Timothy A. Fonte, San Francisco, CA (57) ABSTRACT (US); Eric J. Varady, San Francisco, CA Systems and methods for creating fully custom products from (US) scratch without exclusive use of off-the-shelfor pre-specified components. A system for creating custom products includes (21) Appl. No.: 14/466,615 an image capture device for capturing image data and/or measurement data of a user. A computer is communicatively (22) Filed: Aug. 22, 2014 coupled with the image capture device and configured to constructananatomic model of the user based on the captured O O image data and/or measurement data. The computer provides Related U.S. Application Data a configurable product model and enables preview and auto (60) Provisional application No. 61/869,051, filed on Aug. matic or user-guided customization of the product model. A 22, 2013, provisional application No. 62/002,738, display is communicatively coupled with the computer and filed on May 23, 2014. displays the custom product model Superimposed on the ana tomic model or image data of the user. The computeris further Publication Classification configured to provide the customized product model to a manufacturer for manufacturing eyewear for the user in (51) Int. -
Design and Analysis of Optical Layouts for Free Space Optical Switching
Edith Cowan University Research Online Theses: Doctorates and Masters Theses 2002 Design and analysis of optical layouts for free space optical switching Kung-meng Lo Edith Cowan University Follow this and additional works at: https://ro.ecu.edu.au/theses Part of the Electrical and Computer Engineering Commons Recommended Citation Lo, K. (2002). Design and analysis of optical layouts for free space optical switching. https://ro.ecu.edu.au/theses/1645 This Thesis is posted at Research Online. https://ro.ecu.edu.au/theses/1645 Edith Cowan University Copyright Warning You may print or download ONE copy of this document for the purpose of your own research or study. The University does not authorize you to copy, communicate or otherwise make available electronically to any other person any copyright material contained on this site. You are reminded of the following: Copyright owners are entitled to take legal action against persons who infringe their copyright. A reproduction of material that is protected by copyright may be a copyright infringement. Where the reproduction of such material is done without attribution of authorship, with false attribution of authorship or the authorship is treated in a derogatory manner, this may be a breach of the author’s moral rights contained in Part IX of the Copyright Act 1968 (Cth). Courts have the power to impose a wide range of civil and criminal sanctions for infringement of copyright, infringement of moral rights and other offences under the Copyright Act 1968 (Cth). Higher penalties may apply, and higher damages may be awarded, for offences and infringements involving the conversion of material into digital or electronic form. -
Design for Manufacturability and Optical Performance Trade-Offs Using Precision Glass Molded Aspheric Lenses
Invited Paper Design for Manufacturability and Optical Performance Trade-offs using Precision Glass Molded Aspheric Lenses Alan Symmons, Jeremy Huddleston and Dennis Knowles LightPath Technologies, Inc., 2603 Challenger Tech Ct, Ste 100, Orlando, FL, USA 32826 ABSTRACT Precision glass molding (PGM) enables high-performance, low-cost lens designs through aspheric shapes and a broad array of moldable glass types. While these benefits bring a high potential value, the design of PGM lenses must be skillfully approached to balance manufacturability and cost considerations. Different types of mold tooling and processes used by PGM suppliers can also lead to confusion regarding the manufacturing parameters and design rules that should be considered. The authors discuss the various factors that can affect manufacturability and cost of lenses made to PGM standards, and present a case study to demonstrate the trade-offs in performance. Keywords: Precision glass molding, asphere, optical lens, design rules, manufacturability 1. INTRODUCTION Precision glass molding is a compression molding process (as opposed to the popularized injection molding of plastic) capable of transferring high-quality aspheric shapes from a precision mold set into the optical lens being formed. This technology has the distinct advantage of enabling low cost optical lenses for high volume applications, while maintaining the high quality of aspheric optical surface profiles and utilizing the inherent advantages of glass materials [1]. Modern PGM technology was pioneered in the late 1970’s to early 1980’s by companies such as Corning Glass Works and Eastman Kodak, who then transferred these complex capabilities to PGM manufacturers such as Geltech (acquired by LightPath Technologies in 2000) [2]. -
Linear Light Family Guide
Linear Luminaire Best Illuminance ONE BIN ONLY Durable Performance IP65 Architectural Lighting Linear Solution Exquisite Appearance Projects Applicable Linear Linear Light Architectural lighting As the best top of linear light which it be seamless stitching makes the lighting effect more contributed by many essential factors, such as consistent, without dark area. Each design link adopt professional optical lens design, excellent has been carefully selected, outstanding design, color balance, optimized lens diffusion, precise excellent quality, and high-quality manufacturing. processing technology, ideal lens configuration, The middle of the bottom of the light line design effectively avoid the occurrence of white light concept, the two ends of the line are long and dispersion, ensure the absolute purity of the short, the two ends are directly connected, there overall light and color, and brilliant artistic details will be no extra lines, to avoid the installation of the reproduction. And the high quality of material line warping, construction and installation more Introduction & fully of protective system. Will not produce handy, debugging and installation more quickly, for -Linear Light 03 deformation phenomenon under the long-term you to save more time and energy to focus on your irradiation of the light source; UV resistance, professional field. -Why Linear Light always be the priority of consideration? 04 chemical corrosion resistance, not easy aging -Linear Light family 06 and discoloration in outdoor environment; light -Core-Value 08 transmittance above 92%; It is the best choice material for large buildings. The line hidden at the -What makes Linear Light so professional-grade of lighting? 10 bottom of the light, the appearance of the wire -Specification and Information 12 without exposure is quite beautiful, the craft of 2 3 Architectural lighting Practicability Precise of light-control, and beautiful appearance, suitable for narrow, or large buildings, commercial streets, theaters, and exhibition hall facade lighting. -
Genetic Algorithms for Lens Design: a Review
Genetic Algorithms for Lens Design: a Review Kaspar H¨oschela, Vasudevan Lakshminarayananb aTU Wien, Karlsplatz 13, 1040 Wien, Austria bUniversity of Waterloo, Theoretical and Experimental Epistemology Lab, School of Optometry & Vision Science, Depts. of Physics, ECE and Systems Design Engineering, Waterloo, ON, N2L 3G1, Canada Abstract. Genetic algorithms (GAs) have a long history of over four decades. GAs are adaptive heuristic search algorithms that provide solutions for optimization and search problems. The GA derives expression from the biological terminology of natural selection, crossover, and mutation. In fact, GAs simulate the processes of natural evolution. Due to their unique simplicity, GAs are applied to the search space to find optimal solutions to various problems in science and engineering. Using GAs for lens design was investigated mostly in the 1990s, but were not fully exploited. But in the past few years there have been a number of newer studies exploring the application of GAs or hybrid GAs in optical design. In this paper we discuss the basic ideas behind GAs and demonstrate their application in optical lens design. Keywords: Genetic algorithm, lens optimization, lens system design, optimization strategies. aE-mail: [email protected] 1 Introduction In terms of designing optical lenses there are many constraints and requirements, including restrictions like assembly, potential cost, manufacturing, procurement, and personal decision making [1]. Typical parameters include surface profile types such as spherical, aspheric, diffractive, or holographic. Usually, the design space for optical systems consists of multi-dimensional parameter space. Moreover, the radius of curvature, distance to the next surface, material type and optionally tilt, and decenter are necessary for lens design [2]. -
Self Electronics LED Lighting for Refrigeration from Hawco
LED Lighting 2017/2018 LED Lighting 2017-2018 SELF Electronics Germany GmbH August-Horch-Str. 7,51149 Cologne Phone: +492203-18501-0 Fax: 492203-18501-199 E-mail: [email protected] SELF Electronics USA Corporation 3264 Saturn Ct., Norcross, GA 30092 Phone: +001-770-248-9023 Fax: 1-770-248-9028 E-mail: [email protected] SELF Electronics Co.,Ltd.,Shenzhen Office Room2007, Xinglang Xuan, Xinghe Mingju, Fuming Road, Futian District, Shenzhen Phone: +0086-755-83558850, +86-775-83558851 Fax: +0086-755-83558840 E-mail: [email protected] SELF Electronics Co.,Ltd.(Headquarters) 114 SML Add: No. 1345 JuXian Road,Ningbo Hi Tech Park, Ningbo,China 315103 Phone: +86-574-2880-5765, +86-574-2880-5658 (for English assistance) +86-574-2880-5678 (for Chinese assistance) Fax: +86-574-28805656 E-mail: [email protected] http://www.self-electronics.com Copyright © 2017, SELF Electronics Co.,Ltd. All rights reserved. Designs and specifications may change without prior notice. The story of Three Pine Trees In the west of the SELF new plant standing three pines: “We, plain but of a unique style, remain calm and not disturbed after the relocation. We, together with SELF people, witness the transformation after the raging storms!” In 1997, Ningbo was attacked by disastrous typhoon, and then SELF employees protected the growing spines by steel 1993-2017 bed. The same year, SELF suffered “TüV Incident”, in a pinch, it was the philosophy “be a good SELF employee before doing something” leading us out of trouble and winning good reputation on the market. -
Dielectric Lens Antennas
Dielectric Lens Antennas Carlos A. Fernandes, Instituto de Telecomunicações, Instituto Superior Técnico, Universidade de Lisboa, Lisboa, Portugal Eduardo B. Lima, Instituto de Telecomunicações, Instituto Superior Técnico, Universidade de Lisboa, Lisboa, Portugal Jorge R. Costa, Instituto de Telecomunicações, Instituto Universitário de Lisboa (ISCTE- IUL), Lisboa, Portugal ABSTRACT Dielectric lens antennas are attracting a renewed interest for millimetre- and sub- millimetre wave applications where they become compact, especially for configurations with integrated feeds usually referred as integrated lens antennas. Lenses are very flexible and simple to design and fabricate, being a reliable alternative at these frequencies to reflector antennas. Lens target output can range from a simple collimated beam (increasing the feed directivity) to more complex multi-objective specifications. This chapter presents a review of different types of dielectric lens antennas and lens design methods. Representative lens antenna design examples are described in detail, with emphasis on homogeneous integrated lenses. A review of the different lens analysis methods is performed, followed by the discussion of relevant lens antenna implementation issues like feeding options, dielectric material characteristics, fabrication methods and a few dedicated measurement techniques. The chapter ends with a detailed presentation of some recent application examples involving dielectric lens antennas. KEYWORDS Lens Antennas, Geometric Optics, Physical Optics, Lens Feeds, Dielectric Materials, Lens Manufacturing, Lens Profile Design, Optimization. INTRODUCTION The use of a dielectric lens as part of an antenna is almost as old as the demonstration of electromagnetic waves by Hertz. In fact, in 1888 Oliver Lodge used a dielectric lens in his experiments at 1 m wavelength (Lodge and Howard 1888). -
Genetic Algorithms for Lens Design: a Review
J Opt (March 2019) 48(1):134–144 https://doi.org/10.1007/s12596-018-0497-3 TUTORIAL PAPER Genetic algorithms for lens design: a review 1 2 Kaspar Ho¨schel • Vasudevan Lakshminarayanan Received: 6 July 2018 / Accepted: 27 November 2018 / Published online: 6 December 2018 Ó The Author(s) 2018 Abstract Genetic algorithms (GAs) have a long history of surface profile types such as spherical, aspheric, diffractive, over four decades. GAs are adaptive heuristic search or holographic. Usually, the design space for optical sys- algorithms that provide solutions for optimization and tems consists of multi-dimensional parameter space. search problems. The GA derives expression from the Moreover, the radius of curvature, distance to the next biological terminology of natural selection, crossover, and surface, material type and optionally tilt, and decenter are mutation. In fact, GAs simulate the processes of natural necessary for lens design [2]. evolution. Due to their unique simplicity, GAs are applied The most important aspects for designing optical lenses to the search space to find optimal solutions for various are optical performance or image quality, manufacturing, problems in science and engineering. Using GAs for lens and environmental requisitions. Optical performance is design was investigated mostly in the 1990s, but were not determined by encircled energy, the modulation transfer fully exploited. But in the past few years, there have been a function (MTF), ghost reflection control, pupil perfor- number of newer studies exploring the application of GAs mance, and the Strehl ratio [3, 4]. Manufacturing or hybrid GAs in optical design. In this paper, we discuss requirements include weight, available types of materials, the basic ideas behind GAs and demonstrate their appli- static volume, dynamic volume, center of gravity, and cation in optical lens design. -
A New, Durable and Efficient Optical Lens Design for Driver Cabs' of The
ISBN 978-981-11-3671-9 Proceedings of 2017 the 7th International Workshop on Computer Science and Engineering (WCSE 2017) Beijing, 25-27 June, 2017 , pp. 1044-1048 A New, Durable and Efficient Optical Lens Design for Driver Cabs’ of the DMUs Alper Tasci 1 and Cenk Yavuz 2 1 Turkish Wagon Industry, R&D, Sakarya, Turkey 2 Sakarya University, Eng.Faculty, Electrical&Electronics Eng. Dept, Sakarya, Turkey Abstract. Driver Cabs’ Marker and Tail lights have significant importance in railway transportation. There are several requirements mentioned in the international standards for estimation and operation clauses. In this study a new Polycarbonate lens design for MT15400 series Diesel Multiple Units (DMU) of Turkish Wagon Industry instead of existing Glass lenses is realized. Tests and measurements held to prove the advantages of the new design: better visibility, light intensity and light distribution. Keywords: Lens optic, Lens design, Railway lighting, Visibility 1. Introduction In this study, the effect of changing glass based optical lenses with Polycarbonate based optical lenses on lighting characteristics of Marker lights on MT15400 series Diesel Multiple Units (DMUs), which has been manufactured by TÜVASAŞ “Turkish Wagon Industry Inc.” and owned by TCCD Transportation Inc., is explained. Manufacturing of MT15400 series DMU started in 2010 and twenty four (24) units had been manufactured in the first order. Quantity of MT15400 series DMUs is going to be fifty four (54) until the end of 2017. There is a driver cab on the each end of the MT15400 series DMUs to control the unit. Figure-1 shows the front view of MT-15400 series DMUs. -
Design of a Miniaturized Imaging System for As-Built Performance
Rose-Hulman Institute of Technology Rose-Hulman Scholar Graduate Theses - Physics and Optical Engineering Physics and Optical Engineering Fall 11-23-2020 Design of a Miniaturized Imaging System for As-built Performance Jake Joo Follow this and additional works at: https://scholar.rose-hulman.edu/dept_optics Design of a Miniaturized Imaging System for As-built Performance A Thesis Submitted to the Faculty of Rose-Hulman Institute of Technology by Jake Joo In Partial Fulfillment of the Requirements for the Degree of Master of Science in Optical Engineering November 2020 © 2020 Jake Joo ROSE-HULMAN INSTITUTE OF TECHNOLOGY Final Examination Report Joonha Joo Optical Engineering Name Graduate Major Thesis Title ____________________________________________________Design of a Miniaturized Imaging System for As-Built Performance ______________________________________________________________ DATE OF EXAM: November 23, 2020 EXAMINATION COMMITTEE: Thesis Advisory Committee Thesis Advisor: Hossein Alisafaee PHOE Azad Siahmakoun PHOE Jay McCormack ME X PASSED ___________ FAILED ___________ ABSTRACT Jake Joo M.S.O.E. Rose-Hulman Institute of Technology November 2020 Design of a Miniaturized Imaging System for As-Built Performance Thesis Advisor: Dr. Hossein Alisafaee During the past two decades, many advancements in the field of optical design have occurred. Some of the more recent topics and concepts regarding optical system design are complex and require a comprehensive understanding of aberration theory, in-depth knowledge and experience with optical design software, and extensive lens design experience. This thesis focuses on the development and application of simpler methods for successful lens design for standard and miniaturized imaging systems. The impact of manufacturing tolerances of an optical system is considered, analyzed, and tested. -
A Wearable Head-Mounted Projection Display
A WEARABLE HEAD-MOUNTED PROJECTION DISPLAY by RICARDO F. MARTINS B.S. Fairleigh Dickinson University, 2001 M.S. University of Central Florida, 2003 A dissertation submitted in partial fulfillment of the requirements for the degree of Doctor of Philosophy in the Department of Modeling and Simulation in the College of Sciences at the University of Central Florida Orlando, Florida Fall Term 2010 Major Professor: Thomas Clarke © 2010 (Ricardo F. Martins) ii ABSTRACT Conventional head-mounted projection displays (HMPDs) contain of a pair of miniature projection lenses, beamsplitters, and miniature displays mounted on the helmet, as well as a retro-reflective screen placed strategically in the environment. We have extened the HMPD technology integrating the screen into a fully mobile embodiment. Some initial efforts of demonstrating this technology has been captured followed by an investigation of the diffraction effects versus image degradation caused by integrating the retro-reflective screen within the HMPD. The key contribution of this research is the conception and development of a mobile- HMPD (M-HMPD). We have included an extensive analysis of macro- and microscopic properties that encompass the retro-reflective screen. Furthermore, an evaluation of the overall performance of the optics will be assessed in both object space for the optical designer and visual space for the possible users of this technology. This research effort will also be focused on conceiving a mobile M-HMPD aimed for dual indoor/outdoor applications. The M-HMPD shares the known advantage such as ultra- lightweight optics (i.e. 8g per eye), unperceptible distortion (i.e. ≤ 2.5%), and lightweight headset (i.e. -
Optical Calculation of Structures and Unification of Objectives for Microscopes
Optical calculation of structures and unification of objectives for microscopes Frolov, A.D. *, Frolov D.N. **, PhD. Technical. Science * St. Petersburg State University of Information Technologies, Mechanics and Optics * The Labor-Microscopes, St. Petersburg Phone: +7 (921) 748-02-12, Fax: +7 (812) 590-82-83, E-mail: [email protected] Abstract: We propose to conduct multi-level unification of optical systems of lenses at the time of marker and aberration of the optical calculations and design of the optical design. It is shown that by using a basic optical scheme can obtain a whole range of lenses designed for use in various applications and implementation of various research techniques in the microscope. It is shown that the basis for unification of optical systems of lenses for microscopes is the use of optical calculation as a composition of elements with known marker, aberration properties. 1. Introduction task. At the present level of development of computer As is known, the optical calculation is the first technology, computing speed, formal problem can be after agreeing terms of reference and the main stage solved quite easily. Another thing is that obtained in the development of lenses for microscopes. Mainly with a "unification" of the optical design can not be because it determines not only technical but also the considered as optimal. consumer properties of the developed lens. When the optical calculation was carried out incorrectly or with 4. The unification of the basic elements of optical errors, it turns out this is only after all other stages of design designing and manufacturing the lens, when it spent Now becoming increasingly widespread all of the planned time and material resources.