Table of Contents 5.1 Overview – Perchloroethylene
Total Page:16
File Type:pdf, Size:1020Kb
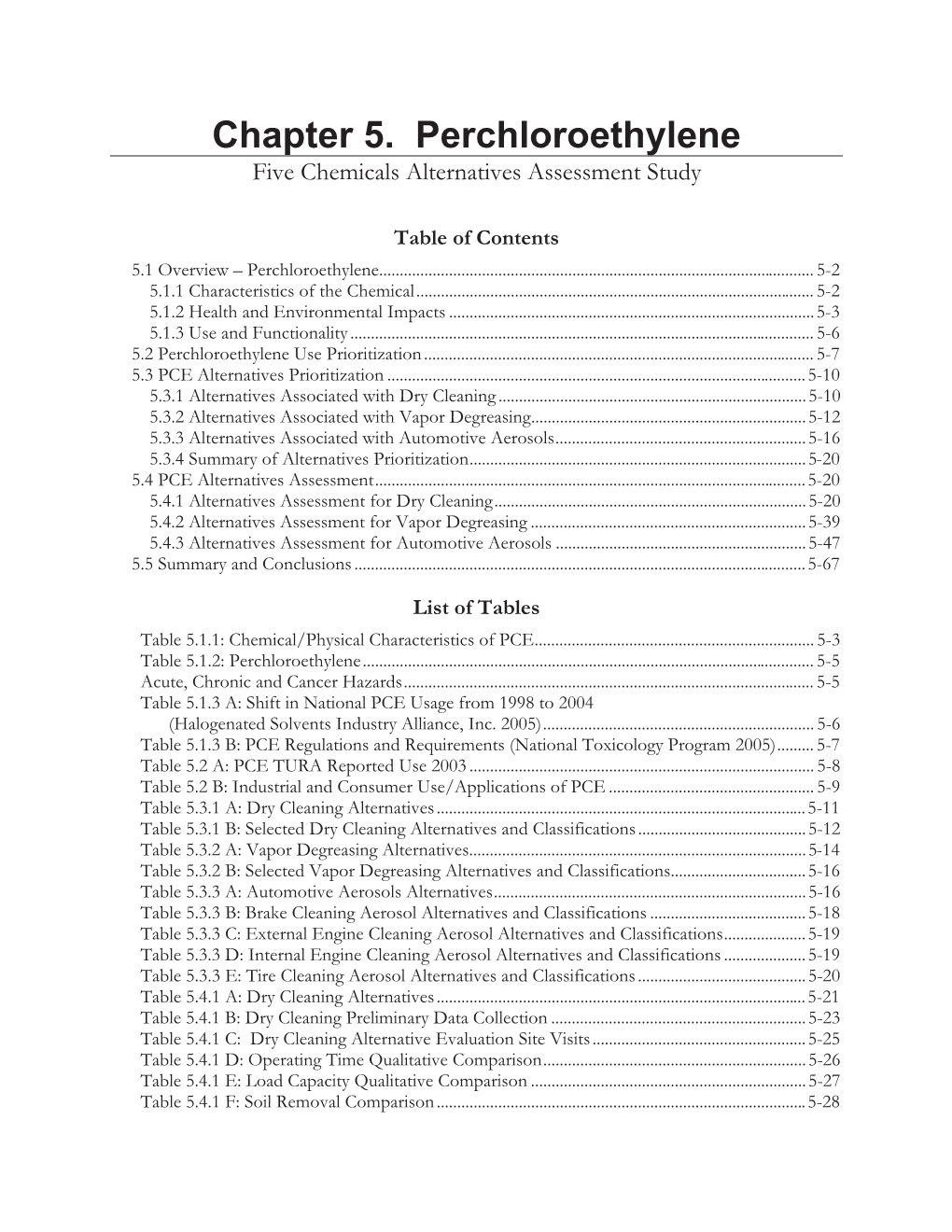
Load more
Recommended publications
-
Problem Formulation of the Risk Evaluation for Perchloroethylene (Ethene, 1,1,2,2-Tetrachloro)
EPA Document# EPA-740-R1-7017 May 2018 DRAFTUnited States Office of Chemical Safety and Environmental Protection Agency Pollution Prevention Problem Formulation of the Risk Evaluation for Perchloroethylene (Ethene, 1,1,2,2-Tetrachloro) CASRN: 127-18-4 May 2018 TABLE OF CONTENTS ABBREVIATIONS ............................................................................................................................ 8 EXECUTIVE SUMMARY .............................................................................................................. 11 1 INTRODUCTION .................................................................................................................... 14 1.1 Regulatory History ..................................................................................................................... 16 1.2 Assessment History .................................................................................................................... 16 1.3 Data and Information Collection ................................................................................................ 18 1.4 Data Screening During Problem Formulation ............................................................................ 19 2 PROBLEM FORMULATION ................................................................................................. 20 2.1 Physical and Chemical Properties .............................................................................................. 20 2.2 Conditions of Use ...................................................................................................................... -
Brake Cleaner BRAKE CLEANER/NON CHLORINATED INFOTRAC: 1-800-535-5053
Safety Data Sheet according to OSHA Hazard Communication 29 CFR Part 1910.1200 SECTION 1. Identification Product Code 44636 24 Hour Emergency: Product Name: Brake Cleaner BRAKE CLEANER/NON CHLORINATED INFOTRAC: 1-800-535-5053 Outside U.S. and Canada Supplied by: KELLER HEARTT OIL Infotrac: 352-323-3500 4411 SOUTH TRIPP AVE CHICAGO, IL 60632 NOTE: INFOTRAC and National Response Center KELLERHEARTT.COM emergency numbers to be used only in the event of chemical emergencies involving a spill, leak, fire, exposure or accident involving chemicals SECTION 2. Hazard(s) Identification *** EMERGENCY OVERVIEW ***: Highly flammable liquid and vapor. May be fatal if inhaled. May be fatal if swallowed. GHS Classification Flam. Liq. 2, STOT SE 3 NE, Skin Irrit. 2 Symbol(s) of Product Signal Word Danger GHS HAZARD STATEMENTS Flammable Liquid, category 2 H225 Highly flammable liquid and vapor. Skin Irritation, category 2 H315 Causes skin irritation. STOT, single exposure, category 3, NE H336 May cause drowsiness or dizziness. GHS PRECAUTIONARY STATEMENTS P210 Keep away from heat, hot surfaces, sparks, open flames and other ignition sources. No smoking. P240 Ground/bond container and receiving equipment. P241 Use explosion-proof electrical/ventilating/lighting/equipment. P242 Use only non-sparking tools. P243 Take precautionary measures against static discharge. P261 Avoid breathing dust/fume/gas/mist/vapors/spray. P264 Wash thoroughly after handling. P271 Use only outdoors or in a well-ventilated area. P280 Wear protective gloves/protective clothing/eye protection/face protection. P302+P352 IF ON SKIN: Wash with plenty of water P303+P361+P353 IF ON SKIN (or hair): Take off immediately all contaminated clothing. -
Berkebile Brake Cleaner B-3220 Safety Data Sheet
BERKEBILE BRAKE CLEANER B-3220 SAFETY DATA SHEET OSHA HCS (29 CFR 1910.1200) SECTION 1: PRODUCT AND COMPANY IDENTIFICATION Product identifier Chemical Name Mixture CAS No. Mixture Trade Name BERLEBILE BRAKE CLEANER B-3220 Product Code EN-4121 Relevant identified uses of the substance or mixture and uses advised against Identified Use(s) Automotive maintenance product Uses Advised Against None Company Identification The Berkebile Oil Company INC. P.O. Box 715 Somerset, PA 15501 Telephone (814) 443-1656 Fax (814) 443-2873 E-Mail (competent person) [email protected] Emergency telephone number Emergency Phone No. Transportation Emergency: CHEMTREC 24 hr. 1-800-424- 9300 / 1 (703) 527-3887 (Collect calls accepted) SECTION 2: HAZARDS IDENTIFICATION Classification of the substance or mixture OSHA HCS (29 CFR 1910.1200) Flam. Aerosol 1; Compressed dissolved gas; STOT SE 1; Repr. 2; STOT RE 2; Skin Irrit. 2; Eye Irrit. 2; Asp. Tox. 1 Label elements Hazard Symbol Signal word(s) DANGER Hazard Statement(s) Extremely flammable aerosol. Contains gas under pressure; may explode if heated. Causes damage to organs: Optic nerve, Central nervous system. May cause drowsiness or dizziness. Suspected of damaging the unborn child. May cause damage to organs through prolonged or repeated exposure: Inhalation - neuropsychological effects, auditory dysfunction and effects on colour vision. Causes skin irritation. Causes serious eye irritation. Repeated exposure may cause skin dryness or cracking. May be harmful if swallowed and enters airways. Revision: March 30, 2017 Page: 1/8 BERKEBILE BRAKE CLEANER B-3220 Precautionary Statement(s) Do not handle until all safety precautions have been read and understood. -
Pollution Prevention Summary Report
This document is made available electronically by the Minnesota Legislative Reference Library as part of an ongoing digital archiving project. http://www.leg.state.mn.us/lrl/lrl.asp Pollution Prevention Summary Report Consolidated from reports submitted by members of the Interagency Pollution Prevention Advisory Team for the fiscal year 2000 September 2001 For more information on pollution prevention activities in Minnesota state government, please contact: Emily Moore Minnesota Office of Environmental Assistance 520 Lafayette Road North, Second Floor St. Paul, Minnesota 55155-4100 651-215-0201 2 Table of Contents Introduction ........................................................................................1 Part I. Agency Descriptions ...................................................................2 Part II. Policy and Regulatory Activities .....................................................6 Part III. Pollution Prevention Activities during the Fiscal Year........................ 12 1. Absorbents................................................................................. 12 2. Adhesives .................................................................................. 14 3. Air Quality, CFCs.......................................................................... 14 4. Antifreeze ................................................................................. 17 5. Audits....................................................................................... 19 6. Automotive Fuels........................................................................ -
Adopted Part 235 Consumer Products and Part 200 General Provisions
Revised Summary of Express Terms 6 NYCRR Part 235, Consumer Products 6 NYCRR Part 200, General Provisions The Division of Air Resources is revising 6 NYCRR Part 235, “Consumer Products” (Part 235) to reduce volatile organic compound (VOC) emissions, improve air quality, and promote regional product consistency. The revisions will help the state attain federal National Ambient Air Quality Standards, and work toward regionally consistent regulations amongst the Ozone Transport Commission (OTC) states. The revisions include adding nine new product categories and revising ten existing categories in order to reduce the VOC content of the products through lower VOC content limits. Part 200 will be revised to incorporate referenced materials, including American Society for Testing Materials (ASTM) testing procedures, the California Air Resources Board (CARB) provisions supporting this regulation, and to update references to Part 235. Part 235 will be revised to incorporate new definitions and revise some categories in the existing definitions. Additionally, Subpart 235-3 will be updated to add new VOC limits, conform to the revised definitions and product categories, and to remove obsolete text and references. Changes throughout the proposal include a January 1, 2022 compliance date for the new VOC limits on new and reformulated products in the regulation. Likewise, changes were made in the definitions section to provide transitional language, where necessary, for those categories of products that were redefined or revised, to cite which emission standards apply before or after the compliance date of the regulation. Page 1 of 4 The revisions include setting VOC content limits for nine new product categories and lowering the VOC content limits for ten existing product categories. -
Env-A 4100: Consumer Products VOC Limits.Pdf
NEW HAMPSHIRE CODE OF ADMINISTRATIVE RULES TABLE OF CONTENTS CHAPTER Env-A 4100 CONSUMER PRODUCTS PART Env-A 4101 PURPOSE, SCOPE, REFERENCES, AND EXEMPTIONS Env-A 4101.01 Purpose Env-A 4101.02 Applicability Env-A 4101.03 References Env-A 4101.04 Exemptions PART Env-A 4102 DEFINITIONS: A THROUGH E Env-A 4102.01 Adhesive Env-A 4102.02 Adhesive Remover Env-A 4102.03 Aerosol Adhesive Env-A 4102.04 Aerosol Cooking Spray Env-A 4102.05 Aerosol Product Env-A 4102.06 Agricultural Use Env-A 4102.07 Air Freshener Env-A 4102.08 All Other Carbon-Containing Compounds Env-A 4102.09 All Other Forms Env-A 4102.10 Antimicrobial Hand or Body Cleaner or Soap Env-A 4102.11 Antiperspirant Env-A 4102.12 Anti-Static Product Env-A 4102.13 Architectural Coating Env-A 4102.14 Aromatic Compound Env-A 4102.15 Artist’s Solvent/Thinner Env-A 4102.16 Astringent/Toner Env-A 4102.17 Automotive Brake Cleaner Env-A 4102.18 Automotive Engine Compartment Adhesive Env-A 4102.19 Automotive Hard Paste Wax Env-A 4102.20 Automotive Headliner Adhesive Env-A 4102.21 Automotive Instant Detailer Env-A 4102.22 Automotive Rubbing or Polishing Compound Env-A 4102.23 Automotive Wax, Polish, Sealant, or Glaze Env-A 4102.24 Automotive Windshield Cleaner Env-A 4102.25 Automotive Windshield Washer Fluid Env-A 4102.26 Bait Station Insecticides Env-A 4102.27 Bathroom and Tile Cleaner Env-A 4102.28 Brake Cleaner Env-A 4102.29 Bug and Tar Remover Env-A 4102.30 Carburetor or Fuel-Injection Air Intake Cleaners Env-A 4102.31 Carpet and Upholstery Cleaner Env-A 4102.32 Charcoal Lighter Material Env-A -
Material Substitution Workshop
Material Substitution Workshop Safer Products That Work: Cleaners and Degreasers for Industrial Maintenance and Auto Repair State/Community Hazardous Material Source Reduction May 4, 2017 Introduction Improving Minnesota’s Air Quality • Collaborative effort launched to develop and implement strategies to improve MN air quality • MnTAP work to improve Minnesota’s air quality by reducing VOCs through material substitution in area source facilities • Discuss strategies developed to • Determine a target sector focus area • Establish what are safer products • Assure safer products are functionally equivalent • Motivate broad adoption of safer products • Leverage implementation resources VOC Opportunity Identification National Emissions Inventory (NEI) as a tool Karl DeWahl VOC Area Sources •2015 EPA NAAQS review •Clean Air Minnesota •Area source focus – MnTAP, MPCA, Minneapolis, EI • which one(s)? National Emissions Inventory (NEI) • 2008, 2011, 2014 • Get data from your state • Criteria pollutants (VOC, CO, SO2, NOx, PM, Pb) • Point air toxics • Some speciation • Source Classification Codes (SCC) VOC Sources worked on •Degreasing - nonpoint • Vehicle maintenance • Industrial maintenance •Other TA focus areas • Autobody painting - nonpoint • Industrial painting - point • FRP - point • Oilseed - point Risk Assessment of Degreasing Products By Michelle Gage How do I find safer products? • TURI – Check out their Cleaner Solutions Database • Look for reputable labels: • EPA’s Safer Choice Label • Green Electronics Council - EPEAT • USDA Organics -
Throttle Muscle 10% Brake Cleaner 13
THROTTLE MUSCLE 10% BRAKE CLEANER 13 OZ. Safety Data Sheet according to Federal Register / Vol. 77, No. 58 / Monday, March 26, 2012 / Rules and Regulations Revision date: 05/15/2015 : Version: 1.1 SECTION 1: Identification of the substance/mixture and of the company/undertaking 1.1. Product identifier Product form : Mixture Trade name : THROTTLE MUSCLE 10% BRAKE CLEANER 13 OZ. Product code : TM8487 1.2. Relevant identified uses of the substance or mixture and uses advised against Use of the substance/mixture : Brake Parts Cleaner 1.3. Details of the supplier of the safety data sheet REV YOUR CAUSE LLC 144O JASON WAY UNIT 100-107 SANTA MARIA, CA 93455 T 805-925-2796 1.4. Emergency telephone number Emergency number : CHEMTREC 24 Hour 1-800-424-9300, 1-703-527-3887 (International) SECTION 2: Hazards identification 2.1. Classification of the substance or mixture Classification (GHS-US) Flam. Aerosol 2 H223 Compressed gas H280 Skin Irrit. 2 H315 Eye Irrit. 2A H319 Repr. 2 H361 STOT SE 1 H370 STOT SE 3 H336 Full text of H-phrases: see section 16 2.2. Label elements GHS-US labeling Hazard pictograms (GHS-US) : GHS02 GHS04 GHS07 GHS08 Signal word (GHS-US) : Danger Hazard statements (GHS-US) : H223 - Flammable aerosol H280 - Contains gas under pressure; may explode if heated H315 - Causes skin irritation H319 - Causes serious eye irritation H336 - May cause drowsiness or dizziness H361 - Suspected of damaging fertility or the unborn child H370 - Causes damage to organs Precautionary statements (GHS-US) : P201 - Obtain special instructions P202 - Do not handle until all safety precautions have been read and understood P210 - Keep away from heat,sparks,open flames,hot surfaces. -
CODE of COLORADO REGULATIONS 5 CCR 1001-25 Air Quality Control Commission
DEPARTMENT OF PUBLIC HEALTH AND ENVIRONMENT Air Quality Control Commission REGULATION NUMBER 21 CONTROL OF VOLATILE ORGANIC COMPOUNDS FROM CONSUMER PRODUCTS AND ARCHITECTURAL AND INDUSTRIAL MAINTENANCE COATINGS 5 CCR 1001-25 [Editor’s Notes follow the text of the rules at the end of this CCR Document.] _________________________________________________________________________ Outline of Regulation PART A CONCERNING CONSUMER PRODUCTS PART B CONCERNING ARCHITECTURAL AND INDUSTRIAL MAINTENANCE COATINGS PART C STATEMENT OF BASIS, SPECIFIC STATUTORY AUTHORITY, AND PURPOSE Pursuant to Colorado Revised Statutes Section 24-4-103(12.5), materials incorporated by reference are available for public inspection during normal business hours or copies may be obtained at a reasonable cost from the Air Quality Control Commission (Commission), 4300 Cherry Creek Drive South, Denver, Colorado 80246-1530. The material incorporated by reference may also be available through the United States Government Printing Office, online at www.govinfo.gov. Materials incorporated by reference are those editions in existence as of the date indicated and do not include any later amendments. PART A CONCERNING CONSUMER PRODUCTS I. Applicability I.A. This part applies to any person who sells, supplies, offers for sale, distributes for sale, or manufactures for sale consumer products in I.A.1. The 8-hour Ozone Control Area. I.A.2. (State Only) Colorado. As marked by (State Only), the requirements are not federally enforceable. I.B. This part does not apply to I.B.1. Consumer products manufactured in Colorado solely for shipment and use outside of Colorado. I.B.2. Consumer products that do not comply with the VOC limits in Table 1 as long as the manufacturer or distributor can demonstrate both that the consumer product is intended for shipment and use outside of Colorado and that the manufacturer or distributor has taken reasonable prudent precautions to assure that the consumer product is not distributed to Colorado. -
Durrns ;:Lj;:: Reparr
Joumalof Occupationaland Envlronmcntal HyghneFor Peer Revlew Only t!A[S.gllI.- .brrnd of Oqndonat gl$[ff[** a$ Emttumandtllt3trtn Joumal of Occupatlonaland EnvlronmentalHyglene Letter to the Edltor regardlng "Alrborne exposures assoclated wlth the typlcal use of an aerosol brake cleaner durrns reparr ;:lj;:: Joumal of Oeupdonal & Envlronmental Hyglene benzeneexposure, toluene, brake cleaner, Industry funded sclstAft0N€* Manuscripts http://mcmanuscriptcentral.com/joeh; E-mail: [email protected] Page1 of9 Journalof Occupationaland EnvironmentalHygiene.For Peer Review Only 1 ,2 3 66Airborne 4 Letter to the Editor regarding exposuresassociated 5 1ryiththe typical useof an aerosolbrake cleanerduring vehicle 6 7 tepair work" 8 9 Keywords:benzene exposure, 10 toluene,brake cleaner, industry funded 11 12 ExpositionWord Count: 2102 13 14 INTRODUCTION 15 l6 17 The recently published article, Airborne exposures associated with the typical use l8 19 of an aerosol brake cleaner during vehicle repair work,o) is scientifically flawed and 20 21 misleading. ln preface, the authors do not disclose at least two important conflicts of 22 23 24 interest: l) While acknowledging that CRC Industries ("CRC") prepared the "historical" 25 26 Brakleen brake cleaner blends and paid for the field simulation, the authors didnot 27 28 mention that CRC lndustries has been a frequent defendant in benzeneexposure lawsuits 29 30 concerning ("Brakleen"), 3t its Brakleen brake cleaners and 2) lnstead ofdisclosing 32 33 specifically that one of the authors, Dr. Williams, has served as a testifying expert for 34 35 CRC in benzeneexposure lawsuits,e) the authors acknowledge only in general terms that 36 37 she is a testifring expert in benzeneexposure cases. -
Safety Data Sheet
SAFETY DATA SHEET 1. Identification Product identifier Carquest/Wearever Non Chlorinated Brake Parts Cleaner Other means of identification Product code W7340 (CRC# 93090) Recommended use Brake parts cleaner Recommended restrictions None known. Manufacturer/Importer/Supplier/Distributor information Manufactured or sold by: Company name CRC Industries, Inc. Address 885 Louis Dr. Warminster, PA 18974 US Telephone General Information 215-674-4300 Technical 800-521-3168 Assistance Customer Service 800-272-4620 24-Hour Emergency 800-424-9300 (US) (CHEMTREC) 703-527-3887 (International) Website www.crcindustries.com 2. Hazard(s) identification Physical hazards Flammable aerosols Category 1 Gases under pressure Compressed gas Health hazards Skin corrosion/irritation Category 2 Serious eye damage/eye irritation Category 2A Specific target organ toxicity, single exposure Category 3 narcotic effects Aspiration hazard Category 1 Environmental hazards Hazardous to the aquatic environment, acute Category 1 hazard Hazardous to the aquatic environment, Category 1 long-term hazard OSHA defined hazards Not classified. Label elements Signal word Danger Hazard statement Extremely flammable aerosol. Contains gas under pressure; may explode if heated. May be fatal if swallowed and enters airways. Causes skin irritation. Causes serious eye irritation. May cause drowsiness or dizziness. Very toxic to aquatic life. Very toxic to aquatic life with long lasting effects. Material name: Carquest/Wearever Non Chlorinated Brake Parts Cleaner SDS US W7340 (CRC# 93090) Version #: 01 Issue date: 12-28-2015 1 / 11 Precautionary statement Prevention Keep away from heat/sparks/open flames/hot surfaces. - No smoking. Do not spray on an open flame or other ignition source. Pressurized container: Do not pierce or burn, even after use. -
Safer Products That Work Cleaners and Degreasers for Auto Repair State/Community Hazardous Material Source Reduction
Safer Products That Work Cleaners and Degreasers for Auto Repair State/Community Hazardous Material Source Reduction Jane Paulson October 25, 2017 Minnesota Technical Assistance Program • Mission Statement: Strengthening Minnesota businesses by improving efficiency while saving money through energy, water, and waste reduction • Based in the University of Minnesota School of Public Health • Confidential, free and non-regulatory • Staff of 12 scientists and engineers with 30 years assisting business through: • Site assessment visits • Intern Program • Company team facilitation • Demonstrations & research projects • Minnesota Materials Exchange • Website, fact sheets & case studies Why Industrial Maintenance and Automotive Repair? • Most businesses perform degreasing for equipment maintenance or production processes • 7,738,000 lb VOC emissions from area sources in MN • 5% of Industrial/Commercial VOC emissions • Common methods • Aerosol degreasing cleaners • Manual parts washers What is “better”? • Does the product work? • No Hazardous Air Pollutants (HAP’s) • Low Volatile Organic Compounds (VOC’s) • Low Ozone Generator (lbs.O3/lbs.product) • Minimize MN Chemicals of Concern • Do a comparison! How do I find safer products? • TURI – Check out their Cleaner Solutions Database • Look for reputable labels: • EPA’s Safer Choice Label • Green Electronics Council - EPEAT • USDA Organics Product Comparison – SDS Information • Product A • Product B • VOC Content: 100% • VOC Content: ??? • HAP Content: 34.72% • Specific Gravity: 0.728 • Section 2: