Filling in the Details
Total Page:16
File Type:pdf, Size:1020Kb
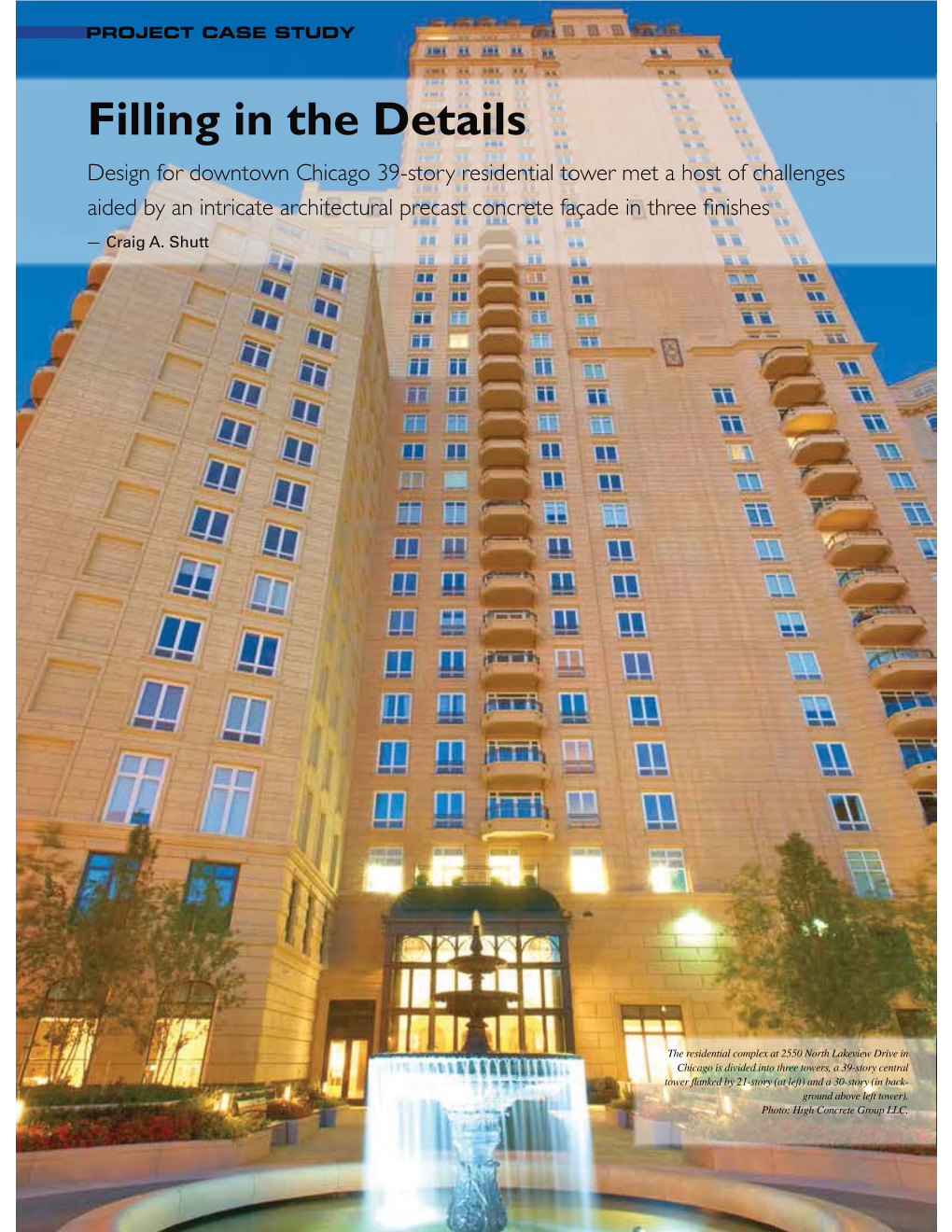
Load more
Recommended publications
-
Today's News - Monday, March 10, 2008 Arcspace Brings Us OMA in Berlin
Home Yesterday's News Calendar Contact Us Subscribe Advertise Today's News - Monday, March 10, 2008 ArcSpace brings us OMA in Berlin. -- We lose a master/inventor of Earth Architecture and Super Adobe; and an author/critic "known for his unsentimental, sometimes cantankerous demeanor." -- Sudjic on his/Burdett's "The Endless City": it's "a powerful affirmation of the city as mankind's greatest single invention." -- Hume on the "apostle of sprawl" (could O'Toole have a point?) -- Plan to spend some time with one of the most comprehensive overviews of development in Abu Dhabi. -- And an eyeful of about 60 of the fantastic (and sometimes phantasmagorical) buildings in Dubai (some are only proposed - whew!). -- An in-depth look at the infrastructure project that's making it all possible. -- Request for Qualifications (RFQ) for phase one of the redevelopment of the New Orleans Riverfront. -- Waterfront Toronto about to issue its own RFQ for two sites. -- Finding the balance between openness and security remains an ongoing challenge. -- It certainly will be with plans to bring a slice of Poundbury to a Jamaican ghetto. -- Seattle should not start genuflecting to its new skyscrapers just yet: the eco-density coalition is beginning to feel some internal splits. -- Heathcote gives a (mostly) hearty thumbs-up to NYC's New Museum. -- Finding the balance between openness and security remains an ongoing challenge. -- There may be a silver lining for Pei's Silver Towers if NYU does the right thing. -- It's a shame that architecture students "learn the best practices of their discipline in some of the worst buildings on their campuses." -- Parsons step in the right direction with an "adroit makeover" combining "style and even wit." -- Kolkata Airport taps RMJM. -
2010 Vol. 54 No. 2
SAH News Newsletter of the Society of Architectural Historians June 2010 Volume LIV, No. 2 INSIDE 2 From the SAH Executive Director 7 Buildings of the United States 3 Recap of Annual Meeting in Chicago 10 Call for Papers SAH 2011 5 SAH Benefit, April 24, 2010 12 Gifts and Donor Support 5 Treasurer’s Report 14 Announcements 6 2010 SAH Book Awards and Citations 16 Booklist SAH News JUNE / 2010 executive director’s UPDATE 2012. With University of Virginia Press, SAH will develop two editions of BUS—a home edition that will be available for free via the Internet, and a more complex scholarly edition that will be available by subscription through University of Virginia Press. NEH has designated BUS online a We the People project for its role in strengthening the teaching, study and understanding of American history and culture. NEA Funds BUS Mississippi and Teacher Workshops At the end of the month, NEA notified SAH that it would fund the initial stages of research for Buildings of Mississippi by Jennifer Baughn and Michael Fazio. The grant also will support dissemination of that research to pre-collegiate teachers throughout the State. The grant signals a new concern on the part of the SAH Board that the Society can and should play a role in developing materials that pre- collegiate teachers can use to bring architectural history and historic preservation to the classroom. The humanities-based curriculum Pauline Saliga at SAH 70th Anniversary Photo: Anne Evans complements other STEM-based curricula that focus on Science, Technology, Engineering and Math. -
Today's News - November 4, 2005 a New Charter School in Los Angeles Is an Incubator for New Ideas and New Approaches to Learning - and Teaching - Technology
Home Yesterday's News Contact Us Subscribe Today's News - November 4, 2005 A new charter school in Los Angeles is an incubator for new ideas and new approaches to learning - and teaching - technology. -- Rarity of green buildings partly because architects go for "wow" and awards. -- San Jose's new city hall is very green - so why didn't it go for LEED? -- Ideas and products (like self-cleaning cement) take green to a new level. -- No fanfare (and a potential snag) for start of construction at Ground Zero. -- Riley to resign from MoMA. -- A look back at Prince Charles urban renewal dreams; his Scully Prize purse pledged to help rebuild the Gulf Coast. -- Tall plans to change the profile of Chicago's Magnificent Mile. -- Charlotte, NC, bets on Botta for new Bechtler Museum. -- Graves tapped for two buildings at Texas A&M. -- Tiny Manhattan infill lots filling up with high-style townhouses. -- Oklahoma City lights up a Beacon of Hope. -- Q&A with Libeskind and how he manages to remain so optimistic. -- Weekend diversions: diverting (and inspiring) NYC exhibition re-imagines the taxi. -- Book reviews: "Sprawl: A Compact History"; "The Edifice Complex"; and "Archigram: Architecture Without Architecture." To subscribe to the free daily newsletter click here High Tech High - Los Angeles: A new charter school is an incubator for new ideas and new approaches to learning - and teaching - technology. -- Berliner and Associates, Architecture [images]- ArchNewsNow Commentary: Green buildings are still rare: The problem is that most architects focus on the visual impacts of their creations in order to win awards. -
MICHAEL PETRUS 209 Todd Avenue Charlottesville VA 22903 USA 434-972-9292 [email protected], [email protected]
MICHAEL PETRUS 209 Todd Avenue Charlottesville VA 22903 USA 434-972-9292 [email protected], [email protected] E D U C A T I O N Harvard University, Graduate School of Design, Master of Architecture in Urban Design, with distinction 1997 Carnegie Mellon University, College of Fine Arts, Bachelor of Architecture 1987 T E A C H I N G University of Virginia School of Architecture, Charlottesville, Virginia, Fall 2007 – Spring 2012. 301, 302, 402 level studio instructor Semester at Sea, Charlottesville, Virginia, Fall 2013, Spring 2010 voyages. Adjunct Instructor: Sustainable Urbanism, Photography. University of Virginia School of Architecture, Charlottesville, Virginia, 2000 - Present. Guest studio critic University of Wisconsin Milwaukee, Summer 2000. Adjunct instructor, traveling studio, Amsterdam-Paris-Rome University of Wisconsin Milwaukee, Spring 2000 semester. Thesis advisor for two graduate students, guest studio critic Boston Architectural Center, Boston, Massachusetts, September 1992 – June 1993. First year studio instructor Harvard University, Cambridge, Massachusetts, July 1991. Guest studio critic for GSD career discovery program North India Institute for Architecture, Ahmedabad, India, February 1994. Guest Urban Design Studio Critic Harvard University, Weld Boathouse, Cambridge, Massachusetts, June - August 1991. Sculling instructor P R O F E S S I O N A L P R A C T I C E Principal, Crisman+Petrus Architects, Charlottesville VA, 1998 – present www.crismanpetrus.us Project Architect, William McDonough + Partners Architects, -
DRUMROLL, PLEASE! Our Ranked List of the Area's Fastest-Growing
CHICAGOBUSINESS.COM | OCTOBER 12, 2020 | $3.50 DRUMROLL, PLEASE! Our ranked list of the area’s fastest-growing companies, plus pro les of the top ve. SECTION BEGINS ON PAGE 14 Divey Gulati, left, and Dhruv Saxena of ShipBob, which took the No. 1 spot on our list. PHOTO BY KENDALL KARMANIAN NEWSPAPER l VOL. 43, NO. 41 l COPYRIGHT 2020 CRAIN COMMUNICATIONS INC. l ALL RIGHTS RESERVED Whatever your heart health challenge, we’re here for you. Cardiovascular Institute At NorthShore Cardiovascular Institute, our experts provide advanced heart care for even the most complex issues. • Atrial Fibrillation—our new AFib Center offers treatment innovations and leading-edge clinical trials • Electrophysiology—pioneering the latest care for abnormal heart rhythms • Structural heart disease—bringing new hope, even to patients who’ve been told nothing can be done • Heart failure—treatment based on your DNA, including new drug therapies and clinical trials At NorthShore, we’re working to keep your heart strong for what’s next. Get the care you need—online, on the phone or in person. northshore.org/cardio | (847) 86-HEART Cardiovascular Institute RESTAURANTS: The industry is bracing for a winter of closures and layoffs. PAGE 3 DAVID GREISING: Pritzker’s “fair tax” amendment could win by losing. PAGE 2 CHICAGOBUSINESS.COM | OCTOBER 12, 2020 | $3.50 At 21 E. Huron St., 14 units are for sale, compared to eight sales in the past year. Advocate takes a turn for the worse eir apparent success in Loss of Beaumont blocking Advocate could en- deal reveals threats courage similar resistance to fu- ture acquisitions from doctors, to expansion plans communities and elected o- cials unwilling to see their local BY STEPHANIE GOLDBERG hospitals absorbed into a large, out-of-state chain. -
The First Modern Skyscraper: New York & Chicago
www.vidyarthiplus.com The The First Modern Skyscraper: New York & Chicago By: Matthew Tucker Ryan Ho Jonathan Megallon www.vidyarthiplus.com 1 www.vidyarthiplus.com Table of Contents: 1. History 2. Culture 3. Style 4. Materials and Procedures 5. The New York World Building By: Matthew Tucker 6. The Chicago Park Tower By: Jonathan Megallon 7. The Chrysler Building By: Ryan Ho www.vidyarthiplus.com 2 www.vidyarthiplus.com History Aspect A rising time: the History of the Skyscraper in New York and Chicago Skyscrapers have always represented the rising industrial age of American society in the 1900’s, and when people think of the skyscraper they imaging massive, fifty stories plus, high-rise structures. However, the term skyscraper was first applied to the first ten to twenty story buildings that began to rise in New York in the 1880’s. While in contemporary culture these building may not compete with the high-rising giants that line the skyline of New York and Chicago, during the time they were built very few building could go up beyond 8 stories with out facing serious structural issues. In 1855 a process to refine and strengthen “pig iron” (raw iron) and turn it into steel was patented by Sir Henry Bessemer, solving the structural load bearing issues that arose with large high-rise structures. Steel is vital to the development of the modern skyscraper as it provided the internal support needed to solve the structural issues that prevented architects from building massive multistory structures safely, and in the 1880’s architect Figure 1Henry Bessemer George A. -
Businesses Benefiting from ERC Training, March 29, 2011
Businesses Benefiting from ERC Training PRIVATE ORGANIZATIONS Abbot Laboratories Global Occupational Adaptive Materials Inc. Health Services ADCO #1 Installation and Design Abbott Construction Addax Petroleum Development Limited 007 Heating and Air Abbott Diagnostic Division Addax Restoration Inc. 2020 Analytical Abbott Laboratories Adena Health System 2Get Motion Physiotherapy Abbott Northwestern Hospital Adjuster Restoration Services 3 C's Cleanout, LLC Abbott Vascular ADK Properties, LLC 3 E Consultants ABC Delaware Administaff 301 Environmental Aberdeen Area IHS Adolfson and Peterson Construction 32 BJ Funds Aberdeen Proving Grounds ADOSH 3M Corporate Abington Health Lansdale Hospital ADP, Inc. 3M Inter'l Consultancy & Trng Abington Memorial Hospital Adriatic Builders 3M Occupational Health & Abisso Cleanse ADT Security Services Environmental Safety Division Abitibi Consolidated Advance Construction Services 478AESW AbitibiBowater Advance Siding 50 Beale Street Property LLC Above and Beyond Home Repair Advance Technologies 5M Inter'l Consultancy & Training ABS Consulting Advanced Elastomer Systems 61st CST (WMD) AC Corporation Advanced Environmental Services 84 Lumber Company Academy for Educational Development Advanced GeoEnvironmental, Inc. A & D Environmental Academy of Journalism and Advanced Health Resources A & J Home Improvement Communication Advanced Micro Devices A & K Painting Company Acadiana Family Physicians Advance-RGU, Inc. A and B Roofing ACANA Advantage Medical A and L Painting A-Carb, LLC Adventist Health A Clear Alternative, Inc. ACC Environmental Consultants, Inc. Advisys Inc A G S Mora ACC Transportation Advocate Healthcare A M Bailey & Associates Acceleron Pharma, Inc. Advocates for Responsible Disposal in A O Smith Water Products AcceptableRisk Texas A&B Labs Access CardioSystems, Inc. Aearo Technologies / 3M A. A. Boos & Sons Access Medical Clinic AECI A. -
View the Chicago Architects
1850 1860 1870 1880 1890 1900 1910 1920 1930 1940 1950 1960 1970 1980 1990 2000 2010 2020 DLR Group Dennis E. Bane (1992-) Amy M. Yurko (2000-2004) The Dobbins Group (1996-) Stephen Wierzbowski (2007-2008) W. Thomas Dobbins, Jr. (1996-) Alt Architecture & Research Associates The Aus n Company (2008-) Paul L. Alt (2008-) (1986-2005) Grant G. McCullagh (-1988) Juan G. Moreno (1999-2005) Aus n AECOM (2005-) CHICAGO ARCHITECTS: A GENEALOGY The McClier Corpora on AECOM/McClier Corpora on Juan G. Moreno (2005-2006) Cosmin Vrajitoru (2005-2007) A Work in Progress that built upon the “Chicago Architects: A Genealogy” published in the (1988-1996) (1996-2005) Jason Nu elman (2005-2007) Art Ins tute of Chicago’s exhibi on catalog tled Chicago Architecture and Design 1923- Grant G. McCullagh (1988-1996) Grant G. McCullagh (1996-2004) Paul L. Alt (2005-2007) Thomas (Gunny) Harboe (1988-1996) Thomas J. Rossiter (1996-2005) 1993: Reconfi guraƟ on of an American Metropolis in 1993. This project was funded through Thomas J. Rossiter (1988-1996) Douglas E. Gilbert (1997-2005) Ghafari Associates W. Thomas Dobbins, Jr. (1988-1996) Kevin M. Angell (1997-2002) a Driehaus Grant in 2012. JGMA (moreno architects) Howard M. Hirsch (1990-1994) Cosmin Vrajitoru (1999-2005) Juan G. Moreno (2006-2010) Jason Nu elman (1999-2005) Kevin M. Angell (2007-) (2010-) Project Directors: Pauline Saliga (Society of Architectural Historians) Paul L. Alt (2000-2005) Jason Nu elman (2007-2011) Juan G. Moreno (2010-) Stanley Tigerman (Tigerman-McCurry Architects) Thomas (Gunny) Harboe (1996-2005) Joseph A. Gonzalez (2010-) Cosmin Vrajitoru (2010-) Jason Nu elman (2011-) Commi ee Members: Harboe Architects Robert Bruegmann (University of Illinois at Chicago) (2006-) Hirsch Associates Kevin Harrington (Illinois Ins tute of Technology) Thomas (Gunny) Harboe (2006-) Douglas E. -
Blackstone Hotel
Click images to view full size Blackstone Hotel Chicago, Illinois Project Type: Hotel Volume 39 Number 07 April–June 2009 Case Number: C039007 PROJECT TYPE A 23-story, 332-room luxury hotel located in downtown Chicago, Illinois, the Blackstone Hotel underwent a two-year renovation and reopened in March 2008. Built in 1910, the hotel has hosted 12 presidents and its Vice- Presidential Suite is the original “Smoke-Filled Room” from which the phrase originated. Developer Sage Hospitality Resources worked to ensure that historic details were repaired or replaced when necessary, yet the hotel also includes modern conference and event facilities, as well as a coffee shop and full-service restaurant. Listed on the National Register of Historic Places and designated a city of Chicago landmark, the rehabilitation of the structure was funded in part through state and federal historic tax credits as well as tax increment financing (TIF). The hotel is now part of the Marriott Renaissance brand. LOCATION Central Business District SITE SIZE 0.44 acre/0.18 hectare LAND USES Downtown Hotel, Restaurant, Convenience Center KEYWORDS/SPECIAL FEATURES Adaptive Use Boutique Hotel Historic Preservation High-Rise Building PROJECT ADDRESS 636 South Michigan Avenue Chicago, Illinois WEB SITE www.marriott.com/chirh DEVELOPER Sage Hospitality Resources Denver, Colorado 303-595-7228 www.sagehospitality.com ARCHITECT AND PLANNER Lucien Lagrange Architects Chicago, Illinois 312-751-7400 www.lucienlagrange.com INTERIOR DESIGN The Gettys Group, Inc. 312-836-1111 Chicago, Illinois www.gettys.com GENERAL CONTRACTOR James McHugh Construction Chicago, Illinois 312-986-8000 www.mchughconstruction.com HISTORIC PRESERVATION CONSULTANT Heritage Consulting Group Portland, Oregon 503-228-0272 www.heritage-consulting.com GENERAL DESCRIPTION Part of the Marriott Renaissance brand, the Blackstone Hotel is a historic 332-room luxury hotel with conference and event space, a Starbucks coffee shop, and a full-service restaurant. -
Projects in the Midwest Region
1 Projects in the Midwest Region Principal Mutual Life Headquarters | Des Moines, IA Architect: Murphy/Jahn University of Iowa, Iowa Center for the Arts | Iowa City, IA Architect: Harrison & Abramovitz University of Chicago, South Campus Residences and Dining Hall | Chicago, IL Architect: Goody Clancy 150 North Riverside - LEED Gold Precertified | Chicago, IL Architect: Goettsch Partners 500 North Lake Shore Drive - LEED Silver | Chicago, IL Architect: Solomon Cordwell Buenz Majestic Harbor Resort | Gurnee, IL Architect: The Hnedak Bobo Group Grand Park Tower One | Chicago, IL Architect: Pappageorge Haymes Partner Left Bank Residential | Chicago, IL Architect: DeStefano + Partners Prairie House/Parcel G Condominiums | Chicago, IL Architect: DeStefano + Partners The Residences on Lake Shore Park (The Pearson - 250 East Pearson and The Belvedere - 270 East Pearson) | Chicago, IL Architect: DeStefano + Partners Thompson, Ventulett, Stainback & Associates Offices - LEED Gold Certified | Chicago, IL Architect: Thompson, Ventulett, Stainback & Associates Steelcase Showroom - LEED Gold Certified | Chicago, IL Architect: Shimoda Design Group Steelcase SPG Showroom - LEED Gold Certified | Chicago, IL Architect: Luce et Studio / Cubellis Ziegler - LEED Certified | Chicago, IL Architect: Solomon Cordwell Buenz Unicom Thermal Technologies, Columbus and Randolph Plant | Chicago, IL 2 2550 Lincoln Park - LEED Gold | Chicago, IL Architect: Lucien Lagrange / Solomon Cordwell Buenz 1233 North Wells - LEED Silver | Chicago, IL Architect: Hartshorne Plunkard -
2007 the Newsletter of CHICAGO WOMEN in ARCHITECTURE Promoting the Interests and Addressing Issues of Women in Architecture Since 1973
winter 2007 The newsletter of CHICAGO WOMEN IN ARCHITECTURE promoting the interests and addressing issues of women in architecture since 1973. [From CWA’s President] [Calendar of Events] GREEN…Reconsidered. Confirm dates, times and locations with the sponsoring organization. Past Presidents 2007-2008 Officers 2007-2008 Corporate Members Be sure to check the CWA website periodically for new events! Meggan Lux Beth Erickson, President Graham Foundation I have to admit that over the past few months I’ve Rebecca Callcott Rachel Miller Branagan, Vice President Harley Ellis Devereaux grown a little tired of hearing about “green” design. Melissa Bogusch Mindy Viamontes, Vice President Hutter Architects, Ltd. It’s everywhere – at conference seminars, on book December 2007 Lisa Kulisek Deborah Fox, Secretary Lucien Lagrange Architects jackets and magazine covers, in the grocery aisle, on television, in the stock market, and on the road. In [06] CWA Holiday Party @ Prairie Avenue Bookshop: 418 S Wabash. Enjoy Susan van der Meulen Rebecca Callcott, Treasurer Muller+Muller, Ltd. the season, support the CWA Scholarship Foundation and start your Elizabeth Purdy Proteus Group, LLC fact, in green building products and services alone, the USGBC estimates that the annual U.S. market was more than $7 billion in 2005 and is now holiday shopping at Prairie Avenue Bookshop. Guest Speaker: Sarah Kay Wulf URBANWorks, Ltd. Herda, Director of the Graham Foundation. Cocktail Reception 6:00pm, Susan King nearing $12 billion in 2007. It’s not that I’m upset that “green” is going 2007-2008 Board of Directors mainstream – quite the contrary, it’s a trend that needs to become ingrained Presentation 6:30pm. -
[From CWA's President] [Calendar of Events]
spring 2008 The newsletter of CHICAGO WOMEN IN ARCHITECTURE promoting the interests and addressing issues of women in architecture since 1973. [From CWA’s President] Past Presidents 2007-2008 Officers 2007-2008 Corporate Members [URBAN] RECONNAISSANCE linger. There are, however, two interesting exceptions: [1] Canal Origins Park: One of the City’s newest parks, this 1.8 acre open Meggan Lux Beth Erickson, President Graham Foundation space marks the starting point of the historic Illinois and Michigan canal, Rebecca Callcott Rachel Miller Branagan, Vice President Harley Ellis Devereaux For years I had heard about Bubbly Creek, a stretch showcases current environmental remediation and restoration efforts to Melissa Bogusch Mindy Viamontes, Vice President Hutter Architects, Ltd. of the Chicago River so polluted by organic waste stabilize the banks of Bubbly Creek, and allows rare public access to the Lisa Kulisek Deborah Fox, Secretary Lucien Lagrange Architects from the Union Stockyards that even a century later water’s edge. Susan van der Meulen Rebecca Callcott, Treasurer Muller+Muller, Ltd. the contamination purportedly still causes bubbles of Elizabeth Purdy Proteus Group, LLC methane and hydrogen sulfide to rise to the surface. [2] Bridgeport Village: With 115 homes already constructed and prices Kay Wulf URBANWorks, Ltd. Curious to see if the notorious creek would live up to its name, I decided ranging from the mid $600,000s to over $1 million, this new residential Susan King 2007-2008 Board of Directors one Saturday last month to investigate. After first spending some time development features a meandering promenade along the east bank of Patricia Saldana Natke Sponsors online researching historic and current maps, I learned that Bubbly Creek Bubbly Creek.