Corrosion in CO2 Post-Combustion Capture with Alkanolamines – a Review
Total Page:16
File Type:pdf, Size:1020Kb
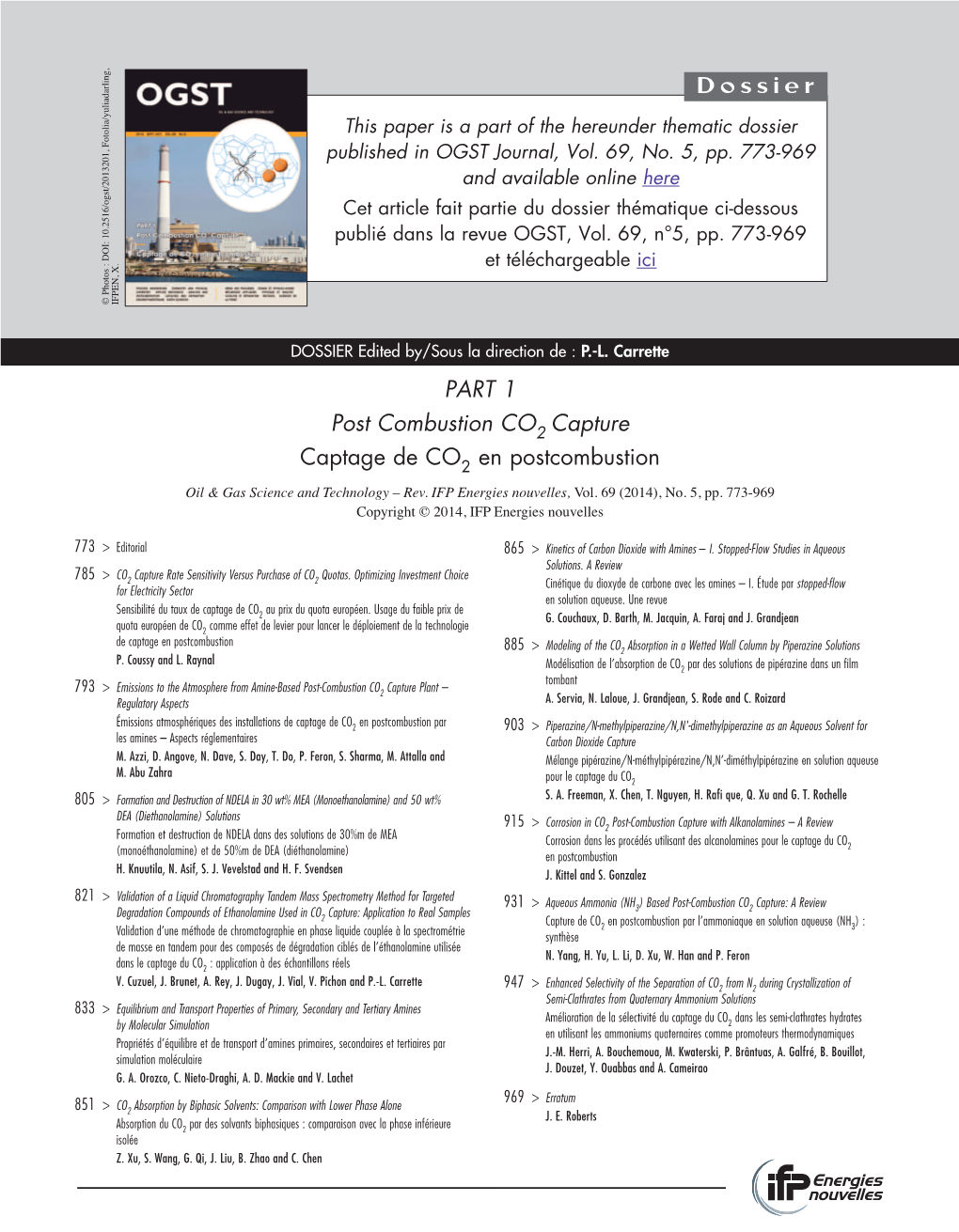
Load more
Recommended publications
-
CO2 Removal by Amine Absorption and Condensed Rotational Separation: Energy Consumption & Equipment Sizing
CO2 removal by Amine Absorption and Condensed Rotational Separation: Energy Consumption & Equipment Sizing by STEVEN JAN MARTIN DE RIJKE BSc in Mechanical Engineering THESIS submitted in partial fulfillment of the requirements for the degree MASTER OF SCIENCE: MECHANICAL ENGINEERING Department of Mechanical Engineering Technical University Eindhoven Document Number: WPT201214 November 30, 2012 Approved by: prof. dr ir J.J.H. Brouwers dr. ir H.P. van Kemenade prof.dr. M. Golombok dr.ir. J. van der Schaaf Acknowledgment The author wishes to thank J.J.H. Brouwers & H.P. van Kemenade for the idea for this work and their support throughout the process R.J. van Benthum for his insightful help and his time Romico Hold for access to proprietary knowledge regarding the RPS and related processes. J.M. de Rijke & E.A. de Rijke-Amesz for their patience and support ii SUMMARY/ABSTRACT The Rotational Particle Separator (RPS) is a compact device capable of separating micron-sized droplets from gases by centrifugation. Combined with expansion cooling in a turbine at semi-cryogenic temperatures, it provides the opportunity to remove contaminants like CO2 and H2S from natural gas. Potential advantages of this technique are lower energy consumption and compactness. To demonstrate its potential, the technology is compared on the basis of installed volume and energy consumption with conventional amine technology for a range of CO2 concentrations. The comparison is made using a model of both processes and their components separating a range of CO2 contents from a 125 MMscf/day gas stream. The results show that for CO2 concentrations greater than 15% the CRS technology offers significant advantages in both installed volume and energy requirement, unlocking natural gas fields with sour gas concentrations that cannot be treated with conventional technology up until well in the 70% CO2 content. -
Environmental, Health, and Safety Guidelines for Petroleum Refining
ENVIRONMENTAL, HEALTH, AND SAFETY GUIDELINES PETROLEUM REFINING November 17, 2016 ENVIRONMENTAL, HEALTH, AND SAFETY GUIDELINES FOR PETROLEUM REFINING INTRODUCTION 1. The Environmental, Health, and Safety (EHS) Guidelines are technical reference documents with general and industry-specific examples of Good International Industry Practice (GIIP).1 When one or more members of the World Bank Group are involved in a project, these EHS Guidelines are applied as required by their respective policies and standards. These industry sector EHS Guidelines are designed to be used together with the General EHS Guidelines document, which provides guidance to users on common EHS issues potentially applicable to all industry sectors. For complex projects, use of multiple industry sector guidelines may be necessary. A complete list of industry sector guidelines can be found at: www.ifc.org/ehsguidelines. 2. The EHS Guidelines contain the performance levels and measures that are generally considered to be achievable in new facilities by existing technology at reasonable costs. Application of the EHS Guidelines to existing facilities may involve the establishment of site-specific targets, with an appropriate timetable for achieving them. 3. The applicability of the EHS Guidelines should be tailored to the hazards and risks established for each project on the basis of the results of an environmental assessment in which site-specific variables— such as host country context, assimilative capacity of the environment, and other project factors—are taken into account. The applicability of specific technical recommendations should be based on the professional opinion of qualified and experienced persons. 4. When host country regulations differ from the levels and measures presented in the EHS Guidelines, projects are expected to achieve whichever is more stringent. -
Amine Systems
2014 JUNE H2S Scavenging: Amine Systems This GATEKEEPER focuses on Amine Systems, one of the most commonly used regenerative H2S scavengers in the Oil & Gas industry. Solution Loading H S > CO Amine 2 2 Amine (wt%) (mole / mole) Selectivity Amines are organic compounds derived from ammonia with substitution of one or all of the hydrogens with MEA 15 - 20 0.30 - 0.35 No alkyl or aryl groups, retaining a basic nitrogen atom with one lone pair of electrons. They can be classified as Primary, Secondary, Tertiary, or Cyclic. DEA 25 - 35 0.30 - 0.35 Limited . Primary – One of three hydrogen atoms is replaced by alkyl or aryl groups DGA 50 - 70 0.30 - 0.35 No . Secondary – Two of the three hydrogen atoms are replaced by alkyl or aryl groups Condition MDEA 20 - 50 0.70 - 0.80 . Tertiary – All three hydrogen atoms are replaced by alkyl or aryl groups Dependent . Cyclic – Either secondary or tertiary amines with a cyclic structure with hydrogen atoms replaced Loading values are based on use in carbon steel systems by alkyl or aryl groups without corrosion inhibitor treatment* Amine Solution Selection Table 1: Amine Operating Ranges The amine selected, as well as the concentration of the solution used, will result in different selectivity of H2S over CO2, mole-to-mole acid gas loading, and degradation of the amine. Blended solutions incorporating more than one amine, as well as specialty designed amine molecules, can be used to increase selectivity, loading, and degradation characteristics of the final solution. Typical operating ranges for common amines have been given in Table 1. -
1983: Fundamentals of Gas Sweetening
FUNDAMENTALS OF GAS SWEETENING K, F, BUTWELL L, KROOP UNION CARBIDE CORPORATION TARRYTOWN, NEW YORK Natural gas has a wide range of acid gas concentrations, from parts per million to 50 volume percent and higher, depending on the nature of the rock formation from which it comes. Because of the corrosiveness of H2S and CO 2 in the presence of water and because of the toxicity of H2S and the lack of heating value of C02, sales gas is required to be sweetened to contain no more than a quarter grain H2S per 100 standard cubic feet (4 parts per million) and to have a heating value of no less than 920 to 980 Btu/SCF, depending on the contract. The most widely used processes to sweeten natural gas are those using the alkanol- amines, and of the alkanolamines the two most common are mono- ethananolamine (MEA) and diethanolamine (DEA). THE AMINE SWEETENING PROCESS The monoethanolamine and diethanolamine sweetening processes are similar in their flow schemes and operations. They are used as aqueous solvents to selectively absorb H2S and CO 2 from sour natural gas streams. The sour gas is introduced at the bottom of an absorber and flows up the tower countercurrent to an aqueous amine stream. Within the tower the acid gases are ab- sorbed by the amine. The amine is described as being lean in acid gas as it enters the top of the absorber, and rich as it exits the bottom, loaded with acid gas. From the absorber the rich amine is directed to the top of a stripping tower where a drop in pressure and application of heat enables the solvent to be stripped of the acid gases. -
Contaminant Reporting in Amine Gas Treating Service
Contaminant Reporting in Amine Gas Treating Service By Randy Haws and Jim Jenkins CCR Technologies Inc. 11375 West Sam Houston Pkwy South Suite 201 Houston, Texas 77031 ABSTRACT For a number of years the gas treating and refining industries have been focusing on Heat Stable Salts (HSS) contamination in amine service. As knowledge continues to improve in this area, amine system efficiencies are improved and turnaround cycles are minimized. However, two unfortunate states still exist in the industry: (1) analytical reporting for HSS is not consistent and is often times confusing to operators, and (2) HSS is only one of the major contaminants in a gas treating solution. A better understanding of the full range of contaminants and degradation products is essential to achieving total solvent quality. This paper will review current reporting and terminology so that confusion in analyzing contaminants and sample results may be minimized. INTRODUCTION There is a wealth of literature available in the industry on the corrosive nature and proper control targets for Heat Stable Salts (HSS).1-4 Unfortunately it is easy to be confused about measured levels and reporting terminology of these HSS anions. This confusion is compounded by the fact that comparing these measured values to proper control points may be difficult if they are not compared on a consistent basis. HSS are also generally only a part of the contaminants present in the gas treating solution so, it is important to understand the total level of contaminants and degradation products present in the processing solution. This is important for the operator to know because, as the level of contaminants and degradation products increase, the physical properties of the solution may change. -
The Hydrodesulfurization of Diesel Fuel to Meet New Epa
THE HYDRODESULFURIZATION OF DIESEL FUEL TO MEET NEW EPA REQUIREMENTS By FAUSTO ISRAEL MARES-DAVILA ____________________ A Thesis Submitted to The Honors College In Partial Fulfillment of the Bachelors degree With Honors in Chemical Engineering THE UNIVERSITY OF ARIZONA M A Y 2016 Approved by: ____________________________ Dr. Kim Ogden Department of Chemical and Environmental Engineering Abstract In December 1, 2010 the EPA reduced the allowable sulfur content in diesel fuel to 15 ppm, which is now known as ultra-low sulfur diesel (ULSD). In order to reach the 15 ppm sulfur maximum, the hydrodesulfurization unit in many refineries had to be upgraded. The group has been tasked with developing an upgrade catalytic hydrodesulfurization unit for a refinery in the Delaware Valley that can treat 35,000 barrels per stream day (BPSD) of liquid feedstock containing 1.9 wt % sulfur. Performance data from the existing catalytic hydrodesulfurization unit was used to predict the performance of the upgraded unit. ChemCAD software was used for the process calculations and the feed was modeled using boiling curve data. The desulfurization reaction kinetics were based on the reduction of dibenzothiophene. The project goals are to achieve a 99% recovery of diesel fuel while reducing the sulfur content below 15 ppm. The liquid feedstock will be run through a packed bed reactor filled with CoMo/Al2O3 catalyst where the sulfur compounds will react with hydrogen gas to form hydrogen sulfide gas. An amine contactor will be used to remove sour gas from the recycle hydrogen stream and a distillation column will produce diesel. The work presented in this report is the combined effort of Fausto Mares-Davila, Jason Green, Toluwani Omotinugbon, and Jun Terashima. -
Statement of Basis for Crude Expansion
Statement of Basis Draft Greenhouse Gas Prevention of Significant Deterioration Preconstruction Permit for the Diamond Shamrock Refining Company, L.P., Valero McKee Refinery Permit Number: PSD-TX-861-GHG July 2013 This document serves as the statement of basis for the above-referenced draft permit, as required by 40 CFR § 124.7. This document sets forth the legal and factual basis for the draft permit conditions and provides references to the statutory or regulatory provisions, including provisions under 40 CFR § 52.21, that would apply if the permit is finalized. This document is intended for use by all parties interested in the permit. I. Executive Summary On December 2, 2011, Diamond Shamrock Refining Company, L.P., (a Valero company), submitted a Greenhouse Gas (GHG) Prevention of Significant Deterioration (PSD) permit application to EPA Region 6 to authorize a modification at Valero McKee Refinery, an existing major source of criteria pollutants. In connection with the same proposed project, Valero submitted a PSD application for non-GHG pollutants to the Texas Commission on Environmental Quality (TCEQ) on December 2, 2011. In November 2012, Valero requested that TCEQ withdraw its permit amendment application. A new permit application was submitted on December 7, 2012 to the TCEQ for non-GHG pollutants, and an update was submitted to the EPA Region 6 for the GHG PSD permit application. The project at the McKee Refinery, herein referred to as the Crude Expansion Project, proposes to modify certain equipment which will allow for an increase in the overall processing of crude oil from 169,000 barrels per day to 210,000 barrels per day. -
FLUOR CORTDORATION, LT E X =
-T_HE FLUOR CORTDORATION, LT e X = "3 4 I5 rar O ,........VI':1 li41%,.. 1 11 Ì' .11 f- . r» 6' .-= ea- ,.. S W: .:frt Al 0.--- .. - 7 - kit.- = , / I = 01 L?' u -7- 4 .!$ 4160i a a SINCE 1 8 9 0 )49 to the Employees and Shareholders of THE FLUOR CORPORATION,, LTD. ENGINEERS MANUFACTURERS CONSTRUCTORS 2500 S. ATLANTIC BLVD., LOS ANGELES 22 Metal Product Fabrication, Mfg. Division, Paola, Kansas Mid-Continent Gas-Gasoline Department, Houston, Texas eX14 awei2emke e#,Ceit he ae QintAaleAWAI Los AngelesSan FranciscoNew York Chicago Boston Pittsburgh Tulsa Houston 7 Yet41 emelY~ke MO/teJenk&9-1 off4We QkWeir Rak,,) 16169/aft e AIal/ Yki4iT ,Ofteeui fitWeritada ,./(ereeo Head Wrightson Processes Ltd. The Fluor Corporation Servicios Indust ria les of Canada, Ltd. De Mexico, S. A. Message to Employees and Shareholders 4. and 5 , 1949 Income and Expenditures 6 and 7 10 Years' Income and Expenditures 8 and 9 Manufactured Products 10 and I 1 "Xe Kezdez notylawyi Wertiff#& eraihrowieft4 Engineering and Construction 12 and I 3 MECHANICAL DESIGN AND CONSTRUCTION OF THIS COMPLETE REFINERY Research J 4 and 15 WAS COMPLETED BY FLUOR IN 1949 Sales 16 and 17 Ownership of Fluor 18 Employee Benefits 19 Balance Sheet 20 and 21 Board of Directors and Honor Roll 22 and 23 e u,,dyiy,/aa, The year 1949 was another outstanding year in the Arrangements have been concluded with the Amen- in the interpretation of company personnel policy, resulting history of The Fluor Corporation, Ltd. The volume of work can Smelting and Refining Company whereby we will handle in a more equitable treatment of all employee problems. -
Environmental, Health, and Safety Guidelines for Petroleum Refining
This document is NO LONGER IN USE by the World Bank Group. The new version of the World Bank Group Environmental, Health and Safety Guidelines are available at http://www.ifc.org/ehsguidelines Environmental, Health, and Safety Guidelines PETROLEUM REFINING RAFT FOR ECOND UBLIC ONSULTATION MARCH D S P C — 2016 WORLD BANK GROUP Environmental, Health, and Safety Guidelines for Petroleum Refining Introduction 1. The Environmental, Health, and Safety (EHS) Guidelines are technical reference documents with general and industry-specific examples of Good International Industry Practice (GIIP)1. When one or more members of the World Bank Group are involved in a project, these EHS Guidelines are applied as required by their respective policies and standards. These industry sector EHS guidelines are designed to be used together with the General EHS Guidelines document, which provides guidance to users on common EHS issues potentially applicable to all industry sectors. For complex projects, use of multiple industry sector guidelines may be necessary. A complete list of industry-sector guidelines can be found at: www.ifc.org/ehsguidelines 2. The EHS Guidelines contain the performance levels and measures that are generally considered to be achievable in new facilities by existing technology at reasonable costs. Application of the EHS Guidelines to existing facilities may involve the establishment of site-specific targets, with an appropriate timetable for achieving them. 3. The applicability of the EHS Guidelines should be tailored to the hazards and risks established for each project on the basis of the results of an environmental assessment in which site-specific variables, such as host country context, assimilative capacity of the environment, and other project factors, are taken into account. -
AMINE DEGRADATION and ASSOCIATED PROBLEMS in the GAS TREATING UNIT E.R.Baumeister1 , R.C.O.Souza2
IBP2323_08 AMINE DEGRADATION AND ASSOCIATED PROBLEMS IN THE GAS TREATING UNIT E.R.Baumeister1 , R.C.O.Souza2 Copyright 2008, Instituto Brasileiro de Petróleo, Gás e Biocombustíveis - IBP Este Trabalho Técnico foi preparado para apresentação na Rio Oil & Gas Expo and Conference 2008, realizada no período de 15 a 18 de setembro de 2008, no Rio de Janeiro. Este Trabalho Técnico foi selecionado para apresentação pelo Comitê Técnico do evento, seguindo as informações contidas na sinopse submetida pelo(s) autor(es). O conteúdo do Trabalho Técnico, como apresentado, não foi revisado pelo IBP. Os organizadores não irão traduzir ou corrigir os textos recebidos. O material conforme, apresentado, não necessariamente reflete as opiniões do Instituto Brasileiro de Petróleo, Gás e Biocombustíveis, seus Associados e Representantes. É de conhecimento e aprovação do(s) autor(es) que este Trabalho Técnico seja publicado nos Anais da Rio Oil & Gas Expo and Conference 2008. Resumo A degradação das aminas e os problemas relacionados em uma unidade de tratamento de gás, não podem ser evitados ou eliminados completamente, entretando, podem ter seus custos eficazmente atenuados usando um programa profundo de gerenciamento da unidade. Os benefícios econômicos e de desempenho, a partir de um programa de gerenciamento da amina, incluem diversas melhorias e índice de desempenho. Melhoria de desempenho, custos operativos mais baixos, e baixo impacto ambiental são algumas das vantagens adicionais de se usar um sistema de gerenciamento detalhado de uma unidade de tratamento de gás. Summary Amine degradation and associated problems in the amine gas treating unit cannot be completely avoided or eliminated. They can be cost effectively mitigated using a thorough amine management program. -
Process Simulation, Economic and Environmental Sustainability
ineering ng & E P l r a o c i c e m s Gai et al., J Chem Eng Process Technol 2018, 9:1 e s Journal of h T C e f c DOI: 10.4172/2157-7048.1000373 h o l ISSN: 2157-7048 n a o n l o r g u y o J Chemical Engineering & Process Technology Research Article Article OpenOpen Access Access Process Simulation, Economic and Environmental Sustainability Assessment of a Gas-To-Liquids Process Huilong Gai, Kailiang Zheng, Julia Lin and Helen H Lou* Dan F Smith Department of Chemical Engineering, Lamar University, Beaumont, USA Abstract Natural gas is recognized as one of the cleanest and most abundant fossil fuels. In the past decades, the price ratio of crude oil to natural gas has continuously fluctuated. The gas-to-liquid industry has received continuous interest due to the abundant supply of conventional and unconventional natural gas (shale gas, etc.), as well as the environmental advantages of FT technology. The GTL process chemically converts natural gas to long chain hydrocarbons (naphtha, diesel, wax, etc.) through three main steps, i.e., natural gas reforming, Fischer-Tropsch synthesis (FTS), and products upgrading. In this work, a rigorous simulation model including gas sweetening, syngas production, FTS, and product fractionation is provided. Among different routes for natural gas reforming and different reactors for FTS in a GTL process, autothermal reforming (ATR) and slurry bubble column reactor (SBCR) were chosen respectively, due to their advantages over other solutions. Meanwhile, the economic and environmental analyses were also conducted for the sustainability assessment of provided GTL process using Aspen Icarus and WAR software. -
Diethanolamine (Dea), Methyldiethanolamine (Mdea)
OIL REFINING AND PETROCHEMICAL APPLICATION NOTE 8.02.02 AMINE GAS TREATING AND H2S/CO2 REMOVAL MONOETHANOLAMINE (MEA), DIETHANOLAMINE (DEA), METHYLDIETHANOLAMINE (MDEA) Typical end products Pipeline quality dry natural gas, liquefed petroleum gas (LPG). unit process used in refneries, petrochemical plants, Chemical curve: MDEA R.I. per Conc% b.w. at Ref. Temp. of 20˚C natural gas processing plants and other industries. The acid gas absorption in amine solution is conducted using a two-column operation: the frst column is used to absorb the acid gas into the absorbent amine, the second column is used to regenerate the amine. The process relies on counter current fow to achieve optimum mixing. A lean solution (low acid gas) enters the top of the absorber and fows to the bottom; acid gas enters the bottom of the absorber tower and bubbles to the top. The rich amine (high acid gas) enters the stripper, Introduction where the acid gases are released, and the clean amine is returned to the absorber. The acid gases Natural gas contains signifcant amount of hydrogen collect and exit at the top of the stripper. sulfde (H2S) and carbon dioxide (CO2). Natural gas is also referred to as sour gas because of its strong odor, Application caused by the sulfur content. These sulfur compounds render it extremely harmful, even lethal, to breathe. In the regeneration process the amine can degrade Natural gas can also be extremely corrosive. Carbon or be depleted. In order to achieve the proper acid dioxide must be removed before the gas can be gas removal, the optimum amine concentration must transformed into liquid form (liquefaction LNG) for be maintained.