Optimum Water Jets Inclination Angle for Better Tensile Strength in Hydroentanglement Process
Total Page:16
File Type:pdf, Size:1020Kb
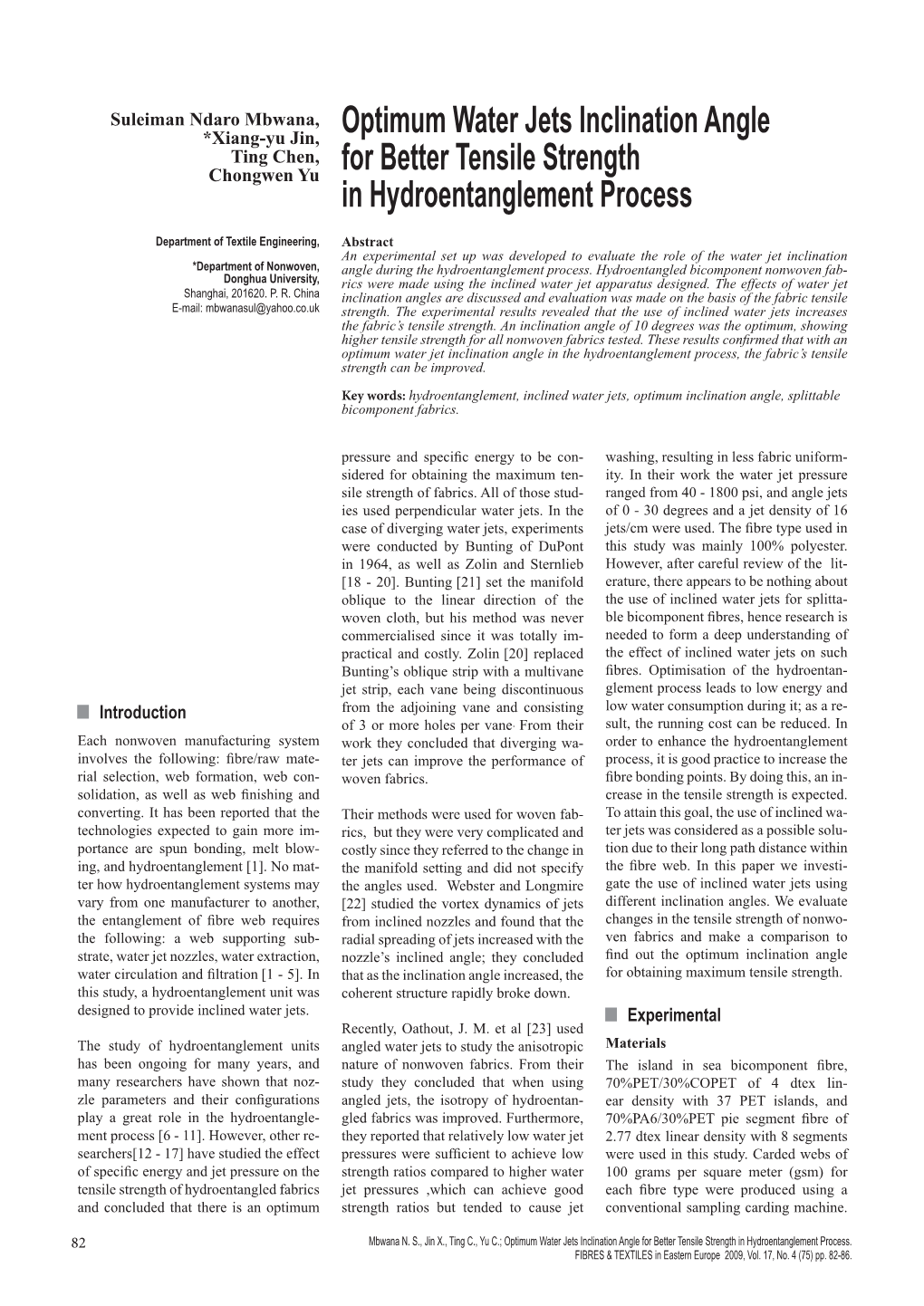
Load more
Recommended publications
-
United States Patent (19) 11 Patent Number: 5,620,785 Watt Et Al
US00562O785A United States Patent (19) 11 Patent Number: 5,620,785 Watt et al. (45) Date of Patent: Apr. 15, 1997 54 MELTBLOWN BARRIER WEBS AND 4,662,005 5/1987 Grier-Idris. PROCESSES OF MAKING SAME 4,807,619 2/1989 Dyrud et al.. 4,813,948 3/1989 Insley . 75) Inventors: James M. Watt, Piedmont; Deborah 4,863,785 9/1989 Berman et al.. K. Lickfield, Easley, both of S.C. 4,874,399 10/1989 Reed et al.. 4,874,659 10/1989 Ando et al. 4,920,960 5/1990 Hubbard et al. 73) Assignee: Fiberweb North America, Inc., 4,921,645 5/1990 Insley. Simpsonville, S.C. 4,969,457 11/1990 Hubbard et al.. 5,122,048 6/1992 Deeds. 21) Appl. No.: 475,949 5,149,468 9/1992 Hershelman. 5,150,703 9/1992 Hubbard et al.. (22 Filed: Jun. 7, 1995 5,254.297 10/1993 Deeds. 5,306,534 4/1994 Bosses. (51 Int. Cl." ........................... A62B 23/00; A62B 23/06; 5,307.796 5/1994 Kronzer et al.. ED04H 1/72 5,322,061 6/1994 Brunson. 52 U.S. Cl. ...................... 428/219; 55/528; 55/DIG. 39; 5,409,766 4/1995 Yuasa et al. ............................ 428/903 128/206. 12; 156/624; 264/DIG. 48; 428/311.11; 5,436,066 7/1995 Chen ....................................... 428/903 428/311.51; 428/315.5; 428/338; 428/903; 5,482,765 1/1996 Bradley et al. ....... ... 428/286 442/400 5,486,411 1/1996 Hassenboehler, Jr. .... ... 428/286 58) Field of Search .................................... -
Glossary Nonwovens Terms
GLOSSARY of GLOSSARY NONWOVENS TERMS For further information please contact EDANA Tel: +32 (0) 2 734 93 10 Fax : +32 (0) 2 733 35 18 Email: [email protected] www.edana.org www.edana.org A ABRASION RESISTANCE The ability of a fibre or fabric to withstand surface wear and rubbing ABSORPTION The process by which a gas or liquid is taken up within a material. ACTINIC DEGRADATION Strength loss or weakening of fibres and fabrics due to exposure to sunlight. ADDITIVES Chemicals added or incorporated in materials to give them different functional or aesthetic properties, such as flame retardancy and/or softness. ADHESION The force that holds different materials together at their interface. ADHESIVE A material, flowable in solution or when heated, that is used to bond materials together. ADHESIVE MIGRATION The movement of adhesive together with its carrier solvent, in a fabric during drying, giving it a non- uniform distribution within the web; usually increasing towards the outer layers. ADSORPTION The process by which a gas or liquid is taken up by the surface of a material. AESTHETICS Properties perceived by touch and sight, such as the hand, colour, lustre, drape, and texture of fabrics. AFTERGLOW The flameless, ember-like burning of a fabric. EDANA 2 AFTER TREATMENT (FINISHING) Process usually carried out after a web has been formed and bonded. Examples are embossing, creping, softening, printing and dyeing. AGGLOMERATION A cluster of particles or fibres. AGEING Processing in which products are exposed to environmental conditions that simulate real use or accelerated use, for the purpose of determining their effect on the functional and aesthetic properties of the products. -
Short Fiber Wood Pulp --- Long Fiber Synthetics U.S
USOO6110848A United States Patent (19) 11 Patent Number: 6,110,848 Bouchette (45) Date of Patent: Aug. 29, 2000 54 HYDROENTANGLED THREE PLY WEBS 5,026,587 6/1991 Austin et al.. AND PRODUCTS MADE THEREFROM 5,151,320 9/1992 Homonoff. 5,246,772 9/1993 Manning. 75 Inventor: Michael Paul Bouchette, Sherwood, 5,393,599 2/1995 Quantrille et al.. Wis 5,413,849 5/1995 Austin et al.. 5,587.225 12/1996 Griesbach et al.. 73 Assignee: Fort James Corporation, Deerfield, Ill. Primary Examiner Terrel Morris ASSistant Examiner-Norca L. Torres 21 Appl. No.: 09/169,067 57 ABSTRACT 22 Filed: Oct. 9, 1998 A three ply Sandwich Structured hydroentangled web is 51) Int. Cl." ................................. B32B5/26: B32B 7/08 disclosed. The top and bottom plies of this web comprise 52 U.S. Cl. .......................... 442/384; 442/381; 442/387; long synthetic fibers having a fiber length of about 30 to 100 442/389; 442/408; 442/412 mm and the middle ply comprises cellulosic fibers having a 58 Field of Search ..................................... 442/387, 384, fiber length of about 1 to 8 mm. The middle layer cellulosic 442/389, 408, 412 fiber can optimally be wholly or partially replaced with short Synthetic or other natural fibers having a fiber length of 56) References Cited about 6 to 27 mm. U.S. PATENT DOCUMENTS These hydroentangled WebS are useful in the manufacture of 4,775,579 10/1988 Hagy et al.. towels, wet wipes, industrial wipes and medical gowns. 4,808,467 2/1989 Suskind et al. -
Development of Nonwoven Fabrics for Clothing Applications
e e Sci nce Cheema et al., J Textile Sci Eng 2018, 8:6 til & x e E T n : g DOI 10.4172/2165-8064.1000382 f o i n l e a e n r r i n u g o Journal of Textile Science & Engineering J ISSN: 2165-8064 Research Article Article OpenOpen Access Access Development of Nonwoven Fabrics for Clothing Applications Cheema MS1*, Anand SC1 and Shah TH2 1Institute of Materials Research and Innovation, University of Bolton, Deane Road, Bolton BL3 5AB, United Kingdom 2National Textile University, Pakistan Abstract The apparel fabric manufacturing is a growing sector of the global textile industry and the fabrics used in this market are mainly produced by the conventional methods such as weaving and knitting processes. These methods of making apparel fabrics are length and costly. However, because of the advancements in nonwoven technology, nonwoven fabrics are finding a niche market in the clothing industry because of its cost effectiveness and high speeds of nonwoven production processes. We have carried out an extensive study on the development of apparel- like nonwoven fabrics. The resultant fabric showed improved drape, hand, durability and thermophysiological comfort characteristics than the reference samples for apparel applications. Results of the study also showed that the developed nonwoven fabrics showed nearly 200% higher tensile strength than the reference nonwoven fabrics. Furthermore, it also showed improved air permeability, for example, the resultant nonwoven fabric exhibited 500% higher air permeability value as compared with the Evolon fabric at 100 Pa pressure. Thus the results of the study indicate that the resultant nonwoven fabrics may be used in a wide range of apparel applications, which can lead to additional benefits in terms of cost and time. -
Influence of Material Variables in Thermal Bonding of Nonwovens
University of Tennessee, Knoxville TRACE: Tennessee Research and Creative Exchange Masters Theses Graduate School 5-2006 Influence of Material ariablesV in Thermal Bonding of Nonwovens Raghavendra Ratnakar Hegde University of Tennessee - Knoxville Follow this and additional works at: https://trace.tennessee.edu/utk_gradthes Part of the Materials Science and Engineering Commons Recommended Citation Hegde, Raghavendra Ratnakar, "Influence of Material ariablesV in Thermal Bonding of Nonwovens. " Master's Thesis, University of Tennessee, 2006. https://trace.tennessee.edu/utk_gradthes/1576 This Thesis is brought to you for free and open access by the Graduate School at TRACE: Tennessee Research and Creative Exchange. It has been accepted for inclusion in Masters Theses by an authorized administrator of TRACE: Tennessee Research and Creative Exchange. For more information, please contact [email protected]. To the Graduate Council: I am submitting herewith a thesis written by Raghavendra Ratnakar Hegde entitled "Influence of Material Variables in Thermal Bonding of Nonwovens." I have examined the final electronic copy of this thesis for form and content and recommend that it be accepted in partial fulfillment of the requirements for the degree of Master of Science, with a major in Materials Science and Engineering. Gajanan Bhat, Major Professor We have read this thesis and recommend its acceptance: Larry C. Wadsworth, Roberto S. Benson Accepted for the Council: Carolyn R. Hodges Vice Provost and Dean of the Graduate School (Original signatures are on file with official studentecor r ds.) To the Graduate Council: I am submitting herewith a thesis written by Raghavendra Ratnakar Hegde entitled "Influence of Material Variables in Thermal Bonding of Nonwovens." I have exam- ined the final electronic copy of this thesis for form and content and recommended that it be accepted in partial fulfillment of the requirements for the degree of Masters of Science, with a major in Material Science and Engineering. -
10. Recent Developments in Spinning and Non-Wovens
10. Recent Developments in Spinning and Non-wovens Martin Prins, Niall Finn and Errol Wood Learning objectives On completion of this topic you should be able to: • Describe the latest developments in worsted spinning including ring, collapsed balloon, and compact spinning • Outline bicomponent yarns, two-folding, winding and clearing • Outline developments in non-woven processing • Describe cross-lapping, and compare bonding systems such as needlepunching, stitch and hydroentanglement Key terms and concepts Ring spinning, self twist, weavable singles, collapsed balloon, spinning triangle, compact spinning, bicomponent yarns, winding, clearing, two-folding, twisting, non-woven, carding, cross-lapping, bonding systems, needle-punching, stitch bonding, hydroentanglement Introduction to the topic Ring spinning (which is discussed in Topics 1 and 9) remains the dominant form of spinning wool into yarn, primarily because it is regarded as producing a superior yarn to alternative spinning systems. However, a number of modifications to long staple ring spinning have been developed in recent years to provide more versatility and to reduce costs. These include methods of eliminating two-folding (or plying) in the production of weaving yarns, with the ultimate aim of producing as a yarn as possible on a spinning frame without resorting to two- plying or sizing. The manufacture of nonwoven fabrics involves converting fibres into fabric, eliminating the need for yarn to be spun as an intermediate step. The ability of wool to felt has enabled nonwoven (ie, felted) products to be made for centuries. However, more modern processes involving needle punching and stitch bonding enable a range of nonwoven products by mechanical means. Useful references for this topic are Hunter (2002) and Crawshaw and Russell (2002). -
(12) United States Patent (10) Patent No.: US 6,692,541 B2 Carlson Et Al
USOO6692,541B2 (12) United States Patent (10) Patent No.: US 6,692,541 B2 Carlson et al. (45) Date of Patent: Feb. 17, 2004 (54) METHOD OF MAKING NONWOVEN 5,142,750 A 9/1992 Dyer et al. FABRIC COMPRISING SPLTTABLE FIBERS 5,142,753 A 9/1992 Bolliand et al. 5.244,711 A 9/1993 Drelich et al. Inventors: Cheryl Carlson, Willow Springs, NC 5,290,626 A 3/1994 Nishioi et al. (75) 5,355,565 A 10/1994 Baravian (US); John Elves, Venray (NL); Kyra 5,482,772 A 1/1996 Strack et al. Dorsey, Charlotte, NC (US); Ralph A. 5,635,290 A 6/1997 Stopper et al. Moody, III, Mooresville, NC (US); 5,670.234 A 9/1997 Suehir et al. Valeria Erdos, Huntersville, NC (US) 5,827,597 A 10/1998 James et al. 5,840,633 A 11/1998 Kurihara et al. (73) Assignee: Polymer Group, Inc., North 5,888,916 A 3/1999 Tadokoro et al. Charleston, SC (US) 5,894,747 A * 4/1999 Abernathy et al. 5,899,785 A 5/1999 Grotein et al. Notice: Subject to any disclaimer, the term of this 5,965,084 A 10/1999 Nishijima patent is extended or adjusted under 35 5,970,583 A 10/1999 Grotein et al. U.S.C. 154(b) by 229 days. 6,103,061 A 8/2000 Anderson et al. 6,200,669 B1 * 3/2001 Marmon et al. 6.228,490 B1 * 5/2001 Nagano et al. (21) Appl. No.: 09/859,049 6,444,312 B1 * 9/2002 Dugan 6,461,729 B1 * 10/2002 Dugan (22) Filed: May 16, 2001 2002/0187329 A1 12/2002 Ista et al. -
Timestamp Ref. Number Company Name Country Type of Mask Mask Production Capacity Offer Material Supply Offer Testing, Certificat
Disclaimer: By submitting the form, the submitter have agreed to make publicly available the information provided. The sole responsbility on the information EURATEX - COVID-19 provided lays with the submitter, EURATEX cannot be held responsible for the contents provided nor for the use which may be made with those contents . Which volume or capacity is your company offering? (n° of mask/week, or Timestamp Ref. number Company name Country Type of mask Mask production capacity offer Material supply offer Testing, certification or other service offer Mask production needs Material supply needs Testing, certification or other service needs Any other comment tons) ISO13485;2016, Declaration of Conformity (CE), SGS Test Reports, Certified Raw 09/07/2020 273 LARISA FACE COVER S.A. Greece Medical (surgery) 1.000.000 masks / day Materials (non-woven fabrics). Production mask TYPE II (BFE>=98%) 09/07/2020 272 MODATIMKAR TRADING Turkey FFP2, Medical (surgery) Surgical mask : 1 million every 2 weeks CE, test reports, certifications for all material used in the product FFP2, FFP3, Medical (surgery), Fabric mask, Surgical masks, Gown, Apron, 09/07/2020 271 MaskServices.de Germany 6500 Cartons/ Fortnightly 100% Cotton Antibacterial Woven Fabric CE / EN / FDA Coveralls, GGloves, Visors, N95 Respirators, 3M Community mask masks 1860, 8210, FFP3 9332+ 09/07/2020 270 Velveta a.s. Czech Republic Community mask Fabrics with antibacterial finish for masks Antibacterial, Antiviral Cotton material, Antibacterial PU Test on 100% Cotton ISO 18184 Virus Test (Hohenstein), and Antibacterial Tests We provide 100% Cotton products with our own 25/06/2020 269 Evteks Ltd. Turkey Community mask 25.000 pcs a day coated fabric (SGS) available, TSE599 in Progress patented technology EOC. -
Mechanical and Comfort Properties of Hydroentangled Nonwovens from Comber Noil
This is a repository copy of Mechanical and Comfort Properties of Hydroentangled Nonwovens from Comber Noil. White Rose Research Online URL for this paper: http://eprints.whiterose.ac.uk/116898/ Version: Accepted Version Article: Ahmad, F, Tausif, M orcid.org/0000-0003-0179-9013, Hassan, MZ et al. (2 more authors) (2018) Mechanical and Comfort Properties of Hydroentangled Nonwovens from Comber Noil. Journal of Industrial Textiles, 47 (8). pp. 2014-2028. ISSN 1528-0837 https://doi.org/10.1177/1528083717716168 © The Author(s) 2017. This is an author produced version of a paper published in Journal of Industrial Textiles. Uploaded in accordance with the publisher's self-archiving policy. Reuse Items deposited in White Rose Research Online are protected by copyright, with all rights reserved unless indicated otherwise. They may be downloaded and/or printed for private study, or other acts as permitted by national copyright laws. The publisher or other rights holders may allow further reproduction and re-use of the full text version. This is indicated by the licence information on the White Rose Research Online record for the item. Takedown If you consider content in White Rose Research Online to be in breach of UK law, please notify us by emailing [email protected] including the URL of the record and the reason for the withdrawal request. [email protected] https://eprints.whiterose.ac.uk/ Mechanical and Comfort Properties of Hydroentangled Nonwovens from Comber Noil Faheem Ahmad1,2, Muhammad Tausif3,4, Muhammad Zahid Hassan5, Sheraz -
ABSTRACT SURAGANI VENU, LALITH BHARGAVA. a Study on Hydroentangling Mechanisms and Structures. (Under the Direction of Dr. Behna
ABSTRACT SURAGANI VENU, LALITH BHARGAVA. A Study on Hydroentangling Mechanisms and Structures. (Under the direction of Dr. Behnam Pourdeyhimi and Dr. Eunkyoung Shim). Hydroentangling is a nonwoven mechanical bonding technique which uses a curtain of fine, high-speed water-jets to entangle fibers in a web structure. The interactions among fibers, impinging water-jets and forming surface create a strong textile-like fabric as fibers twist, turn, intermingle and penetrate through the web as a result of water-jet(s) impact. Such integrated web structures are found in diverse applications Nevertheless, the entangling characteristics like fiber movement, fiber entangling and its possible path in the integrated structures are not well understood. Thereby, the purpose of this research is to study the effect of hydroentangling parameters like jet pressure, nozzle diameter, nozzle-to-nozzle distance and number of manifolds on fiber entangling and changes occurring within the web structure. To meet the above objectives, a comprehensive hydroentangled web structure needs to be analyzed. Hydroentangled structure is three-dimensional (3D) in nature because water jet impact cause movement of fibers in all directions as well as twisting and turning of fibers. Thus, digital volumetric imaging (DVI) technique, originally used for medical imaging has been successfully employed as a means to visualize and characterize the web structures. This technique is a block-face imaging technique (based on principle of micro-tomography) and successfully employed to acquire 3D images of the hydroentangled web structure. In the first part of the study, 3D structures of hydroentangled nonwoven were comprehensively analyzed using DVI. This study focused on developing and modifying the available characterizing techniques respectively. -
Abstract KENNERLY, PAIGE. the Application of Hydroentangling to Enhance the Mechanical Properties of Woven Jacquards
Abstract KENNERLY, PAIGE. The Application of Hydroentangling to Enhance the Mechanical Properties of Woven Jacquards. (Under the direction of Dr. Behnam Pourdeyhimi.) Hydroentangling is traditionally a nonwoven process of manufacturing fabrics through entangling loose webs of fiber using jets of water. This research proposes hydroentangling woven jacquard base fabrics using several speed and pressure combinations to mechanically enhance the structure. It also proposes to hydroentangle a loose web of fibers onto a woven jacquard fabric as a form of mechanically bonding the two structures. By bonding these fibers onto the woven fabric, the structure will be stabilized and mechanical properties will be enhanced. Control fabrics were compared to hydroentangled samples in order to select optimal hydroentangling processing parameters. The effects of these process parameters on fabric properties were studied. The mechanical properties of the woven fabrics before and after hydroentangling were also assessed. One objective of this research is to determine if hydroentangling is a feasible means to overcome certain physical and mechanical shortcomings of jacquard woven fabrics. Test data indicates that certain aspects will be improved, while others may be negatively impacted by hydroentanlging. There are also critical energy points where any further enhancement in properties is diminished. The end use application of the fabric, as well as performance criteria will play a key role in determining if hydroentangling can be used as an alternate means of finishing a jacquard woven fabric, and will be unique to the specific company and production capabilities. A second objective of this research is to determine if hydroentangling is a feasible means of bonding a single fiber carded web onto a base jacquard woven fabric. -
Development and Characterisation of Nonwoven Fabrics for Apparel Applications
The 22nd International Conference STRUTEX 2018 DEVELOPMENT AND CHARACTERISATION OF NONWOVEN FABRICS FOR APPAREL APPLICATIONS M. S. Cheema1, T. H. Shah2 and S. C. Anand1 1Institute of Materials Research and Innovation (IMRI), University of Bolton, Deane Road, Bolton BL3 5AB, UK 2 National Textile University, Pakistan [email protected] Abstract: The cost of making apparel fabrics for garment manufacturing is very high because of their conventional manufacturing processes and new methods/processes are being constantly developed for making fabrics by unconventional methods. With the advancements in technology and the availability of the innovative fibres, durable nonwoven fabrics by using the hydroentanglement process that can compete with the woven fabrics in terms of their aesthetic and tensile properties are being developed. In the work reported here, the hydroentangled nonwoven fabrics were developed through a hybrid nonwoven manufacturing processes by using fibrillated Tencel® and bi-component (sheath/core) polyethylene/polyester (PE/PET) fibres, in which the initial nonwoven fabrics were prepared by the needle- punching method followed by hydroentanglement process carried out at optimal pressures of 50 to 250 bars. The prepared fabrics were characterised according to the British Standards (BS 3356:1990, BS 9237:1995, BS 13934-1:1999) and the attained results were compared with those for a standard plain- weave cotton, polyester woven fabric and commercially available nonwoven fabric (Evolon®). The developed hydroentangled fabrics showed better drape properties owing to their flexural rigidity of 252 mg.cm in the MD, while the corresponding commercial hydroentangled fabric displayed a value of 1340 mg.cm in the MD. Tensile strength of the developed hydroentangled fabrics showed an approximately 200% increase than the commercial hydroentangled fabrics.