Mechanical and Comfort Properties of Hydroentangled Nonwovens from Comber Noil
Total Page:16
File Type:pdf, Size:1020Kb
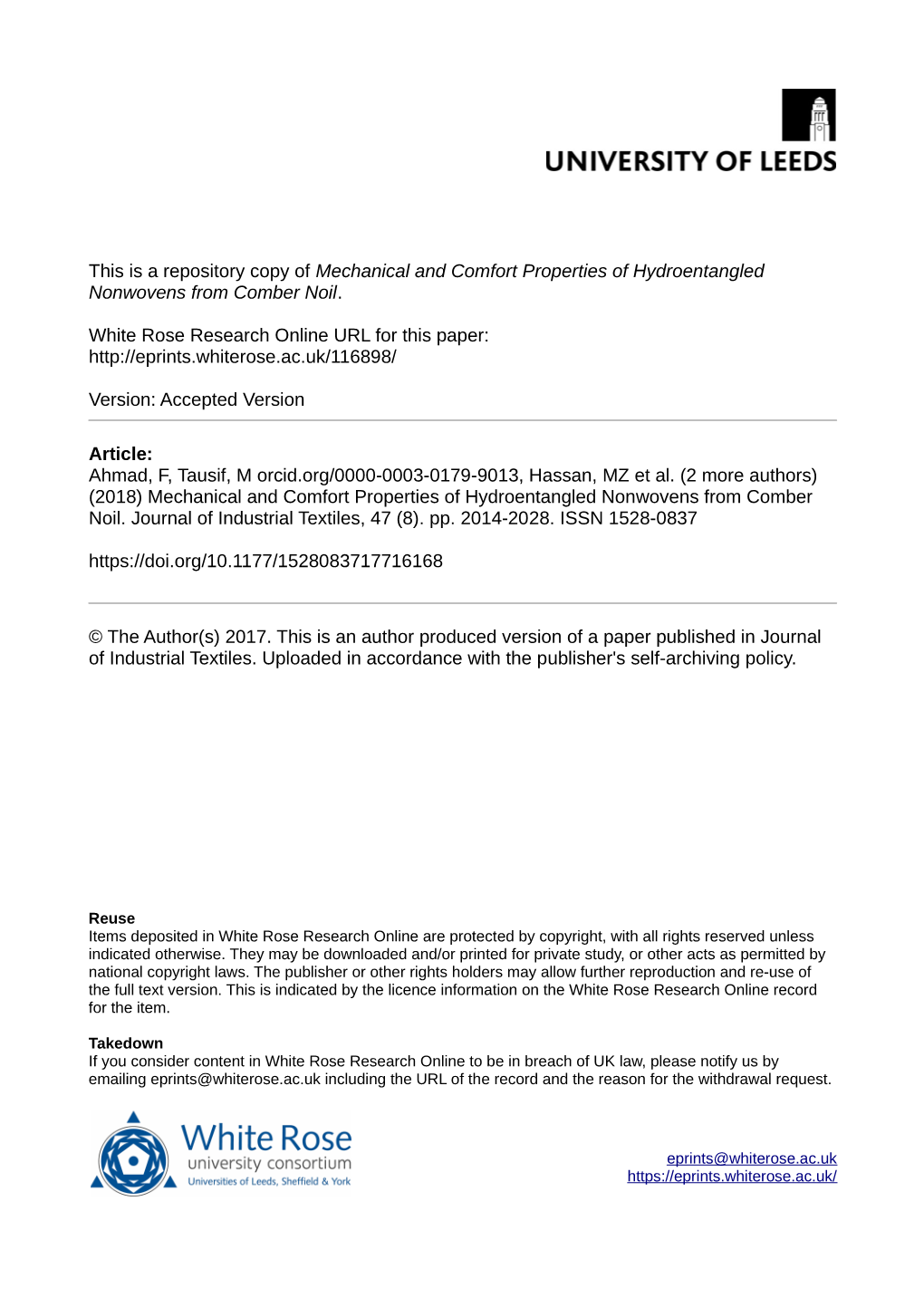
Load more
Recommended publications
-
United States Patent (19) 11 Patent Number: 5,620,785 Watt Et Al
US00562O785A United States Patent (19) 11 Patent Number: 5,620,785 Watt et al. (45) Date of Patent: Apr. 15, 1997 54 MELTBLOWN BARRIER WEBS AND 4,662,005 5/1987 Grier-Idris. PROCESSES OF MAKING SAME 4,807,619 2/1989 Dyrud et al.. 4,813,948 3/1989 Insley . 75) Inventors: James M. Watt, Piedmont; Deborah 4,863,785 9/1989 Berman et al.. K. Lickfield, Easley, both of S.C. 4,874,399 10/1989 Reed et al.. 4,874,659 10/1989 Ando et al. 4,920,960 5/1990 Hubbard et al. 73) Assignee: Fiberweb North America, Inc., 4,921,645 5/1990 Insley. Simpsonville, S.C. 4,969,457 11/1990 Hubbard et al.. 5,122,048 6/1992 Deeds. 21) Appl. No.: 475,949 5,149,468 9/1992 Hershelman. 5,150,703 9/1992 Hubbard et al.. (22 Filed: Jun. 7, 1995 5,254.297 10/1993 Deeds. 5,306,534 4/1994 Bosses. (51 Int. Cl." ........................... A62B 23/00; A62B 23/06; 5,307.796 5/1994 Kronzer et al.. ED04H 1/72 5,322,061 6/1994 Brunson. 52 U.S. Cl. ...................... 428/219; 55/528; 55/DIG. 39; 5,409,766 4/1995 Yuasa et al. ............................ 428/903 128/206. 12; 156/624; 264/DIG. 48; 428/311.11; 5,436,066 7/1995 Chen ....................................... 428/903 428/311.51; 428/315.5; 428/338; 428/903; 5,482,765 1/1996 Bradley et al. ....... ... 428/286 442/400 5,486,411 1/1996 Hassenboehler, Jr. .... ... 428/286 58) Field of Search .................................... -
Glossary Nonwovens Terms
GLOSSARY of GLOSSARY NONWOVENS TERMS For further information please contact EDANA Tel: +32 (0) 2 734 93 10 Fax : +32 (0) 2 733 35 18 Email: [email protected] www.edana.org www.edana.org A ABRASION RESISTANCE The ability of a fibre or fabric to withstand surface wear and rubbing ABSORPTION The process by which a gas or liquid is taken up within a material. ACTINIC DEGRADATION Strength loss or weakening of fibres and fabrics due to exposure to sunlight. ADDITIVES Chemicals added or incorporated in materials to give them different functional or aesthetic properties, such as flame retardancy and/or softness. ADHESION The force that holds different materials together at their interface. ADHESIVE A material, flowable in solution or when heated, that is used to bond materials together. ADHESIVE MIGRATION The movement of adhesive together with its carrier solvent, in a fabric during drying, giving it a non- uniform distribution within the web; usually increasing towards the outer layers. ADSORPTION The process by which a gas or liquid is taken up by the surface of a material. AESTHETICS Properties perceived by touch and sight, such as the hand, colour, lustre, drape, and texture of fabrics. AFTERGLOW The flameless, ember-like burning of a fabric. EDANA 2 AFTER TREATMENT (FINISHING) Process usually carried out after a web has been formed and bonded. Examples are embossing, creping, softening, printing and dyeing. AGGLOMERATION A cluster of particles or fibres. AGEING Processing in which products are exposed to environmental conditions that simulate real use or accelerated use, for the purpose of determining their effect on the functional and aesthetic properties of the products. -
7. Wool Combing
7. Wool Combing Errol Wood Learning objectives On completion of this topic you should be able to: • Outline the objectives of wool combing • Describe the design of a typical rectilinear comb • Explain the steps in rectilinear combing – feeding, initial combing, final combing and drawing off, and sliver formation • Discuss the means by which noils are removed, and the balance required in setting the amount to be removed • Explain the purpose of re-combing • Calculate: tear ratio, noil(%), romaine, regain and combing production • Discuss the factors that affect the combing quality of fine wools Key terms and concepts Combing (Nobel and rectilinear), nips per minute, doublings, noils, finisher gilling, packaging, re- combing, tear, noil(%), romaine, percent fibres less than 30 mm, combing production. Introduction to the topic Wool combing is a comprehensive term when used in its widest sense, and it embraces all the operations carried out in a topmaking plant. It includes the processes of raw wool scouring, drying, carding, backwashing and preparer gilling. Then follows the actual combing operation and the sequence of topmaking processes concludes with two gilling steps called top finishing (or finisher gilling). Combing is not included in the semiworsted or woollen processing routes. Wool combing, the single process, is indispensable in the manufacture of a worsted yarn. The card has disentangled the fibres in the mass of scoured wool and has mixed them in a roughly parallel formation. However, during the carding process many fibres will have been broken, and the card sliver will consist of a variety of fibre lengths. Some vegetable matter will have been removed but fragments remain. -
TRI-1016-Random-Slub-Rotor-Yarn
TECHNICAL BULLETIN 6399 Weston Parkway, Cary, North Carolina, 27513 • Telephone (919) 678-2220 ________________________________________________________________________________ TRI 1016 RANDOM SLUB ROTOR YARN PRODUCTION ON CONVENTIONAL EQUIPMENT © 2004 Cotton Incorporated. All rights reserved; America’s Cotton Producers and Importers. Concept Spinning mills have long desired a way to produce a 100% cotton novelty rotor yarn with slubs of random size and length using conventional mill machinery without any special attachments. New technology provides a method to create very short and small size slubs, which are not attainable with most electro-mechanical designs due to their inherent limitations and the rotor diameter that controls the minimum slub length. This random slub process can be a cost- effective alternative for producing novelty slub yarns on rotor-spinning machines. Introduction Cotton Incorporated developed a process for producing a random slub rotor yarn by using small amounts (10%-25%) of comber noils (0.5 in/12.5mm or less) in the final drawing process (usually two “short cotton” slivers in the creel). The practical count range of yarn from this process is projected to be Ne 20/1 and coarser. The main targets for this yarn include denim, shirting, fashion fabrics for women’s wear, and home products. Fiber Processing Specifications for Producing Random Slub Rotor Yarn General Procedure One or two slivers made from comber noil/short staple virgin cotton are introduced into the drawing creel at the finisher drawing step with six to seven ends of “base” cotton or virgin lint (base cotton slivers can be produced in the normal manner). These short fiber slivers produce drafting waves, which later become random thick places (slubs) in the yarn. -
Recommendations for Producing Linen-Look Yarn on Conventional Equipment
TECHNICAL BULLETIN 6399 Weston Parkway, Cary, North Carolina, 27513 • Telephone (919) 678-2220 TRI 1010 RECOMMENDATIONS FOR PRODUCING LINEN-LOOK YARN ON CONVENTIONAL EQUIPMENT © 1992 Cotton Incorporated. All rights reserved; America’s Cotton Producers and Importers. TABLE OF CONTENTS Page CONCEPT 2 INTRODUCTION 2 FIBER ANALYSIS 3 LINEN-LOOK YARN--PREPARATORY PROCEDURE 3 SPINNING PROCEDURE 4 PROCESSING SEQUENCE AND EQUIPMENT SETTINGS 4 OPENING AND CLEANING 4 CARDING 4 DRAWING--FIRST PROCESS 4 DRAWING--SECOND PROCESS 5 ROVING 5 SPINNING 5 TEST RESULTS--18/1 Ne 6 CONCEPT To produce a 100% cotton novelty yarn with long linen-like slubs using standard mill machinery without special attachments. INTRODUCTION Cotton Incorporated developed a totally new novelty yarn with a linen look which can be produced on conventional mill machinery without special attachments. It is called "linen look" because it simulates long slubs common to linen yarn but is made using 100% cotton. The slubs are formed by using small amounts of comber noils (short fibers) in the final drawing operation. One of the main targets for this yarn is women's wear fabrics for blouses and skirts. In the current work, counts of 18/1 Ne were spun. The effective count range of this type yarn is projected to be from 8/1 Ne to 28/1 Ne. Example: Linen-Look vs. Regular Yarn (Ne 18/1 Ring TM 3.8) 2 FIBER ANALYSES 1. Characteristics of fiber used in this project Type - U.S. upland cotton Grade - SLM Length (inches) - 1.12 Mic - 3.8 - 4.6 Strength (grams/tex) - 24 and up 2. -
Short Fiber Wood Pulp --- Long Fiber Synthetics U.S
USOO6110848A United States Patent (19) 11 Patent Number: 6,110,848 Bouchette (45) Date of Patent: Aug. 29, 2000 54 HYDROENTANGLED THREE PLY WEBS 5,026,587 6/1991 Austin et al.. AND PRODUCTS MADE THEREFROM 5,151,320 9/1992 Homonoff. 5,246,772 9/1993 Manning. 75 Inventor: Michael Paul Bouchette, Sherwood, 5,393,599 2/1995 Quantrille et al.. Wis 5,413,849 5/1995 Austin et al.. 5,587.225 12/1996 Griesbach et al.. 73 Assignee: Fort James Corporation, Deerfield, Ill. Primary Examiner Terrel Morris ASSistant Examiner-Norca L. Torres 21 Appl. No.: 09/169,067 57 ABSTRACT 22 Filed: Oct. 9, 1998 A three ply Sandwich Structured hydroentangled web is 51) Int. Cl." ................................. B32B5/26: B32B 7/08 disclosed. The top and bottom plies of this web comprise 52 U.S. Cl. .......................... 442/384; 442/381; 442/387; long synthetic fibers having a fiber length of about 30 to 100 442/389; 442/408; 442/412 mm and the middle ply comprises cellulosic fibers having a 58 Field of Search ..................................... 442/387, 384, fiber length of about 1 to 8 mm. The middle layer cellulosic 442/389, 408, 412 fiber can optimally be wholly or partially replaced with short Synthetic or other natural fibers having a fiber length of 56) References Cited about 6 to 27 mm. U.S. PATENT DOCUMENTS These hydroentangled WebS are useful in the manufacture of 4,775,579 10/1988 Hagy et al.. towels, wet wipes, industrial wipes and medical gowns. 4,808,467 2/1989 Suskind et al. -
Development of Nonwoven Fabrics for Clothing Applications
e e Sci nce Cheema et al., J Textile Sci Eng 2018, 8:6 til & x e E T n : g DOI 10.4172/2165-8064.1000382 f o i n l e a e n r r i n u g o Journal of Textile Science & Engineering J ISSN: 2165-8064 Research Article Article OpenOpen Access Access Development of Nonwoven Fabrics for Clothing Applications Cheema MS1*, Anand SC1 and Shah TH2 1Institute of Materials Research and Innovation, University of Bolton, Deane Road, Bolton BL3 5AB, United Kingdom 2National Textile University, Pakistan Abstract The apparel fabric manufacturing is a growing sector of the global textile industry and the fabrics used in this market are mainly produced by the conventional methods such as weaving and knitting processes. These methods of making apparel fabrics are length and costly. However, because of the advancements in nonwoven technology, nonwoven fabrics are finding a niche market in the clothing industry because of its cost effectiveness and high speeds of nonwoven production processes. We have carried out an extensive study on the development of apparel- like nonwoven fabrics. The resultant fabric showed improved drape, hand, durability and thermophysiological comfort characteristics than the reference samples for apparel applications. Results of the study also showed that the developed nonwoven fabrics showed nearly 200% higher tensile strength than the reference nonwoven fabrics. Furthermore, it also showed improved air permeability, for example, the resultant nonwoven fabric exhibited 500% higher air permeability value as compared with the Evolon fabric at 100 Pa pressure. Thus the results of the study indicate that the resultant nonwoven fabrics may be used in a wide range of apparel applications, which can lead to additional benefits in terms of cost and time. -
The Ideal Rotor Spinning Process for a High Short-Fiber Content Rieter
John Spatafora Harald Schwippl Technology & Process Analytics Head Technology & Process Analytics Rieter Machines & Systems Rieter Machines & Systems July 2020 The Ideal Rotor Spinning Process for a High Short-Fiber Content Rieter . The Ideal Rotor Spinning Process for a High Short-Fiber Content 2 Rieter . The Ideal Rotor Spinning Process for a High Short-Fiber Content Contents 1. Introduction 4 2. Process Shortening for a High Short-Fiber Content 5 3. Trial Setup 6 4. Optimal Process Sequence 8 4.1. Sliver Evenness and Adhesive Strength on the Intermediate Product 8 4.2. Evenness of the Rotor Yarn 10 4.3. Tenacity and Elongation of the Rotor Yarn 11 4.4. Hairiness and Abrasion of the Rotor Yarn 13 4.5. Running Behavior of the Rotor Spinning Machine 14 5. Advantages of the RSB Module with Two Draft Zones 15 6. Effects on the End Product 17 7. Process Recommendation 20 8. Economic Viability 21 9. Summary 22 3 Rieter . The Ideal Rotor Spinning Process for a High Short-Fiber Content 1. Introduction Unevenness in staple fiber yarns has Improvements of Yarn Unevenness Since 1957 TM been improving constantly in recent de- 100% Cotton, USP 50% (Uster Statistics Percentile) cades despite high production speeds at the individual process steps – from fiber 22 preparation through the end-spinning machine (see Fig. 1). 20 On the one hand, the improvement in 18 unevenness is due to innovations in me- chanical engineering, such as optimiza- 16 tions in drafting system design or newly developed technology components. On 14 Mass variation[%] CVm the other hand, the increasingly precise definition and coordination of raw ma- 12 terial, process sequence and yarn count 10 plays an important role. -
Combing Process
COMBING PROCESS The combing process is normally used to produce smoother, finer, stronger and more uniform yarns. Therefore, combing is commonly confined to high grade, long staple natural fibers. In recent years, combing has been utilized for upgrading the quality of medium staple fibers. In addition, a yarn made of combed cotton needs less twist than a carded yarn. However, these quality improvements are obtained at the cost of additional expenditure on machines, floor-space and personnel, together with a loss of raw material. Yarn production coast is increased by something under 1 US$/Kg of yarn (depending on the intensity of combing). To improve the yarn quality, the comber must perform the following operations: ➢ Elimination of precisely pre-determined quantity of short fibers; ➢ Elimination of the remaining impurities; ➢ Elimination of a large proportion (not all) of the neps in the fiber material; ➢ Formation of a sliver having maximum possible evenness; ➢ .Producing of more straight and parallel fibers. Elimination of short fibers produces an improvement mainly in staple length, but also affects the fineness of the raw material. The micronaire value of combed sliver is slightly higher than that of feedstock (elimination of dead fibers). Also the degree of parallelization might reduce the inter-fiber adhesion in the sliver to such an extent that fibers slide apart while being pulled out of the can – i.e. sliver breaks or false drafts might be caused. Types of applications: The amount of material combed out varies within the range 5 – 25% of the in feed stock. Three major groups of spinning mills using combing are as follows: ➢ Long staple combing mills; Processing first-class, expensive cotton of high strength, containing a low proportion of short fibers and little dirt. -
Influence of Material Variables in Thermal Bonding of Nonwovens
University of Tennessee, Knoxville TRACE: Tennessee Research and Creative Exchange Masters Theses Graduate School 5-2006 Influence of Material ariablesV in Thermal Bonding of Nonwovens Raghavendra Ratnakar Hegde University of Tennessee - Knoxville Follow this and additional works at: https://trace.tennessee.edu/utk_gradthes Part of the Materials Science and Engineering Commons Recommended Citation Hegde, Raghavendra Ratnakar, "Influence of Material ariablesV in Thermal Bonding of Nonwovens. " Master's Thesis, University of Tennessee, 2006. https://trace.tennessee.edu/utk_gradthes/1576 This Thesis is brought to you for free and open access by the Graduate School at TRACE: Tennessee Research and Creative Exchange. It has been accepted for inclusion in Masters Theses by an authorized administrator of TRACE: Tennessee Research and Creative Exchange. For more information, please contact [email protected]. To the Graduate Council: I am submitting herewith a thesis written by Raghavendra Ratnakar Hegde entitled "Influence of Material Variables in Thermal Bonding of Nonwovens." I have examined the final electronic copy of this thesis for form and content and recommend that it be accepted in partial fulfillment of the requirements for the degree of Master of Science, with a major in Materials Science and Engineering. Gajanan Bhat, Major Professor We have read this thesis and recommend its acceptance: Larry C. Wadsworth, Roberto S. Benson Accepted for the Council: Carolyn R. Hodges Vice Provost and Dean of the Graduate School (Original signatures are on file with official studentecor r ds.) To the Graduate Council: I am submitting herewith a thesis written by Raghavendra Ratnakar Hegde entitled "Influence of Material Variables in Thermal Bonding of Nonwovens." I have exam- ined the final electronic copy of this thesis for form and content and recommended that it be accepted in partial fulfillment of the requirements for the degree of Masters of Science, with a major in Material Science and Engineering. -
Spinning Daily Presents Alternative Fibers: the Spinner's Guide To
presents Alternative Fibers: The Spinner’s Guide to Vegan, Natural, and Wool-Free Yarns ©F+W Media, Inc. ■ All rights reserved ■ F+W Media grants permission for any or all pages in this issue to be copied for personal use Spin.Off ■ spinningdaily.com ■ 1 pinners have worked with wool for thousands of years, and with good reason: it dyes easily, wears well, and Scomes from cute sheep. But it’s not the only option available nowadays. We can spin fiber produced from other animals, from plants, or from manufacturing processes. Bam- boo, soy, and corn can all be made into yarn. So can wood pulp and seaweed: if you’ve never heard of Seacell, Modal, or Lyocell, read on. Do all of these spinnable fibers qualify as natural? Are they vegan (i.e., animal-friendly) or at least animal- neutral? How sustainable are the different production methods? It depends on your personal definitions and choices. Some people might see rayon, extruded from wood pulp, as too far removed from Nature, while others might prefer rayon to water-intensive hemp retting. You’ll read about protein and cellulose fibers in the first article, then find others on plant-based fibers, either directly from the plant or processed in some way. If you want to spin something other than wool, you can find the perfect substitute here. Happy spinning, Anne Merrow [email protected] ©F+W Media, Inc. ■ All rights reserved ■ F+W Media grants permission for any or all pages in this issue to be copied for personal use Spin.Off ■ spinningdaily.com ■ 2 What are natural fi bers? BY A MY C LARKE M OORE atural fi bers occur naturally in na- not usually included in the natural fi ber catego- a Nture, naturally. -
US5504975.Pdf
|||||||||I|| US005504975A United States Patent (19) 11 Patent Number: 5,504,975 Bar et al. 45) Date of Patent: Apr. 9, 1996 54 METHOD AND APPARATUS FOR NOIL 5,003,670 4/1991 Waeber et al. ....................... 19/66 CC REDUCTION IN WOOL COMBING 75 Inventors: Herzel Bar, Bat-Yam; Amotz Primary Examiner-John J. Calvert Weinberg, Tel-Aviv, both of Israel Attorney, Agent, or Firm-Edwin D. Schindler (73) Assignee: Shenkar College of Textile Technology & Fashion, Ramat Gan, Israel (57) ABSTRACT A method and apparatus for combing wool in which the (21) Appl. No.: 417,806 wool is heated prior to being fed to the combing process. The 22 Filled: 6, 1 wool is heated by heat rollers or other means to a tempera (22 File Apr. 6, 1996 ture such that it becomes more plasticized and better lubri (51) Int. Cl. ................. D01G 19/30 cated due to the liquification of the natural fat of wool which 52 U.S. Cl. ................. 19166 R; 19/66 CC then acts better as a lubricant. As a result of this process, 58 Field of Search ............................... 19166R, 66 CC, there is a reduction in the amount of noil produced. The 19/115 R, 115 B, 2 invention is also applicable to various other animal-based natural fibers. (56) References Cited U.S. PATENT DOCUMENTS 4,989,297 2/1991 Yicheskel et al. ............... 19/66 CCX 8 Claims, 1 Drawing Sheet U.S. Patent Apr. 9, 1996 5,504,975 5,504,975 1 2 METHOD AND APPARATUS FOR NOIL wool on the fibre surface acts at such temperature as a REDUCTION IN WOOL COMBING lubricant to reduce the friction between the wool and the comb.