Preparation and Characterization of Polymeric Dispersants Based on Vegetable Oils for Printing Ink Application Nadia A.Yossif 1, Nadia G
Total Page:16
File Type:pdf, Size:1020Kb
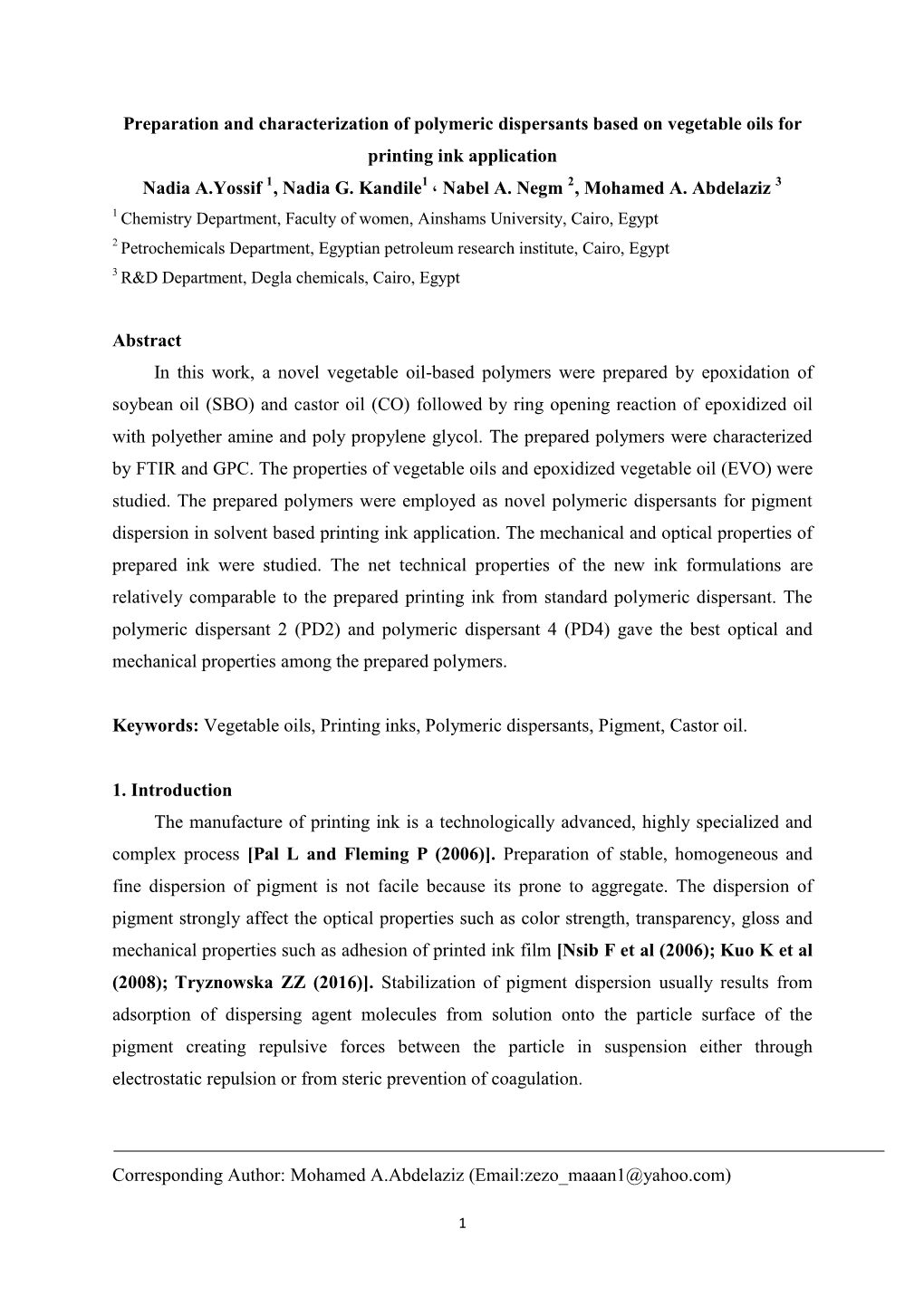
Load more
Recommended publications
-
Phthalocyanine Green Aluminum Pigment Prepared by Inorganic Acid Radical/Radical Polymerization for Waterborne Textile Applications
Int J Ind Chem DOI 10.1007/s40090-016-0084-x RESEARCH Phthalocyanine green aluminum pigment prepared by inorganic acid radical/radical polymerization for waterborne textile applications 1,2 2 2 1 Benjamin Tawiah • Benjamin K. Asinyo • William Badoe • Liping Zhang • Shaohai Fu1 Received: 16 January 2016 / Accepted: 17 May 2016 Ó The Author(s) 2016. This article is published with open access at Springerlink.com Abstract Polymer-encapsulated phthalocyanine green preparation of polymer-encapsulated aluminum pigments aluminum pigment was prepared via inorganic acid radical/ for waterborne textile applications. radical polymerization route, and its properties were investigated by FT-IR, TGA, XPS, SEM, and TEM. SEM Keywords Aluminum pigment Á Phthalocyanine green Á and TEM images showed that the aluminum pigment was Polymer encapsulation Á Radical polymerization Á encapsulated by a thin film of polymer which ensured good Inorganic acid radical anti-corrosive performance in alkaline (pH 12) and acidic (pH 1) mediums. XPS results showed significant chemical shifts, and increase in binding energies to higher levels Introduction after raw aluminum pigment was phosphate coated and colored by phthalocyanine green pigment. TGA results Colored aluminum pigments having colorful pigment suggest a marginal reduction in its thermal stability. Major adhered closely, uniformly and firmly on its surface are absorbance peaks, such as aluminum phosphate (AlPO4), suitably used in paints, automotive metallic finish, printing different monomer units and CH2 stretching vibration of inks, molded resins and in decoration finish of plastics phthalocyanine green G were highlighted in the FTIR [1–3]. The application of aluminum pigment has expanded spectra of the colored aluminum matrix. -
FIG. 2 00 © O O W O 2013/038278 A2 1II III II II III I I11 III I Llll M III I III I Ll
(12) INTERNATIONAL APPLICATION PUBLISHED UNDER THE PATENT COOPERATION TREATY (PCT) (19) World Intellectual Property Organization I International Bureau (10) International Publication Number (43) International Publication Date WO 2013/038278 A2 21 March 2013 (21.03.2013) P O P C T (51) International Patent Classification: (US). WEI, Ning [US/US]; 1010 Wilde Run Court, G01N 31/22 (2006.01) G01N 21/81 (2006.01) Roswell, Georgia 30075 (US). (21) International Application Number: (74) Agents: STOKER, Denise, L. et al; 2300 Winchester PCT/IB2012/053943 Road, Neenah, Wisconsin 54956 (US). (22) International Filing Date: (81) Designated States (unless otherwise indicated, for every 1 August 2012 (01 .08.2012) kind of national protection available): AE, AG, AL, AM, AO, AT, AU, AZ, BA, BB, BG, BH, BN, BR, BW, BY, English (25) Filing Language: BZ, CA, CH, CL, CN, CO, CR, CU, CZ, DE, DK, DM, (26) Publication Language: English DO, DZ, EC, EE, EG, ES, FI, GB, GD, GE, GH, GM, GT, HN, HR, HU, ID, IL, IN, IS, JP, KE, KG, KM, KN, KP, (30) Priority Data: KR, KZ, LA, LC, LK, LR, LS, LT, LU, LY, MA, MD, 13/230,102 12 September 201 1 (12.09.201 1) US ME, MG, MK, MN, MW, MX, MY, MZ, NA, NG, NI, (71) Applicant (for all designated States except US): KIM¬ NO, NZ, OM, PE, PG, PH, PL, PT, QA, RO, RS, RU, RW, BERLY-CLARK WORLDWIDE, INC. [US/US]; Nee- SC, SD, SE, SG, SK, SL, SM, ST, SV, SY, TH, TJ, TM, nah, Wisconsin 54956 (US). TN, TR, TT, TZ, UA, UG, US, UZ, VC, VN, ZA, ZM, ZW. -
Pigment Green 7 Is with Highly Transparent Mid Shade, High Heat Resistance and Overall Properties
Dongguan Baoxu Chemical Technology.,ltd. P:+86-0769-22821082 Fax:0769-22821083 Email:[email protected] Web:www.additivesforpolymer.com Room1118 Caijin Business Building Nancheng Distinct Guangdong China Pigment Green 7 is with highly transparent mid shade, high heat resistance and overall properties. P.G.7 tinting strength is much lower than phthalocyanine blue C.I.Pigment Green 7 fastness properties is much better than phthalocyanine blue. PG 7 is the standard green color for plastics, used in polyolefins,engineerrings,PP,terylene,acrylic fibers,nylons Chemistry Synonym name:C.I.Pigment Green 7,P.G.7, PG 7, C.I.74260,Phthalocyanine green G, phthalo green, viridian hue, pigment green 7, copper phthalocyanine green, non- flocculating green G, polychloro copper phthalocyanine, CAS Number:1328-53-6 EU Number: 215-524-7 Chemical Family: Cu-Phthalogreen Chemical Structure Application Data Heat Resistance In HDPE The information and statement herein are believed to be reliable but are not to be construed as a warranty or representation for which we assume legal responsibility, Users should undertake sufficient verification and testing to determine the suitable for their own particular purpose of any information or products referred to herein. No warranty of fitness for a particular purpose is made. Dongguan Baoxu Chemical Technology.,ltd. P:+86-0769-22821082 Fax:0769-22821083 Email:[email protected] Web:www.additivesforpolymer.com Room1118 Caijin Business Building Nancheng Distinct Guangdong China Heat resistance 250 Fastness -
Pigment Dispersion and Inkjet Ink Composition Using the Pigment Dispersion
Europäisches Patentamt *EP001116757A2* (19) European Patent Office Office européen des brevets (11) EP 1 116 757 A2 (12) EUROPEAN PATENT APPLICATION (43) Date of publication: (51) Int Cl.7: C09D 17/00, C09D 11/00 18.07.2001 Bulletin 2001/29 (21) Application number: 01100577.4 (22) Date of filing: 10.01.2001 (84) Designated Contracting States: (72) Inventors: AT BE CH CY DE DK ES FI FR GB GR IE IT LI LU • Taniguchi, Keishi, c/o Ricoh Company Ltd. MC NL PT SE TR Tokyo 143-8555 (JP) Designated Extension States: • Hatada, Shigeo, c/o Ricoh Company Ltd. AL LT LV MK RO SI Tokyo 143-8555 (JP) (30) Priority: 11.01.2000 JP 2000002068 (74) Representative: Barz, Peter, Dr. Patentanwalt (71) Applicant: Ricoh Company, Ltd. Kaiserplatz 2 Tokyo 143-8555 (JP) 80803 München (DE) (54) Pigment dispersion and inkjet ink composition using the pigment dispersion (57) A pigment dispersion comprising one or more pigments, a dispersant, and a dispersion medium comprising water, wherein the dispersant comprises a compound having the following formula (I): wherein R1 represents an alkyl group having from 1 to 20 carbon atoms, an aryl group, or an aralkyl group; and k is 0 or an integer of from 1 to 7 and m is an integer of from 30 to 60. EP 1 116 757 A2 Printed by Jouve, 75001 PARIS (FR) EP 1 116 757 A2 Description [0001] The present invention relates to a pigment dispersion, and an ink composition useful for ink jet printing using the pigment dispersion. 5 [0002] As having been disclosed in Japanese Laid-Open Patent Publications Nos. -
Book XIV Art and Psychology
8 88 88 88ycology 8888on.com 8888 Basic Photography in 180 Days Book XIV - Art and Psychology Editor: Ramon F. aeroramon.com Contents 1 Day 1 1 1.1 Visual perception ........................................... 1 1.1.1 Visual system ......................................... 1 1.1.2 Study ............................................. 1 1.1.3 The cognitive and computational approaches ......................... 3 1.1.4 Transduction ......................................... 4 1.1.5 Opponent process ....................................... 4 1.1.6 Artificial visual perception .................................. 4 1.1.7 See also ............................................ 4 1.1.8 Further reading ........................................ 4 1.1.9 References .......................................... 4 1.1.10 External links ......................................... 5 1.2 Depth perception ........................................... 6 1.2.1 Monocular cues ........................................ 6 1.2.2 Binocular cues ........................................ 7 1.2.3 Theories of evolution ..................................... 8 1.2.4 In art ............................................. 8 1.2.5 Disorders affecting depth perception ............................. 9 1.2.6 See also ............................................ 9 1.2.7 References .......................................... 9 1.2.8 Bibliography ......................................... 10 1.2.9 External links ......................................... 10 2 Day 2 11 2.1 Human eye ............................................. -
Kupferphthalocyanin, Chloriert Nr
Die BG RCI ist seit 2010 Rechtsnachfolger der BG Chemie TOXIKOLOGISCHE BEWERTUNGEN ISBN 0937-4248 Kurfürsten-Anlage 62⋅69115 Heidelberg Telefon: 06221 5108-28451 1 E-Mail: [email protected] 1 Internet: www.bgrci.de/toxikologischebewertungen KURZFASSUNG TOXIKOLOGISCHE BEWERTUNGEN Kupferphthalocyanin, chloriert Nr. 229 Ausgabe 06/95 1 Stoffname 1.1 Gebrauchsname Kupferphthalocyanin, chloriert 1.2 IUPAC-Name Kupferphthalocyanin, chloriert 1.3 CAS-Nr. 1328-53-6 1.4 EINECS-Nr. 215-524-7 2 Synonyme, Trivial- und Handelsnamen Accosperse Cyan Green G C-Ext. Grün 5 C.I. Pigment Green 42 C.I. Pigment Grün 7 CI 74260 Calcotone Green G Ceres Green 3B Chromatex Green G Colanyl Green GG Copper Phthalocyanine Green Cromophthal Green GF Cyan Green 15-3100 Cyanine Green (GP; NB; T; Toner) Dainichi Cyanine Green (FG; FGH) Daltolite Fast Green GN Duratint Green 1001 Fastogen Green (B; 5005) Fastolux Green KURZFASSUNG TOXIKOLOGISCHE BEWERTUNG 1 Nr. 229 Kupferphthalocyanin, chloriert 06/95, BG Chemie Fenalac Green (G; G Disp) Granada Green Lake GL Graphtol Green 2GLS Green 7 Heliogen Green (A; G; GA; GN; GNA; GTA; GV; GWS; 8681K; 8682T; 8730) Heliogen Grün 8730 Hostaperm Green GG Irgalite Fast Brilliant Green (GL; 3GL) Irgalite Green GLN Klondike Yellow X-2261 Lutetia Fast Emerald J Monarch Green WD Monastral Fast Green (BGNA; G; GD; GF; GFNP; GN; GNA; GTP; GV; GWD; GX; GXB; GYH; LGNA; 2GWD) Monastral Green (B; B Pigment; G; GFN; GH; GN) Monolite Fast Green GVSA Non-Flocculating Green G-25 Opaline Green G-1 Perchlorkupferphthalocyanin Permanent Green Toner GT-376 Phthalocyanine green Phthalocyanine Green (LX; V; VFT-1080) Pigment Fast Green (G; GN) Pigment Green Phthalocyanine Pigment Green Phthalocyanine V Pigment Green 7 Pigment Green GK Polychloro-Kupferphthalocyanin Polymo Green (FBH; FGH) Polymon Green (G; GN; 6G) PV-Fast Green G Resinated Phthalocyanine Green G-5025 Sanyo Cyanine Green Sanyo Phthalocyanine (Green FB Pure; F6G) 2 KURZFASSUNG TOXIKOLOGISCHE BEWERTUNG Nr. -
Colour, Pigments and Dyes Science, Art & Nature
COLOUR, PIGMENTS AND DYES SCIENCE, ART & NATURE Ken Derham Halesworth U3A Science Group, April 2019 WHAT IS COLOUR? • Colour is a characteristic of human visual perception. • This perception of colour derives from the stimulation of cone cells in the human eye by electromagnetic radiation in the visible spectrum. Wikipedia VISIBLE LIGHT A triangular prism dispersing a beam of white light. The longer wavelengths (red) and the shorter wavelengths (blue) are separated. Wikipedia Violet light - Shorter wavelength, higher frequency has higher energy E = h v (Planck’s equation) WHY DO OBJECTS APPEAR COLOURED? Objects appear different colours because they absorb some colours (wavelengths) and reflected or transmit other colours. The colours we see are the wavelengths that are reflected or transmitted. White objects appear white because they reflect all colours. Black objects absorb all colours so no light is reflected. TRANSMITTED LIGHT PRIMARY COLOURS: ADDITIVE MIXING OF LIGHT • Mix Red, Green, and Blue light, you get white light. • Red, green, and blue (RGB) are referred to as the primary colours of light. • Mixing the colours generates new colours, as shown on the colour wheel. This is additive colour. • As more colours are added, the result becomes lighter, heading towards white. • RGB is used to generate colour on a computer screen, a TV, and other electronic displays. PRIMARY COLOURS: SUBTRACTIVE MIXING OF PIGMENTS • Mixing colours using paint, or ink, uses subtractive colour mixing. • The primary colours of light are red, green, and blue. • If you subtract these from white you get cyan, magenta, and yellow. • Mixing the colours generates new colours as shown on the colour wheel. -
(Lca) of Artificial Vs Natural Christmas Tree
COMPARATIVE LIFE CYCLE ASSESSMENT (LCA) OF ARTIFICIAL VS NATURAL CHRISTMAS TREE Sylvain Couillard, ing. M.Sc. Gontran Bage, ing. Ph.D. Jean-Sébastien Trudel, B.Com B.Sc.Soc. M.Env. February 2009 1043-RF3-09 Strategists in Sustainable Development ellipsos is a consulting firm based in Montreal. We offer solid professional expertise in sustainable development. We help business leaders build a competitive advantage using Life Cycle Management. This approach is used by the most qualified teams of executives in large corporations worldwide, 1030 Beaubien E. Suite 305 recognized by the United Nations and supported by the International Montreal Quebec H2S 1T4 standardization Organization (ISO 14040). 514.463.9336 We are different. We exist to help businesses evolve into sustainable organizations. We believe solutions are available. We believe that businesses, [email protected] governments and people are part of the solution. We believe in human www.ellipsos.ca creativity, innovation and action. For leaders to make better decisions, they need credible indicators that take into account all stages of a product or service life cycle. Life Cycle Management tools provide such indicators, and we assist organizations to make the most out of it. About the Authors Sylvain Couillard ing. M.Sc. Jean-Sébastien Trudel B.Com B.Sc.Soc. M.Env. Sylvain Couillard graduated as a Mechanical Engineer from École Polytechnique Founder of ellipsos, Jean-Sébastien Trudel helps executives and management de Montréal (1998). He obtained his Master’s Degree in Biomedical Engineering deal with and benefit from the ever changing conditions of emerging markets, a from the University of Calgary (2002). -
And Fe(III)-Phthalocyanine Molecular Films
UPTEC F 10021 Examensarbete 30 hp Juni 2015 X-Ray Photoemission Spectroscopy Characterization of Fe(II)- and Fe(III)-Phthalocyanine Molecular Films Sonja Droschke Abstract X-Ray Photoemission Spectroscopy Characterization of Fe(II)- and Fe(III)-Phthalocyanine Molecular Films Sonja Droschke Teknisk- naturvetenskaplig fakultet UTH-enheten This thesis investigates the electronic structure of iron phthalocyanine (Fe(II)Pc) and iron phthalocyanine chloride (Fe(III)PcCl) immobilized on surfaces. For this purpose Besöksadress: two different deposition methods are used and compared: smearing the molecular Ångströmlaboratoriet Lägerhyddsvägen 1 powder under atmosphere condition and evaporation of a molecular layer in Hus 4, Plan 0 ultra-high vacuum. The electronic states of FePc and FePcCl are probed with photoelectron spectroscopy (PES) and compared in relation to the ionic state of the Postadress: central metal (Fe). The PE spectra show that evaporation of FePcCl at around 350°C Box 536 751 21 Uppsala results in dissociation of the chlorine from the FePc molecule, which is stable at this temperature. Mass spectroscopic measurements during heating of FePcCl in ultra-high Telefon: vacuum (UHV) show a clear Cl signal for temperature still below 250°C. Theoretical 018 – 471 30 03 calculations of the binding energy for Cl in FePcCl seem to indicate dissociation of the Telefax: Cl from the molecules. 018 – 471 30 00 Hemsida: http://www.teknat.uu.se/student Handledare: Joachim Schiessling Ämnesgranskare: Carla Puglia Examinator: Tomas Nyberg ISSN: 1401-5757, UPTEC F 10021 1 Introduction ................................................................................. 4 2 Phthalocyanines .......................................................................... 5 3 Experimental set-up and technique ............................................. 6 3.1 Principles of photoelectron spectroscopy ................................................. 6 3.2 Chemical shift ............................................................................................ -
Micador Metallic Pencils
MATERIAL SAFETY DATA SHEET Micador Metallic Pencils 1. Product Identifier & Identity for the Chemical Product name Micador Metallic Pencils Other name Product code FMMP12 Recommended use Art and Craft Restrictions on use None kown Modern Teaching Aids Pty Ltd Office: Level 1, 122-126 Old Pittwater Road, Brookvale NSW 2100 Australia Post: PO BOX 6367 Frenchs Forest NSW 2086 Australia Freephone: 1800 251 497 (AU) 0800 808 044 (NZ) FreeFax: 1800 151 492 (AU) 0800 682 329 (NZ) Email: [email protected] [email protected] Website: www.teaching.com.au www.teaching.co.nz 2. Hazard Identification Classification of the hazardous chemical Classified as non-hazardous and non-dangerous goods according to the criteria of NOHSC Label Elements, including precautionary statements None allocated as non-hazardous Other Hazards which do not result in classification None allocated as non-hazardous 3. Composition/Information on Ingredients Material Name CAS NO. Kaolin Clay 1332-58-7 Beeswax 8006-40-4 Stearic Acid 57-11-4 Carnauba Wax 8015-86-9 Paraffin 8002-74-2 CMC 9004-32-4 Phthalocyanine Green G 1328-53-6 Yellow GR 5102-83-0 Carmine 6B 1234986 Permanent Orange G 3520-72-7 Black Carbon 1333-86-4 64742-82-1 40 Gold-Silver Pigment 7429-90-5 60 Pigment Yellow 184 14059-33-7 Aluminiurn 7429-90-5 Solvent Blue 38 1328-51-4 Solvent Violet 31 70956-27-3 Solvent Yellow 21 5601-29-6 Solvent Violet 56 61116-28-7 5601-29-6 Transparent green 12237-24-0 Phthalocyanine blue 147-14-8 Safety Data Sheet | Page 1 of 5 © 2013 Micador Group 4. -
WO 2015/081441 Al 11 June 2015 (11.06.2015) P O P C T
(12) INTERNATIONAL APPLICATION PUBLISHED UNDER THE PATENT COOPERATION TREATY (PCT) (19) World Intellectual Property Organization International Bureau (10) International Publication Number (43) International Publication Date WO 2015/081441 Al 11 June 2015 (11.06.2015) P O P C T (51) International Patent Classification: AO, AT, AU, AZ, BA, BB, BG, BH, BN, BR, BW, BY, A01N3/00 (2006.01) BZ, CA, CH, CL, CN, CO, CR, CU, CZ, DE, DK, DM, DO, DZ, EC, EE, EG, ES, FI, GB, GD, GE, GH, GM, GT, (21) International Application Number: HN, HR, HU, ID, IL, IN, IR, IS, JP, KE, KG, KN, KP, KR, PCT/CA20 14/05 1169 KZ, LA, LC, LK, LR, LS, LU, LY, MA, MD, ME, MG, (22) International Filing Date: MK, MN, MW, MX, MY, MZ, NA, NG, NI, NO, NZ, OM, 5 December 2014 (05.12.2014) PA, PE, PG, PH, PL, PT, QA, RO, RS, RU, RW, SA, SC, SD, SE, SG, SK, SL, SM, ST, SV, SY, TH, TJ, TM, TN, (25) Filing Language: English TR, TT, TZ, UA, UG, US, UZ, VC, VN, ZA, ZM, ZW. (26) Publication Language: English (84) Designated States (unless otherwise indicated, for every (30) Priority Data: kind of regional protection available): ARIPO (BW, GH, 61/913,102 6 December 2013 (06. 12.2013) US GM, KE, LR, LS, MW, MZ, NA, RW, SD, SL, ST, SZ, 2836757 6 December 2013 (06. 12.2013) CA TZ, UG, ZM, ZW), Eurasian (AM, AZ, BY, KG, KZ, RU, TJ, TM), European (AL, AT, BE, BG, CH, CY, CZ, DE, (71) Applicant: SUNCOR ENERGY INC. -
Synthesis and Characterization of 7-Hydroxycoumarin Containing New Type of Phthalocyanine Compounds and Investigation of Thermal and Electrochemical Properties
REPUBLIC OF TURKEY FIRAT UNIVERSITY INSTITUTE OF NATURAL AND APPLIED SCIENCES SYNTHESIS AND CHARACTERIZATION OF 7-HYDROXYCOUMARIN CONTAINING NEW TYPE OF PHTHALOCYANINE COMPOUNDS AND INVESTIGATION OF THERMAL AND ELECTROCHEMICAL PROPERTIES Master Thesis Aminu Dauda (152117103) Department: Chemistry Supervisor: Prof. Dr. Sinan SAYDAM June-2017 REPUBLIC OF TURKEY FIRAT UNIVERSITY INSTITUTE OF NATURAL AND APPLIED SCIENCES SYNTHESIS AND CHARACTERIZATION OF 7-HYDROXYCOUMARIN CONTAINING NEW TYPE OF PHTHLOCYANINE COMPOUNDS AND INVESTIGATION OF THERMAL AND ELECTROCHEMICAL PROPERTIES Master Thesis Aminu Dauda (152117103) Department of Chemistry Date Submitted to the Institute: 05.06.2017 Thesis Defense Date: 21.06.2017 Supervisor: Prof. Dr. Sinan SAYDAM (F.U) Jury member: Prof. Dr. Ayşegül YAZICI (F.U) Jury member: Prof. Dr. Mustafa SÜLÜ (I.U) June-2017 ii DEDICATION This work is dedicated to my dear parents, son and wife. This is a sign of my gratitude because, i can never thank you as much as necessary for your guidance, love, patient, encouragement, and prayers. ACKNOWLEDGEMENT All praises and thanks are due to almighty Allah by whose grace all good deeds are accomplished. Peace and blessing be upon our noble Prophet Muhammad (Sallallahu alaihi wasallam) his household and companions. I wish to express my extreme gratitude to my supervisor Prof. Dr. Sinan SAYDAM for his advice, patience, motivational guidance, courage, commitment, considerate, optimistic approach that gave me an opportunity to get the best concepts from you. Our discussions which are very countless helped me understand the direction and the importance of the research work. Sir! Once again may Almighty Allah in his infinite mercy continue to uplift you and reward you in abundant.