Characterization of Boron Nitride Nanosheets Synthesized by Boron-Ammonia Reaction
Total Page:16
File Type:pdf, Size:1020Kb
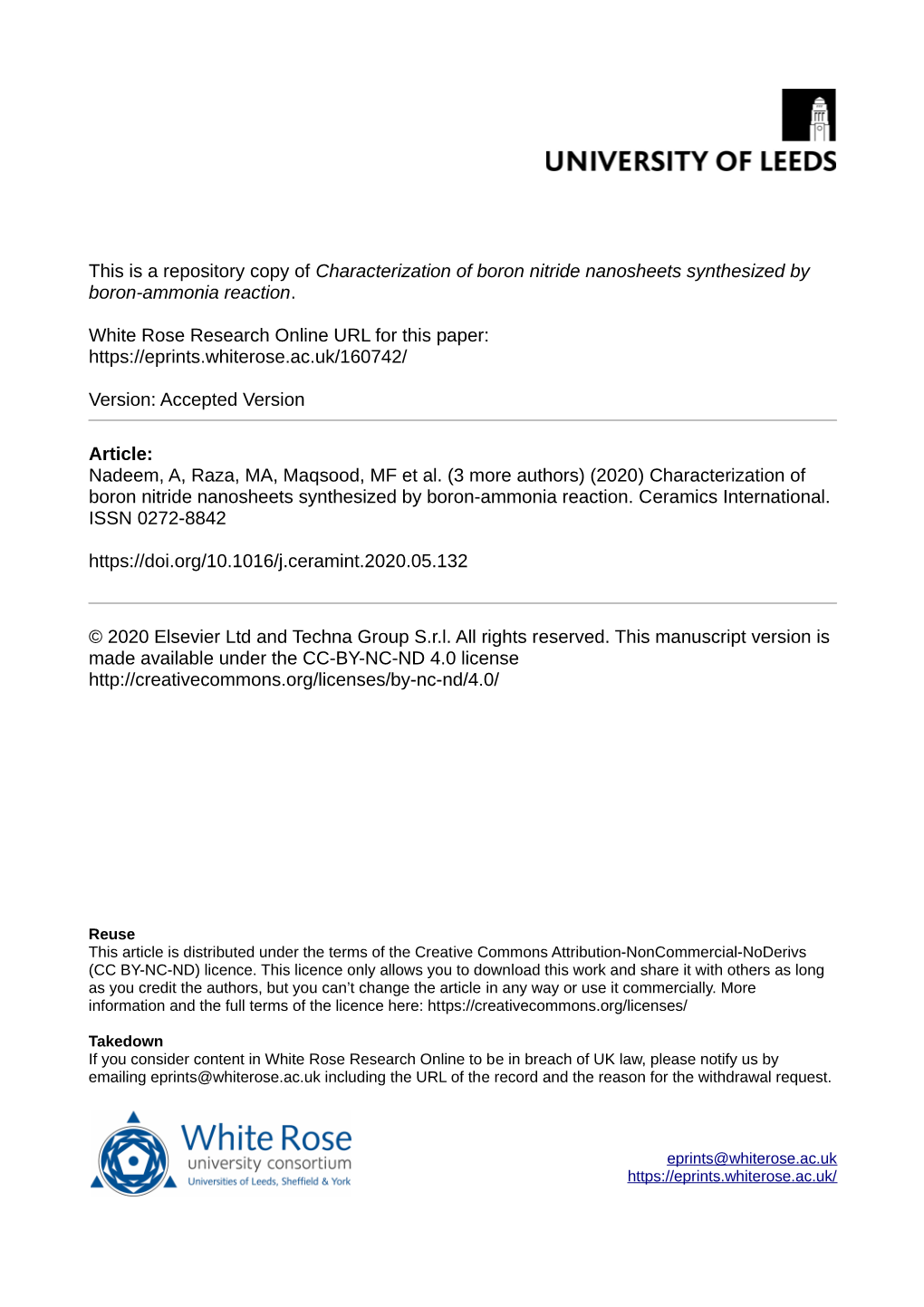
Load more
Recommended publications
-
Boron Nitride Substrates for High-Quality Graphene Electronics C
LETTERS PUBLISHED ONLINE: 22 AUGUST 2010 | DOI: 10.1038/NNANO.2010.172 Boron nitride substrates for high-quality graphene electronics C. R. Dean1,2*,A.F.Young3,I.Meric1,C.Lee4,5,L.Wang2,S.Sorgenfrei1,K.Watanabe6,T.Taniguchi6, P. Kim 3,K.L.Shepard1 and J. Hone2* Graphene devices on standard SiO2 substrates are highly disor- atomically planar surface should suppress rippling in graphene, dered, exhibiting characteristics that are far inferior to the which has been shown to mechanically conform to both corrugated expected intrinsic properties of graphene1–12. Although suspend- and flat substrates9,21. The dielectric properties of h-BN (e ≈ 3–4 ≈ 21 ing the graphene above the substrate leads to a substantial and Vbreakdown 0.7 V nm ) compare favourably with those of 13,14 improvement in device quality ,thisgeometryimposes SiO2, allowing the use of h-BN as an alternative gate dielectric with severe limitations on device architecture and functionality. no loss of functionality22. Moreover, the surface optical phonon There is a growing need, therefore, to identify dielectrics that modes of h-BN have energies two times larger than similar modes allow a substrate-supported geometry while retaining the in SiO2, suggesting the possibility of an improved high-temperature quality achieved with a suspended sample. Hexagonal boron and high-electric-field performance of h-BN based graphene devices nitride (h-BN) is an appealing substrate, because it has an atom- over those using typical oxide/ graphene stacks23,24. ically smooth surface that is relatively free of dangling bonds and To fabricate graphene-on-BN, we used a mechanical transfer charge traps. -
BN Nanosheet/Polymer Films with Highly Anisotropic Thermal Conductivity for Thermal Management Applications Yuanpeng Wu Deakin University
University of Wollongong Research Online Australian Institute for Innovative Materials - Papers Australian Institute for Innovative Materials 2017 BN Nanosheet/Polymer Films with Highly Anisotropic Thermal Conductivity for Thermal Management Applications Yuanpeng Wu Deakin University Ye Xue Rowan University Si Qin Deakin University Dan Liu Deakin University Xuebin Wang Nanjing University See next page for additional authors Publication Details Wu, Y., Xue, Y., Qin, S., Liu, D., Wang, X., Hu, X., Li, J., Wang, X., Bando, Y., Golberg, D., Chen, Y., Gogotsi, Y. & Lei, W. (2017). BN Nanosheet/Polymer Films with Highly Anisotropic Thermal Conductivity for Thermal Management Applications. ACS Applied Materials and Interfaces, 9 (49), 43163-43170. Research Online is the open access institutional repository for the University of Wollongong. For further information contact the UOW Library: [email protected] BN Nanosheet/Polymer Films with Highly Anisotropic Thermal Conductivity for Thermal Management Applications Abstract The development of advanced thermal transport materials is a global challenge. Two-dimensional nanomaterials have been demonstrated as promising candidates for thermal management applications. Here, we report a boron nitride (BN) nanosheet/polymer composite film with excellent flexibility and toughness prepared by vacuum-assisted filtration. The mechanical performance of the composite film is highly flexible and robust. It is noteworthy that the film exhibits highly anisotropic properties, with superior in-plane thermal conductivity of around 200 W m -1 K -1 and extremely low through-plane thermal conductivity of 1.0 W m -1 K -1 , making this material an excellent candidate for thermal management in electronics. Importantly, the composite film shows fire-resistant properties. -
Optimization of Wear Loss in Silicon Nitride (Si3n4)–Hexagonal Boron Nitride (Hbn) Composite Using Doe–Taguchi Method
Ghalme et al. SpringerPlus (2016) 5:1671 DOI 10.1186/s40064-016-3379-7 CASE STUDY Open Access Optimization of wear loss in silicon nitride (Si3N4)–hexagonal boron nitride (hBN) composite using DoE–Taguchi method Sachin Ghalme1,2*, Ankush Mankar3 and Y. J. Bhalerao4 *Correspondence: [email protected] Abstract 2 Mechanical Engineering Introduction: The contacting surfaces subjected to progressive loss of material Department, Manoharbhai Patel Institute of Engineering known as ‘wear,’ which is unavoidable between contacting surfaces. Similar kind of and Technology, Gondia, phenomenon observed in the human body in various joints where sliding/rolling Maharashtra, India contact takes place in contacting parts, leading to loss of material. This is a serious issue Full list of author information is available at the end of the related to replaced joint or artificial joint. article Case description: Out of the various material combinations proposed for artificial joint or joint replacement Si3N4 against Al2O3 is one of in ceramic on ceramic category. Minimizing the wear loss of Si3N4 is a prime requirement to avoid aseptic loosening of artificial joint and extending life of joint. Discussion and evaluation: In this paper, an attempt has been made to investigate the wear loss behavior of Si3N4–hBN composite and evaluate the effect of hBN addition in Si3N4 to minimize the wear loss. DoE–Taguchi technique is used to plan and analyze experiments. Conclusion: Analysis of experimental results proposes 15 N load and 8 % of hBN addi- tion in Si3N4 is optimum to minimize wear loss against alumina. Keywords: Silicon nitride (Si3N4), Hexagonal boron nitride (hBN), Alumina (Al2O3), Design of experiment (DoE), Taguchi technique Background Mechanical behavior of various machine elements, such as gears, cams, wheels, rails and sealing parts are influenced by the interaction between contact elements and surfaces. -
Ceramic Carbides: the Tough Guys of the Materials World
Ceramic Carbides: The Tough Guys of the Materials World by Paul Everitt and Ian Doggett, Technical Specialists, Goodfellow Ceramic and Glass Division c/o Goodfellow Corporation, Coraopolis, Pa. Silicon carbide (SiC) and boron carbide (B4C) are among the world’s hardest known materials and are used in a variety of demanding industrial applications, from blasting-equipment nozzles to space-based mirrors. But there is more to these “tough guys” of the materials world than hardness alone—these two ceramic carbides have a profile of properties that are valued in a wide range of applications and are worthy of consideration for new research and product design projects. Silicon Carbide Use of this high-density, high-strength material has evolved from mainly high-temperature applications to a host of engineering applications. Silicon carbide is characterized by: • High thermal conductivity • Low thermal expansion coefficient • Outstanding thermal shock resistance • Extreme hardness FIGURE 1: • Semiconductor properties Typical properties of silicon carbide • A refractive index greater than diamond (hot-pressed sheet) Chemical Resistance Although many people are familiar with the Acids, concentrated Good Acids, dilute Good general attributes of this advanced ceramic Alkalis Good-Poor (see Figure 1), an important and frequently Halogens Good-Poor overlooked consideration is that the properties Metals Fair of silicon carbide can be altered by varying the Electrical Properties final compaction method. These alterations can Dielectric constant 40 provide knowledgeable engineers with small Volume resistivity at 25°C (Ohm-cm) 103-105 adjustments in performance that can potentially make a significant difference in the functionality Mechanical Properties of a finished component. -
Carbon and Boron Nitride Nanostructures for Hydrogen Storage Applications Through a Theoretical Perspective
CARBON AND BORON NITRIDE NANOSTRUCTURES FOR HYDROGEN STORAGE APPLICATIONS THROUGH A THEORETICAL PERSPECTIVE Y. T. Singha,b, B. Chettria,b, A. Banikc , K. O. Obodod and D. P. Raia,* aPhysical Science Research Center (PSRC), Department of Physics, Pachhunga University College, Mizoram University, Aizawl 796001, India bDepartment of Physics, North-Eastern Hill University, Shillong 793022, India cDepartment of Electrical Engineering, National Institute of Technical Teachers' Training & Research (NITTTR), Kolkata, India dHySA Infrastructure Centre of Competence, Faculty of Engineering, North-WestUniversity (NWU), P. Bag X6001, Potchefstroom, 2520, South Africa Abstract: The recent progress in the field of hydrogen storage in carbon and boron nitride nanostructures has been summarized. Carbon and boron nitride nanostructures are considered advantageous in this prospect due to their lightweight and high surface area. Demerits of pristine structures to hold hydrogen molecules for mobile applications have been highlighted by many researchers. In such cases, weak van der Waals interaction comes into account, hence, the hydrogen molecules are weakly bonded with the host materials and hence weak adsorption energy and low hydrogen molecules uptake. So, to tune the adsorption energy as well as overall kinetics, methods such as doping, light alkali-alkaline earth metals decoration, vacancy, functionalization, pressure variation, application of external electric field, and biaxial strain has been adopted by many researchers. Physisorption with atoms decoration is promising for hydrogen storage application. Under this condition, the host materials have high storage capacity with considerable average adsorption energy, feasible adsorption/desorption kinetics. Keywords: Density Functional Theory; hydrogen storage; boron nitride; graphene; carbon nanotube; adsorption energy; desorption temperature; physisorption; chemisorption; temperature; pressure. -
Effective Mechanical Properties and Thickness Determination of Boron Nitride Nanosheets Using Molecular Dynamics Simulation
nanomaterials Article Effective Mechanical Properties and Thickness Determination of Boron Nitride Nanosheets Using Molecular Dynamics Simulation Venkatesh Vijayaraghavan and Liangchi Zhang * Laboratory for Precision and Nano Processing Technologies, School of Mechanical and Manufacturing Engineering, The University of New South Wales, Sydney, NSW 2052, Australia; [email protected] * Correspondence: [email protected]; Tel.: +61-2-9385-6078 Received: 3 July 2018; Accepted: 17 July 2018; Published: 19 July 2018 Abstract: Research in boron nitride nanosheets (BNNS) has evoked significant interest in the field of nano-electronics, nanoelectromechanical (NEMS) devices, and nanocomposites due to its excellent physical and chemical properties. Despite this, there has been no reliable data on the effective mechanical properties of BNNS, with the literature reporting a wide scatter of strength data for the same material. To address this challenge, this article presents a comprehensive analysis on the effect of vital factors which can result in variations of the effective mechanical properties of BNNS. Additionally, the article also presents the computation of the correct wall thickness of BNNS from elastic theory equations, which is an important descriptor for any research to determine the mechanical properties of BNNS. It was predicted that the correct thickness of BNNS should be 0.106 nm and the effective Young’s modulus to be 2.75 TPa. It is anticipated that the findings from this study could provide valuable insights on the true mechanical properties of BNNS that could assist in the design and development of efficient BN-based NEMS devices, nanosensors, and nanocomposites. Keywords: boron nitride nanosheet; molecular dynamics; thickness; mechanical strength; vacancy defects 1. -
High-Quality Graphene and Hexagonal- Boron Nitride Transfers on Sio2
High-Quality Graphene and Hexagonal- Boron Nitride Transfers on SiO2 1 MELISSA HUYNH CHEMICAL ENGINEERING DEPARTMENT OF OREGON STATE UNIVERSITY DR. JUN JIAO, LESTER LAMPERT REU - PORTLAND STATE UNIVERSITY Overview 2 Importance High- Results and Quality Methodology Interpretation Graphene & HBN Raman Analysis Overview 3 Importance High- Results and Quality Methodology Interpretation Graphene & HBN Raman Analysis 2D Materials 4 Graphene Zero overlap semimetal Durable Heat and electricity conductivity Hexagonal-Boron Nitride Similar properties to graphene Future Application 5 Biological engineering Optical Electronics Composite materials Super Capacitors/ Energy Storage Overview 6 Importance High- Results and Quality Methodology Interpretation Graphene & HBN Raman Analysis Growth 7 Chemical Vapor Deposition (CVD) Copper catalyst Vertical growth with furnace Methane, hydrogen, argon gases Transfer of Graphene 8 PMMA spin coat Ammonium Persulfate (APS) Rinse Heat Acetone bath Transfer of HBN 9 Copper foil APS Corral Pumps Polymer-Free Approach 10 Similar to H-BN Outflow: APS Inflow: DI H2O and Isopropyl Alcohol Overview 11 Importance High- Results and Quality Methodology Interpretation Graphene & HBN Raman Analysis Graphene Spectrum 12 D band G band D/g 2D Band 2D/G Ideal Spectrum HBN spectrum 13 1300-1400 range Weak readings Carbon contamination Ideal Spectrum Overview 14 Importance High- Results and Quality Methodology Interpretation Graphene & HBN Raman Analysis Graphene Analysis Grown at 830 ̊ C [edge] -
Production of Boron Nitride Using Chemical Vapor Deposition Method a Thesis Submitted to the Graduate School of Nature
PRODUCTION OF BORON NITRIDE USING CHEMICAL VAPOR DEPOSITION METHOD A THESIS SUBMITTED TO THE GRADUATE SCHOOL OF NATURE AND APPLIED SCIENCES OF MIDDLE EAST TECHNICAL UNIVERSITY BY ÖZGE MERCAN IN PARTIAL FULFILLMENT OF THE REQUIREMENTS FOR THE DEGREE OF MASTER OF SCIENCE IN CHEMICAL ENGINEERING FEBRUARY 2014 Approval of the thesis: PRODUCTION OF BORON NITRIDE USING CHEMICAL VAPOR DEPOSITION METHOD submitted by ÖZGE MERCAN in partial fulfillment of the requirements for the degree of Master of Science in Chemical Engineering Department, Middle East Technical University by, Prof. Dr. Canan Özgen Dean, Graduate School of Natural and Applied Sciences Prof. Dr. Halil Kalıpçılar Head of Department, Chemical Engineering, Prof. Dr. H. Önder Özbelge Supervisor, Chemical Engineering Dept, Assoc. Prof. Dr. Naime Aslı Sezgi Co-supervisor, Chemical Engineering Dept, Examining Committee Members Prof. Dr. Hayrettin Yücel Chemical Engineering Department, METU Prof. Dr. H. Önder Özbelge Chemical Engineering Department, METU Prof. Dr. Nail Yaşyerli Chemical Engineering Department, Gazi Unv. Prof. Dr. Halil Kalıpçılar Chemical Engineering Department, METU Yard. Doç. Dr. Zeynep Çulfaz Emecen Chemical Engineering Department, METU Date : I hereby declare that all information in this document has been obtained and presented in accordance with academic rules, and ethical conduct. I also declare that, as required by these rules and conduct, I have fully cited and referenced all material and results that are not original to this work. Name, Last Name : ÖZGE MERCAN Signature : iv ABSTRACT PRODUCTION OF BORON NITRIDE USING CHEMICAL VAPOR DEPOSITION METHOD Mercan, Özge Master of Science, Department of Chemical Engineering Supervisor : Prof. Dr. H. Önder Özbelge Co-Supervisor: Assoc. -
Synthesis and Characterization of Borazine-Doped Polyphenylenes: Towards the Construction of Boron-Nitrogen- Carbon Hybrid Polyc
Cardiff University Cardiff School of Chemistry Synthesis and characterization of borazine -doped polyphenylenes: towards the construction of boron -nitrogen - carbon hybr id polycyclic aromatic hydrocarb ons Davide MARINELLI PhD Thesis December 2017 Supervisor: Prof. Dr. Davide BONIFAZI Doctoral commission: Prof. Emilio M. Pérez Dr. Louis Morrill Acknowledgements First of all, I would like to thank Professor Bonifazi , my supervisor. I am very grateful to him for his constant support and help. Nonetheless, thanks to him I had the possibility to travel and work in different countries , gathering all the best from the fantastic people I’ve met around Europe . I’d like to say a big thank you to Tanja , for the help she gave me during these years and for the revision of this manuscript. I am extremely grateful to the members of the borazine team: María , Jacopo, Francesco, Jack, Jonathan, and Hamid . Many thanks also to the rest of the group members at Cardiff University: Andrea, Alexandre, Antoine , Nicolas, Andrea, Rodolfo, Lou, Cataldo, Dmytro, Olesia, Elisa, Andrey, and Matte o, Tommas o, and Oliwia . I am also thankful to all the other lab mates and friends I’ve met at the Université de Namur (Belgium) and Università di T rieste (Italy). II Table of contents Table of Contents ABSTRACT ................................ ................................ ................................ ................................ V LIST OF ABBREVIATIONS ................................ ................................ ............................... -
Enhanced Thermal Conductivity of Polyimide Composites with Boron
www.nature.com/scientificreports OPEN Enhanced Thermal Conductivity of Polyimide Composites with Boron Nitride Nanosheets Received: 2 November 2017 Ting Wang1, Mengjie Wang1, Li Fu2, Zehui Duan3, Yapeng Chen1, Xiao Hou1, Yuming Wu1, Accepted: 10 January 2018 Shuangyi Li1, Liangchao Guo1, Ruiyang Kang1, Nan Jiang1 & Jinhong Yu1 Published: xx xx xxxx A strategy was reported to prepare boron nitride nanosheets (BNNSs) by a molten hydroxide assisted liquid exfoliation from hexagonal boron nitride (h-BN) powder. BNNSs with an average thickness of 3 nm were obtained by a facile, low-cost, and scalable exfoliation method. Highly thermally conductive polyimide (PI) composite flms with BNNSs fller were prepared by solution-casting process. The in-plane thermal conductivity of PI composite flms with 7 wt% BNNSs is up to 2.95 W/mK, which increased by 1,080% compared to the neat PI. In contrast, the out-of plane thermal conductivity of the composites is 0.44 W/mK, with an increase by only 76%. The high anisotropy of thermal conductivity was verifed to be due to the high alignment of the BNNSs. The PI/BNNSs composite flms are attractive for the thermal management applications in the feld of next-generation electronic devices. With the rapid development of electronics industry, there is an increasing demand for electrically insulating polymer-based materials with enhanced capability of heat dissipation1–5. Furthermore, low cost and light weight polymer-based materials for next-generation electronic device, power systems, and communication equipment are needed. Polymers such as polyimide (PI) has been widely used as an electronic packaging material due to good thermal and mechanical properties6,7. -
Syntheses and Characterization of BH₂ NH₂ Species
This dissertation has been 65—5644 microfilmed exactly as received X HICKAM, Jr., Cecil William, 1939- SYNTHESES AND CHARACTERIZATION OF BHgNHg SPECIES. The Ohio State University, Ph.D., 1964 Chemistry, inorganic I University Microfilms, Inc., Ann Arbor, Michigan SYNTHESES AND CHARACTERIZATION OF BHgNHg SPECIES DISSERTATION Presented in Partial Fulfillment of the Requirements for the Degree Doctor of Philosophy in the Graduate School of The Ohio State University by Cecil William Hickam, Jr., B.S. The Ohio State University 1964 Approved hy idviser Department of Chemistry ACKNOWLEDGMENTS A grant from the National Science Foundation helped to provide equipment and chemicals for this work. Financial support for myself was given hy E, I. DuPont De Nemours and Company for the summers of 1963 and 1964, and by General Electric for the school year of 1963-64. I would like to thank Dr. Sheldon G, Shore for his continued encouragement throughout my graduate studies, and to gratefully acknowledge his help and guidance in this investigation. I am indebted to my student colleagues, Mr. G. E. McAchran, and Dr. B. Z. Egan, and especially Mr. K. W. Boddeker, who performed some of the molecular weight de terminations and analyses reported here; and my uncle and aunt, Mr. and Mrs. W. D. Hedges, and my wife, Lydia, for their financial and moral support. 11 CONTENTS Acknowledgments............................ ii Tables...................... v Illustrations....................................... vil I. INTRODUCTION........................ 1 A, General Background........................ 1 B, Statement of Problem...................... 16 II. EXPERIMENTAL............ 18 A. Apparatus................................ 18 B. Chemicals................................ $6 C. Analytical Procedures.................... 39 D. Determination of the Cryoscopic Constant of Dimethyl Sulfoxide..... -
On the Electronic Structure of Benzene and Borazine: an Algebraic Description
On the electronic structure of benzene and borazine: An algebraic description Y. Hern´andez-Espinosa1, R. A. M´endez-S´anchez2 and E. Sadurn´ı3 1 Universidad Nacional Aut´onoma de M´exico, Instituto de F´ısica, A.P. 20-364, CDMX 01000, M´exico 2 Universidad Nacional Aut´onoma de M´exico, Instituto de Ciencias Fisicas, Apartado Postal 48-3, 62210 Cuernavaca Mor., M´exico 3 Benem´erita Universidad Aut´onoma de Puebla, Instituto de F´ısica, Apartado Postal J-48, 72570 Puebla, M´exico E-mail: [email protected] Abstract. The spectrum of a hexagonal ring is analysed using concepts of group theory and a tight-binding model with first, second and third neighbours. The two doublets in the spectrum are explained with the C3 symmetry group together with time-reversal symmetry. Degeneracy lifts are induced by means of various mechanisms. Conjugation symmetry breaking is introduced via magnetic fields, while C3 breaking is studied with the introduction of defects, similar to the inclusion of fluorine atoms. Concrete applications to benzene and borazine are shown to illustrate the generality of our description. Wave functions are described in connection with partial or full aromaticity. Electronic density currents are found for all cases. A detailed study of a supersymmetry in a 6-ring is presented and its consequences on electronic spectra are discussed. PACS numbers: 02.20.Rt, 03.65.Aa, 03.65.Vf, 31.15.-p, 31.15.xh, 31.10.+z arXiv:1912.05059v1 [physics.chem-ph] 2 Dec 2019 On the electronic structure of benzene and borazine 2 1.