Characteristic Properties and Performance Of
Total Page:16
File Type:pdf, Size:1020Kb
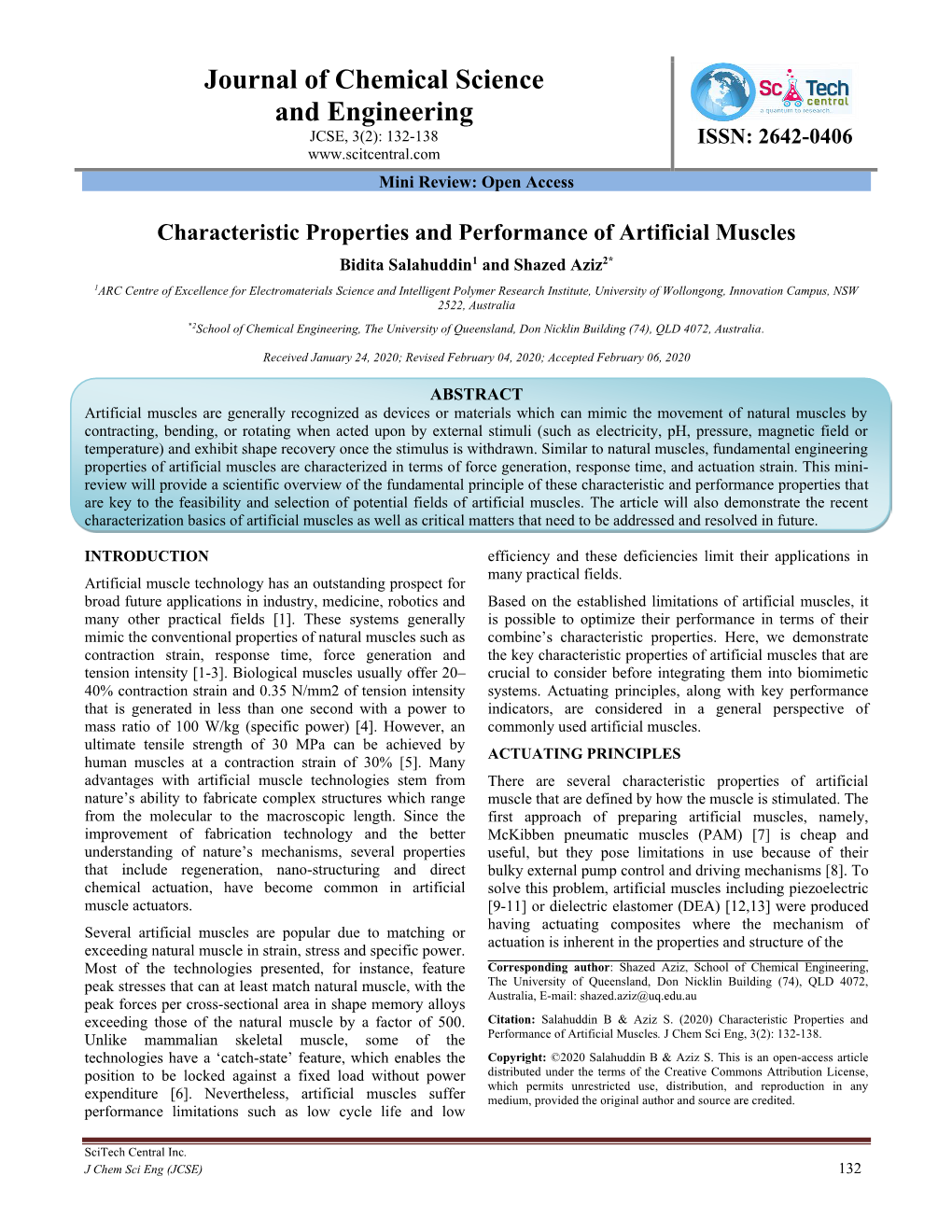
Load more
Recommended publications
-
Shape-Memory Polymeric Artificial Muscles Stress That Is Applied to the Polymer [8,70]
molecules Review Shape-Memory Polymeric Artificial Muscles: Mechanisms, Applications and Challenges 1, 1, 1, , 1 2 2 Yujie Chen y , Chi Chen y, Hafeez Ur Rehman * y, Xu Zheng , Hua Li , Hezhou Liu and Mikael S. Hedenqvist 3,* 1 State Key Laboratory of Metal Matrix Composites, School of Materials Science and Engineering, Shanghai Jiao Tong University, Shanghai 200240, China; [email protected] (Y.C.); [email protected] (C.C.); [email protected] (X.Z.) 2 Collaborative Innovation Centre for Advanced Ship and Dee-Sea Exploration, Shanghai Jiao Tong University, Shanghai 200240, China; [email protected] (H.L.); [email protected] (H.L.) 3 Department of Fibre and Polymer Technology, School of Engineering Sciences in Chemistry, Biotechnology and Health, KTH Royal Institute of Technology, SE-100 44 Stockholm, Sweden * Correspondence: [email protected] (H.U.R.); [email protected] (M.S.H.) These authors contributed equally to this work. y Academic Editor: Laura Peponi Received: 7 July 2020; Accepted: 3 September 2020; Published: 16 September 2020 Abstract: Shape-memory materials are smart materials that can remember an original shape and return to their unique state from a deformed secondary shape in the presence of an appropriate stimulus. This property allows these materials to be used as shape-memory artificial muscles, which form a subclass of artificial muscles. The shape-memory artificial muscles are fabricated from shape-memory polymers (SMPs) by twist insertion, shape fixation via Tm or Tg, or by liquid crystal elastomers (LCEs). The prepared SMP artificial muscles can be used in a wide range of applications, from biomimetic and soft robotics to actuators, because they can be operated without sophisticated linkage design and can achieve complex final shapes. -
3D Printable Linear Soft Vacuum Actuators: Their Modeling, Performance Quantification and Application in Soft Robotic Systems
University of Wollongong Research Online Faculty of Engineering and Information Faculty of Engineering and Information Sciences - Papers: Part B Sciences 2019 3D Printable Linear Soft Vacuum Actuators: Their Modeling, Performance Quantification and Application in Soft Robotic Systems Charbel Tawk University of Wollongong, [email protected] Geoffrey M. Spinks University of Wollongong, [email protected] Marc in het Panhuis University of Wollongong, [email protected] Gursel Alici University of Wollongong, [email protected] Follow this and additional works at: https://ro.uow.edu.au/eispapers1 Part of the Engineering Commons, and the Science and Technology Studies Commons Recommended Citation Tawk, Charbel; Spinks, Geoffrey M.; in het Panhuis, Marc; and Alici, Gursel, "3D Printable Linear Soft Vacuum Actuators: Their Modeling, Performance Quantification and Application in Soft Robotic Systems" (2019). Faculty of Engineering and Information Sciences - Papers: Part B. 3375. https://ro.uow.edu.au/eispapers1/3375 Research Online is the open access institutional repository for the University of Wollongong. For further information contact the UOW Library: [email protected] 3D Printable Linear Soft Vacuum Actuators: Their Modeling, Performance Quantification and Application in Soft Robotic Systems Abstract Conventional robotic systems have proved their versatility in the industry where complex tasks requiring high force, high speed and high precision are desired. However, these rigid-bodied systems cannot collaborate safely with humans. -
Two-Dimensional Mos2 Electromechanical Actuators
Two-dimensional MoS2 electromechanical actuators Nguyen T. Hung1, Ahmad R. T. Nugraha1, Riichiro Saito1 1Department of Physics, Tohoku University, Sendai 980-8578, Japan E-mail: [email protected] February 2014 Abstract. We investigate electromechanical properties of two-dimensional MoS2 monolayers in the 1H, 1T, and 1T0 structures as a function of charge doping by using density functional theory. We find isotropic elastic moduli in the 1H and 1T structures, while the 1T0 structure exhibits an anisotropic elastic modulus. Moreover, the 1T structure is shown to have a negative Poisson's ratio, while Poisson's ratios of the 0 1H and 1T are positive. By charge doping, the monolayer MoS2 shows a reversibly strain and work density per cycle ranging from −0:68% to 2:67% and from 4.4 to 36.9 MJ/m3, respectively, making them suitable for applications in electromechanical actuators. Stress generated is also examined in this work and we find that 1T and 1T0 MoS2 monolayers relatively have better performance than 1H MoS2 monolayer. We argue that such excellent electromechanical performance originate from the electrical conductivity of the metallic 1T and semimetallic 1T0 structures high Young's modulus of about 150 − 200 GPa. arXiv:1711.00188v1 [cond-mat.mtrl-sci] 1 Nov 2017 Two-dimensional MoS2 electromechanical actuators 2 1. Introduction Natural muscle is an example of good-performance actuator with work cycles involving contractions of more than 20%, although the stress generation ability of natural muscle is quite low (0:35 MPa) [1] compared with mechanical machine. Various actuation materials have been studied to replace natural muscle that can directly convert electrical energy into mechanical energy, with wide potential applications in soft robotics, adaptive wings for aircraft, and biometric machines [1]. -
Direct Writing Corrugated PVC Gel Artificial Muscle Via Multi-Material
polymers Article Direct Writing Corrugated PVC Gel Artificial Muscle via Multi-Material Printing Processes Bin Luo 1,2,3,*, Yiding Zhong 2, Hualing Chen 1,2,*, Zicai Zhu 2 and Yanjie Wang 4 1 State Key Laboratory for Strength and Vibration of Mechanical Structures, Xi’an Jiaotong University, Xi’an 710049, China 2 School of Mechanical Engineering, Xi’an Jiaotong University, Xi’an 710049, China; [email protected] (Y.Z.); [email protected] (Z.Z.) 3 School of Mechanical and Energy Engineering, Shaoyang University, Shaoyang 422000, China 4 Changzhou Campus, School of Mechanical and Electrical Engineering, Hohai University, Changzhou 213022, China; [email protected] * Correspondence: [email protected] (B.L.); [email protected] (H.C.) Abstract: Electroactive PVC gel is a new artificial muscle material with good performance that can mimic the movement of biological muscle in an electric field. However, traditional manufacturing methods, such as casting, prevent the broad application of this promising material because they cannot achieve the integration of the PVC gel electrode and core layer, and at the same time, it is difficult to create complex and diverse structures. In this study, a multi-material, integrated direct writing method is proposed to fabricate corrugated PVC gel artificial muscle. Inks with suitable rheological properties were developed for printing four functional layers, including core layers, electrode layers, sacrificial layers, and insulating layers, with different characteristics. The curing conditions of the printed CNT/SMP inks under different applied conditions were also discussed. The structural parameters were optimized to improve the actuating performance of the PVC gel artificial Citation: Luo, B.; Zhong, Y.; Chen, muscle. -
ROBOTIC ARTIFICIAL MUSCLES University of Technology and Education, Cheonan 330-708, South Korea (E- Mail: [email protected])
1 Robotic Artificial Muscles: Current Progress and Future Perspectives Jun Zhang, Jun Sheng, Ciaran´ T. O’Neill, Conor J. Walsh, Robert J. Wood, Jee-Hwan Ryu, Jaydev P. Desai, and Michael C. Yip Abstract—Robotic artificial muscles are a subset of artificial details about the selection, design, and usage considerations muscles that are capable of producing biologically inspired mo- of various prominent robotic artificial muscles for generating tions useful for robot systems - i.e., large power-to-weight ratios, biomimetic motions. Past survey papers have either covered inherent compliance, and large range of motions. These actuators, ranging from shape memory alloys to dielectric elastomers, are the broad topic of general artificial muscles [1] or focused increasingly popular for biomimetic robots as they may operate on a few particular aspects of a specific robotic artificial without using complex linkage designs or other cumbersome muscle. For example, [2], [3] focused on the working mech- mechanisms. Recent achievements in fabrication, modeling, and anisms of artificial muscles, [17], [18] focused on aerospace control methods have significantly contributed to their potential applications and soft robots composed of SMA actuators, and utilization in a wide range of applications. However, no survey paper has gone into depth regarding considerations pertaining [4] focused on wearable robotic orthoses applications using to their selection, design, and usage in generating biomimetic robotic artificial muscles. [19], [20] reviewed the models of motions. This paper will discuss important characteristics and SMA and McKibben actuators, [18] discussed the designs and considerations in the selection, design, and implementation of applications of SMA actuators, [21] reviewed the technology, various prominent and unique robotic artificial muscles for applications, and challenges of dielectric elastomer actuators biomimetic robots, and provide perspectives on next-generation muscle-powered robots. -
New Twist on Artificial Muscles
University of Wollongong Research Online Faculty of Engineering and Information Faculty of Engineering and Information Sciences - Papers: Part A Sciences 1-1-2016 New twist on artificial muscles Carter S. Haines University of Texas Na Li University of Texas, Nankai University Geoffrey M. Spinks University of Wollongong, [email protected] Ali E. Aliev University of Texas Jiangtao Di University of Texas See next page for additional authors Follow this and additional works at: https://ro.uow.edu.au/eispapers Part of the Engineering Commons, and the Science and Technology Studies Commons Recommended Citation Haines, Carter S.; Li, Na; Spinks, Geoffrey M.; Aliev, Ali E.; Di, Jiangtao; and Baughman, Ray H., "New twist on artificial muscles" (2016). Faculty of Engineering and Information Sciences - Papers: Part A. 6167. https://ro.uow.edu.au/eispapers/6167 Research Online is the open access institutional repository for the University of Wollongong. For further information contact the UOW Library: [email protected] New twist on artificial muscles Abstract Lightweight artificial muscle fibers that can match the large tensile stroke of natural muscles have been elusive. In particular, low stroke, limited cycle life, and inefficient energy conversion have combined with high cost and hysteretic performance to restrict practical use. In recent years, a new class of artificial muscles, based on highly twisted fibers, has emerged that can deliver more than 2,000 J/kg of specific work during muscle contraction, compared with just 40 J/kg for natural muscle. Thermally actuated muscles made from ordinary polymer fibers can deliver long-life, hysteresis-free tensile strokes of more than 30% and torsional actuation capable of spinning a paddle at speeds of more than 100,000 rpm. -
Polymer Artificial Muscles: Controls and Applications with Low-Cost Twist Insertion Fiber Actuators William Daniel Hunt Worcester Polytechnic Institute
Worcester Polytechnic Institute Digital WPI Major Qualifying Projects (All Years) Major Qualifying Projects March 2016 Polymer Artificial Muscles: Controls and Applications with Low-Cost Twist Insertion Fiber Actuators William Daniel Hunt Worcester Polytechnic Institute Follow this and additional works at: https://digitalcommons.wpi.edu/mqp-all Repository Citation Hunt, W. D. (2016). Polymer Artificial Muscles: Controls and Applications with Low-Cost Twist Insertion Fiber Actuators. Retrieved from https://digitalcommons.wpi.edu/mqp-all/51 This Unrestricted is brought to you for free and open access by the Major Qualifying Projects at Digital WPI. It has been accepted for inclusion in Major Qualifying Projects (All Years) by an authorized administrator of Digital WPI. For more information, please contact [email protected]. Polymer Artificial Muscles Controls and Applications with Low-Cost Twist Insertion Fiber Actuators A Major Qualifying Project Submitted to the Faculty of Worcester Polytechnic Institute in partial fulfillment of the requirements for the Degree of Bachelor of Science in Robotics Engineering By ____________________________________ William Hunt Robotics Engineering Program Date: 6 May 2015 Project Advisor: ____________________________________ Professor Cagdas Onal This report represents the work of a WPI undergraduate student submitted to the faculty as evidence of a degree requirement. WPI routinely publishes these reports on its web site without editorial or peer review. For more information about the projects program at WPI, see http://www.wpi.edu/Academics/Projects. Abstract Functional artificial muscle fibers could reduce the cost, weight and complexity of many robotic systems, and are therefore an attractive development goal in robotics engineering. When coiled into flexible helical artificial muscle fibers, Nylon monofilaments produce linear tensile actuation under thermal stimulus. -
Artificial Muscle Technology: Physical Principles and Naval Prospects
J. Madden et. al. Artificial Muscle Technology, Paper # 17 1 Artificial Muscle Technology: Physical Principles and Naval Prospects John D. Madden, Nathan Vandesteeg, Patrick A. Anquetil, Peter G. Madden, Arash Takshi, Rachel Z. Pytel, Serge R. Lafontaine, Paul A. Wieringa and Ian W. Hunter benefit for medical implants and human assist devices, as Abstract—The increasing understanding of the advantages well as for minimally invasive surgical and diagnostic offered by fish and insect-like locomotion is creating a demand tools. Combustion engines and high revving electric for muscle-like materials capable of mimicking nature’s motors feature high specific power [1] but require complex mechanisms. Actuator materials that employ voltage, field, transmission systems to perform discontinuous and non- light or temperature driven dimensional changes to produce repetitive tasks, greatly reducing their efficiency and forces and displacements are suggesting new approaches to increasing cost. Direct drive electric motors are low in propulsion and maneuverability. Fundamental properties of these new materials are presented, and examples of potential force and torque to mass compared to muscle [1]. These undersea applications are examined in order to assist those deficiencies make human motion and dexterity challenging involved in device design and in actuator research to evaluate to reproduce in robots, toys and medical devices. For the current status and the developing potential of these example, the walking speed of Honda’s impressive artificial muscle technologies. Technologies described are humanoid robot, Asimo [2], is limited to 2 km/hr by the based on newly explored materials developed over the past torque available in the direct drive motors actuating each decade, and also on older materials whose properties are not joint. -
Colloidal Electronics
Colloidal Electronics by (Albert) Tianxiang Liu B.S. Chemical Engineering, California institute of Technology, 2014 SUBMITTED TO THE DEPARTMENT OF CHEMICAL ENGINEERING IN PARTIAL FULFILLMENT OF THE REQUIREMENTS FOR THE DEGREE OF DOCTOR OF PHILOSOPHY IN CHEMICAL ENGINEERING AT THE MASSACHUSETTS INSTITUTE OF TECHNOLOGY July 2020 © 2020 Massachusetts Institute of Technology. All rights reserved. Signature of author ............................................................................................................................. Department of Chemical Engineering July 27, 2020 Certified by ........................................................................................................................................ Michael S. Strano Carbon P. Dubbs Professor of Chemical Engineering Thesis Supervisor Accepted by ....................................................................................................................................... Patrick S. Doyle Robert T. Haslam (1911) Professor of Chemical Engineering Graduate Officer 2 Colloidal Electronics by (Albert) Tianxiang Liu Submitted to the Department of Chemical Engineering on July 27, 2020, in partial fulfillment of the requirements for the degree of Doctor of Philosophy in Chemical Engineering Abstract Arming nano-electronics with mobility extends artificial systems into traditionally inaccessible environments. Carbon nanotubes (1D), graphene (2D) and other low-dimensional materials with well-defined lattice structures can be incorporated into polymer microparticles, -
A REVIEW and STUDY of VERY HIGH NANOFILLER-CONTENT NANOCOMPOSITES: THEIR PREPARATION METHODS, CHARACTERIZATION and PROPERTIES By
A REVIEW AND STUDY OF VERY HIGH NANOFILLER-CONTENT NANOCOMPOSITES: THEIR PREPARATION METHODS, CHARACTERIZATION AND PROPERTIES by JEFFREY PHILIP GEORGE Submitted for partial fulfillment of the requirements For the degree of Master of Science Thesis adviser: Dr. Hatsuo Ishida Department of Macromolecular Science and Engineering CASE WESTERN RESERVE UNIVERSITY August, 2019 CASE WESTERN RESERVE UNIVERSITY SCHOOL OF GRADUATE STUDIES We hereby approve the thesis/dissertation of Jeffrey Philip George candidate for the degree of Master of Science*. Committee Chair Dr. Hatsuo Ishida Committee Member Dr. David Schiraldi Committee Member Dr. Gary Wnek Date of Defense June 6th, 2019 *We also certify that written approval has been obtained for any proprietary material contained therein. Table of Contents Table of Contents................................................................................................ i List of Figures..................................................................................................... iv List of Tables...................................................................................................... x Acknowledgement.............................................................................................. xi Abstract............................................................................................................... xii Chapter 1: A Review on the Very High Nanofiller-Content Nanocomposites: Their Preparation Methods and Properties with High Aspect Ratio Filler........ 1 1.1 Introduction.............................................................................................. -
Tethered and Untethered 3D Microactuators Fabricated by Two-Photon Polymerization: a Review
micromachines Review Tethered and Untethered 3D Microactuators Fabricated by Two-Photon Polymerization: A Review Zhaoxin Lao 1,2,3,* , Neng Xia 1, Shijie Wang 1 , Tiantian Xu 4, Xinyu Wu 4 and Li Zhang 1,* 1 Department of Mechanical and Automation Engineering, The Chinese University of Hong Kong, Sha Tin, Hong Kong 999077, China; [email protected] (N.X.); [email protected] (S.W.) 2 Anhui Province Key Laboratory of Measuring Theory and Precision Instrument, School of Instrument Science and Opto-Electronics Engineering, Hefei University of Technology, Hefei 230009, China 3 CAS Key Laboratory of Mechanical Behavior and Design of Materials, Key Laboratory of Precision Scientific Instrumentation of Anhui Higher Education Institutes, Department of Precision Machinery and Precision Instrumentation, University of Science and Technology of China, Hefei 230022, China 4 Guangdong Provincial Key Laboratory of Robotics and Intelligent System, Shenzhen Institutes of Advanced Technology, Chinese Academy of Sciences, Shenzhen 518055, China; [email protected] (T.X.); [email protected] (X.W.) * Correspondence: [email protected] (Z.L.); [email protected] (L.Z.) Abstract: Microactuators, which can transform external stimuli into mechanical motion at microscale, have attracted extensive attention because they can be used to construct microelectromechanical systems (MEMS) and/or microrobots, resulting in extensive applications in a large number of fields such as noninvasive surgery, targeted delivery, and biomedical machines. In contrast to classical 2D MEMS devices, 3D microactuators provide a new platform for the research of stimuli-responsive Citation: Lao, Z.; Xia, N.; Wang, S.; functional devices. However, traditional planar processing techniques based on photolithography are Xu, T.; Wu, X.; Zhang, L. -
Symmetry-Breaking Actuation Mechanism for Soft Robotics and Active Metamaterials
Symmetry-breaking Actuation Mechanism for Soft Robotics and Active Metamaterials Shuai Wua,1, Qiji Zea,1, Rundong Zhanga, Nan Hub, Yang Chengc, Fengyuan Yangc, Ruike Zhaoa,* aSoft Intelligent Materials Laboratory, Department of Mechanical and Aerospace Engineering, The Ohio State University, Columbus, OH, 43210, USA; bDepartment of Civil, Environmental and Geodetic Engineering, The Ohio State University, Columbus, OH, 43210, USA; cDepartment of Physics, The Ohio State University, Columbus, OH, 43210, USA 1S. W. and Q. Z. contributed equally to this work. *Correspondence and requests for materials should be addressed to R. Z. ([email protected]) 1 ABSTRACT Magnetic-responsive composites that consist of soft matrix embedded with hard-magnetic particles have recently been demonstrated as robust soft active materials for fast-transforming actuation. However, the deformation of the functional components commonly attains only a single actuation mode under external stimuli, which limits their capability of achieving tunable properties. To greatly enhance the versatility of soft active materials, we exploit a new class of programmable magnetic-responsive composites incorporated with a multifunctional joint design that allows asymmetric multimodal actuation under an external stimulation. We demonstrate that the proposed asymmetric multimodal actuation enables a plethora of novel applications ranging from the basic 1D/2D active structures with asymmetric shape-shifting to biomimetic crawling and swimming robots with efficient dynamic performance