HCIO@·•F"'Vfl' O~ON
Total Page:16
File Type:pdf, Size:1020Kb
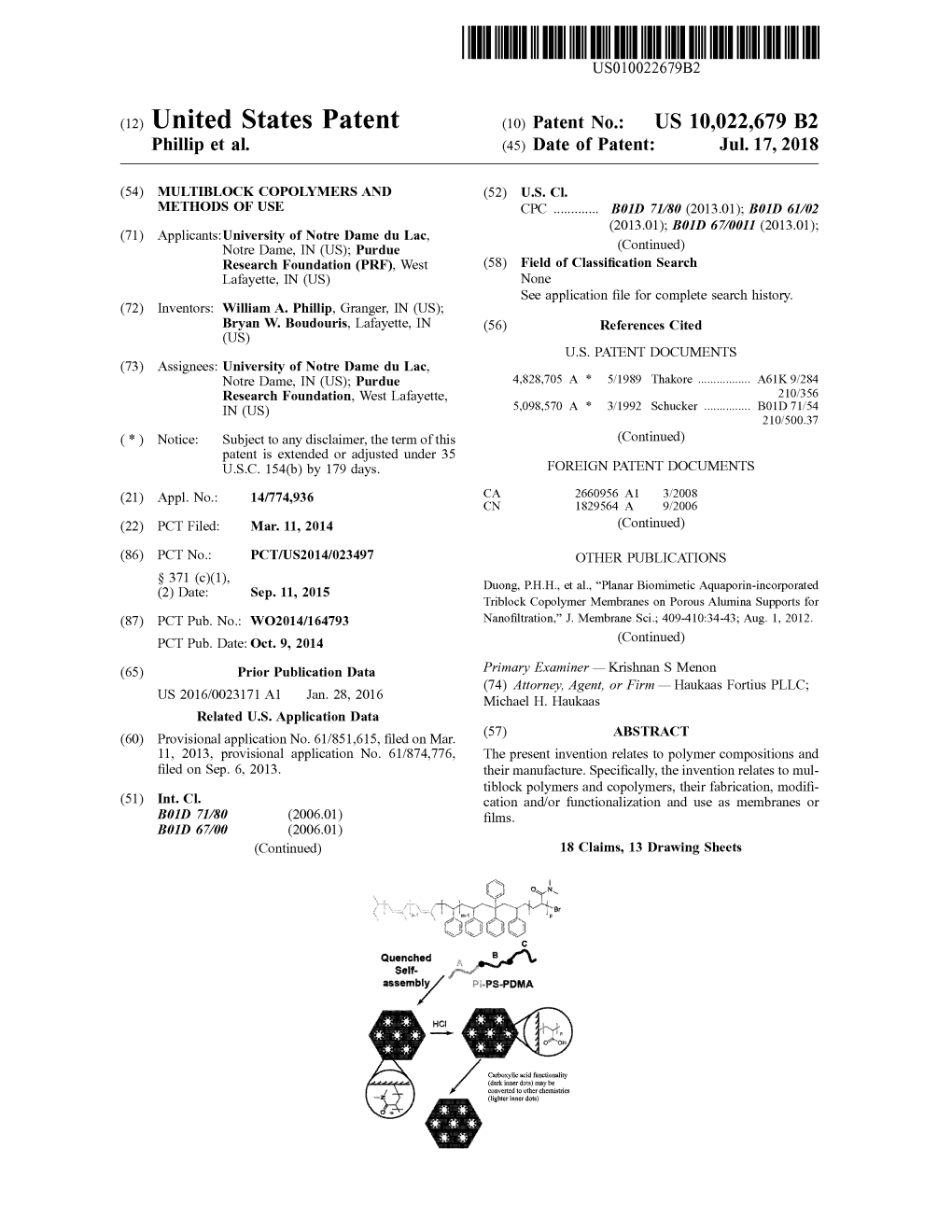
Load more
Recommended publications
-
Allium Discoloration: the Nature of Onion Pinking and Garlic Greening
Czech J. Food Sci. Vol. 22, Special Issue Allium Discoloration: The Nature of Onion Pinking and Garlic Greening R. KUBEC1*, M. HRBÁČOVÁ1, R. A. MUSAH2 and J. VELÍŠEK1 1Department of Food Chemistry and Analysis, Institute of Chemical Technology, Prague, Czech Republic, *E-mail: [email protected]; 2Department of Chemistry, SUNY Albany, Albany, NY, USA Abstract: Precursors involved in the formation of pink and green-blue pigments during onion and garlic process- ing, respectively, have been studied. It has been confirmed that the formation of both pigments is of a very similar nature, with (E)-S-(1-propenyl)cysteine sulfoxide (isoalliin) serving as the primary precursor. Upon disruption of the tissue, isoalliin and other S-alk(en)ylcysteine sulfoxides are enzymatically cleaved, yielding prop-1-enyl- containing thiosulfinates [CH3CH = CHS(O)SR; R = methyl, allyl, propyl, 1-propenyl], among others. The latter compounds subsequently react with amino acids to produce the pigments. Whereas the onion and leek-related propyl, prop-1-enyl and methyl derivatives can form pink, pink-red and magenta compounds, those containing the allyl group yield dark blue products after reacting with glycine at pH 5.0. Keywords: Allium; garlic; onion; discoloration; pigment INTRODUCTION sulfoxide (isoalliin, 1). Isoalliin is the major free amino acid occurring in onion and it is also present During processing of garlic (Allium sativum L.), as a minor S-substituted cysteine sulfoxide deriva- onion (A. cepa L.) and leek (A. porrum L.) intensely tive in garlic. The key role of isoalliin in the dis- colored pigments are often formed. In the case of coloration of garlic was later confirmed by L���� garlic, green, blue-green or blue compounds are [5]. -
Proceedings of the Indiana Academy of Science
The Structure of the Stereoisomeric Trithianes 1 E. Capaigne and Walter M. Budded, Indiana University When acetaldehyde is treated with hydrogen sulfide and hydrogen chloride, trithioacetaldehyde is formed, and originally (1) three different isomers; a, m.p. 101°; /3; m.p. 125-6°, and 7; m.p. 81°; were isolated. It was possible to convert a into p by heating with iodine or acetyl chloride. Since the trithiane ring was assumed to be planar, only two isomers, cis-cis (I) and cis-trans (II) should exist. Suyver (2) demon- strated that a eutectic mixture of 60% a and 40% p isomer melts sharply at 75-76° and it was generally conceded that this is the explana- tion of the 7-isomer. It is still reported in the handbooks, however, and crops up as justification for different structures of the trithiane ring. In 1947, Schonberg and Barakat (3), disturbed by the ready interchange of a to jS forms in a cylic system in which tautomerism is presumably impossible, proposed the following theory: "The three carbon atoms and the three sulfur atoms in 1, 3, 5- trithiane molecules do not lie in one plane, but may be regarded as 'boat' and 'chair' structures, the interconversion then being readily explained. According to this explanation, the a- and /3-forms of trithioacetaldehyde, for example, are either both cis- or both trans- forms; the isomeric change is due to a change of 'boat' into 'chair' structures, or vice versa. This new theory demands a greater number of isomers than have, so far, been isolated, but it is not thereby neces- sarily invalidated, for some isomers (7-forms) have occasionally been described, which have been attributed inter alia to polymorphism or the occurrence of eutectic mixtures. -
(12) Patent Application Publication (10) Pub. No.: US 2014/0220346A1 Heller Et Al
US 20140220346A1 (19) United States (12) Patent Application Publication (10) Pub. No.: US 2014/0220346A1 Heller et al. (43) Pub. Date: Aug. 7, 2014 (54) MODULAR POLYMER HYDROGEL (22) Filed: Dec. 4, 2013 NANOPARTICLES AND METHODS OF THER MANUFACTURE Related U.S. Application Data (60) Provisional application No. 61/733,366, filed on Dec. (71) Applicants: Memorial Sloan-Kettering Cancer 4, 2012. Center, New York, NY (US); Massachusetts Institute of Technology, Publication Classification Cambridge, MA (US) (51) Int. Cl. (72) Inventors: Daniel A. Heller, New York, NY (US); A647/48 (2006.01) Jasmine Wallas, New York, NY (US); A614.9/00 (2006.01) Yair Levi, Cambridge, MA (US); (52) U.S. Cl. George W. Pratt, Waban, MA (US); CPC ......... A61K 47/4823 (2013.01); A61K 49/0054 Daniel G. Anderson, Sudbury, MA (2013.01); A61K 49/0073 (2013.01) (US); Robert Langer, Newton, MA USPC .............................. 428/402:536/51:536/112 (US) (57) ABSTRACT (73) Assignees: Memorial Sloan-Kettering Cancer In certain embodiments, a nano-sized vehicle (e.g., a nanogel Center, New York, NY (US); comprising nanoparticles) is provided herein for drug deliv Massachusetts Institute of Technology, ery with tunable biodistribution, low toxicity, and degradabil Cambridge, MA (US) ity, and with demonstrated targeting to bone. The composi tion is useful, for example, in the treatment of bone disease, particularly bone metastases from cancers such as breast, (21) Appl. No.: 14/097,212 prostate, or lung cancer. Patent Application Publication Aug. 7, 2014 Sheet 1 of 36 US 2014/0220346 A1 N Patent Application Publication Aug. 7, 2014 Sheet 2 of 36 US 2014/0220346 A1 8],'04- Patent Application Publication Aug. -
Selected Reactions of Thiocarbonyl Compounds Oac O Ncy Oac CN 2 Shyam Krishnan Me Meo Monday, June 12, 2006 Me H Me N O H 8 P.M
OH S Me S O O N SEt TBSO Ph O Me Me N OH BnO S Selected Reactions of Thiocarbonyl Compounds OAc O NCy OAc CN 2 Shyam Krishnan Me MeO Monday, June 12, 2006 Me H Me N O H 8 p.m. N O Me 147 Noyes H O O O HN O H H S Me S S H H BnO BnO N N i) ICH2CO2Et, CHCl3 S ii) PPh , DABCO, 3 CO2Et CHCl3, reflux (92% yield) I I OMe OMe Selected Reactions of Thiocarbonyl Compounds 1) Thiocarbonyl compounds: nomenclature and structural properties 2) Methods of Synthesis 3) Reactions of thiocarbonyl compounds and their application in the synthesis of functionalized molecules 1) Reactions of carbanions derived from Thiocarbonyl compounds. 2) Carbanion addition to the thiocarbonyl group. 3) Reactions with electrophiles - the Eschenmoser sulfide contraction. 4) Radical mediated reactions. 5) [3,3] sigmatropic rearrangements - the thio-Claisen rearrangement. 6) [4+2] cycloaddition reactions. 7) [3+2] Dipolar cycloadditions. 8) Summary and future directions. Reviews: General review: Metzner, P. Top. Curr. Chem. 1999, 204, 127. General review: Metzner, P. Synthesis 1992, 1185. Synthesis of heterocycles: Jagodzinski, T.S. Chem. Rev. 2003, 103, 197. Radical chemistry: Crich, D.; Quintero, L. Chem. Rev. 1989, 89, 1413. Photochemistry: Coyle, J. D. Tetrahedron 1985, 41, 5393. Thiocarbonyl Compounds Structures, Nomenclature and Stability Thiocarbonyl compounds possess a carbon-sulfur double bond Thiocarbonyl compounds with at least one organic group bound to the thiocarbonyl carbon: O S S S S S S R H R R' R OR R NR2 R SR R R' Thioaldehyde Thioketone Thionoester Thioamide Dithioester Sulfine/Thiocarbonyl oxide Typically display greater reactivity than their carbonyl (oxygen) analogs • Larger covalent radius of sulfur vs oxygen (104.9 nm vs 70.2 nm), less efficient overlap in S3p-C2p π-bond • Dissociation energy of C=S (115 kcal/mol) is significantly lower than for C=O (162 kcal/mol). -
Chemistry Based Enrichable Cross‐
Accepted Article Title: A Click-chemistry based enrichable cross-linker for structural and protein interaction analysis by mass spectrometry Authors: Michael Stadlmeier, Leander Simon Runtsch, Filipp Streshnev, Martin Wühr, and Thomas Carell This manuscript has been accepted after peer review and appears as an Accepted Article online prior to editing, proofing, and formal publication of the final Version of Record (VoR). This work is currently citable by using the Digital Object Identifier (DOI) given below. The VoR will be published online in Early View as soon as possible and may be different to this Accepted Article as a result of editing. Readers should obtain the VoR from the journal website shown below when it is published to ensure accuracy of information. The authors are responsible for the content of this Accepted Article. To be cited as: ChemBioChem 10.1002/cbic.201900611 Link to VoR: http://dx.doi.org/10.1002/cbic.201900611 A Journal of www.chembiochem.org ChemBioChem 10.1002/cbic.201900611 COMMUNICATION A Click-chemistry based enrichable cross-linker for structural and protein interaction analysis by mass spectrometry Michael Stadlmeier[a],+, Leander Simon Runtsch[a],+, Filipp Streshnev[a], Martin Wühr[b] and Thomas Carell[a],* Abstract: Mass spectrometry (MS) is the method of choice for the characterization of proteomes. Most proteins operate in protein complexes, where their close association modulates their function. However, with standard MS analysis the information of protein-protein interactions is lost and no structural information is retained. In order to gain structural and interactome data, new cross-linking reagents are needed that freeze inter- and intramolecular interactions. -
Indolecarbonyl Coupling Reactions Promoted by Samarium Diiodide. Application to the Synthesis of Indole-Fused Compounds
J. Org. Chem. 1998, 63, 2909-2917 2909 Indolecarbonyl Coupling Reactions Promoted by Samarium Diiodide. Application to the Synthesis of Indole-Fused Compounds Shu-Chen Lin, Fwu-Duo Yang, Jiann-Shyng Shiue, Shyh-Ming Yang, and Jim-Min Fang* Department of Chemistry, National Taiwan University, Taipei 106, Taiwan, Republic of China Received November 11, 1997 By the assistance of an N-sulfonyl group or a cyano group at the C-2 position, hydroxyalkylations of indole-3-carbonyls were achieved by the promotion of samarium diiodide. The indolecarbonyl coupling reactions proceeded in high stereoselectivity via chelate transition states. Intramolecular indolecarbonyl couplings of 1-(3-oxopropyl)indole-3-carboxaldehydes were realized as the indole- carbonyl group was more reactive toward SmI2 than the aliphatic carbonyl group. Elaboration of the coupling products with oxidizing agents, acid, phosphorus pentasulfide (or Lawesson’s reagent), amines, and hydrazine led to a variety of indole derivatives and indole-fused polycyclic compounds of synthetic interest and pharmaceutical uses. Introduction Table 1. Self-Coupling Reactions of Indole-3-carboxaldehydes Promoted by SmI2 in THF The chemistry of indole compounds1 has been exten- Solution sively studied, partly due to their uses in pharmaceutical and industrial products. However, most studies of indole- 3-carbonyls are limited to the conventional reactions, such as reductions, oxidations (for indole-3-carboxalde- hydes), nucleophilic reactions of organometallic reagents, condensations with active methylene compounds, and aldol reactions (for 3-acetylindoles), similar to those found in common aromatic aldehydes and ketones. In a previ- ous paper,2 we demonstrated a new method for hydroxy- alkylations at the C-2 positions of indole-3-carbonyls by the SmI2-promoted coupling reactions. -
Bioactive S-Alk(En)Yl Cysteine Sulfoxide Metabolites in the Genus Allium: the Chemistry of Potential Therapeutic Agents
http://www.paper.edu.cn REVIEW Bioactive S-alk(en)yl cysteine sulfoxide metabolites in the genus www.rsc.org/npr Allium: the chemistry of potential therapeutic agents NPR Peter Rose,*a Matt Whiteman,a Philip K. Mooreb and Yi Zhun Zhu*b a Department of Biochemistry, National University of Singapore, 8 Medical Drive, Singapore, 117597. E-mail: [email protected]; Fax: (65)-6779-1453; Tel: (65)-6874-4996 b Department of Pharmacology, National University of Singapore, 18 Medical Drive, Singapore, 117597. E-mail: [email protected]; Fax: (65)-6773-7690; Tel: (65)-6874-3676 Received (in Cambridge, UK) 30th March 2005 First published as an Advance Article on the web 10th May 2005 Covering: 1892 to 2004 S-Alk(en)yl cysteine sulfoxides are odourless, non-protein sulfur amino acids typically found in members of the family Alliaceae and are the precursors to the lachrymatory and flavour compounds found in the agronomically important genus Allium. Traditionally, Allium species, particularly the onion (Allium cepa) and garlic (A. sativum), have been used for centuries in European, Asian and American folk medicines for the treatment of numerous human pathologies, however it is only recently that any significant progress has been made in determining their mechanisms of action. Indeed, our understanding of the role of Allium species in human health undoubtedly comes from the combination of several academic disciplines including botany, biochemistry and nutrition. During tissue damage, S-alk(en)yl cysteine sulfoxides are converted to their respective thiosulfinates or propanethial-S-oxide by the action of the enzyme alliinase (EC 4.4.1.4). -
United States Patent Office 2,610,164
Patented Sept. 9, 1952 2,610,164 UNITED STATES PATENT OFFICE 2,610,164. COMPOSITIONS OF WINYL CHLORIDE RESINS AND AROMATIC ESTERS OF . suLFONATED ALKANES Earl W. Gluesenkamp, Centerville, and Joachim Dazzi, Dayton, Ohio, assignors to Monsanto Chemical Company, St. Louis, Mo., a corpora tion of Delaware NoDrawing. Application August 20, 1949, serial No. 111,562 Claims. (Cl. 260-30.8) This invention relates to vinyl chloride com Thus, the... useful. plasticizers2 for practicing this positions having unusual flexibility and high invention are the esters corresponding to the stability at elevated temperatures. More Specif following structural formula ically the invention relates to a novel group of plasticizers for vinyl chloride polymers which X. O , have unusual efficacy in developing desirable physical properties. X >-o-s-ch,-(CH)-ons6. The esters of sulfonated aliphatic hydrocar wherein X is a radical of the group consisting bons are known chemical compounds, some of of hydrogen, chlorine and methyl, and wherein which have been used as plasticizers. The esters, n is a whole number from eight to twelve. which are prepared from petroleum products The new esters may be prepared from 1-olefins are mixtures of very many different compounds. as derived from the Fischer-Tropsch reaction, They have wide variations in the length and or from the primary n-mercaptains. The 1-olefins configuration of the aliphatic chain and in the may be reacted with hydrogen sulfide or 6-mer place on the chain where the sulfonic acid group captoethanol. The mercaptain, its thial, or the is substituted. Many of the ester mixtures are alkyl mercaptoethanols are then oxidized, for too volatile for successful application as plasti example with nitric acid and thereby converted cizers, and others are incompatible and conse to the corresponding sulfonic acids. -
Allium Thiosulfinates: Chemistry, Biological Properties and Their Potential Utilization in Food Preservation
Food ©2007 Global Science Books Allium Thiosulfinates: Chemistry, Biological Properties and their Potential Utilization in Food Preservation Noureddine Benkeblia1,2* • Virginia Lanzotti3 1 Department of Food and Nutrition Sciences, Graduate School of Dairy Science Research, Rakuno Gakuen University, Ebetsu, Hokkaido, 060-8501, Japan 2 Graduate School of Agriculture, Hokkaido University, Sapporo 060-8589, Japan 3 Department of STAAM, University of Molise, 86100 Campobasso, Italy Corresponding author : * [email protected], [email protected] ABSTRACT Onion (Allium cepa L.), garlic (Allium sativum L.) and other edible Allium are among the oldest cultivated plants, and are used for multiple purposes. They are a rich source of several phytonutrients, and recognized to have significant and wide biological activities. These biological activities are related to the thiosulfinates, volatile sulfur compounds which are responsible for the pungency of these vegetables. The thiosulfinates or alkane(ene) thial-S-oxide are formed by the action of the enzyme alliinase (E.C. 4.4.1.4) from their respective S-alk(en)yl cysteine sulfoxides. However, depending on the Allium species, and under differing conditions, thiosulfinates can decompose to form additional sulfur constituents, including diallyl, methyl allyl, and diethyl mono-, di-, tri-, tetra-, penta-, and hexasulfides, vinyldithiins, and (E)- and (Z)-ajoene. With increasing interest into the utilization of natural biologically active compounds and the development of specific packaging, mainly active packaging, the thiosulfinates aroused much interest for the improvement of shelf-life and safety of perishable foods, and their potency as food preservatives and substitutes for chemicals. This review examines the nature and the biological activities of Allium thiosulfinates and their potential values as food preservatives in food preservation and shelf- life extension. -
Functional Groups in Organic Chemistry
FUNCTIONAL GROUPS IN ORGANIC CHEMISTRY Functional groups are the characteristic groups in organic molecules that give them their reactivity. In the formulae below, R represents the rest of the molecule and X represents any halogen atom. Hydrocarbons Halogen-containing groups Oxygen-containing groups Nitrogen-containing groups Sulfur-containing groups Phosphorus-containing groups H H O O O R1 R2 O O R1 C C R2 C C 1 C C 2 R C C C R R R X R OH C C 1 O 2 3 4 1 2 R R H H R R R H R R R OH ALKANE ALKENE ALKYNE ARENE HALOALKANE ALCOHOL ALDEHYDE KETONE CARBOXYLIC ACID ACID ANHYDRIDE Naming: -ane Naming: -ene Naming: -yne Naming: -yl benzene Naming: halo- Naming: -ol Naming: -al Naming: -one Naming: -oic acid Naming: -oic anhydride e.g. ethane e.g. ethene e.g. ethyne e.g. ethyl benzene e.g. chloroethane e.g. ethanol e.g. ethanal e.g. propanone e.g. ethanoic acid e.g. ethanoic anhydride O O O O O O O R1 C C 2 N 3 R N C C 1 2 R R1 R C R N+ R C N N+ 1 2 R R 3 4 2 – O O – R X R OR R R R R NH2 O O R O ACYL HALIDE ESTER ETHER EPOXIDE AMINE AMIDE NITRATE NITRITE NITRILE NITRO Naming: -oyl halide Naming: -yl -oate Naming: -oxy -ane Naming: -ene oxide Naming: -amine Naming: -amide Naming: -yl nitrate Naming: -yl nitrite Naming: -nitrile Naming: nitro- e.g. -
Nomenclature of Organic Chemistry. IUPAC Recommendations and Preferred Names 2013
International Union of Pure and Applied Chemistry Division VIII Chemical Nomenclature and Structure Representation Division Nomenclature of Organic Chemistry. IUPAC Recommendations and Preferred Names 2013. Prepared for publication by Henri A. Favre and Warren H. Powell, Royal Society of Chemistry, ISBN 978-0-85404-182-4 Chapter P-6 APPLICATIONS TO SPECIFIC CLASSES OF COMPOUNDS (continued) (P-66 to P-69) (continued from P-60 to P-65) P-60 Introduction P-61 Substitutive nomenclature: prefix mode P-62 Amines and imines P-63 Hydroxy compounds, ethers, peroxols, peroxides and chalcogen analogues P-64 Ketones, pseudoketones and heterones, and chalcogen analogues P-65 Acids and derivatives P-66 Amides, hydrazides, nitriles, aldehydes P-67 Oxoacids used as parents for organic compounds P-68 Nomenclature of other classes of compounds P-69 Organometallic compounds P-66 AMIDES, IMIDES, HYDRAZIDES, NITRILES, AND ALDEHYDES, P-66.0 Introduction P-66.1 Amides P-66.2 Imides P-66.3 Hydrazides P-66.4 Amidines, amidrazones, hydrazidines, and amidoximes (amide oximes) P-66.5 Nitriles P-66.6 Aldehydes P-66.0 INTRODUCTION The classes dealt with in this Section have in common the fact that their retained names are derived from those of acids by changing the ‘ic acid’ ending to a class name, for example ‘amide’, ‘ohydrazide’, ‘nitrile’, or ‘aldehyde’. Their systematic names are formed substitutively by the suffix mode using one of two types of suffix, one that includes the carbon atom, for example, ‘carbonitrile’ for –CN, and one that does not, for example, ‘-nitrile’ for –(C)N. Amidines are named as amides, hydrazidines as hydrazides, and amidrazones as amides or hydrazides. -
University Microfilms
INFORMATION TO USERS This dissertation was produced from a microfilm copy of the original document. While the most advanced technological means to photograph and reproduce this document have been used, the quality is heavily dependent upon the quality of the original submitted. The following explanation of techniques is provided to help you understand markings or patterns which may appear on this reproduction. 1. The sign or "target" for pages apparently lacking from the document photographed is "Missing Page(s)". If it was possible to obtain the missing page(s) or section, they are spliced into the film along with adjacent pages. This may have necessitated cutting thru an image and duplicating adjacent pages to insure you complete continuity. 2. When an image on the film is obliterated with a large round black mark, it is an indication that the photographer suspected that the copy may have moved during exposure and thus cause a blurred image. You will find a good image of the page in the adjacent frame. 3. When a map, drawing or chart, etc., was part of the material being photographed the photographer followed a definite method in "sectioning" the material. It is customary to begin photoing at the upper left hand corner of a large sheet and to continue photoing from left to right in equal sections with a small overlap. If necessary, sectioning is continued again — beginning below the first row and continuing on until complete. 4. The majority of users indicate that the textual content is of greatest value, however, a somewhat higher quality reproduction could be made from "photographs" if essential to the understanding of the dissertation.