Manual for Expanded Polystyrene (EPS) Core Panel System and Its Field Application
Total Page:16
File Type:pdf, Size:1020Kb
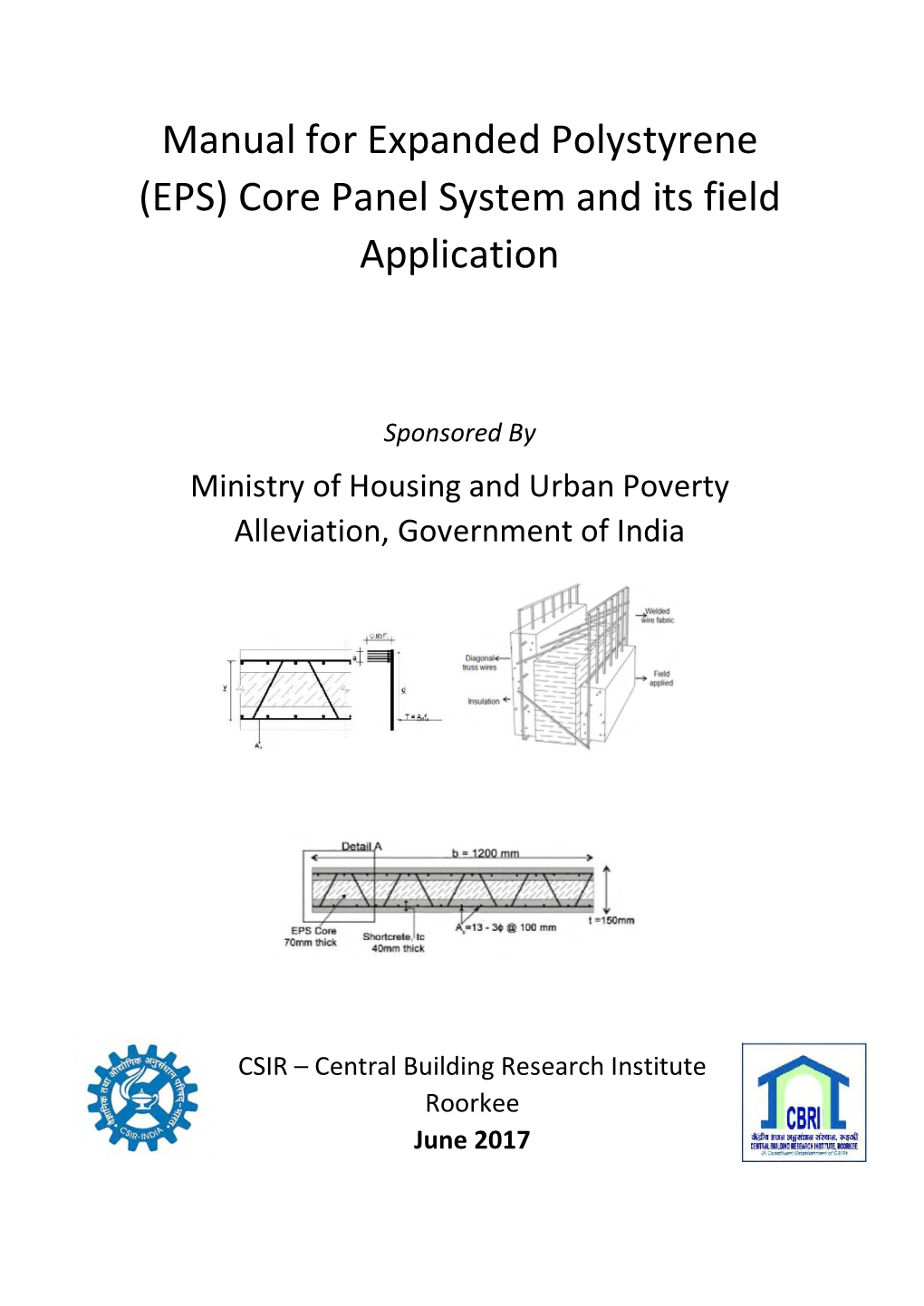
Load more
Recommended publications
-
STRUCTURAL BEHAVIOUR of REINFORCED CONCRETE BEAMS CONTAINING a NOVEL LIGHTWEIGHT AGGREGATE 1. Introduction
STRUCTURAL BEHAVIOUR OF REINFORCED CONCRETE BEAMS CONTAINING A NOVEL LIGHTWEIGHT AGGREGATE ABSTRACT: This paper reports the results of an experimental investigation into the structural behaviour of reinforced concrete beams incorporating a novel EPS-based Lightweight Aggregate (LWA) called Stabilised Polystyrene (SPS) aggregate. Four concrete mixtures with Water to Cement ratio (W/C) of 0.8 were used. The replacement levels of natural aggregate by SPS were 0, 30, 60 and 100%. The volume ratio to manufacture SPS aggregate was 8:1:1 (80% waste EPS: 10% cement: 10% clay). A total of 24 beams were cast and tested at 28-day age. Three types of tension reinforcement were used: 2 bars, 3 bars and 2 bars + shear links. There were no compression bars at the top for all beams. Four point- loading flexural tests were conducted up to failure. In general, it can be observed that the structural behaviour of SPS concrete beams is similar to that of other types of lightweight aggregate concretes used around the world. Keywords: Waste Polystyrene; Lightweight Aggregates; Compressive Strength; Structural Behaviour; Deflection; Reinforced Concrete Beam. 1. Introduction Expanded Polystyrene (EPS) is a thermoplastic material and is mainly used as packaging and insulating products in various industrial fields around the world. A large quantity of EPS is disposed of as waste and left as stockpiles, landfill material or illegally dumped in selected areas. It has been reported that more than 112,000 tons of EPS were used for post-consumer protective packaging in the USA only in 1996. It has also been reported that around 300,000 tons of waste EPS are disposed of in landfill in the UK each year; because up to 95% of EPS is air, it occupies 38,000,000 m3 of space in landfill, which is enough to fill 15,000 Olympic- sized swimming pools! This will ultimately cause pollution and is harmful to the ecosystem. -
Buildblock Building Systems LLC Installation Manual
INSTALLATION MANUAL REVISED 7-2013 BUILDBLOCK BUILDING SYSTEMS, LLC | 9705 N. BROADWAY EXTENSION, SUITE 200, OKLAHOMA CITY, OK 73114 OFFICE: 405-840-3386 | TOLL FREE: 866-222-2575 | FAX: 831-597-0792 BUILDBLOCK.COM BUILDBLOCK BUILDING SYSTEMS, LLC INSTALLATION MANUAL This version of the installation manual was published on January 19, 2011. Changes to this document, however, may occur without notice and users should contact BuildBlock Building Systems LLC, for the most current printed or downloadable version at www.buildblock.com. It is the purchaser’s and/or contractor’s responsibility to always use the most current and up-to-date version of the installation manual when installing BuildBlock forms and/or products. This manual was designed to be used as a reference guide only. This manual is not intended to be used as a replacement or substitute for the actual training by an experienced and properly trained BuildBlock building professional. Before starting any project BuildBlock recommends that you receive proper training. BuildBlock also recommends that you consult with design professionals familiar with the type and scope of project to be built. Training is available by contacting BuildBlock Building Systems LLC at www.buildblock.com or 866-222-2575. BuildBlock Building Systems, LLC, believes the information contained herein to be accurate at the time of writing and preparation. The information has been compiled using sources believed to be reliable. Neither BuildBlock Building Systems, LLC, nor its employees or representatives make any representation or warranty, either expressed or implied, whether arising by statute, operation of law, custom of trade or otherwise, with respect to the accuracy or completeness of information contained in this document or its fitness for any particular purpose, nor do they assume any liability for damages or injury resulting from the application of such information. -
Use of Recycled Concrete Aggregates in Production of Green Cement-Based Concrete Composites: a Review
crystals Review Use of Recycled Concrete Aggregates in Production of Green Cement-Based Concrete Composites: A Review Natt Makul 1, Roman Fediuk 2 , Mugahed Amran 3,4,*, Abdullah M. Zeyad 5 , Gunasekaran Murali 6, Nikolai Vatin 7 , Sergey Klyuev 8 , Togay Ozbakkaloglu 9 and Yuriy Vasilev 7 1 Department of Civil Engineering Technology, Faculty of Industrial Technology, Phranakhon Rajabhat University, Bangkok 10220, Thailand; [email protected] 2 School of Engineering, Far Eastern Federal University, 8, Sukhanova Str., 690950 Vladivostok, Russia; [email protected] 3 Department of Civil Engineering, College of Engineering, Prince Sattam Bin Abdulaziz University, Alkharj 11942, Saudi Arabia 4 Department of Civil Engineering, Faculty of Engineering and IT, Amran University, Amran 9677, Yemen 5 Department of Civil Engineering, Faculty of Engineering, Jazan University, Jazan 45142, Saudi Arabia; [email protected] 6 School of Civil Engineering, SASTRA Deemed to Be University, Thanjavur, Tamil Nadu 613401, India; [email protected] 7 Moscow Automobile and Road Construction University, 125319 Moscow, Russia; [email protected] (N.V.); [email protected] (Y.V.) 8 Department of Theoretical Mechanics and Strength of Materials, Belgorod State Technological University Named after V.G. Shukhov, 308012 Belgorod, Russia; [email protected] 9 Ingram School of Engineering, Texas State University, San Marcos, TX 78666, USA; [email protected] * Correspondence: [email protected] or [email protected] Citation: Makul, N.; Fediuk, R.; Amran, M.; Zeyad, A.M.; Murali, G.; Abstract: Recycled concrete aggregates (RCA) are used in existing green building composites to Vatin, N.; Klyuev, S.; Ozbakkaloglu, promote the environmental preservation of natural coarse aggregates (NCA). -
Volumetric Concrete Mixers
SUPPLEMENTAL SPECIFICATION July 1, 2019 Delete Section 701.4.4.7 Mobile Concrete Mixing Plants and replace it with the following: 701.4.4.7 Volumetric Concrete Mixers Provide volumetric mixers with rating plates indicating that the performance of the mixer is in accordance with the Volumetric Mixer Manufacturer Bureau (VMMB). Ensure that mixers comply with ASTM C685. Unless otherwise specified, ensure that all mixing operations are in strict accordance with the manufacturer's recommended procedures. Provide such procedures to the RCE for review upon request. Ensure that the concrete mixing truck is an auger-type continuous mixer used in conjunction with volumetric proportioning. Ensure that the mixer produces concrete, uniform in color and appearance, with homogeneous distribution of the material throughout the mixture. Establish the mixing time necessary to produce uniform concrete and comply with other requirements of these specifications. Only acceptable equipment capable of producing uniform results will be permitted. Continuous volumetric concrete mixers may be used, with the approval of the RCE and State Materials Engineer, for non-structural concrete. Ensure that mix designs meet the requirements of Section 701.2.12.2 and all materials used meet the requirements of Section 701. Ensure that continuous volumetric concrete mixers are capable of combining aggregate, cement and/or fly ash, water and admixtures, into a uniform mixture within the specified mixing period. Ensure that all materials used are listed on the appropriate QPL -
Concrete Mixing Methods and Concrete Mixers: State of the Art
Volume 106, Number 2, March–April 2001 Journal of Research of the National Institute of Standards and Technology [J. Res. Natl. Inst. Stand. Technol. 106, 391–399 (2001)] Concrete Mixing Methods and Concrete Mixers: State of the Art Volume 106 Number 2 March–April 2001 Chiara F. Ferraris As for all materials, the performance of ule (volume of concrete needed per hour), concrete is determined by its microstruc- and the cost. Ultimately, the quality of National Institute of Standards and ture. Its microstructure is determined by its the concrete produced determines its per- Technology, composition, its curing conditions, and formance after placement. An important Gaithersburg, MD 20899-8621 also by the mixing method and mixer con- measure of the quality is the homogeneity ditions used to process the concrete. This of the material after mixing. This paper paper gives an overview of the various will review mixing methods in regards to [email protected] types of mixing methods and concrete the quality of the concrete produced. mixers commercially available used by the Some procedures used to determine the ef- concrete industry. There are two main fectiveness of the mixing will be exam- types of mixers used: batch mixers and ined. continuous mixers. Batch mixers are the most common. To determine the mixing Key words: concrete mixers; mixer effi- method best suited for a specific applica- ciency. tion, factors to be considered include: loca- tion of the construction site (distance Accepted: August 30, 2000 from the batching plant), the amount of concrete needed, the construction sched- Available online: http://www.nist.gov/jres 1. -
Field Energy Performance of an Insulating Concrete Form (ICF) Wall
Research Report No. IRC-RR 326 Field Energy Performance of an Insulating Concrete Form (ICF) Wall W. Maref, M. M. Armstrong, H. Saber, M. Rousseau, G. Ganapathy, M. Nicholls and M.C. Swinton March 2012 Acknowledgements The authors wish to thank Mr. Silvio Plescia at the Canada Mortgage and Housing Corporation (CMHC) and Mr. Anil Parekh at Natural Resources Canada (NRCan) for contributing funding for this project and NRC for providing the funding to enable researchers to build, operate and maintain a state-of-the-art Field Exposure of Walls facility. Our thanks are also extended to Ross Monsour at Ready Mix Concrete Association of Ontario (RMCAO) for his contribution in providing the test specimens. Disclaimer This Project was partially funded by Canada Mortgage and Housing Corporation (CMHC) under Part IX of the National Housing Act, however the analysis, Interpretations and recommendations expressed in this report are those exclusively offered by the National Research Council Canada, Institute for Research in Construction. CMHC assumes no liability for any damage, injury, expense or loss that may result from the use of this report, particularly, the extrapolation of the results to specific situations or buildings. ii Executive Summary The National Research Council of Canada‘s Institute for Research in Construction (NRC-IRC) in collaboration with Canada Mortgage and Housing Corporation (CMHC) and Natural Resources Canada (NRCan) evaluated the dynamic heat transmission characteristics through two identical Insulating Concrete Form (ICF) wall assemblies. The ICF specimens were provided by an industry partner – the Ready Mixed Concrete Association of Ontario (RCMAO). The walls were exposed to naturally occurring climate at the in the NRC-IRC Field Exposure of Walls (FEWF) test facility in Ottawa, Canada from 13-Oct-09 to 16-Sep-10. -
CRACK-RESISTANT CONCRETE MIX Pre-Blended, Fiber-Reinforced, Portland Cement and Sand Mix for 1½” Or Greater Depth
CRACK-RESISTANT CONCRETE MIX Pre-blended, fiber-reinforced, Portland cement and sand mix for 1½” or greater depth 1. PRODUCT NAME Coverage Tech-Mix® Crack-Resistant Concrete Mix • 60 lb. (27.2 kg) bag yields approximately 0.45 cu. ft. (12.7 L) of wet mortar. Coverage will vary based on waste and job site 2. MANUFACTURER conditions. Tech-Mix® is a registered trademark of TCC Materials 2025 Centre Pointe Blvd., Suite 300 5. INSTALLATION Mendota Heights, MN 55120 USA Preparation Phone: 1.651.688.9116 Read all directions before starting work. Stake out the planned Web: techmixpro.com area and remove sod or soil to the desired depth. Nail and stake forms securely in place. Tamp and compact the sub-base 3. PRODUCT DESCRIPTION until firm. Subgrade surface should be brought to a saturated Tech-Mix® Crack-Resistant Concrete Mix consists of a pre- surface dry (SSD) condition with potable water. All repair blended mixture of Portland cement, aggregates, air-entraining overlay surfaces must be sound and be clean of any admixtures, special synthetic reinforcing fibers, and other contaminants. Dampen adjoining concrete surfaces to SSD ingredients to reduce shrinkage cracks and improve impact condition with potable water. For increased bond to existing resistance. The special reinforcing fibers eliminate the need for concrete, a latex bonding additive such as Akona Concrete wire mesh in typical slab-on-grade applications. Use for Bonding Additive may be used. pouring concrete 1½ in. (38 mm) thick or greater. It is also used for building or repairing steps, walks, and floors. Note: It is the responsibility of the installer/applicator to ensure the suitability of the product for its intended use. -
Concrete Construction
Concrete Construction Six (6) Continuing Education Hours Course #CV1216 Approved Continuing Education for Licensed Professional Engineers EZ-pdh.com Ezekiel Enterprises, LLC 301 Mission Dr. Unit 571 New Smyrna Beach, FL 32170 800-433-1487 [email protected] Concrete Construction Ezekiel Enterprises, LLC Course Description: The Concrete Construction course satisfies six (6) hours of professional development. The course is designed as a distance learning course that overviews essentially all aspects of concrete construction. Objectives: The primary objective of this course is to enable the student to understand all the essentials of concrete, this includes characteristics, mix design, formwork, joints, placement, finishing, and pre-cast. Grading: Students must achieve a minimum score of 70% on the online quiz to pass this course. The quiz may be taken as many times as necessary to successful pass and complete the course. A copy of the quiz questions are attached to last pages of this document. ii Concrete Construction Ezekiel Enterprises, LLC Table of Contents Concrete Construction 1. Concrete Characteristics ..................................... 1 2. Concrete Ingredients .......................................... 5 3. Concrete Mix Design ........................................ 12 4. Mixing Concrete ............................................... 24 5. Formwork ........................................................ 28 6. Reinforced Concrete ......................................... 48 7. Concrete Construction Joints ........................... -
Standard Specifications
SECTION 03300 CAST IN PLACE CONCRETE PART 1 GENERAL 1.1 DESCRIPTION A. Provide cast-in-place concrete as indicated on the Drawings and as specified and required. Work includes but is not limited to the following: 1. Furnishing all materials, labor, equipment, and supplies. 2. Mixing, placing, testing, finishing, and curing cast in place concrete. 1.2 QUALITY ASSURANCE A. Conform to applicable requirements of the International Building Code currently in force unless more stringent requirements are specified or shown on the Drawings. B. Perform work in accordance with ACI 301, ACI 304, ACI 305R, ACI 306R, ACI 318, ACI 347, and ACI 350. Maintain the latest copy of these and other appropriate documents referred to therein on the project site at all times. 1. Do not exceed 1.5-hrs. between batching and complete discharge of concrete. 2. Use mechanical high-frequency internal vibrators to compact concrete during and immediately after depositing. a. Provide sufficient standby equipment to ensure vibration will be continuous. b. Only use approved external vibrators for compacting concrete when concrete is inaccessible for adequate compaction by other means. c. Vibrate concrete to ensure no movement of reinforcing steel from its final position. 3. Acquire cement and aggregate from same source for all work. 4. Do not use excess grout or mortar to lubricate pipelines when pumping concrete. Also, do not discharge washout water into the forms. C. Unless otherwise indicated, use an independent testing agency hired by the Contractor and approved by the Engineer to perform all testing. Sampling shall be the Contractor’s responsibility. -
SECTION 03 11 19 PERMANENT FORMS—Insulating Concrete Forms Rev 7.20.17
SECTION 03 11 19 PERMANENT FORMS—Insulating Concrete Forms Rev 7.20.17 PART 1 GENERAL 1.01 SUMMARY A. Supply and installation of permanent insulating concrete forms as formwork, placement of steel reinforcement and placement of concrete into formwork. B. Comply with the requirements of Division 1 – General Requirements 1.02 RELATED SELECTIONS A. Drawings and general provisions to the Contract, including General and Supplementary Conditions and Division 1 Specification Sections, apply to this Section. B. Section 03 05 00 - Common Work Results for Concrete C. Section 03 20 00 - Concrete Reinforcing D. Section 03 21 00 - Steel Reinforcement E. Section 03 30 00 - Cast-In-Place Concrete F. Section 03 40 00 - Pre-cast Concrete G. Section 04 00 00 - Masonry H. Section 05 16 00 - Metal Framing Systems I. Section 06 00 00 - Wood, Plastics and Composites J. Section 07 11 00 - Damp proofing K. Section 07 13 00 - Sheet Waterproofing L. Section 07 14 00 - Fluid-Applied Waterproofing M. Section 07 24 00 - Exterior Insulation Finishing Systems N. Section 07 46 00 - Siding O. Section 07 60 00 - Flashing and Sheet Metal P. Section 08 00 00 - Openings Q. Section 09 20 00 - Plaster and Gypsum Board R. Section 09 22 00 - Plaster S. Section 09 70 00 - Wall Finishes 1.03 REFERENCES A. American Society for Testing and Materials (ASTM) 1. ASTM C 578 -- Standard Specification for Rigid, Cellular Polystyrene Thermal Insulation (ASTM C203, ASTM C303, ASTM C518, ASTM C272, ASTM D1621, ASTM D2126, ASTM D2863, ASTM E84, ASTM E96) 2. ASTM C 236 -- Steady State Thermal Performance of Building Assemblies 3. -
Sustainability of Residential Concrete
Research Series Report No. 112 The Pennsylvania Housing Research Center Sustainability of Residential Concrete Report prepared by: Pragati Singh Dr Andrew Scanlon December 2013 Pennsylvania Housing Research Center Penn State University 219 Sackett Building University Park, PA 16802 Telephone: (814) 865-2341 Facsimile: (814) 863-7304 E-mail: [email protected] Web Site: www.phrc.psu.edu Penn State is an equal opportunity, affirmative action employer, and is committed to providing employment opportunities to minorities, women, veterans, individuals with disabilities, and other protected groups. Nondiscrimination: http://guru.psu.edu/policies/AD85.html The Pennsylvania Housing Research Center (PHRC) exists to be of service to the housing community, especially in Pennsylvania. The PHRC conducts technical projects—research, development, demonstration, and technology transfer—with the support of numerous agencies, associations, companies and individuals. Neither the PHRC, nor any of its supporters, makes any warranty, expressed or implied, as to the accuracy or validity of the information contained in this report. Similarly, neither the PHRC, nor its supports, assumes any liability for the use of the information and procedures provided in this report. Opinions, when expressed, are those of the authors and do not necessarily reflect the views of either the PHRC or any one of its supports. It would be appreciated, however, if any errors, of fact or interpretation or otherwise, could be promptly brought to our attention. PHRC | 219 Sackett Building | University Park, PA 16802 i Sustainability of Residential Concrete Summary: Concrete is an established construction material known for its strength, durability and versatility. Its application in buildings consists of construction of foundations, structural frames, interior & exterior walls and slabs. -
Use of a Moisture Sensor for Monitoring the Effect of Mixing Procedure on Uniformity of Concrete Mixtures Kejin Wang1 and Jiong Hu2
Journal of Advanced Concrete Technology Vol. 3, No. 3, 371-384, October 2005 / Copyright © 2005 Japan Concrete Institute 371 Scientific paper Use of a Moisture Sensor for Monitoring the Effect of Mixing Procedure on Uniformity of Concrete Mixtures Kejin Wang1 and Jiong Hu2 Received 9 January 2005, accepted 18 June 2005 Abstract The present research is to explore a new approach to monitoring uniformity of concrete mixtures. A given concrete mix was subjected to three different mixing procedures. A moisture sensor was installed inside a pan mixer to monitor mois- ture content of the concrete mixtures during mixing. The concrete mixtures were considered as uniformly mixed when stable moisture content was detected by the moisture sensor. The concrete workability and strength were then evaluated, and the concrete’s microstructure (pore distributions and aggregate-paste interface) was examined. The preliminary re- sults indicated that the moisture sensor provided reliable test results describing moisture distribution in concrete mix- tures. The sensor readings well captured the subtle changes, such as the loading sequence of concrete materials, in the concrete mixing process. The material loading sequence, mixing time, and aggregate moisture condition had significant influences on the concrete workability, air void system, and strength. These research results provide researchers and engineers with insight into the control of concrete mixing quality and the optimization of mixing procedures in the lab and field. 1. Introduction Thorough mixing is essential to produce a homoge- neous mixture. A well-mixed mixture will permit all Concrete production consists of multiple and closely concrete components to distribute in its system uni- interrelated steps, including batching, mixing, consoli- formly and allow cementitious materials to hydrate uni- dation, finishing, and curing.