Successful Well Design and Remedial Cementing by Top Squeeze Method at Steamboat, NV, USA
Total Page:16
File Type:pdf, Size:1020Kb
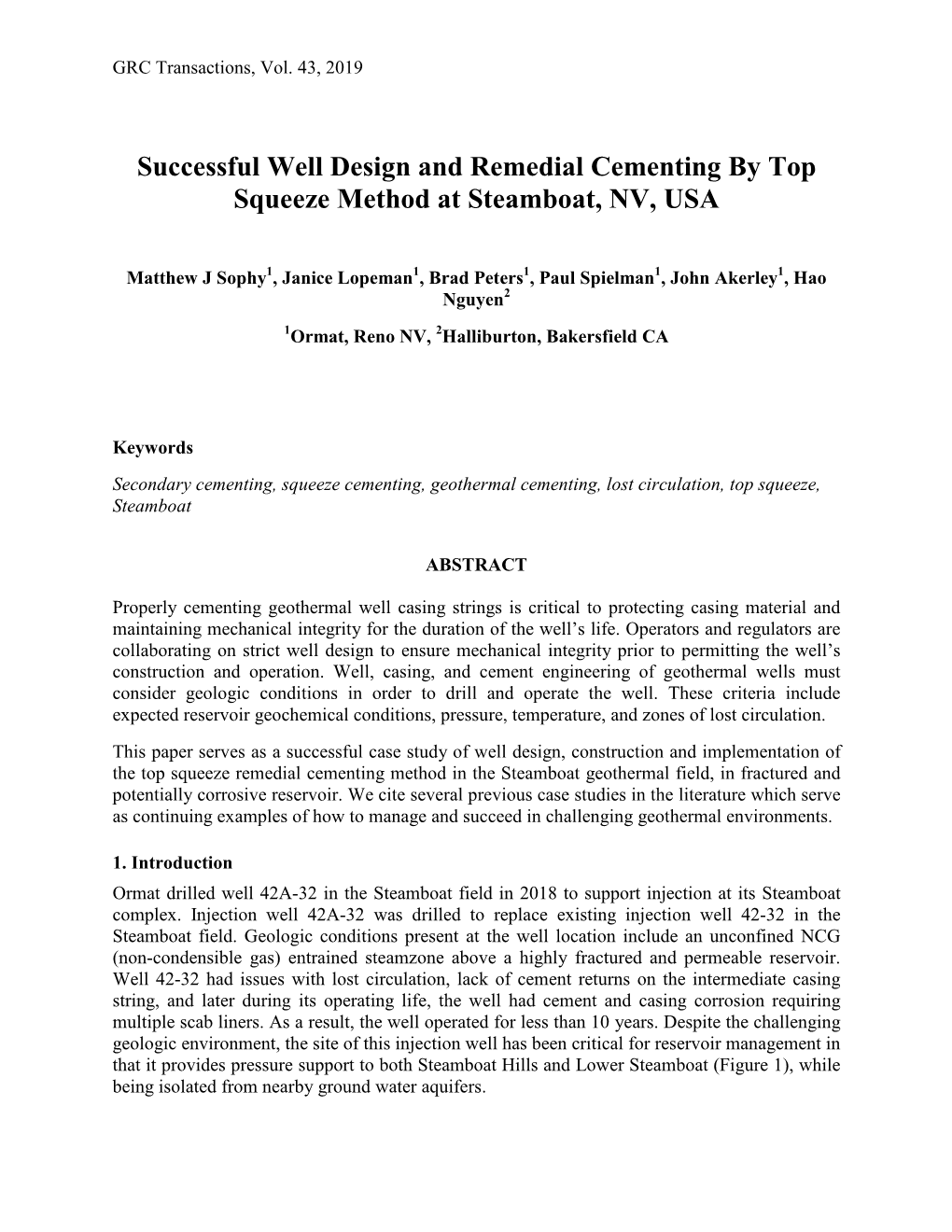
Load more
Recommended publications
-
بسمهللا الرحمن الرحيم Squeeze Cement Volume Estimation ﺣﺟم
بسم هللا الرحمن الرحيم Sudan University of Science and Technology College of Petroleum and Mining Engineering Department of Petroleum Engineering Project title: Squeeze Cement Volume Estimation (Case Study Hamra Field – Sudan) تقدير حجم اﻻسمنت المضغوط )دراسة حالة حقل هجليج النفطي -السودان( Submitted in Partial Fulfillment of the Requirements of the Degree of B.Sc. in Petroleum Engineering Prepared by: Ahmed Rashad Mustafa Awad Awadelkarim Elkheir Alamein Youssif Mohammed Seaed Abbass Mohamed Moataz Osman Alrayah Edries Supervised by: Eng. Mohamed Abd Alkhalig Joubara Bakheit November 2020 بسم هللا الرحمن الرحيم Sudan University of Science and Technology College of Petroleum and Mining Engineering Department of Petroleum Engineering Project title: Squeeze Cement Volume Estimation (Case Study Hamra Field – Sudan) تقدير حجم اﻻسمنت المضغوط )دراسة حالة حقل هجليج النفطي- السودان( This project is accepted by college petroleum engineering and technology department of petroleum engineering Prepared by: Ahmed Rashad Mustafa Awad Awadelkarim Elkheir Alamein Youssif Mohammed Seaed Abbass Mohamed Moataz Osman Alrayah Edries Project Supervisor: Eng. Mohamed Abd Alkhalig Joubara Signature…….……………………………………………………… Head of Department: Eng. Abdelwhab Mohammed Fadoul. Signature ……………………………………………….................... Dean of College: Dr. Elham Mohammed Mohammed Khair. Signature ……………………………………………....................... Date: / / 2020 اﻹستهﻻل I Dedication We would like to donate this unpretentious effort to Our Parents; Who have endless presence and for the never ending love and encouragement Our brothers and sisters; Who sustained us in our life and still Our teachers; Who lighted candle in our ways and provided us with light of knowledge Finally; our best friends; Our Classmates Researchers… II Acknowledgements Thanking to Allah before and after... First and foremost; the greatest thanking to our teachers for their continuous support.. -
Railroad Commission of Texas Oil Well Potential Test
RAILROAD COMMISSION OF TEXAS Form W-2 1701 N. Congress Status: Approved P.O. Box 12967 Date: 01/10/2018 Austin, Texas 78701-2967 Tracking No.: 179641 OIL WELL POTENTIAL TEST, COMPLETION OR RECOMPLETION REPORT, AND LOG OPERATOR INFORMATION Operator Name: PERISCOPE OPERATING LLC Operator No.: 653787 Operator Address: 115 E VIRGINIA ST SUITE 201 MCKINNEY, TX 75069-0000 WELL INFORMATION API No.: 42-371-38886 County: PECOS Well No.: 601 RRC District No.: 08 Lease Name: CUNNING WOLF UL Field Name: WOLFBONE (TREND AREA) RRC Lease No.: 43061 Field No.: 98359800 Location: Section: 6, Block: 23, Survey: UL, Abstract: Latitude: Longitude: This well is located 9 miles in a E direction from FORT STOCKTON, which is the nearest town in the county. FILING INFORMATION Purpose of filing: Reclass Producing to Injection Type of completion: Other/Recompletion Well Type: Active UIC Completion or Recompletion Date: 06/07/2017 Type of Permit Date Permit No. Permit to Drill, Plug Back, or Deepen 05/04/2012 732016 Rule 37 Exception Fluid Injection Permit O&G Waste Disposal Permit 15288 Other: COMPLETION INFORMATION Spud date: 05/17/2017 Date of first production after rig released: 06/07/2017 Date plug back, deepening, recompletion, or Date plug back, deepening, recompletion, or drilling operation commenced: 05/17/2017 drilling operation ended: 06/07/2017 Number of producing wells on this lease in Distance to nearest well in lease & this field (reservoir) including this well: 0 reservoir (ft.): 0.0 Total number of acres in lease: 640.00 Elevation (ft.): 2920 GL -
Pressure Control During Oil Well Drilling
Pressure Control During Oil Well Drilling Pål Skalle Download free books at Pål Skalle Pressure control 2 Download free eBooks at bookboon.com Pressure control 6th edition © 2015 Pål Skalle & bookboon.com ISBN 978-87-403-1140-2 3 Download free eBooks at bookboon.com Pressure control Contents Contents 1 Introduction 7 1.1 Scope of this book 7 1.2 The drilling process 7 1.3 Geological sediments 9 1.4 About Pressure Control in sedimentary rocks 10 1.5 Principle of barriers and safety aspects 13 2 Pressure in the sediments 14 2.1 Predictive models 14 2.2 Quantifying formation pressure 25 2.3 Fracture pressure 36 3 Well Control Equipment 39 3.1 BOP stack and associated equipment 41 3.2 Remote control of the BOP 46 3.3 Volumetric unstable well (kicking well) 47 www.sylvania.com We do not reinvent the wheel we reinvent light. Fascinating lighting offers an infinite spectrum of possibilities: Innovative technologies and new markets provide both opportunities and challenges. An environment in which your expertise is in high demand. Enjoy the supportive working atmosphere within our global group and benefit from international career paths. Implement sustainable ideas in close cooperation with other specialists and contribute to influencing our future. Come and join us in reinventing light every day. Light is OSRAM 4 Click on the ad to read more Download free eBooks at bookboon.com Pressure control Contents 3.4 Closing procedure during drilling operations 48 3.5 Well integrity during drilling operations 49 4 Standard killing methods 51 4.1 Surface and bottom pressure of a shut-in well 53 4.2 Hydraulic friction during killing 59 4.3 Killing by means of Driller’s Method 60 4.4 Engineer’s Method 65 4.5 Killing when unable to circulate from bottom 67 4.6 Pressure control during Underbalanced Drilling 69 4.7 Killing operations 79 360° 5 Modification of the standard killing method 81 5.1 Modification due to narrow pressure window 81 thinking 5.2 Killing with irregular drill string geometry360° 86 . -
Sandven, Sondre.Pdf
Faculty of Science and Technology MASTER’S THESIS Study program/ Specialization: Petroleum Engineering/ Spring semester, 2010 Drilling Open / Restricted access Writer: Sondre Sandven ………………………………………… (Writer’s signature) Faculty supervisor: Bernt S. Aadnøy External supervisor: Jofrid Marie Hegreberg Title of thesis: Evaluation of a method of placing cross-sectional barriers during permanent plugging of wells Credits (ECTS): 30 Key words: Pages: 61 Plug and abandonment, Squeeze cementing, + enclosure: 10 Slot recovery, Cement plugs Stavanger, 14th of June 2010 Date/year Abstract When oil and gas wells reach the end of their production life, they need to be permanently plugged and abandoned. The requirements for a permanent barrier state that it must cover the entire cross-section of the wellbore, including all annuli. This thesis evaluates a new method of establishing a cross-sectional barrier in areas with poor, non-sealing annular cement. The traditional method is to mill away the section with poor cement and set an open hole cement plug, but due to the ECD effect of milling fluids, this is not always desirable. In some formations on the Gullfaks field, the operational pressure window is too small for section milling. An alternative solution was therefore tried out on a well that needed plugging. This method, referred to as punch and squeeze, consisted of perforating the section of poorly cemented casing and squeezing cement into the annulus. In this thesis, the equipment and techniques used are presented and evaluated, along with general theory relevant to plugging and abandonment. On Gullfaks, two punch and squeeze techniques were used. In the first, cement was pumped through a packer plug and squeezed into the perforations. -
The Defining Series: Introductino to Well Completions
THE DEFINING SERIES Introduction to Well Completions Rick von Flatern Senior Editor Once a well has been drilled to total depth (TD), evaluated, cased and that the cement sheath between the casing and the borehole wall is without cemented, engineers complete it by inserting equipment, designed to opti- flaws (below left). If gaps exist, engineers remedy the problem by injecting mize production, into the hole. The driver behind every well completion cement through holes made in the casing at the appropriate depths. This is strategy, whether for a complex or basic well, is to recover, at a reasonable referred to as a cement squeeze job. cost, as large a percentage of the original oil in place (OOIP) as possible. Engineers then perforate through the casing and cement sheath into The decision to case and cement a well for production or plug and aban- sections of the formation where FE analysis indicates conditions are favor- don it as a dry hole relies heavily on formation evaluation (FE) using open- able for hydrocarbon flow. Perforations are holes made in the casing, usually hole logs. For the purposes of this article, completion refers to all operations using small, shaped charges fired from perforating guns. The guns may be following the placement of cement behind the production casing, which is lowered into the hole on wireline, tubing or coiled tubing. performed after FE. Often, these operations leave debris in the well and in the perforations Once FE log analysis indicates the existence and depth of formations themselves, which may hamper the flow of formation fluids into the bore- likely to produce commercial volumes of hydrocarbons, steel casing is run in hole. -
Mechanical Integrity Testing Workshop Elwood Vogel, Brian Pfeiff Technical Advisor’S Halliburton Oklahoma City, OK Sept 15 Th , 2019 Safety Moment!
Mechanical Integrity Testing Workshop Elwood Vogel, Brian Pfeiff Technical Advisor’s Halliburton Oklahoma City, OK Sept 15 th , 2019 Safety Moment! • With wild swings in Temperatures about to start happening this time of year. • Keep your tire pressure within the recommended range for your vehicle. Agenda • Introduction to Open Hole Logging • Primary Cementing 101 • Interpreting Cement Evaluation Tools • Remedial Cementing 101 • Casing Inspection 101 • New Technologies Introduction to Open Hole Logging Electric Well Logging • The practice of making a detailed record of the geologic formations penetrated by a borehole. • Usually Continuous but can be Stationary • Includes Testing and Sampling Services Open Hole Logs, What Information Do We Want To get. Everything! What we usually get! Traditional Rock - Shale Model (with Hydrocarbons) Rock Effective Matrix Shale Porosity Volume of Volume of Hydrocarbons Rock Matrix Volume Volume of of Shale Water Volume Total = V RM + V SH + V W + V HC Open Hole Borehole Conditions Gamma Ray Rock Matrix Shale Gamma Ray Detection • Passive Detection • Geiger-Mueller Detectors • Scintillation Detectors • Detect Naturally Occurring Gamma Ray GR Environmental Corrections • Corrections • Borehole Diameter • Mud Weight • Washout • Standoff • Tool Position Gamma Ray Porosity Volume of Volume of Water Hydrocarbons Neutron Apparent Porosity Measures Hydrogen Index Epithermal Thermal Gamma Ray of Capture Specific Porosity Equations Based on Test Pits at U of H Density Apparent Porosity • Measures Electron Density -
Oil and Gas Well Drilling and Servicing Etool
U.S. Department of Labor Occupational Safety & Health Administration www.osha.gov [skip navigational links] Search Advanced Search | A-Z Index Home General Safety Site Preparation Drilling Well Completion Servicing Plug and Abandon the Well Illustrated Glossary Drilling Rig Components Click on the name below or a number on the graphic to see a definition and a more detailed photo of the object. 1. Crown Block and Water Table 2. Catline Boom and Hoist Line 3. Drilling Line 4. Monkeyboard 5. Traveling Block 6. Top Drive 7. Mast 8. Drill Pipe 9. Doghouse 10. Blowout Preventer 11. Water Tank 12. Electric Cable Tray 13. Engine Generator Sets 14. Fuel Tank 15. Electrical Control House 16. Mud Pumps 17. Bulk Mud Component Tanks 18. Mud Tanks (Pits) 19. Reserve Pit 20. Mud-Gas Separator 21. Shale Shakers 22. Choke Manifold 23. Pipe Ramp 24. Pipe Racks 25. Accumulator Additional rig components not illustrated at right. 26. Annulus 27. Brake 28. Casing Head 29. Cathead 30. Catwalk 31. Cellar 32. Conductor Pipe Equipment used in drilling 33. Degasser 34. Desander 48. Ram BOP 35. Desilter 49. Rathole 36. Drawworks 50. Rotary Hose 37. Drill Bit 51. Rotary Table 38. Drill Collars 52. Slips 39. Driller's Console 53. Spinning chain 40. Elevators 54. Stairways 41. Hoisting Line 55. Standpipe 42. Hook 56. Surface Casing 43. Kelly 57. Substructure 44. Kelly Bushing 58. Swivel 45. Kelly Spinner 59. Tongs 46. Mousehole 60. Walkways 47. Mud Return Line 61. Weight Indicator eTool Home | Site Preparation | Drilling | Well Completion | Servicing | Plug & Abandon Well General Safety | Additional References | Viewing/Printing Instructions | Credits | JSA Safety and Health Topic | Site Map | Illustrated Glossary | Glossary of Terms www.osha.gov www.dol.gov Back to Top Contact Us | Freedom of Information Act | Information Quality | Customer Survey Privacy and Security Statement | Disclaimers Occupational Safety & Health Administration 200 Constitution Avenue, NW Washington, DC 20210 U.S. -
Overview of Port Au Port #1 ST #3 Bullhead Acid Squeeze
Overview of Port au Port #1 ST #3 Bullhead Acid Squeeze Rev. 0 Submitted by Enegi Oil Inc. 36, Quidi Vidi Road St. John’s Newfoundland A1A 1C1 May 2014 This document is confidential. Neither the whole nor any part of this document may be disclosed to any third party without the prior written consent of Enegi Oil Inc. All rights reserved. Neither the whole nor any part of this document may be reproduced, stored in any retrieval system or transmitted in any form or by any means (electronic, mechanical, reprographic, recording or otherwise) without the prior written consent of Enegi Oil Inc, the copyright owner. Report Approval Cover Sheet Report Title: Overview of Port au Port #1 ST #3 Bullhead Acid Squeeze Project Name: Garden Hill South Approval Record Rev. No. Date Prepared Reviewed Approved 0 6th May 2014 A. Pegram D. Lau A. Minty This document is confidential. Neither the whole nor any part of this document may be disclosed to any third party without the prior written consent of Enegi Oil Inc. All rights reserved. Neither the whole nor any part of this document may be reproduced, stored in any retrieval system or transmitted in any form or by any means (electronic, mechanical, reprographic, recording or otherwise) without the prior written consent of Enegi Oil Inc, the copyright owner. Report Record of Revision Report Title: Overview of Port au Port #1 ST #3 Bullhead Acid Squeeze Project Name: Garden Hill South Record of Revision Rev. No. Date Revision Details 0 May 2014 Original. Overview of Port au Port #1 ST #3 Bullhead Acid Squeeze Rev. -
View Transcript
PETROLEUM INDUSTRY ORAL HISTORY PROJECT TRANSCRIPT INTERVIEWEE: Paul Evans INTERVIEWER: Aubrey Kerr DATE: December 4, 1992 Side 1 - 46:40 AK: The today is December the 4, 1992 and I am in the home of Paul and Sarah Beth Evans. And this is Apartment 405 in the Renfrew house up in Rideau Heights. I guess we could call it Rideau Heights. Yeah, right. And I'm very pleased to be here today, Paul because you have a long history of involvement in the oil patch, having come up here from the States. So, I'd like to get from you the year you were born and where, and a little bit about your parents. PE: Thank you Aubrey. I was born in Galesburg, Illinois on June 13th, 1915. And my parents moved from Illinois to Texas when I was only one year old, and they settled it Ranger, Texas. And my father worked in the oil business for about a year, year and a half, and then they moved to Fort Worth. I was raised, in my childhood in Fort Worth and later went through, graduated from high school and went to Texas A&M in 1933 and graduated in Petroleum Engineering in 1937. AK: Okay, that's a good start. Just let's go back to your dad. For whom did he work? And what was his job in the oil business? PE: My father worked primarily in the sales industry. He was a truck salesman, worked for White and Mack Truck Company during all of my school time and he was still working with them when I went to college. -
Welllock® Resin Provided Well Integrity to Withstand Forty-Two Fracturing Stages
A CASE STUDY: Well remediation WellLock® Resin provided well integrity to withstand forty-two fracturing stages. CHALLENGE Prior to a fracturing operation on a well in the Utica Shale basin in Ohio, an operator conducted a pressure test and found indica- tions of a casing leak. A casing patch was installed, but with a 5,000 psi pressure test the well continued to lose pressure at a rate of 2,000 psi in 15 minutes. The pressure continued to leak off until stabilizing just below 1,750 psi. With the inner diameter already narrowed by the casing patch, the operator wanted to avoid running a second one; a second casing patch would further narrow the inner diameter, increasing completion operations expenses by requiring the use of slim-hole plugs. A squeeze job using cement would not further narrow the inner diameter, but the results of the injection test indicated a minimum Monroe injection rate. In this situation, cement would be prone to County providing nothing more than a skin effect or simply bridging off. As a result, remediation with cement was not an option. Halliburton recommended the WellLock® resin system. Not only is WellLock resin proven to penetrate and seal off even micron-sized leaks, it is field-proven for mill out when left behind in the casing. The operator approved use of WellLock resin, convinced by data that it would not further restrict the inner diameter of the well (enabling use of standard plugs for the completion operation) and that the low yield point of the resin would allow it to flow deep into the crack yet resist the flow dynamics of the leak. -
Dr. Ingraffea Gives You Permission to Use These Slides with the Proviso That You Must Retain All Attributions on All Slides
Dr. Ingraffea gives you permission to use these slides with the proviso that you must retain all attributions on all slides. 1 The Science of Shale Gas: The Latest Evidence on Leaky Wells, Methane Emissions, and Implications for Policy A. R. Ingraffea Dwight C. Baum Professor Cornell University and Physicians, Scientists, and Engineers for Healthy Energy, Inc. Youngstown State University March 26, 2014 2 From the Supporters of Increased Development of Shale Gas/NGL/Oil “It is just business as usual, fracking has been around for 60 years, no new concerns.” (My Nov. 2012 Talk) “The methane in private water wells was always there: we did not do it. With 4 or more layers of steel casing and cement barriers, our wells do not leak.” “Methane is a clean fossil fuel. Methane is a cleaner fossil fuel. Methane is the bridge fuel to a green renewable energy future.” 3 Shale Gas/Oil Production Must Use Clustered, Multi-Well Pads and High-Volume Long Laterals Because GEOLOGY RULES: Permeability, Depth, Thickness, Thermal Maturity, Total Organic Carbon pad ~ 2 miles ~ 1 mile > 4000 ft Laterals ~ 500 ft > 5000 ft Not to scale 4 Why NOT More Shale Gas/NGL/Oil? “The methane in private water wells was always there: we did not do it. With 4 or more layers of steel casing and cement barriers, our wells do not leak.” Part 1 of My Talk: “Leaking wells” is a chronic, ubiquitous, well-understood problem. It is unresponsive to “tough regulation”. It is causing contamination of drinking water at an increasing rate. 5 Source of Methane Migration into Groundwater? Hundreds of Private Water Wells Contaminated in PA “There are at least three possible mechanisms for fluid migration into the shallow drinking-water aquifers that could help explain the increased methane concentrations we observed near gas wells…A second mechanism is leaky gas-well casings…Such leaks could occur at hundreds of meters underground, with methane passing laterally and vertically through fracture systems.” From Osborn et al. -
Well Stimulation Effects on Annular Seal of Production Casing in Ocs Oil and Gas
FINAL REPORT: WELL STIMULATION EFFECTS ON ANNULAR SEAL OF PRODUCTION CASING IN OCS OIL AND GAS OPERATIONS Prepared for: BSEE 9/28/2015 Contract Number: E14PC00037 Prepared By: Paul Sonnier Position: Research and Development Manager, Lab Manager CSI TECHNOLOGIES • 2202 Oil Center Court • Houston, Texas 77073 • 281.784.7990 • www.csi-tech.net CTMS-TM-PM-03 (2.1) 2 | P a g e CONTENTS 1 Acronyms and Abbreviations ...................................................................................................................................... 8 2 Introduction .............................................................................................................................................................. 10 2.1 Objective ............................................................................................................................................................ 10 2.2 Conclusions and Recommendations .................................................................................................................. 10 2.2.1 Literature Review ........................................................................................................................................ 10 2.2.2 Failure modes ............................................................................................................................................. 11 2.2.3 Small Scale Physical Modeling .................................................................................................................... 12 2.2.4 Large scale modeling