Geotechnical Properties and Flow Behavior of Coal Refuse
Total Page:16
File Type:pdf, Size:1020Kb
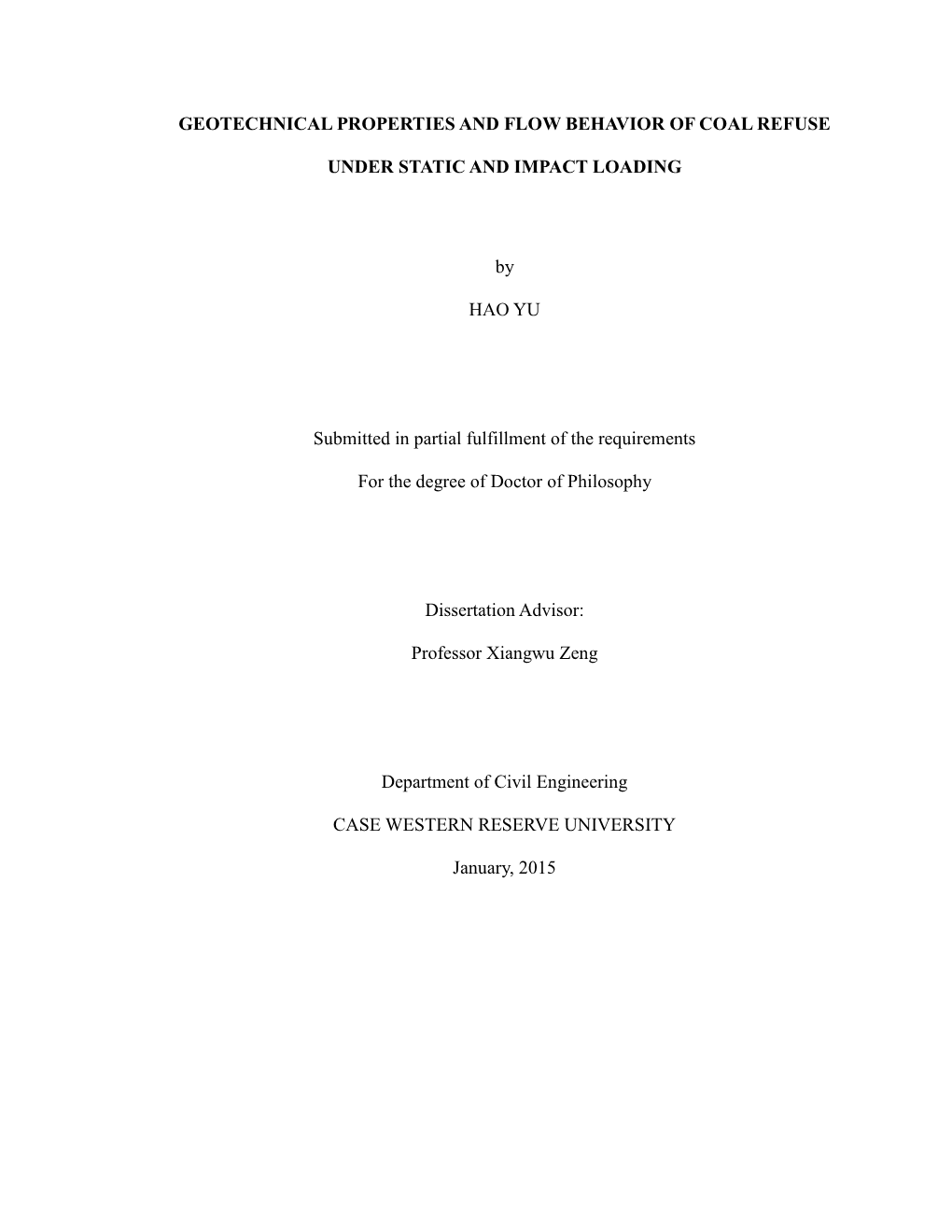
Load more
Recommended publications
-
Investigation of the Gasification Performance of Lignite Feedstock and the Injection Design of an E-Gas Like Gasifier
Proceedings of the 29th Annual International Pittsburgh Coal Conference, Pittsburgh, PA, USA, October 15 - 18, 2012 Investigation of the Gasification Performance of Lignite Feedstock and the Injection Design of an E-Gas like Gasifier Yan-Tsan Luan and Yau-Pin Chyou* Ting Wang Chemistry Division Energy Conversion & Conservation Center Institute of Nuclear Energy Research University of New Orleans Atomic Energy Council New Orleans, Louisiana 70148, USA Longtan, Taoyuan, Taiwan (R.O.C.) ABSTRACT CO2 capture among the four reference power plants: coal In the last three years, the Institute of Nuclear Energy combustion, integrated gasification combine cycle (IGCC), Research (INER) has been developing the E-GAS gasification oxy-combustion, and natural-gas combustion. In the second numerical model and analyzing the gasification performance column, coal pre-combustion carbon capture has the lowest by conducting several parametric studies. A preliminary cost of CO2 avoided, which makes it more competitive and a numerical model considering coal particles tracking, two-step welcoming choice when it comes to low-carbon electricity volatiles thermal cracking, and nine chemical reactions has generation. With its inherence of low emissions and cost been established. In last year’s results, the single lateral including CCS, IGCC has the potential to replace traditional injector design in the 2nd stage of E-GAS gasifier is found PC plants. Therefore, conducting research in coal gasification non-ideal for the gasificaiton process. Therefore, one of the and CO2 capture technology to improve its availability, objectives in this study is to modify the 2nd stage injection increase its efficiency, and reduce the cost is essential for and investigate its effect on gasification performance. -
Solutions for Energy Crisis in Pakistan I
Solutions for Energy Crisis in Pakistan i ii Solutions for Energy Crisis in Pakistan Solutions for Energy Crisis in Pakistan iii ACKNOWLEDGEMENTS This volume is based on papers presented at the two-day national conference on the topical and vital theme of Solutions for Energy Crisis in Pakistan held on May 15-16, 2013 at Islamabad Hotel, Islamabad. The Conference was jointly organised by the Islamabad Policy Research Institute (IPRI) and the Hanns Seidel Foundation, (HSF) Islamabad. The organisers of the Conference are especially thankful to Mr. Kristof W. Duwaerts, Country Representative, HSF, Islamabad, for his co-operation and sharing the financial expense of the Conference. For the papers presented in this volume, we are grateful to all participants, as well as the chairpersons of the different sessions, who took time out from their busy schedules to preside over the proceedings. We are also thankful to the scholars, students and professionals who accepted our invitation to participate in the Conference. All members of IPRI staff — Amjad Saleem, Shazad Ahmad, Noreen Hameed, Shazia Khurshid, and Muhammad Iqbal — worked as a team to make this Conference a success. Saira Rehman, Assistant Editor, IPRI did well as stage secretary. All efforts were made to make the Conference as productive and result oriented as possible. However, if there were areas left wanting in some respect the Conference management owns responsibility for that. iv Solutions for Energy Crisis in Pakistan ACRONYMS ADB Asian Development Bank Bcf Billion Cubic Feet BCMA -
Chapter 1. Overview: Coal Ash Beneficial Use and Mine Land Reclamation
CHAPTER 1. OVERVIEW: COAL ASH BENEFICIAL USE AND MINE LAND RECLAMATION Alfred D. Dalberto, Barry E. Scheetz, Roger J. Hornberger, Timothy C. Kania, Michael J. Menghini, Scott E. Walters 1.1 INTRODUCTION—PENNSYLVANIA’S ABANDONED MINE LAND PROBLEM Since commercial coal mining began in Pennsylvania prior to 1800 (Dodge & Edwards, 2003), the Commonwealth’s miners have extracted approximately 16.3 billion tons of coal from the Anthracite and Bituminous Coal Fields combined (PA DEP, 2002). The efforts of Pennsylvania’s miners helped fuel the nation’s industrial revolution and fed families for generations. However, the other legacy of the state’s rich mining heritage is an unparalleled abandoned mine land (AML) problem. Prior to the enactment of the federal Surface Mining Control and Reclamation Act (SMCRA) in August 1977, laws and regulations governing surface mining and the surface effects of underground mining, were largely ineffective in achieving reclamation of mined lands. SCMRA, which applies to all surface mining conducted after August 1977, requires complete reclamation of surface mine-affected lands and requires the posting of financial assurances, usually in the form of bonds, to ensure reclamation. While present-day mine sites are occasionally abandoned, the Pennsylvania Department of Environmental Protection (DEP) has well-established programs in place to reclaim those sites. However, much of the vast AML problem from the pre-1977 mining remains. There are more than 5000 abandoned, unreclaimed mine problem areas encompassing more than 189,000 acres in Pennsylvania, according to the DEP Bureau of Abandoned Mine Reclamation (BAMR). BAMR’s inventory of abandoned mine sites also identifies over 820 abandoned coal refuse piles. -
Voice 2012 01Febmar.Pdf
AppalachianThe February / March 2012 VOICE Forty years ago, a wave of coal slurry swept away Then communities along Buffalo Creek, killing 125. Some problems from our past have improved — others & Now seem stuck in time. Have we learned our lesson? ALSO INSIDE: The Habits of Hibernating Bears • Georgia’s Historic Blood Mountain • Standing Up for Clean Water TheAppalachian VOICE Yesterday and Today: Defending the Clean Water Act A publication of A Note From Our Executive Director By Jamie Goodman AppalachianVoices TOP: Councilmen from Cleveland, Forty years ago, it took a Ohio, examine a white cloth that came 191 Howard Street • Boone, NC 28607 There’s a common saying in Appalachia: what we do to the land, 1-877-APP-VOICE flaming river to spur our nation up dripping with oil after being dipped we do to the people. www.AppalachianVoices.org to protect its waterways. in the Cuyahoga River in 1964. The [email protected] What the coal industry is doing to the citizens in our region is river notoriously caught fire in June The river that played a promi- unforgivable. In the last several years, 21 peer-reviewed studies have 1969, bringing it national attention nent role in the creation of the EDITOR ....................................................... Jamie Goodman confirmed the worst of our fears -- that mountaintop removal coal min- and leading to renewed efforts toward MANAGING EDITOR ........................................... Brian Sewell Clean Water Act and the Envi- ing is destroying not only the land, but also the people of Appalachia. improving water quality (Photo ASSOCIATE EDITOR ............................................Molly Moore ronmental Protection Agency is by Jerry Horton). -
Endangered Species Act Section 7 Consultation Final Programmatic
Endangered Species Act Section 7 Consultation Final Programmatic Biological Opinion and Conference Opinion on the United States Department of the Interior Office of Surface Mining Reclamation and Enforcement’s Surface Mining Control and Reclamation Act Title V Regulatory Program U.S. Fish and Wildlife Service Ecological Services Program Division of Environmental Review Falls Church, Virginia October 16, 2020 Table of Contents 1 Introduction .......................................................................................................................3 2 Consultation History .........................................................................................................4 3 Background .......................................................................................................................5 4 Description of the Action ...................................................................................................7 The Mining Process .............................................................................................................. 8 4.1.1 Exploration ........................................................................................................................ 8 4.1.2 Erosion and Sedimentation Controls .................................................................................. 9 4.1.3 Clearing and Grubbing ....................................................................................................... 9 4.1.4 Excavation of Overburden and Coal ................................................................................ -
COAL CONFERENCE University of Pittsburgh · Swanson School of Engineering ABSTRACTS BOOKLET
Thirty-Fifth Annual INTERNATIONAL PITTSBURGH COAL CONFERENCE University of Pittsburgh · Swanson School of Engineering ABSTRACTS BOOKLET Clean Coal-based Energy/Fuels and the Environment October 15-18, 2018 New Century Grand Hotel Xuzhou Hosted by: The conference acknowledges the support of Co-hosted by: K. C. Wong Education Foundation, Hong Kong A NOTE TO THE READER This Abstracts Booklet is prepared solely as a convenient reference for the Conference participants. Abstracts are arranged in a numerical order of the oral and poster sessions as published in the Final Conference Program. In order to facilitate the task for the reader to locate a specific abstract in a given session, each paper is given two numbers: the first designates the session number and the second represents the paper number in that session. For example, Paper No. 25.1 is the first paper to be presented in the Oral Session #25. Similarly, Paper No. P3.1 is the first paper to appear in the Poster Session #3. It should be cautioned that this Abstracts Booklet is prepared based on the original abstracts that were submitted, unless the author noted an abstract change. The contents of the Booklet do not reflect late changes made by the authors for their presentations at the Conference. The reader should consult the Final Conference Program for any such changes. Furthermore, updated and detailed full manuscripts, published in the Conference Proceedings, will be sent to all registered participants following the Conference. On behalf of the Thirty-Fifth Annual International Pittsburgh Coal Conference, we wish to express our sincere appreciation and gratitude to Ms. -
Recommendation of the Council on Coal and the Environment 8
Recommendation of the Council on Coal and the Environment 8 OECD Legal Instruments This document is published under the responsibility of the Secretary-General of the OECD. It reproduces an OECD Legal Instrument and may contain additional material. The opinions expressed and arguments employed in the additional material do not necessarily reflect the official views of OECD Member countries. This document, as well as any data and any map included herein, are without prejudice to the status of or sovereignty over any territory, to the delimitation of international frontiers and boundaries and to the name of any territory, city or area. For access to the official and upto-date texts of OECD Legal Instruments, as well as other related information, please consult the Compendium of OECD Legal Instruments at http://legalinstruments.oecd.org. Please cite this document as: OECD, Recommendation of the Council on Coal and the Environment, OECD/LEGAL/0173 Series: OECD Legal Instruments © OECD 2021 This document is provided free of charge. It may be reproduced and distributed free of charge without requiring any further permissions, as long as it is not altered in any way. It may not be sold. This document is available in the two OECD official languages (English and French). It may be translated into other languages, as long as the translation is labelled "unofficial translation" and includes the following disclaimer: "This translation has been prepared by [NAME OF TRANSLATION AUTHOR] for informational purpose only and its accuracy cannot be guaranteed by the OECD. The only official versions are the English and French texts available on the OECD website http://legalinstruments.oecd.org" _____________________________________________________________________________________________OECD/LEGAL/0173 3 Background Information The Recommendation on Coal and the Environment was adopted by the OECD Council on 8 May 1979 on the proposal of the Environment Committee (now called Environment Policy Committee). -
Coal Resources of the United States, January 1, 1974
Coal Resources of the - United States, " January 1,1 * GEOLOGICAL SURVEY BULLETIN 1412 > Coal Resources of the ' - % United States,y January 1,1974 By PAUL AVERITT GEOLOGICAL SURVEY BULLETIN 1412 <- /4 summary of information concerning the quantity and distribution of coal in the United States. Supersedes Bulletin 1275 UNITED STATES GOVERNMENT PRINTING OFFICE, WASHINGTON : 1975 UNITED STATES DEPARTMENT OF THE INTERIOR GEOLOGICAL SURVEY V. E. McKelvey, Director Library of Congress Cataloging in Publication Data Averitt, Paul, 1908- Coal resources of the United States, January 1, 1974. (Geological Survey Bulletin 1412) "Supersedes Bulletin 1275." Bibliography: p. Includes index. Supt.ofDocs.no.: 119.3:1412 1. Coal-United States. I. Title. II. Series: United States Geological Survey Bulletin 1412. QE75.B9 No. 1412 [TN805.A5] 557.3'08s [553'.2'0973] 75-619188 For sale by the Superintendent of Documents, U. S. Government Printing Office Washington, D. C. 20402 Stock Number 024-001-02703-8 CONTENTS Page Abstract........................................................................................................................... 1 Introduction.................................................................................................................... 2 Conversion to metric system ................................................................................... 4 Acknowledgments........................................................................................................... 4 Distribution of coal in the United States...................................................................... -
Evaluation of Time Rate of Consolidation and Undrained Shear Strength of Hydraulically Placed Fine Coal Refuse
University of Tennessee, Knoxville TRACE: Tennessee Research and Creative Exchange Doctoral Dissertations Graduate School 5-2019 EVALUATION OF TIME RATE OF CONSOLIDATION AND UNDRAINED SHEAR STRENGTH OF HYDRAULICALLY PLACED FINE COAL REFUSE Cyrus Jedari Sefidgari University of Tennessee, [email protected] Follow this and additional works at: https://trace.tennessee.edu/utk_graddiss Recommended Citation Jedari Sefidgari, Cyrus, "EVALUATION OF TIME RATE OF CONSOLIDATION AND UNDRAINED SHEAR STRENGTH OF HYDRAULICALLY PLACED FINE COAL REFUSE. " PhD diss., University of Tennessee, 2019. https://trace.tennessee.edu/utk_graddiss/5408 This Dissertation is brought to you for free and open access by the Graduate School at TRACE: Tennessee Research and Creative Exchange. It has been accepted for inclusion in Doctoral Dissertations by an authorized administrator of TRACE: Tennessee Research and Creative Exchange. For more information, please contact [email protected]. To the Graduate Council: I am submitting herewith a dissertation written by Cyrus Jedari Sefidgari entitled "EVALUATION OF TIME RATE OF CONSOLIDATION AND UNDRAINED SHEAR STRENGTH OF HYDRAULICALLY PLACED FINE COAL REFUSE." I have examined the final electronic copy of this dissertation for form and content and recommend that it be accepted in partial fulfillment of the equirr ements for the degree of Doctor of Philosophy, with a major in Civil Engineering. Angelica M. Palomino, Eric C. Drumm, Major Professor We have read this dissertation and recommend its acceptance: Khalid A. Alshibli, John S. Schwartz Accepted for the Council: Dixie L. Thompson Vice Provost and Dean of the Graduate School (Original signatures are on file with official studentecor r ds.) EVALUATION OF TIME RATE OF CONSOLIDATION AND UNDRAINED SHEAR STRENGTH OF HYDRAULICALLY PLACED FINE COAL REFUSE A Dissertation Presented for the Doctor of Philosophy Degree The University of Tennessee, Knoxville Cyrus Jedari Sefidgari May 2019 Copyright © 2019 by Cyrus Jedari Sefidgari All rights reserved. -
Nittany Mineralogical Society Bulletin
THE SOCIETY FOR ORGANIC PETROLOGY NEWSLETTER Vol. 22, No. 2 June, 2005 ISSN 0743-3816 2005 Annual Meeting, September 11 - 14: Louisville, Kentucky Early registration discount ends July 31 Accommodation deadline is August 19 2005 TSOP Meeting September 11 - 14 Louisville, Kentucky, USA Early registration discount ends July 31 Accommodation deadline is August 19 - see page 10. Conference themes will include Planned schedule includes CO2 sequestration Sunday, September 11 coal utilization CO2 Sequestration Workshop (a.m.) coalbed methane Field Trip: Falls of the Ohio (p.m.) coal petrography Monday, September 12 organic geochemistry Technical Sessions Reception, Louisville Slugger Museum Tuesday, September 13 Technical Sessions Wednesday, September 14 Post-meeting coal mine field trip And mark your calendars now for the 23rd Annual TSOP Meeting Beijing, China September 15 - 22 , 2006 See page 19 The Society for Organic Petrology TSOP is a society for scientists and engineers involved with coal petrology, kerogen petrology, organic geochemistry and related disciplines. The Society organizes an annual technical meeting, other meetings, and field trips; sponsors research projects; provides funding for graduate students; and publishes a web site, this quarterly Newsletter, a membership directory, annual meeting program and abstracts, and special publications. Members may elect not to receive the printed Newsletter by marking their dues forms or by contacting the Editor. This choice may also be reversed at any time, or specific printed Newsletters may be requested. Members are eligible for discounted subscriptions to the Elsevier journals International Journal of Coal Geology and Review of Paleobotany and Palynology. Subscribe by checking the box on your dues form, or using the form at www.tsop.org. -
Environmental Protection Subtitle D: Mine Related Water Pollution Chapter I: Pollution Control Board
IPCB 35 ILLINOIS ADMINISTRATIVE CODE CH. I, SEC. 402 SUBTITLE D TITLE 35: ENVIRONMENTAL PROTECTION SUBTITLE D: MINE RELATED WATER POLLUTION CHAPTER I: POLLUTION CONTROL BOARD PART 402 DEFINITIONS Section 402.100 Terms Defined Elsewhere 402.101 Definitions 402.APPENDIX A References to Previous Rules AUTHORITY: Implementing Sections 12 and 13 and authorized by Section 27 of the Environmental Protection Act [415 ILCS 5]. SOURCE: Adopted at 4 Ill. Reg. 34, p. 164, effective August 7, 1980; codified at 5 Ill. Reg. 34, p. 8527; amended in R84-29 at 11 Ill. Reg. 12890, effective July 27, 1987; amended in R18-24 at 43 Ill. Reg.11580, effective September 25, 2019. Section 402.100 Terms Defined Elsewhere Unless otherwise stated or unless the context clearly indicates a different meaning, the definition of terms used in Subtitle D are the same as those found in the Illinois Environmental Protection Act [415 ILCS 5] (Act), 35 Ill. Adm. Code Subtitle C, Chapter I, and the Federal Water Pollution Control Act of 1972 (FWPCA) (33 USC 1251). (Source: Amended at 43 Ill. Reg. 11580, effective September 25, 2019) Section 402.101 Definitions For purposes of this Subtitle D, the following terms are defined: "Abandon": to transfer ownership of or to close down mining activities, a mine or mine refuse area with no intention by the operator to reopen the affected land. A mine or mine refuse area that has been inoperative for one year is rebuttably presumed abandoned. "Acid or Ferruginous Mine Drainage": mine drainage that, before any treatment, has a pH of less than 6.0 or a total iron concentration greater than 10 mg/L. -
FINAL TECHNICAL REPORT January 1, 2012 Through December 30, 2014
FINAL TECHNICAL REPORT January 1, 2012 through December 30, 2014 Project Title: INFLUENCE OF MACERAL AND MINERAL COMPOSITION ON OHD PROCESSING OF ILLINOIS COAL ICCI Project Number: 12/7A-3 Principal Investigator: Sue M. Rimmer, Southern Illinois University Carbondale Other Investigators: Ken B. Anderson, Southern Illinois University Carbondale John C. Crelling, Southern Illinois University Carbondale Project Manager: Francois Botha, ICCI ABSTRACT Oxidative Hydrothermal Dissolution (OHD) is a coal conversion technology that solubilizes coal by mild oxidation, using molecular oxygen as the oxidant and hydrothermal water (liquid water at high temperature and pressure) as both reaction medium and solvent, producing low-molecular weight organic acids, which are widely used as chemical feedstocks. The primary objectives of this proposal were to determine how maceral composition and rank influence the OHD process, and to determine if OHD could be applied successfully to high-ash (clay-rich) waste products, including slurry pond deposits and beneficiation plant wastes. Our results show that OHD of all Illinois Basin lithotypes studied produced the same suite of compounds. Examination of residues from pulse OHD runs (different timed oxidant pulses) showed that OHD preferentially attacks the vitrinites and liptinites over the inertinites. Collotelinite ("band" vitrinite) develops reaction rims relatively quickly, whereas collodetrinite ("matrix" vitrinite) develops vacuoles before the collotelinite. Liptinites ultimately develop reaction rims and loose fluorescence. Fusinite shows only minimal alteration. OHD of maceral concentrates showed that vitrinite and inertinite macerals produced products similar to those seen for the lithotypes. However, liptinite maceral concentrates (sporinite and cutinite) produced very different compounds including long-chain aliphatic acids, in addition to some of those seen previously in the other lithotypes.