Quality Procedure (QP) 158 (Process Controle
Total Page:16
File Type:pdf, Size:1020Kb
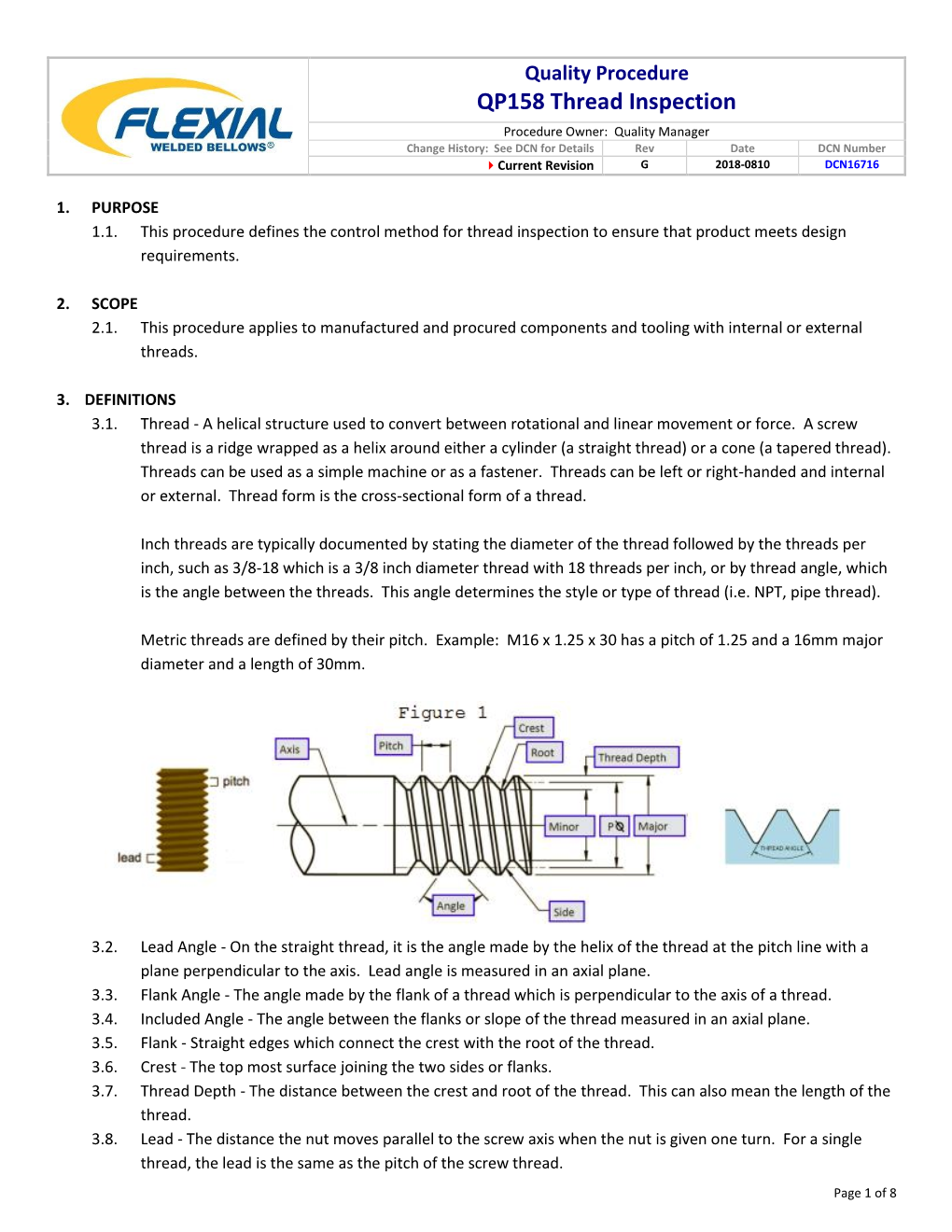
Load more
Recommended publications
-
PLUMBING DICTIONARY Sixth Edition
as to produce smooth threads. 2. An oil or oily preparation used as a cutting fluid espe cially a water-soluble oil (such as a mineral oil containing- a fatty oil) Cut Grooving (cut groov-ing) the process of machining away material, providing a groove into a pipe to allow for a mechani cal coupling to be installed.This process was invented by Victau - lic Corp. in 1925. Cut Grooving is designed for stanard weight- ceives or heavier wall thickness pipe. tetrafluoroethylene (tet-ra-- theseveral lower variouslyterminal, whichshaped re or decalescensecryolite (de-ca-les-cen- ming and flood consisting(cry-o-lite) of sodium-alumi earthfluo-ro-eth-yl-ene) by alternately dam a colorless, thegrooved vapors tools. from 4. anonpressure tool used by se) a decrease in temperaturea mineral nonflammable gas used in mak- metalworkers to shape material thatnum occurs fluoride. while Usedheating for soldermet- ing a stream. See STANK. or the pressure sterilizers, and - spannering heat resistantwrench and(span-ner acid re - conductsto a desired the form vapors. 5. a tooldirectly used al ingthrough copper a rangeand inalloys which when a mixed with phosphoric acid.- wrench)sistant plastics 1. one ofsuch various as teflon. tools to setthe theouter teeth air. of Sometimesaatmosphere circular or exhaust vent. See change in a structure occurs. Also used for soldering alumi forAbbr. tightening, T.F.E. or loosening,chiefly Brit.: orcalled band vapor, saw. steam,6. a tool used to degree of hazard (de-gree stench trap (stench trap) num bronze when mixed with nutsthermal and bolts.expansion 2. (water) straightenLOCAL VENT. -
Technical Data
HI·TECH (800) 677-8942 I (303) 680-5159 www.hitechcontrols.con CONTROLS, INC. Click or Call for a Quotel • "Hybrid" Torque Specifications S rint/BSP and Pro-Fit/NPTF --l ......."' 'Hybrid' Torque Specifications - (Sprint - BSP Fittings assembled into female NPTF ports) <au lion: Mating material and female parls may be too soft for high torque values. {heck material hardness to ovoid Slripping, galling or (foss-threading. This table is ONLY a guide for "hybrid" siluatiom; that require inteHhonging thread Iypes to ouommodote tubing requirements. T1wilOO Size MiWn.m ToltpJel'l:U AW:itun IClqJe VWe Sprint N. fl-l.lI$ N. h-lbs 1/8" • 10 0.1 10.0 1.' 1/4" • 4.0 1.9 20.0 14,8 3/8" 27.0 10.0 54.0 40.0 1/2" 27.0 100 67.0 ~O • Hrllll! TOIq1N "loti III rlMll Tbllocf ~III QlIIIlVIll Illhl lorqilt WIlIII for (1lOIIa~OlII1l ~ (ISP Inale II ISP ftlnale). ·Hybrid" TOfque SpecificationS - (Profit - NPTF Fittings assembled into female BSP portS) (llulilln: Mating malelial and female parIs may be too soh for high la/que values. {heck material hardness ra avaid stripping, galling ar Closs·rhleading. This rable is ONLY a guide for "hybrid" silualians lhat require intmhonging rhreod Iypes 10 ouommadare tubing requilemenrs. ihleod Size Miifun ltll~ VIM Moxirun 'onp VtU Sprint N. fl-lbs N. fl-Lbs 1/8" • 0.1 10.0 - I' 1.' w 1/4 • 4.' 1.9 20.0 14.8 3/8" • I.' 3.1 20.0 14.8 1/2" 21.0 20.0 54,0 40.0 c< lit " ,tI,,,,, ," "Il' " .." ....1, ..1 I, ......" ."l.., "",, 179 "MOnO at "j"" ,. -
Pipe Joining for Plumbing and Heating Systems
TM 26 January 2020 JOURNAL OF DESIGN INNOVATION FOR HYDRONIC AND PLUMBING PROFESSIONALS Pipe Joining for Plumbing and Heating Systems TM 5212 Series SinkMixer Scald Protection Point-of-use Mixing Valve • 4-way design simplifies piping and minimizes connection points. • Stand-off mounting bracket for simple sturdy installation. • Patented design, wide flow range to handle a variety of fixtures. • Forged low lead dezincification resistant brass for durability. Controlling and protecting your water www.caleffi.com - Milwaukee, WI USA FROM THE GENERAL MANAGER & CEO Dear Plumbing and Hydronic Professional, It was the 1990s when I attempted my first soldering job. What a mess! Although the replacement water softener ended up working fine, my workmanship was nothing short of “bush league”. There was more solder on the basement floor and on the outside of the pipe, than there was in the completed joint. Fortunately the softener was in my own home. I’ve long since moved on from there but would not be surprised if someday that work is posted up on one of those “hacked-up install” websites! That experience gave me an appreciation for the skill that goes into producing a reliable pipe connection in a timely manner. Fast forwarding to today there are several new pipe joining technologies available that not only produce a reliable connection, but require significantly less time than traditional methods. As skilled labor becomes increasingly scarce, it’s likely that manufacturers will introduce even more innovate “quick-joining” technologies and methods. This issue of idronics discusses classic and contemporary methods of joining piping in hydronic and plumbing applications. -
Western Riverside County Regional Wastewater Authority
Western Riverside County Regional Wastewater Authority 14 MGD Plant Expansion - Volume IIB September 2014 For Bidding Purposes Only WESTERN RIVERSIDE COUNTY REGIONAL WASTEWATER AUTHORITY 14.0 MGD PLANT EXPANSION VOLUME IIB Technical Specifications Section # of Pages SECTION 00020 – CONTRACT DOCUMENTS TABLE OF CONTENTS TECHNICAL SPECIFICATIONS – VOLUME II-B DIVISION 22 – PLUMBING 220050 General Pipes and Fittings ................................................................................................ 11 220513 Common Motor Requirements for Equipment ................................................................... 7 220517 Sleeves and Sleeve Seals for Piping ................................................................................... 2 220518 Escutcheons for Piping ....................................................................................................... 2 220519 Meters and Gages ................................................................................................................ 3 220523 Valves ............................................................................................................................... 11 220529 Hangers and Supports for Piping and Equipment ............................................................... 8 220553 Identification for Piping and Equipment ............................................................................. 4 220719 Piping Insulation ................................................................................................................ -
Definition of Pipe Thread Acronyms National Pipe Thread Taper (NPT) Is a U.S
Pipe Thread Definitions Checking thread type can be done with a thread gauge. Thread types can also be specified on existing pipe labels, manufacturer specifications or on manufacturer drawings. The specified sealant tape or paste should be used when required for installation. Definition of Pipe Thread Acronyms National Pipe Thread Taper (NPT) is a U.S. standard for tapered NPT National Pipe Thread (tapered) threads on threaded pipes and fittings. In contrast to straight threads, a taper thread will be tighter and have a fluid/air-tight seal . FPT is a term for pipe fittings that MIP (male iron pipe) or MNPT (male Female Pipe Thread FPT national pipe thread) fittings fit into. Female threads are internal located (interchangeable with NPT) inside of the pipe or fitting. Female Iron Pipe (interchangeable FIP, Female Iron Pipe, or Female International Pipe- Similar to FPT, FIP FIP with NPT) connect NPT pipe together with internal threads. National pipe thread connection to an FPT (Female Pipe Thread) or Male Pipe Thread (interchangeable MPT equivalently an FIP (Female Iron Pipe). MPT the threads are located on the with NPT) outside of the pipe or fitting. Male Iron Pipe (interchangeable MIP Male Iron Pipe, a threaded pipe or fitting connection to an FIP or FPT fitting. with NPT) PTF SAE short taper pipe thread SAE Short is mainly used in low pressure pneumatic and fuel applications. National Pipe Thread Fine National Pipe Thread Fine– also called Dry seal American National Standard (American National taper pipe NPTF Taper Pipe Thread is designed to provide a more leak-free seal without the thread for dry seal pressure tight use of Teflon tape or other sealant compound. -
Progress Report of the National Screw Thread Commission
DEPARTMENT OF COMMERCE BUREAU OF STANDARDS S. W. STSATTON, Duticrot PROGRESS REPORT OF THE NATIONAL SCREW THREAD COMMISSION (AUTHORIZED BY CONGRESS, JULY 18, 1918, H. R. 10852) AS APPROVED JUNE 19, 1920 JANUARY 4, 1921 MISCELLANEOUS PUBLICATIONS OF THE BUREAU OF STANDARDS No. 42 WASHINGTON «OVIRNMENT PRINTING OFFICE - . - NATIONAL SCREW THREAD COMMISSION, WASHINGTON, June ig, 1920. The accompanying Progress Report of the National Screw Thread Commission has been approved by the Commission, and by the Secretaries of War, Navy, and Commerce, in accordance with the provisions of the law establishing the Commission. APPROVAL BY THE MEMBERS OF THE COMMISSION. The Progress Report of the National Screw Thread Commission, as revised in accordance with the vote of November 23-24, 1919, and embodying certain changes recommended by a special committee of the Society of Automotive Engineers, is hereby approved. S. W. Stratton, Chairman. B. C. Peck, J. O. Johnson, Representing the United States Army. N. H. Wright, P. M. McNair, Representing the United States Navy. James Hart'ness, F. O. Wells, Nominated by the American Society of Mechanical Engineers. E. H. Ehrman, H. T. Herr, Nominated by the Society of Automotive Engineers. approval by the secretaries of war, navy, and commerce. The attached report prepared by the National Screw Thread Com- mission, in accordance with the law establishing the Commission (Public doc. No. 201, 65th Cong., H. R. 10852), is hereby accepted and approved. Newton D. Baker, Secretary of War. Josephus Daniels, Secretary of the Navy. Joshua W. Alexander, Secretary of Commerce. 35455°—21 WASHINGTON : GOVERNMENT PRINTING OFFICE : 1921 DEPARTMENT OF COMMERCE BUREAU OF STANDARDS S. -
Thread/Screw
THREAD/SCREW - Drill & Tap Chart Tap Drills Clearance Hole Drills Machine Screw Alum, Brass, Stainless Steel, All Materials Size & Plasitcs Steels & Iron Threads Minor Close Fit Free Fit Per Inch Dia 75% Thread 50% Thread Major Drill Decimal Drill Decimal Drill Decimal Drill Decimal # or Dia Dia Size Equiv. Size Equiv. Size Equiv. Size Equiv. 0 .0600 80 .0447 3/64 .0469 55 .0520 52 .0635 50 .0700 64 .0538 53 .0595 1/16 .0625 1 .0730 48 .0760 46 .0810 72 .0560 53 .0595 52 .0635 56 .0641 50 .0700 49 .0730 2 .0860 43 .0890 41 .0960 64 .0668 50 .0700 48 .0760 48 .0734 47 .0785 44 .0860 3 .0990 37 .1040 35 .1100 56 .0771 45 .0820 43 .0890 40 .0813 43 .0890 41 .0960 4 .1120 32 .1160 30 .1285 48 .0864 42 .0935 40 .0980 40 .0943 38 .1015 7/64 .1094 5 .125 30 .1285 29 .1360 44 .0971 37 .1040 35 .1100 32 .0997 36 .1065 32 .1160 6 .138 27 .1440 25 .1495 40 .1073 33 .1130 31 .1200 32 .1257 29 .1360 27 .1440 8 .1640 18 .1695 16 .1770 36 .1299 29 .1360 26 .1470 24 .1389 25 .1495 20 .1610 10 .1900 9 .1960 7 .2010 32 .1517 21 .1590 18 .1695 24 .1649 16 .1770 12 .1890 12 .2160 28 .1722 14 .1820 10 .1935 2 .2210 1 .2280 32 .1777 13 .1850 9 .1960 20 .1887 7 .2010 7/32 .2188 1/4 .2500 28 .2062 3 .2130 1 .2280 F .2570 H .2660 32 .2117 7/32 .2188 1 .2280 18 .2443 F .2570 J .2770 5/16 .3125 24 .2614 I .2720 9/32 .2812 P .3230 Q .3320 32 .2742 9/32 .2812 L .2900 16 .2983 5/16 .3125 Q .3320 3/8 .3750 24 .3239 Q .3320 S .3480 W .3860 X .3970 32 .3367 11/32 .3438 T .3580 14 .3499 U .3680 25/64 .3906 7/16 .4375 20 .3762 25/64 .3906 13/32 .4062 29/64 .4531 15/32 -
Pipe Threading and Testing
TRADE OF Pipefitting PHASE 2 Module 3 Pipe Processes UNIT: 6 Pipe Threading and Testing In cooperation with subject matter expert: Finbar Smith © SOLAS 2014 Module 3– Unit 6 Pipe Threading & Testing Table of Contents Unit Objective ........................................................................................................... 1 Learning Outcome .................................................................................................... 2 1.0 Pipe Thread Types and Designations ..................................................... 3 1.1 Introduction to Pipe Threads ................................................................... 3 1.2 Types of Pipe Threads............................................................................... 3 1.3 British Standard Pipe (BSP) Thread ........................................................ 4 1.4 National Pipe Thread (NPT) .................................................................... 4 1.5 Sealing a Tapered Thread .......................................................................... 5 2.0 Pipe Threading Equipment ...................................................................... 6 2.1 Hand Held Threading Handle .................................................................. 6 2.2 Threading Dies ........................................................................................... 7 2.3 Hand Held Threading Machine ............................................................... 7 2.4 Threading Machine ................................................................................... -
Report of the National Screw Thread Commission
DEPARTMENT OF COMMERCE BUREAU OF STANDARDS George K. Burgess, Director REPORT OF THE NATIONAL SCREW THREAD COMMISSION (REVISED, 1924) MISCELLANEOUS PUBLICATIONS, BUREAU OF STANDARDS, No. 61 DEPARTMENT OF COMMERCE BUREAU OF STANDARDS GEORGE K. BURGESS, Director REPORT OF THE NATIONAL SCREW THREAD COMMISSION (REVISED, 1924) (AUTHORIZED BY CONGRESS, JULY 18, 1918, H. R. 10852) AS APPROVED AUGUST 19, 1924 FEBRUARY 11, 1925 MISCELLANEOUS PUBLICATIONS OF THE BUREAU OF STANDARDS No. 61 PRICE 35 CENTS Sold only by the Superintendent of Documents, Government Printing Office Washington, D. C. WASHINGTON GOVERNMENT PRINTING OFFICE 1925 PREFACE This report is the first revision of the progress report of the Na- tional Screw Thread Commission published in 1921. The material has been generally rearranged and subdivided into sections, all specifications relating to a given class of product being included in a single section. Among the more important changes made in the specifications as previously published are the following: The classes of fit have been renamed and renumbered; the tolerance on major diameter of screws of classes 3 and 4 has been made the same as for class 2; specifications for gages have been extensively revised, and the allowances and tolerances on fire-hose coupling threads have been revised to decrease the maximum permissible looseness. In general, any screw thread product which met the previous specifications will meet the revised specifications. New material added includes speci- fications for threading tools, recommended tool shapes, tap dimen- sions, and tap drill sizes; specifications for screw threads of special diameters, pitches and lengths of engagement; specifications for gages for fire-hose coupling threads; specifications for wood screws; and the appendixes, which embody information supplementing the specifications. -
Tapered Pipe Threads and Fittings: Making the Connection | ISM
30/5/2564 Tapered Pipe Threads and Fittings: Making the Connection | ISM 800.781.8487 ISM End your search, simplify your supply chain Industrial Specialties Mfg. & IS MED Specialties ISO 9001:2015 Certied Companies Menu TAPERED PIPE THREADS AND FITTINGS: MAKING THE CONNECTION ENSURING A GAS OR LIQUID-TIGHT CONNECTION MEANS UNDERSTANDING TAPERED PIPE THREADS NPT, National Pipe Taper (American) and BSPT (British standard Pipe Taper) are tapered pipe thread standards. Male and female tapered pipe threads wedge themselves together but need a sealant for a completely leak-free connection. Sealants ll any voids between the threads that could travel along the thread spiral. Tube and pipe are not the same thing Tube and pipe are hollow structures designed to provide a path for the ow of uids or gases. The main difference between tube and pipe is that pipe walls are thicker and stiffer. Tubing is never threaded because its walls are too thin. Pipe walls are strong enough to support cut or molded threads. Threaded pipe can provide gas or liquid-tight connections that are mechanically strong. Pipe threads There are many national and international standards for pipe threads. They vary by intended use such as garden hose threads and re hose threads among others. There are also historical developments behind “standard” pipe sizes and the shapes of threads. Examples of this are the differences between American and British threads. Units of measure play a part too. How to Install The two basic categories of pipe thread Plastic Thread Fittings • Parallel or straight pipe thread • Tapered pipe thread Take a look at a selection of ISM's metal threaded ttings and plastic threaded ttings.