One-Step Green Synthesis of Graphene Nanomesh by Fluid-Based Method
Total Page:16
File Type:pdf, Size:1020Kb
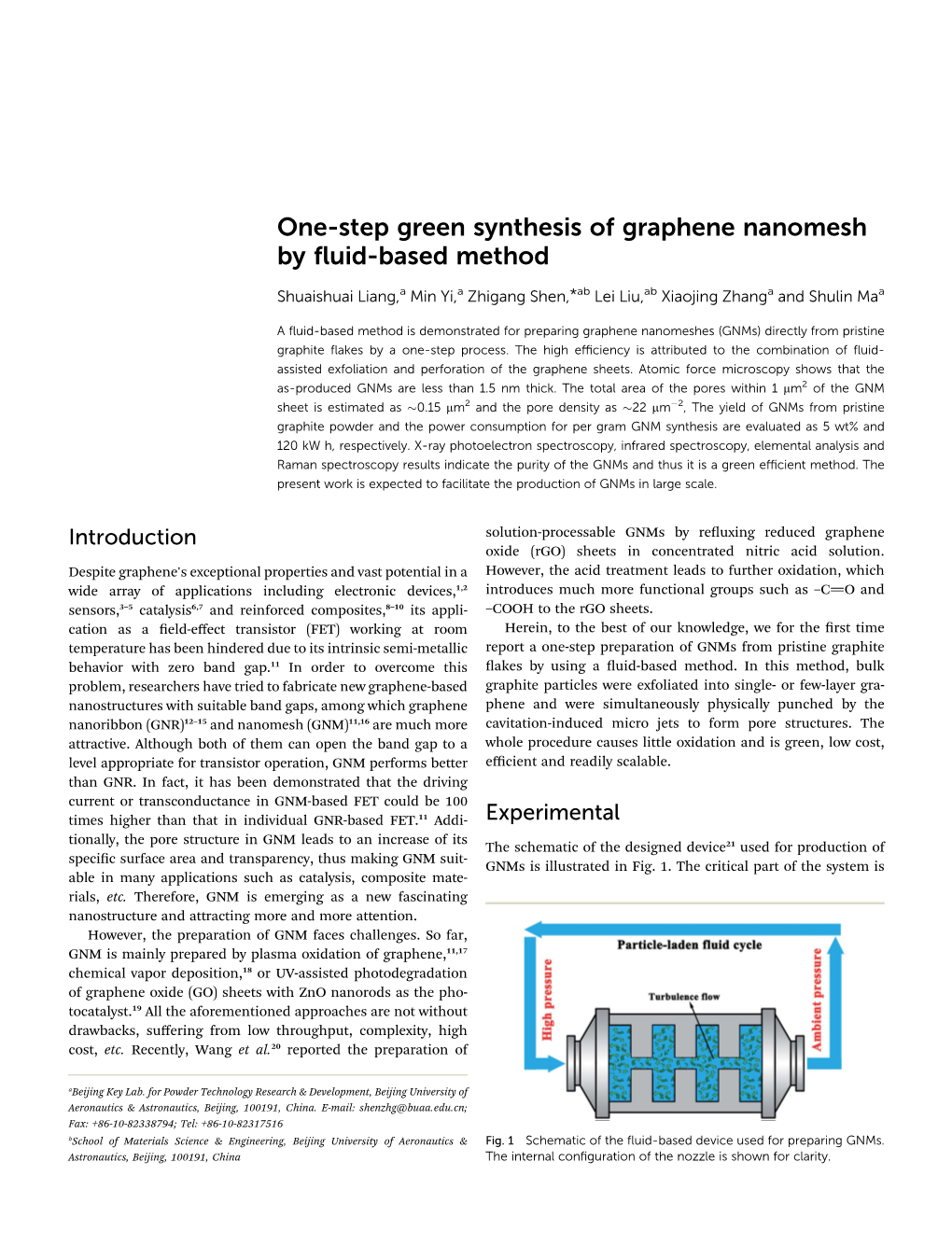
Load more
Recommended publications
-
(12) United States Patent (Io) Patent No.: US 7,001,669 B2 Lu Et Al
(12) United States Patent (io) Patent No.: US 7,001,669 B2 Lu et al. (45) Date of Patent: Feb. 21,2006 (54) PROCESS FOR THE PREPARATION OF 6,395,230 B1 512002 Guerin et al. METAL-CONTAINING NANOSTRUCTURED 6,409,907 B1 612002 Braun et al. FILMS 6,423,411 B1 712002 Balkus, Jr. et al. 6,465,052 B1 1012002 wu Inventors: Yunfeng Lu, New Orleans, LA (US); 6,565,763 B1 * 512003 Asakawa et al. ............. 216156 (75) 6,805,972 B1 * 1012004 Erlebacher et al. ......... 4281613 Donghai Wang, New Orleans, LA (US) 200210034626 A1 312002 Liu, et al. 200210034827 A1 312002 Singh, et al. (73) Assignee: The Administration of the Tulane 200210055239 A1 512002 Tuominen, et al. Educational Fund, New Orleans, LA 200210102396 A1 812002 MacDougall, et al. (US) 200210118027 A1 812002 Routkevitch, et al. 200210119455 A1 812002 Chan ( * ) Notice: Subject to any disclaimer, the term of this 200210138049 A1 912002 Allen, et al. patent is extended or adjusted under 35 200210146745 A1 1012002 Natan, et al. U.S.C. 154(b) by 133 days. (Continued) (21) Appl. No.: 10/328,631 FOREIGN PATENT DOCUMENTS (22) Filed: Dec. 23, 2002 EP 1 123 753 A2 812001 (Continued) (65) Prior Publication Data OTHER PUBLICATIONS US 200410118698 A1 Jun. 24, 2004 Michael H. Huang, et al., “Ag Nanowire Formation Within (51) Int. C1. Mesoporous Silica,” Chem. Commun., pp. 1063-1064 B32B 5/00 (2006.0 1) (2000). (52) U.S. C1. .................... 4281613; 4281304.4; 1481430 (Continued) (58) Field of Classification Search ................ 4281613, 4281605, 608,304.4; 205167,75,224; 1481518, Primary Examiner-John J. -
Nanodata Landscape Compilation
NanoData Landscape Compilation Environment Written by the Joint Institute for Innovation Policy, Brussels, Belgium, in co-operation with CWTS, University of Leiden, Leiden, Netherlands; Frost & Sullivan Limited, London, United Kingdom; Joanneum Research Forschungsgesellschaft mbH, Graz, Austria; the Nanotechnology Industries Association, Brussels, Belgium; Tecnalia Research and Innovation, Bilbao, Spain; and TNO, The Hague, Netherlands. August 2016 EUROPEAN COMMISSION Directorate-General for Research and Innovation Directorate Industrial Technologies Unit D.3 - Advanced Materials and Nanotechnologies E-mail: [email protected] European Commission B-1049 Brussels EUROPEAN COMMISSION NanoData Landscape Compilation Environment Written by: Jacqueline E M Allan Babette Bakker Harrie Buist Guillaume Flament Christian Hartmann Iain Jawad Eelco Kuijpers Hanna Kuittinen Ed Noyons Claire Stolwijk Xabier Uriarte Olaeta and Alfredo Yegros Additional contributions: Ashfeen Aribea Iker Barrondo Saez Robbert Fisher Milica Misojcic Luca Remotti Directorate-General for Research and Innovation 2017 Key Enabling Technologies EN EUROPE DIRECT is a service to help you find answers to your questions about the European Union Freephone number (*): 00 800 6 7 8 9 10 11 (*) The information given is free, as are most calls (though some operators, phone boxes or hotels may charge you) LEGAL NOTICE This document has been prepared for the European Commission however it reflects the views only of the authors, and the Commission cannot be held responsible for any use which may be made of the information contained therein. More information on the European Union is available on the internet (http://europa.eu). Luxembourg: Publications Office of the European Union, 2017. PDF ISBN 978-92-79-68388-6 doi: 10.2777/017097 KI-02-17-427-EN-N © European Union, 2017. -
Molecular Transport Across a Two-Dimensional Nanomesh Membrane–Graphdiyne
Journal of Physics D: Applied Physics J. Phys. D: Appl. Phys. 53 (2020) 493003 (8pp) https://doi.org/10.1088/1361-6463/abafdd Topical Review Molecular transport across a two-dimensional nanomesh membrane–graphdiyne Jiyu Xu1,2 and Sheng Meng1,2,3 1 Beijing National Laboratory for Condensed Matter Physics and Institute of Physics, Chinese Academy of Sciences, Beijing 100190, People’s Republic of China 2 School of Physical Sciences, University of Chinese Academy of Sciences, Beijing 100049, People’s Republic of China 3 Songshan Lake Materials Laboratory, Dongguan, Guangdong 523808, People’s Republic of China E-mail: [email protected] Received 7 May 2020, revised 27 July 2020 Accepted for publication 17 August 2020 Published 21 September 2020 Abstract The purification and separation technologies are of great importance to industry and agriculture in modern society. Two-dimensional (2D) crystals emerge as superior membrane materials showing desirable molecular permeability and selectivity. Among them, 2D materials with a nanomesh structure show the greatest potential in molecular transport and separation. Here, we highlight the recent theoretical progresses in molecular transport across 2D graphdiyne membrane with the nanomesh structure. Firstly, the nonlinear and activated water flow were demonstrated through the graphdiyne membranes under external hydrostatic pressure. Then, the superior proton conductivity and perfect selectivity were shown for graphdiyne membrane at ambient conditions. Lastly, graphdiyne was shown to exhibit perfect small gas molecule permeability and selectivity at the atmospheric conditions. The mechanisms for molecular transport and selectivity are also discussed. Keywords: nanomesh membrane, graphdiyne, molecular transport and separation, molecular dynamics (Some figures may appear in colour only in the online journal) 1. -
Download Monograph [PDF]
NANOTECHNOLOGY...| 1 IDSA Monograph Series No. 48 October 2015 NANOTECHNOLOGY THE EMERGING FIELD FOR FUTURE MILITARY APPLICATIONS Sanjiv Tomar 2 | SANJIV TOMAR Cover Illustration Courtesy: http://2.bp.blogspot.com/-XfhWNz2_bpY/ T3dVp2eYz1I/AAAAAAAARDY/Y3TZBL4XaHU/s1600/ 1325267213444.png available at http://fortressaustralia.blogspot.in/ 2012_04_01_archive.html Institute for Defence Studies and Analyses, New Delhi. All rights reserved. No part of this publication may be reproduced, sorted in a retrieval system or transmitted in any form or by any means, electronic, mechanical, photo-copying, recording or otherwise, without the prior permission of the Institute for Defence Studies and Analyses (IDSA). ISBN: 978-93-82169-58-1 Disclaimer: It is certified that views expressed and suggestions made in this monograph have been made by the author in his personal capacity and do not have any official endorsement. First Published: October 2015 Price: Rs. 200/- Published by: Institute for Defence Studies and Analyses No.1, Development Enclave, Rao Tula Ram Marg, Delhi Cantt., New Delhi - 110 010 Tel. (91-11) 2671-7983 Fax.(91-11) 2615 4191 E-mail: [email protected] Website: http://www.idsa.in Cover & Layout by: Geeta Kumari Printed at: M/S A. M. Offsetters A-57, Sector-10, Noida-201 301 (U.P.) Mob: 09810888667 E-mail: [email protected] NANOTECHNOLOGY...| 3 Contents Acknowledgements 5 Abbreviations 6 Introduction 9 1. ADVENT OF NANOTECHNOLOGY 13 1.1. A Brief Historical Account 13 1.2 What makes nanoparticle properties so alluring? 16 1.3 Nanomaterials 19 2. NANOTECHNOLOGY R&D INITIATIVES AND THE CURRENT GLOBAL LANDSCAPE 23 2.1 United States 24 2.2 China 25 2.3 Russia 27 2.4 Japan 28 2.5 European Union 29 2.6 India 30 2.7 Pakistan 33 2.8 South Korea 33 2.9 Elsewhere in the World 24 3. -
Nanotechnology, November 2008
“Nanomaterials exemplify the kind of challenge for which attention to closing gaps in knowledge and regulation is necessary but insufficient. Effective governance will mean looking beyond traditional regulation for other, more imaginative solutions, often involving a wider range of actors and institutions than has been customary in the past…Ultimately however, many of the questions raised…extend beyond the (important) issues of risk and risk management to questions about the direction, application and control of innovation.” – The UK’s Royal Commission on Environmental Pollution (RCEP), Novel Materials in the Environment: The Case of Nanotechnology, November 2008. (In July 2010, the UK’s Environment Secretary Caroline Spelman announced she was abolishing the RCEP as part of a deficit reduction effort.) About the cover From Georges Seurat’s ‘Bathers at Asnières’ (National Gallery, London) painted in 1884 (as shown here). Against a backdrop of smokestacks spewing industrial pollution, Seurat’s anonymous workers from a suburb of Paris relax along and in the River Seine. In Shtig’s adaptation for our cover, the scene of workers at leisure is made ominous by nanotech’s new form of industrial pollution, visible only by its effects on the environment and human health. Acknowledgements ETC Group owes a tremendous debt of gratitude to Stephanie Howard, whose careful, original and comprehensive research forms the basis of this report. We have also benefitted from discussions that took place We are extremely grateful to all of the Nano-hazard symbol (reproduced on during a series of meetings organized to participants. ETC Group gratefully this report’s cover) by Kypros explore the implications of BANG acknowledges the financial support Kyprianou. -
Coupling Epitaxy, Chemical Bonding, and Work Function at the Local Scale in Transition Metal-Supported Graphene
ACS Nano 4, 5773-5782 (2010) Coupling Epitaxy, Chemical Bonding, and Work Function at the Local Scale in Transition Metal-Supported Graphene Bo Wang, Marco Caffio, Catherine Bromley, Herbert Früchtl, and Renald Schaub* School of Chemistry, University of St. Andrews, St. Andrews, KY16 9ST, United Kingdom Corresponding Author (*): [email protected]. Resonance tunneling spectroscopy and density functional theory calculations are employed to explore local variations in the electronic surface potential of a single graphene layer grown on Rh(111). A work function modulation of 220 meV is experimentally measured, indicating that the chemical bonding strength varies significantly across the supercell of the Moiré pattern formed when graphene is bonded to Rh(111). In combination with high-resolution images, which provide precise knowledge of the local atomic registry at the carbonmetal interface, we identify experimentally, and confirm theoretically, the atomic configuration of maximum chemical bonding to the substrate. Our observations are at odds with reported trends for other transition metal substrates. We explain why this is the case by considering the various factors that contribute to the bonding at the graphene/metal interface. KEYWORDS Graphene, rhodium, chemical bonding, scanning tunnelling microscopy, density functional theory, work function dx.doi.org/10.1021/nn101520k Received: July 5, 2010 Accepted: September 24, 2010 Published: October 1, 2010 1 ACS Nano 4, 5773-5782 (2010) Graphene has attracted considerable interest since resonance tunnelling spectroscopy (RTS) researchers at the University of Manchester measurements to probe for the modulation of the extracted a single graphene sheet by electronic surface potential (or work function) across micromechanical cleavage.1 This sp2-bonded carbon the unit cell of the graphene superlattice. -
Single Layer Templates for Molecules: from H-BN Nanomesh to Graphene Based Quantum Dot Arrays
Single layer templates for molecules: From h-BN Nanomesh to Graphene based Quantum dot arrays Thomas Greber, Physik-Institut, University of Zurich The assembly of molecules on surfaces is a central issue for the understanding and exploitation of processes in heterogeneous catalysis, selective gas detection or single molecule electronics. In this keynote I will focus on the role of templates that act as scaffolds for molecular arrays. Such functional nano-templates enable self-assembly of otherwise impossible arrangements of molecules. A particular class of templates is that of sp2 hybridised single layers of boron nitride or carbon (graphene) on metal supports which can be prepared with atomic precision [1] - and they are stable in liquids [2]. If the substrate and the single layer have a lattice mismatch, superstructures with unit cells containing more that 1000 surface atoms may be formed. These superstructures contain sub-units, which behave like single molecule traps [3] or quantum dots [4]. They are an ideal construction lot for supra-molecular architecture where the template function is related to lateral electric fields (dipole rings) on the nanometer scale [3]. For the case of smaller molecules like water it is e.g. shown that new phases assemble on such artificial structures [5]. [1] Comparison of electronic structure and template function of single- layer graphene and a hexagonal boron nitride nanomesh on Ru(0001), Brugger et al., PRB 79 (2009) 045407. [2] Electrolytic in situ STM investigation of h-BN-Nanomesh Widmer et al., Electrochemistry Communications 9 (2007) 2484. [3] Surface Trapping of Atoms and Molecules with Dipole Rings Dil et al., Science 319 (2008) 1826. -
From Patterning of Polymer-Based Films to Their Subsequent Filling with Various Nanomaterials
polymers Review Multifunctional Structured Platforms: From Patterning of Polymer-Based Films to Their Subsequent Filling with Various Nanomaterials Madalina Handrea-Dragan 1,2 and Ioan Botiz 1,* 1 Interdisciplinary Research Institute in Bio-Nano-Sciences, Babes-Bolyai University, 42 Treboniu Laurian Str. 400271 Cluj-Napoca, Romania; [email protected] 2 Faculty of Physics, Babes-Bolyai University, 1 M. Kogalniceanu Str. 400084 Cluj-Napoca, Romania * Correspondence: [email protected] Abstract: There is an astonishing number of optoelectronic, photonic, biological, sensing, or storage media devices, just to name a few, that rely on a variety of extraordinary periodic surface relief miniaturized patterns fabricated on polymer-covered rigid or flexible substrates. Even more extraor- dinary is that these surface relief patterns can be further filled, in a more or less ordered fashion, with various functional nanomaterials and thus can lead to the realization of more complex structured architectures. These architectures can serve as multifunctional platforms for the design and the development of a multitude of novel, better performing nanotechnological applications. In this work, we aim to provide an extensive overview on how multifunctional structured platforms can be fabricated by outlining not only the main polymer patterning methodologies but also by emphasizing various deposition methods that can guide different structures of functional nanomaterials into periodic surface relief patterns. Our aim is to provide the readers with a toolbox of the most suitable patterning and deposition methodologies that could be easily identified and further combined when the fabrication of novel structured platforms exhibiting interesting properties is targeted. Citation: Handrea-Dragan, M.; Botiz, I. -
Fabrication and Manipulation of Metallic Nanofeatures and CVD Graphene Through Nanopatterning and Templating
Fabrication and Manipulation of Metallic Nanofeatures and CVD Graphene through Nanopatterning and Templating by Copyright 2014 Christina M. Edwards Submitted to the graduate degree program in Chemistry and the Graduate Faculty of the University of Kansas in partial fulfillment of the requirements for the degree of Doctor of Philosophy. Chairperson Cindy L. Berrie Michael A. Johnson Susan M. Lunte Timothy A. Jackson Prajna Dhar Date Defended: July 16, 2014 The Dissertation Committee for Christina M. Edwards certifies that this is the approved version of the following dissertation: Fabrication and Manipulation of Metallic Nanofeatures and CVD Graphene through Nanopatterning and Templating Chairperson Cindy L. Berrie Date Defended: July 16, 2014 ii Abstract Nanotechnology holds exciting potential to significantly advance research in many fields such as sensors, environmental sustainability and cleanup, energy harvesting and storage, as well as nanoelectronics. The resulting high demand for implementation into these areas has simultaneously created a large need for effective fabrication methods for nanostructured materials. It is important the fabrication methods are capable of significant control over size, orientation, and structural configuration of nanomaterials for effective function in these applications. Nanopatterning and templating are a promising means to achieve extreme selectivity over these parameters, and additionally be used as tools to control the growth and structure of large-scale materials through nanoscale manipulation. In this research, nanopatterning and templating are implemented to create metallic nanowire structures on surfaces of silicon substrates with highly selectivity over nanowire placement and design. Additionally, templating is incorporated in graphene growth on metallic substrates to influence the quality of graphene films,and further film patterning is used to improve the graphene electrical and optical properties. -
Plasmonic Absorbers with Optical Cavity for the Enhancement of Photothermal/Opto-Calorimetric Infrared Spectroscopy
University of Calgary PRISM: University of Calgary's Digital Repository Schulich School of Engineering Schulich School of Engineering Research & Publications 2017-01 Plasmonic absorbers with optical cavity for the enhancement of photothermal/opto-calorimetric infrared spectroscopy Kim, Seonghwan Applied Physics Letters Dongkyu Lee, Inseok Chae, Ohwon Kwon, Kangho Lee, Changwon Kim, Seonghwan Kim, Thomas Thundat. (2017). "Plasmonic absorbers with optical cavity for the enhancement of photothermal/opto-calorimetric infrared spectroscopy," Applied Physics Letters, 110, 011901 http://hdl.handle.net/1880/51777 journal article Downloaded from PRISM: https://prism.ucalgary.ca Plasmonic absorbers with optical cavity for the enhancement of photothermal/opto-calorimetric infrared spectroscopy Dongkyu Lee1 ・*, Inseok Chae2 ・, Ohwon Kwon1, Kang-Ho Lee1, Changwon Kim1, Seonghwan Kim3, and Thomas Thundat2 1Daegu Research Center for Medical Devices, Korea Institute of Machinery and Materials (KIMM), Daegu, 42994, Republic of Korea 2Department of Chemical and Materials Engineering, University of Alberta, Edmonton, AB T6G 2V4, Canada 3Department of Mechanical and Manufacturing Engineering, University of Calgary, Calgary, Alberta T2N 1N4, Canada Plasmonic absorbers with optical cavity are fabricated using deposition of thin gold films on both sides of nanoporous anodic aluminum oxide (AAO) microcantilevers. Photothermal/opto-calorimetric responses of the microcantilevers are investigated with respect to various pore sizes and gold coating thicknesses. Photothermal/opto- calorimetric response of the AAO cantilever is significantly amplified when gold layer thickness is at 40 nm due to scattering and trapping of infrared (IR) radiation in the gold nanomesh/AAO nanochannels/gold layer structure. Unlike previous photothermal IR spectroscopy of adsorbed molecules with a bimetallic AAO cantilever, the reversed IR spectra are obtained due to significantly amplified baseline photothermal signal and IR absorption of free molecules. -
3. Scanning Tunneling Microscopy
3. SCANNING TUNNELING MICROSCOPY JIN-FENG JIA, WEI-SHENG YANG, AND QI-KUN XUE 1. BASIC PRINCIPLES OF SCANNING TUNNELING MICROSCOPY In spite of its conceptually simple operation principle, scanning tunneling microscope (STM) can resolve local electronic structures on an atomic scale in real space on virtually any kind of conducting solid surface under various environments, with little damage or interference to the sample [1]. It has been invented for more than 20 years. Over the years, the STM has been proved to be an extremely versatile and powerful technique for many disciplines in condensed matter physics, chemistry, material science, and biology. In addition, STM can be used as a nano-tool for nano-scale fabrication, manipulation of individual atoms and molecules, and for building nanometer scale devices one atom/molecule at a time. STM was originally developed to image the topography of surfaces by Binnig and Rohrer in 1982 [1]. For this great invention, they were awarded the Nobel Prize in Physics in 1986. The principle of STM is very simple, in which electron tunneling is used as the mechanism to probe a surface. In the following, in order to understand the operation principle of STM, we first give a brief introduction to the electron tunneling phenomenon. 1.1. Electronic Tunneling Tunneling phenomena have been studied for long time and can be well understood in terms of quantum theory. As shown in Fig. 1, considering an one-dimensional vacuum barrier between two electrodes (the sample and the tip) and assuming their 56 I. Optical Microscopy, Scanning Probe Microscopy, Ion Microscopy and Nanofabrication Figure 1. -
Successful European Nanotechnology Research Outstanding Science and Technology to Match the Needs of Future Society
EUROPEAN Research & Industrial COMMISSION Innovation technologies Successful European Nanotechnology Research Outstanding science and technology to match the needs of future society projects Studies and reports EUROPEAN COMMISSION Directorate-General for Research and Innovation Directorate G – Industrial Technologies Unit G.4 – Nano-and converging Sciences and Technologies Contact: Hans Hartmann Pedersen European Commission Office SDME 06/120 B-1049 Brussels Tel. +32 2 29 64906 Fax +32 2 29 86150 E-mail: [email protected] EUROPEAN COMMISSION Successful European Nanotechnology Research Outstanding science and technology to match the needs of future society Edited by the European Commission Directorate-General for Research and Innovation Directorate Industrial Technologies Directorate-General for Research and Innovation Nanosciences, nanotechnologies, materials 2011 and new production technologies (NMP) EUR 24524 EN Europe Direct is a service to help you find answers to your questions about the European Union Freephone number(*): 00 800 6 7 8 9 10 11 (*)Certain mobile telephone operators do not allow access to 00 800 numbers or these calls may be billed LEGAL NOTICE Neither the European Commission nor any person acting on behalf of the Commission is responsible for the use which might be made of the following information. The views expressed in this publication are the sole responsibility of the author and do not necessarily reflect the views of the European Commission. A great deal of additional information on the European Union is available on the Internet. It can be accessed through the Europa server (http://europa.eu). Cataloguing data can be found at the end of this publication.