The Impact of Information Technology on Industrial Automation–A Critical Evaluation
Total Page:16
File Type:pdf, Size:1020Kb
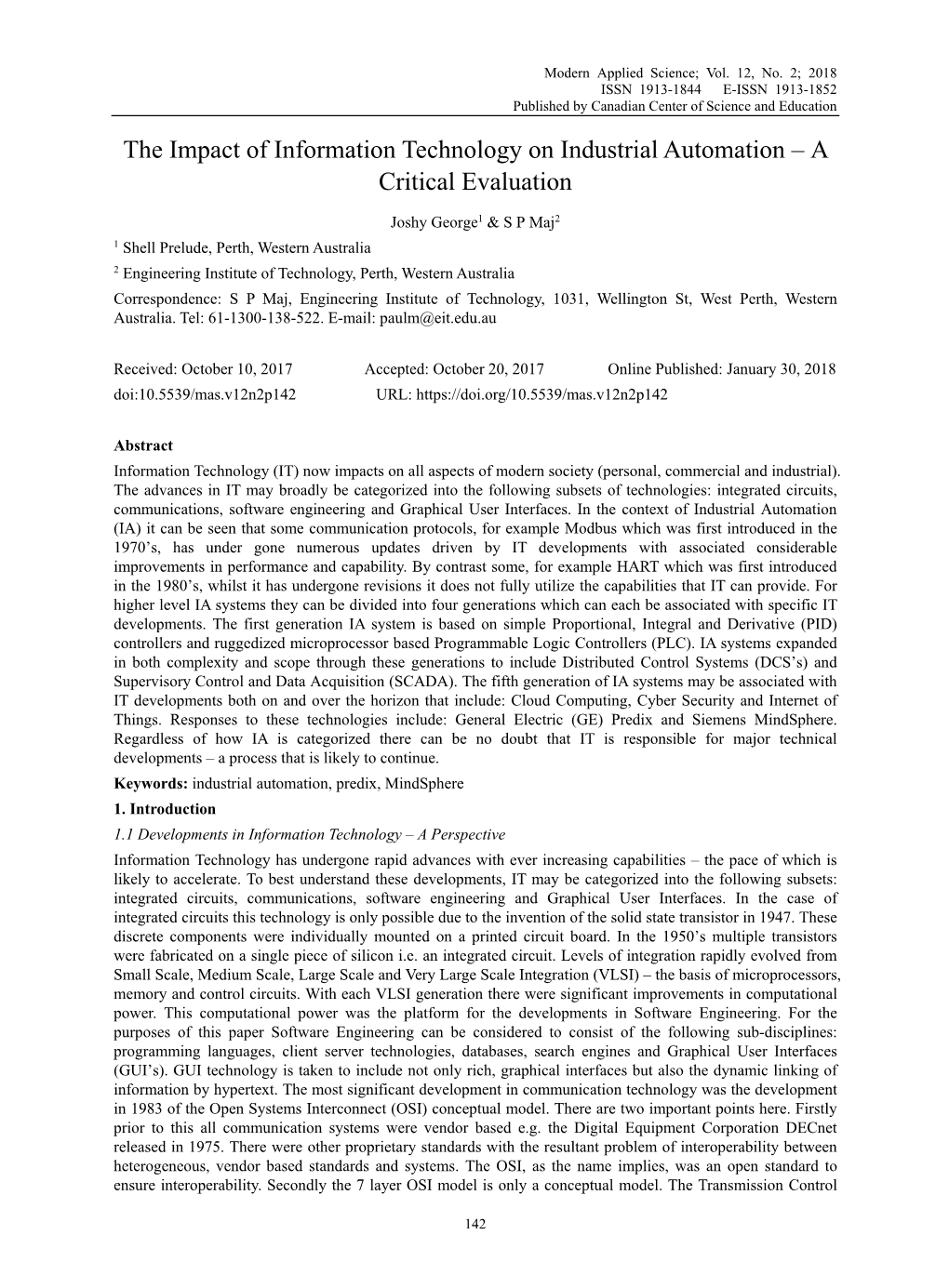
Load more
Recommended publications
-
ML50 Catalog R5p0
ML50 Compact Logic Controller AUTOMATION MADE EASY & COMPACT Honeywell Solutions for Machine Automation 1 | P a g e M a s t e r L o g i c 5 0 S e r i e s SPECIAL FEATURE Compact ML50 series is extremely compact providing both powerful functions and performance. The dual combination of Compactness & Performance is what makes ML50 such an ideal product. unit=mm(in) Item W H D W Main Unit MLM-D_ _S 30(1.18) 90(3.54) 60(2.36) MLC(I)-D_32H 114(4.49) 90(3.54) 64(2.52) D MLC(I)-D_64H 180(7.09) 90(3.54) 64(2.52) MLI-D_SU 135(5.3) 90(3.54) 64(2.52) MLI-D20E/30E MLI-D_10E/14E 100(3.94) 90(3.54) 64(2.52) H MLI-D_ _U 135(5.31) 90(3.54) 64(2.52) Expansion Modules 20(0.79) 90(3.54) 60(2.36) H H W D W D H D W For detailed dimension information, please refer to it for each module. 1 | P a g e M a s t e r L o g i c 5 0 S e r i e s SPECIAL FEATURE Ultimate ‘U’ Performance Block Type (MLI series / MLI-D_ _U_) MLI U sets new standards in Ultimate Performance with its many innovations. IoT(Internet of Things) realizes smart factories, MLI-U series is a ‘User-Oriented’ controller. Exandable with existed modules for ML50 Applicable max 2 expansion modules with High speed backplane(for network-positioning modules only) Applicable upto 10 expansion modules Max. -
Exporting Fieldbuses to Europe 1. Product Description
Exporting fieldbuses to Europe Last updated: 05 July 2017 The development of Smart Industry and the Internet of Things has created a strong demand for industrial communication networks and their components, including fieldbuses. Fieldbuses make up over two thirds of the market for industrial communication networks. Due to their relative technical complexity, fieldbuses provide good market opportunities for manufacturers from developing countries. Contents of this page 1. Product description 2. Which European markets offer opportunities for exporters of fieldbuses? 3. What trends offer opportunities on the European market for fieldbuses? 4. What requirements should fieldbuses comply with to be allowed on the European market? 5. What competition do you face on the European fieldbus market? 6. Through what channels can you get fieldbuses on the European market? 7. What are the end-market prices for fieldbuses? 1. Product description The fieldbus is an industrial network system for real-time distributed control. It is an option to link instruments in a manufacturing plant and works in a network structure which typically allows daisy chain, star, ring, branch and tree network topologies. In the past, computers were connected using serial connections such as RS-232. In that way, no more than two devices were able to communicate. This would be the equivalent of the currently used 4-20 mA communication scheme, which requires that each device has its own communication point at the controller level. By contrast, the fieldbus is the equivalent of the current LAN-type connections, which require only one communication point at the controller level and allow multiple (hundreds) of analogue and digital points to be connected in parallel. -
Parock1 Flyer
OPTO22 PAC Rx/Sx controllers Overview: The Opto 22 Ethernet driver provides an easy and reliable way to connect Opto 22 Controllers to your OPC client applications, including HMI, SCADA, Historian, MES, ERP, and countless custom applications. Properties Screen Shot Features - Supports all OPTO 22 PACs or any other device which uses OPTO22’s native protocol CONT over Ethernet TCP/IP - high-speed Ascii based communication - Different from Optomux and OptoMMP - Same native protocol as used by Opto Sim & OPTO PAC Display. - Index of table support - Pointer towards tag support - Performance – 2.2GHz Dual Core - 10 words: 15 ms - Data Types supported o I32 o I64 o Float o Timer o String For More Info: Overview of Parijat Drivers: Click here Additional supporting Info about Parijat Drivers: Click here Complete Related Driver options: Click here Copyright © parijat controlware, inc. Any other legal rights belong to their respective owners. Any useage here is only for reference purpose contents subject to change without notice. 7/25/16 9603 Neuens Rd, Houston Tx 77080 . tel: (713) 935-0900 . fax: (713) 935-9565 . http://www.parijat.com . Email: [email protected] PCI PC-resident Drivers: General Information General Info about PCI driver Products PCI sells & supports the world’s largest range of communications drivers for Industrial automation, PLC, process control industry applications for Microsoft, Google, Apple, Linux products & ASP.NET core for web portal products. This document outlines various common features & knowledge base to help you make a decision. Welcome to the world of PCI, your exclusive and most mature, experienced (since 1989) source of help in Industrial data acquisition, control, HMI, SCADA and MIS, MRP, ERP or Browser based Internet applications based on non-proprietary open architecture. -
Connect-And-Protect: Building a Trust-Based Internet of Things for Business-Critical Applications Table of Contents
WHITE PAPER CONNECT-AND-PROTECT: BUILDING A TRUST-BASED INTERNET OF THINGS FOR BUSINESS-CRITICAL APPLICATIONS TABLE OF CONTENTS THE INTERNET OF WHATEVER 3 LET’S GET PHYSICAL 8 TALK THE TALK 11 PROTECTED INTEREST 14 PICTURE ME ROLLING 23 DATA: THE NEW BACON 25 CONCLUSION 29 SOURCES 29 ABOUT ARUBA NETWORKS, INC. 30 WHITE PAPER CONNECT-AND-PROTECT: INTERNET OF THINGS THE INTERNET OF WHATEVER Today it’s almost impossible to read a technical journal, sometimes a daily paper, without some reference to the Internet of Things (IoT). The term IoT is now bandied about in so many different contexts that its meaning, and the power of the insights it represents, are often lost in the noise. Enabling a device to communicate with the outside world isn’t by itself very interesting. The value of the IoT comes from applications that can make meaning of what securely connected devices have to say – directly and/or inferentially in combination with other devices – and then act on them. Combining sensors and device with analytics can reveal untapped operational efficiencies, create end-to-end process feedback loops, and help streamline and optimize processes. Action can take many forms, from more efficiently managing a building or factory, controlling energy grids, or managing traffic patterns across a city. IoT has the potential to facilitate beneficial decision making that no one device could spur on its own. But that potential can only be realized if the integrity of the information collected from the devices is beyond reproach. Put another way, regardless of how data gathered from IoT are used, they’re only of value if they come from trusted sources and the integrity of the data is assured. -
Pac Control User's Guide
PAC CONTROL USER’S GUIDE Form 1700-101124—November 2010 43044 Business Park Drive • Temecula • CA 92590-3614 Phone: 800-321-OPTO (6786) or 951-695-3000 Fax: 800-832-OPTO (6786) or 951-695-2712 www.opto22.com Product Support Services 800-TEK-OPTO (835-6786) or 951-695-3080 Fax: 951-695-3017 Email: [email protected] Web: support.opto22.com PAC Control User’s Guide Form 1700-101124—November 2010 Copyright © 2010 Opto 22. All rights reserved. Printed in the United States of America. The information in this manual has been checked carefully and is believed to be accurate; however, Opto 22 assumes no responsibility for possible inaccuracies or omissions. Specifications are subject to change without notice. Opto 22 warrants all of its products to be free from defects in material or workmanship for 30 months from the manufacturing date code. This warranty is limited to the original cost of the unit only and does not cover installation, labor, or any other contingent costs. Opto 22 I/O modules and solid-state relays with date codes of 1/96 or later are guaranteed for life. This lifetime warranty excludes reed relay, SNAP serial communication modules, SNAP PID modules, and modules that contain mechanical contacts or switches. Opto 22 does not warrant any product, components, or parts not manufactured by Opto 22; for these items, the warranty from the original manufacturer applies. These products include, but are not limited to, OptoTerminal-G70, OptoTerminal-G75, and Sony Ericsson GT-48; see the product data sheet for specific warranty information. -
Iec 61784-3 ®
This is a preview - click here to buy the full publication IEC 61784-3 ® Edition 3.0 2016-05 REDLINE VERSION INTERNATIONAL STANDARD colour inside Industrial communication networks – Profiles – Part 3: Functional safety fieldbuses – General rules and profile definitions INTERNATIONAL ELECTROTECHNICAL COMMISSION ICS 25.040.40; 35.100.05 ISBN 978-2-8322-3372-6 Warning! Make sure that you obtained this publication from an authorized distributor. ® Registered trademark of the International Electrotechnical Commission This is a preview - click here to buy the full publication – 2 – IEC 61784-3:2016 RLV IEC 2016 CONTENTS FOREWORD ......................................................................................................................... 8 0 Introduction ................................................................................................................. 10 0.1 General ............................................................................................................... 10 0.2 Transition from Edition 2 to extended assessment methods in Edition 3 ................ 12 0.3 Patent declaration ............................................................................................... 12 1 Scope .......................................................................................................................... 14 2 Normative references................................................................................................... 14 3 Terms, definitions, symbols, abbreviated terms and conventions.................................. -
IS7 Rapienet+ Option Module
LS ELECTRIC strives to maximize your profits in gratitude for choosing us as your partner. IS7 RAPIEnet+ Option Module SV-iS7 Series [ RAPIEnet, EtherNet/IP, Modbus TCP Protocol ] iS7 RAPIEnet+ Option Manual Before using the product Thank you for purchasing the iS7 RAPIEnet+ communication board. SAFETY PRECAUTIONS Always follow safety instructions to prevent accidents and potentially hazardous situations. Safety precautions are classified into “WARNING” and “CAUTION,” and their meanings are as follows: Indicates a potentially hazardous situation which, if not avoided, WARNING may cause death or serious injury. Indicates a potentially hazardous situation, which, if not CAUTION avoided, may cause minor injury or damage to the product. Symbols used in this document and on the product indicate the following. Read and follow the instructions carefully to avoid dangerous situations. Presence of "dangerous voltage" inside the product that may cause harm or electric shock. Keep the operating instructions handy for quick reference. Read the operating instructions carefully to fully understand the functions of the SV-iS7 series inverters and use them properly. CAUTION Be careful not to damage the CMOS elements on the communication board. Static charge may cause malfunctioning of the product. Turn off the inverter before connecting communication cables. Otherwise, the module may be damaged or a communication error may result. Correctly align the communication board to the installation connector for installation and ensure that it is firmly connected to the inverter. Otherwise, the module may be damaged or a communication error may result. Check the parameter units when configuring the parameter values. Otherwise, a communication error may occur. -
Opto 22’S SNAP Control System Is a Versatile SNAP Digital Modules Switch Or Sense Either AC Or DC Combination of Hardware and Software to Support Signals
SNAP I/O Control System Product Guide page 1/9 Form 788-001113 Opto 22’s SNAP Control System is a versatile SNAP digital modules switch or sense either AC or DC combination of hardware and software to support signals. Each module includes four channels and provides a wide variety of business applications. The system 4,000 volts of optical isolation from the field side to the consists of high-density digital, analog, and special- logic side. purpose I/O modules, compact industrial controllers, SNAP analog modules provide two or four channels. high-performance processor brains, and a series of They are factory calibrated and software configurable, mounting racks. Coupled with Opto 22’s powerful handling a wide variety of signal levels. FactoryFloor industrial automation software, SNAP offers SNAP special-purpose modules provide specific unparalleled flexibility and power for your control, functionality. Using serial modules, for example, you can monitoring, and data acquisition needs. communicate with serial devices such as chart recorders and barcode readers. Data-logging modules provide data storage SNAP I/O MODULES capacity, so that data from other modules on the same rack can SNAP analog and digital input and output modules be stored for later retrieval. PID modules monitor input signals provide compact, high-density I/O, with top-mounted and adjust output signals to control a proportional integral connectors for easy field wiring. derivative (PID) loop, performing all PID calculations in the module. SNAP I/O Modules, Rack, and SNAP Ethernet Brain SNAP I/O Control System Product Guide page 2/9 Form 788-001113 SNAP BRAINS SNAP RACKS SNAP brains are high-performance, intelligent SNAP racks come in four sizes to accommodate a maximum processors designed to meet your distributed control needs. -
LONWORKS for Audio Computer Control Network Applications
LONWORKS® for Audio Computer Control Network Applications January 1995 Executive Summary LONWORKS is a control network technology developed by Echelon for monitoring and controlling electrical devices of all kinds. LONWORKS meets the criteria specified by the audio industry for a computer control network, and is ideal for amplifier and equalizer control, automatic crossover control, sequential load control, equipment fault monitoring, set-top box automation, and home theater control. Neuron Chips embedded with the LONWORKS protocol have been produced by both Motorola and Toshiba since 1992, and hundreds of thousands of chips have been sold worldwide. Neuron Chips can communicate with one another, allowing data and decisions to be shared between equipment manufactured by different companies. Transceivers, routers, gateways, development tools, and programming and diagnostic tools are available off-the-shelf. Instead of developing control network technology, customers can use LONWORKS technology to build better, more intelligent, less expensive audio products. Introduction A control network is a system of sensors, actuators, displays, and logging devices (referred to as "nodes") that are linked together to monitor and control electrical devices. Supervisory functions are typically handled automatically and require no manual intervention except to respond to faults that the system cannot itself correct. In audio applications, a control network may monitor equipment fault conditions, adjust gain and crossover settings, monitor MIDI inputs, -
XGT Series XGT Series, Innovative Solutions for System Integration from Field to Information Level
Programmable Logic Controller XGT Series XGT series, innovative solutions for system integration from field to information level. Open Network System Integration FEATURES CPU SYSTEM NETWORK SSPECCIAL SOFTWARE 2 / 3 2_3 120 ~141 4 ~ 13 48 ~ 85 86 ~ 119 32 ~ 47 14 ~ 31 FEATURES FEATURES CPU SYSTEM NETWORK SPECIAL SOFTWARE Programmable Logic Controller neXt Generation Technology echnology Series T eneration eneration G t X ne Intro Welcome to XGT World! XGT series will meet your needs and expectations, enabling the highest possible productivity and performance levels and more. Programmable Logic Controller 4 / 5 Features XGT series is the next-generation solution with a new concept providing advanced engineering environment based on open network, fastest processing speed, compact size and user-friendly software. Programmable Logic Controller 6 / 7 The smallest size The smallest size(Dimensions 27 X 98 X 90) achieves cost-efficiency and various applications. Item Power Supply CPU 8-slot Base Size (WXHXD) 55X98X90 27X98X90 318X98X17 Features XGT series, neXt Generation Technology for easier, faster and smarter automation, will provide you with future-oriented solutions, bringing greener, safer and more convenient life for you... System Integration of Open Network XGT series support various communication solutions ranging from field control to information level with Fast Ethernet, Profibus-DP, DeviceNet, Modbus, etc. Programmable Logic Controller 8 / 9 FEn e t , Et h e r Ne t / IP, RAPIEn e t FEn e t , Et h e r Ne t / IP, RAPIEn e t , Fn e t D e v i c e Ne t , Pr o f i b u s - D P, Mo d b u s , CANo p e n , Rn e t Fast Ethernet Profibus- Item RAPIEnet EtherNet/IP Cnet Fnet DeviceNet Rnet FEnet FDEnet DP Transmission speed 10/100Mbps 100Mbps 100Mbps 300~115,200bps 1Mbps Max.12Mbps Max.500Kbps 1Mbps Transmission 100m (Node to Node, UTP/STP) Max. -
Communications
Communications The Drilling Systems Automation Roadmap Communications section provides guidance to the future technologies and processes used to communicate information in all forms across all aspects of drilling systems automation. Contents Functional Description .................................................................................................................................. 4 Performance targets (including KPI’s with dates) ......................................................................................... 4 Current and future situation of systems that use communications ............................................................. 5 Downhole Transmission Tools .................................................................................................................. 5 Current situation: .................................................................................................................................. 5 Challenges: ............................................................................................................................................ 5 Future State: ......................................................................................................................................... 5 Downhole to surface (vice Versa telemetry) review ............................................................................ 6 Surface acquisition systems ...................................................................................................................... 8 Current situation: -
Extracting and Mapping Industry 4.0 Technologies Using Wikipedia
Computers in Industry 100 (2018) 244–257 Contents lists available at ScienceDirect Computers in Industry journal homepage: www.elsevier.com/locate/compind Extracting and mapping industry 4.0 technologies using wikipedia T ⁎ Filippo Chiarelloa, , Leonello Trivellib, Andrea Bonaccorsia, Gualtiero Fantonic a Department of Energy, Systems, Territory and Construction Engineering, University of Pisa, Largo Lucio Lazzarino, 2, 56126 Pisa, Italy b Department of Economics and Management, University of Pisa, Via Cosimo Ridolfi, 10, 56124 Pisa, Italy c Department of Mechanical, Nuclear and Production Engineering, University of Pisa, Largo Lucio Lazzarino, 2, 56126 Pisa, Italy ARTICLE INFO ABSTRACT Keywords: The explosion of the interest in the industry 4.0 generated a hype on both academia and business: the former is Industry 4.0 attracted for the opportunities given by the emergence of such a new field, the latter is pulled by incentives and Digital industry national investment plans. The Industry 4.0 technological field is not new but it is highly heterogeneous (actually Industrial IoT it is the aggregation point of more than 30 different fields of the technology). For this reason, many stakeholders Big data feel uncomfortable since they do not master the whole set of technologies, they manifested a lack of knowledge Digital currency and problems of communication with other domains. Programming languages Computing Actually such problem is twofold, on one side a common vocabulary that helps domain experts to have a Embedded systems mutual understanding is missing Riel et al. [1], on the other side, an overall standardization effort would be IoT beneficial to integrate existing terminologies in a reference architecture for the Industry 4.0 paradigm Smit et al.