EGT Myths Debunked Email to Kristin at [email protected]
Total Page:16
File Type:pdf, Size:1020Kb
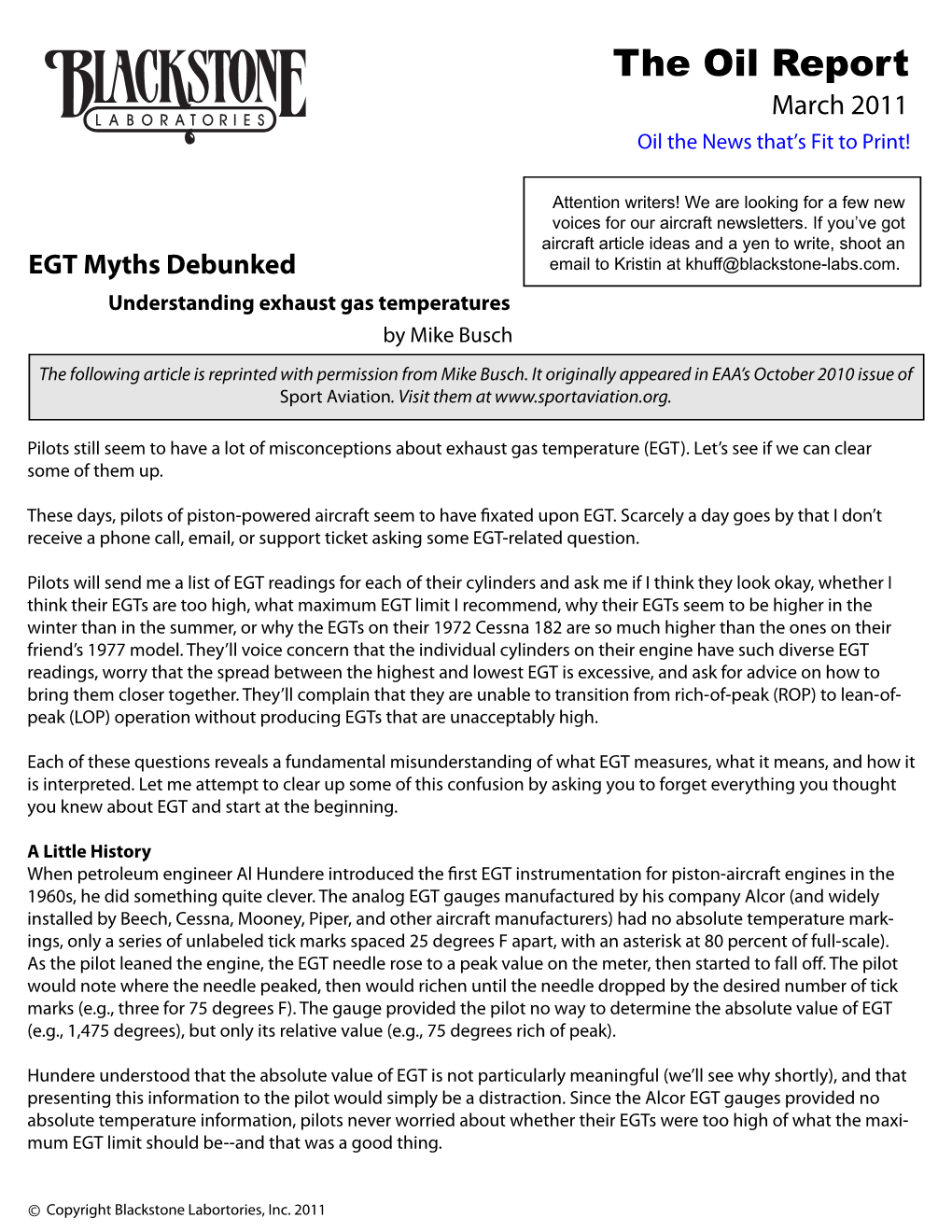
Load more
Recommended publications
-
Éc 84 2 132 E 118 2 C 130 2 136
US 2011 0023812A1 (19) United States (12) Patent Application Publication (10) Pub. No.: US 2011/0023812 A1 Inden (43) Pub. Date: Feb. 3, 2011 (54) CRANKSHAFT-FREE INTERNAL (52) U.S. Cl. ..................................................... 123/1973 COMBUSTON ENGINE OF IMPROVED EFFICIENCY (57) ABSTRACT (75) Inventor: Michael Inden, Belmont, CA (US) The crankshaft-free internal combustion engine which is of the type that contains at least one cylinder having a longitu Correspondence Address: dinal axis, at least one piston that has a pivot pin and is MICHAEL INDEN slidingly installed in the cylinder, a main driveshaft having a 2241 SEMERAAVENUE central axis, which is offset at a distance from the longitudinal BELMONT, CA 94002-1521 (US) axis of the cylinder, and a cylindrical eccentric which is eccentrically and non-rotationally secured on the main drive (73) Assignee: ALEXANDER KHAMSKY shaft A distinguishing feature of the engine is a connecting rod that has a Substantially L-shaped configuration formed by (21) Appl. No.: 12/462,315 one portion which is substantially straight and is pivotally connected to the pivot pin of the cylinder and a second portion (22) Filed: Aug. 3, 2009 which is substantially transverse to the first portion and piv O O otally receives the cylindrical eccentric. The distance from Publication Classification the central axis of the main driveshaft to the longitudinal axis (51) Int. Cl. of the cylinder is always greater than 0. Such a construction FI6C 7700 (2006.01) significantly improves efficiency of the engine. 134 82 2 2 éC 84 2 132 e 118 2 C 130 2 136 74 Patent Application Publication Feb. -
EGT Myths Debunked Understanding Exhaust Gas Temperatures by MIKE BUSCH
MIKE BUSCH HANDS ON / SAVVY AVIATOR EGT Myths Debunked Understanding exhaust gas temperatures BY MIKE BUSCH PILOTS STILL SEEM TO have a lot of misconceptions about exhaust gas (See Figure 1). As the pilot leaned the temperature (EGT). Let’s see if we can clear some of them up. engine, the EGT needle rose to a peak value These days, pilots of piston-powered aircraft seem to be fi xated on the meter, then started to fall off . The upon EGT. Scarcely a day goes by that I don’t receive a phone call, pilot would note where the needle peaked, e-mail, or support ticket asking some EGT-related question. then would richen until the needle dropped Pilots will send me a list of EGT readings for each of their cylin- by the desired number of tick marks (e.g., ders and ask me if I think they look okay, whether I think their EGTs three for 75 degrees Fahrenheit). The gauge are too high, what maximum EGT limit I recommend, why their provided the pilot no way to determine the EGTs seem to be higher in the winter than in the summer, or why absolute value of EGT (e.g., 1,475 degrees), the EGTs on their 1972 Cessna 182 are so much higher than the ones but only its relative value (e.g., 75 degrees on their friend’s 1977 model. They’ll voice concern that the individ- rich of peak). ual cylinders on their engine have such diverse EGT readings, worry Hundere understood that the absolute that the spread between the highest and lowest EGT is excessive, value of EGT is not particularly meaningful and ask for advice on how to bring them closer together. -
Indian Motorcycle Rider's Manual
2019 RIDER’S MANUAL ! WARNING Read, understand, and follow all of the instructions and safety precautions in this manual and on all product labels. Failure to follow the safety precautions could result in serious injury or death. ! WARNING Operating, servicing, and maintaining a passenger vehicle or off-road vehicle can expose you to chemicals including engine exhaust, carbon monoxide, phthalates, and lead, which are known to the State of California to cause cancer and birth defects or other reproductive harm. To minimize exposure, avoid breathing exhaust, do not idle the engine expect as necessary, service your vehicle in a well-ventilated area and wear gloves or wash your hands frequently when servicing your vehicle. For more information go to www.P65Warnings.ca.gov/passenger-vehicle. 2019 Rider’s Manual Chief Dark Horse® Chief® Vintage Chieftain® Dark Horse® Indian Springfield® Dark Horse® Chieftain® Limited Indian Springfield® Roadmaster® Chieftain® Classic Roadmaster® Limited Chieftain® Copyright 2018 Indian Motorcycle International, LLC All information contained within this publication is based on the latest product information available at the time of publication. Product improvements or other changes may result in differences between this manual and the motorcycle. Depictions and/or procedures in this publication are intended for reference use only. No liability can be accepted for omissions or inaccuracies. Indian Motorcycle Company reserves the right to make changes at any time, without notice and without incurring obligation to make the same or similar changes to motorcycles previously built. Any reprinting or reuse of the depictions and/or procedures contained within, whether whole or in part, is expressly prohibited. -
Aviation Maintenance Alerts
ADVISORY CIRCULAR 43-16A AVIATION MAINTENANCE ALERTS ALERT DECEMBER NUMBER 2009 377 CONTENTS AIRPLANES BEECH ........................................................................................................................................1 CANADAIR ................................................................................................................................3 CESSNA ......................................................................................................................................6 PIPER...........................................................................................................................................8 HELICOPTERS BELL............................................................................................................................................9 POWERPLANTS ECI CYLINDER........................................................................................................................13 LYCOMING..............................................................................................................................15 ROTAX......................................................................................................................................15 ACCESSORIES KELLY TURBOCHARGER.....................................................................................................16 MOST AIRCRAFT FLUSH-MOUNT FUEL CAP ..................................................................17 AIR NOTES INTERNET SERVICE DIFFICULTY REPORTING (iSDR) WEB SITE...............................19 -
Torque Accuracy Improvement Via Explicit Torque Feedback Control for Internal Combustion Spark Ignition Engines Anwar Alkeilani Wayne State University
Wayne State University Wayne State University Dissertations 1-1-2016 Torque Accuracy Improvement Via Explicit Torque Feedback Control For Internal Combustion Spark Ignition Engines Anwar Alkeilani Wayne State University, Follow this and additional works at: https://digitalcommons.wayne.edu/oa_dissertations Part of the Electrical and Computer Engineering Commons, and the Mechanical Engineering Commons Recommended Citation Alkeilani, Anwar, "Torque Accuracy Improvement Via Explicit Torque Feedback Control For Internal Combustion Spark Ignition Engines" (2016). Wayne State University Dissertations. 1418. https://digitalcommons.wayne.edu/oa_dissertations/1418 This Open Access Dissertation is brought to you for free and open access by DigitalCommons@WayneState. It has been accepted for inclusion in Wayne State University Dissertations by an authorized administrator of DigitalCommons@WayneState. TORQUE ACCURACY IMPROVEMENT VIA EXPLICIT TORQUE FEEDBACK CONTROL FOR INTERNAL COMBUSTION SPARK IGNITION ENGINES by ANWAR ALKEILANI DISSERTATION Submitted to the Graduate School, of Wayne State University, Detroit, Michigan in partial fulfillment of the requirements for the degree of DOCTOR OF PHILOSOPHY 2016 MAJOR: ELECTRICAL ENGINEERING Approved By: _____________________________________ Advisor Date _____________________________________ Advisor Date _____________________________________ _____________________________________ _____________________________________ DEDICATION To my beloved parents, who raised me tenderly, Dr. Aref Alkeilani and Karama Albarazi, to all of my dear sisters and brothers who supported me, to my treasured wife and life partner Ruqaia Muradagha who stood by and comforted me, and our children Karama, Aref and Mustafa for their patience, to my precious sisters-in-law and brothers-in-law for their encouragement, and to Songping Yu, my previous manager, for all his assistance and cooperation. ii ACKNOWLEDGEMENTS I am much obleeged perpetually to Professors Le Yi Wang and Hao Ying, who contributed time to my research. -
Cold Test Rejection Analysis and Quality Improvement
ISSN (Print) : 2320 – 3765 ISSN (Online): 2278 – 8875 International Journal of Advanced Research in Electrical, Electronics and Instrumentation Engineering (A High Impact Factor, Monthly, Peer Reviewed Journal) Website: www.ijareeie.com Vol. 8, Issue 3, March 2019 Cold Test Rejection Analysis and Quality Improvement Poonguzhali.I1, Gloria Pauline Diamond2, Prithi.P3 Assistant Professor, Department of ECE, Panimalar Institute of Technology, Chennai, Tamilnadu, India1 UG Student, Department of ECE, Panimalar Institute of Technology, Chennai, Tamilnadu, India2 UG Student, Department of ECE, Panimalar Institute of Technology, Chennai, Tamilnadu, India3 ABSTRACT: On manufacturing process of Engines, the Engine assembly line consists of 32 machines that perform various activities that contribute to production of engines. Our project involves the identification of the major problem in those machines and choosing one of the best problems (cold test) and improving the pass ratio of that particular machine. After the in-depth analysis of the cold testing we infer five basic problems like the crank and cam issue, oil leak, fuel leak, vibrations and breakaway torque. Out of these problems the crank and cam issue was chosen and various techniques were performed to reduce the rejection count in order to reduce the rejection in the overall cold testing. Each problem is entitled around the production line of the engines, and involves out of the box solution for complex problem. Solving these problems would eventually improve the quality of the manufacturing process by 80%. KEYWORDS: Cold test, Crank and Cam, GEMS, Crimping, Rejection analysis, Pass ratio I. INTRODUCTION The quality of a machine is improved by performing some improvement activities. -
01 2007 NG6 Engines WB
Table of Contents 2007 NG6 Engines Workbook Subject Page New NG6 Engines for 2007 . .5 New Engine Designations . .6 Crankcase Identification . .7 New NG6 Versions . .8 New Vehicles for 2007 . .8 Engine Mechanical Overview . .9 Crankcase . .9 Bolts . .10 Cylinder Head Cover . .10 Cylinder Head . .11 Valvetrain . .11 Camshafts . .11 VANOS . .12 Valvetronic . .12 Gaskets and Seals . .13 Head Gasket . .13 Oil Pan Gasket . .13 Bedplate Sealing . .13 Crankshaft Drive Components . .13 Crankshaft . .13 Piston and Connecting Rods . .13 Torsional Vibration Damper . .13 Initial Print Date: 10/06 Revision Date: 12/06 Table of Contents Subject Page Intake Manifold . .14 Crankcase Ventilation . .20 Crankcase Ventilation (N51 and N52KP) . .20 Crankcase Ventilation (N54) . .21 Crankcase Ventilation System Overview (N54) . .22 Crankcase Ventilation System Overview (N54) . .23 Summary of Mechanical Changes . .26 MSD80 Engine Management Overview (E9X) . .28 MSV80 Engine Management Overview (E70) . .30 Air Management . .32 Air Management N52KP and N51 . .32 Throttle Valve . .32 Air Intake Ducting . .33 Air Intake Ducting Function . .34 Exhaust Gas Turbocharging . .36 Bi-turbocharging . .37 Boost-pressure Control . .38 Blow-off Control . .39 Charge-air Cooling . .40 Load Control . .. -
Sulzer RTA-C, Technology Review
Technology Review This document, and more, is available for downloading at Martin's Marine Engineering Page - www.dieselduck.net Sulzer RTA84C and RTA96C engines: The reliable driving forces for large, fast containerships by Rudolf Demmerle Product Manager, RTA-C Engines Wärtsilä NSD Switzerland Ltd, Winterthur October 1997 Contents Page Introduction 3 Market factors in containership propulsion 5 Market success of the RTA-C engines 7 Engine parameters 10 Development goals 12 Design features of RTA-C engines 13 Engine management systems 31 Service experience of RTA84C engines 33 Test results from the first RTA96C 39 Conclusion 47 Bibliography 47 Appendix: Main data of RTA-C engines 48 1 This document, and more, is available for downloading at Martin's Marine Engineering Page - www.dieselduck.net Fig. 1 The first 12-cylinder Sulzer RTA96C engine on test at Diesel United Ltd, Aioi, Japan [7797-3038] Summary Containerships continue to be a most interesting sector of the newbuilding market. Not only is it still a strong market in terms of overall volume but it also puts continual demands on engine development. Larger, faster containerships require high-output propulsion engines which must operate most reliably with the least time out of service. Sulzer diesel engines have proved to be particularly successful in this market sector. To the RTA84C type which was introduced in 1988, and upgraded in 1993, has been added the RTA96C to extend the power range up to 89 640 bhp (65 880 kW) for the new generation of large ‘Post-Panamax’ containerships that load 6000 TEU or more. The Sulzer RTA84C is the leader in this market sector, with 155 engines delivered or on order. -
MIS 2018 Sportsman Rules 01082018
Madison International Speedway 2018 NASCAR Sportsman Rules 1-8-2018 The Guidelines and/or regulations set forth herein are designed to provide for the orderly conduct of racing events and to establish minimum acceptable requirements for such events. These guidelines shall govern the condition of events and participation therein. They are intended as a guide for the conduct of events and are in no way a guarantee against injury or death to a participant, spectator, or official. The Director of competition, or his authorized designate, shall be empowered to permit minor deviation from any of the guidelines and or regulations herein, or impose any further restriction, which, in his or her opinion, does not alter the purpose of the organization. Deviation of these guidelines and or regulations will be the responsibility of MIS officials, whose decisions are final. All drivers competing in this division will be required to obtain an annual or temporary NASCAR License. The rules as outlined below will be applied to all cars – however minor variations may be allowed on cars that race at area tracks and follow their rules. MIS may impose weight penalties for these variations. MIS may change any rule at any time in an effort to reduce the cost of racing, maintain equal competition, or improve safety. INDEX: A. SEATS B. SAFETY BELTS C. DRIVING COMPARTMENT D. DRIVER AND DRIVER’S ATTIRE E. CHASSIS ELIGIBILITY F. WHEELBASE AND TREAD WIDTH G. GROUND CLEARANCE H. CHASSIS I. ROLL CAGE J. INTERIOR K. SPINDLES, HUBS, STEERING L. SUSPENSION M. BRAKES N. METRIC EXCEPTION O. FUEL AND FUEL CONTAINER P. -
D2009 Neu Englisch.Qxd
® 2009. The engine for construction. 15-50 kW at 1500-3000 rpm These are the characteristics of the 2009: 3 and 4 cylinder naturally aspirated in-line engines. 4 cylinder also as turbocharged version. Water cooled . Compact engine design. Innovative and efficient injection- and combustion system. Customized component system with many different peripheral parts. Cold starting ability even under extreme climatic conditions. Full power PTO at flywheel end for axial or radial drives, two optional laid back PTOs from gear end cover. Your benefit: u Compact engine, thus reducing equipment redesigning cost. u Convincing power to weight ratio. u Low exhaust emissions meeting EU-RL 97/68 Stage 2 and US-EPA Nonroad (Tier 2). u High reliability combined with long maintenance intervals means less after sales cost for your customers. u Impressed low level on complexity helps your after sales business. u Engine description Type of cooling: Water-cooled, water circulation pump driven by a V belt, thermostat and integrated bypass system Crankcase: Ribbed, thin-wall grey cast iron with detachable sump Crankcase breather: Closed-circuit breather Cylinder head: Adaptable inlet manifold Valve arrangement/ Timing: Overhead valves in cylinder head, one inlet and one exhaust valve per cylinder, actuated via hydraulic tappets, push rods and rocker arms, driven by anti-backslash helical cut gears and camshaft Piston Three-ring piston, two compressions rings and one oil scraper ring Piston cooling: Splash oil-cooled with under crown oil jets on turbo version Connecting -
THREE-Cyllnder Dlesel Englne in Hyundai Grand
TECHNOLOGY ENGINES THREE-CYLINDER DIESEL ENGINE IN HYUNDAI GRAND i10 Hyundai Motor Company (HMC) decided to develop the Grand i10, a higher-end version of i10, to cater to the Indian high-end compact car market. Powering the vehicle is the U2 1.1 l three-cylinder diesel engine, which offers significant fuel economy and enjoyable driving experience. It has been mass-produced and sold since 2011, and the performance and fuel efficiency has already been proven in the European market. AUTHORS LEE BYUNG CHUL is Part Manager in the Passenger Car Diesel Engine Engineering Design department at Hyundai Motor Com- pany in Namyang (South Korea). PYO SOON CHAN is Part Manager in the Passenger Car Diesel Engine Test department at Hyundai Motor Company in Namyang (South Korea). INTRODUCTION adapted to terrain and driving condi- tions of India. The U2 1.1 l three-cylinder diesel engine Produced at Hyundai’s engine plant in achieves a class-leading CO2 emission of Chennai, Tamil Nadu, the U2 1.1 l three- CHO SUNG MOON is Part Manager in the Passenger Car 85 g/km. In the development of this cylinder diesel engine delivers a maxi- Diesel Engine Test department at engine, engineers at Hyundai focussed on mum power of 68 hp at 4,000 rpm, better Hyundai Motor Company in Namyang four key areas: than many of its competitors in the mar- (South Korea). :: Better fuel economy, which is offered ket. Torque peaks at about 160 Nm in an by competing models in the same rpm range of 1,500 to 2,750. -
2011 Dabla Englisch
® u Standard engines The engine for construction equipment. ...............................................................................................................................2011. ........................... 12.5 - 65 kW at 1500 - 2800 rpm Engines with conventional cooling system. Best.-Nr. 0031 1949 / 04 / 00 / MM-V These are the characteristics of the 2011: 2-, 3- and 4-cylinder naturally aspirated in-line engines. 3- and 4-cylinder engines also turbocharged. Oil-cooled (with conventional cooling system). 13% more power in comparison to the successor 1011F. 100% extended belt change interval. PTO for hydraulic pump drive is increased by 55%. All service points on one engine side. Compact engine design. Your benefit: u Designed specifically for construction equipment the dimensions of the engines are DEUTZ AG extremely compact. Thus reducing installation costs. Deutz-Mülheimer Str. 147-149 u The new engines, which display an exceptional power /weight ratio, perform brilliantly D-51057 Köln while at the same time complying with the stricter regulations on environmental Telefon: ++49(0)221-822-2510 protection. ® Telefax: ++ 49 (0) 2 21-8 22-25 29 u Cooling and lubrication with oil avoid corrosion and cavitation. High reliability Knowing it´s DEUTZ. Internet: http://www.deutz.de combined with long maintenance intervals and less wear parts. u Low noise emission, no expensive insulation measures for noise reduction. u Engine Description u Technical Data Engine type F2M2011 F3M2011 BF3M2011 F4M2011 BF4M2011 Type of cooling:................. Oil-cooled (with conventional cooling system) Numer of cylinder 2 3 3 4 4 Crankcase:........................... Grey cast iron Crankcase Bore/stroke mm 94/112 94/112 94/112 94/112 94/112 breather:.............................. Closed-circuit breather Displacement l 1.55 2.33 2.33 3.11 3.11 Compression ratio 18.5 18.5 17.5 18.5 17.5 Cylinder head: ..................