Bio-Mimicking Rotary Nanomotors
Total Page:16
File Type:pdf, Size:1020Kb
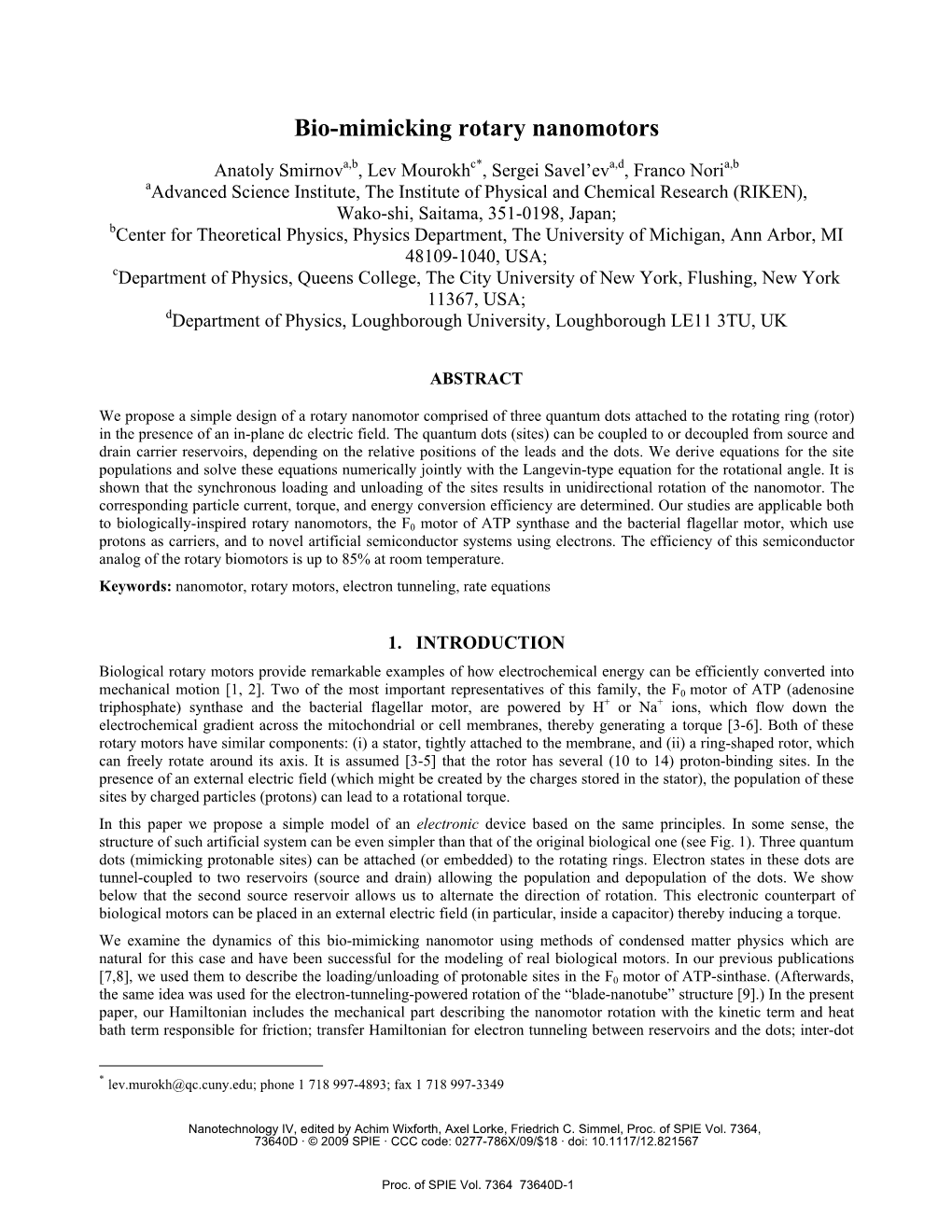
Load more
Recommended publications
-
Appendix B: Soft Starter Application Considerations BBB
AAPPENDIXPPENDIX APPENDIX B: SOFT STARTER APPLICATION CONSIDERATIONS BBB TABLE OF CONTENTS Appendix B: Soft Starter Application Considerations �� � � � � � � � � � � � � � � � � � � � � � � B–1 B�1 – Motor Suitability and Associated Considerations� � � � � � � � � � � � � � � � � � � � � B–2 B�1�1 – Suitability� � � � � � � � � � � � � � � � � � � � � � � � � � � � � � � � � � � � � � � � � � � � � � B–2 B�1�2 – Induction Motor Characteristics �� � � � � � � � � � � � � � � � � � � � � � � � � � � � � � � � � B–2 B�1�3 – Rating� � � � � � � � � � � � � � � � � � � � � � � � � � � � � � � � � � � � � � � � � � � � � � � � B–2 B�1�4 – Maximum Motor Cable Length� � � � � � � � � � � � � � � � � � � � � � � � � � � � � � � � � � B–3 B�1�5 – Power Factor Correction Capacitors �� � � � � � � � � � � � � � � � � � � � � � � � � � � � � � � B–3 B�1�6 – Lightly Loaded Small Motors � � � � � � � � � � � � � � � � � � � � � � � � � � � � � � � � � � � B–3 B�1�7 – Motors Installed with Integral Brakes � � � � � � � � � � � � � � � � � � � � � � � � � � � � � � B–3 B�1�8 – Older Motors� � � � � � � � � � � � � � � � � � � � � � � � � � � � � � � � � � � � � � � � � � � � B–3 B�1�9 – Wound-rotor or Slip-ring Motors � � � � � � � � � � � � � � � � � � � � � � � � � � � � � � � � B–3 B�1�10 – Enclosures � � � � � � � � � � � � � � � � � � � � � � � � � � � � � � � � � � � � � � � � � � � � B–3 B�1�11 – Efficiency �� � � � � � � � � � � � � � � � � � � � � � � � � � � � � � � � � � � � � � � � � � � � � B–4 B�1�12 – High-Efficiency Motors � � � � � � -
Parameters Effects on Force in Tubular Linear Induction Motors with Blocked Rotor
Proc. of the 5th WSEAS/IASME Int. Conf. on Electric Power Systems, High Voltages, Electric Machines, Tenerife, Spain, December 16-18, 2005 (pp92-97) Parameters Effects on Force in Tubular Linear Induction Motors with Blocked Rotor REZA HAGHMARAM(1,2), ABBAS SHOULAIE(2) (1) Department of Electrical Engineering, Imam Hosein University, Babaie Highway, Tehran (2) Department of Electrical Engineering, Iran University of Science & Technology, Narmak, Tehran IRAN Abstract: This paper is concerned with the study of several parameters effects on longitudinal force applied on the rotor in the generator driven air-core tubular linear induction motors with blocked rotor. With developing the motor modeling by involving temperature equations in the previous computer code, we first study variations of the coils and rings temperatures and the effect of the temperature on the rotor force. In the next section, the effect of the rotor length on the rotor force is studied and it is shown that there is an almost linear relation between the rotor length and the rotor force. Finally we have given the optimum time step for solving the state equations of the motor and calculating the force. By this time step the code will have reasonable speed and accuracy. These studies can be useful for the force motors and for finding a view for dynamic state analysis of the acceleration motors. Keywords: - Air Core Tubular Linear Induction Motor, Coilgun, Linear Induction Launcher 1 Introduction the value of coils and rings currents and calculating Tubular Linear Induction Motors (TLIMs) may the gradient of mutual inductance between coils and have unique applications as electromagnetic rings, we can calculate the force applied on the launchers with very high speed and acceleration rotor [3]. -
Pulsed Rotating Machine Power Supplies for Electric Combat Vehicles
Pulsed Rotating Machine Power Supplies for Electric Combat Vehicles W.A. Walls and M. Driga Department of Electrical and Computer Engineering The University of Texas at Austin Austin, Texas 78712 Abstract than not, these test machines were merely modified gener- ators fitted with damper bars to lower impedance suffi- As technology for hybrid-electric propulsion, electric ciently to allow brief high current pulses needed for the weapons and defensive systems are developed for future experiment at hand. The late 1970's brought continuing electric combat vehicles, pulsed rotating electric machine research in fusion power, renewed interest in electromag- technologies can be adapted and evolved to provide the netic guns and other pulsed power users in the high power, maximum benefit to these new systems. A key advantage of intermittent duty regime. Likewise, flywheels have been rotating machines is the ability to design for combined used to store kinetic energy for many applications over the requirements of energy storage and pulsed power. An addi - years. In some cases (like utility generators providing tran- tional advantage is the ease with which these machines can sient fault ride-through capability), the functions of energy be optimized to service multiple loads. storage and power generation have been combined. Continuous duty alternators can be optimized to provide Development of specialized machines that were optimized prime power energy conversion from the vehicle engine. for this type of pulsed duty was needed. In 1977, the laser This paper, however, will focus on pulsed machines that are fusion community began looking for an alternative power best suited for intermittent and pulsed loads requiring source to capacitor banks for driving laser flashlamps. -
Open Fwong Phd Dissertation.Pdf
The Pennsylvania State University The Graduate School Department of Chemistry CATALYTIC NANOMOTORS AND MICROPUMP SYSTEMS UTILIZING ALTERNATE FUELS A Dissertation in Chemistry by Flory K. Wong © 2016 Flory K. Wong Submitted in Partial Fulfillment of the Requirements for the Degree of Doctor of Philosophy December 2016 ii The dissertation of Flory K. Wong was reviewed and approved* by the following: Ayusman Sen Distinguished Professor of Chemistry Dissertation Advisor Chair of Committee Thomas E. Mallouk Evan Pugh University Professor of Chemistry, Biochemistry, Molecular Biology, and Physics Head of the Department of Chemistry Raymond E. Schaak DuPont Professor of Materials Chemistry Darrell Velegol Distinguished Professor of Chemical Engineering *Signatures are on file in the Graduate School. iii ABSTRACT Colloidal assemblies of self-powered active particles have become a focus area of research. Ranging from microscopic particle suspensions to nanoscale molecules, these systems transduce chemical energy into mechanical motion across multiple length scales following a variety of mechanisms. Understanding the energy transduction processes and the subsequent nature of particle dynamics offers unprecedented opportunities to explore the physics of small-scale colloidal systems and to harness their behavior in many useful applications. However, over a decade after the initial discovery of autonomous bimetallic nanorods, we continue to struggle to bring such systems into real-world applications. Part of the setback has been the in-depth research into hydrogen peroxide fuel. While the studies have built up the fundamental knowledge necessary for the advancement of the field, we have yet to do the same for other systems that employ alternate fuels. This dissertation aims to fill that void by developing nano- and micromotor and pump systems that does not rely on traditional hydrogen peroxide fuel, uses novel material by taking inspiration in other areas of research, and complete in-depth studies to provide a clear understanding of such systems. -
An Engineering Guide to Soft Starters
An Engineering Guide to Soft Starters Contents 1 Introduction 1.1 General 1.2 Benefits of soft starters 1.3 Typical Applications 1.4 Different motor starting methods 1.5 What is the minimum start current with a soft starter? 1.6 Are all three phase soft starters the same? 2 Soft Start and Soft Stop Methods 2.1 Soft Start Methods 2.2 Stop Methods 2.3 Jog 3 Choosing Soft Starters 3.1 Three step process 3.2 Step 1 - Starter selection 3.3 Step 2 - Application selection 3.4 Step 3 - Starter sizing 3.5 AC53a Utilisation Code 3.6 AC53b Utilisation Code 3.7 Typical Motor FLCs 4 Applying Soft Starters/System Design 4.1 Do I need to use a main contactor? 4.2 What are bypass contactors? 4.3 What is an inside delta connection? 4.4 How do I replace a star/delta starter with a soft starter? 4.5 How do I use power factor correction with soft starters? 4.6 How do I ensure Type 1 circuit protection? 4.7 How do I ensure Type 2 circuit protection? 4.8 How do I select cable when installing a soft starter? 4.9 What is the maximum length of cable run between a soft starter and the motor? 4.10 How do two-speed motors work and can I use a soft starter to control them? 4.11 Can one soft starter control multiple motors separately for sequential starting? 4.12 Can one soft starter control multiple motors for parallel starting? 4.13 Can slip-ring motors be started with a soft starter? 4.14 Can soft starters reverse the motor direction? 4.15 What is the minimum start current with a soft starter? 4.16 Can soft starters control an already rotating motor (flying load)? 4.17 Brake 4.18 What is soft braking and how is it used? 5 Digistart Soft Starter Selection 5.1 Three step process 5.2 Starter selection 5.3 Application selection 5.4 Starter sizing 1. -
Rolling Bearings and Seals in Electric Motors and Generators
Rolling bearings and seals in electric motors and generators ® SKF, @PTITUDE, BAKER, CARB, DUOFLEX, DURATEMP, ICOS, INSOCOAT, MARLIN, MICROLOG, MONOFLEX, MULTILOG, SEAL JET, SKF EXPLORER, SYSTEM 24 and WAVE are registered trademarks of the SKF Group. © SKF Group 2013 The contents of this publication are the copyright of the publisher and may not be reproduced (even extracts) unless permission is granted. Every care has been taken to ensure the accuracy of the information contained in this publication but no liability can be accepted for any loss or damage whether direct, indirect or consequential arising out of the use of the information contained herein. PUB 54/P7 13459 EN · August 2013 This publication supersedes publication 5230 E and 6230 EN. Certain image(s) used under license from Shutterstock.com. 1 Rolling bearings in electric machines 1 2 Bearing systems 2 3 Seals in electric machines 3 4 Tolerances and fits 4 5 Lubrication 5 6 Bearing mounting, dis mounting and motor testing 6 7 Bearing damage and corrective actions 7 8 SKF solutions 8 Rolling bearings and seals in electric motors and generators A handbook for the industrial designer and end-user 2 Foreword This SKF applications, lubrication and maintenance handbook for bearings and seals in electric motors and generators has been devel oped with various industry specialists in mind. For designers of electric machines1), this handbook provides the information needed to optimize a variety of bearing arrangements. For specialists working in various industries using electric machines, there are recommendations on how to maximize bearing service life from appropriate mounting, mainten ance and lubrication. -
Electric Motors
SPECIFICATION GUIDE ELECTRIC MOTORS Motors | Automation | Energy | Transmission & Distribution | Coatings www.weg.net Specification of Electric Motors WEG, which began in 1961 as a small factory of electric motors, has become a leading global supplier of electronic products for different segments. The search for excellence has resulted in the diversification of the business, adding to the electric motors products which provide from power generation to more efficient means of use. This diversification has been a solid foundation for the growth of the company which, for offering more complete solutions, currently serves its customers in a dedicated manner. Even after more than 50 years of history and continued growth, electric motors remain one of WEG’s main products. Aligned with the market, WEG develops its portfolio of products always thinking about the special features of each application. In order to provide the basis for the success of WEG Motors, this simple and objective guide was created to help those who buy, sell and work with such equipment. It brings important information for the operation of various types of motors. Enjoy your reading. Specification of Electric Motors 3 www.weg.net Table of Contents 1. Fundamental Concepts ......................................6 4. Acceleration Characteristics ..........................25 1.1 Electric Motors ...................................................6 4.1 Torque ..............................................................25 1.2 Basic Concepts ..................................................7 -
Equating a Car Alternator with the Generated Voltage Equation by Ervin Carrillo
Equating a Car Alternator with the Generated Voltage Equation By Ervin Carrillo Senior Project ELECTRICAL ENGINEERING DEPARTMENT California Polytechnic State University San Luis Obispo 2012 © 2012 Carrillo TABLE OF CONTENTS Section Page Acknowledgments ......................................................................................................... i Abstract ........................................................................................................................... ii I. Introduction ........................................................................................................ 1 II. Background ......................................................................................................... 2 III. Requirements ...................................................................................................... 8 IV. Obtaining the new Generated Voltage equation and Rewinding .................................................................................................................................... 9 V. Conclusion and recommendations .................................................................. 31 VI. Bibliography ........................................................................................................ 32 Appendices A. Parts list and cost ...................................................................................................................... 33 LIST OF FIGURES AND TABLE Section Page Figure 2-1: Removed drive pulley from rotor shaft [3]……………………………………………. 4. -
Motor Starting Fundamentals
Application Guidance Notes: Technical Information from Cummins Generator Technologies AGN 090 – Motor Starting Fundamentals INTRODUCTION There are a number of aspects to be considered regarding the electrical supply required for starting a motor. Guidance is offered for Motor Starting applications, because ‘Motor Starting’ continues to create technical problems for Generating Set manufacturers. This guidance is intended to assist Generating Set manufacturers when they discuss with their customers, the characteristics of the motor or motors to be started. The information on the motor will determine the type and size of alternator that is nominated and assist in the selection of a suitable Generating Set. MOTOR DESIGN FUNDAMENTALS To help with identifying the information required for alternator sizing purposes, it is necessary to understand the basic design of an induction motor. Induction Motor Basics Motors are part of the family of Rotating Electrical Machines (REMs). The industry standard for REM's is IEC 60034. This international standard consists of many parts covering all aspects of performance from efficiency through to Duty Type and includes sections on ratings, protection, noise, vibration etc. Enclosure protection design can be from IP22 through to a totally enclosed design rated at IP55. For further information, refer to AGN066 – Alternator IP Protection. AGN 090 ISSUE B/1/11 Rotor The cylindrical rotor has a cast-in aluminum 'squirrel-cage' with round /oval bars running axially just below the surface of the cylindrically shaped, laminated steel constructed rotor core assembly. The aluminum cage-bars are circumferentially equi-spaced around the rotor, with the number of such bars being decided by a design relationship with stator winding's number of poles. -
2016-09-27-2-Generator-Basics
Generator Basics Basic Power Generation • Generator Arrangement • Main Components • Circuit – Generator with a PMG – Generator without a PMG – Brush type –AREP •PMG Rotor • Exciter Stator • Exciter Rotor • Main Rotor • Main Stator • Laminations • VPI Generator Arrangement • Most modern, larger generators have a stationary armature (stator) with a rotating current-carrying conductor (rotor or revolving field). Armature coils Revolving field coils Main Electrical Components: Cutaway Main Electrical Components: Diagram Circuit: Generator with a PMG • As the PMG rotor rotates, it produces AC voltage in the PMG stator. • The regulator rectifies this voltage and applies DC to the exciter stator. • A three-phase AC voltage appears at the exciter rotor and is in turn rectified by the rotating rectifiers. • The DC voltage appears in the main revolving field and induces a higher AC voltage in the main stator. • This voltage is sensed by the regulator, compared to a reference level, and output voltage is adjusted accordingly. Circuit: Generator without a PMG • As the revolving field rotates, residual magnetism in it produces a small ac voltage in the main stator. • The regulator rectifies this voltage and applies dc to the exciter stator. • A three-phase AC voltage appears at the exciter rotor and is in turn rectified by the rotating rectifiers. • The magnetic field from the rotor induces a higher voltage in the main stator. • This voltage is sensed by the regulator, compared to a reference level, and output voltage is adjusted accordingly. Circuit: Brush Type (Static) • DC voltage is fed External Stator (armature) directly to the main Source revolving field through slip rings. -
Unit VI Superconductivity JIT Nashik Contents
Unit VI Superconductivity JIT Nashik Contents 1 Superconductivity 1 1.1 Classification ............................................. 1 1.2 Elementary properties of superconductors ............................... 2 1.2.1 Zero electrical DC resistance ................................. 2 1.2.2 Superconducting phase transition ............................... 3 1.2.3 Meissner effect ........................................ 3 1.2.4 London moment ....................................... 4 1.3 History of superconductivity ...................................... 4 1.3.1 London theory ........................................ 5 1.3.2 Conventional theories (1950s) ................................ 5 1.3.3 Further history ........................................ 5 1.4 High-temperature superconductivity .................................. 6 1.5 Applications .............................................. 6 1.6 Nobel Prizes for superconductivity .................................. 7 1.7 See also ................................................ 7 1.8 References ............................................... 8 1.9 Further reading ............................................ 10 1.10 External links ............................................. 10 2 Meissner effect 11 2.1 Explanation .............................................. 11 2.2 Perfect diamagnetism ......................................... 12 2.3 Consequences ............................................. 12 2.4 Paradigm for the Higgs mechanism .................................. 12 2.5 See also ............................................... -
Design and Analysis of Rotor Shapes for IPM Motors in EV Power Traction Platforms
energies Article Design and Analysis of Rotor Shapes for IPM Motors in EV Power Traction Platforms Myeong-Hwan Hwang 1,2, Jong-Ho Han 1, Dong-Hyun Kim 1 and Hyun-Rok Cha 1,* 1 EV Components & Materials R&D Group, Korea Institute of Industrial Technology, 6 Cheomdan-gwagiro 208 beon-gil, Buk-gu, Gwangju 61012, Korea; [email protected] (M.-H.H.); [email protected] (J.-H.H.); [email protected] (D.-H.K.) 2 Department of Electrical Engineering, Chonnam National University, 77 Youngbong-ro, Buk-gu, Gwangju 61186, Korea * Correspondence: [email protected]; Tel.: +82-62-600-6212 Received: 7 September 2018; Accepted: 27 September 2018; Published: 29 September 2018 Abstract: The recent increase in the use of permanent magnet rotor motors underlines the importance of designing a rotor with an interior permanent magnet (IPM) structure, high power, and high efficiency. This study analyzed the rotor shapes of IPM motors for electric vehicles. Five types of motor rotors for automobiles were analyzed, including two hybrid vehicles. In order to minimize the number of variables in the analysis, the size of the motor stators was fixed and only the rotor shapes were modified to compare torque, torque ripple, efficiency and back-electromotive voltage. When the motor properties were compared as a function of rotor shape, the rotor shape with the smallest magnet volume exhibited excellent results for torque, efficiency and torque ripple. Keywords: traction motor; electric vehicle; interior permanent magnet; vehicle motor; electromagnetic field analysis; cogging torque 1. Introduction Various regulations in the car industry are being introduced to respond to environmental changes caused by global warming [1]; for example, electrically powered powertrains have been developed to reduce exhausted gas and improve the power efficiency of vehicles.