Mechanism of {332}<113> Twinning Formation in Cold-Rolled Ti-Nb-Ta-Zr-O Alloy
Total Page:16
File Type:pdf, Size:1020Kb
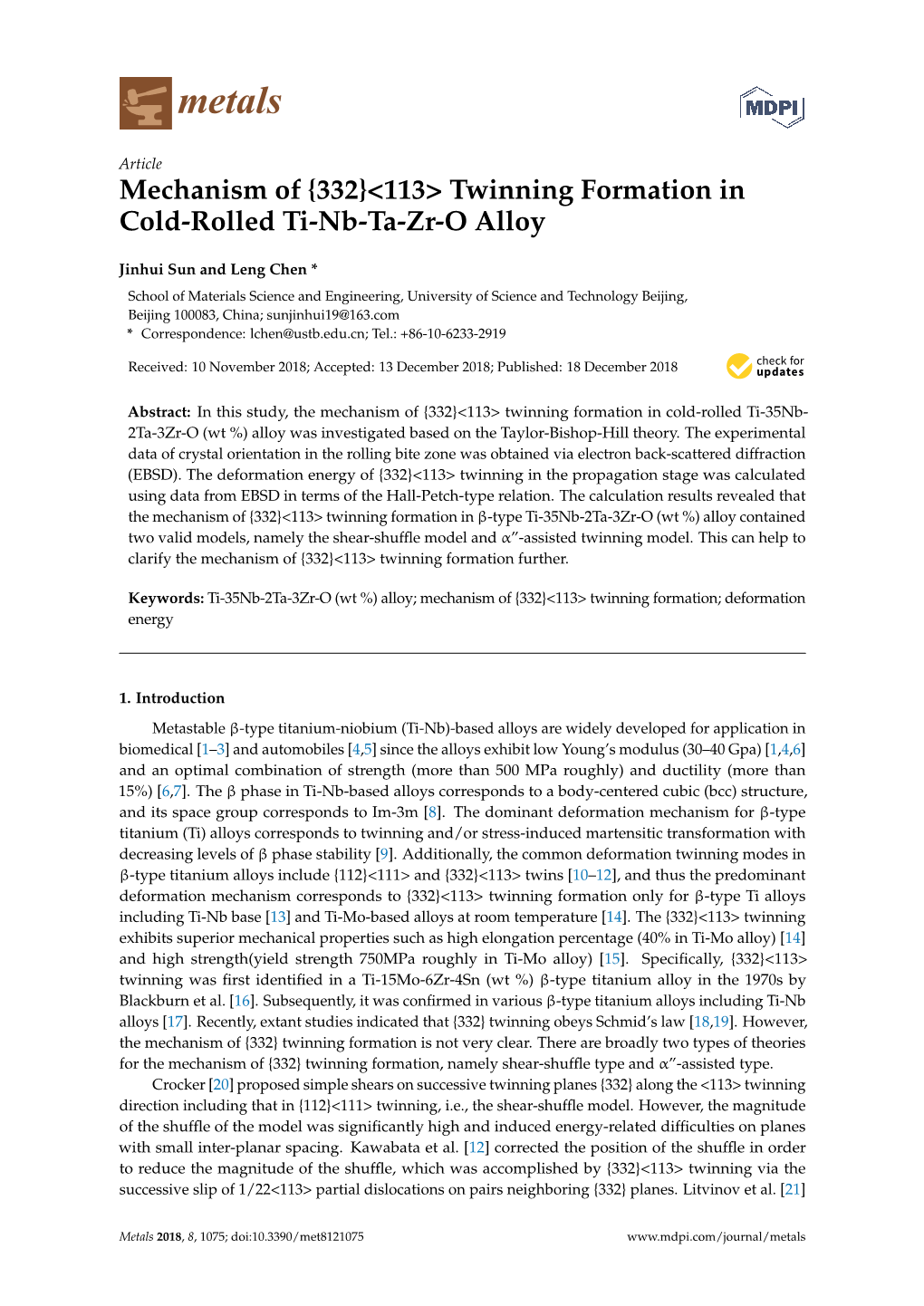
Load more
Recommended publications
-
Chapter 3 Design of Twinned Structure in Ti-Nb Gum Metal ………….…………………… 80 3.1 Literature Review ……………………………………….……………………
UC San Diego UC San Diego Electronic Theses and Dissertations Title Mechanical Properties Optimization via Microstructural Control of a Metastable β-type Ti-Nb based Gum Metal Permalink https://escholarship.org/uc/item/14g6d5sx Author Shin, Sumin Publication Date 2019 Peer reviewed|Thesis/dissertation eScholarship.org Powered by the California Digital Library University of California UNIVERSITY OF CALIFORNIA SAN DIEGO Mechanical Properties Optimization via Microstructural Control of a Metastable β- type Ti-Nb based Gum Metal A dissertation submitted in partial satisfaction of the requirements for the degree Doctor of Philosophy In Materials Science and Engineering by Sumin Shin Committee in charge: Professor Kenneth S. Vecchio, Chair Professor John Kosmatka Professor Jian Luo Professor Chia-Ming Uang Professor Kesong Yang 2019 Copyright Sumin Shin, 2019 All rights reserved. The Dissertation of Sumin Shin is approved, and it is acceptable in quality and form for publication on microfilm and electronically: Chair University of California Sand Diego 2019 iii TABLE OF CONTENTS Signature Page ……………………………………………………………………………………… iii Table of Contents …………………………………………………………………………………… iv List of Figures ……………………………………………………………………………………… vii List of Tables ………………………………………………………………………………………… xv Acknowledgement ………………………………………………………………………..………... xvi Vita ……………………………………………………………………………………….………. xviii Abstract of the Dissertation ……………………………………………………………………… xix Chapter 1 Introduction ……………………………………………………………………… 1 1.1 General introduction …………………………………………………………. -
A Review of Metastable Beta Titanium Alloys
metals Review A Review of Metastable Beta Titanium Alloys R. Prakash Kolli 1,* ID and Arun Devaraj 2 1 Department of Materials Science and Engineering, University of Maryland, College Park, MD 20742, USA 2 Physical and Computational Sciences Directorate, Pacific Northwest National Laboratory, Richland, WA 99354, USA; [email protected] * Correspondence: [email protected]; Tel.: +1-301-405-5217; Fax: 301-405-6327 Received: 21 May 2018; Accepted: 25 June 2018; Published: 30 June 2018 Abstract: In this article, we provide a broad and extensive review of beta titanium alloys. Beta titanium alloys are an important class of alloys that have found use in demanding applications such as aircraft structures and engines, and orthopedic and orthodontic implants. Their high strength, good corrosion resistance, excellent biocompatibility, and ease of fabrication provide significant advantages compared to other high performance alloys. The body-centered cubic (bcc) b-phase is metastable at temperatures below the beta transus temperature, providing these alloys with a wide range of microstructures and mechanical properties through processing and heat treatment. One attribute important for biomedical applications is the ability to adjust the modulus of elasticity through alloying and altering phase volume fractions. Furthermore, since these alloys are metastable, they experience stress-induced transformations in response to deformation. The attributes of these alloys make them the subject of many recent studies. In addition, researchers are pursuing development of new metastable and near-beta Ti alloys for advanced applications. In this article, we review several important topics of these alloys including phase stability, development history, thermo-mechanical processing and heat treatment, and stress-induced transformations. -
Investigation of the Martensitic Transformation and the Deformation Mechanisms Occurring in the Superelastic Ti-24Nb-4Zr-8Sn Alloy Yang Yang
Investigation of the martensitic transformation and the deformation mechanisms occurring in the superelastic Ti-24Nb-4Zr-8Sn alloy Yang Yang To cite this version: Yang Yang. Investigation of the martensitic transformation and the deformation mechanisms occurring in the superelastic Ti-24Nb-4Zr-8Sn alloy. Material chemistry. INSA de Rennes, 2015. English. <NNT : 2015ISAR0002>. <tel-01136204> HAL Id: tel-01136204 https://tel.archives-ouvertes.fr/tel-01136204 Submitted on 26 Mar 2015 HAL is a multi-disciplinary open access L'archive ouverte pluridisciplinaire HAL, est archive for the deposit and dissemination of sci- destin´eeau d´ep^otet `ala diffusion de documents entific research documents, whether they are pub- scientifiques de niveau recherche, publi´esou non, lished or not. The documents may come from ´emanant des ´etablissements d'enseignement et de teaching and research institutions in France or recherche fran¸caisou ´etrangers,des laboratoires abroad, or from public or private research centers. publics ou priv´es. THESE INSA Rennes présentée par sous le sceau de l’Université européenne de Bretagne pour obtenir le titre de Yang YANG DOCTEUR DE L’INSA DE RENNES ECOLE DOCTORALE : SDLM Spécialité : Sciences des Matériaux LABORATOIRE : ISCR/CM Thèse soutenue le 24.02.2015 Etude de la transformation devant le jury composé de : Joël DOUIN martensitique et des Directeur de Recherche CNRS - CEMES Toulouse / Président et Rapporteur Denis FAVIER mécanismes de Professeur des Universités - Université de Grenoble / Rapporteur Yulin HAO déformation -
Structure and Properties of Titanium Tantalum Alloys for Biocompatibility
Structure and Properties of Titanium Tantalum Alloys for Biocompatibility Dissertation Presented in Partial Fulfillment of the Requirements for the Degree Doctor of Philosophy in the Graduate School of The Ohio State University By Daniel E. Huber Graduate Program in Materials Science and Engineering The Ohio State University 2016 Committee: Dr. Hamish L. Fraser, Advisor Dr. David McComb Dr. Stephen Niezgoda Copyrighted by Daniel E. Huber 2016 Abstract In this thesis, the phase stability and elastic modulus of Ti–Ta simple binary alloys as well as alloys with small additions of ternary elements have been studied. The binary alloy from a nominal 8 to 28 wt.% Ta was first explored using a combinatorial approach. This approach included Laser Engineered Net Shape (LENS™) processing of materials and subsequent characterization by instrumented indentation and site specific Transmission Electron Microscopy (TEM). The composition range of 15 to 75 wt.% Ta was further explored by more traditional methods that included vacuum arc melting high purity elements, X-Ray Diffraction (XRD) and modulus measurements made by ultrasonic methods. Beyond the simple binary, alloys with low levels of ternary elements, oxygen, aluminum, zirconium and small additions of rare earth oxides were investigated. The crystal structure with space group Cmcm was chosen for it applicability with P63/mmc and !"3! sub group / super group symmetry. This provides a consistent crystal structure framework for the purpose of studying the α to β transformation pathway and associated α’ and α’’ martensitic phases. In this case, the pathway is defined by both the lattice parameters and the value of the parameter “y”, where the parameter “y” describes the atomic positions of the [002]α’’ plane. -
Design of Strain-Transformable Titanium Alloys Philippe Castany, Thierry Gloriant, Fan Sun, Frédéric Prima
Design of strain-transformable titanium alloys Philippe Castany, Thierry Gloriant, Fan Sun, Frédéric Prima To cite this version: Philippe Castany, Thierry Gloriant, Fan Sun, Frédéric Prima. Design of strain-transformable titanium alloys. Comptes Rendus Physique, Centre Mersenne, 2018, 19 (8), pp.710-720. 10.1016/j.crhy.2018.10.004. hal-01978011 HAL Id: hal-01978011 https://hal-univ-rennes1.archives-ouvertes.fr/hal-01978011 Submitted on 16 Jan 2019 HAL is a multi-disciplinary open access L’archive ouverte pluridisciplinaire HAL, est archive for the deposit and dissemination of sci- destinée au dépôt et à la diffusion de documents entific research documents, whether they are pub- scientifiques de niveau recherche, publiés ou non, lished or not. The documents may come from émanant des établissements d’enseignement et de teaching and research institutions in France or recherche français ou étrangers, des laboratoires abroad, or from public or private research centers. publics ou privés. Design of strain-transformable titanium alloys Conception d’alliages de titane transformables par déformation Philippe Castany1*, Thierry Gloriant1, Fan Sun2*, Frédéric Prima2 1 Univ Rennes, INSA Rennes, CNRS, ISCR – UMR 6226, F-35000 Rennes, France 2 PSL Research University, Chimie ParisTech-CNRS, Institut de Recherche de Chimie Paris, F- 75005 Paris, France * Corresponding authors: [email protected] ; [email protected] Résumé Parmi les alliages de titane, ceux de type β métastable sont les plus prometteurs pour améliorer les performances des matériaux utilisés actuellement dans de nombreux secteurs tels que l’aéronautique ou le biomédical. En particulier, certains alliages de titane β métastable sont sujet à une transformation martensitique induite sous contrainte (vers la phase α" orthorhombique) qui peut être ajustée afin d’obtenir de la superélasticité ou un effet TRIP (TRansformation Induced Plasticity). -
Mechanical Behaviour of Ti-Nb-Hf Alloys
Mechanical behaviour of Ti-Nb-Hf alloys R. Yang a, K.M. Rahman a, A.N. Rakhymberdiyev a, D. Dye a, V.A. Vorontsov a aDepartment of Materials, Royal School of Mines, Imperial College, Prince Consort Road, South Kensington, London SW7 2BP, UK Abstract Ti-(24-26)Nb-(2-4)Hf at.% alloys were designed by assuming that hafnium has a sim- ilar effect to zirconium in the Ti-Nb-Zr system. Alloy specimens were produced using vacuum arc melting and subsequently hot-rolled. Uniaxial tensile testing was then performed both at ambient temperature and in liquid nitrogen at -196◦C. While the alloys showed no obvious superelastic behaviour, they exhibited pronounced strain hardening and could achieve high elongations before failure (>30% engineer- ing strain). Post-mortem examination revealed that the mechanism of strain hard- ening was extensive bluef332g and/or f211g deformation twinning. Twinning was found to be more prevalent in alloys with 2 at.% Hf compared to those with 4 at.%. The cryogenic temperature deformation also promoted deformation twinning when compared to ambient temperature results. As is the case with other metastable β-Ti alloys, maintaining control over the precipitation of ! phases was found to be crucial for attaining desirable mechanical behaviour. Further, microstructural engineering and alloying may be used to develop strong, lightweight alloys based on the Ti-Nb-Hf system with beneficial strain hardening characteristics for energy absorption, cryogenic and biomedical applications. Key words: Titanium alloys, mechanical behaviour, deformation twinning, martensitic transformation, cryogenic testing 1 Introduction Stabilising the body-centred cubic (b.c.c.) β phase in titanium through al- loying can yield improved and often unique mechanical properties. -
Synthesis and Structural Characterization of Multifunctional Ti Alloy: Gum Metal a Thesis Submitted to the Graduate School of Na
SYNTHESIS AND STRUCTURAL CHARACTERIZATION OF MULTIFUNCTIONAL TI ALLOY: GUM METAL A THESIS SUBMITTED TO THE GRADUATE SCHOOL OF NATURAL AND APPLIED SCIENCES OF MIDDLE EAST TECHNICAL UNIVERSITY BY ORKUN ELÇİN IN PARTIAL FULFILLMENT OF THE REQUIREMENTS FOR THE DEGREE OF MASTER OF SCIENCE IN METALLURGICAL AND MATERIALS ENGINEERING JANUARY 2020 Approval of the thesis: SYNTHESIS AND STRUCTURAL CHARACTERIZATION OF MULTIFUNCTIONAL TI ALLOY: GUM METAL submitted by ORKUN ELÇİN in partial fulfillment of the requirements for the degree of Master of Science in Metallurgical and Materials Engineering, Middle East Technical University by, Prof. Dr. Halil Kalıpçılar Dean, Graduate School of Natural and Applied Sciences Prof. Dr. Hakan Gür Head of the Department, Met. and Mat. Eng. Prof. Dr. M. Vedat Akdeniz Supervisor, Met. and Mat. Eng., METU Prof. Dr. Amdulla Mekhrabov Co-Supervisor, Met. and Mat. Eng., METU Examining Committee Members: Prof. Dr. Rıza Gürbüz Metallurgical and Material Eng., METU Prof. Dr. M. Vedat Akdeniz Metallurgical and Material Eng., METU Prof. Dr. Amdulla Mekhrabov Metallurgical and Material Eng., METU Prof. Dr. Cevdet Kaynak Metallurgical and Material Eng., METU Assist. Prof. Dr. Mehmet Yıldırım Metallurgical and Material Eng., KTUN Date: 31.01.2020 I hereby declare that all information in this document has been obtained and presented in accordance with academic rules and ethical conduct. I also declare that, as required by these rules and conduct, I have fully cited and referenced all material and results that are not original to this work. Name, Last name : Orkun Elçin Signature : iv ABSTRACT SYNTHESIS AND STRUCTURAL CHARACTERIZATION OF MULTIFUNCTIONAL TI ALLOY: GUM METAL Elçin, Orkun Master of Science, Metallurgical and Materials Engineering Supervisor: Prof. -
Mechanisms of Deformation in Gum Metal TNTZ-O and TNTZ Titanium Alloys: a Comparative Study on the Oxygen Influence Magali Besse, Philippe Castany, Thierry Gloriant
Mechanisms of deformation in gum metal TNTZ-O and TNTZ titanium alloys: A comparative study on the oxygen influence Magali Besse, Philippe Castany, Thierry Gloriant To cite this version: Magali Besse, Philippe Castany, Thierry Gloriant. Mechanisms of deformation in gum metal TNTZ-O and TNTZ titanium alloys: A comparative study on the oxygen influence. Acta Materialia, Elsevier, 2011, 59 (15), pp.5982-5988. 10.1016/j.actamat.2011.06.006. hal-00926966 HAL Id: hal-00926966 https://hal.archives-ouvertes.fr/hal-00926966 Submitted on 13 Jan 2014 HAL is a multi-disciplinary open access L’archive ouverte pluridisciplinaire HAL, est archive for the deposit and dissemination of sci- destinée au dépôt et à la diffusion de documents entific research documents, whether they are pub- scientifiques de niveau recherche, publiés ou non, lished or not. The documents may come from émanant des établissements d’enseignement et de teaching and research institutions in France or recherche français ou étrangers, des laboratoires abroad, or from public or private research centers. publics ou privés. Mechanisms of deformation in gum metal TNTZ-O and TNTZ titanium alloys: A comparative study on the oxygen influence M. Besse, P. Castany, T. Gloriant INSA Rennes, UMR CNRS 6226 SCR/Chimie-Métallurgie, 20 avenue des Buttes de Coësmes, 35708 Rennes Cedex 7, France Abstract In this work, Ti–23Nb–0.7Ta–2Zr (TNTZ) and gum metal Ti–23Nb–0.7Ta–2Zr–1.2O (TNTZ-O) alloys were synthesized by cold crucible levitation melting with the objective of investigating the influence of oxygen on the deformation mechanisms. By tensile tests, electron backscatter diffraction, atomic force microscopy and transmission electron microscopy analyses, we showed that the deformation in the TNTZ-O alloy is only accommodated by dislocation slip. -
Microstructure and Mechanical Behavior of Superelastic Ti-24Nb-0.5O and Ti-24Nb-0.5N Biomedical Alloys A
Microstructure and mechanical behavior of superelastic Ti-24Nb-0.5O and Ti-24Nb-0.5N biomedical alloys A. Ramarolahy, Philippe Castany, F. Prima, P. Laheurte, Isabelle Péron, Thierry Gloriant To cite this version: A. Ramarolahy, Philippe Castany, F. Prima, P. Laheurte, Isabelle Péron, et al.. Microstruc- ture and mechanical behavior of superelastic Ti-24Nb-0.5O and Ti-24Nb-0.5N biomedical al- loys. Journal of the mechanical behavior of biomedical materials, Elsevier, 2012, 9, pp.83-90. 10.1016/j.jmbbm.2012.01.017. hal-00926952 HAL Id: hal-00926952 https://hal.archives-ouvertes.fr/hal-00926952 Submitted on 10 Jan 2014 HAL is a multi-disciplinary open access L’archive ouverte pluridisciplinaire HAL, est archive for the deposit and dissemination of sci- destinée au dépôt et à la diffusion de documents entific research documents, whether they are pub- scientifiques de niveau recherche, publiés ou non, lished or not. The documents may come from émanant des établissements d’enseignement et de teaching and research institutions in France or recherche français ou étrangers, des laboratoires abroad, or from public or private research centers. publics ou privés. Microstructure and mechanical behavior of superelastic Ti–24Nb–0.5O and Ti–24Nb–0.5N biomedical alloys A. Ramarolahya, P. Castanya, F. Primab, P. Laheurtec, I. Pérona, T. Glorianta, a INSA Rennes, UMR CNRS 6226 SCR / Chimie-Métallurgie, 20 avenue des Buttes de Coësmes, 35708 Rennes cedex 7, France b ENSCP Paris, UMR CNRS 7045 Laboratoire de Physico-Chimie des Surface, 11 rue Pierre et Marie Curie, 75231 Paris cedex 5, France c Université de Metz, UMR CNRS 7239 Laboratoire d’Etude des Microstructures et Mécanique des Matériaux, Ile du Saulcy, 57045 Metz cedex, France Abstract In this study, the microstructure and the mechanical properties of two new biocompatible superelastic alloys, Ti–24Nb–0.5O and Ti–24Nb–0.5N (at.%), were investigated. -
On the Mechanism of Superelasticity in Gum Metal (Ti-36Nb- 2Ta-3Zr-0.3O)
On the Mechanism of Superelasticity in Gum metal (Ti-36Nb- 2Ta-3Zr-0.3O) R. J. Talling1, R.J. Dashwood2, M. Jackson3 and D. Dye1 1 Department of Materials, Imperial College, South Kensington, London SW7 2AZ, UK. 2 Warwick Manufacturing Group, Warwick University, Coventry CV4 7AL, UK 3 Department of Engineering Materials, University of Sheffield, Sheffield S1 3JD UK. The deformation mechanisms of the recently developed multifunctional β titanium alloy, Gum metal were investigated with the aid of in-situ synchrotron X-ray diffraction (SXRD) and transmission electron microscopy (TEM). SXRD results showed that Gum metal undergoes a reversible stress-induced martensitic (α") phase transformation. It is suggested that oxygen may increase the resistance to shear by increasing C′ and limiting the extent of α" growth in Gum metal. Prior deformation was found to aid the formation of α" by providing nuclei, such as twins and stress-induced ω plates. The formation of {112}<111> deformation twins and stress-induced ω plates, both observed in TEM, are believed to be a result of a low G111 in this alloy. Features similar to the giant faults seen previously were observed in TEM, their formation is believed to be a result of {112}<111> shear. Keywords: Gum metal, martensitic phase transformation, titanium alloys, synchrotron radiation, transmission electron microscopy. 1. Introduction The recently developed multifunctional β titanium alloy, Gum metal (Ti-36Nb-2Ta-3Zr-0.3O) possesses low elastic modulus (~60 GPa), high strength (>1 GPa), high yield strain (~2.5%) and high ductility (>10%) at room temperature [1, 2]. This alloy also possesses the invar and elinvar properties and is highly cold workable. -
The Structure, Morphology, and Mechanical Properties of Ta-Hf-C Coatings Deposited by Pulsed Direct Current Reactive Magnetron Sputtering
coatings Article The Structure, Morphology, and Mechanical Properties of Ta-Hf-C Coatings Deposited by Pulsed Direct Current Reactive Magnetron Sputtering Alexis de Monteynard 1,2 , Huan Luo 3, Mohamed Chehimi 4, Jaafar Ghanbaja 5, Sofiane Achache 1,2, Manuel François 1 , Alain Billard 3 and Frédéric Sanchette 1,2,* 1 ICD LASMIS: Université de Technologie de Troyes, Antenne de Nogent, Pôle Technologique de Haute-Champagne, 52800 Nogent, France; [email protected] (A.M.); sofi[email protected] (S.A.); [email protected] (M.F.) 2 Nogent International Center for CVD Innovation, LRC CEA-ICD LASMIS, UT.T, Antenne de Nogent-52, Pôle Technologique de Haute-Champagne, 52800 Nogent, France 3 Institut FEMTO-ST: CNRS, UTBM, Univ. Bourgogne Franche-Comté, Site de Montbéliard, F-90010 Belfort Cedex, France; [email protected] (H.L.); [email protected] (A.B.) 4 Université Paris Est: ICMPE (UMR 7182), CNRS, UPEC, 2-8 rue Henri Dunant, 94320 Thiais, France; [email protected] 5 Institut Jean Lamour (UMR CNRS 7198), Université de Lorraine, 54000 Nancy, France; [email protected] * Correspondence: [email protected] Received: 31 January 2020; Accepted: 27 February 2020; Published: 28 February 2020 Abstract: Ta, Hf, TaCx, HfCx, and TaxHf1-xCy coatings were deposited by reactive pulsed Direct Current (DC) magnetron sputtering of Ta or Hf pure metallic targets in Ar plus CH4 gas mixtures. The properties have been investigated as a function of the carbon content, which is tuned via the CH4 flow rate. The discharge was characterized by means of Optical Emission Spectroscopy and, in our conditions, both Ta-C and Hf-C systems seem to be weakly reactive. -
Quasi-Static and Dynamic Compressive Behavior of Gum Metal: Experiment and Constitutive Model
ORIGINAL RESEARCH ARTICLE Quasi-Static and Dynamic Compressive Behavior of Gum Metal: Experiment and Constitutive Model KAROL MAREK GOLASIN´SKI, JACEK JANISZEWSKI, JUDYTA SIENKIEWICZ, TOMASZ PŁOCIN´SKI, MACIEJ ZUBKO, PAWEŁ S´WIEC, and ELZBIETA_ ALICJA PIECZYSKA The quasi-static and high strain rate compressive behavior of Gum Metal with composition Ti-36Nb-2Ta-3Zr-0.3O (wt pct) has been investigated using an electromechanical testing machine and a split Hopkinson pressure bar, respectively. The stress–strain curves obtained for Gum Metal tested under monotonic and dynamic loadings revealed a strain-softening effect which intensified with increasing strain rate. Moreover, the plastic flow stress was observed to increase for both static and dynamic loading conditions with increasing strain rate. The microstructural characterization of the tested Gum Metal specimens showed particular deformation mechanisms regulating the phenomena of strain hardening and strain softening, namely an adiabatic shear band formed at ~ 45 deg with respect to the loading direction as well as widely spaced deformation bands (kink bands). Dislocations within the channels intersecting with twins may cause strain hardening while recrystallized grains and kink bands with crystal rotation inside the grains may lead to strain softening. A constitutive description of the compressive behavior of Gum Metal was proposed using a modified Johnson–Cook model. Good agreement between the experimental and the numerical data obtained in the work was achieved. https://doi.org/10.1007/s11661-021-06409-z Ó The Author(s) 2021 I. INTRODUCTION Laboratories at the beginning of the twenty-first cen- tury.[1] The typical composition of Gum Metal is HIGH-STRENGTH construction materials, avail- Ti-36Nb-2Ta-3Zr-0.3O (in wt pct).