Railway Track Superstructure Research at Tampere University of Technology, Finland
Total Page:16
File Type:pdf, Size:1020Kb
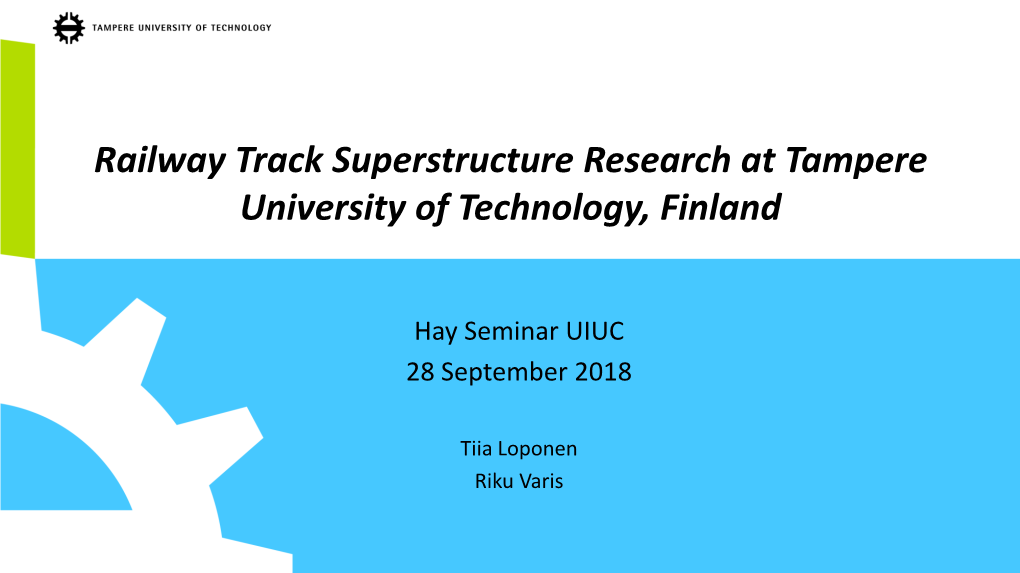
Load more
Recommended publications
-
Application of the Republic of Finland for the Relocation of the European Medicines Agency to Helsinki TABLE of CONTENTS
Application of the Republic of Finland for the relocation of the European Medicines Agency to Helsinki TABLE OF CONTENTS In safe hands 3 A SMOOTH TRANSITION 5 The new location of the European Medicines Agency 7 Continuity and a smooth handover 10 LIFE IN HELSINKI 13 Livable Helsinki 15 Easily accessible 17 Superb and internationally acclaimed education 21 Employment, social security and healthcare 26 A NEW CENTRE OF EXCELLENCE FOR THE PROTECTION OF HUMAN HEALTH 28 A strategic decision – EMA alongside ECHA 30 Helsinki – a hub for the life sciences 32 emahelsinki.fi 2 — Helsinki for EMA In safe hands The most crucial criterion for transferring the European Medicines Agency (EMA) to its new location is the ability to affect a smooth transition. To get the job done. Placing EMA alongside the European Chemicals Agency (ECHA) in Helsinki enhances the EU’s global regulatory competitiveness. Finland, simply stated, is known synergies to create a centre of Finland and the Helsinki region for its capacity to get the job excellence for the protection of possess top class expertise in the done. As a committed EU member human health. life sciences in terms of a high- and in our many roles on the glob- quality talent pool, world-leading al stage – from diplomatic conflict This decision is not a simple research, strong support servic- resolution initiatives to UN Peace- question of competition within es, and functioning networks of keeping missions – we are viewed the EU or among potential host collaboration among academia, as a partner to be entrusted with states. This is a global compe- industry and the public sector. -
Recovery from Acidification of Lakes in Finland, Norway and Sweden 1990–1999
Hydrology and Earth System Sciences, 5(3), 327–337Recovery from(2001) acidification © EGS of lakes in Finland, Norway and Sweden 1990–1999 Recovery from acidification of lakes in Finland, Norway and Sweden 1990–1999 B.L. Skjelkvåle1, J. Mannio2, A. Wilander3 and T. Andersen1 1 Norwegian Institute for Water Research, PB 173 Kjelsås, N-0411 Oslo, Norway 2 Finnish Environment Institute, PB.140, FIN-00251, Helsinki, Finland 3 University of Agricultural Sciences, PB 7050, S-75007 Uppsala, Sweden Email for corresponding author: [email protected] Abstract Sulphate deposition has decreased by about 60% in the Nordic countries since the early 1980s. Nitrogen deposition has been roughly constant during the past 20 years, with only a minor decrease in the late 1990s. The resulting changes in the chemistry of small lakes have been followed by national monitoring programmes initiated in the 1980s in Finland (163 lakes), Norway (100 lakes) and Sweden (81 lakes). These lakes are partly a subset from the survey of 5690 lakes in the Northern European lake survey of 1995. Trend analyses on data for the period 1990-1999 show that the non-marine sulphate concentrations in lakes have decreased significantly in 69% of the monitored lakes. Changes were largest in lakes with the highest mean concentrations. Nitrate concentrations, on the other hand, were generally low and showed no systematic changes. Concentrations of non-marine base cations decreased in 26% of the lakes, most probably an ionic-strength effect due to the lower concentrations of mobile strong-acid anions. Acid neutralising capacity increased in 32% of the lakes. -
Norway Sweden Finland Russia Iceland Canada Alaska (United
TERRITORIAL DISPUTES Aleutian Islands 1 Delimitation of the boundary between Russia and Norway in the Barents Sea PACIFIC 5 OCEAN 2 The sovereignty of Hans Island, claimed by Greenland (Denmark) and Canada 3 Management and control of the North-West Passage ºbetween the United States BERING SEA EXXON VALDEZ and Canada) Delimitation of the boundary between TRANS-ALASKA Anchorage BERING 4 PIPELINE SYSTEM (TAPS) STRAIT Alaska (United States) and Canada North-East in the Beaufort Sea Alaska Passage (United States) Chukotka 5 Delimitation of the boundary between Alaska (United States) and Russia Fairbanks in the Barents Sea BEAUFORT SEA New 4 Siberian Islands 3 Banks LAPTEV Island SEA Victoria Island Queen ARCTIC North-West Elizabeth OCEAN Canada Islands Passage Russia Alpha Ridge Lomonosov Ridge North Resolute NORTH Land Norilsk Bay POLE HUDSON Ellesmere Nansen BAY Nanisivik Island Gakkel KARA Ridge SEA Franz Novy Urengoï Thulé 2 Hans Josef Land Island (Russia) BAFFIN Baffin Novaya Island BAY Salekhard Zemlya Vorkuta Nadym Svalbard 1 Shtokman Canada Greenland (Norway) gas field (Denmark) USINSK DAVIS BARENTS Peshora STRAIT Bear Island SEA GREENLAND SEA (Norway) Nuuk Murmansk Jan Monchegorsk Mayen Island (Norway) Tromsø Archangelsk NORWEGIAN Apatity SEA Bodø Rovaniemi Severodvinsk Towards the major Major urban populations American ports Iceland 400,000 Finland Towards 200,000 Reykjavik 100,000 Western Europe 50,000 Sea routes which will come into Sweden St Petersburg permanent use within 10 or 15 ATLANTIC Norway Maritime areas claimed by years, -
Digitalisation Beyond Borders: a Case Study of Estonia and Finland's
Digitalisation Beyond Borders: A Case Study of Estonia and Finland’s Collaboration on Cross-Border Information and Communication Technology Development By: Rebecca Curry Student ID number: 1744828 Adviser’s name: Dr. Rod Dacombe Department of study: Political Economy Programme of study: MA Public Policy Word count: 15,480 2 Table of Contents I. Introduction I.1. Research question and hypothesis…………………………………………………….7 I.2. Justification……………………………………………………………………………8 I.3. Structure……………………………………………………………………………….9 I.4. Terms………………………………………………………………………………….9 II. Methodology II.1. Data collection……………………………………………………………………....11 II.2. Analysis…………………………………………………………………………….12 II.3. Limitations………………………………………………………………………….13 III. Literature Review III.1. Overview of multinational e-government Collaboration………………………….15 III.2. E-government information sharing, integration and interoperability……………...17 III.3. Central debates……………………………………………………………………..18 IV. Theoretical Framework IV.1. Underpinnings of the framework………………………………………………….20 IV.1.1 Border theory…………………………………………………………….20 IV.1.2 Collaborative governance theory…………………………………………22 IV.1.3 Inter-organizational cooperation theory………………………………….24 IV.1.4 Integration and interoperability theory…………………………………...25 IV.1.5. Value network theory……………………………………………………26 IV.2. ‘Multinational e-government collaboration, information-sharing, and interoperability’ framework……………………………………………………...27 V. Case Study V.1. Case: Estonia and Finland’s cross-border collaboration on ICT development……..30 V.1.1 Building -
TIN Description Individuals Finland Issues Tins Which Are Reported on Of
Information on Tax Identification Numbers Section I – TIN Description Individuals Finland issues TINs which are reported on official documents of identification. The TIN is the Finnish Social Security number, given at birth or when immigrating by the Population Register Centre of Finland. Legal persons The Business ID (Business Identity Code) is a code given to businesses and organizations by the authorities. A new business will get a Business ID as soon as the authorities have entered the start-up notification in the Business Information System. The registration authorities will provide the Business ID in approximately two working days from the filing of such notification. Section II – TIN Structure The structure of the TIN varies depending on the type of taxpayer. For individuals, it consists of 11 characters: - 6 digits - 1 character which can be + (plus), - (minus) or the letter A - 3 digits - 1 alphanumeric character The 7th character (+, - or A) represents the century of birth and cannot be skipped: it shall be duly noted down and reported in all records. Character + means: born 1800-1899, - means born 1900-1999 and A means born 2000-. This character has no other meaning. For legal persons, it consists of seven digits, a dash and a control mark, i.e. it has the form 1234567-8. Section III – Where to find TINs? TINs for individuals are reported on the following official documents of identification: Identity card (Henkilökortti / Identitetskort) Passport (Passi / Pass) Driving Licence (Ajokortti-Körkort) TIN national website Information -
Mayors Dialogue on Growth and Solidarity City Profile: Helsinki, Finland
Mayors Dialogue on Growth and Solidarity City profile: Helsinki, Finland Population: 648,042 (2019) GDP per capita: $59,289 (2018) Major industries: information and technology, business services Percentage of migrants: 9.6% (2019) Mayor’s name: Jan Vapaavuori | Next election date: 2021 Socioeconomic profile (ibid.). In 2019, the number of employed people in the Helsinki region grew significantly in construction, and Helsinki city has a population of 648,042 which is the accommodation and restaurant sector, compared 11.7% of the population of Finland (City of Helsinki with the previous year, while numbers of people Urban Research and Statistics Unit, 2019a). It is a employed in manufacturing also increased (City of youthful city, with nearly 10% of the population in Helsinki Urban Research and Statistics Unit, 2019b). the 25–29 age group. Relative to other cities in the The unemployment rate in Helsinki is 7.9% (for those Scandinavian peninsula, Helsinki is one the wealthiest, aged 15–74 years), slightly higher than for the country with a GDP per capita of $59,289 in 2018.1 It is a as a whole (7.4%) (City of Helsinki Urban Research buzzing metropolis, with its own international airport and Statistics Unit, 2019a). In 2017, 5.9% of those and cargo port, wherein the Port of Helsinki is the living in Helsinki were at a ‘prolonged poverty risk’ largest cargo port in terms of the valuation of goods. compared with the higher rate of 7.4% for Finland There are five universities in the city (ibid.). Helsinki as a whole (a slight decline on figures recorded in the residents also benefit from ease of access to green previous year) (ibid.). -
Finland Business Culture
FINLAND BUSINESS CULTURE Finland is a fascinating country in northern Europe. Located in Europe’s far northeastern region, Finland shares long borders with Russia, Norway in the north, Sweden, and some of the Baltic states across the Gulf of Finland to the south. The country is often referred to as the “Land of 1.000 lakes,” although this is highly inaccurate. The best estimate of the number of lakes in Finland is 188.000. The lakes provide beautiful scenery during the summer – a season that, according to the Finns, is much too short. In the winter, the landscape is even more magnificent, with layers of snow and ice reflecting the rare sunlight of the day, and northern lights dancing around at night. The population density in Finland is very low: 17 inhabitants per square kilometer. Today, the total population is 5,5 million people. It is important to understand this number is an average between the more densely populated urban centers – mainly located in southern Finland – and the extremely low population density in Finnish Lapland, where there are only two people per square kilometer. Finland became an independent country about one hundred years ago. Previously ruled by Sweden and Russia, the Bill of Independence in Finnish Parliament was adopted on December 6, 1917. Subsequent recognition by the international community, including Russia, allowed Finland to become an Independent Republic. During the Second World War, the Russians invaded Finland, but were defeated, enhancing Finnish national pride. They do not attribute this victory to higher numbers of soldiers, tactical warfare, or superior guns. -
Finland for the Avoidance of Double Taxation and the Prevention of Fiscal Evasion with Respect to Taxes on Income and on Capital
CONVENTION BETWEEN THE REPUBLIC OF ESTONIA AND THE REPUBLIC OF FINLAND FOR THE AVOIDANCE OF DOUBLE TAXATION AND THE PREVENTION OF FISCAL EVASION WITH RESPECT TO TAXES ON INCOME AND ON CAPITAL The Government of the Republic of Estonia and the Government of the Republic of Finland, Desiring to conclude a Convention for the avoidance of double taxation and the prevention of fiscal evasion with respect to taxes on income and on capital, Have agreed as follows: Article 1 PERSONAL SCOPE This Convention shall apply to persons who are residents of one or both of the Contracting States. Article 2 TAXES COVERED 1. The existing taxes to which the Convention shall apply are: a) In Estonia: (i) the personal income tax (üksikisiku tulumaks); (ii) the corporate income tax (ettevõtte tulumaks); (iii) the licence tax (tegevusloa maks); (hereinafter referred to as "Estonian tax"); b) In Finland: (i) the state income taxes (valtion tuloverot; de statliga inkomstskatterna); (ii) the communal tax (kunnalisvero; kommunalskatten); (iii) the church tax (kirkollisvero; kyrkoskatten); (iv) the tax withheld at source from interest (korkotulon lähdevero; källskatten på ränteinkomst); (v) the tax withheld at source from non- residents` income (rajoitetusti verovelvollisen lähdevero; källskatten för begränsat skattskyldig); and (vi) the state capital tax (valtion varallisuusvero; den statliga förmögenhetsskatten); (hereinafter referred to as "Finnish tax"). 2. Where a new tax on income or on capital is introduced in a Contracting State after the date of signature of the Convention, the Convention shall apply also to such tax. The competent authorities of the Contracting States shall by mutual agreement determine whether a tax which is introduced in either Contracting State is one to which the Convention shall apply according to the preceding sentence. -
The Åland Islands Solution a Precedent for Successful International Disputes Settlement
(final - 16 January 2012) The Åland Islands Solution A precedent for successful international disputes settlement Remarks by Ms. Patricia O’Brien, Under-Secretary-General for Legal Affairs, The Legal Counsel Tuesday, 17 January 2012, 6.30pm (United Nations Headquarters, Delegates Entrance Lobby) Ambassador Viinanen, Madam Gunell, Excellencies, Ladies and Gentlemen, [Introduction] It is a great pleasure to address you today on the occasion of the opening of an exhibition entitled “The Åland Islands Solution - A precedent for successful international disputes settlement”. Allow me, first of all, to congratulate the Archives of the Ministry for Foreign Affairs of Finland and its Permanent Mission here in New York, the National Archives of Finland, the Museum of Åland and the Library of the United Nations Office at Geneva for organising this interesting event. The archival documents presented to you and on display tonight illustrate the historic context of the successful settlement by the League of Nations of the Åland Islands dispute. [Historical background] The Åland Islands, located at the entrance to the Gulf of Bothnia, have always been of strategic importance in the Baltic region. In the aftermath of the First World War the islands - inhabited by the Swedish-speaking population but belonging to Finland - became an object of a territorial dispute between Finland and Sweden. 1 The residents of the islands claimed their right to self-determination and demanded a reunification with Sweden. This separatist movement was supported by Sweden but opposed by Finland who insisted on its sovereignty over the archipelago and was only willing to offer it an autonomous status. -
Remembering and Forgetting the 1918 Finnish Civil War
International Journal of Communication 6 (2012), 1200–1221 1932–8036/20121200 Collective Memory and the Stranger: Remembering and Forgetting the 1918 Finnish Civil War PIOTR M. SZPUNAR1 University of Pennsylvania Collective remembering is central to forming the bonds that constitute a group’s identity. This identity is not only communicated between group members but also projected outward. That is, a group displays or stages its past for strangers who find themselves in a foreign country or context. These stagings are interesting and important because they are often a stranger’s only glimpse into how the group collectively remembers important events of its past. Contemporary societies are enthralled by memory, in part out of concern with how their memory and identity are communicated to outsiders. Using the case study of Tampere, Finland, and its collective remembering of the Finnish Civil War of 1918, this article addresses the stranger’s position in examining a collective’s efforts to project its identity through memory. It thus highlights the challenges and advantages (methodological and other) of studying the workings of memory from outside the group that is the focus. Finns wishing to commemorate the civil war of 1918 have long struggled with the question of what to remember and why. The war, which began in January 1918 and lasted three and a half months, left the Finnish people bitterly divided. In 1933, General Mannerheim decreed that it was no longer important to ask which side one had fought on, thus instituting an official policy of forgetting that for 1The author would like to thank Dr. -
Minority Cultures and the Making of Cultural Heritage Archives in Finland
MINORITY CULTURES AND THE MAKING OF CULTURAL HERITAGE ARCHIVES IN FINLAND Kati Mikkola, Finnish Literature Society Pia Olsson, University of Helsinki Eija Stark, Åbo Akademi University The article analyzes the logic behind the archival policies concerning language and ethnic minorities in Finland, drawing examples from three minority groups: the Sámi, the Finnish Roma (the Kaale), and the Finland-Swedes. We base our discussion on the documented descriptions, manuscripts, questionnaires, and fieldwork activities dealing with language and ethnic minority groups archived by the Finnish Literature Society (Suomalaisen Kirjallisuuden Seura, SKS) and the Society of Swedish Literature in Finland (Svenska litteratursällskapet i Finland, SLS) from the beginning of the nineteenth century until early twenty-first century. Viewed from a historical per- spective, the establishment of archives in Finland was inextricably connected to the societal power enjoyed by certain ethnic and language groups seeking to preserve their heritage. Keywords: archival practices, ethnicities, minorities, nationalism, Finland Since the nineteenth century, cultural heritage Furthermore, it has been argued that archives for materials in Western countries have been collected folklore and ethnographic materials have not only and stored in archives in which they later have be- been used to create an idealized and polished picture come signified as national legacies. Within archive of the past but that they also have participated in the practices, however, questions of heterogeneous cul- erasure or minimization of conflicts (see e.g. Skott tural identities have been mostly overlooked (see e.g. 2008: 21). Daniel 2010: 84). Archives were long seen only as a In Finland, the collection and uses of folk tradi- means of promoting the representative character- tion have played a part in the construction of the istics of the national (majority) and of serving the nation. -
Nuclear Legislation in OECD and NEA Countries
N uclear Legislation in OECD and NEA Countries Regulatory and Institutional Framework for Nuclear Activities Finland Nuclear Legislation in OECD Countries © OECD 2019 Finland I. General Regulatory Regime ................................................................. 3 1. Introduction ..................................................................................................... 3 2. Mining regime .................................................................................................. 5 3. Radioactive substances, nuclear fuel and equipment ............................................. 5 4. Nuclear installations .......................................................................................... 6 a) Licensing and inspection, including nuclear safety .......................................... 6 b) Emergency response .................................................................................. 8 5. Trade in nuclear materials and equipment ........................................................... 9 6. Radiation protection ......................................................................................... 10 7. Radioactive waste management ........................................................................ 10 8. Nuclear security .............................................................................................. 12 9. Transport ....................................................................................................... 13 10. Nuclear third party liability ..............................................................................