Oct. 5, 1965 A
Total Page:16
File Type:pdf, Size:1020Kb
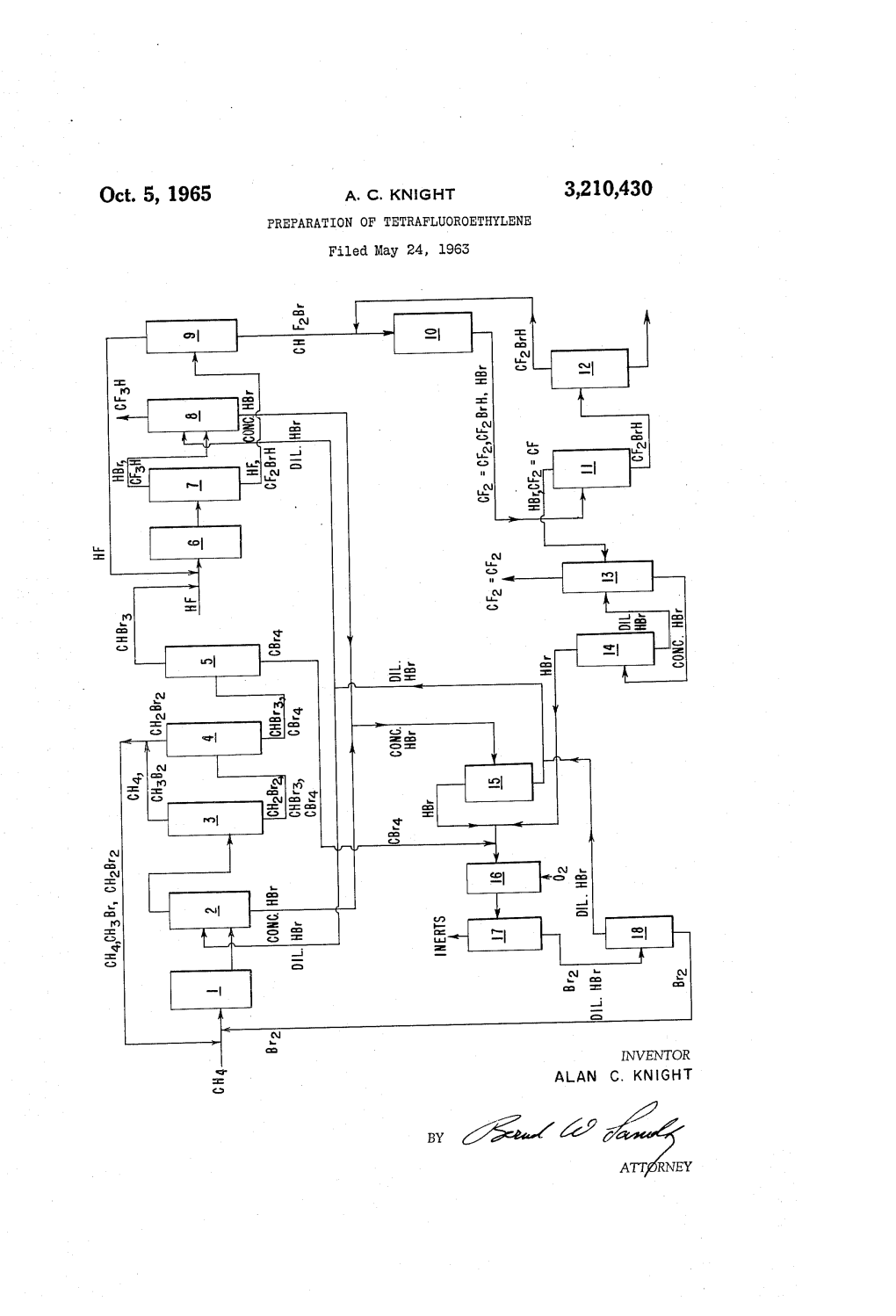
Load more
Recommended publications
-
Vibrationally Excited Hydrogen Halides : a Bibliography On
VI NBS SPECIAL PUBLICATION 392 J U.S. DEPARTMENT OF COMMERCE / National Bureau of Standards National Bureau of Standards Bldg. Library, _ E-01 Admin. OCT 1 1981 191023 / oO Vibrationally Excited Hydrogen Halides: A Bibliography on Chemical Kinetics of Chemiexcitation and Energy Transfer Processes (1958 through 1973) QC 100 • 1X57 no. 2te c l !14 c '- — | NATIONAL BUREAU OF STANDARDS The National Bureau of Standards' was established by an act of Congress March 3, 1901. The Bureau's overall goal is to strengthen and advance the Nation's science and technology and facilitate their effective application for public benefit. To this end, the Bureau conducts research and provides: (1) a basis for the Nation's physical measurement system, (2) scientific and technological services for industry and government, (3) a technical basis for equity in trade, and (4) technical services to promote public safety. The Bureau consists of the Institute for Basic Standards, the Institute for Materials Research, the Institute for Applied Technology, the Institute for Computer Sciences and Technology, and the Office for Information Programs. THE INSTITUTE FOR BASIC STANDARDS provides the central basis within the United States of a complete and consistent system of physical measurement; coordinates that system with measurement systems of other nations; and furnishes essential services leading to accurate and uniform physical measurements throughout the Nation's scientific community, industry, and commerce. The Institute consists of a Center for Radiation Research, an Office of Meas- urement Services and the following divisions: Applied Mathematics — Electricity — Mechanics — Heat — Optical Physics — Nuclear Sciences" — Applied Radiation 2 — Quantum Electronics 1 — Electromagnetics 3 — Time 3 1 1 and Frequency — Laboratory Astrophysics — Cryogenics . -
1-Bromopropane
Right to Know Hazardous Substance Fact Sheet Common Name: 1-BROMOPROPANE Synonyms: Propyl Bromide CAS Number: 106-94-5 Chemical Name: Propane, 1-Bromo- RTK Substance Number: 4198 Date: October 2009 Revision: March 2016 DOT Number: UN 2344 Description and Use EMERGENCY RESPONDERS >>>> SEE BACK PAGE 1-Bromopropane is a clear, colorless liquid with a sweet odor. Hazard Summary It is used in dry cleaning, and as a solvent, adhesive, and an Hazard Rating NJDHSS NFPA aerosol propellant. HEALTH 2 - FLAMMABILITY 3 - REACTIVITY 1 - Reasons for Citation 1-Bromopropane is on the Right to Know Hazardous FLAMMABLE Substance List because it is cited by the EPA, NTP, ACGIH POISONOUS GASES ARE PRODUCED IN FIRE and DOT. CONTAINERS MAY EXPLODE IN FIRE This chemical is on the Special Health Hazard Substance Hazard Rating Key: 0=minimal; 1=slight; 2=moderate; 3=serious; List. 4=severe 1-Bromopropane can affect you when inhaled and may be absorbed through the skin. 1-Bromopropane should be handled as a CARCINOGEN-- WITH EXTREME CAUTION. 1-Bromopropane may cause reproductive damage. SEE GLOSSARY ON PAGE 5. HANDLE WITH EXTREME CAUTION. Contact can irritate the skin and eyes. FIRST AID Inhaling 1-Bromopropane can irritate the nose, throat and lungs. Eye Contact Exposure can cause headache, dizziness, lightheadedness, Immediately flush with large amounts of water for at least 15 trouble concentrating, and weakness. minutes, lifting upper and lower lids. Remove contact 1-Bromopropane may damage the nervous system causing lenses, if worn, while rinsing. numbness, “pins and needles,” and/or weakness in the hands and feet. Skin Contact 1-Bromopropane may affect the liver. -
Transport of Dangerous Goods
ST/SG/AC.10/1/Rev.16 (Vol.I) Recommendations on the TRANSPORT OF DANGEROUS GOODS Model Regulations Volume I Sixteenth revised edition UNITED NATIONS New York and Geneva, 2009 NOTE The designations employed and the presentation of the material in this publication do not imply the expression of any opinion whatsoever on the part of the Secretariat of the United Nations concerning the legal status of any country, territory, city or area, or of its authorities, or concerning the delimitation of its frontiers or boundaries. ST/SG/AC.10/1/Rev.16 (Vol.I) Copyright © United Nations, 2009 All rights reserved. No part of this publication may, for sales purposes, be reproduced, stored in a retrieval system or transmitted in any form or by any means, electronic, electrostatic, magnetic tape, mechanical, photocopying or otherwise, without prior permission in writing from the United Nations. UNITED NATIONS Sales No. E.09.VIII.2 ISBN 978-92-1-139136-7 (complete set of two volumes) ISSN 1014-5753 Volumes I and II not to be sold separately FOREWORD The Recommendations on the Transport of Dangerous Goods are addressed to governments and to the international organizations concerned with safety in the transport of dangerous goods. The first version, prepared by the United Nations Economic and Social Council's Committee of Experts on the Transport of Dangerous Goods, was published in 1956 (ST/ECA/43-E/CN.2/170). In response to developments in technology and the changing needs of users, they have been regularly amended and updated at succeeding sessions of the Committee of Experts pursuant to Resolution 645 G (XXIII) of 26 April 1957 of the Economic and Social Council and subsequent resolutions. -
Transfer of Bromoform Present in Asparagopsis Taxiformis to Milk and Urine of Lactating Dairy Cows
foods Article Safety and Transfer Study: Transfer of Bromoform Present in Asparagopsis taxiformis to Milk and Urine of Lactating Dairy Cows Wouter Muizelaar 1,2,* , Maria Groot 3 , Gert van Duinkerken 1, Ruud Peters 3 and Jan Dijkstra 2 1 Wageningen Livestock Research, Wageningen University & Research, P.O. Box 338, 6700 AH Wageningen, The Netherlands; [email protected] 2 Animal Nutrition Group, Wageningen University & Research, P.O. Box 338, 6700 AH Wageningen, The Netherlands; [email protected] 3 Wageningen Food Safety Research, Wageningen University & Research, P.O. Box 230, 6700 AE Wageningen, The Netherlands; [email protected] (M.G.); [email protected] (R.P.) * Correspondence: [email protected]; Tel.: +31-317-487-941 Abstract: Enteric methane (CH4) is the main source of greenhouse gas emissions from ruminants. The red seaweeds Asparagopsis taxiformis (AT) and Asparagopsis armata contain halogenated compounds, including bromoform (CHBr3), which may strongly decrease enteric CH4 emissions. Bromoform is known to have several toxicological effects in rats and mice and is quickly excreted by the animals. This study investigated the transfer of CHBr3 present in AT to milk, urine, feces, and animal tissue when incorporated in the diet of dairy cows. Twelve lactating Holstein-Friesian dairy cows were randomly assigned to three treatment groups, representing the target dose (low), 2× target dose (medium), and 5× target dose (high). The adaptation period lasted seven days, and subsequently Citation: Muizelaar, W.; Groot, M.; cows were fed AT for 22 days maximally. The transfer of CHBr3 to the urine at days 1 and 10 (10–148 van Duinkerken, G.; Peters, R.; µg/L) was found with all treatments. -
Cylinder Valve Selection Quick Reference for Valve Abbreviations
SHERWOOD VALVE COMPRESSED GAS PRODUCTS Appendix Cylinder Valve Selection Quick Reference for Valve Abbreviations Use the Sherwood Cylinder Valve Series Abbreviation Chart on this page with the Sherwood Cylinder Valve Selection Charts found on pages 73–80. The Sherwood Cylinder Valve Selection Chart are for reference only and list: • The most commonly used gases • The Compressed Gas Association primary outlet to be used with each gas • The Sherwood valves designated for use with this gas • The Pressure Relief Device styles that are authorized by the DOT for use with these gases PLEASE NOTE: The Sherwood Cylinder Valve Selection Charts are partial lists extracted from the CGA V-1 and S-1.1 pamphlets. They can change without notice as the CGA V-1 and S-1.1 pamphlets are amended. Sherwood will issue periodic changes to the catalog. If there is any discrepancy or question between these lists and the CGA V-1 and S-1.1 pamphlets, the CGA V-1 and S-1.1 pamphlets take precedence. Sherwood Cylinder Valve Series Abbreviation Chart Abbreviation Sherwood Valve Series AVB Small Cylinder Acetylene Wrench-Operated Valves AVBHW Small Cylinder Acetylene Handwheel-Operated Valves AVMC Small Cylinder Acetylene Wrench-Operated Valves AVMCHW Small Cylinder Acetylene Handwheel-Operated Valves AVWB Small Cylinder Acetylene Wrench-Operated Valves — WB Style BV Hi/Lo Valves with Built-in Regulator DF* Alternative Energy Valves GRPV Residual Pressure Valves GV Large Cylinder Acetylene Valves GVT** Vertical Outlet Acetylene Valves KVAB Post Medical Valves KVMB Post Medical Valves NGV Industrial and Chrome-Plated Valves YVB† Vertical Outlet Oxygen Valves 1 * DF Valves can be used with all gases; however, the outlet will always be ⁄4"–18 NPT female. -
MATERIAL SAFETY DATA SHEET According to the Hazard Communication Standard (29 CFR 1910.1200)
MATERIAL SAFETY DATA SHEET according to the Hazard Communication Standard (29 CFR 1910.1200) Date of issue: 12/20/2012 Version 1.0 SECTION 1. Identification Product identifier Product number 101944 Product name Bromoform for separation of minerals mixtures Relevant identified uses of the substance or mixture and uses advised against Identified uses Reagent for analysis Details of the supplier of the safety data sheet Company EMD Millipore Corporation | 290 Concord Road, Billerica, MA 01821, United States of America | SDS Phone Support: +1-978-715-1335 | General Inquiries: +1-978-751-4321 | Monday to Friday, 9:00 AM to 4:00 PM Eastern Time (GMT-5) e-mail: [email protected] Emergency telephone 800-424-9300 CHEMTREC (USA) +1-703-527-3887 CHEMTREC (International) 24 Hours/day; 7 Days/week SECTION 2. Hazards identification GHS Classification Acute toxicity, Category 3, Inhalation, H331 Acute toxicity, Category 4, Oral, H302 Eye irritation, Category 2, H319 Skin irritation, Category 2, H315 Chronic aquatic toxicity, Category 2, H411 For the full text of the H-Statements mentioned in this Section, see Section 16. GHS-Labeling Hazard pictograms Signal Word Danger Hazard Statements H331 Toxic if inhaled. Page 1 of 11 MATERIAL SAFETY DATA SHEET according to the Hazard Communication Standard (29 CFR 1910.1200) Product number 101944 Version 1.0 Product name Bromoform for separation of minerals mixtures H302 Harmful if swallowed. H319 Causes serious eye irritation. H315 Causes skin irritation. H411 Toxic to aquatic life with long lasting effects. Precautionary Statements P273 Avoid release to the environment. P304 + P340 IF INHALED: Remove victim to fresh air and keep at rest in a position comfortable for breathing. -
Synthesis of Bromochloromethane Using Phase Transfer Catalysis
1 SYNTHESIS OF BROMOCHLOROMETHANE USING PHASE TRANSFER CATALYSIS By LANCELOT LUCRETIUS BROOKS Baccalaureus Scientiae Honores-Chemistry, Nelson Mandela Metropolitan University A dissertation submitted in fulfillment of the requirements for the Masters Degree in Chemistry In the Faculty of Science at the NELSON MANDELA METROPOLITAN UNIVERSITY Nov. 2011 Promoter : Dr G. Dugmore Co-Promoter : Prof B. Zeelie 2 DECLARATION I, Lancelot Brooks, hereby declare that the above-mentioned treatise is my own work and that it has not previously been submitted for assessment to another University, or for another qualification. ……………………………….. ……………………….. Mr. L.L. Brooks Date 3 ACKNOWLEDGEMENTS To my promoters Dr. Gary Dugmore, and Prof. Ben Zeelie for their invaluable input, help and guidance. To NRF and NMMU for financial assistance To my parents and brothers for their love and support To Peter, Batsho, Unati, and friends in NMMU chemistry research laboratory, thank you guys. To my dearest fiancée, Natasha, a very special thank you for always being there and supporting me. Love you angel. “And we know that all things work together for good to those who love God, to those who are called according to His purpose” -Romans 8:28. 4 TABLE OF CONTENTS DECLARATION……………………………………………………………………. 2 ACKNOWLEDGEMENTS……………………………………………………………. 3 TABLE OF CONTENTS………………………………………………………………. 4 LIST OF FIGURES…………………………………………………………………….. 8 LIST OF TABLES……………………………………………………………………… 9 LIST OF EQUATIONS………………………………………………………………… 11 SUMMARY……………………………………………………………………………… 12 CHAPTER 1…………………………………………………………………………….. 14 INTRODUCTION………………………………………………………………………. 14 1.1. Technology of leather production……………………………………………….. 14 1.2. Synthesis of TCMTB……………………………………………………………… 17 1.3. Bromine……………………………………………………………………………. 20 1.3.1. Overview……………………………………………………………. 20 1.3.2. Applications of bromine compounds…………..…………………. 22 1.3.2.1. Photography……………………………………………… 22 1.3.2.2. -
Anhydrous Hydrogen Bromide
Product Safety Assessment Anhydrous Hydrogen Bromide Anhydrous hydrogen bromide is primarily used in two types of applications: 1) To etch poly-silicon wafers for the manufacture of computer chips that are part of electronic devices 2) As a “building block” chemical, meaning it is often reacted with other chemicals in highly-controlled industrial settings to make other chemicals. Anhydrous hydrogen bromide is made using bromine (for more information see the Product Safety Assessment for bromine). Hydrogen bromide is a colorless gas that can be compressed to liquid form when pressurized. It fumes strongly in moist air, forming hydrobromic acid, which is corrosive to common metals. Anhydrous hydrogen bromide is toxic, irritating to the respiratory system when inhaled, and corrosive to the eyes, skin, and mucous membranes. Anhydrous hydrogen bromide is transported in sturdy cylinders to industrial customers or laboratories. Identification Anhydrous hydrogen bromide is identified by several names, all of them referring to the same chemical product. These names include: • H-Br • CAS Number [10035-10-6] • Anhydrous hydrogen bromide • Anhydrous HBr • Hydrogen bromide (HBr) • Hydrogen dibromide (H2Br2) • Hydrogen monobromide • Hydrobromic acid (in aqueous solutions) Last Revised: March 2017 Page 1 of 6 Product Safety Assessment: Anhydrous Hydrogen Bromide Description Production: Anhydrous hydrogen bromide is made in dedicated manufacturing units. During production, hydrogen and bromine are combined and burned in specially designed furnaces. The anhydrous hydrogen gas generated is purified and packaged for shipment. Uses: Hydrogen bromide is commonly used in combination with other chemicals by the semi-conductor industry for plasma etching of polysilicon computer chips used in electronic devices. -
PAPERS READ BEFORE the CHEMICAL SOCIETY. XXII1.-On
View Article Online / Journal Homepage / Table of Contents for this issue 773 PAPERS READ BEFORE THE CHEMICAL SOCIETY. XXII1.-On Tetrabromide of Carbon. No. II. By THOMASBOLAS and CHARLESE. GROVES. IN a former paper* we described several methods for the preparation of the hitherto unknown tetrabromide of carbon, and in the present communication we desire to lay before the Society the results of our more recent experiments. In addition to those methods of obtaining the carbon tetrabromide, which we have already published, the fol- lowing are of interest, either from a theoretical point of view, or as affording advantageous means for the preparation of that substance. Action of Bromine on Carbon Disulphide. Our former statement that? bromine had no action on carbon disul- phide requires some modification, as we find that when it is heated to 180" or 200" for several hundred hours with bromine free from both chlorine and iodine, and the contents of the tubes are neutralised and distilled in the usual way, a liquid is obtained, which consists almost entirely of unaltered carbon disulphide ; but when this is allowed to evaporate spontaneously, a small quantity of a crystalline substance is left, which has the appearance and properties of carbon tetrabromide. The length of time required for this reaction, and the very small relative amount of substance obtained, would, however, render this Published on 01 January 1871. Downloaded by Brown University 25/10/2014 10:39:25. quite inapplicable as a process for the preparation of the tetra- bromide. Action of Bromine on Carbon Disdphide in, presence of Certain Bromides. -
Gas Conversion Factor for 300 Series
300GasTable Rec # Gas Symbol GCF Density (g/L) Density (g/L) 25° C / 1 atm 0° C / 1 atm 1 Acetic Acid C2H4F2 0.4155 2.7 2.947 2 Acetic Anhydride C4H6O3 0.258 4.173 4.555 3 Acetone C3H6O 0.3556 2.374 2.591 4 Acetonitryl C2H3N 0.5178 1.678 1.832 5 Acetylene C2H2 0.6255 1.064 1.162 6 Air Air 1.0015 1.185 1.293 7 Allene C3H4 0.4514 1.638 1.787 8 Ammonia NH3 0.7807 0.696 0.76 9 Argon Ar 1.4047 1.633 1.782 10 Arsine AsH3 0.7592 3.186 3.478 11 Benzene C6H6 0.3057 3.193 3.485 12 Boron Trichloride BCl3 0.4421 4.789 5.228 13 Boron Triflouride BF3 0.5431 2.772 3.025 14 Bromine Br2 0.8007 6.532 7.13 15 Bromochlorodifluoromethane CBrClF2 0.3684 6.759 7.378 16 Bromodifluoromethane CHBrF2 0.4644 5.351 5.841 17 Bromotrifluormethane CBrF3 0.3943 6.087 6.644 18 Butane C4H10 0.2622 2.376 2.593 19 Butanol C4H10O 0.2406 3.03 3.307 20 Butene C4H8 0.3056 2.293 2.503 21 Carbon Dioxide CO2 0.7526 1.799 1.964 22 Carbon Disulfide CS2 0.616 3.112 3.397 23 Carbon Monoxide CO 1.0012 1.145 1.25 24 Carbon Tetrachloride CCl4 0.3333 6.287 6.863 25 Carbonyl Sulfide COS 0.668 2.456 2.68 26 Chlorine Cl2 0.8451 2.898 3.163 27 Chlorine Trifluoride ClF3 0.4496 3.779 4.125 28 Chlorobenzene C6H5Cl 0.2614 4.601 5.022 29 Chlorodifluoroethane C2H3ClF2 0.3216 4.108 4.484 30 Chloroform CHCl3 0.4192 4.879 5.326 31 Chloropentafluoroethane C2ClF5 0.2437 6.314 6.892 32 Chloropropane C3H7Cl 0.308 3.21 3.504 33 Cisbutene C4H8 0.3004 2.293 2.503 34 Cyanogen C2N2 0.4924 2.127 2.322 35 Cyanogen Chloride ClCN 0.6486 2.513 2.743 36 Cyclobutane C4H8 0.3562 2.293 2.503 37 Cyclopropane C3H6 0.4562 -
Techniques for Quantifying Gaseous Hocl Using Atmospheric Pressure Ionization Mass Spectrometry
View Article Online / Journal Homepage / Table of Contents for this issue Techniques for quantifying gaseous HOCl using atmospheric pressure ionization mass spectrometry Krishna L. Foster, Tracy E. Caldwell,¤ Thorsten Benter,* Sarka Langer,” John C. Hemminger and Barbara J. Finlayson-Pitts* Department of Chemistry, University of California, Irvine, CA 92697-2025, USA Received 10th September 1999, Accepted 1st November 1999 HOCl is speculated to be an important intermediate in mid-latitude marine boundary layer chemistry and at high latitudes in spring-time when surface-levelO3 depletion occurs. However, techniques do not currently exist to measure HOCl in the troposphere. We demonstrate that atmospheric pressure ionization mass spectrometry (API-MS) is a highly sensitive and selective technique which has promise for HOCl measurements both in laboratory systems and in Ðeld studies. While HOCl can be measured as the Æ ~ (HOCl O2) adduct with air as the chemical ionization (CI) reagent gas, the intensity of this adduct is sensitive to the presence of acids and to the amount of water vapor, complicating its use for quantitative measurements. However, the addition of bromoform vapor to the corona discharge region forms bromide ions that attach to HOCl and allow its detection via the (HOCl Æ Br)~ adduct. The ionÈmolecule chemistry associated with the use of air or bromoform as the CI reagent gas is discussed, with particular emphasis on the e†ects of relative humidity and gas phase acid concentrations. HOCl is quantiÐed by measuring the amount of Cl2 formed by its heterogeneous reaction with condensed-phaseHCl/H2O. Detection limits are D3 parts per billion (ppb) using air as the CI reagent gas and D0.9 ppb using bromoform. -
Safe Handling and Disposal of Chemicals Used in the Illicit Manufacture of Drugs
Vienna International Centre, PO Box 500, 1400 Vienna, Austria Tel.: (+43-1) 26060-0, Fax: (+43-1) 26060-5866, www.unodc.org Guidelines for the Safe handling and disposal of chemicals used in the illicit manufacture of drugs United Nations publication USD 26 Printed in Austria ISBN 978-92-1-148266-9 Sales No. E.11.XI.14 ST/NAR/36/Rev.1 V.11-83777—September*1183777* 2011—300 Guidelines for the Safe handling and disposal of chemicals used in the illlicit manufacture of drugs UNITED NATIONS New York, 2011 Symbols of United Nations documents are composed of letters combined with figures. Mention of such symbols indicates a reference to a United Nations document. ST/NAR/36/Rev.1 UNITED NATIONS PUBLICATION Sales No. E.11.XI.14 ISBN 978-92-1-148266-9 eISBN 978-92-1-055160-1 © United Nations, September 2011. All rights reserved. The designations employed and the presentation of material in this publication do not imply the expression of any opinion whatsoever on the part of the Secretariat of the United Nations concerning the legal status of any country, territory, city or area, or of its authorities, or concerning the delimitation of its frontiers or boundaries. Requests for permission to reproduce this work are welcomed and should be sent to the Secretary of the Publications Board, United Nations Headquarters, New York, N.Y. 10017, U.S.A. or also see the website of the Board: https://unp.un.org/Rights.aspx. Governments and their institutions may reproduce this work without prior authoriza- tion but are requested to mention the source and inform the United Nations of such reproduction.