Current Progress of 3D Concrete Printing Technologies
Total Page:16
File Type:pdf, Size:1020Kb
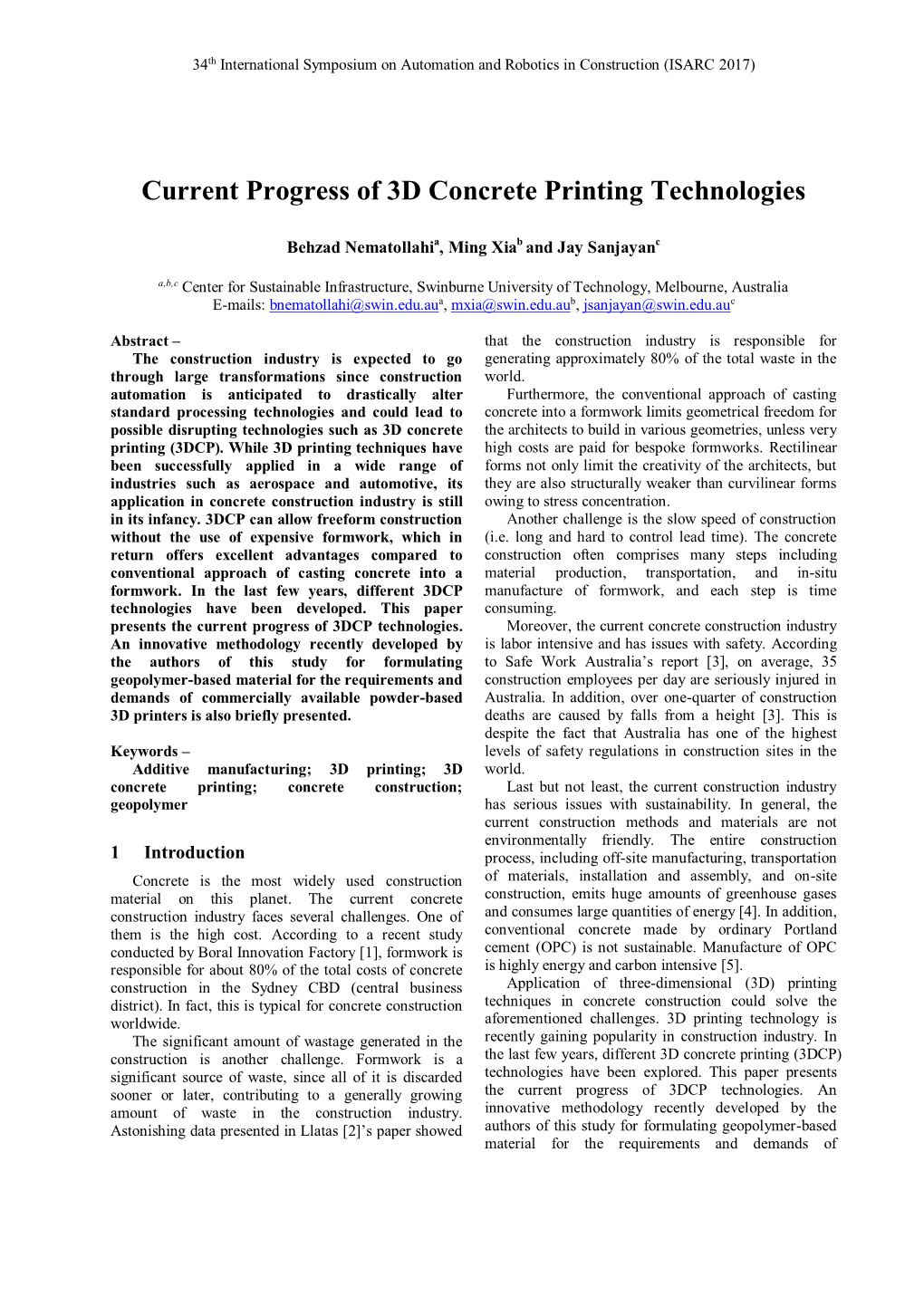
Load more
Recommended publications
-
JRC Horizon Scanning on Dual-Use Civil and Military Research
JRC horizon scanning on dual-use civil and military research G. Bordin, M. Hristova and E. Luque-Perez 2020 EUR 30301 EN This publication is a Science for Policy report by the Joint Research Centre (JRC), the European Commission’s science and knowledge service. It aims to provide evidence-based scientific support to the European policymaking process. The scientific output expressed does not imply a policy position of the European Commission. Neither the European Commission nor any person acting on behalf of the Commission is responsible for the use that might be made of this publication. For information on the methodology and quality underlying the data used in this publication for which the source is neither Eurostat nor other Commission services, users should contact the referenced source. The designations employed and the presentation of material on the maps do not imply the expression of any opinion whatsoever on the part of the European Union concerning the legal status of any country, territory, city or area or of its authorities, or concerning the delimitation of its frontiers or boundaries. Contact information Name: Guy Bordin, Mayya Hristova and Encarnación Luque-Perez Address: Rue du Champ de Mars 21, 1049 Brussels, Belgium Email: [email protected]; [email protected]; [email protected] EU Science Hub https://ec.europa.eu/jrc JRC120638 EUR 30301 EN PDF ISBN 978-92-76-20775-7 ISSN 1831-9424 doi:10.2760/47988 Luxembourg: Publications Office of the European Union, 2020 © European Union, 2020 The reuse policy of the European Commission is implemented by the Commission Decision 2011/833/EU of 12 December 2011 on the reuse of Commission documents (OJ L 330, 14.12.2011, p. -
Developments in 3D Printing a Sector by Sector Overview
3D Printing Quarterly Report—Q42018 3D PRINTING–A FAST MOVING MARKET Developments in 3D Printing A Sector by Sector Overview Overview This report explores developments in 3D printing across several sectors and categories for the quarterly period of October 10, 2018 to January 10, 2019. For more information, Table of Contents please contact: Overview ................................... 1 Miscellaneous Partnerships ..... 11 Clothing & Wearables ............... 23 Mark E. Avsec (216) 363-4151 General ..................................... 2 Patents & Copyright ................ 12 Food ....................................... 24 [email protected] Materials .................................. 4 Auto & Transportation ............... 12 Education ................................ 26 Printing Techniques & Aviation & Aerospace .............. 15 Environmental Efforts ............... 27 Capabilities ............................. 8 Health & Life Sciences ............ 16 Arts & Entertainment ................ 28 www.beneschlaw.com M&A and Investments ............... 9 Manufacturing & Construction... 21 3D PRINTING–A FAST MOVING MARKET 3D Printing Quarterly Report—Q4 A Sector by Sector Overview General Mass manufacturing set to be next step in 3D printing, experts say There is a sense mass production is the next big thing in 3D printing and Christoph Schell, President 3D Printing & Digital Manufacturing at HP, lent credence to that when he said 2019 will be the year additive manufacturing moves from prototyping into full production in the automotive industry. HP aims to play a prominent role in this evolution with its Multi Jet Fusion and Metal Jet 3D printing technologies, both of which are designed for large batch production. Startups like Evolve Additive and Origin are using their own technologies for 3D printing large runs of plastic parts. Most companies working toward mass metal manufacturing, including HP, have developed binder jet platforms for mass printing parts. Boston-based Digital Alloys has a novel approach to fusing metal parts called Joule Printing. -
A Review of 3D Printing in Construction and Its Impact on the Labor Market
sustainability Review A Review of 3D Printing in Construction and its Impact on the Labor Market Md. Aslam Hossain 1,* , Altynay Zhumabekova 1, Suvash Chandra Paul 2 and Jong Ryeol Kim 1,* 1 Department of Civil and Environmental Engineering, Nazarbayev University, Nur-Sultan 010000, Kazakhstan; [email protected] 2 Department of Civil Engineering, International University of Business Agriculture and Technology, Dhaka 1230, Bangladesh; [email protected] * Correspondence: [email protected] (M.A.H.); [email protected] (J.R.K.); Tel.: +7-7172-709123 (M.A.H.); +7-7172-70-9136 (J.R.K.) Received: 7 September 2020; Accepted: 25 September 2020; Published: 15 October 2020 Abstract: Construction industry is very labor-intensive and one of the major sources of employment in the world. The industry is experiencing low productivity with minimum technological innovations for decades. In recent times, various automation technologies including 3D printing have received increasing interests in construction. 3D printing in construction is found to be very promising to automate the construction processes and have the potential of saving laborious work, material waste, construction time, risky operation for humans, etc. There has been a comprehensive body of research conducted to understand the recent advances, future prospects and challenges of large-scale adoption of 3D printing in construction projects. Being one the labor-intensive industries, this study also investigates the possible impact on the labor market with increasing adoption of 3D printing in construction. It is found that 3D printing can reduce significant number of labors which can solve the labor shortage problem, especially for the countries where construction is heavily dependent on immigrant workers. -
Strategic Latency: Red, White, and Blue Managing the National and International Security Consequences of Disruptive Technologies Zachary S
Strategic Latency: Red, White, and Blue Managing the National and International Security Consequences of Disruptive Technologies Zachary S. Davis and Michael Nacht, editors Center for Global Security Research Lawrence Livermore National Laboratory February 2018 Disclaimer: This document was prepared as an account of work sponsored by an agency of the United States government. Neither the United States government nor Lawrence Livermore National Security, LLC, nor any of their employees makes any warranty, expressed or implied, or assumes any legal liability or responsibility for the accuracy, completeness, or usefulness of any information, apparatus, product, or process disclosed, or represents that its use would not infringe privately owned rights. Reference herein to any specific commercial product, process, or service by trade name, trademark, manufacturer, or otherwise does not necessarily constitute or imply its endorsement, recommendation, or favoring by the United States government or Lawrence Livermore National Security, LLC. The views and opinions of authors expressed herein do not necessarily state or reflect those of the United States government or Lawrence Livermore National Security, LLC, and shall not be used for advertising or product endorsement purposes. LLNL-BOOK-746803 Strategic Latency: Red, White, and Blue: Managing the National and International Security Consequences of Disruptive Technologies Zachary S. Davis and Michael Nacht, editors Center for Global Security Research Lawrence Livermore National Laboratory February -
Developments in 3D Printing a Sector by Sector Overview
3D Printing Quarterly Report—Q42019 3D PRINTING–A FAST-MOVING MARKET Developments in 3D Printing A Sector by Sector Overview This report explores developments in 3D printing across several sectors and categories for the quarterly period of October 1, 2019 to December 15, 2019. For more information, Table of Contents please contact: General ..................................... 2 Miscellaneous Partnerships ...... 14 Wearables ............................... 25 Mark E. Avsec Materials ................................... 5 Patents & Copyright ................. 18 Food ....................................... 25 (216) 363-4151 [email protected] Printing Techniques & Transportation .......................... 19 Education ................................ 26 Capabilities .............................. 8 Navy, Military, Aviation & Environmental Efforts & Manufacturing & Construction... 11 Aerospace ............................. 20 Energy ................................... 26 M&A and Investments .............. 12 Life Sciences ........................... 22 History, Arts & Entertainment .... 26 www.beneschlaw.com 3D PRINTING–A FAST-MOVING MARKET 3D Printing Quarterly Report—Q4 A Sector by Sector Overview General Rösler expands AM Solutions division to offer 3D printing services AM Solutions, the Italian 3D printing subsidiary of the Rösler Group, a German company specializing in surface finishing solutions, will expand to offer a range of 3D printing services. Originally limited to post processing for Rösler, AM Solutions is now providing -
Cr2017 Report Layout1bss.Qxd 2018.03.20
cr2017_report layout1bss.qxd 2018.03.20. 17:52 Page bI celab.ceu.edu ................................................................... | C | E | L | A | B | ..................................................................................................................... CENTER FOR ETHICS AND LAW IN BIOMEDICINE 2016–2017 ...................................................... ANNUAL REPORT....................................... ..................................... cr2017_report layout1bss.qxd 2018.03.20. 17:52 Page bII Editor-in-chief: Judit Sándor Executive editor: Enikő Demény © March 2018 Center for Ethics and Law in Biomedicine (CELAB) ISSN 1992-4038 CELAB Report is published annually Address: 1051 Budapest Nádor u. 9. Hungary Telephone: +36-1-327-3000/ext.2128 Fax: +36-1-327-3220 E-mail: [email protected] Website: http://www.celab.ceu.edu Design and layout: Zsolt Sándor Printed in Hungary by FOM kft. www.celab.ceu.edu www.celab.ceu.edu ............................ ......................... cr2017_report layout1bss.qxd 2018.03.20. 17:52 Page 1 | C | E | L | A | B ||A | N | N | U | A | L ||R | E | P | O | R | T | 1 TABLE OF CONTENTS 1. FOREWORD........................................................................................................................................................2 2. RESEARCH AND POLICY ACTIVITIES...............................................................................................................6 2.1. PARTICIPATION AND COLLABORATION IN RESEARCH NETWORKS....................................................6 -
3D Printing in Building and Construction
TECHNOLOGY SCAN: 3D PRINTING IN BUILDING AND CONSTRUCTION WITH INPUT FROM METHODOLOGY DISCLAIMER 1. Dataset used for the report The information, analysis, and opinions (the “Content”) The patent dataset was retrieved on 22 February 2019 and contained herein are based on information reasonably comprises worldwide patent applications relating to 3D printing available and accessible as of the date of the analysis. in building and construction published in 2009-2018. While IPOS endeavours to ensure that the Content is correct as of the date of the analysis, IPOS does not Relevant business information, market data, and national warrant the accuracy or completeness of the Content. policies that are available from commercial databases or on the The Content in this report does not constitute any web are also used to support the findings of the report. legal, business or financial advice and nothing contained herein shall be construed as such. Neither 2. Counting the number of inventions IPOS nor any of its affiliates shall be liable for any claims, expenses or liabilities which may arise from this This report counts the number of inventions by the total report. number of unique patent families and utility models. Counting individual patent applications will result in double counting as each patent family may contain several patent publications if the applicant files the same invention for patent protection in COPYRIGHT NOTICE multiple destinations. As a patent family is a group of patent applications relating to the same invention, analyses based on © IPOS 2019 counting one invention per unique patent family can reflect innovation activity more accurately. -
Future Technology Trends
OECD Science, Technology and Innovation Outlook 2016 © OECD 2016 Chapter 2 Future technology trends Technological change is set to have profound impacts over the next 10-15 years, widely disrupting economies and societies. As the world faces multiple challenges, including ageing, climate change, and natural resource depletion, technology will be called upon to contribute new or better solutions to emerging problems. These socio- ecological demands will shape the future dynamics of technological change, as will developments in science and technology. This chapter discusses ten key or emerging technologies that are among the most promising and potentially most disruptive and that carry significant risks. The choice of technologies is based on the findings of a few major foresight exercises carried out in recent years. The ten technologies are as follows: the Internet of Things; big data analytics; artificial intelligence; neurotechnologies; nano/microsatellites; nanomaterials; additive manufacturing; advanced energy storage technologies; synthetic biology; and blockchain. The chapter describes each technology in turn, highlighting some of its possible socioeconomic impacts and exploring related policy issues. A final section highlights some common themes across the ten technologies. 77 2. FUTURE TECHNOLOGY TRENDS Introduction Technological change is a significant megatrend in its own right, constantly reshaping economies and societies, often in radical ways. The scope of technology – in terms of its form, knowledge bases and application areas – is extremely broad and varied, and the ways it interacts with economies and societies are complex and co-evolutionary. These conditions create significant uncertainty about the future directions and impacts of technological change, but also offer opportunities for firms, industries, governments and citizens to shape technology development and adoption. -
GOVERNING CONSTRUCTION PROJECTS in WHICH 3D PRINTING IS APPLIED an Integration of Traditional Project Governance, Product Design and Innovation
GOVERNING CONSTRUCTION PROJECTS IN WHICH 3D PRINTING IS APPLIED An integration of traditional project governance, product design and innovation Rik Tersteeg | 4095928 MSc Construction Management and Engineering Delft University of Technology i Author Name Rik Tersteeg Student Number 4095928 Graduation Thesis University Delft University of Technology Faculty Civil Engineering and Geosciences Master Construction Management and Engineering (CME) Graduation Committee Chairman Prof.dr.ir. M.J.C.M. Hertogh Faculty of Civil Engineering and Geosciences Supervisor Dr.ir. H.H. Bier Faculty of Architecture Supervisor F. Setaki Faculty of Architecture Company Supervisor J. Hutten Senior Project Manager Arup Company Supervisor R. Kluwer Senior Project Manager Arup Commissioned by Company Arup (Amsterdam office) Naritaweg 118 1043 CA Amsterdam ii Preface The process of conducting this research shows strong similarities to the 3D printing projects that it aimed to investigate. It involved many experts from different disciplines and industries, lots of initial unknowns, and was highly iterative. The lessons I learned therefore, are interestingly similar to what is required to bring 3D printing technology forward. Skills to manage uncertainty, looking across industry boundaries and disciplines, deal with the resulting conflicting perspectives, and bringing them together in a final deliverable. I think this approach embodies the spirit and added value of the MSc Construction Management and Engineering, and have worked on this project with great enthusiasm. I would like to thank my committee members for their active support, the experts in Arup who were happy to share their expertise with me, and all interviewees that enthusiastically shared their vision and perspectives. Henriette, thank you for introducing me to this fascinating topic. -
Mud and Modernity
Goodbun, J. Mud and Modernity. ARENA Journal of Architectural Research. 2016; 1(1): 4. DOI: http://dx.doi.org/10.5334/ajar.6 TECHNOLOGICAL ESSAY Mud and Modernity Jon Goodbun* What is concrete? Loved and loathed in equal measure, this building material, as soon as we try to define it, to specify it, to describe it, becomes, well, not very concrete at all, but rather fluid and surprisingly abstract! Concrete is a material which has been going through an interesting intellectual and practical renaissance in recent years, in no small part driven by the convergence of several different kinds of technology-driven manufacturing changes - ranging from computer aided manufacturing of formworks, to photograph etching, to engineering software, to nano- and bio-chemistry to 3D printing - which have opened up new worlds of realizable, expressive and performance optimised form. The demands posed by anthropogenic climate change, energy use, resource scarcity, and the environmental question more generally, have equally transformed the technologies and industries that are now feeding into developments in this material. On its own though, that is not enough to understand the revival in interest. In this paper I will argue that there are indeed profound relationships between capital, modernity and concrete. However, I will suggest that in order to really start to grasp these relations, we will need to explore some ways of thinking about concrete that have not been developed so far within the recent literature on the material. Notably I will develop an ecological approach to thinking about what concrete is, and in so doing redefine this material as a particular form of mud, or mudcrete: a material which is deployed by both human and non-human builders. -
ABSTRACT KEARNS, ALEXA JO. Cotton
ABSTRACT KEARNS, ALEXA JO. Cotton Cellulose Fibers for 3D Print Material. (Under the direction of Dr. Jesse S. Jur and Dr. Richard Venditti). Consumers often desire clean, energy efficient and sustainable solutions to many societal obstacles, including the production of consumer good from the manufacturing sector. New products advocating environmental consciousness and supporting modern consumerism must maintain consistent mechanical and optical properties aligned with those found in petroleum- based materials while lowering energy consumption and retaining biodegradable properties. Manufacturing typically uses subtractive techniques where raw material is milled into the desired product shapes. However, the additive manufacturing sector has garnered attention for its ability to generate products with a range of materials and surface finishes while minimizing use of raw materials. The structures developed with additive manufacturing allow for customization and localized printing, along with reducing costs and transportation energy. This research focuses on fused deposition modeling (FDM), where products develop by layering molten filament upon previously laid and cooled material. Neat polymers, such as poly(lactic) acid (PLA), are frequently used as filament and have virtuous mechanical properties, such as tensile and compressive strength, that allow for substitution with petroleum based products. Adding reinforcing fibers to bridgeable polymer filaments has the potential to increase mechanical properties and expand the prospective applications -
Yapı Üretiminde Eklemeli İmalat Teknolojilerinin Karşılaştırmalı Değerlend
Uludağ Üniversitesi Mühendislik Fakültesi Dergisi, Cilt 25, Sayı 2, 2020 DERLEME DOI: 10.17482/uumfd.696952 YAPI ÜRETİMİNDE EKLEMELİ İMALAT TEKNOLOJİLERİNİN KARŞILAŞTIRMALI DEĞERLENDİRMESİ Cemal İrfan ÇALIŞKAN * Ümit ARPACIOĞLU ** Alınma: 02.03.2020; düzeltme: 18.04.2020; kabul: 08.06.2020 Öz: Bu çalışma, mimarlık alanında kullanılan eklemeli imalat teknolojileri konusunda gerçekleştirilen bir derleme çalışmasıdır. Temel olarak, eklemeli imalatın mimarlık alanındaki uygulama alanlarını, belirli sistematik içerisinde ele alan araştırma, gerek literatürde yer alan örnekler, gerekse uygulamaları bulunan yeni teknolojiler hakkında bilgi vermeyi amaçlamaktadır. Çalışmada, karşılaştırmalı olarak incelenen üretim teknolojilerinin güçlü ve zayıf yönleri, sistemlerin kullanım alanları, sistemlerde kullanılan malzemeler, mimari alan uygulamaları özelinde ele alınmıştır. Eklemeli imalat teknolojilerinin dezavantajlarından birisi olarak bilinen yüksek üretim ve malzeme maliyetinin, zaman içerisinde üretim yöntemlerinin yaygınlaşması ile çözümleneceği öngörülmektedir. Malzeme üretimi ve teknoloji konusunda halen gelişme sürecinde olan eklemeli imalat üretim sistemleri, gelecek endüstri uygulamalarında ve mimarisinde etkin olarak kullanılacağı düşünülmektedir. Yüksek maliyet sorununa çözüm olarak, eklemeli imalat yöntemi ile kalıp üretimlerinin ilerleyen yıllarda daha fazla gündemde olacağı öngörülmektedir. Anahtar Kelimeler: Eklemeli imalat, İleri teknolojiler, Yapı üretimi. A Review of Additive Manufacturing Technologies in Building Production Abstract: