Specification for the Poloidal Field Bank Modules Capacitor
Total Page:16
File Type:pdf, Size:1020Kb
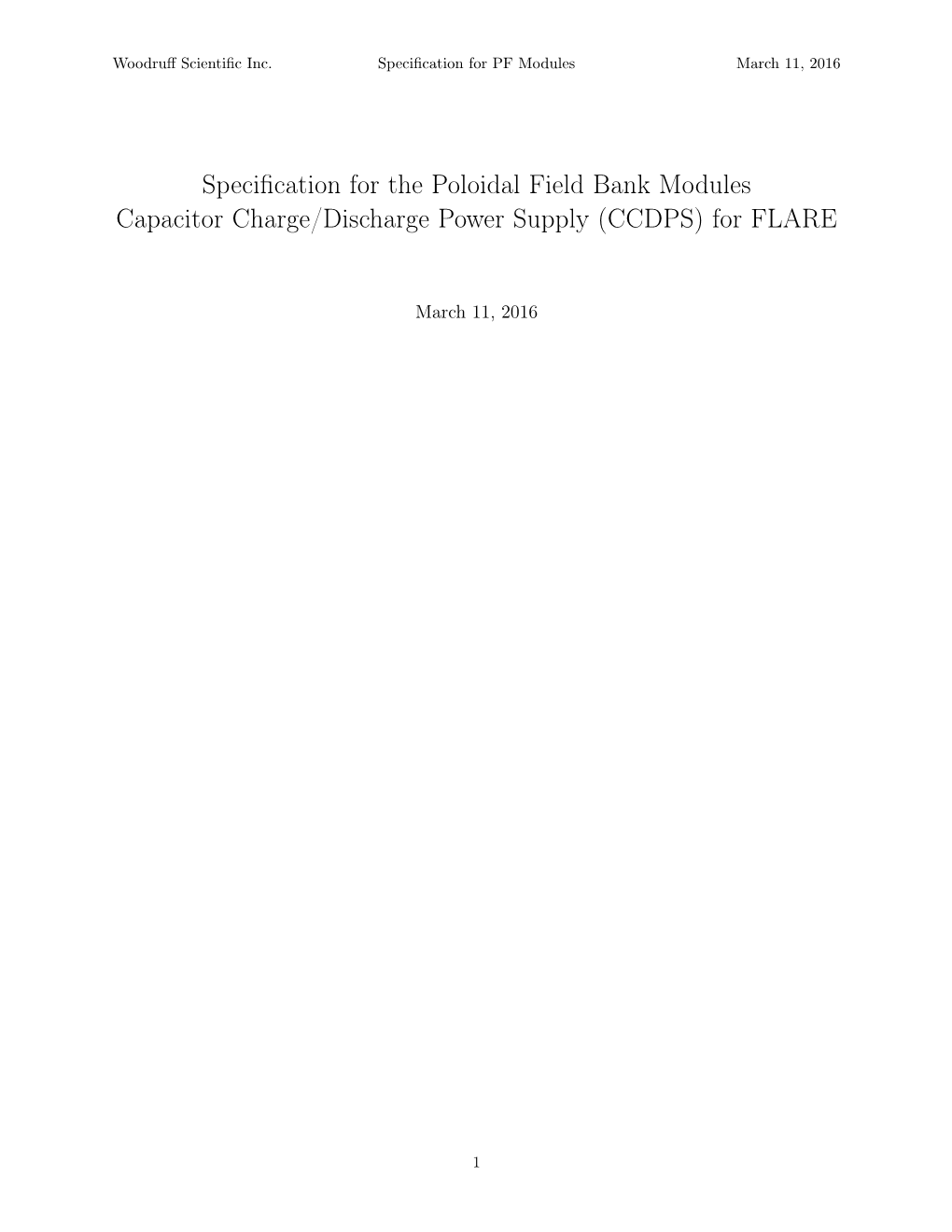
Load more
Recommended publications
-
Pulsed Power Engineering Materials, Components, & Devices
Pulsed Power Engineering Switching Devices June 13-17, 2011 Craig Burkhart & Mark Kemp Power Conversion Department SLAC National Accelerator Laboratory Ideal Switch • V = ∞ • I = ∞ • Closing/opening time = 0 • L = C = R = 0 • Simple to control • No delay or jitter • Lasts forever • Never fails June 13 - 17, 2011 USPAS Pulsed Power Engineering Burkhart & Kemp 2 Switches • Electromechanical • Vacuum • Gas – Spark gap – Thyratron – Ignitron – Plasma Opening • Solid state – Diodes • Diode opening switch – Thyrsitors • Electrically triggered • Optically triggered • dV/dt triggered – Transistors • IGBT • MOSFET June 13 - 17, 2011 USPAS Pulsed Power Engineering Burkhart & Kemp 3 Switches • Electromechanical – Open relay • To very high voltages, set by size of device • Commercial devices to ~0.5 MV, ~50 kA – Ross Engineering Corp. • Closing time ~10’s of ms typical – Large jitter, ~ms typical • Closure usually completed by arcing – Poor opening switch • Commonly used as engineered ground – Vacuum relay • Models that can open under load are available • Commercial devices – Maximum voltage ~0.1 MV – Maximum current ~0.1 kA – Tyco-kilovac – Gigavac June 13 - 17, 2011 USPAS Pulsed Power Engineering Burkhart & Kemp 4 Gas/Vacuum Switch Performance vs. Pressure June 13 - 17, 2011 USPAS Pulsed Power Engineering Burkhart & Kemp 5 Vacuum Tube (Switch Tube) • Space-charge limited current flow 1.5 – VON α V – High power tubes have high dissipation • Similar opening/closing characteristics • Maximum voltage ~0.15 MV • Maximum current ~0.5 kA, more typically << 100 A • HV grid drive • Decreasing availability • High Cost June 13 - 17, 2011 USPAS Pulsed Power Engineering Burkhart & Kemp 6 Spark Gaps • Closing switch • Generally inexpensive - in simplest form: two electrodes with a gap • Can operated from vacuum to high pressure (both sides of Paschen Curve) • Can use almost any gas or gas mixture as a dielectric. -
Pulsed Power Engineering Switching Devices
Pulsed Power Engineering Switching Devices January 12-16, 2009 Craig Burkhart, PhD Power Conversion Department SLAC National Accelerator Laboratory Ideal Switch •V = ∞ •I = ∞ • Closing/opening time = 0 • L = C = R = 0 • Simple to control • No delay or jitter •Lasts forever • Never fails January 12-16, 2009 USPAS Pulsed Power Engineering C Burkhart 2 Switches • Electromechanical • Vacuum •Gas – Spark gap – Thyratron – Ignitron – Plasma Opening • Solid state – Diodes • Diode opening switch – Thyrsitors • Electrically triggered • Optically triggered • dV/dt triggered – Transistors •IGBT • MOSFET January 12-16, 2009 USPAS Pulsed Power Engineering C Burkhart 3 Switches • Electromechanical – Open relay • To very high voltages, set by size of device • Commercial devices to ~0.5 MV, ~50 kA – Ross Engineering Corp. • Closing time ~10’s of ms typical – Large jitter, ~ms typical • Closure usually completed by arcing – Poor opening switch • Commonly used as engineered ground – Vacuum relay • Models that can open under load are available • Commercial devices – Maximum voltage ~0.1 MV – Maximum current ~0.1 kA – Tyco-kilovac –Gigavac January 12-16, 2009 USPAS Pulsed Power Engineering C Burkhart 4 Gas/Vacuum Switch Performance vs. Pressure January 12-16, 2009 USPAS Pulsed Power Engineering E Cook 5 Vacuum Tube (Switch Tube) • Space-charge limited current flow 1.5 –VON α V – High power tubes have high dissipation • Similar opening/closing characteristics • Maximum voltage ~0.15 MV • Maximum current ~0.5 kA, more typically << 100 A • HV grid drive • Decreasing availability • High Cost January 12-16, 2009 USPAS Pulsed Power Engineering C Burkhart 6 Spark Gaps • Closing switch • Generally inexpensive - in simplest form: two electrodes with a gap • Can operated from vacuum to high pressure (both sides of Paschen Curve) • Can use almost any gas or gas mixture as a dielectric. -
Proof-Of-Concept Experiments on a Gallium- Based Ignitron for Pulsed Power Applications
National Aeronautics and NASA/TM—2015–218202 Space Administration IS20 George C. Marshall Space Flight Center Huntsville, Alabama 35812 Proof-of-Concept Experiments on a Gallium- Based Ignitron for Pulsed Power Applications H.K. Ali, V.S. Hanson, K.A. Polzin, and J.B. Pearson Marshall Space Flight Center, Huntsville, Alabama February 2015 The NASA STI Program…in Profile Since its founding, NASA has been dedicated to the • CONFERENCE PUBLICATION. Collected advancement of aeronautics and space science. The papers from scientific and technical conferences, NASA Scientific and Technical Information (STI) symposia, seminars, or other meetings sponsored Program Office plays a key part in helping NASA or cosponsored by NASA. maintain this important role. • SPECIAL PUBLICATION. Scientific, technical, The NASA STI Program Office is operated by or historical information from NASA programs, Langley Research Center, the lead center for projects, and mission, often concerned with NASA’s scientific and technical information. The subjects having substantial public interest. NASA STI Program Office provides access to the NASA STI Database, the largest collection of • TECHNICAL TRANSLATION. aeronautical and space science STI in the world. English-language translations of foreign The Program Office is also NASA’s institutional scientific and technical material pertinent to mechanism for disseminating the results of its NASA’s mission. research and development activities. These results are published by NASA in the NASA STI Report Specialized services that complement the STI Series, which includes the following report types: Program Office’s diverse offerings include creating custom thesauri, building customized databases, • TECHNICAL PUBLICATION. Reports of organizing and publishing research results…even completed research or a major significant providing videos. -
Methods of Magnetizing Permanent Magnets EMCW Coil Winding Show 1 October-2 November 2000 Cincinnati , Ohio
Methods of Magnetizing Permanent Magnets EMCW Coil Winding Show 1 October-2 November 2000 Cincinnati , Ohio Joseph J. Stupak Jr. Oersted Technology Corp. 19480 SW Mohave Ct. Tualatin, Oregon USA 97063 Tel (503) 612-9860 fax (503) 692-3518 email [email protected] Copyright Oersted Technology 2000 Methods of Magnetizing Permanent Magnets 1. Introduction Many people find magnets to be strange, mysterious things, and I think that physicists are puzzled a good deal more by them then they like to admit. Magnets have been with us a long time, in fact from our earliest history, long before formal science was started, or the mathematics we use to describe it. We all know what magnets do. Magnets have locations on them, called poles. Poles come in two types, which we call North-seeking poles, or just North poles, and South poles. They always occur in pairs of equal strength, although they may have more than just two poles, of course. Opposite pole types attract, while poles of the same type repel each other. Poles of either type attract iron, steel, and a few other metals such as nickel. These things have been known for thousands of years. Much more recently, that is in the last two hundred years, we have found out that electricity and magnetism are related, and most of the time today we will be talking about ways to use electricity to make certain special materials, called permanent magnet materials, to be magnetic. When magnets are first produced, they are usually not magnetic at all, or possibly they are only very weakly magnetic. -
H DEC 1067 /G&L
SIMPLE THYRISTOR CIRCUITS TO PULSE-FIRE IGNITRONS FOR EP-RR 16 CAPACITOR DISCHARGE H DEC 1067 /G&l C. F. VANCE March, 1967 Department of Engineering Physics Research School of Physical Sciences THE AUSTRALIAN NATIONAL UNIVERSITY ra, A.C.T., Australia. HANCOCK TJ163.A87 EP-RR16. f T.J 1 63* 1924138 . A87 F. P - R R 1 6 A.N.U. LIBRARY This book was published by ANU Press between 1965–1991. This republication is part of the digitisation project being carried out by Scholarly Information Services/Library and ANU Press. This project aims to make past scholarly works published by The Australian National University available to a global audience under its open-access policy. SIMPLE THYRISTOR CIRCUITS TO PULSE-FIRE IGNITRONS FOR CAPACITOR DISCHARGE H DEC 1967 by C. F. VANCE M arch. 1967 Publication EP-RR 16 Department of Engineering Physics Research School of Physical Sciences THE AUSTRALIAN NATIONAL UNIVERSITY C anberra, A.C.T. A ustralia S UMMARY Simple thyristor circuits have been used for firing capacitor-discharge ignitrons in a plasma physics * experiment. Experience of over 18, 000 discharges shows that the problem of semiconductor failure in an environ ment of high voltage transients can be overcome by atten tion to screening and filtering. Speed limitations of present-day thyristors are discussed and found acceptable for medium-speed plasma experiments. *(By October 1967, 48, 000 trouble-free discharges have been obtained). ii 1 . INTRODUCTION The use of thyristors in place of thyratrons has been advertised by a number of manufacturers for some time, including their use for firing ignitrons. -
Semiconductor Switches Replace Thyratrons and Ignitrons
SEMICONDUCTOR SWITCHES REPLACE THYRATRONS AND IGNITRONS A. Welleman, E. Ramezani, U. Schlapbach ABB Semiconductors AG, CH-5600 Lenzburg, Switzerland Abstract A solid state switching system is presented which is designed a high reliable, long life, low maintenance product for short repetitive and high di/dt pulses. The solid state switch uses special designed semiconductor devices with integrated fast triggering circuits which are powered by one closed loop current source power supply. Blocking voltages of over 30 kV are possible by stacking several devices in series connection. The solid state system has no environmental restrictions and can be used in any position 1) INTRODUCTION Since several years ABB is offering complete solid state switches which are based on a wide range of specific devices which are designed for non-repetitive pulsed power applications. More recently, interest has been shown in fast semiconductor switches which can be used at medium frequencies, to replace thyratrons and ignitrons because of longer life, no use of mercury and almost no maintenance. For this applications, ABB has designed a new platform technology and is using this concept in a range of different switches. These switches are so called Power Parts, as they are built up as an assembly with semiconductors, drivers, clamping, cooling, power supply and triggering, but are without cabinet or control system. 2) SEMICONDUCTOR DEVICES The evolution of silicon wafers for high di/dt application started about 1975 with the central gate SCR’s capable to handle 200 – 400 A/ms, followed later by higher interdigitated gate structures which allowed about to double these values. -
ERADICATION of MERCURY IGNITRON from the 400 Ka MAGNETIC HORN PULSE GENERATOR for CERN ANTIPROTON DECELERATOR V
9th International Particle Accelerator Conference IPAC2018, Vancouver, BC, Canada JACoW Publishing ISBN: 978-3-95450-184-7 doi:10.18429/JACoW-IPAC2018-WEPMF086 ERADICATION OF MERCURY IGNITRON FROM THE 400 kA MAGNETIC HORN PULSE GENERATOR FOR CERN ANTIPROTON DECELERATOR V. Namora, M. Calviani, L. Ducimetière, P. Faure, L.E. Fernandez, G. Grawer, V. Senaj, CERN, Geneva, Switzerland Abstract AD-HORN DESCRIPTION The CERN Antiproton Decelerator (AD) produces low- energy antiprotons for studies of antimatter. A 26 GeV A very low inductance stripline connects the AD horn to proton beam impacts the AD production target which the 400 kA pulse generator. The power pulse is produces secondary particles including antiprotons. A synchronized with the PS 26 GeV/c proton beam magnetic Horn (AD-Horn) in the AD target area is used to impinging on the target. focus the diverging antiproton beam and increase the The nuclear interactions between the proton beam and antiproton yield enormously. The Horn is pulsed with a the spallation material of the target are responsible for the current of 400 kA, generated by capacitor discharge type production of secondary particles, among which anti- generators equipped with ignitrons. These mercury-filled protons. The secondary particles emerge from the target devices present a serious danger of environmental with a large spectrum momentum and angular distribution. pollution in case of accident and safety constraints. An A fraction of the charged particles entering the magnetic alternative has been developed using solid-state switches volume generated in the horn can be deviated into a parallel and diodes. Similar technology was already implemented beam towards the magnetic spectrometer in the target area at CERN for ignitron eradication in the SPS Horizontal which further selects the particle momentum to beam dump in the early 2000s. -
Reproduced DISTRIBUTI
HlU <epoit wo |>tcpand H an icccn.nl of wi.it •PonaoiM oy eile üiul«! Staici Gommimi. Neilkei PIT NrllRAL INJf.CrUW ICMTKO', ACCEI.FfcAïiNG SlTPl.Y» Ine Un»«« Sui» noi il» Unii«) SUM Enei» Keieaith and Development Uminìattation, IM» any of Hie» employe«, not any or »Kit antluclora. uiknnloclon. 01 theli «mploytea, makes any D. L. Ashcroft, 1. I", "urray, R. A. N\,-an, F. L. Petir^on waranly, etpieu 01 implied, ot ammea any letal liability 01 leiponiltiilily for tneaccuraty.tomplelene» Plasn.i Physics Laboratory, l'rliu-i.-ton L'nivcrsity m welulne* of any Moiniaiioi, appaiali», produci oi Princeton, New Jersey 08540 profeti diatloiea. or tepieietiti thai Ut we would not infringe privately owned lithli, Siimjrv pulse current, while the ignitron average current rating can be closer to the value averaged over A |h 1-.1. -cont ml led rectifier has been designed for the entire interval between pulses. t!ic ii c.Kr.it in« supply on the PLT Neutral Beim Injec- tion 4v«.tera .it i'l'FI.. The rectifier must furnish 70 3. Arc-backs and overloads do not result in pi-rr.ti;enc ...,-vriS .ic up to 50 KV for 300 milliseconds, with a damage Co ignitrons if. the faults are tcouwti in .lutv i-vr to of up to 102. Protection of the injectors the time it takes a circuit breaV.tr to open, r-. ini res the supply to withstand repeated crowbarring. whereas they can be catastrophic to SCR's (the Pi-.- rectifying element selected to satisfy those re- ignitrons in tiiis rectifier could withstand a )ju i ri-.-:i-nts was a comnerc ia.1 ly-avai table ignttron, bolted output short with the current limited by i.i-t.il li'd in .i supporting frame and using firing cir- the reactance in the transformer and power 1 ine . -
Lawrence Berkeley National Laboratory Recent Work
Lawrence Berkeley National Laboratory Recent Work Title BEVATRON POWER SUPPLY OPERATING AND MAINTENANCE PROBLEMS Permalink https://escholarship.org/uc/item/6hs149rh Author Harding, J.G. Publication Date 1957-08-12 eScholarship.org Powered by the California Digital Library University of California UCRL q%7 - UNIVERSITY OF CALIFORNIA TWO-WEEK LOAN COPY This is a Library Circulating Copy which may be borrowed for two weeks. For a personal retention copy, call Tech. Info. Division, Ext. 5545 BERKELEY, CALIFORNIA DISCLAIMER This document was prepared as an account of work sponsored by the United States Government. While this document is believed to contain correct information, neither the United States Government nor any agency thereof, nor the Regents of the University of California, nor any of their employees, makes any warranty, express or implied, or assumes any legal responsibility for the accuracy, completeness, or usefulness of any information, apparatus, product, or process disclosed, or represents that its use would not infringe privately owned rights. Reference herein to any specific commercial product, process, or service by its trade name, trademark, manufacturer, or otherwise, does not necessarily constitute or imply its endorsement, recommendation, or favoring by the United States Government or any agency thereof, or the Regents of the University of California. The views and opinions of authors expressed herein do not necessarily state or reflect those of the United States Government or any agency thereof or the Regents of the University of California. 39;'? Text bf, AlEE Conference paper on Bevatron Power Supply and presented at Pasco, Washington, August, 1957 BEVATRON POWER SUPPLY OPERATING AND MAINTENANCE PROBLEMS by J. -
Design and Construction of a Z-Pinch Apparatus for Metal
DESIGN AND CONSTRUCTION OF A Z-PINCH APPARATUS FOR METAL- CATALYZED FUSION EXPERIMENTS by Shannon R. Walch Submitted to Brigham Young University in partial fulfillment of graduation requirements for University Honors Advisor: Steven E. Jones Honors Representative: Brian Woodfield Signature:________________________ Signature:_______________________ ABSTRACT DESIGN AND CONSTRUCTION OF A Z-PINCH APPARATUS FOR METAL- CATALYZED FUSION EXPERIMENTS Metal-catalyzed fusion, also called laboratory nuclear astrophysics, is the study of the interactions of deuterium and metals. Previous experiments in this field have focused primarily on the interactions of deuterium in metal lattices. The Alternate Energy Research Group at BYU decided to build a z-pinch device to explore the interactions of deuterium in metal plasmas. This paper describes the design and construction of a z- pinch device to be used for these experiments. A brief history of metal-catalyzed fusion and of the use of z-pinch devices in fusion experiments is included. Our reasons for choosing a z-pinch device is discussed, and our goals for the apparatus and the planned experiments. The designs and construction of the device are included, as well as those for accompanying voltage and current sensors. Our z-pinch has successfully blown up 25 micron copper wires at voltages of approximately 18 kV. Further calibration of our current sensor is required before accurate measurement of the current through the exploding wire is made. We plan to continue refining our apparatus and set up a neutron detector so that we may begin measuring the neutrons emitted from the explosion of deuterium-loaded wires for possible enhancements. -
Ignitron Trigger Circuit
IGNITRON TRIGGER CIRCUIT by John F. O’Hara III Senior Project ELECTRICAL ENGINEERING DEPARTMENT California Polytechnic State University San Luis Obispo June, 2012 i Table of Contents Table of Contents ........................................................................................................................................... i List of Tables and Figures ............................................................................................................................. ii Abstract ........................................................................................................................................................ iii Acknowledgements ...................................................................................................................................... iv CHAPTER 1 - INTRODUCTION ............................................................................................................. 1 1.1 Electromagnetic Rail Gun Triggering Circuit ............................................................................ 1 1.2 Background ................................................................................................................................ 2 CHAPTER 2 – SYSTEM COMPONENT DESIGN ................................................................................ 3 2.1 Ignitron ....................................................................................................................................... 3 2.2 Arduino ..................................................................................................................................... -
Use of Diode As a Crowbar for Electromagnetic Launcher
Downloaded from http://iranpaper.ir http://www.itrans24.com/landing1.html 2016 International Conference on Automatic Control and Dynamic Optimization Techniques (ICACDOT) International Institute of Information Technology (I²IT), Pune Use Of Diode As A Crowbar For Electromagnetic Launcher Pradnya Pawar, A.B.Patil Gaurav Kumar, Pradeep Kumar Pimpri Chinchwad College of Engineering ARDE-DRDO, Pashan Pune, India Pune, India [email protected] Abstract— High current high voltage switches are extensively others due to its simplicity but found limitations in case of used for power applications. Electromagnetic launcher (Railgun) modular power supplies. As evident from previous discussion requires switching large current in the proper sequence to ensure the switch used in the railgun has to discharge the stored acceleration of projectiles to attain required velocities. These energy from the capacitors and the response time should be power applications require current of the order of Mega Ampere minimal, and can handle very high di/dt. The selection of for 5-10 ms and hence need special purpose switches. The Spark Gap or Ignitron are conventionally used for power application as switches mainly based on the power rating and the technology a crowbar switch. These switches operate at high voltage and used [1]. The conventional switches are having limitations to high current capacity but have low reliability, robustness and operate at these high voltage and high current capacity. Spark lifespan. In this paper ignitron as a crowbar switch is replaced by gap gives poor reliability and Ignitron is having drawback of diode switch. This reduced negative overshoot in the current. short service life.