File No.APPCB-11022/29/2018-TEC-CFO-APPCB
Total Page:16
File Type:pdf, Size:1020Kb
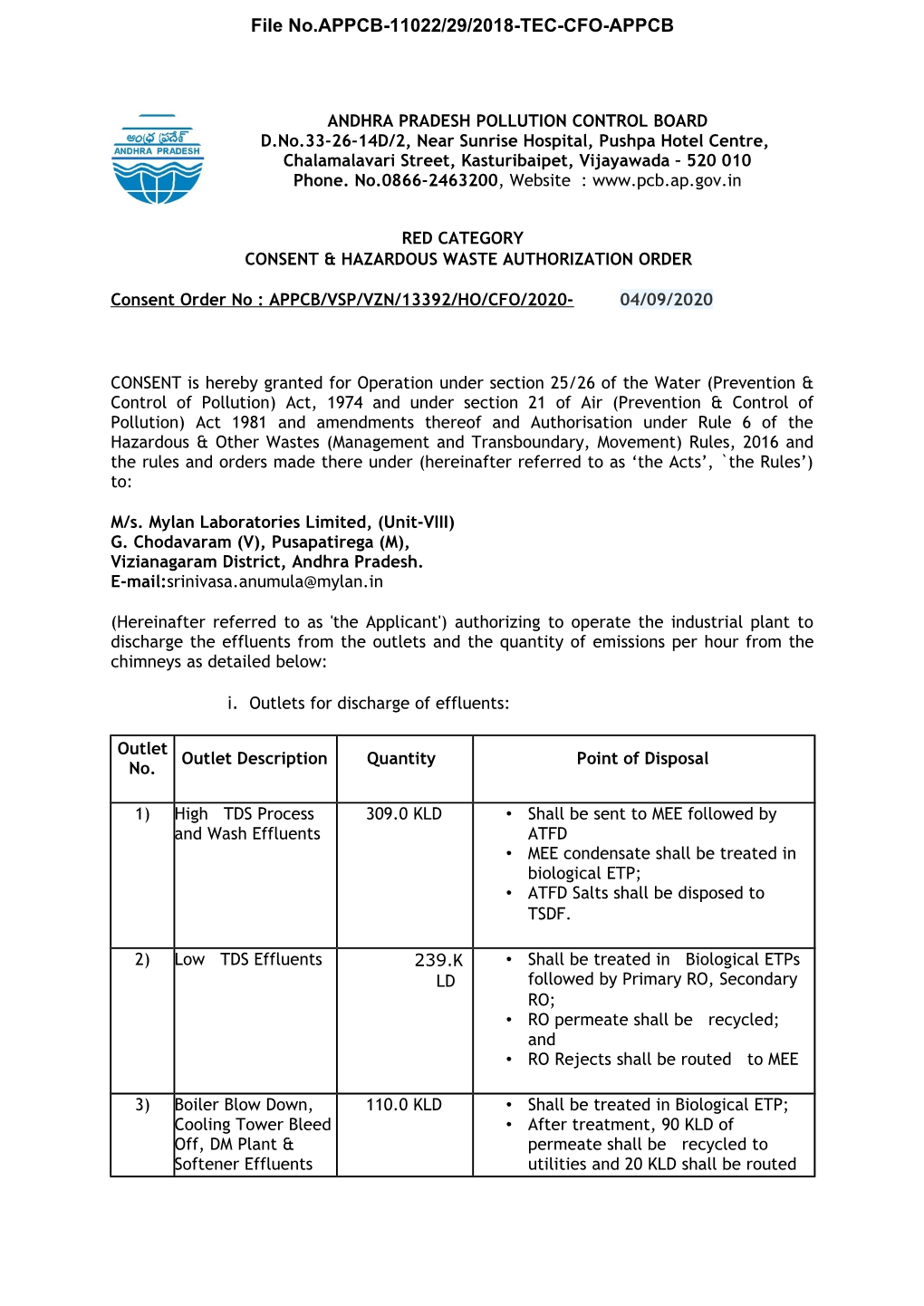
Load more
Recommended publications
-
Nadu Nedu Status 31.01.2020.Xlsx
MANA BADI :: NEDU-NEDU Estimation Sl.No U-Dise Code Mandal School Name Cost(Rs.) 1 28120100202 KOMARADA GTWAS YENDABHADRA 1774691 2 28120100402 KOMARADA MPPS PEDASEKHA 1788018 3 28120101804 KOMARADA MPUPS KUNERU 1795851 4 28120102001 KOMARADA MPPS JAKURU 1790596 5 28120103401 KOMARADA MPPS RAMABHADRAPURAM 1795204 6 28120103404 KOMARADA GTWAS ULIPIRI 4065352 7 28120104101 KOMARADA MPPS RAVIKONA 1802201 8 28120104201 KOMARADA MPPS TULASIVALSA 1671646 9 28120104205 KOMARADA GTWAS KEMISEELA 2209003 10 28120104501 KOMARADA MPPS DEVUKONA 1084658 11 28120105410 KOMARADA APSWRS KOMARADA 4347202 12 28120105411 KOMARADA APTWRS(BOYS) KOMARADA 5402775 13 28120105413 KOMARADA KGBV KOMARADA 3224302 14 28120106001 KOMARADA MPPS SARVAPADU 1782638 15 28120106104 KOMARADA GTWAS PEDAKHERJALA 4093219 16 28120106501 KOMARADA MPPS MADALANGI 1767129 17 28120106901 KOMARADA MPPS DALAIPETA 1742497 18 28120107202 KOMARADA MPPS GUMADA 1780099 19 28120107403 KOMARADA MPPS KOTIPAM BC COL 1759449 20 28120107404 KOMARADA ZPHS KOTIPAM 3258493 21 28120107704 KOMARADA MPUPS RAJYALAXMIPURAM 1747037 22 28120107901 KOMARADA MPPS KUMMARIGUNTA 1748347 23 28120108501 KOMARADA MPPS KALLIKOTA 1787473 24 28120108701 KOMARADA MPPS DUGGI 2379167 25 28120108801 KOMARADA MPPS ARTHAM 1118425 26 28120109604 KOMARADA MPPS SIVINI 1771139 27 28120109702 KOMARADA MPPS VIKRAMPURAM 1759597 28 28120109801 KOMARADA MPUPS PARASURAMPURAM 1786535 29 28120109901 KOMARADA MPPS GUNNANAPURAM 1776239 30 28120200701 G.L.PURAM GPS KEESARI 1834782 31 28120200901 G.L.PURAM GPS VANGARA 1829861 32 28120201204 -
Government of India India Meteorological Department आंध्र प्रदेश केलिए साप्तालिक मौसम रिपो셍ट Weekly Weather Report for Andhra Pradesh & Yanam
1 GOVERNMENT OF INDIA INDIA METEOROLOGICAL DEPARTMENT आंध्र प्रदेश केलिए साप्तालिक मौसम रिपो셍ट WEEKLY WEATHER REPORT FOR ANDHRA PRADESH & YANAM आन्ध्र प्रदेश के लिए लदना車क 29-09-2021/ 7th अश्विन 1943 ( शक) For the week ending Wednesday 29th September, 2021 / 7th Asvina 1943 (SAKA) मौसम का सािा車श /SUMMARY OF WEATHER सप्ताहकीवषाादिना車क 23-09-2021 से 29-09-2021 (जिलावार) Week's Rainfall from 23-09-2021 से 29-09-2021(Districtwise) SRIKAKULAM, VIZIANAGARAM, VISAKHAPATNAM, EAST GODAVARI, LARGE EXCESS WEST GODAVARI, KRISHNA, YANAM. EXCESS GUNTUR NORMAL NELLORE, PRAKASAM, CUDDAPAH, CHITTOOR. DEFFICIENT NIL LARGE DEFICIENT ANANTAPUR, KURNOOL. NO RAIN NIL. वषााकीमु奍यमात्रा (से.मी. मᴂ)/Chief amounts of rainfall (in cm.): COASTAL A.P. & YANAM 09-23-2021 Yelamanchili (dist Vishakhapatnam) 8, Bobbili (dist Vizianagaram) 4, Rajahmundry (dist East Godavari) 3, Tuni (dist East Godavari) 3, Chintur (dist East Godavari) 2, Tadepalligudem (dist West Godavari) 2, Peddapuram (dist East Godavari) 1, Kakinada (dist East Godavari) 1, Veeraghattam (dist Srikakulam) 1, Prathipadu (dist East Godavari) 1, Koida (dist West Godavari) 1, Dowleshwaram (dist East Godavari) 1, Jiyyamma Valasa (dist Vizianagaram) 1, Avanigada (dist Krishna) 1, Parvathipuram (dist Vizianagaram) 1, Cheepurupalle (dist Vizianagaram) 1, Pusapatirega (dist Vizianagaram) 1 2 09-24-2021 Bondapalle (dist Vizianagaram) 5, Gajapathinagaram (dist Vizianagaram) 3, Koida (dist West Godavari) 3, Visakhapatnam Ap (dist Vishakhapatnam) 3, Paderu (dist Vishakhapatnam) 3, Vararamachandrapur (dist East Godavari) -
District Survey Report Vizianagaram District
District Survey Report - 2018 DEPARTMENT OF MINES AND GEOLOGY Government of Andhra Pradesh DISTRICT SURVEY REPORT VIZIANAGARAM DISTRICT Prepared by ANDHRA PRADESH SPACE APPLICATIONS CENTRE (APSAC) DMG, GoAP 1 District Survey Report - 2018 Planning Department, Govt. of Andhra Pradesh 2018 ACKNOWLEDGEMENTS We are grateful to the Secretary to Government (Mines) and the Director, Department of Mines and Geology, Govt. of Andhra Pradesh for entrusting the work for preparation of District Survey Reports of Andhra Pradesh. We gratefully acknowledge the help of the Director, Directorate of Economics and Statistics, Planning Department, Govt. of A.P. for providing valuable literature. We owe a great deal to Sri. G.Sreenivas Choudhary, Deputy Director, (Mines) for his overall support and guidance during the execution of this work. We are also thankful to the Assistant Directors of Mines and Geology of Vijayawada and Nandigama offices for their support in providing information. Our sincere thanks are due to the scientific staff of APSAC who has generated all the thematic maps. VICE CHAIRMAN APSAC DMG, GoAP 2 District Survey Report - 2018 Table of Contents ........................................................................................... 6 1. Salient Features of Vizianagaram District .................................................................................................................... 6 1.1 Administrative Setup ..................................................................................................................................... -
Srikakulam District Vizianagaram District
! ! ! ! ! ! ! ! ! ! ! ! ! ! ! ! ! ! ! ! ! ! ! ! ! ! ! ! ! ! ! ! ! ! ! ! ! ! ! ! ! ! ! ! ! ! ! ! ! ! ! ! ! ! ! ! ! ! ! ! ! ! ! ! ! ! ! ! ! ! ! ! ! ! ! ! ! ! ! ! ! ! ! ! ! ! ! ! ! ! ! ! ! ! ! ! ! ! ! ! ! ! ! ! ! ! ! ! Å!"! !! ! ! ! ! ! ! ! ! ! ! ! ! ! ! ! ! ! ! ! ! ! ! ! ! ! ! ! ! ! ! ! ! ! ! ! ! ! ! ! ! ! ! ! ! ! ! ! ! ! ! ! ! ! ! ! ! ! ! ! ! ! ! ! ! ! ! ! ! ! ! ! ! ! ! ! ! ! ! ! ! ! ! ! ! ! ! ! ! ! ! ! ! ! ! ! ! ! ! ! ! ! Zam m unarayanapuram Dam arasingi VIiZzIiAaNnAagGaArRaAmM GURLA MANDAL Gushini Municipal 18m MASTER PLAN FOR VISAKHAPATNAM MANDAL 18 m Dannanapeta Madhupada Corporation Alugolu m METROPOLITAN REGION 0 3 6 GARIVIDI 0m m 18 MANDAL Artham uru PUSAPATIREGA MANDAL 30m Thangudubilli m 8 (PROPOSED LANDUSE - 2041) 1 Korlam Saripalle m 45m 18 3 m (Pre pare d a s per p rovisions o f sectio n 1 1(2) A ndhra Prad esh M etropo litan R egions and Urban D evelopm ent 0 8 4 m Atm aram uniagraharam 5 1 45m Autho rities (A PMR & UDA A ct, 2016 ) 2 m Sathivada m 3 8 0 1 6 m 3 1 m 45m 8 60 m 5 m m 8 30 1 3 7 2 0 4 4 m m 30m 8 30m 10 Pinatharim i Legend 2 2 Pedatadivada 4 4 m Nandigam a m m 0 25 23 8m 6 9 1 0m 24 11 Altipalem 2 Munginapalle 8 m VMR Boundary 4m 14 8 122 12 1 Boppadam 2 26 22 4 27 45m m m 86 29 8 0m 13 Mandal Boundary 1 8 1 85 21 123 87 28 24 121 m 18m 20 1 80m 80 84 18 8 m 119 91 Tham m apuram 1 ZDP Boundary m 92 15 8m 30 45m 118 88 31 NELLIMARLA 45m m 93 19 4 83 1 2 18 120 82 17 16 m m m 117 94 MANDAL Village Boundary 8 8 89 90 96 2 1 1 33 4 3 45m 4 m 81 32 2 24 80m 115 18 m 124 99 35 11 m 4 m 97 95 34 6 5m 8 75 80 Municipal -
(SAKA) Week's Rainfall from 13-06-2019 to 19-06-2019 (Dis
1 GOVERNMENT OF INDIA INDIA METEOROLOGICAL DEPARTMENT तेलंगाना के िलए सााहक मौसम रपोट WEEKLY WEATHER REPORT FOR ANDHRA PRADESH & Yanam of Puducherry (UT) For the week ending Wednesday, 19th June , 2019 /29th Jyaistha, 1941 (SAKA) मौसम का सारांश/SUMMARY OF WEATHER Week's Rainfall from 13-06-2019 to 19-06-2019 (Districtwise) LARGE EXCESS NIL EXCESS NIL NORMAL NIL DEFFICIENT VIZIANAGARAM EAST GODAVARI , GUNTUR , KRISHNA , NELLORE , SRIKAKULAM , VISHAKHAPATNAM , WEST GODAVARI , YANAM , ANANTAPUR , LARGE DEFICIENT CHITTOOR , CUDDAPAH , KURNOOL, NO RAIN PRAKASAM Chief amounts of rainfall (in cm.): COASTAL A.P. & YANAM 13-06-2019: Araku Valley (dist Vishakhapatnam) 2, Guntur (dist Guntur) 2, Salur (dist Vizianagaram) 1, Sattenapalle (dist Guntur) 1 14-06-2019: NONE 15-06-2019: Chintur (dist East Godavari) 3, Chodavaram (dist Vishakhapatnam) 1, Merakamudidam (dist Vizianagaram) 1, Sullurpeta (dist Nellore) 1 16-06-2019: Ichchapuram (dist Srikakulam) 3, Gajapathinagaram (dist Vizianagaram) 2, Tekkali (dist Srikakulam) 1, Kalingapatnam (dist Srikakulam) 1 17-06-2019: Ranastalam (dist Srikakulam) 6, Pusapatirega (dist Vizianagaram) 3, Therlam (dist Vizianagaram) 2, Balajipeta (dist Vizianagaram) 2, Chodavaram (dist Vishakhapatnam) 2, Gajapathinagaram (dist Vizianagaram) 2, Bobbili (dist Vizianagaram) 2, Bheemunipatnam (dist Vishakhapatnam) 2, Cheepurupalle (dist Vizianagaram) 2, Yelamanchili (dist Vishakhapatnam) 1, Mentada (dist Vizianagaram) 1, Merakamudidam (dist Vizianagaram) 1, Garugubilli (dist Vizianagaram) 1, Bondapalle (dist Vizianagaram) -
Andhra Pradesh 155Th SEAC , Andhra
State Expert Appraisal Committee (SEAC) Andhra Pradesh 155th SEAC , Andhra Pradesh Meeting , Part-5 AGENDA Venue: Visakhapatnam , A.P. Please Check MoEF&CC Website at www.parivesh.nic.in for details and updates From Date:08 Dec 2020 TO Date:11 Dec 2020 Date when Agenda was Created:12 May 2021 CONSIDERATION/RECONSIDERATION OF ENVIRONMENTAL CLEARANCE S.No Proposal M/s. Amaravati Life Sciences S. State District Tehsil Village (1) No. (1.) Andhra Pradesh Guntur Durgi Kolagutla village [SIA/AP/IND2/176185/2020 , AP GTR MIN 11 2020 2448 ] SRI SIRIGUDI GOVINDA RAO S. State District Tehsil Village (2) No. (1.) Andhra Pradesh Vizianagaram Pusapatirega Kumili [SIA/AP/MIN/182597/2020 , AP VZM MIN 11 2020 2336 ] Sri B.Subhagiri (Road Metal, Building Stone & Gravel Extent:4.89 Acres / 1.980 Hectares) S. State District Tehsil Village (3) No. Chandragiri (1.) Andhra Pradesh Chittoor Chandragiri (Pichinaidupalli) [SIA/AP/MIN/182620/2020 , AP CTR MIN 11 2020 2335 ] Sri. G. B. Siva Kumar S. State District Tehsil Village (4) No. (1.) Andhra Pradesh Anantapur Gudibanda Kekathi [SIA/AP/MIN/182689/2020 , AP ANT MIN 11 2020 2334 ] M/s. Sree Raksha Constructions (5) S. State District Tehsil Village No. (1.) Andhra Pradesh Anantapur Gorantla Budili [SIA/AP/MIN/182733/2020 , AP ANT MIN 11 2020 2348 ] Sri B.Subhagiri (Road Metal, Building Stone & Gravel Extent:5.68 Acres / 2.300 Hectares) S. State District Tehsil Village (6) No. Chandragiri (1.) Andhra Pradesh Chittoor Chandragiri (Pichinaidupalli) [SIA/AP/MIN/182750/2020 , AP CTR MIN 11 2020 2333 ] Sri S.Narayana Reddy (Road Metal & Building Stone) Ex:4.402 Ha) S. -
Brief Industrial Profile of Vizianagaram District
1 G o v e r n me n t o f I n d i a Mi n i s t r y o f MS ME Brief Industrial Profile of Vizianagaram District Carried out by M S ME - De v e l o pm e nt I ns t it u t e ( B r a nc h) (Ministry of MSME, Govt. of India,) F-19-22, Block-D, Autonagar, Visakhapatnam TeleFax: 0891-2517942; Ph.No: 0891-2701061 e-mail: [email protected] [email protected] Brief profile of Vizianagaram District, Andhra Pradesh 2 Contents S. No. Topic 1. General Characteristics of the District 1.1 Location & Geographical Area 1.2 Topography 1.3 Availability of Minerals. 1.4 Forest 1.5 Administrative set up 2. District at a glance 2.1 Existing Status of Industrial Area in the District Vizianagaram 3. Industrial Scenario Of Vizianagaram district 3.1 Industry at a Glance 3.2 Year Wise Trend Of Units Registered 3.3 Details Of Existing Micro & Small Enterprises & Artisan Units In The District 3.4 Large Scale Industries / Public Sector undertakings 3.5 Major Exportable Item 3.6 Growth Trend 3.7 Vendorisation / Ancillarisation of the Industry 3.8 Medium Scale Enterprises 3.8.1 List of the units in Vizianagaram & near by Area 3.8.2 Major Exportable Item 3.9 Service Enterprises 3.9.1 Coaching Industry 3.9.2 Potentials areas for service industry 3.10 Potential for new MSMEs 4. Existing Clusters of Micro & Small Enterprise 4.1 Detail Of Major Clusters 4.1.1 Manufacturing Sector 4.1.2 Service Sector 4.2 Details of Identified cluster 4.2.1 Welding Electrodes 4.2.2 Stone cluster 4.2.3 Chemical cluster 4.2.4 Fabrication and General Engg Cluster 4.2. -
Visakhapatnam District Vizianagaram District
! ! ! ! ! ! ! ! ! ! ! ! ! ! ! ! ! ! ! ! ! ! ! ! ! !! ! ! ! ! ! ! ! ! ! ! ! ! ! ! ! ! ! ! ! ! ! ! ! ! ! ! ! ! ! ! ! ! ! ! ! ! ! ! ! ! ! ! ! ! ! ! ! m 24m m 4 8 Dwarapureddipalem 5m 5 1 Kum ili 4 Vedullavalasa m Ch ittigunkalam 18 Am akam Pinatadivada MASTER PLAN FOR VISAKHAPATNAM m m 3 5 5 0 4 m 4 45m 45m METROPOLITAN REGION m 8 1 Jonnada 1 BHOGHAPURAM MANDAL 8m m m 8 Bellam 18m 5 1 4 4 Korada 5m (PROPOSED LANDUSE - 2041) 45 m PADMANABHAM (Pre pare d a s per p rovisions o f sectio n 1 1(2) A ndhra Prad esh M etropo litan R egions and Urban D evelopm ent 18 m Autho rities (A PMR & UDA A ct, 2016 ) m 4 MANDAL 4 2 5m m 18 3 5 m 0 4 m Rellivalasa 2 1 Rajula 4 m 18 8 Denkada m 4 m m 4 2 T am m apuram 5m m m 5 18m 8 4 2 1 4m D.T allavalasa 18m Legend m 4m 5 2 Pedada 4 m 5 2 4 4 VMR Boundary m 18m 18m m 5 Mandal Boundary 2 4 1 4 Bodam ettapalem 45m m 18 4m m m m 2 m 2 5 8 5 4 1 m 4 ZDP Boundary m 4 24 3 5 5 24 13 4 m m 4 5m 5 4 1 8m 8m Village Boundary 1 6 18 45 m m m 2 14 8 m 4m 7 18 1 5 4 Municipal Boundary 8m 1 8 m 19 Singavaram 5 18m m 15 17 4 4 5 52 2 5m 4 Gantlam 9 Survey Boundary 4 m m 10 24 3 4 8 23 6 5 Pusapatipalem 1 18 m 1 m 8 m 16 20 m 90/2017 m 5 4 11 22 Residential Layout 4 Bantupalle 5m m 45 12 m Vizianagaram m 25 5 8 1 1 8 APIIC 4 m Industrial Layout m 45 2 21 26 1 4 m DENKADA 270 4 8 2 18m 3 18 m m 0 m 30 m 1 m m Dakam arri 8 27 6m 5 MANDAL 3 National Highway 5 m 28 1 4 4 8 4 31 m 5 33 m m District 8 252 32 1 m 1 24m m State Highway 5 8 24 1 1 251 42 4 m 1 8 8 8 m 87 m 3 43 m m 29 1 271 0 8 4 1 253 250 34 m m 2 m m 45 4 8 m 84 -
Land Capability and Suitability in Vizianagaram District of Andhra Pradesh Using Remote Sensing and GIS Techniques
IOSR Journal Of Humanities And Social Science (IOSR-JHSS) Volume 20, Issue 7, Ver. VII (July 2015), PP 56-64 e-ISSN: 2279-0837, p-ISSN: 2279-0845. www.iosrjournals.org Land Capability and Suitability in Vizianagaram district of Andhra Pradesh using Remote sensing and GIS Techniques Dr.N.Appala Raju Dept.of.Geography, Andhra University, Visakhapatnam-530003, Andhra Pradesh, India Abstract: India’s future is threatened by shortage of food, water and energy and these should be given priority. Agricultural productivity has to be enhanced to meet the increasing demand of ever growing population of the country. The study area covering an about 6533 sq km has been studied for the land systems, landforms, soils, land use and hydro-geomorphology using IRS-P6, LISS III data on scale 1: 50,000. The major soils of the study area are red loamy soils, red sandy soils, deltaic alluvial soils, laterite soils and coastal soils. The major part of the land is utilized for cultivation of paddy (Kharif). The hills of the region contain degraded forest. The land capability has been evaluated based on the physical characteristics of the study area seven classes of land are identified. Land capability classification is a scientific appraisal of the physical characteristics of land, its inherent soil qualities and the farm management practices. The land capability maps are more useful for the delineation of potential arable lands. The information on land suitability gives an idea about the soils, which are suitable(S) and not suitable (N) for a given crop. Within the class suitable, soils are further grouped into highly suitable, moderately suitable and marginally suitable. -
Draft Electoral Roll of Srikakulam-Vizianagaram-Visakhapatnam Teachers Constituency of the A.P Legislative Council As Published on 15-12-2012
Draft Electoral Roll of Srikakulam-Vizianagaram-Visakhapatnam Teachers Constituency of the A.P Legislative Council as published on 15-12-2012 Polling Station Number : ( 39 ) Komarada District: Vizianagaram - 02 Zilla Parishad High School, Sl.No. House address Full Name of the Name of father/ mother / Name of educational Age (Place of ordinary elector husband institution, if any, in residence) which he is teaching (1) (2) (3) (4) (5) (6) Mandal : KOMARADA Village: ARTHAM 0 Galavilli Ganga Visweswra Rao Late Surayya ZPHS GARUGUBILLI 47 1 ARTHAM VILLAGE 0 Kolluru Prasada Rao Ramamurthy ZPHSCHOOL KOTIPAM 49 2 ARTHAM VILLAGE Mandal : KOMARADA Village: CHEKKAVALASA 1-14 Simidi Trinadha Rao Gumpaswami ZPHSCHOOL 40 3 EDULAVALASA TALLABURIDI Mandal : KOMARADA Village: GUNANUPURAM 00 Miriyala Sowjanya Suryanarayana SVD COLLAGE, 25 4 GUNANUPURAM PARVATHIPURAM Mandal : KOMARADA Village: KOMARADA 00 Jannipalaka Prabhavathi Gumpayya GOVERNMENT GIRL 28 5 KUMMARIGUNTA VILLAGE HIGHT SCHOOL 0 Parasurampuram Venkata Ranga Suryanarayana ZPHSCHOOL KOTIPAM 55 6 GANGAREGUVALASA VILLAGE Rao 00 Pata Venkataramana Suryanarayana GJC 30 7 KUMMARIGUNTA VILLAGE GAJAPATHINAGARAM 14-19 Pola Venkataniadu Late Raminiadu APTWR SCHOOL 40 8 APTWR SCHOOL A1 Kongarapu Govinda Appalaswamy ZPHS PBPALLI 33 9 APSWRSCHOOL A1 Sripathi Ramarao Divya Prakash Rao APTWRSCHOOL 54 10 APTWRSCHOOL A1 Mercy Madhuri Latha Sappa Kongarapu Govinda A.P.SWRS/JUNIOR 34 11 APSWR SCHOOL COLLAGE KOMARADA A2 Pyla Padmavathi Maripi Chinnarao APSWRS/JUNIOUR 40 12 APSWR SCHOOL COLLAGE A3 V Swarnalatha Rani P Devakumar APSWRS/JUNIOUR 38 13 SPSWR SCHOOL COLLAGE KOMARADA A11 Avu Trimurthy Niadu Krishnamurthy APTWRSCHOOL 37 14 APTWRSCHOOL A11 Botcha Applaraju Simhachlam APTWRSCHOOL 40 15 APTWRSCHOOL 1of 223 Draft Electoral Roll of Srikakulam-Vizianagaram-Visakhapatnam Teachers Constituency of the A.P Legislative Council as published on 15-12-2012 Polling Station Number : ( 39 ) Komarada District: Vizianagaram - 02 Zilla Parishad High School, Sl.No. -
Press Release
Government of India Earth System Science Organisation Ministry of Earth Sciences India Meteorological Department Earth System Science Organisation PRESS RELEASE Time of issue: 1600 hours IST Dated:18-12-2018 Sub: Cyclonic Storm ‘PHETHAI” weakened into Low Pressure Area Yesterday’s cyclonic storm, “PHETHAI” over coastal Andhra Pradesh moved north- northeastwards and weakened into deep depression over westcentral Bay of Bengal (BoB) in the same evening (1730 hrs IST). Moving further north-northeastwards, it crossed Andhra Pradesh coast close to Tuni during same evening (1930 to 2030 hrs IST). It weakened into a depression over coastal Andhra Pradesh in the same midnight (2330 hrs IST). Moving north-northeastwards, it weakened into a well marked low pressure area over northwest & adjoining westcentral BoB and Odisha in the early morning (0530 hrs IST) and into a low pressure area over northwest BoB and adjoining Odisha in the morning (0830 hrs IST) of today, the 18th December, 2018. Warnings: (i) Heavy rainfall warning: No adverse weather is likely over coastal Andhra Pradesh, Chattisgarh, Odisha, Jharkhand and West Bengal. However, light to moderate rainfall is likely at a few places over Gangetic West Bengal during next 12 hours. Rainfall at many places with isolated heavy rainfall likely over northeastern states during next 24 hours. (ii) Wind warning for Odisha coast Strong wind speed reaching 30-40 kmph gusting to 50 kmph likely over northwest Bay of Bengal and along & off north Odisha and West Bengal coasts during next 12 hours. (iii) Sea condition The sea condition is likely to be rough to very rough over northwest Bay of Bengal along & off north Odisha and West Bengal coasts during next 12 hours. -
Andhra Pradesh
State District Block Name Gender Mobile ANDHRA PRADESH VIZIANAGARAM Badangi PERLA GANESH M 9347516083 ANDHRA PRADESH VIZIANAGARAM Badangi SINGAMSETTI VENKATESH M 6303297681 ANDHRA PRADESH VIZIANAGARAM Badangi GUNTREDDI UPENDRA M 6304057230 ANDHRA PRADESH VIZIANAGARAM Badangi PERIA RAJA SEKHAR M 8367514479 ANDHRA PRADESH VIZIANAGARAM Badangi REDDY NAVEEN M 9014051713 ANDHRA PRADESH VIZIANAGARAM Badangi MUPPID DILEEPKUMAR M 9398157955 ANDHRA PRADESH VIZIANAGARAM Badangi LATCHUPATULA NUKAMNAIDU M 9381821963 ANDHRA PRADESH VIZIANAGARAM Badangi LATCHUPATULA GANESHKUMAR M 7799535201 ANDHRA PRADESH VIZIANAGARAM Badangi TELLA DINESH M 6309657211 ANDHRA PRADESH VIZIANAGARAM Badangi BOGI VINOD M 6304414236 ANDHRA PRADESH VIZIANAGARAM Badangi CHAPPA NARAYANARAO M 7997121870 ANDHRA PRADESH VIZIANAGARAM Badangi MATLA SATYA M 7036218912 ANDHRA PRADESH VIZIANAGARAM Badangi LATCHUPATULA SRINU M 6300425628 ANDHRA PRADESH VIZIANAGARAM Badangi NEMANI DURGARAO M 8247070682 ANDHRA PRADESH VIZIANAGARAM Badangi GENLI NIRMALA F 8367501963 ANDHRA PRADESH VIZIANAGARAM Badangi P ASHOK M 9550712571 ANDHRA PRADESH VIZIANAGARAM Badangi KANDUKURI VINAYKUMAR M 8374606146 ANDHRA PRADESH VIZIANAGARAM Badangi TELLA YELLAMNAIDU M 8096480598 ANDHRA PRADESH VIZIANAGARAM Badangi MATSA SIMHAHALAM M 8297104314 ANDHRA PRADESH VIZIANAGARAM Badangi TENTU SRINUVAS M 9010894828 ANDHRA PRADESH VIZIANAGARAM Badangi GULLIPALLI NAGARAJU M 7095167966 ANDHRA PRADESH VIZIANAGARAM Badangi YAMALI HEMANTHRAO M 9014545772 ANDHRA PRADESH VIZIANAGARAM Badangi KANDI CHINARAJU M 9347854532 ANDHRA