Robustness & Reliability Analysis
Total Page:16
File Type:pdf, Size:1020Kb
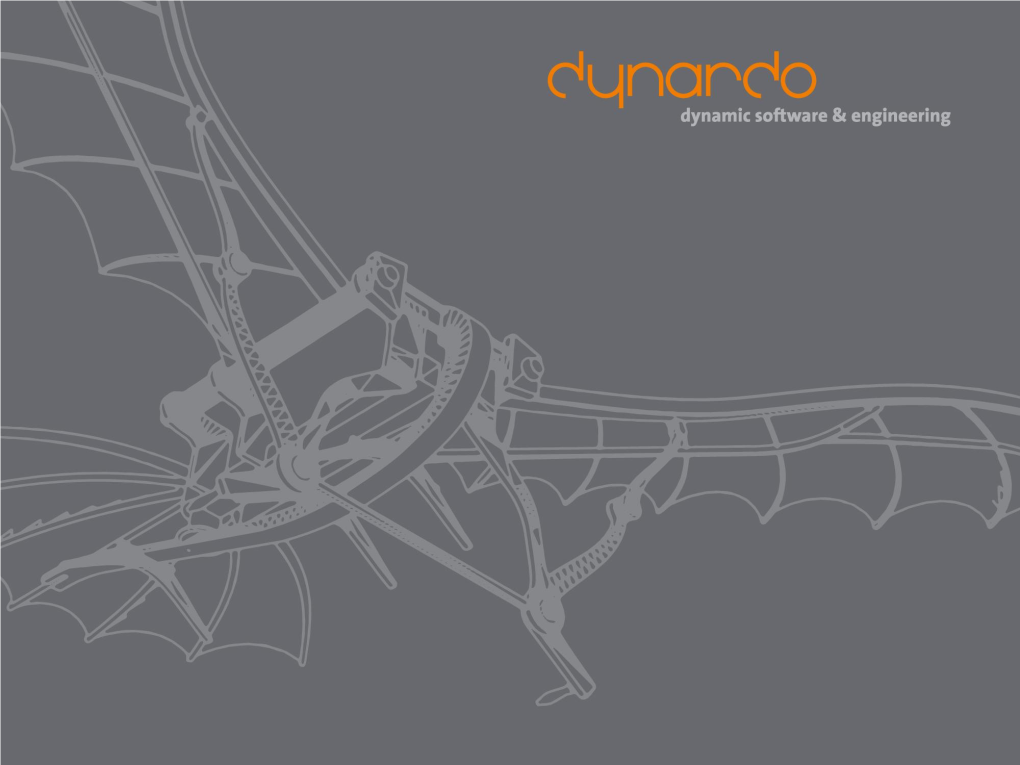
Load more
Recommended publications
-
Robustness & Reliability Analysis
DYNARDO • Robust Design Optimization Workshop • © Dynardo GmbH 2011 Robustness & Reliability Analysis 1 DYNARDO • Robust Design Optimization Workshop • © Dynardo GmbH 2011 Start Robust Design Optimization Robust Design Optimization Variance based Robustness Evaluation Sensitivity Study Probability based Single & Multi objective Robustness Evaluation, (Pareto) optimization (Reliability analysis) CAE process (FEM, CFD, MBD, Excel, Matlab, etc.) Robust Design Optimization Methodology 2 DYNARDO • Robust Design Optimization Workshop • © Dynardo GmbH 2011 What is necessary for successful implementation? 1. Introduction of realistic scatter definitions Distribution function Correlations Random fields 2. Using of reliable stochastic methodology Variance-based robustness evaluation using optimized LHS 3. Development of reliable robustness measurements Standardized post processing Significance filter Reliable variation and correlation measurements Acceptance of method/result documentation/communication! 3 DYNARDO • Robust Design Optimization Workshop • © Dynardo GmbH 2011 Definition of Uncertainties 4 DYNARDO • Robust Design Optimization Workshop • © Dynardo GmbH 2011 Uncertainties and Tolerances • Design variables Property SD/Mean % • Material, geometry, loads, constrains,… Metallic materiales, yield 15 • Manufacturing Carbon fiber rupture 17 • Operating processes (misuse) Metallic shells, buckling 14 strength • Resulting from Deterioration Bond insert, axial load 12 • … Honeycomb, tension 16 Honeycomb, shear, compression 10 Honeycomb, face -
Optislang Connects
Title Story // Process Integration Process Integration ABAQUS | ADAMS | COMSOL | EXCEL | FLOEFD | GT POWER | MATLAB | LS DYNA MOTOR CAD | NASTRAN | PYTHON | ROCKY | SIEMENS NX | ZEMAX ... Product Data Product Statistical Connect PLM/SDM Connect PLM/SDM Analysis TITLE STORY // PROCESS INTEGRATION Parametric Variation Analysis Calibration Sensitivity Analysis Optimization OPTISLANG CONNECTS Robustness Evaluation Metamodeling Data-based ROMs optiSLang enables the building of transparent CAE tool chains and combines them with parametric algorithms for a broader usage of CAE techniques. Fig. 1: Simulation Workfl ow Management with optiSLang One of the major challenges of today’s CAE engineers is the gineers. Also, customers are aware of how many mistakes includes interfaces to all major software tools used in the maintain complex tool chains. The modular process inte- increasing complexity of processes while results have to might occur during this process. When different variants virtual product development. For example, there are inte- gration approach of building programmable nodes provides be delivered in shorter times. At the same time, within the have to be compared for fi nding an optimal design, it can grations of CAD parametric modeling with CATIA, Siemens a very economical way to standardize and automatize CAE engineering process, multiple disciplines like NVH, thermal- lead to an unsorted crowd of data. If simulations are done NX and ProE. CAE parametric modeling is supported by link- workfl ows. There are many examples of successful projects mechanical-electrical analyses, safety evaluation, tolerance by different engineers, it can be very hard to compare the ing ANSYS, ABAQUS, ADAMS, COMSOL, FLOEFD, GT POWER, with Dynardo’s customers like Bosch, Daimler, et al. -
Dynardo Gmbh
dynamic software & engineering Software & Consulting Sensitivity Analysis Multidisciplinary Optimization Multiobjective Optimization Robustness Evaluation Reliability Analysis Parameter Identifi cation Model Calibration Dynardo GmbH optiSLang SoS ETK LEONARDO DA VINCI dynamic software & engineering Without reason, no eff ect is produced in nature; understand the reason and you will not need experience. from Leonardo da Vinci’s „Codice Atlantico“ DYNARDO GMBH The Dynardo GmbH develops software for CAE-based sensitivity analyses, robustness evaluations and Robust Design Optimizations. Additionally Dynardo offers, in cooperation with worldwide distributors, an extensive support and training program. The range of services also includes consulting and simula- Tasks, tion services in virtual product development. Ideas, Solutions History & Expertise The Dynardo GmbH was founded in 2001 as a company for Dynardo’s engineering expertise and software products software development and engineering computing services enable fast and effi cient solutions of your tasks. Through with three partners and two employees in Weimar. With close cooperation with renowned research institutions and unique features such as complex non-linear fi nite element international partners, Dynardo has an extensive network computations in geomechanics and civil engineering as well of experts to respond fl exibly to worldwide customer re- as RDO in virtual product development, Dynardo has suc- quirements. cessfully established itself in the CAE-market. The fi rst op- tiSLang version was released in 2002 and has since evolved into a leading CAE software platform. Today, Dynardo runs 3 branches in Weimar, Vienna and San Francisco to help you meet the challenges of virtual product development. Philosophy Leonardo da Vinci was not only a great artist, but also a tion enables an appropriate analysis of system properties for visionary engineer and scientist. -
•Full Support Limited Capability Requires More Than 1 Product
• Full Support ▲ Limited Capability ▪ Requires more than 1 product / CONTENTS STRUCTURES FLUIDS Vibrations .................................................................................................................... 3 General Solver Capabilities ........................................................................22 Webservice ..............................................................................................................33 High Frequency Electromagnetics ....................................................44 Wave Hydrodynamics ...................................................................................... 3 Single Phase, Non-Reacting Flows ......................................................22 General .......................................................................................................................34 Power and Signal Integrity Board Additional Physics ................................................................................................ 3 Heat Transfer ..........................................................................................................23 Designing Optimization and Parameter Simulation Capabilities ................................................................................. 47 Composite Materials ......................................................................................... 5 Particle Flows (Multiphase) ........................................................................23 Identificaton (Calibration) ..........................................................................34 -
Sensitivity Analysis, • Consumer Goods Industry Optimization, Robustness Evaluation • Power Generation and Robust Design Optimization
DYNARDO • © Dynardo GmbH 2012 Founded: 2001 (Will, Bucher, CADFEM International) More than 40 employees, offices at Weimar and Vienna Leading technology companies Daimler, Bosch, Eon, Nokia, Siemens, BMW, are supported by us Software Development CAE-Consulting Our expertise: •Mechanical engineering • Civil engineering & Geomechanics • Automotive industry Dynardo is your engineering specialist for CAE-based sensitivity analysis, • Consumer goods industry optimization, robustness evaluation • Power generation and robust design optimization. 2 DYNARDO • © Dynardo GmbH 2012 Premium Consultancy and Software Company for CAE-based Robustness Evaluation, Reliability Analysis and Robust Design Optimization using Stochastic Analysis Dynardo is the consulting company which successfully introduced stochastic analysis into complex CAE-based virtual product development processes. Recently, it is applied in the power generation industry, automotive industry and high-level consumer goods industry DYNARDO Field of Excellence 3 DYNARDO • © Dynardo GmbH 2012 Introduction of optiSLang 4 DYNARDO • © Dynardo GmbH 2012 Challenges in Virtual Prototyping • Virtual prototyping is necessary for cost efficiency • Test cycles are reduced and placed late in the product development • CAE-based optimization and CAE-based robustness evaluation becomes more and more important in virtual prototyping – Optimization is introduced into virtual prototyping – Robustness evaluation is the key methodology for safe, reliable and robust products – The combination of optimizations and robustness evaluation will lead to robust design optimization strategies 5 DYNARDO • © Dynardo GmbH 2012 optiSLang is an algorithmic toolbox for sensitivity analysis, optimization, robustness evaluation, reliability analysis and robust design optimization. optiSLang is the commercial tool that has completed the necessary functionality of stochastic analysis to run real world industrial applications in CAE-based robust design optimizations. -
Daniel Krätschmer Friederike Loerke
VIRTUAL ECU ANSYS BEST PRACTICE SESSION: „SIMULATION DRIVEN PRODUCT DEVELOPMENT FOR EVERYONE“ DANIEL KRÄTSCHMER FRIEDERIKE LOERKE CASCON 2019 Simulation Process Management: Virtual ECU Motivation System: How to establish a robust data / information Vehicle exchange between product-independent design Load derivation from a system perspective 0 Level element assessments & product-specific load Sub-System: RB system derivation and load path design? (e.g. injection Level 1 Level system) Manufactured Motivation Item: Only with standardized load path methods Level 2 Level ECU transparent requirements for design elements can be derived ? Assembly Level 3 Level Standardized load path methods as enabler for Cut out design element load / load tool based, automatized evaluation of design for product integration capacity level Component elements in mechanical architectures Reliability Assessments 4 Level geometry-independent stress / strength Material, design rule, e.g. 휎 ≤ 휎푚푎푥 level Level 5 Level Interface 4 Automotive Electronics | AE/EBS | 2019-08-07 © Robert Bosch GmbH 2017.2019. All rights reserved, also regarding any disposal, exploitation, reproduction, editing, distribution, as well as in the event of applications for industrial property rights. Simulation Process Management: Virtual ECU Motivation System: Democratization in CAE-based product Vehicle Load derivation from a system perspective 0 Level development means to empower non- Sub-System: experts to take advantage from simulation RB system technology (e.g. injection Level 1 Level system) CAE experts could put the power of Automated setup of ECU models to feed Manufactured Item: simulation safely into non-experts hands to reliability models with needed information Level 2 Level ECU overcome the general lack of CAE engineers Assembly Level 3 Level Cut out design element load / load for product integration capacity level Democratization ? Component Hosting of detailed reliability models 4 Level geometry-independent stress / strength Material, design rule, e.g. -
OPTISLANG - READY for DIGITAL TWIN to BRIDGE Fig
Title Story // Process Integration & Automation DOE Virtual Product manuell HiL Calibration Simulation = Hardware Connect PLM Digital Twin Connect PLM autom. complex CAx workflow Laboratory Development parametric studies, RDO, … CAx rd party Product CAE-Data 3 Production Statistical Database ROM TITLE STORY // PROCESS INTEGRATION & AUTOMATION Analysis OPTISLANG - READY FOR DIGITAL TWIN TO BRIDGE Fig. 1: Integration of optiSLang within and beyond CAx Processes, Product Lifecycle Management and Hardware-in-Loop INTO PRODUCTION 4.0 & INTERNET OF THINGS optiSLang is capable to bridge the gap between modern Product Lifecycle Management (PLM) systems and individual product development hubs. Motivation The new generation of process automation within Industry should be noted, however, that simulation technology is 4.0 has transformed the scope of Business Process Models not an IoT product itself but is proving to be a pivotal driver (BPM) for leading global manufacturers. With tools such as of IoT processes in the future. Virtual Manufacturing Execution Systems, Cloud Computing and Big Data Analytics, the Internet of Things (IoT) is becom- In the various phases of Product Development Processes ing a modern and efficient umbrella of planning, processing, (PDPs), optiSLang is capable to play a vital role to shorten pro- feedback and control systems, paving the way for the next duction cycles, deliver enhancements and resolve conflicts generation of smart designs and manufacturing systems. with respect to quality, product robustness and costs. Apart from optimizing individual process workflows within various Within the scope of Industry 4.0, there has been a wide- stages of PDPs, optiSLang could be used to bridge the gap be- CAx 3rd party spread development of standalone tools, each offering tween modern Product Lifecycle Management (PLM) systems special solutions to underlying problems and requiring and individual product development hubs. -
Sensitivity Analysis, • Consumer Goods Industry Optimization, Robustness Evaluation • Power Generation and Robust Design Optimization
DYNARDO • Robust Design Optimization Workshop • © Dynardo GmbH 2011 Founded: 2001 (Will, Bucher, CADFEM International) More than 35 employees, offices at Weimar and Vienna Leading technology companies Daimler, Bosch, Eon, Nokia, Siemens, BMW, are supported by us Software Development CAE-Consulting Our expertise: • Mechanical engineering • Civil engineering & Geomechanics • Automotive industry Dynardo is your engineering specialist for CAE-based sensitivity analysis, • Consumer goods industry optimization, robustness evaluation • Power generation and robust design optimization. 2 DYNARDO • Robust Design Optimization Workshop • © Dynardo GmbH 2011 Challenges in Virtual Prototyping • Virtual prototyping is necessary for cost efficiency • Test cycles are reduced and placed late in the product development • CAE-based optimization and CAE-based robustness evaluation becomes more and more important in virtual prototyping – Optimization is introduced into virtual prototyping – Robustness evaluation is the key methodology for safe, reliable and robust products – The combination of optimizations and robustness evaluation will lead to robust design optimization strategies 3 DYNARDO • Robust Design Optimization Workshop • © Dynardo GmbH 2011 Challenge of RDO – reliable input Successful RDO needs a balance between – Reliable input = know how and definition of input uncertainties – Reliable analysis = reliable stochastic analysis methodology – Reliable post processing = use of stochastic/statistic results in the design process Let’s derive the functionality -
ANSYS Optislang Brochure
dynamic software & engineering CAE-Software Sensitivity analysis Multiobjective optimization Multidisciplinary optimization Robustness evaluation Reliability analysis Robust Design Optimization (RDO) optiSLang optiSLang multiPlas ETK SoS ANSYS optiSLang ANSYS optiSLang Combining powerful parametric model capabilities with Robust Design Optimization ANSYS Workbench provides leading technology for parametric and persistent CAD and CAE modelling for simulation driven product development. optiSLang focuses on effi ciency and automation of RDO methods for complex non-linear analysis models with many parameters, including stochastic variables. ANSYS Workbench project screen with the three optiSLang drag and drop modules sensitivity analysis, optimization and robustness evaluation to defi ne an RDO analysis. This includes robust handling of design failures and solver noise. ANSYS optiSLang offers several modes of interoperability • using parametric ANSYS Workbench models with the In addition ANSYS optiSLang provides eral cores with ANSYS Remote Solve Manager and the use • using the optiSLang Workbench plugin to expose optiSLang GUI with the help of the optiSLang ANSYS • Flexible text-based interfacing tools that can connect of ANSYS HPC Pack Parametric Licenses for simultaneous optiSLang technology within the ANSYS Workbench GUI Workbench integration node ANSYS products, or any scriptable products, that may be computing of different designs are fully integrated. With • using text-based interfacing between ANSYS and optiS- part of your engineering -
Introduction to Parametric Optimization and Robustness Evaluation with Optislang
Introduction to Parametric Optimization and Robustness Evaluation with optiSLang Dynardo GmbH 1 © Dynardo GmbH 1. Introduction 2. Process to optiSLang integration 6. Training 3. Sensitivity analysis 5. Robustness 4. Parametric analysis Optimization Introduction to the parametric optimization and robustness evaluation with 2 optiSLang © Dynardo GmbH 1. Introduction 2. Process to optiSLang integration 6. Training 3. Sensitivity analysis 5. Robustness 4. Parametric analysis Optimization Introduction to the parametric optimization and robustness evaluation with 3 optiSLang © Dynardo GmbH Dynardo • Founded: 2001 (Will, Bucher, CADFEM International) • More than 50 employees, offices at Weimar and Vienna • Leading technology companies Daimler, Bosch, E.ON, Nokia, Siemens, BMW are supported Software Development CAE-Consulting • Mechanical engineering • Civil engineering & Dynardo is engineering specialist for Geomechanics CAE-based sensitivity analysis, • Automotive industry optimization, robustness evaluation • Consumer goods industry and robust design optimization • Power generation Introduction to the parametric optimization and robustness evaluation with 4 optiSLang © Dynardo GmbH Robust Design Optimization (RDO) in virtual product development optiSLang enables you to: • Identify optimization potentials • Improve product performance • Secure resource efficiency • Adjust safety margins without limitation of input parameters • Quantify risks • Save time to market Introduction to the parametric optimization and robustness evaluation with 5 optiSLang -
Product Brochure Optislang
dynamic software & engineering CAE-Software Model Calibration Sensitivity Analysis Optimization Robustness Evaluation Robust Design Optimization Metamodeling optiSLang Product Overview PRODUCT OVERVIEW Since its market launch in 2002, optiSLang has developed into one of the leading universal software platforms for CAE-based optimization in virtual prototyping. Based on design variations or measurement and observation points, effi cient variation analyses can be performed with minimal user input and few Typical workfl ow using sensitivity analysis, optimization, meta-models and validation of the best design solver calls. optiSLang supports the engineer with: Metamodeling with optiSLang • Calibration of virtual models to physical tests signs to the boundaries of tolerable stresses, deformations optiSLang’s expands parametric design studies to impact of input variability to the responses. For the identifi ca- • Analysis of parameter sensitivity and importance or other critical responses. As a result, the product behavior metamodeling based on a set of virtual design points, experi- tion process, optiSLang’s Coeffi cient of Prognosis (CoP) quanti- • Metamodeling may become sensitive to scatter with regard to material, mental design responses or fi eld observations. The software fi es the prognosis accuracy of the meta-model regarding the • Optimization of product performance geometric or environmental conditions. Subsequently, a automatically identifi es the corresponding input parameters response variation of a data set. The result is the Metamodel -
Dynardo Gmbh
Design of a control system model in SimulationX using calibration and optimization Dynardo GmbH 1 © Dynardo GmbH Notes • Please let your microphone muted • Use the chat window to ask questions • During short breaks we will answer your questions Supported versions • From version 4.1 optiSLang supports SimulationX since version 3.5 Design of a control system model in SimulationX 2 using calibration and optimization © Dynardo GmbH 1. Introduction 2. Process integration 3. Sensitivity 4. Optimization analysis 5. Trainings & Contact Design of a control system model in SimulationX 3 using calibration and optimization © Dynardo GmbH 1. Introduction 2. Process integration 3. Sensitivity 4. Optimization analysis 5. Trainings & Contact Design of a control system model in SimulationX 4 using calibration and optimization © Dynardo GmbH Dynardo • Founded: 2001 (Will, Bucher, CADFEM International) • More than 60 employees, offices at Weimar and Vienna • Leading technology companies Daimler, Bosch, E.ON, Nokia, Siemens, BMW are supported Software Development CAE-Consulting • Mechanical engineering • Civil engineering & Dynardo is engineering specialist for Geomechanics CAE-based sensitivity analysis, • Automotive industry optimization, robustness evaluation • Consumer goods industry and robust design optimization • Power generation Design of a control system model in SimulationX 5 using calibration and optimization © Dynardo GmbH Application of Multi-disciplinary Optimization • Virtual prototyping is an interdisciplinary process • Multidisciplinary approach requires to run different solvers in parallel and to handle different types of constraints and objectives • Arbitrary engineering software with complex non-linear analysis have to be connected • The resulting optimization problem may become very noisy, very sensitive to design changes or ill conditioned for mathematical function analysis (e.g.