Fault Diagnostics in Air Intake System of Combustion Engine Using Virtual Sensors
Total Page:16
File Type:pdf, Size:1020Kb
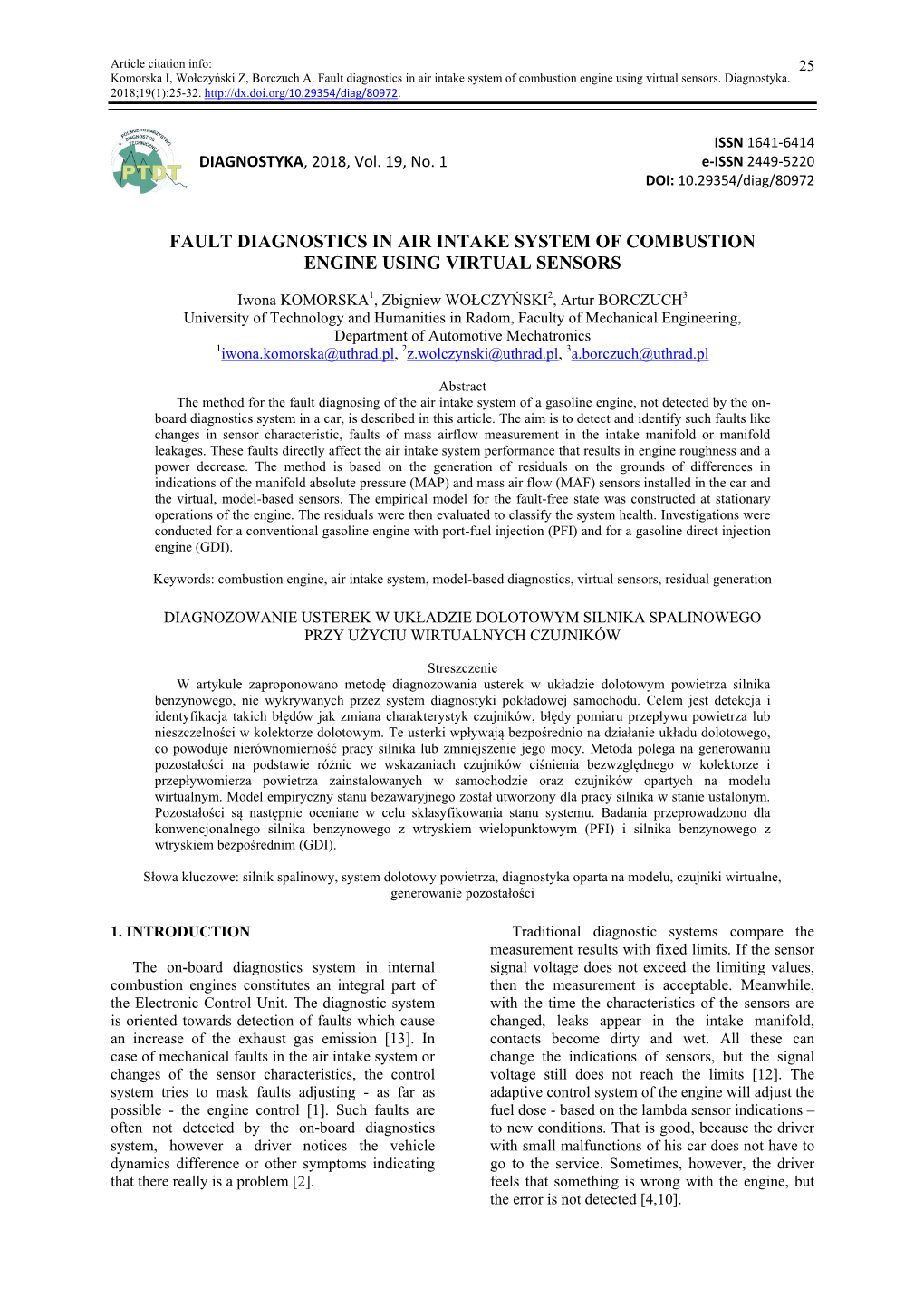
Load more
Recommended publications
-
Engine Control Unit
Engine Control Unit João Filipe Ferreira Vicente Dissertation submitted for obtaining the degree in Master of Electronic Engineering, Instituto Superior Técnico Abstract The car used (Figure 1) has a fibreglass body and uses a Honda F4i engine taken from the Honda This paper describes the design of a fully CBR 600. programmable, low cost ECU based on a standard electronic circuit based on a dsPIC30f6012A for the Honda CBR600 F4i engine used in the Formula Student IST car. The ECU must make use of all the temperature, pressure, position and speed sensors as well as the original injectors and ignition coils that are already available on the F4i engine. The ECU must provide the user access to all the maps and allow their full customization simply by connecting it to a PC. This will provide the user with Figure 1 - FST03. the capability to adjust the engine’s performance to its needs quickly and easily. II. Electronic Fuel Injection Keywords The growing concern of fuel economy and lower emissions means that Electronic Fuel Injection Electronic Fuel Injection, Engine Control Unit, (EFI) systems can be seen on most of the cars Formula Student being sold today. I. Introduction EFI systems provide comfort and reliability to the driver by ensuring a perfect engine start under This project is part of the Formula Student project most conditions while lessening the impact on the being developed at Instituto Superior Técnico that environment by lowering exhaust gas emissions for the European series of the Formula Student and providing a perfect combustion of the air-fuel competition. -
Pressure Sensors
PRESSURE SENSORS Pressure Sensors Pressure sensors are used to measure intake manifold pressure, atmospheric pressure, vapor pressure in the fuel tank, etc. Though the location is different, and the pressures being measured vary, the operating principles are similar. Page 1 © Toyota Motor Sales, U.S.A., Inc. All Rights Reserved. PRESSURE SENSORS Manifold Absolute Pressure (MAP) Sensor In the Manifold Absolute Pressure (MAP) sensor there is a silicon chip mounted inside a reference chamber. On one side of the chip is a reference pressure. This reference pressure is either a perfect vacuum or a calibrated pressure, depending on the application. On the other side is the pressure to be measured. The silicon chip changes its resistance with the changes in pressure. When the silicon chip flexes with the change in pressure, the electrical resistance of the chip changes. This change in resistance alters the voltage signal. The ECM interprets the voltage signal as pressure and any change in the voltage signal means there was a change in pressure. Intake manifold pressure is a directly related to engine load. The ECM needs to know intake manifold pressure to calculate how much fuel to inject, when to ignite the cylinder, and other functions. The MAP sensor is located either directly on the intake manifold or it is mounted high in the engine compartment and connected to the intake manifold with vacuum hose. It is critical the vacuum hose not have any kinks for proper operation. Page 2 © Toyota Motor Sales, U.S.A., Inc. All Rights Reserved. PRESSURE SENSORS The MAP sensor uses a perfect vacuum as a reference pressure. -
POLESTAR Systems
POLE STAR Systems Engine Management Systems Overview: The POLE STAR HS engine management Although originally developed for the Mini A- system is a low cost yet highly sophisticated Series engine the systems can now be used on system, ranging from the basic 2D ignition-only virtually any engine including high revving system up to the full 3D Turbo Fuel Injection motorbike engines. The systems features System. include, • Supports up to 8 cylinders and 4 injector drivers • Fully sequential 4 cylinder operation supported with cam sensor • Special sequential twin-point fuel injection mode specifically designed for the A-Series engine (requires cam sensor) • Single point mode (multi-injector) • Low cost ignition only distributor-less versions also available • Direct crankshaft trigger for greater accuracy. Supports standard 36-1 trigger wheel or existing POLE STAR sensor and disk • Accurate control of ignition timing and fuelling. Timing/Fuelling adjusted with 8 load sites at every 500 rpm from 0-15000rpm with full interpolation. • Optional closed-loop fuelling with wideband lambda input • Integral ‘smooth-cut’ rev limiter • Optional ‘Boost Retard’ feature with integral MAP sensor for Turbo engines POLE STAR Systems, 31 Taskers Drive, Anna Valley, Andover, Hants, SP11 7SA web: www.polestarsystem.com Tel: 01264-333034 POLE STAR Systems depending on the system type. These are typically Details: a throttle position sensor, MAP sensor, water temperature sensor and inlet air temperature Originally developed and tested in conjunction sensor, usually the ECU canbe calibrated to use an with Bryan/Neil Slark of Slark Race Engineering engines existing temperature sensors. and Jon Lee of LynxAE using their dyno facilities. -
Marine Engine Electronics C7 –
C7 - C32 Marine Engine Electronics Application and Installation Guide APPLICATION AND INSTALLATION GUIDE MARINE ENGINE ELECTRONICS C7 – C32 Caterpillar: Confidential Yellow 1 C7 - C32 Marine Engine Electronics Application and Installation Guide 1 Introduction and Purpose…………………………………….…………………5 1.1 Safety……………………………………………………………………………5 1.2 Replacement Parts…………………………………………………………….6 2 Engine System Overview……………………………………………………….7 2.1 Electronic Engine Control……………………………………………………..7 2.2 Factory Configuration Parameters……………………………………………8 2.3 Engine Component Overview…………………………………………………9 2.4 Engine Component Locations……………………………………………….12 3 Customer System Overview…………………………………………………..13 3.1 Customer Configuration Parameters……………………………………….13 3.2 Customer Component Overview…………………………………………….14 4 Power and Grounding Considerations……………………………………….15 4.1 Power Requirements…………………………………………………………15 4.2 Engine Grounding…………………………………………………………….18 4.3 Suppression of Voltage Transients…………………………………………20 4.4 Battery Disconnect Switch…………………………………………………...21 4.5 Welding on a Machine with an Electronic Engine…………………………22 5 Connectors and Wiring Harness Requirements………………………….…23 5.1 Wiring Harness Components………………………………………………..23 5.2 Wiring Harness Design………………………………………………………29 5.3 Service Tool Connector (J66) Wiring……………………………………….32 5.4 SAE J1939/ 11 - Data Bus Wiring…………………………………………..34 6 Customer Equipment I.D. and Passwords…………………………………..37 6.1 Equipment Identification……….……………………………………………..37 6.2 Customer Passwords.………………………………………………………..37 7 Factory -
Developments in Precision Power Train Sensors
109 Hitachi Review Vol. 63 (2014), No. 2 Developments in Precision Power Train Sensors Keiji Hanzawa OVERVIEW: The fuel economy and emissions performance demands on Shinobu Tashiro vehicle power trains are becoming more stringent for reasons relating Hiroaki Hoshika to global environmental protection and the rising price of oil. There has also been a change in thinking on the measurement of emissions and Masahiro Matsumoto fuel economy toward allowing for conditions where the temperature and humidity are closer to real driving conditions. Other changes include the electrifi cation of power trains, such as in hybrid vehicles, and improvements in the running effi ciency of internal combustion engines that result in more frequent use of engine operating modes in which sensor operation is more diffi cult, such as the Atkinson cycle. Hitachi Automotive Systems, Ltd. is supporting ongoing progress in power train control by making further improvements in sensor accuracy. INTRODUCTION Automotive power trains have made rapid progress HITACHI supplies customers around the world with on electrifi cation and reducing fuel consumption in a variety of systems for the driving, cornering, and recent years. This article describes advances in the braking of vehicles. By using a range of different performance of the sensors used in these power trains, sensors to determine conditions in the power train, looking at micro electromechanical system (MEMS) vehicle body movements, and what is happening air fl ow sensors that reduce the error in intake pulsation, around the vehicle, these systems ensure a driving the integration of air intake relative humidity sensors experience that is safe and comfortable, and that is and pressure sensors, and the adoption of digital signal conscious of the global environment (see Fig. -
Cranfield University T Fong Maf to Map Based Engine
CRANFIELD UNIVERSITY T FONG MAF TO MAP BASED ENGINE LOAD ANALOGY CONVERSION SCHOOL OF APPLIED SCIENCES MSc THESIS CRANFIELD UNIVERSITY SCHOOL OF APPLIED SCIENCES MSc THESIS Academic Year 2007-2008 T FONG MAF to MAP based engine load analogy conversion Supervisor: J Nixon September 2008 This thesis is submitted in partial 40% weighting fulfilment of the requirements for the Degree of Motorsport Engineering and Management © Cranfield University 2008. All rights reserved. No part of this publication may be reproduced without the written permission of the copyright owner. ii Abstract In motorsport, high engine power output and engine responsiveness are often desired in order to gain competition advantage. The engine tuner will normally upgrade the standard vehicle with aftermarket components such as a higher rating turbo, a longer duration camshafts, and an exhaust system. As a result of the modifications, some of the standard sensors/actuators are not able to work efficiently. For example, air reversal flow and venting of excess air pressure caused by the aftermarket tuning devices can affect the reading accuracy of the mass air flow (MAF) sensor. This thesis is to develop an Engine Control Unit (ECU) system, which will replace the MAF sensor with a manifold absolute pressure (MAP) sensor to calculate the air flow into the engine. Enduring Solution Limited (ESL) seeks to develop the MAP based system into their existing programmable ECU, thus improve their market position. The challenge of the newly developed system is to be economically viable by minimising hardware and software alterations. The approach is to modify and correlate the load analogy in the system embedded code, while retaining the other comprehensive code designed by the original manufacturer. -
Holley GM LS7 Street Single-Plane Intake Manifold Kits
Holley GM LS7 Street Single-Plane Intake Manifold Kits 300-269 / 300-269BK LS7 Street Single-Plane Intake Manifold, Port-EFI W/Fuel Rails 300-270 / 300-270BK LS7 Street Single-Plane Intake Manifold, Carbureted/TB EFI INSTALLATION INSTRUCTIONS 199R11701 IMPORTANT: Before installation, please read these instructions completely. APPLICATIONS: The Holley LS Street single-plane intake manifolds are designed for GM LS7 engines used in retrofit engine installations into older classic/high performance cars and trucks. This product is intended for carbureted, throttle body EFI, or port EFI applications. The LS Street single-plane intake manifolds are produced for street and performance engine applications, 5.3 to 6.2+ liter displacement, and maximum engine speeds of 6000-7000 rpm, depending on the engine combination. The Street single-plane design provides the lowest carburetor/throttle body flange height possible while providing maximum performance to 7000 rpm. These intake manifolds are sold for (pre-emissions control) applications only and will not accept stock components and hardware. EMISSIONS EQUIPMENT: Holley LS Street single-plane intake manifolds do not accept any emission-control devices. This part is not legal for sale or use for motor vehicles with pollution-controlled equipment. IGNITION CONTROL: For intake manifold P/N’s 300-270 and 300-270BK, retrofit carbureted or throttle body EFI applications, ignition control will need to be accomplished with a separate ignition control module. It is recommended to use an MSD 6LS ignition controller, MSD P/N 6012 for LS7 (58 tooth crank trigger engines). The MSD ignition controller will function with the OE crank trigger, cam timing sensor, and coils. -
Your Vacuum Gauge Is Your Friend
WRENCHIN’ @ RANDOM YOUR VACUUM GAUGE IS YOUR FRIEND Two Essential Diagnostic Tools No Hot Rodder Should Be Without, and How to Use Them Marlan Davis hI’ve been answering read- ers’ Pit Stop tech questions for decades, explaining how to improve performance, troubleshoot pesky problems, or recommend a better combina- tion. Yet rarely do any of these problem- solving requests include information on the problem combo’s vacuum reading. That’s unfor- tunate, as [Above: Two essential diagnostic tools no hot rodder should be with- vacuum out, from left: a Mityvac handheld can tell vacuum pump for testing vacuum you a heck of a lot about an consumers (some models will even engine’s condition, without the aid in brake bleeding), and a large, easy-to-read vacuum gauge like need to invest in a bunch of this one by OTC (this model also high-tech diagnostic tools. includes a pressure gauge for even So what’s the deal on more test possibilities). vacuum? Consider an internal- [Left: Knowing how to use a combustion engine as basically vacuum gauge is the key to a giant air pump that operates diagnosing many performance under the principles of pres- problems. It aids in tuning your sure differential. The difference motor to the tip of the pyramid. It even helps diagnose problems not between normal atmospheric seemingly engine-related, such as pressure (14.7 psi at sea level a weak power-brake system. Add at standard temperature and one to your toolbox today. pressure) and how hard this “pump” sucks under various engine-management system). -
3Gr-Fse Intake Eg 89
ENGINE – 3GR-FSE INTAKE EG 89 3GR-FSE INTAKE General ● A surge tank with a built-in ACIS (Acoustic Control Induction System) and an intake manifold with a built-in SCV (Swirl Control Valve) are used. ● A hot-wire type Mass airflow meter (with a built-in intake air temperature sensor) is provided in the air cleaner cap. ● The ETCS-i system is used and a single-valve, electronically controlled throttle body is installed. Purge VSV Resonator Throttle Body Mass Air Flow Meter SCV Position Sensor Air Cleaner Motor for SCV (Swirl Control Valve) Air Cleaner Inlet Intake Manifold Serge Tank Link Mechanism Rotary Solenoid for ACIS Link Mechanism Resonator Throttle Body Exhaust Manifold Air Cleaner Intake Air Control Valve SCV Serge Tank Mass Air Flow Meter Rotary Solenoid for ACIS Engine Exhaust Manifold Sensor ECM SCV Position Sensor Intake Manifold Motor for SCV (Swirl Control Valve) A4270050P ENGINE – EG 90 3GR-FSE INTAKE Air Cleaner ● A removable cap type air cleaner case is used for enhanced serviceability. Also, an Mass airflow meter (with a built-in intake air temperature sensor) is provided in the air cleaner cap. ● A dry type air cleaner element is used and provided with an ample filtering surface area. ● A compact resonator is provided in the air cleaner hose to reduce intake noise. ● A full fabric air filter element, which does not contain an outer frame or rubber seal, is used. As a result, the case could be made compact, with recyclability in mind. ● A carbon filter,which adsorbs the HC that accumulates in the intake system when the engine is stopped ,has been adopted in the air cleaner cap in order to reduce evaporative emissions.(For U.S.A.,Canada,Koria,Taiwan) Mass Air Flow Meter Air Cleaner Cap Carbon Filter Air Cleaner Hose Full Fabric Air Filter Element Resonator Air Cleaner Element Air Cleaner Case Air Cleaner Inlet A4270051P Mass Air Flow Meter ● This mass air flow meter, which is a plug-in type, allows a portion of the intake air to flow through the detection area. -
The Pennsylvania State University Schreyer Honors College
THE PENNSYLVANIA STATE UNIVERSITY SCHREYER HONORS COLLEGE DEPARTMENT OF MECHANICAL & NUCLEAR ENGINEERING DESIGN AND CALIBRATION OF AN ELECTRONIC FUEL INJECTION SYSTEM FOR A COMPRESSED NATURAL GAS SPARK IGNITION INTERNAL COMBUSTION ENGINE IN A HYBRID VEHICLE SAMUEL H. MILLER SPRING 2013 A thesis submitted in partial fulfillment of the requirements for a baccalaureate degree in Mechanical Engineering with honors in Mechanical Engineering Reviewed and approved* by the following: Joel Anstrom Senior Research Associate at the Larson Institute Thesis Supervisor H.J. Sommer III Professor of Mechanical Engineering Honors Adviser Daniel Haworth Professor of Mechanical Engineering Faculty Reader * Signatures are on file in the Schreyer Honors College. ! ! ! ! !"#$%!&$' The United States has been dependent on foreign oil for many years. In 2011, the United States of America imported 45% of its petroleum from other nations [1]. In addition, efforts are being made to identify more eco-friendly options for fuel to serve as gasoline alternatives. One such fuel, which could decrease the United State dependence on foreign oil while helping the environment, is natural gas. An abundance of natural gas is found in the United States, and the burning of natural gas in internal combustion engines (ICE) releases less pollution and greenhouse gas emissions than gasoline. One of the most complex parts of natural gas ICE is the electronic fuel injection system. These systems are controlled by an electronic control unit (ECU), which is essential for optimizing engine efficiency, performance and emissions. The goal of this research was to reconfigure a hybrid-electric vehicle for compressed natural gas usage. ! ! "! ! ! ! ! TABLE OF CONTENTS LIST OF FIGURES AND TABLES.......................................................................................... -
Edelbrock Superchargers
TECH ARTICLE TECHApplication: DISCUSSIONEdelbrock Superchargers E-Force Boost Measurement (Installing A Boost Gauge Or Pressure Tranducer) 1. The TMAP sensor mounted on top of the manifold at the rear of the driver's side, outputs a 0-5 volt signal through pins 1 & 2 (pin 1 is signal & pin 2 is signal return,) that can be converted to an absolute pressure reading using the below calibration curve. Use of this signal requires an ambient pressure correction for calculating boost pressure. Voltage Pressure 0.62 2.70 0.80 3.69 1.09 5.70 1.40 7.69 1.71 9.70 2.17 12.70 2.46 14.70 2.70 16.21 2.94 17.70 3.25 19.71 3.55 21.70 3.84 23.71 4.15 25.70 4.46 27.70 4.76 29.70 2. The second option is to utilize the pressure port at the rear of the passenger side intake runner flange. Your supercharger has been pre- drilled and tapped for a 1/8" NPT fitting. There is currently a plug sealing the hole, which can be removed, and replaced with a fitting to adapt to your sensor. CAUTION: Never cut into the vacuum lines leading to the fuel rail pressure sensor and bypass actuator, on the driver's side of the manifold, for the purpose of tapping in a boost gauge. Interruption of the vacuum signal to the fuel rail pressure sensor can affect the fuel pressure reading to the PCM, which can result in engine failure! Furthermore, this port reads pressure before the intercooler, and therefore is before the inherent intercooler pressure drop. -
Automotive Sensors Commercial Vehicle Sensors Circuit Protection Solutions Automotive Sensors
Automotive Division PRODUCT PROFILE Automotive Sensors Commercial Vehicle Sensors Circuit Protection Solutions Automotive Sensors he Bourns Automotive Division has played a leading role in Tthe design, development and manufacture of potentiometer sensors for over 70 years. At our engineering centers in Riverside/ California, Taufkirchen/Germany and Auburn Hills/Michigan we develop and design a range of customized automotive position, speed and torque sensors. These products are manufactured in Ajka/Hungary, Chihuahua & Tijuana/Mexico and Xiamen/China. Bourns, Inc. is a privately held company with headquarters in Riverside, California. Currently, there are about 5,300 employees located in 14 different Bourns-owned design and manufacturing locations worldwide. Our research and development work combined with close collaboration with customers helps to ensure that our products meet the highest standards set for the automotive industry. Using state-of-the-art development software and world-class production methods, Bourns can provide innovative and cost-effective solutions for your applications. 2 Automotive Division ur phenolic paper, high aluminum oxide ceramics, Othermosetting plastics and specially developed Bourns® resistor inks are designed to withstand the harshest operating conditions within rated limits, with many of our sensors used in rigorous on and off highway applications. Our non-contacting sensors are developed with a wide range of magneto resistance- based angular sensor solutions supplemented by competitive Hall Effect and 2 Axis Hall Effect technology. Bourns can assist in the selection of the most appropriate technology for your specific applications. Bourns TS16949 certified quality system and the Bourns Production System (BPS) help ensure uncompromised quality and maximum reliability. Lean production methods are also used during the design and manufacturing phases of a project.