Design Considerations for Mortise and Tenon Connections
Total Page:16
File Type:pdf, Size:1020Kb
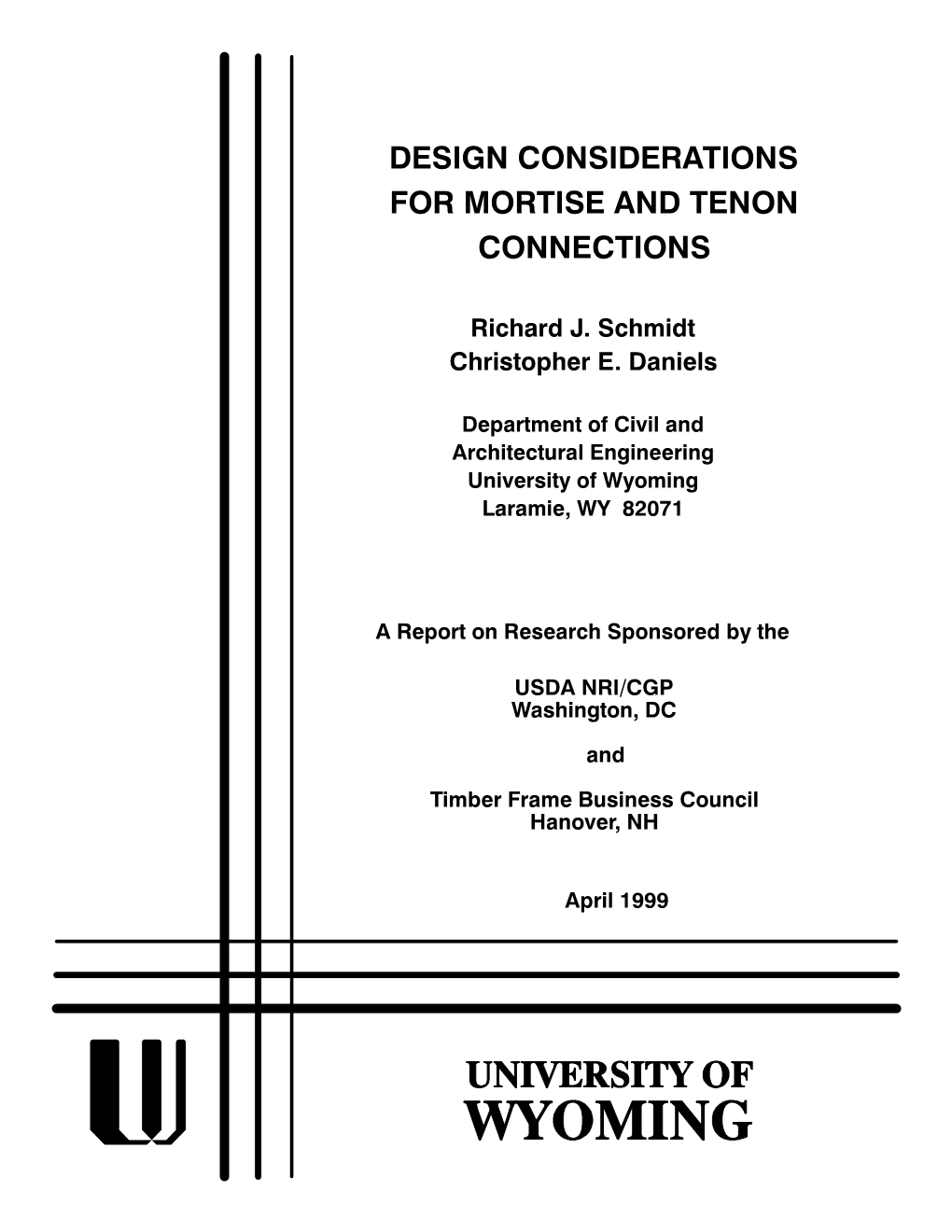
Load more
Recommended publications
-
TFEC 1-2019 Standard for Design of Timber Frame Structures And
TFEC 1-2019 Standard for Design of Timber Frame Structures and Commentary TFEC 1-2019 Standard Page 1 January 2019 TFEC 1-2019 Standard for Design of Timber Frame Structures and Commentary Timber Frame Engineering Council Technical Activities Committee (TFEC-TAC) Contributing Authors: Jim DeStefano Jeff Hershberger Tanya Luthi Jaret Lynch Tom Nehil Dick Schmidt, Chair Rick Way Copyright © 2019, All rights reserved. Timber Framers Guild 1106 Harris Avenue, Suite 303 Bellingham, WA 98225 TFEC 1-2019 Standard Page 2 January 2019 Table of Contents 1.0 General Requirements for Structural Design and Construction .......................................6 1.1 Applicability and Scope ........................................................................................ 6 1.2 Liability ................................................................................................................. 6 1.3 General Requirements ........................................................................................... 7 1.3.1 Strength ........................................................................................................... 7 1.3.2 Serviceability ................................................................................................... 7 1.3.3 General Structural Integrity ............................................................................. 7 1.3.4 Conformance with Standards .......................................................................... 7 1.4 Design Loads ........................................................................................................ -
Drill Bits 101 I've Used Dowels in a Variety of Woodworking Projects
Drill Bits 101 I’ve used dowels in a variety of woodworking projects having bought myself a pretty decent doweling jig a few years ago. The jig itself came with a twist drill bit for each of the three dowel sizes. For my dowel joinery I often need to drill holes of two different depths; so sometimes it is handy to have two bits of the same diameter with stops set at the different depths. One day I inadvertently was using both a twist bit and a brad point bit and noticed very different results. For example, drilling into end grain was far more difficult with a brad point bit than with the twist bit. All of this got me wondering about the different types of woodworking drill bits. Hence my investigation into the family tree of woodworking drill bits. Note that many drill bits may be multi-purpose, but generally speaking there are different families of bits for plastic, metal(s), tile, and masonry, etc. The basic job of a drill bit of course is to stay centered and not wander, cut the wood to form a round hole, and eject the chips. Seems simple, but not so perhaps, which is why there are so many types of drill bits and even options on lips, lands, flutes, margins, and other design elements – details beyond the scope of Bevel Cut. Of all the types, the common twist drill, invented by Steven Morse in 1863 and covered in US Patent 38119 is the simplest. The V-angle of the tip can vary from 60 to 118 degrees, with the latter being most common in today’s hardware stores according to my own research. -
Innovations in Heavy Timber Construction • © 2011 Woodworks
I NNOVAT I ONS I N T I MBER C ONSTRU C T I ON eavy timber construction—used for hundreds of years around the world—successfully combines the Combining beauty of exposed wood with the strength and fire the Beauty Hresistance of heavy timber. The traditional techniques used in ancient churches and temples, with their of Timber high-vaulted ceilings, sweeping curves and enduring strength, still influence today’s structures. The hallmarks of heavy timber—prominent wood beams and timbers—now also include elegant, leaner framing that celebrates the with Modern expression of structure with a natural material. A visual emphasis on beams, purlins and connections lends character and a powerful aesthetic sense Construction of strength. Historically a handcrafted skill of mortise and tenon joinery, heavy timber construction has been modernized by tools such as CNC machines, high- strength engineered wood products, and mass-production techniques. A growing environmental awareness that recognizes wood as the only renewable and sustainable structural building material is also invigorating this type of construction. Heavy timbers are differentiated from dimensional lumber by having minimum dimensions required by the building code. Modern versions include sawn stress-grade lumber, timber tongue and groove decking, glued-laminated timber (glulam), parallel strand lumber (PSL), laminated veneer lumber (LVL) and cross laminated timber (CLT). Structural laminated products can be used as solid walls, floors and columns to construct an entire building. Modern heavy timber construction contributes to the appeal, comfort, structural durability and longevity of schools, churches, large-span recreation centers, mid-rise/multi-family housing and supermarkets, among many other buildings. -
2010 Directory of Maine's Primary Wood Processors
Maine State Library Digital Maine Forest Service Documents Maine Forest Service 9-14-2011 2010 Directory of Maine's Primary Wood Processors Maine Forest Service Forest Policy and Management Division Follow this and additional works at: https://digitalmaine.com/for_docs Recommended Citation Maine Forest Service, "2010 Directory of Maine's Primary Wood Processors" (2011). Forest Service Documents. 253. https://digitalmaine.com/for_docs/253 This Text is brought to you for free and open access by the Maine Forest Service at Digital Maine. It has been accepted for inclusion in Forest Service Documents by an authorized administrator of Digital Maine. For more information, please contact [email protected]. 2010 Directory of Maine’s Primary Wood Processors Robert J. Lilieholm, Peter R. Lammert, Greg R. Lord and Stacy N. Trosper Maine Forest Service Department of Conservation 22 State House Station Augusta, Maine 04333-0022 School of Forest Resources University of Maine Orono, Maine 04469-5755 December 2010 Table of Contents Introduction ......................................................................................................................... 1 Maine's Primary Wood Processors I. Stationary Sawmills ............................................................................................. 4 II. Portable Sawmills ............................................................................................. 67 III. Pulp and Paper Manufacturers ...................................................................... 106 IV. Stand-Alone -
EM-Tec VS42 Universal Spring-Loaded Vise
Technical Support Bulletin EM-Tec VS42 universal spring-loaded vise Products #12-000220 and #12-000320 Description The EM-Tec VS42 universal spring-loaded vise clamp includes two reversible vise plates and four dowel pins which fit into the top of the brass sliding bar. The maximum clamping capacity between the vise jaws is 42mm. Available with either the standard 3.2mm pin or an M4 threaded hole for mounting on the SEM sample stage. Operation Consider wearing gloves to avoid contamination. • To open the EM-Tec universal spring-loaded vise clamp, pull on the side of the brass sliding bars. • Place the sample between the vise jaws and gently release the sliding bars. • The tension on the 4 springs will hold the sample between the jaws in the middle of the holder. • The universal spring-loaded vice clamp acts as a centering vise. The aluminium vise plates are mounted on the brass sliding bars with brass M3 screws. The reversible vise jaws comprise a smooth side and a side with three small grooves. The grooves are more suitable for small round samples or to hold sample with a rough side. For awkwardly shaped samples, the vise jaws can be removed and 4 dowel pins can be inserted in the brass sliding bar to clamp the sample between the 4 dowel pins. Optional vise jaws are available for large round samples. By using longer M3 screws, the vise jaws can be stacked to double the jaw height from 12 to 24mm. For samples which are thinner than 1mm, an alternative vise type holder with a screw should be considered. -
Plain & Pre-Glued Dowel Pin FAQ How Do You Determine What Size
Plain & Pre‐Glued Dowel Pin FAQ How do you determine what size dowel to use? The length of the dowel is generally determined by how much dowel can be inserted into the shortest member of the two piece joint. Twice this length is a common rule of thumb for determining dowel length. For example, if your shortest member is 1” thick and you know your safest drilling depth is 3/4”, then a 1‐1/2” dowel should be used. A 1‐1/2” length equates to two times the 3/4” thickness. The longer the dowel, the greater the holding strength. A similar procedure can be used to determine a proper diameter for the dowel. Generally, the diameter of the dowel should be no greater than half the thickness of the stock. For example, if the side panel is 1” thick, then you want to use a maximum 1/2” dowel. Incorrect hole depth or diameter create improper dowel joints by trapping glue or water at the bottom of the hole which is not properly distributed around the dowel. How deep should a dowel pin be inserted to be most effective? The longer the dowel, the greater the strength. The ideal joint has the dowel hole match the length of the dowel on both ends allowing the dowel to be inserted to the bottom of the hole. To avoid “blowout” on side panels, a small void of 2mm or 5/64”, is often left as insurance to collect excess glue or water in addition to allowing for variations in dowel length. -
VET Job Guide
NSW Department of Education Carpenter and Joiner Carpenters and joiners love working their hands to construct, erect, install, and repair structures made of wood. You’ll get great satisfaction Will I get a job? out of seeing your finished work enliven a home or building. Moderate growth in this occupation is predicted, with 200 What carpenters and joiners do new jobs in Australia in the next four years, Carpenters and joiners use their broad knowledge of building methods and timbers to bringing the total to make, install, repair or renovate structures, fixtures and fittings. They work on residential 117,800. and commercial projects constructing buildings, ships, bridges or concrete formwork, and in maintenance roles in factories, hospitals, institutions, and homes. What will I earn? On residential jobs, carpenters and joiners build the house framework, walls, roof frame, $951–$1,100 median and exterior finish. They install doors, windows, flooring, cabinets, stairs, handrails, full-time weekly salary panelling, moulding, and ceiling tiles. On commercial construction jobs, they build (before tax, excluding concrete forms, scaffolding, bridges, trestles, tunnels, shelters, towers or repair and super). maintain existing structures. Shop fitter, joiners, fixers or finish carpenters create wood furniture, window and door fittings, parquet floors and stairs for new homes and renovation projects. They may also create and sell their own furniture. Joiners are mostly based in workshops while carpenters often travel between sites until each job is completed. Carpenters may work as subcontractors employed by building and construction companies or are self-employed. education.nsw.gov.au NSW Department of Education You’ll like this job if… Roles to look for You enjoy creating things with your hands. -
Creating a Timber Frame House
Creating a Timber Frame House A Step by Step Guide by Brice Cochran Copyright © 2014 Timber Frame HQ All rights reserved. No part of this publication may be reproduced, stored in a retrieval system, or transmitted in any form or by any means, electronic, mechanical, recording or otherwise, without the prior written permission of the author. ISBN # 978-0-692-20875-5 DISCLAIMER: This book details the author’s personal experiences with and opinions about timber framing and home building. The author is not licensed as an engineer or architect. Although the author and publisher have made every effort to ensure that the information in this book was correct at press time, the author and publisher do not assume and hereby disclaim any liability to any party for any loss, damage, or disruption caused by errors or omissions, whether such errors or omissions result from negligence, accident, or any other cause. Except as specifically stated in this book, neither the author or publisher, nor any authors, contributors, or other representatives will be liable for damages arising out of or in connection with the use of this book. This is a comprehensive limitation of liability that applies to all damages of any kind, including (without limitation) compensatory; direct, indirect or consequential damages; income or profit; loss of or damage to property and claims of third parties. You understand that this book is not intended as a substitute for consultation with a licensed engineering professional. Before you begin any project in any way, you will need to consult a professional to ensure that you are doing what’s best for your situation. -
Operating Instructions and Parts Manual 14-Inch Vertical Band Saws Models: J-8201, J-8203, J-8201VS, J-8203VS
Operating Instructions and Parts Manual 14-inch Vertical Band Saws Models: J-8201, J-8203, J-8201VS, J-8203VS JET 427 New Sanford Road LaVergne, Tennessee 37086 Part No. M-414500 Ph.: 800-274-6848 Revision F 09/2018 www.jettools.com Copyright © 2016 JET Warranty and Service JET warrants every product it sells against manufacturers’ defects. If one of our tools needs service or repair, please contact Technical Service by calling 1-800-274-6846, 8AM to 5PM CST, Monday through Friday. Warranty Period The general warranty lasts for the time period specified in the literature included with your product or on the official JET branded website. • JET products carry a limited warranty which varies in duration based upon the product. (See chart below) • Accessories carry a limited warranty of one year from the date of receipt. • Consumable items are defined as expendable parts or accessories expected to become inoperable within a reasonable amount of use and are covered by a 90 day limited warranty against manufacturer’s defects. Who is Covered This warranty covers only the initial purchaser of the product from the date of delivery. What is Covered This warranty covers any defects in workmanship or materials subject to the limitations stated below. This warranty does not cover failures due directly or indirectly to misuse, abuse, negligence or accidents, normal wear-and-tear, improper repair, alterations or lack of maintenance. JET woodworking machinery is designed to be used with Wood. Use of these machines in the processing of metal, plastics, or other materials outside recommended guidelines may void the warranty. -
Measurement and Modeling of the In-Plane Permeability of Oriented Strand-Based Wood Composites
MEASUREMENT AND MODELING OF THE IN-PLANE PERMEABILITY OF ORIENTED STRAND-BASED WOOD COMPOSITES by Chao Zhang B.Sc., Tsinghua University, 2006 A THESIS SUBMITTED IN PARTIAL FULFILMENT OF THE REQUiREMENTS FOR THE DEGREE OF MASTER OF SCIENCE in The Faculty of Graduate Studies (Forestry) THE UNIVERSITY OF BRITISH COLUMBIA (Vancouver) April 2009 © Chao Zhang, 2009 Abstract The objective of this research is to investigate the effects of panel density and air flow direction on the in-plane permeability of oriented strand-based wood composites. In- plane permeability is a key factor governing the energy consumption and pressing time during manufacture. The result is expected to provide information which could potentially reduce the pressing time. The thick, oriented strand boards of five densities were made of aspen (Populus tremuloides), and pressed in the laboratory. The production procedure yielded a uniform vertical density profile and good strand orientation. The specimens were sealed in a specially designed specimen holder and connected to a permeability measurement apparatus. The permeability values in parallel, perpendicular, and 45° to the strand orientation were obtained. The results showed that permeability values decreased rapidly as the density increased. The permeability was highest in the parallel-to-strand direction, and lowest in the perpendicular-to-strand direction. The permeability value in 45° direction was between the values of parallel- and perpendicular-to-strand directions. A polynomial equation was fitted to the results and an R2 was between 0.93 8 and 0.993. To examine the void structure changes during the densification, microscopic techniques were employed. Microscopic slides for each density level were prepared with a typical method widely used for petrography, and then investigated with a fluorescence microscope. -
Allison Lumber Company Collection
Allison Lumber Company Collection Evan F. Allison (1865 - 1937). In the management of his lands he led the way in Alabama to profitable forest conservation through selective tree cutting and reforestation. He restored species of wildlife indigenous to the area and taught methods for their conservation. - Alabama Hall of Fame, 1961. Although born to a family of limited resources, Evan Allison, with Steve Smith, and a third partner, R.C. Derby (also of Sumter County), established the Allison Lumber Company at Bellamy, AL in 1899. Bellamy was founded as a sawmill town. It was home to Sumter County’s first hospital which was established by the Allison Lumber Company. In 1903, the lumber company built a small frame structure near the site of the hospital to be used as a school (and a church on Sundays). Allison Lumber hired and paid the teachers. Over many decades, Mr. Allison guided the company to a position of leadership in the pine and hardwood industries. He was widely respected and solicited to run for Governor, but he declined. He gained control of wide timber interests and took an active part in the economic development of the state. This collection provides excellent documentation about how a successful business was run in the rural South during the nineteen twenties; banking; job applications; correspondence with the most influential people in the state; World War I restrictions on businesses; the fight to establish wildlife conservation; social customs including the hosting of the elaborate annual hunt – a combination of politics and recreation. Collection Span: Bulk of materials from 1917 - 1927 (History and 2 postcards from the 1960s.) (Cancelled checks from 1898 - 1938.) Size: 2 cu. -
Mass Timber Connections
WoodWorks Connection Design Workshop Bernhard Gafner, P.Eng, MIStructE, Dipl. Ing. FH/STV [email protected] Adam Gerber, M.A.Sc. [email protected] Disclaimer: This presentation was developed by a third party and is not funded by WoodWorks or the Softwood Lumber Board. “The Wood Products Council” This course is registered is a Registered Provider with with AIA CES for continuing The American Institute of professional education. As Architects Continuing such, it does not include Education Systems (AIA/CES), content that may be Provider #G516. deemed or construed to be an approval or endorsement by the AIA of any material of Credit(s) earned on construction or any method completion of this course will or manner of handling, be reported to AIA CES for using, distributing, or AIA members. Certificates of dealing in any material or Completion for both AIA product. members and non-AIA __________________________________ members are available upon Questions related to specific materials, methods, and services will be addressed request. at the conclusion of this presentation. Description For engineers new to mass timber design, connections can pose a particular challenge. This course focuses on connection design principles and analysis techniques unique to mass timber products such as cross-laminated timber, glued-laminated timber and nail-laminated timber. The session will focus on design options for connection solutions ranging from commodity fasteners, pre- engineered wood products and custom-designed connections. Discussion will also include a review of timber mechanics and load transfer, as well as considerations such as tolerances, fabrication, durability, fire and shrinkage that are relevant to structural design.