A Performance Analysis of Folding Conformal Propeller Blade Designs
Total Page:16
File Type:pdf, Size:1020Kb
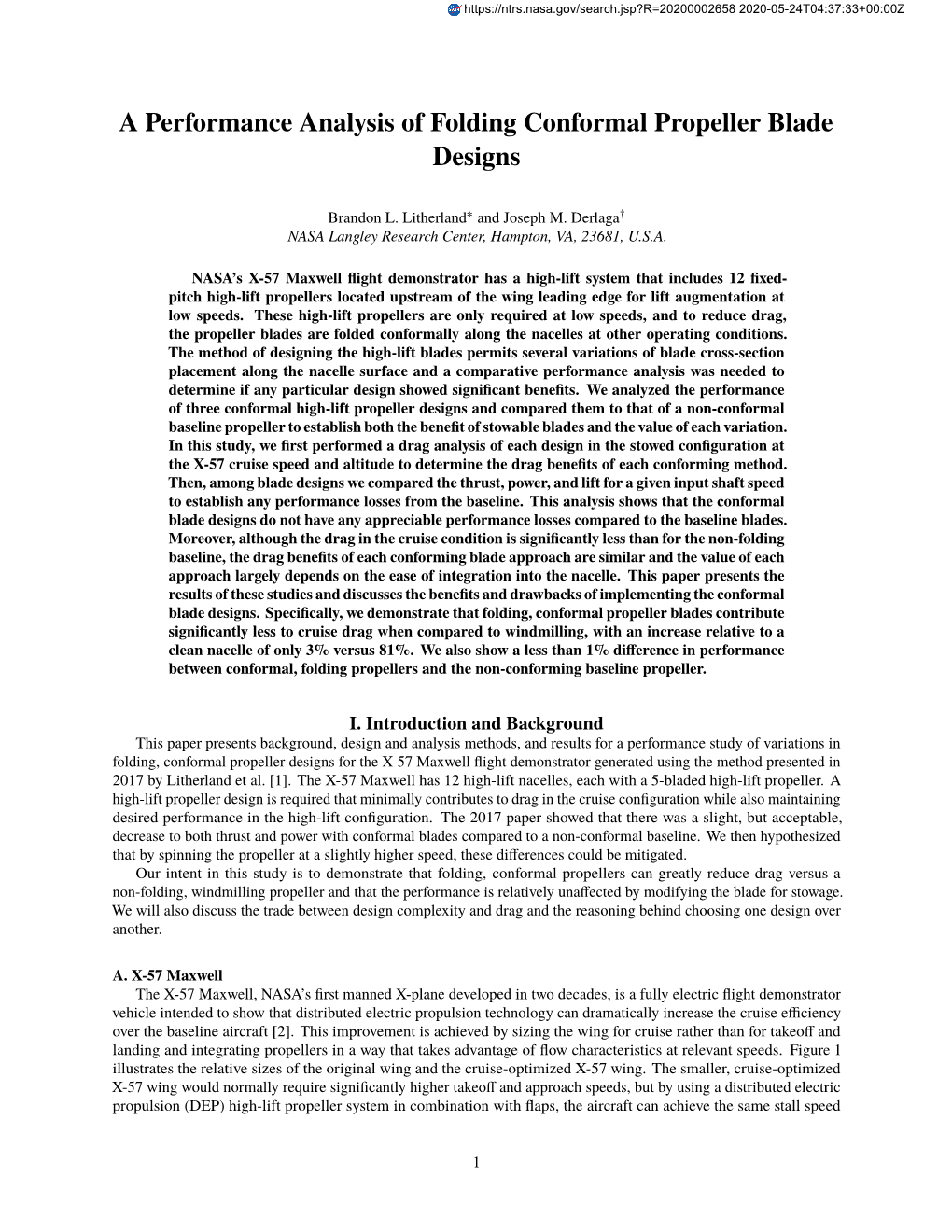
Load more
Recommended publications
-
Propeller Operation and Malfunctions Basic Familiarization for Flight Crews
PROPELLER OPERATION AND MALFUNCTIONS BASIC FAMILIARIZATION FOR FLIGHT CREWS INTRODUCTION The following is basic material to help pilots understand how the propellers on turbine engines work, and how they sometimes fail. Some of these failures and malfunctions cannot be duplicated well in the simulator, which can cause recognition difficulties when they happen in actual operation. This text is not meant to replace other instructional texts. However, completion of the material can provide pilots with additional understanding of turbopropeller operation and the handling of malfunctions. GENERAL PROPELLER PRINCIPLES Propeller and engine system designs vary widely. They range from wood propellers on reciprocating engines to fully reversing and feathering constant- speed propellers on turbine engines. Each of these propulsion systems has the similar basic function of producing thrust to propel the airplane, but with different control and operational requirements. Since the full range of combinations is too broad to cover fully in this summary, it will focus on a typical system for transport category airplanes - the constant speed, feathering and reversing propellers on turbine engines. Major propeller components The propeller consists of several blades held in place by a central hub. The propeller hub holds the blades in place and is connected to the engine through a propeller drive shaft and a gearbox. There is also a control system for the propeller, which will be discussed later. Modern propellers on large turboprop airplanes typically have 4 to 6 blades. Other components typically include: The spinner, which creates aerodynamic streamlining over the propeller hub. The bulkhead, which allows the spinner to be attached to the rest of the propeller. -
2 Review of Composite Propeller Developments
'HIHQFH5HVHDUFKDQG 5HFKHUFKHHWGpYHORSSHPHQW 'HYHORSPHQW&DQDGD SRXUODGpIHQVH&DQDGD Review of Composite Propeller Developments and Strategy for Modeling Composite Propellers using PVAST Tamunoiyala S. Koko Khaled O. Shahin Unyime O. Akpan Merv E. Norwood Prepared By: Martec Limited 1888 Brunswick Street, Suite 400 Halifax, NS B3J 3J8 Team Leader, Reliability & Risk Engineering Contractor's Document Number: TR-11-XX Contract Project Manager: Tamunoiyala S. Koko, 902-425-5101 Ext 243 PWGSC Contract Number: W7707-088100 Task 10 &6$/D\WRQ*LOUR\ The scientific or technical validity of this Contract Report is entirely the responsibility of the Contractor and the contents do not necessarily have the approval or endorsement of Defence R&D Canada. Defence R&D Canada – Atlantic &RQWUDFW5HSRUW '5'&$WODQWLF&5 6HSWHPEHU Review of Composite Propeller Developments and Strategy for Modeling Composite Propellers using PVAST Tamunoiyala S. Koko Khaled O. Shahin Unyime O. Akpan Merv E. Norwood Prepared By: Martec Limited 1888 Brunswick Street, Suite 400 Halifax, NS B3J 3J8 Team Leader, Reliability & Risk Engineering Contractor's Document Number: TR-11-XX Contract Project Manager: Tamunoiyala S. Koko, 902-425-5101 Ext 243 PWGSC Contract Number: W7707-088100 Task 10 &6$/D\WRQ*LOUR\ The scientific or technical validity of this Contract Report is entirely the responsibility of the Contractor and the contents do not necessarily have the approval or endorsement of Defence R&D Canada. Defence R&D Canada – Atlantic Contract Report DRDC Atlantic CR 2011-156 6HSWHPEHU © Her Majesty the Queen in Right of Canada, as represented by the Minister of National Defence, 201 © Sa Majesté la Reine (en droit du Canada), telle que représentée par le ministre de la Défense nationale, 201 Abstract ……. -
Marine Propellers
2.016 Hydrodynamics Reading #10 2.016 Hydrodynamics Prof. A.H. Techet Marine Propellers Today, conventional marine propellers remain the standard propulsion mechanism for surface ships and underwater vehicles. Modifications of basic propeller geometries into water jet propulsors and alternate style thrusters on underwater vehicles has not significantly changed how we determine and analyze propeller performance. We still need propellers to generate adequate thrust to propel a vessel at some design speed with some care taken in ensuring some “reasonable” propulsive efficiency. Considerations are made to match the engine’s power and shaft speed, as well as the size of the vessel and the ship’s operating speed, with an appropriately designed propeller. Given that the above conditions are interdependent (ship speed depends on ship size, power required depends on desired speed, etc.) we must at least know a priori our desired operating speed for a given vessel. Following this we should understand the basic relationship between ship power, shaft torque and fuel consumption. Power: Power is simply force times velocity, where 1 HP (horsepower, english units) is equal to 0.7457 kW (kilowatt, metric) and 1kW = 1000 Newtons*meters/second. P = F*V (1.1) Effective Horsepower (EHP) is the power required to overcome a vessel’s total resistance at a given speed, not including the power required to turn the propeller or operate any machinery (this is close to the power required to tow a vessel). version 3.0 updated 8/30/2005 -1- ©2005 A. Techet 2.016 Hydrodynamics Reading #10 Indicated Horsepower (IHP) is the power required to drive a ship at a given speed, including the power required to turn the propeller and to overcome any additional friction inherent in the system. -
Want Something Better Than the OEM Propeller?
Quick Reference Guide Product Info • Prop Selection • Crossover Info • Part List Want Something Better Than The OEM Propeller? Run FASTER • Pull HARDER • Handle BETTER Get A free Diameter & Pitch Recommendation Today Visit us on the web at: https://turningpointpropellers.com/PROPWIZARD 6-300+hp • 3 AND 4 BLADE • ALUMINUM AND STAINLESS STEEL OUTBOARD AND STERNDRIVE BOAT PROPELLERS AVAILABLE FOR: Coleman® Evinrude® Honda® Johnson® Mariner® Mercury® MerCruiser® Nissan® OMC® Parsun® Suzuki® Tohatsu® Volvo Penta® Yamaha® Turning Point Propellers Industry Leading Manufacturer of Aluminum and Stainless Steel Pleasure Boat Propellers NO FASTER PROP ON THE WATER CONTENTS About Turning Point Propellers 1-6 Propeller Selection 7-14 OEM & Aftermarket Brand Crossover 15 ® Solas Crossover to Turning Point 16-24 Turning Point Propellers Features and Benefits (Con’t) ® Quicksilver Crossover to Turning Point 25-26 ® 11762 Marco Beach Drive STE. 2 Michigan Wheel Crossover to Turning Point 27-30 Jacksonville, FL 32224 Premium ULTRACOAT Powder Coat (Hustler Prop Series) Turning Point Propellers Part List 30-31 United States • Exclusive to Turning Point, the Ultracoat powder coat rivals a fine automotive finish, and 24 Hour Slurry Test: 600% More Wear! Competitor’s Process Office Hours: 9am-5pm ET M-F is more durable than paint. Phone: +1 904-900-7739 • Utilizing a state-of-the-art five step process, Ultracoat gives the propeller a shiny, uniform Who Is Turning Point Propellers Press (1) for Product Installation & Tech Support • One of the worlds largest propeller manufacturers. We own and operate our own aluminum Press (2) for Purchase Orders & Accounting appearance that enhances any boat’s good looks. -
Marine Propellers and Propulsion to Jane and Caroline Marine Propellers and Propulsion
Marine Propellers and Propulsion To Jane and Caroline Marine Propellers and Propulsion Second Edition J S Carlton Global Head of MarineTechnology and Investigation, Lloyd’s Register AMSTERDAM • BOSTON • HEIDELBERG • LONDON • NEW YORK • OXFORD PARIS • SAN DIEGO • SAN FRANCISCO • SINGAPORE • SYDNEY • TOKYO Butterworth-Heinemann is an imprint of Elsevier Butterworth-Heinemann is an imprint of Elsevier Linacre House, Jordan Hill, Oxford OX2 8DP 30 Corporate Drive, Suite 400, Burlington, MA 01803, USA First edition 1994 Second edition 2007 Copyright © 2007, John Carlton. Published by Elsevier Ltd. All right reserved The right of John Carlton to be identified as the authors of this work has been asserted in accordance with the Copyright, Designs and Patents Act 1988 No part of this publication may be reproduced, stored in a retrieval system or transmitted in any form or by any means electronic, mechanical, photocopying, recording or otherwise without the prior written permission of the publisher Permissions may be sought directly from Elsevier’s Science & Technology Rights Department in Oxford, UK: phone ( 44) (0) 1865 843830; fax ( 44) (0) 1865 853333; email: [email protected]. Alternatively+ you can submit your+ request online by visiting the Elsevier web site at http://elsevier.com/locate/permissions, and selecting Obtaining permission to use Elsevier material Notice No responsibility is assumed by the published for any injury and/or damage to persons or property as a matter of products liability, negligence or otherwise, or from any use or operation of any methods, products, instructions or ideas contained in the material herein. Because of rapid advances in the medical sciences, in particular, independent verification of diagnoses and drug dosages should be made British Library Cataloguing in Publication Data Carlton, J. -
Low and High Speed Propellers for General Aviation - Performance Potential and Recent Wind Tunnel Test Results
NASA Technical Memorandum 8 1745 Low and High Speed Propellers for General Aviation - Performance Potential and Recent Wind Tunnel Test Results Robert J. Jeracki and Glenn A. Mitchell Lewis Research Center Cleveland, Ohio i I Prepared for the ! National Business Aircraft Meeting sponsored by the Society of Automotive Engineers Wichita, Kansas, April 7-10, 1981 LOW AND HIGH SPEED PROPELLERS FOR GENERAL AVIATION - PERFORMANCE POTENTIAL AND RECENT WIND TUNNEL TEST RESULTS by Robert J. Jeracki and Glenn A. Mitchell National Aeronautics and Space Administration Lewis Research Center Cleveland, Ohio 441 35 THE VAST MAJORlTY OF GENERAL-AVIATION AIRCRAFT manufactured in the United States are propel- ler powered. Most of these aircraft use pro- peller designs based on technology that has not changed significantlv since the 1940's and early 1950's. This older technology has been adequate; however, with the current world en- ergy shortage and the possibility of more stringent noise regulations, improved technol- ogy is needed. Studies conducted by NASA and industry indicate that there are a number of improvements in the technology of general- aviation (G.A.) propellers that could lead to significant energy savings. New concepts like blade sweep, proplets, and composite materi- als, along with advanced analysis techniques have the potential for improving the perform- ance and lowering the noise of future propel- ler-powererd aircraft that cruise at lower speeds. Current propeller-powered general- aviation aircraft are limited by propeller compressibility losses and limited power out- put of current engines to maximum cruise speeds below Mach 0.6. The technology being developed as part of NASA's Advanced Turboprop Project offers the potential of extending this limit to at least Mach 0.8. -
Hydromatic Propeller
HYDROMATIC PROPELLER International Historic Engineering Landmark Hamilton Standard The American Society of A Division of United Technologies Mechanical Engineers Windsor Locks, Connecticut November 8, 1990 Historical Significance The text of this International Landmark Designation: The Hamilton Standard Hydromatic propeller represented INTERNATIONAL HISTORIC MECHANICAL a major advance in propeller design and laid the groundwork ENGINEERING LANDMARK for further advancements in propulsion over the next 50 years. The Hydromatic was designed to accommodate HAMILTON STANDARD larger blades for increased thrust, and provide a faster rate HYDROMATIC PROPELLER of pitch change and a wider range of pitch control. This WINDSOR LOCKS, CONNECTICUT propeller utilized high-pressure oil, applied to both sides of LATE 1930s the actuating piston, for pitch control as well as feathering — the act of stopping propeller rotation on a non-functioning The variable-pitch aircraft propeller allows the adjustment engine to reduce drag and vibration — allowing multiengined in flight of blade pitch, making optimal use of the engine’s aircraft to safely continue flight on remaining engine(s). power under varying flight conditions. On multi-engined The Hydromatic entered production in the late 1930s, just aircraft it also permits feathering the propeller--stopping its in time to meet the requirements of the high-performance rotation--of a nonfunctioning engine to reduce drag and military and transport aircraft of World War II. The vibration. propeller’s performance, durability and reliability made a The Hydromatic propeller was designed for larger blades, major contribution to the successful efforts of the U.S. and faster rate of pitch change, and wider range of pitch control Allied air forces. -
Wärtsilä Rudder Solutions
Courtesy of Finnlines Oy, photographed by Hannu Laakso. Energopac incorporated in model tests, photographed by HSVA. CFD capabilities within Wärtsilä are state-of-the-art. In 2009, two Energopac systems were delivered to a newbuilding project, and in early 2010 the first Energopac retrofit was successfully installed. Another 12 Energopac systems are currently on order for delivery in 2010 and 2011. OPTIMIZING ENERGY EFFICIENCY The Wärtsilä Propeller-Rudder System, Energopac is an optimized propulsion and Wärtsilä is continuously looking to improve Energopac has been designed to include the manoeuvring solution for coastal and seagoing the energy efficiency of its propulsion following benefits: vessels. Its key objective is to reduce a vessel’s solutions. In so doing, we aim to reduce fuel • improved energy efficiency and reduced fuel fuel consumption and CO2 emissions through consumption, lower the operational costs of consumption, thanks to integrated propeller integrating the propeller and rudder design. seagoing vessels, and, of course, cut back on and rudder design Energopac is tailored for each and every vessel emissions. We design our solutions to meet • excellent manoeuvrability to meet the customer’s specific requirements, specific customer requirements, utilizing our • lower vibration levels and higher comfort and can thus be optimized for energy efficiency, extensive marine industry experience and onboard without compromising manoeuvrability or state-of-the-art, modern techniques, such as • reduced levels of emissions comfort. CFD (Computational Fluid Dynamics). ENERGOPAC INTEGRATED PROPULSION AND DESIGNED FOR PERFECTION MANOEUVRING PERFORMANCE Energopac was developed through co-operation Our high efficiency rudder technology dates back to the 1990s when Wärtsilä started making energy-saving A vessel’s power efficiency level is dependent between Wärtsilä’s propulsion specialists, and rudders. -
Marine Propeller Optimisation - Strategy and Algorithm Development
THESIS FOR THE DEGREE OF DOCTOR OF PHILOSOPHY Marine Propeller Optimisation - Strategy and Algorithm Development FLORIAN VESTING Department of Shipping and Marine Technology CHALMERS UNIVERSITY OF TECHNOLOGY Gothenburg, Sweden 2015 Marine Propeller Optimisation - Strategy and Algorithm Development FLORIAN VESTING ISBN 978-91-7597-263-3 c FLORIAN VESTING, 2015 Doktorsavhandlingar vid Chalmers tekniska hogskola¨ Ny serie nr. 2015:3944 ISSN 0346-718X Department of Shipping and Marine Technology Division of Marine Technology Chalmers University of Technology SE-412 96 Gothenburg Sweden Telephone: +46 (0)31-772 1000 Cover: Marine propeller manufacturing c Rolls-Royce Plc. Reproduced with permission. Printed by Chalmers Reproservice Gothenburg, Sweden 2015 Marine Propeller Optimisation - Strategy and Algorithm Development Thesis for the degree of Doctor of Philosophy FLORIAN VESTING Department of Shipping and Marine Technology Division of Marine Technology Chalmers University of Technology Abstract Recent trends in the shipping industry, e.g., expanded routing in ecologically sensitive areas and emission regulations, have sharpened the perception of efficient propeller designs. Currently, propeller efficiency, estimated fuel consumption and, more often, propeller-radiated noise are parameters that steer the business Zeitgeist. However, a practical propeller design that performs reliably and sufficiently throughout the lifetime of a ship requires numerous limitations, which are typically in conflict with the objectives. This requires judgement by experienced propeller designers to make decisions during the design process. To be ahead of competitors, a propeller designer needs to present a better design for a specific purpose, in a shorter time and at lower costs than the adversary. The current challenge for propeller designers is to develop a propeller that fulfils all the requirements and expectations within a short time frame. -
Federal Aviation Administration, DOT § 23.933
Federal Aviation Administration, DOT § 23.933 affected by the turbocharger system in- clearance necessary to prevent harmful stallations must be evaluated. Turbo- vibration; charger operating procedures and limi- (2) At least one-half inch longitudinal tations must be included in the Air- clearance between the propeller blades plane Flight Manual in accordance or cuffs and stationary parts of the air- with § 23.1581. plane; and (3) Positive clearance between other [Amdt. 23–7, 34 FR 13092, Aug. 13, 1969, as amended by Amdt. 23–43, 58 FR 18970, Apr. 9, rotating parts of the propeller or spin- 1993] ner and stationary parts of the air- plane. § 23.925 Propeller clearance. [Doc. No. 4080, 29 FR 17955, Dec. 18, 1964, as Unless smaller clearances are sub- amended by Amdt. 23–43, 58 FR 18971, Apr. 9, stantiated, propeller clearances, with 1993; Amdt. 23–51, 61 FR 5136, Feb. 9, 1996; the airplane at the most adverse com- Amdt. 23–48, 61 FR 5148, Feb. 9, 1996] bination of weight and center of grav- § 23.929 Engine installation ice protec- ity, and with the propeller in the most tion. adverse pitch position, may not be less than the following: Propellers (except wooden propellers) (a) Ground clearance. There must be a and other components of complete en- clearance of at least seven inches (for gine installations must be protected each airplane with nose wheel landing against the accumulation of ice as nec- gear) or nine inches (for each airplane essary to enable satisfactory func- with tail wheel landing gear) between tioning without appreciable loss of each propeller and the ground with the thrust when operated in the icing con- landing gear statically deflected and in ditions for which certification is re- the level, normal takeoff, or taxing at- quested. -
Structural Considerations in the Design of the POLAR Class of Coast Guard Icebreakers Bruce H
,,.W,+, THE SOCIETYOF NAvAL ARCHITECTSAND MARINE ENGINEERS 74 TrinityPlace,New York,N.Y.,10006 # *: P,PertobeDre$entedattheShipStructureSymPosiUm 8 :c W,sh,rwton,DC.,October68,1975 010 ~+ 2 Q%,,“,,*>>+. Structural Considerations in the Design of the POLAR Class of Coast Guard Icebreakers Bruce H. Barber, Luis M. Baez and Gary J. North, Members, U.S. Coast Guard Headquarters, Washington, DC. c Cowr,8ht1975 by The SOC’etY.f NavalArc17,tects,nd Msr,!,eEnE’neers Artist’s conception of United States Ceast Guard icebreaker POW STAR (WAGB-10 ) structural failures were undertaken to ABSTRACT aesist in the selection of hull mat- erials, Various finite element analyses The design of the Coast Guard’s were conducted for portions of existing POLAR Class icebreakers incorporated and proposed structural arrangements the results of four years of research, with special emphasis on the forward analysis and testing aimed at optimizing structure. With the coperation of other the structural design. Opration and agent ies, studies of the strength of sea load data were gathered by instrumenting ice led to updated ooncepts of loading existing icebreakers. Exten8ive tests that resulted in significant changes in and studies of available steels as we 11 design phi losophy snd refinements over as a methodical analysis of reported previous icebreaker designs. c-1 — INTRODUCTION The need has been apparent since the early 19607S for a new class of ice- Polar icebreakers onerate under the breaking ships to replace aging members most inhospitable ocean ~onditions the of the fleet and to undertake more ex- world has to offer. Designed for opti– tensive duties as Coast Guard Responsi- mum performance at low temperatures in bilities change and expand. -
Design, Construction and Performance Evaluation of Axial Flow Fans
DESIGN, CONSTRUCTION AND PERFORMANCE EVALUATION OF AXIAL FLOW FANS A THESIS SUBMITTED TO THE GRADUATE SCHOOL OF NATURAL AND APPLIED SCIENCES OF MIDDLE EAST TECHNICAL UNIVERSITY BY HAYRETTİN ÖZGÜR KEKLİKOĞLU IN PARTIAL FULFILLMENT OF THE REQUIREMENTS FOR THE DEGREE OF MASTER OF SCIENCE IN MECHANICAL ENGINEERING SEPTEMBER 2019 Approval of the thesis: DESIGN, CONSTRUCTION AND PERFORMANCE EVALUATION OF AXIAL FLOW FANS submitted by HAYRETTİN ÖZGÜR KEKLİKOĞLU in partial fulfillment of the requirements for the degree of Master of Science in Mechanical Engineering Department, Middle East Technical University by, Prof. Dr. Halil Kalıpçılar Dean, Graduate School of Natural and Applied Sciences Prof. Dr. M. A. Sahir Arıkan Head of Department, Mechanical Engineering Prof. Dr. Kahraman Albayrak Supervisor, Mechanical Engineering, METU Examining Committee Members: Assoc. Prof. Dr. Cüneyt Sert Mechanical Engineering. METU Prof. Dr. Kahraman Albayrak Mechanical Engineering, METU Assoc. Prof. Dr. Mehmet Metin Yavuz Mechanical Engineering, METU Assist. Prof. Dr. Özgür Uğraş Baran Mechanical Engineering, METU Assist. Prof. Dr. Ekin Özgirgin Yapıcı Mechanical Engineering, Çankaya University Date: 03.09.2019 I hereby declare that all information in this document has been obtained and presented in accordance with academic rules and ethical conduct. I also declare that, as required by these rules and conduct, I have fully cited and referenced all material and results that are not original to this work. Name, Surname: Hayrettin Özgür Keklikoğlu Signature: iv