The Entropy and Related Thermodynamic Properties Of
Total Page:16
File Type:pdf, Size:1020Kb
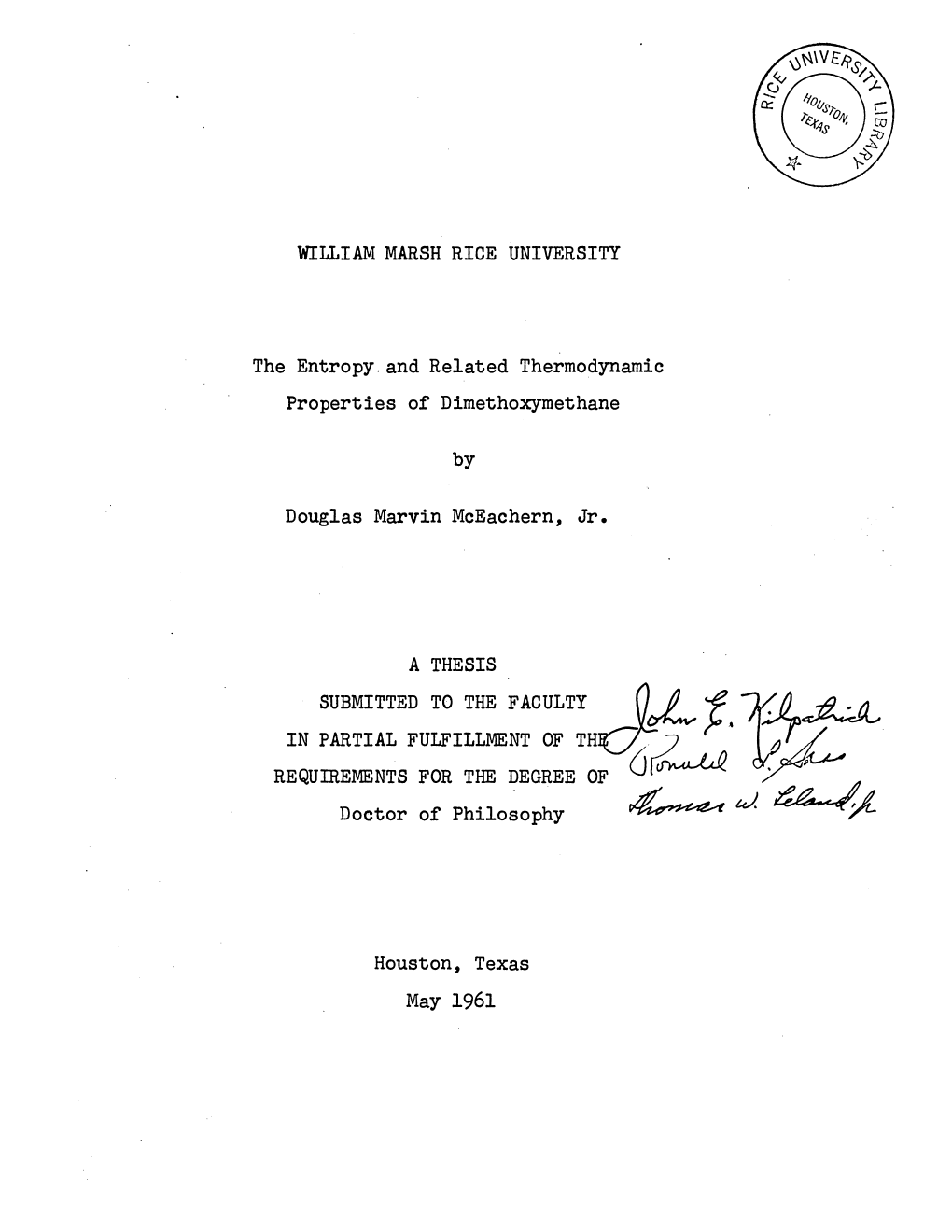
Load more
Recommended publications
-
Feas: Heat Capacity, Enthalpy Increments, Other Thermodynamic Properties from 5 to 1350 K, and Magnetic Transition A
M-2341 J. Chem. Thermodynumics 1989,21, 363-373 FeAs: Heat capacity, enthalpy increments, other thermodynamic properties from 5 to 1350 K, and magnetic transition a DOMINGO GONZALEZ-ALVAREZ, Fact&ad de Ciencias de la Universidad de Zaragoza, Departamento de Fisica Fundamental, 5009 Zaragoza, Spain FREDRIK GR0NVOLD, Chemical Institute, University of Oslo, Blindern, Oslo 3, Norway BENGT FALK,b EDGAR F. WESTRUM, JR., Department of Chemistry, University of Michigan, Ann Arbor, MI 48109, U.S.A. R. BLACHNIK,’ and G. KUDERMANNd Technical University, Siegen, Federal Republic of Germany (Received 2 January 1989) The heat capacity of iron monoarsenide has been determined by adiabatic calorimetry from 5 to 1030 K and bv drou calorimetrv relative to 298.15 K over the range 875 to 1350 K. A small h-type transition is observed at ?;, = (70.95 kO.02) K. It is related & the disappearance of a doubly helically ordered magnetic-spin structure on heating. The obviously cooperative entropy increment of transition is only A&JR = 0.021. The higher-temperature heat capacity rises considerably above lattice expectations. Part of the rise is ascribed to low-spin electron redistribution in iron, while the further excess above 800 K presumably arises from a beginning low- to high-spin transition, possibly connected with interstitial defect formation in the MnP- type structure. FeAs melts at about 1325 K with A,,,Hk=6180R.K. Thermodynamic functions have been evaluated and the values of C,,,(T), S:(T), H:(T), and @i(T), are 6.057R, 7.513R,1177R.K, and 3.567Rat 298.15 K, and 8.75R,16.03R, 6287R.K, and 9.74512at 1000 K. -
High Temperature Enthalpies of the Lead Halides
HIGH TEMPERATURE ENTHALPIES OF THE LEAD HALIDES: ENTHALPIES AND ENTROPIES OF FUSION APPROVED: Graduate Committee: Major Professor Committee Member Min fessor Committee Member X Committee Member UJ. Committee Member Committee Member Chairman of the Department of Chemistry Dean or the Graduate School HIGH TEMPERATURE ENTHALPIES OF THE LEAD HALIDES: ENTHALPIES AND ENTROPIES OF FUSION DISSERTATION Presented to the Graduate Council of the North Texas State University in Partial Fulfillment of the Requirements For the Degree of DOCTOR OF PHILOSOPHY By Clarence W, Linsey, B. S., M. S, Denton, Texas June, 1970 ACKNOWLEDGEMENT This dissertation is based on research conducted at the Oak Ridge National Laboratory, Oak Ridge, Tennessee, which is operated by the Uniofl Carbide Corporation for the U. S. Atomic Energy Commission. The author is also indebted to the Oak Ridge Associated Universities for the Oak Ridge Graduate Fellowship which he held during the laboratory phase. 11 TABLE OF CONTENTS Page LIST OF TABLES iv LIST OF ILLUSTRATIONS v Chapter I. INTRODUCTION . 1 Lead Fluoride Lead Chloride Lead Bromide Lead Iodide II. EXPERIMENTAL 11 Reagents Fusion-Filtration Method Encapsulation of Samples Equipment and Procedure Bunsen Ice Calorimeter Computer Programs Shomate Method Treatment of Data Near the Melting Point Solution Calorimeter Heat of Solution Calculations III. RESULTS AND DISCUSSION 41 Lead Fluoride Variation in Heat Contents of the Nichrome V Capsules Lead Chloride Lead Bromide Lead Iodide Summary BIBLIOGRAPHY ...... 98 in LIST OF TABLES Table Pa8e I. High-Temperature Enthalpy Data for Cubic PbE2 Encapsulated in Gold 42 II. High-Temperature Enthalpy Data for Cubic PbF2 Encapsulated in Molybdenum 48 III. -
THERMODYNAMIC EVALUATION of the Cu-Ti SYSTEM in VIEW of SOLID STATE AMORPHIZATION REACTIONS L
THERMODYNAMIC EVALUATION OF THE Cu-Ti SYSTEM IN VIEW OF SOLID STATE AMORPHIZATION REACTIONS L. Battezzati, M. Baricco, G. Riontino, I. Soletta To cite this version: L. Battezzati, M. Baricco, G. Riontino, I. Soletta. THERMODYNAMIC EVALUATION OF THE Cu- Ti SYSTEM IN VIEW OF SOLID STATE AMORPHIZATION REACTIONS. Journal de Physique Colloques, 1990, 51 (C4), pp.C4-79-C4-85. 10.1051/jphyscol:1990409. jpa-00230769 HAL Id: jpa-00230769 https://hal.archives-ouvertes.fr/jpa-00230769 Submitted on 1 Jan 1990 HAL is a multi-disciplinary open access L’archive ouverte pluridisciplinaire HAL, est archive for the deposit and dissemination of sci- destinée au dépôt et à la diffusion de documents entific research documents, whether they are pub- scientifiques de niveau recherche, publiés ou non, lished or not. The documents may come from émanant des établissements d’enseignement et de teaching and research institutions in France or recherche français ou étrangers, des laboratoires abroad, or from public or private research centers. publics ou privés. ~OLLOQUEDE PHYSIQUE Colloque C4, suppl6ment au 11'14, Tome 51, 15 juillet 1990 THERMODYNAMIC EVALUATION OF THE Cu-Ti SYSTEM IN VIEW OF SOLID STATE AMORPHIZATION REACTIONS L. BATTEZZATI* , M. BARICCO*~ *""" , G. RIONTINO" *"* and I. SOLETTA** * '~ipartimento di Chimica Inorganics, Chimica Fisica e Chimica dei Materiali, Universitd di Torino, Italy ""~stitutoElettrotecnico Nazionale Galileo Perraris, Torino, Italy *.* Dipartimento di Chimica, Universitd di Sassari, Italy *et* INPM, Unita' di Ricerca di Torino, Italy Resumk -La description thermodynamique du sist6me Cu-Ti est reconsideree, car les calculs he la littgrature, bien que donnant une bonne representation du diagramme de phase, ne prevoient pas la possibilit6 de l'amorphisation. -
National Fire Protection Association Report
National Fire Protection Association Report https://submittals.nfpa.org/TerraViewWeb/ContentFetcher?commentPar... Public Input No. 329-NFPA 99-2018 [ Global Input ] Create committee input to clarify differences between medical gases and medical support gases, particularly in sections 3.3.99, 3.3.100, 3.3.101, and 5.1.13.3.1. Statement of Problem and Substantiation for Public Input Potentially reduce requirements for medical support gases. Submitter Information Verification Submitter Full Name: Thomas Deary Organization: Compressed Gas Association Street Address: City: State: Zip: Submittal Date: Mon Jun 25 13:55:22 EDT 2018 Committee: HEA-PIP Committee Statement Resolution: The submitter did not provide any specific suggestion as to how to accomplish their request. 1 of 192 11/2/2018, 10:45 AM National Fire Protection Association Report https://submittals.nfpa.org/TerraViewWeb/ContentFetcher?commentPar... Public Input No. 129-NFPA 99-2018 [ Section No. 3.3.19.4 ] 3.3.19.4 Micro-Bulk Cryogenic System. An assembly of equipment including a container that is permanently installed through anchoring to a foundation, pressure regulators, pressure relief devices, vaporizers, manifolds, and interconnecting piping that is designed to be filled at the health care facility with a cryogenic gas, that has a storage capacity of less than or equal to 566 m 3 [20,000 ft 3 (scf)] of oxygen, including unconnected reserves on hand at the site, and that terminates at the source valve. Statement of Problem and Substantiation for Public Input Term is no longer used in NFPA 99 and is only found in the definitions section. Submitter Information Verification Submitter Full Name: Rob Early Organization: Compressed Gas Association Affiliation: NFPA 55/99 task group Street Address: City: State: Zip: Submittal Date: Sun Jun 03 19:48:44 EDT 2018 Committee: HEA-PIP Committee Statement Resolution: FR-909-NFPA 99-2018 Statement: Term is no longer used in NFPA 99 and is only found in the definitions section. -
The Resurgence Carbon Dioxide Calculator
The Resurgence Carbon Dioxide Calculator An on-line version of this calculator can be used at www.resurgence.org/carboncalculator/ This calculator is designed to make it easy to work out your personal annual carbon-dioxide emissions. You can print out this document, and fill in the tables using a pocket calculator, which is quite easy. What we are going to do is use your domestic fuel bills for a year, get your annual car mileage from your MOT certificate, and sum up your train and air travel in a way which is easy to estimate. You can then enter these pieces of information into the tables, which will calculate the CO2 emissions produced by each activity, and give you a sum total. In the following tables fill in the white boxes with your numbers. The boxes which contain a “0” need to be calculated using a pocket calculator. Simply follow the instructions in the title for that box, e.g. a x b = c. “/” means “divide-by”. Electricity On your electricity bills you will find the number of “units” you have used for each quarter, measured in kilo-Watt-hours (kWh). Enter these into the table below. If you have an electricity meter, enter the amount of money you put into it each week, on average. The table will multiply by 52 to get the cost per year, and then divide this by the cost per unit, currently 8.8p, to end up with the number of units used per year. Electricity bills Units Electricity meter £ 1st Quarter kWh Average cost per week 2nd Quarter kWh x Weeks per year 52 3rd Quarter kWh = Cost per year 0 4th Quarter kWh / cost per unit 0.09 kWh Total units per year 0 kWh = Total units per year 0 kWh x Conversion Factor 0.43 x Conversion Factor 0.43 = CO2 Emissions 0 kg = CO2 Emissions 0 kg Gas Piped gas is normally “natural gas”. -
Gas Alarm for Natural Or Bottled (LPG) Gas with Relay Output User's
1. DESCRIPTION The gas alarm is designed for single station use. Small and compact, the design and color makes it ideal for LK-GA502 use in the home, small commercial properties, and recreational vehicles. It is intended to detect leakage of Gas Detector natural gas (methane gas), town gas, and bottled gas (propane gas). The unit is designed for DC wire-in applications. The gas alarm can be mounted high (for methane gas) or low (for propane (LPG) gas). It is Gas Alarm for equipped with a sturdy metal mounting bracket for quick, easy, and secure installation. Natural or Bottled (LPG) Gas 2. FEATURES With Relay Output Detect all sorts of combustible gases, natural gas (methane), bottled gas (propane), LPG (Liquefied petroleum Gas), LNG (Liquefied natural gas), coal User’s Guide gas, including town gas. Easy to install, mounting bracket included. Loud 85dB alarm and LED warning light. High quality durable sensor. Self diagnostic function by MCU intelligent software. Excellent reliability & High stability. Ideal for all kitchens. 3. TECHNICAL SPECIFICATIONS Unit Dimensions: 103mm (D) x 55 mm (H) Color: Ceiling White Weight: 155g Operating Temperature: -10°C to +50°C Ambient Humidity: ≤95% RH Alarm Horn: 85dB at 3m (10 feet) Operating Voltage: DC9-28V Power Consumption: <1.5W (Standby), <5W (Alarm) For your convenience, Value of Detection Threshold (Lower Explosive Limit): write down the following information. Natural Gas: 7500ppm (15% LEL) If you call Us for Service, these are the first questions LPG: 2000PPM (10% LEL) Coal Gas: 800PPM (2% LEL) you will be asked. Method of Alarm: Flashing Red LED with 85dB alarm Gas Alarm Model Number (located on back of alarm): Warm Up Time: approximately 60 Seconds Alarm Output: Relay Output (N/O 2A@DC24V) Gas Alarm Assembly Number (Located on back of alarm): 4. -
Efficient Approach to Compute Melting Properties Fully from Ab Initio With
PHYSICAL REVIEW B 96, 224202 (2017) Efficient approach to compute melting properties fully from ab initio with application to Cu Li-Fang Zhu,* Blazej Grabowski, and Jörg Neugebauer Max-Planck-Institut für Eisenforschung GmbH, D-40237 Düsseldorf, Germany (Received 3 August 2017; revised manuscript received 16 October 2017; published 13 December 2017) Applying thermodynamic integration within an ab initio-based free-energy approach is a state-of-the-art method to calculate melting points of materials. However, the high computational cost and the reliance on a good reference system for calculating the liquid free energy have so far hindered a general application. To overcome these challenges, we propose the two-optimized references thermodynamic integration using Langevin dynamics (TOR-TILD) method in this work by extending the two-stage upsampled thermodynamic integration using Langevin dynamics (TU-TILD) method, which has been originally developed to obtain anharmonic free energies of solids, to the calculation of liquid free energies. The core idea of TOR-TILD is to fit two empirical potentials to the energies from density functional theory based molecular dynamics runs for the solid and the liquid phase and to use these potentials as reference systems for thermodynamic integration. Because the empirical potentials closely reproduce the ab initio system in the relevant part of the phase space the convergence of the thermodynamic integration is very rapid. Therefore, the proposed approach improves significantly the computational efficiency while preserving the required accuracy. As a test case, we apply TOR-TILD to fcc Cu computing not only the melting point but various other melting properties, such as the entropy and enthalpy of fusion and the volume change upon melting. -
NIST Workshop on Gas Sensors: Strategies for Future Technologies
United States Department of Commerce Technology Adm nistration National Institute of Standards and Technology NIST Special Publication 865 LI '.^^i^..^ NIST Workshop on Gas Sensors: Strategies for Future Technologies Proceedings of a Workshop Held in Gaithersburg, Maryland September 8-9, 1993 Steve Semancik, Editor QC 100 U57 NO. 865 1994 Jhe National Institute of Standards ana lecnnology was established in 1988 by Congress to "assist industry in the development of technology . needed to improve product quality, to modernize manufacmring processes, to ensure product reliability . and to facilitate rapid commercialization ... of products based on new scientific discoveries." NIST, originally founded as the National Bureau of Standards in 1901, works to strengthen U.S. industry's competitiveness; advance science and engineering; and improve public health, safety, and the environment. One of the agency's basic functions is to develop, maintain, and retain custody of the national standards of measurement, and provide the means and methods for comparing standards used in science, engineering, manufacturing, commerce, industry, and education with the standards adopted or recognized by the Federal Government. As an agency of the U.S. Commerce Department's Technology Administration, NIST conducts basic and applied research in the physical sciences and engineering, and develops measurement techniques, test methods, standards, and related services. The Institute does generic and precompetitive work on new and advanced technologies. NIST's research -
Bottled Biogas—An Opportunity for Clean Cooking in Ghana and Uganda
energies Article Bottled Biogas—An Opportunity for Clean Cooking in Ghana and Uganda Mairi J. Black 1, Amitava Roy 2, Edson Twinomunuji 3 , Francis Kemausuor 4, Richard Oduro 1 , Matthew Leach 1,*, Jhuma Sadhukhan 1 and Richard Murphy 1 1 Centre for Environment and Sustainability, University of Surrey, Guildford GU2 7XH, UK; [email protected] (M.J.B.); [email protected] (R.O.); [email protected] (J.S.); [email protected] (R.M.) 2 Engas UK Ltd., Horsham RH13 5JZ, UK; [email protected] 3 Uganda Cleaner Production Centre, P.O. Box 69 Kyambogo, Kampala, Uganda; [email protected] 4 The Brew-Hammond Energy Centre, Kwame Nkrumah University of Science and Technology, Kumasi AK-039-5028, Ghana; [email protected] * Correspondence: [email protected] Abstract: Anaerobic digestion (AD) can bring benefits in terms of effective management of organic waste, recovery of nutrients and energy recovery, and is consistent with circular economy principles. AD has been promoted and implemented worldwide, but at widely differing scales, influenced by the availability and location of feedstocks. In developing countries, feedstock arises from small- to medium-scale agriculture and agro-processing operations, as well as from household and municipal waste. Biogas produced from residues from agro-processing facilities may be used for on-site heat and power, but the lack of a gas and electricity grid infrastructure can limit opportunities to distribute gas or generated electricity to wider users. This paper presents the findings of the first study to consider Citation: Black, M.J.; Roy, A.; novel technologies for small-scale and low-cost biogas clean-up into biomethane, and compression Twinomunuji, E.; Kemausuor, F.; into small bottles, suitable as a clean cooking fuel. -
Green Goods and Services Sorted by Inclusion-March 2010
BUREAU OF LABOR STATISTICS Green Goods and Services Industries by Inclusion For Public Comment (Federal Register Notice): 3/15/2010 LEGEND: Categories of green economic activity: Definition Elements: Y: Included 1. Renewable energy 5. Recycling and waste reduction 1. Direct green good or service N: Excluded 2. Energy efficiency 6. Agricultural and natural resources conservation 2. Indirect green good or service 3. Greenhouse gas reduction 7. Education, compliance, public awareness, and training 3. Specialized input to elements 1 or 2 4. Pollution reduction and cleanup 4. Distribution of green goods Category of green Definition NAICS 2007 Title Included economic elements Example of green good or service activity (1-4) (1-7) 111110 Soybean farming Y 6 2 USDA certified organic produce, soybeans for biodiesel 111120 Oilseed, except soybean, farming Y 6 2 USDA certified organic produce 111130 Dry pea and bean farming Y 6 2 USDA certified organic produce 111140 Wheat farming Y 6 2 USDA certified organic produce 111150 Corn farming Y 6 2 USDA certified organic produce, growing corn for ethanol 111160 Rice farming Y 6 2 USDA certified organic produce 111191 Oilseed and grain combination farming Y 6 2 USDA certified organic produce 111199 All other grain farming Y 6 2 USDA certified organic produce, growing sorghum for ethanol 111211 Potato farming Y 6 2 USDA certified organic produce 111219 Other vegetable and melon farming Y 6 2 USDA certified organic produce 111310 Orange groves Y 6 2 USDA certified organic produce 111320 Citrus, except orange, -
Download Nitrogen Generation Datasheet
NITROGEN SYSTEMS Submarine Manufacturing & Products Limited Manufacturer of Commercial Diving, Medical Hyperbaric Applications and Military Subsea & Emergency Rescue Solutions. Nano Nitrogen Generator This technologically advanced nitrogen generator operates on the Pressure Swing Adsorption (PSA) principle to produce a continuous uninterrupted stream of nitrogen gas from clean dry compressed air. Dual chamber extruded aluminum columns are filled with Carbon Molecular Sieve (CMS). Joined via an upper and lower manifold, the high density filled columns produce a dual bed system. After a preset time the control system automatically switches the beds. One bed is always online generating nitrogen while the other is being regenerated. During regeneration, the oxygen that has been collected in the CMS stage is exhausted to atmosphere. A small portion of the outlet nitrogen gas is expanded into the bed to accelerate the regeneration process. About our Nitrogen Generation Systems General Specifications Benefits SMP offer Nitrogen generation systems that are bespoke to the client’s needs. The systems are customised • Design operating pressure • Maximum inlet oil content: • 100% function and performance range: 6 - 12 barg 0.01 ppm tested at our factory to work within a defined space. • Design operating temp. range: • Recommended inlet dew • Significant cost savings over cylinder 5 - 50°C point: -40°C PDP or liquid supply Nitrogen generators produce nitrogen gas from compressed air and offer a cost effective, reliable and safe • Recommended operating • Supply voltage: 100-240 VAC • ecomode energy savings control alternative to traditional nitrogen gas supplies such as cylinder or liquid. Nitrogen generators are available temp.: 5 - 25°C (50 or 60Hz) reduces energy consumption during in 20 standard models with capacity in the range from 1 - 1800Nm³/hour from 95% to 99.9995% purity. -
Thermodynamic Properties of Solid and Liquid Ethylbenzene from 0 to 300 Degrees K
U. S. DEPARTMENT OF COMMERCE NATIONAL BUREAU OF STANDARDS RESEARCH PAPER RP1684 Part of Journal of Research of the National Bureau of Standards, Volume 35, December 1945 THERMODYNAMIC PROPERTIES OF SOLID AND LIQUID ETHYLBENZENE FROM 0° TO 300° K By Russell B. Scott and Ferdinand C. Brickwedde ABSTRACT The following properties of a sample of high purity ethylbenzene were measured: (1) Specific heat of solid and liquid from 15 0 to 3000 Ie; (2) triple-point tempera ture (-95.005 ±0.01O° C for pure ethyl benzene) ; (3) heat of fusion (86.47 into i g -1); (4) heat of vaporization at 2940 Ie (400.15 into j g -1); and (5) vapor pres sure from 273 0 to 296 0 Ie. With these experimental data, the enthalpy and entropy of the solid and of the liquid in the range 0 0 to 3000 Ie were calculated. CONTENTS Page I. Introduction ______ ____ ___ _____ _______ ____________ ___________ __ 501 II. Purification of the sample_ _ _ _ _ _ _ _ _ _ _ _ _ _ _ _ _ _ _ _ _ _ _ _ _ _ _ _ _ _ _ _ _ _ _ _ __ _ 502 III. Calorimetric measurements _____ _________ _______ __ ______ _____ ____ 502 1. Apparatus ________________ __ __ __________________ _______ _ 502 2. Specific heat of solid and liquid ___ _____________ ________ ___ 503 3. Heat of fusion and triple-point temperature ___ _______ ______ _ 505 4. Heat of vaporization ____ ___ ____ _______ _______ ____ ___ ___ __ 506 IV.