Mechanical Characterisation of Novel Polyethylene Nanocomposites by Nanoindentation
Total Page:16
File Type:pdf, Size:1020Kb
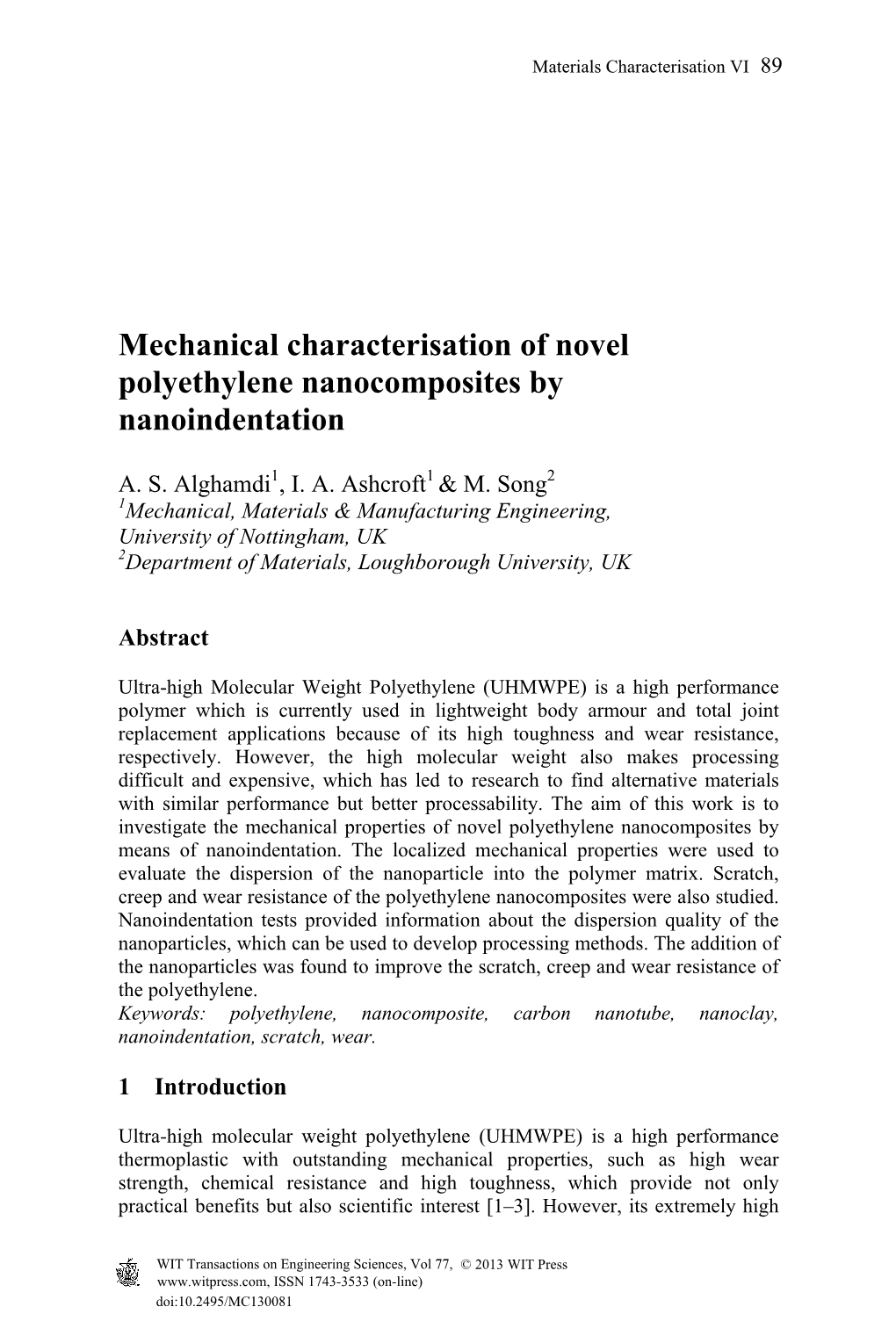
Load more
Recommended publications
-
Nanoindentations in Kinking Nonlinear Elastic Solids
Nanoindentations in Kinking Nonlinear Elastic Solids A Thesis Submitted to the Faculty of Drexel University by Anand Murugaiah in partial fulfillment of the requirements for the degree of Doctor of Philosophy May 2004 ii ACKNOWLEDGMENTS I am very grateful to a lot of people who were instrumental in my studies at Drexel University. First, I would like to thank my advisors, Dr. Michel W. Barsoum and Dr. Surya Kalidindi for their help, guidance, support and patience during trying times. I have learnt so much under their tutelage. They have been there always to correct me, guide me, motivate me and work with me. I am truly fortunate to have them as my advisors. I am grateful to Dr. Tamer El-Raghy for his help and guidance during my research. I am very thankful to my thesis committee: Prof. Yury Gogotsi, Dr. David Stepp (Army Research Labs) and Dr. El-Raghy for their time, help and assistance in helping me complete my work. I also would like to thank the Department of Materials Science and Engineering, the faculty, staff and my dear colleagues for their support and those wonderful moments that I shared with them. I would like to thank my family and friends for being there for me when I needed them. I would like to thank Prof. Y. Gogotsi again for many stimulating and useful discussions and Mr. Thomas F. Juliano, for his help with the nanoindenter. I am also grateful to Dr. T. El-Raghy of 3-ONE-2 LLC for supplying the Ti3SiC2 samples. The graphite single crystals were provided by Prof. -
Operando Nanoindentation
A3840 Journal of The Electrochemical Society, 164 (14) A3840-A3847 (2017) Operando Nanoindentation: A New Platform to Measure the Mechanical Properties of Electrodes during Electrochemical Reactions Luize Scalco de Vasconcelos, Rong Xu, and Kejie Zhao∗,z School of Mechanical Engineering, Purdue University, West Lafayette, Indiana 47907, USA We present an experimental platform of operando nanoindentation that probes the dynamic mechanical behaviors of electrodes during real-time electrochemical reactions. The setup consists of a nanoindenter, an electrochemical station, and a custom fluid cell integrated into an inert environment. We evaluate the influence of the argon atmosphere, electrolyte solution, structural degradation and volumetric change of electrodes upon Li reactions, as well as the surface layer and substrate effects by control experiments. Results inform on the system limitations and capabilities, and provide guidelines on the best experimental practices. Furthermore, we present a thorough investigation of the elastic-viscoplastic properties of amorphous Si electrodes, during cell operation at different C-rates and at open circuit. Pure Li metal is characterized separately. We measure the continuous evolution of the elastic modulus, hardness, and creep stress exponent of lithiated Si and compare the results with prior reports. operando indentation will provide a reliable platform to understand the fundamental coupling between mechanics and electrochemistry in energy materials. © The Author(s) 2017. Published by ECS. This is an open access article distributed under the terms of the Creative Commons Attribution 4.0 License (CC BY, http://creativecommons.org/licenses/by/4.0/), which permits unrestricted reuse of the work in any medium, provided the original work is properly cited. -
Nanoindentation Technique for Characterizing Cantilever Beam Style RF Microelectromechanical Systems (MEMS) Switches Hyukjae Lee Air Force Institute of Technology
Marquette University e-Publications@Marquette Electrical and Computer Engineering Faculty Electrical and Computer Engineering, Department Research and Publications of 4-29-2005 Nanoindentation Technique for Characterizing Cantilever Beam Style RF Microelectromechanical Systems (MEMS) Switches Hyukjae Lee Air Force Institute of Technology Ronald A. Coutu Jr. Marquette University, [email protected] Shankar Mall Air Force Institute of Technology Paul E. Kladitis Air Force Institute of Technology Accepted version. Journal of Micromechanics and Microengineering, Vol. 15, No. 6 (April 29, 2006): 1230. DOI. © 2006 IOP Publishing. Used with permission. Ronald A Coutu Jr. Sensors Directorate, Air Force Research Laboratory, Wright-Patterson Air Force Base, OH at the time of publication. Marquette University e-Publications@Marquette Electrical and Computer Engineering Faculty Research and Publications/College of Engineering This paper is NOT THE PUBLISHED VERSION; but the author’s final, peer-reviewed manuscript. The published version may be accessed by following the link in the citation below. Journal of Micromechanics and Microengineering, Vol. 15, No. 6, (April, 2005): 1230-1235. DOI. This article is © Institute of Physics and permission has been granted for this version to appear in e-Publications@Marquette. Institute of Physics does not grant permission for this article to be further copied/distributed or hosted elsewhere without the express permission from Institute of Physics. Contents Abstract ........................................................................................................................................................ -
Mechanical Properties of Nanoparticles: Characterization By
Mechanical Properties of Nanoparticles: Characterization by In situ Nanoindentation Inside a Transmission Electron Microscope Lucile Joly-Pottuz, Emilie Calvié, Julien Réthoré, Sylvain Meille, Claude Esnouf, Jérome Chevalier, Karine Masenelli-Varlot To cite this version: Lucile Joly-Pottuz, Emilie Calvié, Julien Réthoré, Sylvain Meille, Claude Esnouf, et al.. Mechani- cal Properties of Nanoparticles: Characterization by In situ Nanoindentation Inside a Transmission Electron Microscope. Mahmood Aliofkhazraei. Handbook of Mechanical Nanostructuring, Wiley, pp.163-180, 2015, 9783527335060. 10.1002/9783527674947.ch8. hal-01670827 HAL Id: hal-01670827 https://hal.archives-ouvertes.fr/hal-01670827 Submitted on 22 Feb 2021 HAL is a multi-disciplinary open access L’archive ouverte pluridisciplinaire HAL, est archive for the deposit and dissemination of sci- destinée au dépôt et à la diffusion de documents entific research documents, whether they are pub- scientifiques de niveau recherche, publiés ou non, lished or not. The documents may come from émanant des établissements d’enseignement et de teaching and research institutions in France or recherche français ou étrangers, des laboratoires abroad, or from public or private research centers. publics ou privés. Distributed under a Creative Commons Attribution| 4.0 International License Mechanical Properties of Nanoparticles: Characterization by In situ Nanoindentation Inside a Transmission Electron Microscope Lucile Joly-Pottuz, Emilie Calvié, Julien Réthoré, Sylvain Meille, Claude Esnouf, Jérôme -
Influences of Sample Preparation on the Indentation Size Effect and Nanoindentation Pop-In on Nickel
University of Tennessee, Knoxville TRACE: Tennessee Research and Creative Exchange Doctoral Dissertations Graduate School 5-2012 Influences of sample preparation on the indentation size effect and nanoindentation pop-in on nickel Zhigang Wang Department of Materials Science & Engineering, [email protected] Follow this and additional works at: https://trace.tennessee.edu/utk_graddiss Part of the Materials Science and Engineering Commons Recommended Citation Wang, Zhigang, "Influences of sample preparation on the indentation size effect and nanoindentation pop- in on nickel. " PhD diss., University of Tennessee, 2012. https://trace.tennessee.edu/utk_graddiss/1371 This Dissertation is brought to you for free and open access by the Graduate School at TRACE: Tennessee Research and Creative Exchange. It has been accepted for inclusion in Doctoral Dissertations by an authorized administrator of TRACE: Tennessee Research and Creative Exchange. For more information, please contact [email protected]. To the Graduate Council: I am submitting herewith a dissertation written by Zhigang Wang entitled "Influences of sample preparation on the indentation size effect and nanoindentation pop-in on nickel." I have examined the final electronic copy of this dissertation for form and content and recommend that it be accepted in partial fulfillment of the equirr ements for the degree of Doctor of Philosophy, with a major in Materials Science and Engineering. George Pharr, Major Professor We have read this dissertation and recommend its acceptance: George Pharr, Robert Mee, Yanfei Gao, Erik Herbert Accepted for the Council: Carolyn R. Hodges Vice Provost and Dean of the Graduate School (Original signatures are on file with official studentecor r ds.) INFLUENCES OF SAMPLE PREPARATION ON THE INDENTATION SIZE EFFECT & NANOINDENTATION POP-IN IN NICKEL A Dissertation Presented for the Doctor of Philosophy Degree The University of Tennessee, Knoxville Zhigang Wang May 2012 Copyright © 2012 by Zhigang Wang. -
Examination of Deformation in Magnesium Using Instrumented Spherical Indentation
EXAMINATION OF DEFORMATION IN MAGNESIUM USING INSTRUMENTED SPHERICAL INDENTATION by Ghazal Nayyeri B.Sc., University of Tehran, 2007 M.Sc., University of Tehran, 2009 A THESIS SUBMITTED IN PARTIAL FULFILLMENT OF THE REQUIREMENTS FOR THE DEGREE OF DOCTOR OF PHILOSOPHY in THE FACULTY OF GRADUATE AND POSTDOCTORAL STUDIES (Materials Engineering) THE UNIVERSITY OF BRITISH COLUMBIA (Vancouver) April 2016 © Ghazal Nayyeri, 2016 Abstract This investigation examines the use of instrumented indentation to extract information on the deformation behaviour of commercial purity magnesium, AZ31B (Mg-2.5Al-0.7Zn), and AZ80 (Mg-8Al-0.5Zn). In particular, indentation was conducted with spherical indenter using a range of spherical indenter tip radii of R = 1 m to 250.0 m. A detailed examination has been conducted for the load-displacement data combined with three-dimensional electron backscatter diffraction (3D EBSD) characterization of the deformation zone under the indenter after the load has been removed. It was proposed that the initial deviation of the load-depth data from the elastic solution of Hertz is associated with the point when the critical resolved shear stress (CRSS) for basal slip is reached. Also, it was observed that reproducible large discontinuities could be found in the loading and the unloading curves. It is proposed that these discontinuities are related to the nucleation and growth of {101̅2} extension twins during loading and their subsequent retreat during unloading. For the case of c-axis indentation, 3D EBSD studies showed that the presence of residual deformation twins depended on the depth of the indent. Further, a detailed analysis of the residual geometrically necessary dislocation populations in the deformation zone was conducted based on the EBSD data. -
Nanoindentation and Atomic Force Microscopy Measurements on Reactively Sputtered Tin Coatings
CORE Metadata, citation and similar papers at core.ac.uk Provided by NAL-IR Bull. Mater. Sci., Vol. 27, No. 1, February 2004, pp. 35–41. © Indian Academy of Sciences. Nanoindentation and atomic force microscopy measurements on reactively sputtered TiN coatings HARISH C BARSHILIA and K S RAJAM* Surface Engineering Division, National Aerospace Laboratories, Bangalore 560 017, India MS received 19 February 2003; revised 29 December 2003 Abstract. Titanium nitride (TiN) coatings were deposited by d.c. reactive magnetron sputtering process. The films were deposited on silicon (111) substrates at various process conditions, e.g. substrate bias voltage (VB) and nitrogen partial pressure. Mechanical properties of the coatings were investigated by a nanoindentation technique. Force vs displacement curves generated during loading and unloading of a Berkovich diamond in- denter were used to determine the hardness (H) and Young’s modulus (Y) of the films. Detailed investigations on the role of substrate bias and nitrogen partial pressure on the mechanical properties of the coatings are presented in this paper. Considerable improvement in the hardness was observed when negative bias voltage 2 was increased from 100–250 V. Films deposited at |VB| = 250 V exhibited hardness as high as 3300 kg/mm . This increase in hardness has been attributed to ion bombardment during the deposition. The ion bombard- ment considerably affects the microstructure of the coatings. Atomic force microscopy (AFM) of the coatings revealed fine-grained morphology for the films prepared at higher substrate bias voltage. The hardness of the coatings was found to increase with a decrease in nitrogen partial pressure. -
Analysis of Nano Indentation Size Effect Based on Dislocation Dynamics and Crystal Plasticity H.J
Analysis of Nano indentation Size effect based on Dislocation Dynamics and Crystal Plasticity H.J. Chang To cite this version: H.J. Chang. Analysis of Nano indentation Size effect based on Dislocation Dynamics and Crystal Plasticity. Chemical and Process Engineering. Institut National Polytechnique de Grenoble - INPG, 2009. English. tel-00526500 HAL Id: tel-00526500 https://tel.archives-ouvertes.fr/tel-00526500 Submitted on 15 Oct 2010 HAL is a multi-disciplinary open access L’archive ouverte pluridisciplinaire HAL, est archive for the deposit and dissemination of sci- destinée au dépôt et à la diffusion de documents entific research documents, whether they are pub- scientifiques de niveau recherche, publiés ou non, lished or not. The documents may come from émanant des établissements d’enseignement et de teaching and research institutions in France or recherche français ou étrangers, des laboratoires abroad, or from public or private research centers. publics ou privés. INSTITUT POLYTECHNIQUE DE GRENOBLE N° attribué par la bibliothèque |__|__|__|__|__|__|__|__|__|__| THESE EN COTUTELLE INTERNATIONALE pour obtenir le grade de DOCTEUR DE L’Institut polytechnique de Grenoble et de Seoul National University Spécialité : 2MGE : Matériaux, Mécanique, Génie civil, Electrochimie préparée au laboratoire Science et Ingénierie des Matériaux et des Procédés (SIMaP) Groupe Génie Physique et Mécanique des Matériaux (GPM2) dans le cadre de l’Ecole Doctorale I-MEP2 et au laboratoire Material Deformation and Processing (LMDP) dans la Seoul National Université présentée et soutenue publiquement par Hyung-Jun CHANG le 15 Juin 2009 TITRE : Analysis of Nano indentation Size effect based on Dislocation Dynamics and Crystal Plasticity Sous la direction de : Marc FIVEL, Laurent TABOUROT et Marc VERDIER JURY M. -
An Atomic Force Microscopy Nanoindentation Study of Size Effects in Face-Centered Cubic Metal and Bimetallic Nanowires Erin Leigh Wood University of Vermont
University of Vermont ScholarWorks @ UVM Graduate College Dissertations and Theses Dissertations and Theses 2014 An Atomic Force Microscopy Nanoindentation Study of Size Effects in Face-Centered Cubic Metal and Bimetallic Nanowires Erin Leigh Wood University of Vermont Follow this and additional works at: https://scholarworks.uvm.edu/graddis Part of the Mechanical Engineering Commons, Mechanics of Materials Commons, and the Nanoscience and Nanotechnology Commons Recommended Citation Wood, Erin Leigh, "An Atomic Force Microscopy Nanoindentation Study of Size Effects in Face-Centered Cubic Metal and Bimetallic Nanowires" (2014). Graduate College Dissertations and Theses. 260. https://scholarworks.uvm.edu/graddis/260 This Dissertation is brought to you for free and open access by the Dissertations and Theses at ScholarWorks @ UVM. It has been accepted for inclusion in Graduate College Dissertations and Theses by an authorized administrator of ScholarWorks @ UVM. For more information, please contact [email protected]. AN ATOMIC FORCE MICROSCOPY NANOINDENTATION STUDY OF SIZE EFFECTS IN FACE-CENTERED CUBIC METAL AND BIMETALLIC NANOWIRES A Dissertation Presented by Erin Leigh Wood to The Faculty of the Graduate College of The University of Vermont In Partial Fulfillment of the Requirements for the Degree of Doctor of Philosophy Specializing in Mechanical Engineering October, 2014 Accepted by the Faculty of the Graduate College, The University of Vermont, in partial fulfillment of the requirements for the degree of Doctor of Philosophy specializing in Mechanical Engineering Dissertation Examination Committee: ____________________________________ Advisor Frederic Sansoz, Ph.D. ____________________________________ Dryver Huston, Ph.D. ____________________________________ Rachael Oldinski, Ph.D. ____________________________________ Chairperson John Hughes, Ph. D. ____________________________________ Dean, Graduate College Cynthia Forehand, Ph.D. -
Measuring the Elastic Modulus of Polymers Using the Atomic Force Microscope
Michigan Technological University Digital Commons @ Michigan Tech Dissertations, Master's Theses and Master's Dissertations, Master's Theses and Master's Reports - Open Reports 2010 Measuring the elastic modulus of polymers using the atomic force microscope Daniel Hoffman Michigan Technological University Follow this and additional works at: https://digitalcommons.mtu.edu/etds Part of the Engineering Science and Materials Commons Copyright 2010 Daniel Hoffman Recommended Citation Hoffman, Daniel, "Measuring the elastic modulus of polymers using the atomic force microscope", Master's Thesis, Michigan Technological University, 2010. https://doi.org/10.37099/mtu.dc.etds/27 Follow this and additional works at: https://digitalcommons.mtu.edu/etds Part of the Engineering Science and Materials Commons Measuring the Elastic Modulus of Polymers using the Atomic Force Microscope By Daniel Hoffman A THESIS Submitted in partial fulfillment for the degree of MASTER OF SCIENCE IN MATERIALS SCIENCE AND ENGINEERING MICHIGAL TECHNOLOGICAL UNIVERSITY 2010 © 2010 Dan Hoffman This thesis, “Measuring the Elastic Modulus of Polymers using the Atomic Force Microscope,” is hereby approved in partial fulfillment of the requirements for the Degree of MASTER OF SCIENCE IN MATERIALS SCIENCE AND ENGINEERING. Department of Materials Science and Engineering Signatures: Thesis Advisor Jaroslaw Drelich Department Chair Mark Plichta Date 2 Table of Contents Acknowledgements ...........................................................................................................4 -
Low Temperature Nanoindentation: Development and Applications
micromachines Review Low Temperature Nanoindentation: Development and Applications Shunbo Wang 1 and Hongwei Zhao 1,2,* 1 School of Mechanical and Aerospace Engineering, Jilin University, Changchun 130025, China; [email protected] 2 Key Laboratory of CNC Equipment Reliability, Ministry of Education, Changchun 130025, China * Correspondence: [email protected]; Tel.: +86-0431-85095757 Received: 15 March 2020; Accepted: 30 March 2020; Published: 13 April 2020 Abstract: Nanoindentation technique at low temperatures have developed from initial micro-hardness driving method at a single temperature to modern depth-sensing indentation (DSI) method with variable temperatures over the last three decades. The technique and implementation of representative cooling systems adopted on the indentation apparatuses are discussed in detail here, with particular emphasis on pros and cons of combination with indentation technique. To obtain accurate nanoindentation curves and calculated results of material properties, several influence factors have been carefully considered and eliminated, including thermal drift and temperature induced influence on indenter and specimen. Finally, we further show some applications on typical materials and discuss the perspectives related to low temperature nanoindentation technique. Keywords: low temperature; nanoindentation; hardness test; apparatus; mechanical properties 1. Introduction Nanoindentation technique has become one of the most popular mechanical property testing methods in recent years [1–5]. Compared with uniaxial tension and compression tests, the specimen requirements of nanoindentation were more simplified: a flat, no shape required surface. The mechanical properties, including but not limited to hardness and elastic modulus, can be obtained automatically via commercial system using Hertz contact theory [6] and Oliver-Pharr analysis method [7]. -
Characterization of Ferroelasticity in Rare-Earth Orthophosphates by Nanoindentation
CHARACTERIZATION OF FERROELASTICITY IN RARE-EARTH ORTHOPHOSPHATES BY NANOINDENTATION by Taylor M. Wilkinson A thesis submitted to the Faculty and the Board of Trustees of the Colorado School of Mines in partial fulfillment of the requirements for the degree of Doctor of Philosophy (Materials Science). Golden, Colorado Date _________________________ Signed: __________________________________ Taylor M. Wilkinson Signed: __________________________________ Dr. Corinne E. Packard Thesis Advisor Golden, Colorado Date _________________________ Signed: _________________________ Dr. Ryan P. O’Hayre Professor and Program Head Materials Science Program ii ABSTRACT Superelasticity, or the rubber-like effect, describes the phenomenon of a material being able to ‘recover’ after an external strain, beyond the elastic limit, is removed. This behavior has been exhibited by shape memory alloys, as well as the emerging materials field of shape memory ceramics, and may be caused by the material undergoing deformation mechanisms such as phase transformation or twinning/detwinning – also known as ferroelasticity. Superelastic materials are known to be attractive candidates for shape memory materials as well as applications with actuating, sensing, and damping needs. Rare-earth orthophosphates are a group of ceramics that are known to exhibit incredible flexibility with lanthanide element substitution as well as high resistance to chemical and thermal degradation. These materials have also been shown to undergo both of the deformation mechanisms associated with superelasticity. Nanoindentation is a promising technique for studying superelasticity due to its ability to run large-scale experimental matrices and the fact that the technique is highly sensitive and therefore able to pick up even the smallest amounts of recovery. Pioneer indentation testing of several rare-earth orthophosphates near the monazite/xenotime boundary has shown indentation recovery as a slope change that occurs during the unloading portion of test.