Thermal Operability Improvements for the Mars 2020 Rover Surface Mission
Total Page:16
File Type:pdf, Size:1020Kb
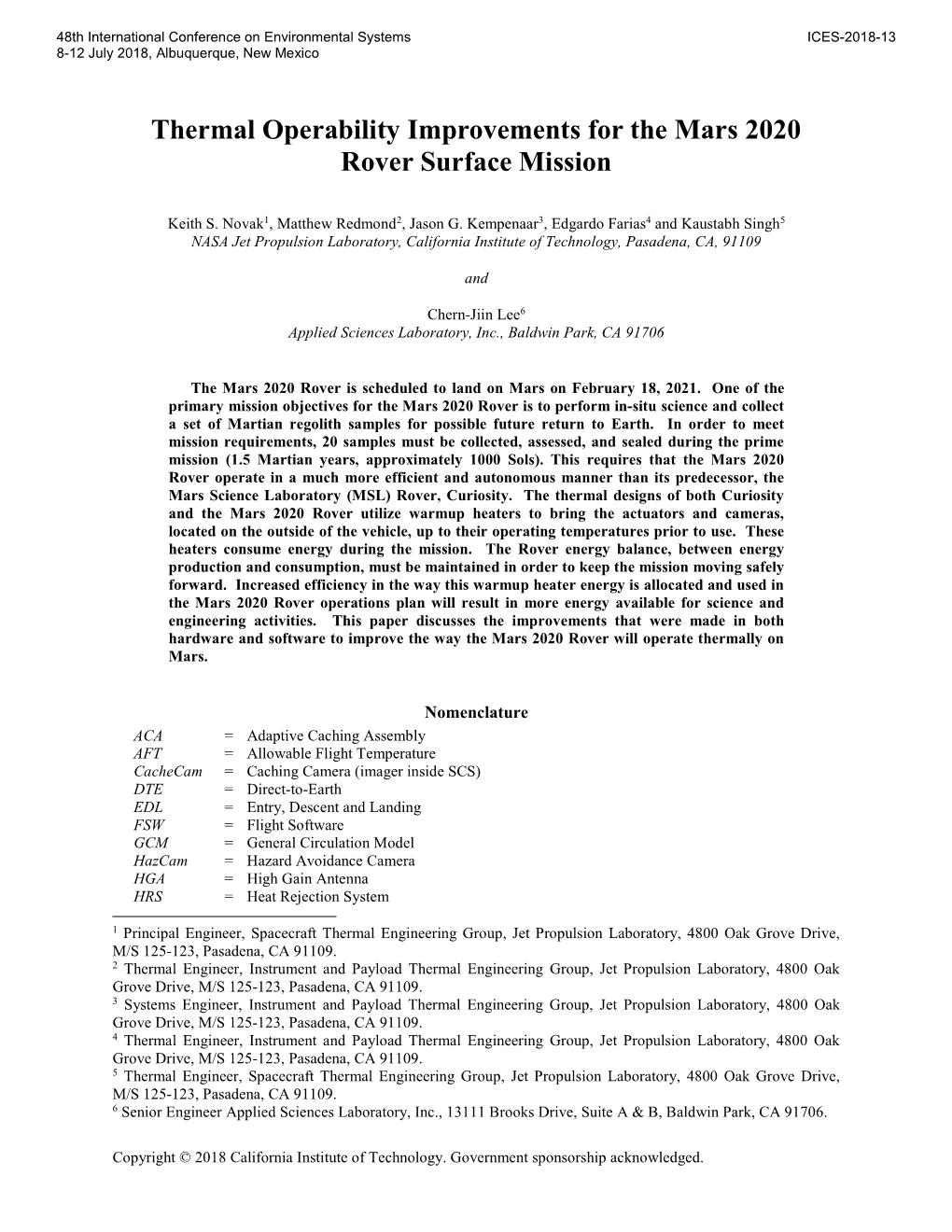
Load more
Recommended publications
-
Mars Reconnaissance Orbiter
Chapter 6 Mars Reconnaissance Orbiter Jim Taylor, Dennis K. Lee, and Shervin Shambayati 6.1 Mission Overview The Mars Reconnaissance Orbiter (MRO) [1, 2] has a suite of instruments making observations at Mars, and it provides data-relay services for Mars landers and rovers. MRO was launched on August 12, 2005. The orbiter successfully went into orbit around Mars on March 10, 2006 and began reducing its orbit altitude and circularizing the orbit in preparation for the science mission. The orbit changing was accomplished through a process called aerobraking, in preparation for the “science mission” starting in November 2006, followed by the “relay mission” starting in November 2008. MRO participated in the Mars Science Laboratory touchdown and surface mission that began in August 2012 (Chapter 7). MRO communications has operated in three different frequency bands: 1) Most telecom in both directions has been with the Deep Space Network (DSN) at X-band (~8 GHz), and this band will continue to provide operational commanding, telemetry transmission, and radiometric tracking. 2) During cruise, the functional characteristics of a separate Ka-band (~32 GHz) downlink system were verified in preparation for an operational demonstration during orbit operations. After a Ka-band hardware anomaly in cruise, the project has elected not to initiate the originally planned operational demonstration (with yet-to-be used redundant Ka-band hardware). 201 202 Chapter 6 3) A new-generation ultra-high frequency (UHF) (~400 MHz) system was verified with the Mars Exploration Rovers in preparation for the successful relay communications with the Phoenix lander in 2008 and the later Mars Science Laboratory relay operations. -
A Lunar Micro Rover System Overview for Aiding Science and ISRU Missions Virtual Conference 19–23 October 2020 R
i-SAIRAS2020-Papers (2020) 5051.pdf A lunar Micro Rover System Overview for Aiding Science and ISRU Missions Virtual Conference 19–23 October 2020 R. Smith1, S. George1, D. Jonckers1 1STFC RAL Space, R100 Harwell Campus, OX11 0DE, United Kingdom, E-mail: [email protected] ABSTRACT the form of rovers and landers of various size [4]. Due to the costly nature of these missions, and the pressure Current science missions to the surface of other plan- for a guaranteed science return, they have been de- etary bodies tend to be very large with upwards of ten signed to minimise risk by using redundant and high instruments on board. This is due to high reliability re- reliability systems. This further increases mission cost quirements, and the desire to get the maximum science as components and subsystems are expected to be ex- return per mission. Missions to the lunar surface in the tensively qualified. next few years are key in the journey to returning hu- mans to the lunar surface [1]. The introduction of the As an example, the Mars Science Laboratory, nick- Commercial lunar Payload Services (CLPS) delivery named the Curiosity rover, one of the most successful architecture for science instruments and technology interplanetary rovers to date, has 10 main scientific in- demonstrators has lowered the barrier to entry of get- struments, requires a large team of people to control ting science to the surface [2]. Many instruments, and and cost over $2.5 billion to build and fly [5]. Curios- In Situ Surface Utilisation (ISRU) experiments have ity had 4 main science goals, with the instruments and been funded, and are being built with the intention of the design of the rover specifically tailored to those flying on already awarded CLPS missions. -
2008 60 Pages 3.8 MB
Illustrations Key: Five of the most interesting articles this publica- tion year, (see the five illustrations at right) were on: • The Concept of “World” from flat to round to the realm of human activity “wherever” • “Assuring Mental Health among Future Lunar Pioneers” • “Railroading on Mars” • “Bursting Apollo’s Envelope” and • The Moon’s Remarkable “Alpine Valley.” Other articles of note include: • “Thinking Outside the Mass Fraction Box” (we have handicapped our options for space transpor- tation because of slavery to an unexamined assum- ption dating from Penemunde! • MMM’s “Platform for Mars 2.0” and other articles on Mars in our annual “March is for Mars” theme issue • Aspects of an Early Lunar Community • Taking the Green Movement to the Moon (several articles); • Hewn Basalt Products • Saddlebag Shielding for Vertical Habitats • Shadow Pioneers (Earthbound teleoperators) • Distance limits to tele-conversation • Does it rally take more fuel to land on the Moon than on Mars as Robert Zubrin claims? • A major article series by Dave Dietzler focuses on “LUNAR ENTERPRISE & OPPORTUNITY Parts 1-4 • The “Mother Earth & Father Sky” article touched again on the green themes. • Gordon Haverland contributed a critique on the options for “Engineering on the Moon and Beyond with local materials. • The tragedy of discarding of External Tanks, was touched on again: something MMM has opposed from the very beginning. In Addition There were a number of Book Reviews We do not preplan the article spread in any publication year. Some topics are revisited more often than others. It all depends on the inspirations of the contributing authors. -
Moon-Miners-Manifesto-Mars.Pdf
http://www.moonsociety.org/mars/ Let’s make the right choice - Mars and the Moon! Advantages of a low profile for shielding Mars looks like Arizona but feels like Antarctica Rover Opportunity at edge of Endeavor Crater Designing railroads and trains for Mars Designing planes that can fly in Mars’ thin air Breeding plants to be “Mars-hardy” Outposts between dunes, pulling sand over them These are just a few of the Mars-related topics covered in the past 25+ years. Read on for much more! Why Mars? The lunar and Martian frontiers will thrive much better as trading partners than either could on it own. Mars has little to trade to Earth, but a lot it can trade with the Moon. Both can/will thrive together! CHRONOLOGICAL INDEX MMM THEMES: MARS MMM #6 - "M" is for Missing Volatiles: Methane and 'Mmonia; Mars, PHOBOS, Deimos; Mars as I see it; MMM #16 Frontiers Have Rough Edges MMM #18 Importance of the M.U.S.-c.l.e.Plan for the Opening of Mars; Pavonis Mons MMM #19 Seizing the Reins of the Mars Bandwagon; Mars: Option to Stay; Mars Calendar MMM #30 NIMF: Nuclear rocket using Indigenous Martian Fuel; Wanted: Split personality types for Mars Expedition; Mars Calendar Postscript; Are there Meteor Showers on Mars? MMM #41 Imagineering Mars Rovers; Rethink Mars Sample Return; Lunar Development & Mars; Temptations to Eco-carelessness; The Romantic Touch of Old Barsoom MMM #42 Igloos: Atmosphere-derived shielding for lo-rem Martian Shelters MMM #54 Mars of Lore vs. Mars of Yore; vendors wanted for wheeled and walking Mars Rovers; Transforming Mars; Xities -
REMS: the Environmental Sensor Suite for the Mars Science Laboratory Rover
Space Sci Rev DOI 10.1007/s11214-012-9921-1 REMS: The Environmental Sensor Suite for the Mars Science Laboratory Rover J. Gómez-Elvira · C. Armiens · L. Castañer · M. Domínguez · M. Genzer · F. Gómez · R. Haberle · A.-M. Harri · V. Jiménez · H. Kahanpää · L. Kowalski · A. Lepinette · J. Martín · J. Martínez-Frías · I. McEwan · L. Mora · J. Moreno · S. Navarro · M.A. de Pablo · V. Pe i n a d o · A. Peña · J. Polkko · M. Ramos · N.O. Renno · J. Ricart · M. Richardson · J. Rodríguez-Manfredi · J. Romeral · E. Sebastián · J. Serrano · M. de la Torre Juárez · J. Torres · F. Torrero · R. Urquí · L. Vázquez · T. Velasco · J. Verdasca · M.-P. Zorzano · J. Martín-Torres Received: 9 January 2012 / Accepted: 10 July 2012 © Springer Science+Business Media B.V. 2012 J. Gómez-Elvira () · C. Armiens · F. Gómez · A. Lepinette · J. Martín · J. Martín-Torres · J. Martínez-Frías · L. Mora · S. Navarro · V. Peinado · J. Rodríguez-Manfredi · J. Romeral · E. Sebastián · J. Torres · J. Verdasca · M.-P. Zorzano Centro de Astrobiología (CSIC-INTA), Carretera de Ajalvir, km. 4, 28850 Torrejón de Ardoz, Madrid, Spain e-mail: [email protected] I. McEwan · M. Richardson Ashima Research, Pasadena, CA, USA L. Castañer · M. Domínguez · V. Jiménez · L. Kowalski · J. Ricart Universidad Politécnica de Cataluña, Barcelona, Spain M.A. de Pablo · M. Ramos Universidad de Alcalá de Henares, Alcalá de Henares, Spain M. de la Torre Juárez Jet Propulsion Laboratory, Pasadena, CA, USA J. Moreno · A. Peña · J. Serrano · F. Torrero · T. Velasco EADS-CRISA, Tres Cantos, Spain N.O. Renno Michigan University, Ann Arbor, MI, USA M. -
Unlocking the Climate Record Stored Within Mars' Polar Layered Deposits
Unlocking the Climate Record Stored within Mars' Polar Layered Deposits Final Report Keck Institute for Space Studies Isaac B. Smith York University and Planetary Science Instute Paul O. Hayne University of Colorado - Boulder Shane Byrne University of Arizona Pat Becerra University Bern Melinda Kahre NASA Ames Wendy Calvin University of Nevada - Reno Chrisne Hvidberg University of Copenhagen Sarah Milkovich Jet Propulsion Laboratory Peter Buhler Jet Propulsion Laboratory Margaret Landis Planetary Science Instute Briony Horgan Purdue University Armin Kleinböhl Jet Propulsion Laboratory Mahew Perry Planetary Science Instute Rachel Obbard Dartmouth University Jennifer Stern Goddard Space Flight Center Sylvain Piqueux Jet Propulsion Laboratory Nick Thomas University Bern Kris Zacny Honeybee Robocs Lynn Carter University of Arizona Lauren Edgar United States Geological Survey Jeremy EmmeM New Mexico State University Thomas Navarro University of California, Los Angeles Jennifer Hanley Lowell Observatory Michelle Koutnik University of Washington Nathaniel Putzig Planetary Science Instute Bryana L. Henderson Jet Propulsion Laboratory John W. Holt University of Arizona Bethany Ehlmann California Instute of Technology Sergio Parra Georgia Instute of Technology Daniel Lalich Cornell University Candy Hansen Planetary Science Instute Michael Hecht Haystack Observatory Don Banfield Cornell University Ken Herkenhoff United States Geological Survey David A. Paige University of California, Los Angeles Mark Skidmore Montana State University Robert L. Staehle Jet Propulsion Laboratory Mahew Siegler Planetary Science Instute 0. Execu)ve Summary 1. Background 1.A Mars Polar Science Overview and State of the Art 1.A.1 Polar ice deposits overview and present state 1.A.2 Polar Layered Deposits formaon and layers 1.A.3 Climate models and PLD formaon 1.A.4 Terrestrial Climate Studies Using Ice 1.B History of Mars Polar Invesgaons 1.B.1 Orbiters 1.B.2 Landers 1.B.3 Previous Concept Studies 2. -
02 FEB 2012.Wps
IN THIS ISSUE: FEBRUARY 2012 ! Event Calendar, News Notes ! Minutes of the January Meeting. Thanks. ! MVAS Reminders: Dues, An Anniversary, Binocular Marathon ! MVAS Activities: Scopes and Eclipsers ! Observer’s Notes: A Martian Flyby ! MVAS Homework: Mars and Syrtis Major Homework Charts: R Leo, asteroid (5) Astraea ! Constellation of the Month: Leo ! March 2012 Sky Almanac ! Gallery: Mars Up Close Meteorite Editor: Phil Plante 1982 Mathews Rd. #2 Youngstown OH 44514 FEBRUARY 2012 NEWS NOTES Newsletter of the Mahoning Valley Astronomical Society, Inc. Pluto’s Rings? Planetary Science Institute senior scientist Henry Throop and associates have used data from the four- meter Anglo-Australian Telescope in Australia to search for MVAS CALENDAR signs that Pluto may have rings orbiting it- Just like Jupiter, FEB 25 Business meeting at YSU. 8:00 PM Show. Saturn, Uranus and Neptune. Pluto's rings would be too faint and too small to see directly from Earth based telescopes. But MAR 24 Binocular Marathon at the MVCO. Sunset 7:41. occasionally, Pluto occults a star. By studying the resulting occultation light curve that was recorded, one could define the MAR 31 Business meeting at YSU. 8:00 PM Show. system in great detail. As Pluto or any ring passes in front of the APR 21 First Chili-Quest at the MVCO. Chili cook-off with a star, the starlight blinks out, revealing its size and shape. Galaxy Quest to follow. Sunset at 8:11 PM. Throop’s team searched through several observations to try and find any hint of occulting rings of Pluto. So far, they haven't APR 28 Business meeting at the MVCO. -
Modern Mars' Geomorphological Activity
Title: Modern Mars’ geomorphological activity, driven by wind, frost, and gravity Serina Diniega, Ali Bramson, Bonnie Buratti, Peter Buhler, Devon Burr, Matthew Chojnacki, Susan Conway, Colin Dundas, Candice Hansen, Alfred Mcewen, et al. To cite this version: Serina Diniega, Ali Bramson, Bonnie Buratti, Peter Buhler, Devon Burr, et al.. Title: Modern Mars’ geomorphological activity, driven by wind, frost, and gravity. Geomorphology, Elsevier, 2021, 380, pp.107627. 10.1016/j.geomorph.2021.107627. hal-03186543 HAL Id: hal-03186543 https://hal.archives-ouvertes.fr/hal-03186543 Submitted on 31 Mar 2021 HAL is a multi-disciplinary open access L’archive ouverte pluridisciplinaire HAL, est archive for the deposit and dissemination of sci- destinée au dépôt et à la diffusion de documents entific research documents, whether they are pub- scientifiques de niveau recherche, publiés ou non, lished or not. The documents may come from émanant des établissements d’enseignement et de teaching and research institutions in France or recherche français ou étrangers, des laboratoires abroad, or from public or private research centers. publics ou privés. 1 Title: Modern Mars’ geomorphological activity, driven by wind, frost, and gravity 2 3 Authors: Serina Diniega1,*, Ali M. Bramson2, Bonnie Buratti1, Peter Buhler3, Devon M. Burr4, 4 Matthew Chojnacki3, Susan J. Conway5, Colin M. Dundas6, Candice J. Hansen3, Alfred S. 5 McEwen7, Mathieu G. A. Lapôtre8, Joseph Levy9, Lauren Mc Keown10, Sylvain Piqueux1, 6 Ganna Portyankina11, Christy Swann12, Timothy N. Titus6, -
MARS 2020 Project
D-96554 Mars 2020 Science Team Guidelines 6 January 2020 MARS 2020 Project Science Team Guidelines Prepared by: Ken Farley, M2020 Project Scientist Ken WilliFord, M2020 Deputy Project Scientist Katie Stack Morgan, M2020 Deputy Project Scientist JPL D-96554 Last revision: 06 January 2020 National Aeronautics and Space Administration Jet Propulsion Laboratory CaliFornia Institute of Technology Pasadena, CaliFornia This document has been reviewed and determined not to contain export controlled technical data. D-96554 Mars 2020 Science Team Guidelines 6 January 2020 CHANGE LOG DATE SECTIONS CHANGED REASON FOR CHANGE REVISION 01/25/2016 ALL First draft DRAFT 10/11/2016 Section 2.0 and AppendiX Updated Section 2.0 and AppendiX A to Initial Release A include deFinitions For collaborators and revised procedure For adding new team members. Added URL For location oF science team list. 4/5/2019 Section 2.0, Section 3.0, Updated Section 2.0 to remove AppendiX B, AppendiX D reFerences to the Return Sample Science Board and clariFying what it means For a collaborator to cease to have a relationship with their sponsor. Updated Section 3.0 to reFerence AppendiX B and AppendiX D. Updated AppendiX B to include guidelines for communicating intent to publish a manuscript to the Science Team, abstract submission, and author guidelines. Added AppendiX D with NASA guidelines For social media interaction. 1/6/2020 Section 3.0b, Section 2.0, Updated Section 3.0 to reFlect name Appendix C change From JPL Public Relations Office to JPL Digital News and Media OFFice. EXpanded media to include online news and video outlets. -
Mars 2020 Perseverance Launch Press Kit
National Aeronautics and Space Administration Mars 2020 Perseverance Launch Press Kit JUNE 2020 www.nasa.gov Table of contents INTRODUCTION 3 MEDIA SERVICES 11 QUICK FACTS 16 MISSION OVERVIEW 21 SPACECRAFT PERSEVERANCE ROVER 30 GETTING TO MARS 34 POWER 38 TELECOMMUNICATIONS 40 BIOLOGICAL CLEANLINESS 42 EXPERIMENTAL TECHNOLOGIES 45 SCIENCE 49 LANDING SITE 56 MANAGEMENT 58 MORE ON MARS 59 Introduction NASA’s next mission to Mars — the Mars 2020 Perseverance mission — is targeted to launch from Cape Canaveral Air Force Station no earlier than July 20, 2020. It will land in Jezero Crater on the Red Planet on Feb. 18, 2021. Perseverance is the most sophisticated rover NASA has ever sent to Mars, with a name that embodies NASA’s passion for taking on and overcoming challenges. It will search for signs of ancient microbial life, characterize the planet’s geology and climate, collect carefully selected and documented rock and sediment samples for possible return to Earth, and pave the way for human exploration beyond the Moon. Perseverance will also ferry a separate technology experiment to the surface of Mars — a helicopter named Ingenuity, the first aircraft to fly in a controlled way on another planet. Update: As of June 24, the launch is targeted for no earlier than July 22, 2020. Additional updates can be found on the mission’s launch page. Seven Things to Know About the Mars 2020 Perseverance Mission The Perseverance rover, built at NASA’s Jet Propulsion Laboratory in Southern California, is loaded with scientific instruments, advanced computational capabilities for landing and other new systems. -
On Mars Thermosphere, Ionosphere and Exosphere: 3D Computational Study of Suprathermal Particles by Arnaud Valeille
On Mars thermosphere, ionosphere and exosphere: 3D computational study of suprathermal particles by Arnaud Valeille A dissertation submitted in partial fulfillment of the requirements for the degrees of Doctor of Philosophy (Atmospheric and Space Science and Scientific Computing) in the University of Michigan 2009 Doctoral Committee: Research Professor Michael R. Combi, Chair Research Professor Stephen W. Bougher Professor Edward W. Larsen Professor Andrew F. Nagy “The time will come when diligent research over long periods will bring to light things which now lie hidden. A single lifetime, even though entirely devoted to the sky, would not be enough for the investigation of so vast a subject... And so this knowledge will be unfolded only through long successive ages. There will come a time when our descendents will be amazed that we did not know things that are so plain to them… Many discoveries are reserved for the ages still to come, when the memory of us will have been effaced. Our universe is a sorry little affair unless it has in it something for every age to investigate… Nature does not reveal her mysteries once and for all.” - Seneca, Natural Questions, Book 7, First century. © Arnaud Valeille 2009 A mes parents, Marie-Louise et Georges ii Acknowledgements First and foremost, I would like to thank my dissertation committee chair and academic advisor, Prof. Mike Combi. His continuous guidance, support, encouragement have made this work possible. I am grateful to him for giving me the intellectual freedom and challenge to follow two different Master programs at the same time in the Atmospheric and Space Science department (AOSS), College of Engineering and in the Mathematics department, College of Literature Science and Art (LSA), both at the University of Michigan. -
Final Environmental Impact Statement for the Mars 2020 Mission
Availability of the Final Environmental Impact Statement for the Mars 2020 Mission NASA will maintain a website that provides the public with the most up-to-date project information, including electronic copies of the EIS, as they are made available. The website may be accessed at http://www.nasa.gov/agency/nepa/mars2020eis Final Environmental Impact Statement for the Mars 2020 Mission FINAL ENVIRONMENTAL IMPACT STATEMENT FOR THE MARS 2020 MISSION ABSTRACT LEAD AGENCY: National Aeronautics and Space Administration Washington, DC 20546 COOPERATING AGENCY: U.S. Department of Energy Washington, DC 20585 POINT OF CONTACT George Tahu FOR INFORMATION: Planetary Science Division Science Mission Directorate NASA Headquarters Washington, DC 20546 (202) 358-4800 DATE: November 2014 This Final Environmental Impact Statement (FEIS) has been prepared by the National Aeronautics and Space Administration (NASA) in accordance with the National Environmental Policy Act (NEPA) of 1969, as amended, to assist in the decision-making process for the proposed Mars 2020 mission. This Environmental Impact Statement (EIS) is a tiered document (Tier 2 EIS) under NASA’s Programmatic EIS for the Mars Exploration Program. The Proposed Action addressed in this FEIS is to continue preparations for and implementation of the Mars 2020 mission. The Mars 2020 spacecraft would be launched on an expendable launch vehicle during a launch opportunity from July through August 2020. The Mars 2020 spacecraft would deliver a large, mobile science laboratory (rover) with advanced instrumentation to a scientifically interesting location on the surface of Mars early in 2021. The design of the Mars 2020 spacecraft and rover would be based upon and similar to that used in the 2011 Mars Science Laboratory Mission, including the use of a Multi-Mission Radioisotope Thermoelectric Generator.