Effect of the Type of Aging After Supersaturating on Hardness and Aw-7020 Stop Structure
Total Page:16
File Type:pdf, Size:1020Kb
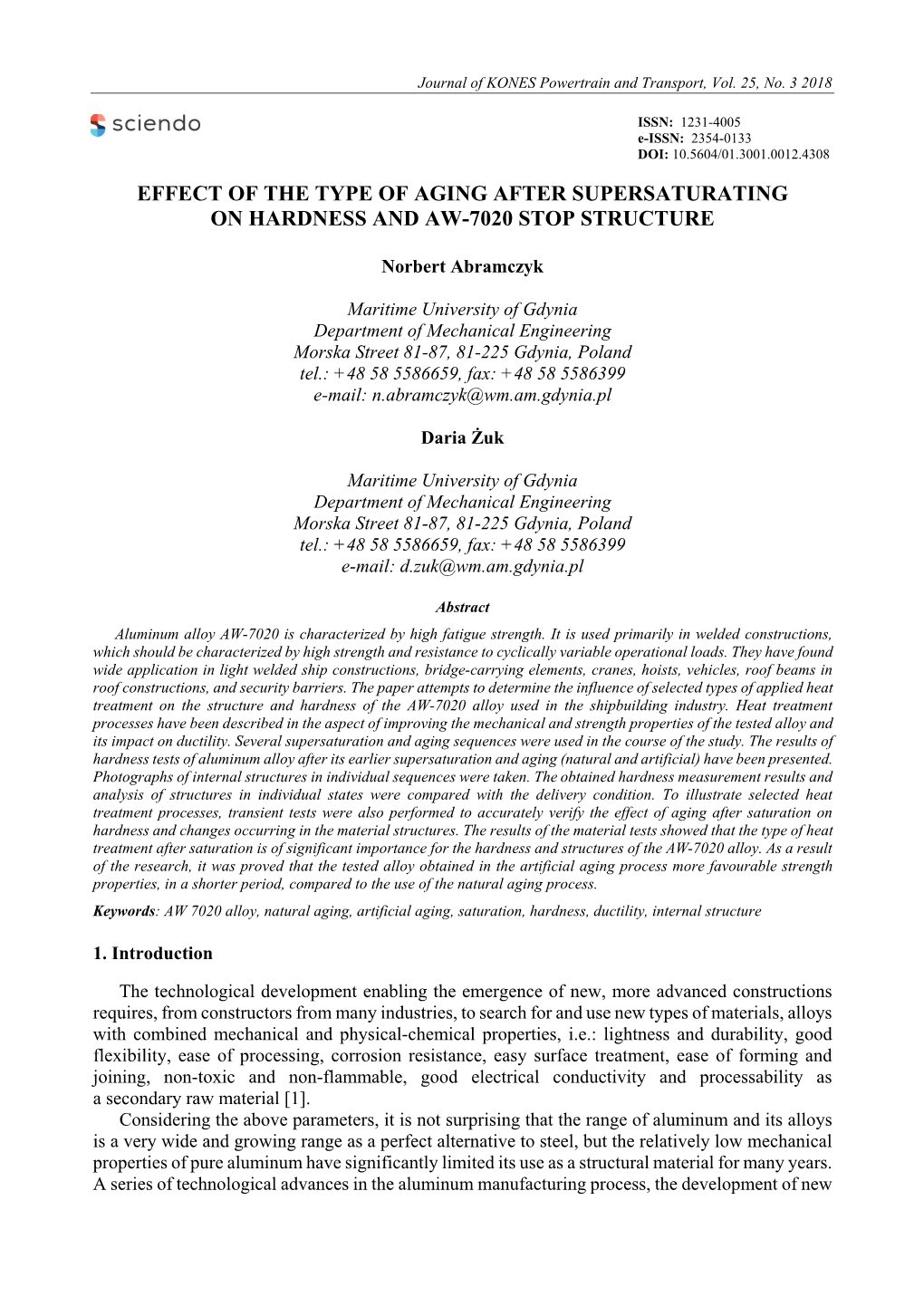
Load more
Recommended publications
-
Hiduminium Technical Data
HIDUMINIUM TECHNICAL DATA HIGH DUTY ALLOYS LTD SLOUGH F oreword Extensive research carried out in recent years, com bined with an increasing demand for " H ID UM IN IUM " high tensile aluminium alloys, has necessitated the revision and increase of the series of data sheets pre viously issued by the Company. As before, our aim is to place before designers and constructors the fullest possible particulars regarding the physical and mechanical properties of " H ID U M IN IU M ," which will enable them to select the materials most suitable for their requirements and to adapt their designs in accordance with the outstanding character istics of this range of alloys. " HIDUMINIUM" is produced under conditions of strict scientific control and progressive inspection and a staff of expert Metallurgists, Research W orkers and Technicians is always ready to give advice on all problems connected with the use of these alloys. Fresh data, as it is revealed by further research, will be issued on additional sheets. This will ensure that all information contained in this volume is up-to-date and may thus be referred to at all times with complete confidence. HIGH DUTY ALLOYS LIMITED 3 CONTENTS Page Index to Specifications 6-9 Hiduminium 15 10-11 Hiduminium 23 12-13 Hiduminium 33 14-15 Hiduminium 35 16-17 H iduminium 40 & 42 18-19 Hiduminium 45 20-21 Hiduminium R.R. 50 22-23 Hiduminium R.R. 53 24-26 Hiduminium R.R. 53.C 27-29 Hiduminium R.R. 56 30-32 H iduminium R.R. 59 33-35 Hiduminium 72 36-37 Hiduminium R.R. -
Inhaltsverzeichnis Seite Schrifttum 5 Abkürzungen 6 Einleitung I Waren
Inhaltsverzeichnis Seite Schrifttum 5 Abkürzungen 6 Einleitung i Waren. — Warenkunde. — Einteilung der Waren. — Hilfs- wissenschaften der Warenkunde 7— 8 I. Metalle und Metallwaren 8 A. Edelmetalle. 1. Gold. — 2. Silber. — 3. Platin. — 4. Queck- silber 10—18 B. Unedle Schwermetalle. 1. Eisen und Eisenwaren (Roh- eisen, schmiedbares Eisen, Erzeugnisse aus Eisen und Stahl). — 2. Kupfer. — 3. Blei. — 4. Zink. — 5. Zinn. — 6. Nickel. — 7. Arsen. — 8. Antimon. — 9. Wismut 18—35 C. Leichtmetalle. 1. Aluminium. — 2. Magnesium 35—37 D. Legierungen. 1. Bronze. — 2. Tombak. — 3. Messing. — 4. Neusilber. — 5. Konstantan .— 6. Britanniametall. — 7. Schriftmetall. — 8. Lagermetalle. — 9. Duralumin. — lO.Hydronalium. — 11. Silumin. —12. Elektron. — 13. Heus- ler'sche Legierungen 37—40 II. Edelsteine und Schmucksteine 40 A. Edelsteine. 1. Diamant. — 2. Rubin und Saphir. — 3. Spinell. — 4. Chrysoberyll. — 5. Smaragd. — 6. Topas. — 7. Zirkon. — 8. Granat. — 9. Türkis. — 10. Edelopal 41—46 B. Schmucksteine. 1. Quarz. — 2. Chalcedon. — S.Mond- stein. — 4. Lasurstein. — 5. Malachit. — 6. Blutstein. — 7. Bernstein 46—48 III. Bildhauersteine 48 1. Marmor. — 2. Alabaster. — 3. Serpentin. — 4. Meer- schaum. — 5. Talk 48—51 IV. Baustoffe 51 A. Bausteine. 1. Kalkstein. — 2. Sandsteine. — 3. Granit. — 4. Porphyr. — 5. Basalt. — 6. Magnesit. — 7. Kunststeine .... 51—53 B. Bindemittel. 1. Branntkalk. — 2. Zement. — 3. Gips 54—56 V. Schleif- und Glättemittel, Mühlsteine 57 1. Schleifsteine. — 2. Schmirgel. — 3. Gemeiner Korund. — 4. Siliziumkarbid. — 5. Bimsstein. — 6. Tripel. — 7. Polier- rot. — 8. Zinnasche. — 9. Wiener Kalk. — 10. Schlämm- kreide.—11. Mühlsteine 67—58 VI. Tonwaren 59 Ton. — 1. Porzellan. — 2. Steinzeug. — 3. Steingut. — 4. Töpferware. — 5. Ziegel. — 6. Feuerfeste Steine 59—67 VII. -
Aluminium Appications CML514 2016.Pdf
Elements of Gr. 13 Unique Property Applications Boron Lewis acid Nuclear reactors‐ control 10B‐ High Nuclear cross rods section for thermal Lewis acid, BNCT neutrons Light metal Bulk usage: Airplanes, Aluminium Surface passivity ships, cars, trains Good strength to weight AlCl3: Friedel Crafts rxn ratio and conductivity MAO: In olefin m.p. 660.3 °C polymerization Gallium Liquid metal Gallium Arsenide solar m.p.29.77 °C cells Gallium nitride LED Low melting soft solid ITO Indium (m.p.156 °C) production of transparent conductive coatings Thallium Poison, non metallic The poisoner's poison“ (tasteless , odorless) Chemistry of Aluminium More than its compounds, the bulk usage of aluminium, especially its alloys dominate the industry •Lightest metal; also relatively inexpensive metal . •Tin was 19,830 USD/Metric Ton, zinc was 2,180 USD/MT and aluminium was 1,910 USD/MT •Third most abundant element on the earths crust: combined in 270 minerals •Low density and ability to resist corrosion by passivation. Pure aluminium has about one‐third the density and stiffness of steel. The yield strength of pure aluminium is 7–11 MPa, while aluminium alloys have yield strengths ranging from 200 MPa to 600 MPa. Yield strength of mild steel is 250 Mpa while that of high strength alloy steel is 690 Mpa A yield strength or yield point of a material is defined as the stress at which a material begins to deform plastically. Prior to the yield point the material will deform elastically and will return to its original shape when the applied stress is removed. ( Mpa = megapascal = 145psi) Three main reasons why aluminium alloys are used instead of pure aluminium •Increased strength to weight ratio over pure aluminium. -
Applied Chemistry-Ii L T P 3 - 2
2.4 APPLIED CHEMISTRY-II L T P 3 - 2 RATIONALE The role of chemistry in every branch of engineering and technology is expanding greatly. Now a days, various chemical products are playing important role in the field of engineering with increasing number of such products each successive years. The strength of materials, the chemical composition of substances, their behaviour when subjected to different treatment and environment, and the laws of heat and dynamic energy have entered in almost every activity of modern life. Chemistry is considered as one of the core subjects for diploma students in engineering and technology for developing in them scientific temper and appreciation of chemical properties of materials, which they have to handle in their professional career. Effort should be made to teach this subject through demonstrations/ minor projects and with the active involvement of students. Note:- Teachers should give examples of engineering/technology applications of various concepts and principles in each topic so that students are able to appreciate learning of these concepts and principles. DETAILED CONTENTS 1. Metallurgy (08 hrs) A brief introduction of the terms: Metallurgy (types), mineral, ore, gangue or matrix, flux, slag, concentration (methods of concentrating the ores), ore, roasting, calcinations, smelting and refining of metal. Metallurgy of (i) Aluminium (ii) Iron Definition of an alloy, purposes of alloying, composition, properties and uses of alloys- brass, bronze, monel metal, magnalium, duralumin, alnico, stainless steel and invar. 2. Fuels (10 hrs) 2.1 Definition of a „Fuel‟, characteristics of a good fuel and classification of fuels with suitable examples 2.2 Definition of Calorific value of a fuel and determination of calorific value of a solid fuel with the help of Bomb calorimeter. -
Aluminium Laminate
Aluminum Al Product format: Laminate Technical characteristics: Aluminum sheet and strip rolled www.bronmetal.com Aluminum Al Product format: Laminate Technical characteristics : Aluminum sheet and strip rolled EQUIVALENCES 1050 PURE ALUMINIUM (99,5%) EQUIVALENTS NATIONAL STANDARDS AND TRADE NAMES ISO SPAIN GERMANY CANADA E.E.U.U. FRANCE UNITED KINGDOM ITALY OTHERS Al-99,5 L-3051 Al-99,5 Al-99,5 A5 1B 9001/2 17010 Puraltok 99,5 3,0255 1S Durcilium T 4007 WG-1S Hiduminium A1 1150/55 Impalco 0,5 Aluran 99,5 EQUIVALENCES 1200 PURE ALUMINIUM (99 %) EQUIVALENTS NATIONAL STANDARDS AND TRADE NAMES ISO SPAIN GERMANY CANADA E.E.U.U. FRANCE UNITED KINGDOM ITALY OTHERS Al 99,0 L-3001 Al 99,0 2S 1100 A-4 1C 3567 4010 Puraltok 99 3,0205 2S 1100 5090 WG-2S Birmetal 2 9001/1 17005 90 Hiduminium-1C 1008 1010 NA-2S 1191 2584 A0 Aluran 99 www.bronmetal.com Aluminum Al Product format: Laminate Technical characteristics : Aluminum sheet and strip rolled EQUIVALENCES 2007 ALUMINIUM-COPPER EQUIVALENTS NATIONAL STANDARDS AND TRADE NAMES SPAIN GERMANY FRANCE SUIZA L-3121 DIN 1725 A U4Pb Al-CuMgPb Cobreltok 07 DIN 1746 Al-CuMgCd DIN 1747 Decotal 200 Tordal 1970 Aludur D 505 Spanal 320 MFK Aludur 570 A Automat EQUIVALENCES 2011 ALUMINIUM-COPPER EQUIVALENCIAS COMERCIALES SPAIN CANADA E.E.U.U. FRANCE SUIZA ITALY UNITED KINGDOM L-3192 CB 60 2011 A-U5PbBi Decotal 500 Recidal 11 28 S 28-S CSA HA,5 ASTM B 211 Fortal 2011 28 S QQ-R-225/3 QQ-R-365 WW-P-471 Ty III QQ-R-566 www.bronmetal.com Aluminum Al Product format: Laminate Technical characteristics : Aluminum sheet and strip rolled EQUIVALENCES 2030 ALUMINIUM-COPPER EQUIVALENTS NATIONAL STANDARDS AND TRADE NAMES SPAIN GERMANY FRANCE SUIZA L-3121 Al CuMgPb A U4Pb Al-CuMgPb 3,1645 NF A 57.350 Al-CuMgCd DIN 1725 Fortal D Decotal 200 DIN 1746 Fortal 2030 Aludur D 505 DIN 1747 Carbium al Pbl MFK Tordal 1970 Duralumin DE Spanal 320 Aludur 570 A Automat EQUIVALENCES 2014 ALUMINIUM-COPPER EQUIVALENTS NATIONAL STANDARDS AND TRADE NAMES ISO SPAIN GERMANY CANADA E.E.U.U. -
A Study of Interrupted Aging in Al-Cu-Mg Alloys
A STUDY OF INTERRUPTED AGING IN AL-CU-MG ALLOYS by Joseph Ming-Ju Tsai A thesis submitted to the Faculty and Board of Trustees of the Colorado School of Mines in partial fulfillment of the requirements for the degree of Doctor of Philosophy (Metallurgy and Materials Engineering). Golden, Colorado Date: Signed: Joseph Ming-Ju Tsai Signed: Michael J. Kaufman Thesis Advisor Golden, Colorado Date: Signed: Professor Michael J. Kaufman, Department Head Department of Metallurgical and Materials Engineering ii ABSTRACT Recently, a novel interrupted aging treatment, T6I6, was reported to improve the strength and toughness of heat treatable Al alloys. It consisted of the following three stages, namely, 1) artificially underaging at a typical temperature (150-200 ◦C) and quenching to room temperature, 2) reheating to a lower aging temperature (60-100 ◦C) for times that result in hardening, and 3) reheating to the initial aging temperature again and holding until peak hardness is observed. The improvements were reported to be due to precipitate refinement and secondary precipitation during the low temperature age. However, the improvements in properties have not been consistently reproduced in the litera- ture, and an explanation for the discrepancies remains unclear. Therefore, the focus of this study was to investigate the interrupted aging processes and the effects of each aging stage, as well as the effect of cold work, on precipitate development in commercial 2024 Al and a high-purity variant of the commercial 2014 alloy, Al-4.2Cu-0.4Mg (wt%). The aging responses, precipitation behavior, and microstructural changes were examined using Vickers microhardness, electrical resistivity, and electron microscopy. -
Aluminium Alloys (2004) 1 Edited by J.F
Proceedings of the 9th International Conference on Aluminium Alloys (2004) 1 Edited by J.F. Nie, A.J. Morton and B.C. Muddle © Institute of Materials Engineering Australasia Ltd Aluminium Alloys – A Century of Age Hardening I.J. Polmear Emeritus Professor, School of Physics and Materials Engineering, Monash University, Melbourne, 3800, Australia Keywords: Alfred Wilm, age hardening, precipitation Abstract A century has elapsed since Alfred Wilm made the accidental discovery of age hardening in an aluminium alloy that became known as Duralumin. His work, and the gradual realization that hardening arose because of the presence of fine precipitates which provided barriers to the motion of dislocations, is a good example of the transition of metallurgy from an art to a science. A brief account is given of the development of age hardenable aluminium alloys and the way that modern experimental techniques allow precipitation processes to be understood on an atomic scale. Some contemporary issues in age hardening are then discussed. 1. Discovery of Age Hardening If a poll was taken to decide the most important metallurgical development during the 20th century, it would be surprising if the discovery of age hardening by Alfred Wilm 100 years ago was not the popular choice. Although this phenomenon has been associated particularly with aluminium alloys, it is now realized that far more types of alloys may be strengthened by this method of heat treatment than through the traditional martensitic transformation in ferrous alloys. Alfred Wilm was born on a farm in 1869 in Silesia, which was then in South Eastern Germany. While a student at an agricultural school, he became interested in chemistry and later, in 1901, he was appointed metallurgist at the Neubabelsberg Scientific and Technical Analysis Centre near to Berlin. -
Advanced Materials for Light Weight Body Design
ISSN (Online): 2319-8753 ISSN (Print) : 2347-6710 International Journal of Innovative Research in Science, Engineering and Technology (A High Impact Factor, Monthly, Peer Reviewed Journal) Visit: www.ijirset.com Vol. 7, Issue 1, January 2018 Advanced Materials for Light Weight Body Design Tejas Pawar1, Atul Ekad2, Nitish Yeole3, Aditya Kulkarni4, Ajinkya Taksale5 BE-Mech. (2016), Dept. of Mechanical Engineering, VIIT, Pune, India.1 BE-Mech. (2016), Dept. of Mechanical Engineering, NBN Sinhgad School of Engineering, Pune, India.2 BE-Mech. (2016), Dept. of Mechanical Engineering, NBN Sinhgad School of Engineering, Pune, India.3 BE-Mech. (2017), Dept. of Mechanical Engineering, RMD Sinhgad School of Engineering, Pune, India.4 BE-Mech. (2016), Dept. of Mechanical Engineering, VPK Bajaj Inst. of Engg. & Technology, Baramati, India.5 ABSTRACT: With the emergent industrial development and dependence on fossil fuels, Green House Gas (GHG) emission has become most important problem. However, car manufacturers have to remain in competition with peers and design their products innovatively that fulfil the new regulations too. Nevertheless of various different approaches to improve fuel economy such as enhancing fuel quality, development of high performance engines and fuel injection system, weight reduction is one of the encouraging approaches. With 10% weight reduction in passenger cars, the fuel economy improves by as much as 6–8%. KEYWORDS: Carbon Fibre, Magnesium, Aluminium, Titanium, light-weight body materials, poly-acrylonitrile I. INTRODUCTION Car body design in view of structural performance and weight reduction is a challenging task due to the various performance objectives that must be satisfied such as vehicle safety, fuel efficiency, endurance and ride quality. -
Comparison of Aluminum Alloys from Aircraft of Four Nations Involved in the WWII Conflict Using Multiscale Analyses and Archival Study
heritage Article Comparison of Aluminum Alloys from Aircraft of Four Nations Involved in the WWII Conflict Using Multiscale Analyses and Archival Study Toufa Ouissi 1,2,*, Gilles Collaveri 3, Philippe Sciau 1, Jean-Marc Olivier 2 and Magali Brunet 1,* 1 CEMES, UPR 8011 CNRS, 31055 Toulouse, France; [email protected] 2 FRAMESPA, UMR 5136, University of Toulouse Jean-Jaurès, 31058 Toulouse, France; [email protected] 3 Aerocherche, 31700 Blagnac, France; [email protected] * Correspondence: [email protected] (T.O.); [email protected] (M.B.) Received: 30 September 2019; Accepted: 14 November 2019; Published: 22 November 2019 Abstract: Aluminum alloys are very interesting witnesses of industrial and technical development. The first ever developed was Duralumin, a light metal with good mechanical properties. In the 1930s, the rise of nationalism stimulated research and development, generating various aluminum alloys. This work reports the comparison of two versions of aluminum alloys, which were found in collected parts of WWII crashed aircraft from four nations: a Messerschmitt Bf 109 (DE), a Dewoitine D.520 (FR), and a P-51 Mustang (USA) and an Avro Lancaster (United Kingdom). The first version of alloy with magnesium content below or equal to 1 wt.% and the second version with higher magnesium content (1.5 wt.%), were identified as respectively AlCuMg1, AlCuMg2 in Germany; Duralumin, Duralumin F.R. in France; Hiduminium DU Brand, Hiduminium 72 in the UK and 17S, 24S in the USA. This study uses a multiscale approach based on historical research complimented by laboratory analyses of materials directly collected on the crashed aircraft. -
Aluminium Alloys – a Century of Age Hardening
View metadata, citation and similar papers at core.ac.uk brought to you by CORE provided by Advanced Materials and Processes Research Institute, Bhopal MATERIALS FORUM VOLUME 28 - Published 2004 1 Edited by J.F. Nie, A.J. Morton and B.C. Muddle © Institute of Materials Engineering Australasia Ltd Aluminium Alloys – A Century of Age Hardening I.J. Polmear Emeritus Professor, School of Physics and Materials Engineering, Monash University, Melbourne, 3800, Australia Keywords: Alfred Wilm, age hardening, precipitation Abstract A century has elapsed since Alfred Wilm made the accidental discovery of age hardening in an aluminium alloy that became known as Duralumin. His work, and the gradual realization that hardening arose because of the presence of fine precipitates which provided barriers to the motion of dislocations, is a good example of the transition of metallurgy from an art to a science. A brief account is given of the development of age hardenable aluminium alloys and the way that modern experimental techniques allow precipitation processes to be understood on an atomic scale. Some contemporary issues in age hardening are then discussed. 1. Discovery of Age Hardening If a poll was taken to decide the most important metallurgical development during the 20th century, it would be surprising if the discovery of age hardening by Alfred Wilm 100 years ago was not the popular choice. Although this phenomenon has been associated particularly with aluminium alloys, it is now realized that far more types of alloys may be strengthened by this method of heat treatment than through the traditional martensitic transformation in ferrous alloys. -
Strain Curves in Aluminium Alloys
Dissertation State parameter based modelling of stress- strain curves in aluminium alloys carried out for the purpose of obtaining the degree of Doctor technicae (Dr. techn.), submitted at TU Wien, Faculty of Mechanical and Industrial Engineering, by Dipl.-Ing. Johannes Franz KREYCA Mat.Nr.: 0627834 under the supervision of Univ.Prof. Dipl.-Ing. Dr. Ernst Kozeschnik Institute of Material Science and Technology reviewed by Univ. Prof. Dr. Prof. E.h. mult. Rudolf Ass. Prof. Dr. Stefan Pogatscher Kawalla Technische Universität Bergakademie Montanuniveristät Leoben Freiberg Kurzfassung In dieser Arbeit wird ein neues Modell zur Simulation von Spannungs-Dehnungs Diagrammen in Abhängigkeit von Temperatur, Dehnrate und Materialzustand in Aluminiumlegierungen beschrieben. Der Materialzustand wird dabei unter Zuhilfenahme der Simulationssoftware MatCalc in Abhängigkeit der thermo-mechanischen Vorgeschichte modelliert. Die Simulation des dehnungsabhängigen Spannungs-Anteils beruht auf einer Entwicklung der durchschnittlichen Versetzungsdichte als Funktion von Temperatur und Dehnrate. Zur Modellierung des dehnungsunabhängigen Spannungs-Anteils wird zuerst die Streckgrenze bei 0K berechnet wobei unterschiedliche Verfestigungsmechanismen wie z.B. Mischkristall-, Ausscheidungs- oder Korngrenzenverfestigung berücksichtigt werden können. Ausgehend von der Streckgrenze bei 0K wird das Materialverhalten bei gegebener Temperatur und Dehnrate mithilfe eines physikalischen Modells zur thermischen Aktivierung beschrieben. Das beschriebene Modell wird mit experimentellen Daten, die zum Teil im Zuge dieser Arbeit entstanden sind verglichen und kalibriert. Im Zuge dieser Arbeit sind auch mehrere Fachartikel in anerkannten wissenschaftlichen Journalen veröffentlicht worden. I confirm, that going to press of this thesis needs the confirmation of the examination committee. Affidavit I declare in lieu of oath, that I wrote this thesis and performed the associated research myself, using only literature cited in this volume. -
(Extremely Resistible to Corrosion by Sea Water.) 2. Non-Corrodibility
No. 4.1 161 49. A New Aluminium Light Alloy " Chlumin." (Extremely resistible to corrosion by sea water.) By Ichiro IITAKA. Research Laboratory, Mitsubishi Company Ltd., Tokyo. (Comm. by K. TAWARA, M.I.A., April 12,1931.) 1. Aluminium light alloys are all very weak forsea water corrosion. Even Duralumin, the best rolling alloy, and Silumin, one of the best casting ones, are not good on this point. Some alloys are really non- corrodible but not used for their inferior mechanical properties and difficulties incasting, rolling or forging. A new alloy was invented in our laboratory 6 years ago, industrial researches were completed and the products are now used insome works. It was named "Chlumin " as itcontains chromium, but a few per cent of magnesium and iron are also added. A brief description will be given of it in the following pages. 2. Non-corrodibility. Castings of Chlumin and of an alloy of composition Cu 801o,Al 92%, themost common one, both made by metallic mould, were immersed in 551o NaCl solution. Photo. I shows the result after 4 years. Chlumin gave only little deposit retaining evensome luster, while, the other was severely corroded precipitating considerable mass of aluminium hydroxide. The machined surfacesof Chlumin and Silumin plates were exposed to air being sprayed by salt water every day. Many black spots appeared soon on Silumin but Chlumin remained bright for a long time. This difference was observed also on specimens immersed in sea water for a year. Experiments were next carried out somewhat quantitatively. Specimens were im- mersed in 5%, NaCl solution in separate bottles.