Influence of the Wearing of the Saw Unit Elements of the Wood Shaper on the System Vibration
Total Page:16
File Type:pdf, Size:1020Kb
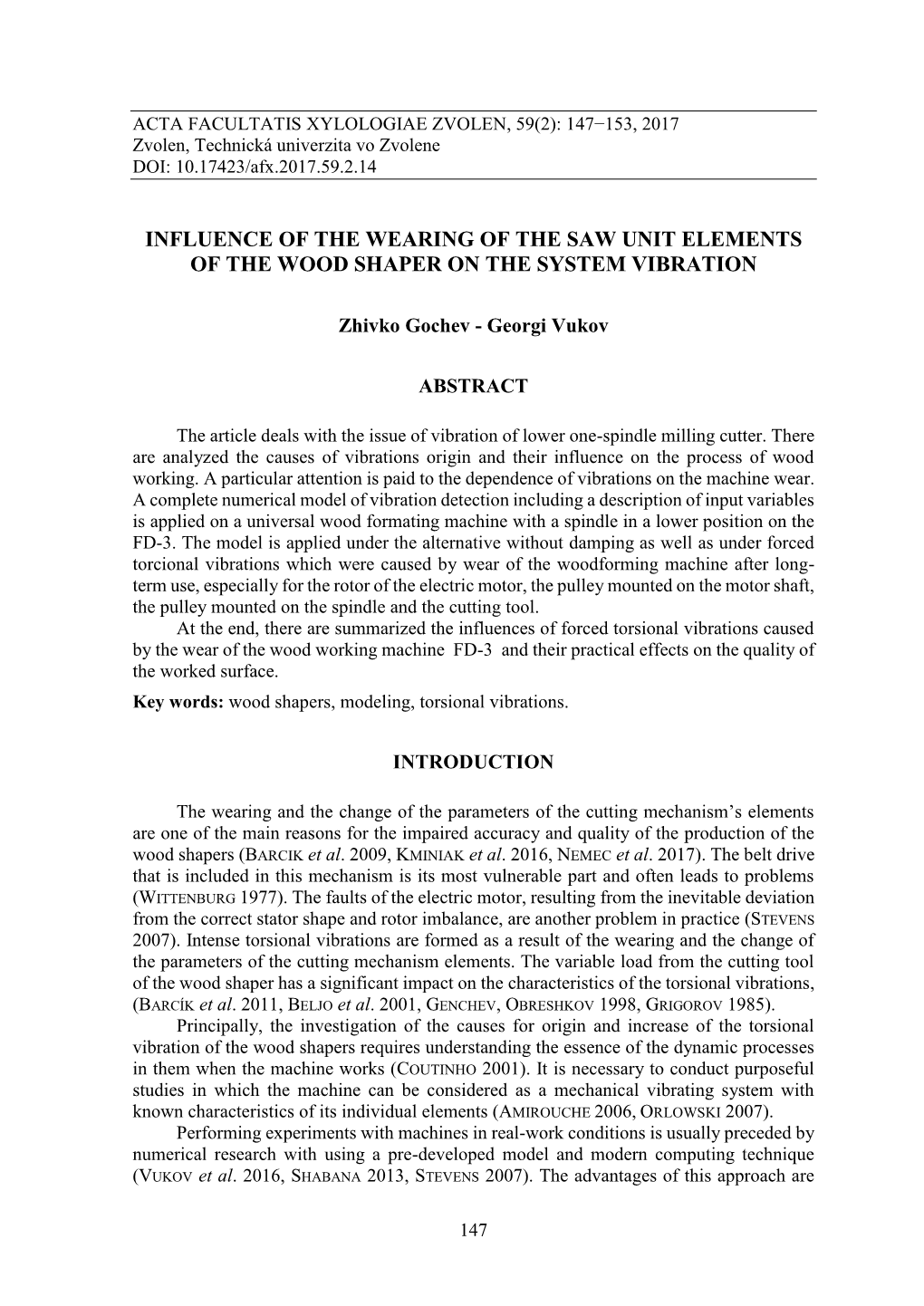
Load more
Recommended publications
-
Cx303 1-Hp Wood Shaper User Manual
CX303 1-HP WOOD SHAPER USER MANUAL TABLE OF CONTENTS General Safety Instructions.....................................................................................3 Specific Safety Instructions.....................................................................................4 CX303 Features......................................................................................................5 Physical Features ...................................................................................................6 Un-Packing .............................................................................................................7 Set Up.....................................................................................................................7 Proper Grounding ...................................................................................................8 Assembly ................................................................................................................9 Spindle....................................................................................................................9 Fence & Shaper Guard ...........................................................................................9 Basic Controls.........................................................................................................10 Test Run .................................................................................................................11 Installing the Cutter.................................................................................................11 -
2-Speed Heavy-Duty Wood Shaper
2-Speed Heavy-Duty INSTRUCTION MANUAL Wood Shaper (Models 43-460 & 43-459) PART NO. 432-02-651-0041 - 05-10-04 Copyright © 2004 Delta Machinery To learn more about DELTA MACHINERY visit our website at: www.deltamachinery.com. For Parts, Service, Warranty or other Assistance, please call 1-800-223-7278 (In Canada call 1-800-463-3582). SAFETY GUIDELINES - DEFINITIONS This manual contains information that is important for you to know and understand. This information relates to protect- ing YOUR SAFETY and PREVENTING EQUIPMENT PROBLEMS. To help you recognize this information, we use the symbols to the right. Please read the manual and pay attention to these sections. Indicates an imminently hazardous situation which, if not avoided, will result in death or serious injury. Indicates a potentially hazardous situation which, if not avoided, could result in death or serious injury. Indicates a potentially hazardous situation which, if not avoided, may result in minor or moderate injury. Used without the safety alert symbol indicates potentially hazardous situation which, if not avoided, may result in property damage. SOME DUST CREATED BY POWER SANDING, SAWING, GRINDING, DRILLING, AND OTHER CONSTRUCTION ACTIVITIES contains chemicals known to cause cancer, birth defects or other reproductive harm. Some examples of these chemicals are: · lead from lead-based paints, · crystalline silica from bricks and cement and other masonry products, and · arsenic and chromium from chemically-treated lumber. Your risk from these exposures varies, depending on how often you do this type of work. To reduce your exposure to these chemicals: work in a well ventilated area, and work with approved safety equipment, always wear MSHA/NIOSH approved, properly fitting face mask or respirator when using such tools. -
Woodworking Machinery
® Woodworking Machinery ® BAILEIGH INDUSTRIAL, INC. 1625 Dufek Drive Manitowoc, WI 54220 Phone: 920. 684. 4990 Fax: 920. 684. 3944 www. baileighindustrial.com Baileigh means...precision. performance. perfection. Baileigh Industrial® was founded in 1999 with the core principles of providing the highest quality industrial metalworking and woodworking machinery backed by unsurpassed after sale support. Since our humble beginnings we have grown into becoming one of the most respected suppliers of metal forming, chip removal, welding, cutting, sheet metal, and fabrication equipment, as well as contractor grade and industrial cabinet making woodworking equipment. Baileigh Industrial’s worldwide headquarters are located in Manitowoc, WI (USA) with additional central distribution facilities located around the world. A large dealer network around the world provides a local source in most cases. We take pride in offering industrial grade equipment providing profitable solutions for metal and wood machinery project requirements. We further back up our quality metal and wood equipment with timely machinery shipments (typically 72 hour or less), and unsurpassed after sale support. Our goal is to become a lifetime supplier to our customers of quality metal and wood working machinery. We strive to offer a great experience in the entire process of machinery selection, sale, and support. Baileigh Industrial means, Precision, Performance, Perfection! Best regards, Stephan B. Nordstrom – President/CEO Router Tables 2 ® Table Saws 5 Sliding Table Saws 14 The Best Resource On The Planet. Baileigh Industrial is an international provider of quality metal and Multi Function Machines 16 woodworking equipment. Our proven industry leadership results Jointers 19 in profitable solutions for any job you may have. -
Woodworking Machinery Catalogs Manuals Parts
WOODWORKING MACHINERY CATALOGS MANUALS PARTS LISTS COMPANY PUBLICATIONS TEXTS Mr. Dana Martin Batory, 402 E. Bucyrus St., Crestline, OH 44827 Order By Full Title And Date Postage Paid Within U.S. Outside U.S. Add $3.50 Per Item No Minimum Order NO PHONE CALLS PLEASE U.S. Funds Only Money Orders Preferred Allow Three Weeks For Delivery Web Catalog Updated Quarterly—Jan.1, April 1, July 1 & Oct. 1 Master List Updated Daily Listings & Prices Valid Only Through January, 2018 Current Master List Available As CD Copy Only (Word 2000) $7.50 PLEASE NOTE: Quality of photocopies is dependent on the quality of the original or master copy. Age, paper quality, condition, ink colors, printing, etc., are all contributing factors. Therefore photocopies are sold “as is” with No returns accepted. Pagination: Page numbers listed represent the number of pages making up the document not necessarily the actual number of photocopy pages. Unfortunately, I lack both the time and expertise to serve as an appraiser or broker. Nor to give advice on locating or fabricating replacement parts. In order to continue my definitive history series on American manufacturers of woodworking machinery, I’m interested in acquiring by loan, gift, or photocopy, any and all documents, catalogs, manuals, photos, trade journals, personal reminiscences, etc., pertaining to woodworking machinery and/or their manufacturers, past or present. All assistance will be acknowledged in print. Loaned material will be treated with care and promptly returned. WRITE with particulars. 2 Cir.=Circular/Bul.=Bulletin/Bro.=Brochure -
Introducing the NEW FAMILY of Jet® WOODWORKING SHAPERS
25CS & 22CS WOODWORKING SHAPERS FEATURES SPECIFICATIONS A • Starting pins for irregular shaping Stock Number 708322 G • Forward/reverse switch for left and right hand Model Number JWS-25CS operation Spindle Speed (RPM) 8000 and 10000 • Two speed step pulley drive lets you select Spindle Diameter (in.) 1/2 and 3/4 F B the best speed and torque for different cutter Spindle Size Under Nut (in.) (1/2) 2-3/4, (3/4) 3 diameters Spindle Travel (in.) 3 • Independent left and right fences feature Table Size (in.) 25 x 25 micro-adjustment and have zero clearance Table T-Slot (in.) 3/8 x 3/4 capability E Table Opening Diameter (in.) 6-7/8 • Extra large handwheel is conveniently located Table Insert Opening Diameter (in.) 1-5/8, 3, 3-1/2 INTRODUCING THE NEW FAMILY OF for fast, easy and accurate spindle height adjustments Fence Size (2) (L x H/in.) 9-1/2 x 2-3/4 ® Router Bit Collet Diameter (in.) 1/4, 3/8 and 1/2 JET WOODWORKING SHAPERS C • 4" dust port connects to your collection system to keep your workplace dust and debris free Table Height From Floor (in.) 34 Dust Port Diameter (OD/in.) 4 • Fully enclosed, heavy-duty steel stand has a removable cover for easy motor access Amps 16 The new line up of shapers from JET delivers power, quality, and precision for all of today's Motor HP 3HP • 1/2" and 3/4" interchangeable spindles and D router bit collets for use with shaper cutter Motor Phase 1Ph woodworkers. -
Programs. Accompanied by Illugfrationslearning
.4* DOCUMENT RESUME- ED 213 858 CE 031 481 . Machine and Woodworking Tool Safety. Module SH-24., T ITLE c , Safety and Health. ITUTION Center for Occupational Researchand,Developmen t, Ine., Waco, Tex. SPONS AGENCY bffice of Vocational and Adult Education (ED). Washington, DC. Div. of National Vocational Programs. PUB DATE 81 CONTRACT- 300-79-0709 NOTE= 51p.; For.re,lAted documents see CE031'450-507. AVAILABLE FROMThe Center for Occupational Research andDevelopment, . 601 Lake Air Dr., Suite C,Waco,ja,76710 (Instructor Guides, $9.75 each; Learning Modules, $3.00 each. Entire set of Learning Modules ayailable, at two subsets": SH-21, SK -41, SH-43, SH-45, and SH-48, $12.00; remaining 45 modules, $97.50). EDRS PRICE MF01 Plus Postage. PC Not Available from EDRS. DEStRIPTORS Behavioral Objectives; *Equipment Utilization; / *Health Education; Learning Activities;Learning Modules; *Machine Tools; Postsecondary Education; *Safely EdUcation; Secondary Education;*vocational , Education; *Woodworking IDENTIFIERS *Occupational. Safety and Health . A /- . A BSTRACT . , This student module on machine andwoodworking tool Safety is one of 50 modules concerned W. hjob safety end health. This module discusses specific ptaGtic ,precautions concerned with the efficient operation and useolli6machine and woodworking tools in use today. Following theintroduction,. 13 objectives (each keyed_to a page in the text) the studentis expected to accomplish are listed (e.g., Cite'nine general safety rules that apply to all machine tools). Then each objective is taughtin detail, sometimes accompanied by illugfrationsLearningactivities are. included. A 7,-* .list of references and answers tolearning activities complete the ,.. module. (CT) .1 .111M11.. ******************A****************************************i******** .* Reproductions supplied bY EDRS are the bestthat can be made from the original document; ********************************************************************* 1IFETY AND HEALTH MACHINE AND WOODWORKING TOOL SAFETY .,:: ? ; ,1. -
They Have Interchangeable Cutters Profiled to Match the Required Shape
Yale Environmental Health & Safety Equipment/Task WOOD SHAPER Name: Equipment/Task 5 Hazard Class: http://ehs.yale.edu/forms-tools/tool- classification-matrix Shop Name: Shop Hazard Class: Purpose Wood shapers are powerful vertical rotating head devices used to profile edges of wood stock. They have interchangeable cutters profiled to match the required shape. The cutter head assembly and spindle height can be adjusted to suit the desired profile. There is also an adjustable fence to set the depth of the cutter profiled into the workpiece. Due to a large possible variation in the cutter diameter the shaper usually has a stepped pulley assembly so that the operator can set the correct speed for the cutting edge and material. Due to the large cutting forces involved, hold-down “fingerboards” or a power feed should be utilized whenever possible (See Diagrams/Illustrations). For the purpose of this Procedure, it will be assumed that no power feed is attached to the shaper. Specific manufacturer and Shop Supervisor instructions must be followed for power feeds. Hazards As with all shop tools, there are many potential hazards associated with the use of a shaper. Consequently, wood shapers are Class 5 tools (http://ehs.yale.edu/forms-tools/tool-classification- matrix). Particular hazards associated with shapers are listed below. Note that the list is not exhaustive as unusual or specialized uses may generate additional unique hazards. Amputation and Laceration • Due to the nature of the high speed rotating cutter any contact with the cutter will result in serious injury. • All body parts should be kept outside of the guarded area and push sticks/blocks utilized for moving workpiece beyond the cutter. -
Routers and Router Tables (Aw) : How to Choose and Use the Most Versatile Power Tool in the Workshop Pdf, Epub, Ebook
ROUTERS AND ROUTER TABLES (AW) : HOW TO CHOOSE AND USE THE MOST VERSATILE POWER TOOL IN THE WORKSHOP PDF, EPUB, EBOOK Randy Johnson | 240 pages | 01 Aug 2011 | Fox Chapel Publishing | 9781565235083 | English | East Petersberg, United States Routers and Router Tables (AW) : How to Choose and Use the Most Versatile Power Tool in the Workshop PDF Book This will save you a lot of time when you are working on a project. Woodcraft Tech Tip. Feet have wheels that make transporting it easy Compact design Dual fence slot configuration A heavy-duty rigid one-piece aluminum frame. Dewalt is such an excellent brand to be manufacturing routers that this is the third product to make this list. DEWALT gives you loads of nice features that include a cam lock on the motor that you can access and adjust without any tools and depth adjustment ring that you can change with just one hand. Router Lift with Cast Table Kit. Some of the other features that you'll really love include:. Moving the router in the opposite direction in rotating motion achieves the best results, done from left to right. The original form of the router is a hand tool type. They make routing safer, and allow you to cut smoothly and accurately. The Dewalt DWPK is a new and innovative table mount router that takes precision working to a whole new level. Moving the router in the opposite direction in rotating motion achieves the best results, done from left to right. That puts a tremendous amount of stress on motor and shaft bearings. -
INDUSTRIAL SHAPER/ROUTER Model 95668 Set up and Operating Instructions
INDUSTRIAL SHAPER/ROUTER Model 95668 SET UP AND OperatinG INSTRUCTIONS Visit our website at: http://www.harborfreight.com Read this material before using this product. Failure to do so can result in serious injury. Save THIS MANUAL. Copyright© 2007 by Harbor Freight Tools®. All rights reserved. No portion of this manual or any artwork contained herein may be reproduced in any shape or form without the express written consent of Harbor Freight Tools. Diagrams within this manual may not be drawn proportionally. Due to continuing improve- ments, actual product may differ slightly from the product described herein. Tools required for assembly and service may not be included. For technical questions or replacement parts, please call 1-800-444-3353. Revised Manual 10d PRODUCT SPECIFICATIONS Electrical Requirements 110 VAC / 60 Hz / 10.54 Amps (With Load) Motor Size: 1 HP / Single Phase Motor RPM: 3450 Spindle Speed: 11,000 Power Cord Length: 70” Power Cord Specifications: SJT 16 AWG x 3C Plug Type: 3 Prong / Grounded Spindle Diameter 1/2” Spindle Thread 12mm x 1.5 pitch, fine thread Spindle Travel 7/8” Router Collets ¼” and ½” (included) Maximum Cutting Diameter 2-7/8” Table Size 24” Wide x 19” Deep Footprint 18-7/8” Wide x 16-5/8” Deep Miter Guide 0 ~ 60° Left to Right Fence Dimensions 9/16” Long x 11-3/4” Wide x 2-3/4” High (Qty. 2) Overall Dimensions 26-1/8” Long x 27-1/2” Wide x 36-1/2” High Gross Weight 187.5 Lb. SAVE THIS MANUAL You will need this manual for the safety warnings and precautions, assembly, operating, inspection, maintenance and cleaning procedures, parts list and assembly diagram. -
B1363n Wood Shaper 2
OWNER’S MANUAL B1363N WOOD SHAPER 2 TABLE OF CONTENTS GENERAL SAFETY INSTRUCTIONS…………………………………………………Page 3 Introduction………………………………………………………………………..………..Page 4 Package Contents…………………………………………………………..………….……Page 5 Assembly Instructions…………………………………………..…………………………..Page 6 Assembly Instructions Installing the Dust Hood/Guard & Fence Assembly…...……………………………….Page 7 Installing the Shaper Head Spindles…………...………………………………………..Page 8 Installing the Shaper Head Spindles, Continued………..………………………………Page 9 Installing the Shaper Head Spindles, Continued……..…………………………………Page 10 Adjusting the Speeds…………………………..………………………………………..Page 10 Mitre Gauge Adjusting……………….…………………………………………………Page 10 Operating Instructions…………..…………………………………………………………..Page 11 Wiring Plan…………….……………………………………………………………………Page 12 Parts List………………………...…………………………………………………………..Page 13 Schematic Diagram…….……………………………………………………………………Page 14 Accessories…….……………………………………………………………………………Page 15 Warranty Policy…………..…………………………………………………………………Page 16 3 GENERAL SAFETY INSTRUCTIONS EXTREME CAUTION SHOULD BE USED IN OPERATING ALL POWER TOOLS. KNOW YOUR POWER TOOL, BE FAMILIAR WITH ITS OPERATION. READ THE OWNER’S MANUAL AND PRACTICE SAFE USAGE PROCEDURES AT ALL TIMES. CONNECT your machine ONLY to the matched and specified power source. WEAR SAFETY GLASSES, RESPIRATORS, HEARING PROTECTION and SAFETY SHOES when operating this machine. DO NOT wear loose clothing or jewellery when operating machinery. A Safe Environment is important. Keep the area free of dust, dirt and other debris in the immediate vicinity of the machine. BE ALERT! Do Not Use prescription or other drugs that may affect your ability or judgement to safely use this machine. DISCONNECT the power source when changing drill bits, hollow chisels, router bits, shaper heads, blades, knives or making other adjustments or repairs. NEVER leave an operating tool unattended. NEVER reach over the table when the tool is in operation. NEVER make crosscuts with the rip fence in place. NEVER attempt cut material that is warped or twisted. -
Platinum Edition 2-Speed Heavy-Duty Wood Shaper
Platinum Edition 2-Speed INSTRUCTION MANUAL Heavy-Duty Wood Shaper (Model 43-424) DATED 7-12-00 PART NO. 432-02-651-0018 © Delta Machinery 2000 SAFETY RULES Woodworking can be dangerous if safe and proper operating procedures are not followed. As with all machinery, there are certain hazards involved with the operation of the product. Using the machine with respect and caution will considerably lessen the possibility of personal injury. However, if normal safety precautions are overlooked or ignored, personal injury to the operator may result. Safety equipment such as guards, push sticks, hold-downs, featherboards, goggles, dust masks and hearing protection can reduce your potential for injury. But even the best guard won’t make up for poor judgment, carelessness or inattention. Always use common sense and exercise caution in the workshop. If a procedure feels dangerous, don’t try it. Figure out an alternative procedure that feels safer. REMEMBER: Your personal safety is your responsibility. This machine was designed for certain applications only. Delta Machinery strongly recommends that this machine not be modified and/or used for any application other than that for which it was designed. If you have any questions relative to a particular application, DO NOT use the machine until you have first contacted Delta to determine if it can or should be performed on the product. Technical Service Manager Delta Machinery 4825 Highway 45 North P.O. Box 2468 Jackson, TN 38302-2468 (IN CANADA: 505 Southgate Drive, GUELPH, ONTARIO N1H 6M7) WARNING: FAILURE TO FOLLOW THESE RULES MAY RESULT IN SERIOUS PERSONAL INJURY 1. -
WOOD SHAPER Model 27 & 27 Super
WOOD SHAPER Model 27 & 27 Super Instruction Manual & Parts List EDP # 0460232 (800) 248-0144 wwwpowermaticcom This manual has been prepared for the owner and operators of a Powermatic Model 27 or Super 27 Shaper Its purpose, aside from machine operation, is to promote safety through the use of accepted correct operating and maintenance procedures Completely read the safety and main- tenance instructions before operating or servicing the machine To obtain maximum life and efficiency from your shaper and to aid in using the machine safely, read this manual thoroughly and follow all instructions carefully Warranty & Service The JET Group warrants every product it sells If one of our tools needs service or repair, one of our Autho- rized Repair Stations located throughout the United States can give you quick service In most cases, any one of these JET Group Repair Stations can authorize warranty repair, assist you in obtaining parts, or perform routine maintenance and major repair on your JET, Performax or Powermatic tools For the name of an Authorized Repair Station in your area, please call 1-800-274-6848 More Information Remember, the JET Group is consistently adding new products to the line For complete, up-to-date product information, check with your local JET Group distributor JET Group Warranty The JET Group (including Performax and Powermatic brands) makes every effort to assure that its products meet high quality and durability standards and warrants to the original retail consumer/purchaser of our products that each product be free