Refractory Metal Fasteners for Extreme Conditions: the Basics
Total Page:16
File Type:pdf, Size:1020Kb
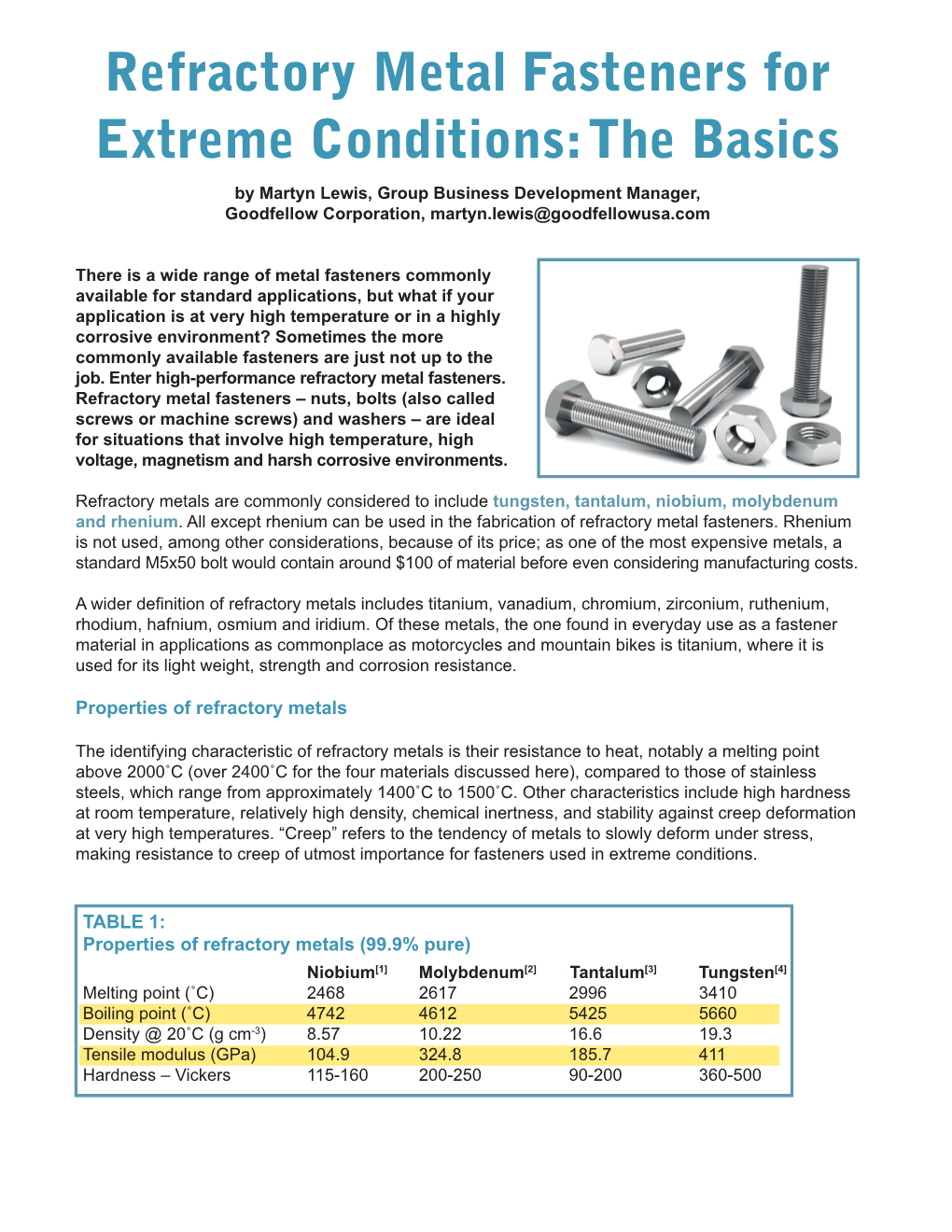
Load more
Recommended publications
-
Electrodeposition of Alloys Or Compounds in Molten Salts and Applications
Journal of Mining and Metallurgy, 39 (1‡2) B (2003) 177 - 200. ELECTRODEPOSITION OF ALLOYS OR COMPOUNDS IN MOLTEN SALTS AND APPLICATIONS P. Taxil, P. Chamelot, L. Massot and C. Hamel Laboratoire de Génie Chimique, Département Procédés Electrochimiques et Matériaux, CNRS UMR 5503, Université Paul-Sabatier, 118 route de Narbonne, 31062 Toulouse Cedex 04, France (Received 12 February 2003; accepted 18 April 2003) Abstract This article deals with the different modes of preparation of alloys or intermetallic compounds using the electrodeposition in molten salts, more particularly molten alkali fluorides. The interest in this process is to obtain new materials for high technology, particularly the compounds of reactive components such as actinides, rare earth and refractory metals. Two ways of preparation are considered: (i) electrocoating of the more reactive metal on a cathode made of the noble one and reaction between the two metals in contact, and (ii) electrocoating on an inert cathode of the intermetallic compound by coreduction of the ions of each elements. The kinetic is controlled by the reaction at the electrolyte interface. A wide bibliographic survey on the preparation of various compounds (intermetallic compounds, borides, carbides…) is given and a special attention is paid to the own experience of the authors in the preparation of these compounds and interpreta- tion of their results. Keywords: Electrosynthesis, alloys, intermetallic, compounds, molten salts, alkali fluorides, co-reduction, reactive electrodeposition 1. Introduction Laboratories of chemical engineering are often interested in high technology processes to prepare coatings of new materials or compounds; most of these compounds J. Min. Met. 39 (1 ‡ 2) B (2003) 177 taxil.indd 1 6/26/03, 12:06 PM P. -
Metallurgy Materials Programs
WASH-1181-73 METALLURGY AND MATERIALS PROGRAMS 0 FY 1973 UNITED STATES ATOMIC ENERGY COMMISSION DIVISION of PHYSICAL RESEARCH LEGAL NOTICE This report was prepared as an account of work sponsored by the United States Government. Neither the United States nor the United States Atomic Energy Commission. nor any of their employees, nor any of their contractors, subcontractors, or their employees, makes any warranty, express or implied, or assumes any legal liability or responsibility for the accuracy, completeness or usefulness of any information, apparatus, product or process disclosed, or represents that its use would not infringe privately owned rights. WASH-1181-73 METALLURGY AND MATERIALS PROGRAMS Fiscal Year 1973 July 1973 U. S. Atomic Energy Commission Division of Physical Research FORWORD The Metallurgy and Materials Program constitutes one portion of a wide range of research supported by the AEC Division of Physical Research. Other programs are administered by the Division's Chemistry, High Energy Physics, and Physics and Mathematics Offices. Metallurgy and Materials research is supported primarily at AEC National Laboratories and Univer- sities. The research covers a wide spectrum of scientific and engineering areas of interest to the Atomic Energy Commission and is conducted generally by personnel trained in the disciplines of Solid State Physics, Metallurgy, Ceramics, and Physical Chemistry. This report contains a listing of all research underway in FY 1973 together with a convenient index to the program. Donald K. Stevens Assistant Director (for Metallurgy and Materials Programs) Division of Physical Research i INTRODUCTION The purpose of this report is to provide a convenient compilation and index of the AEC's Metallurgy and Materials Programs. -
Interactions of Lanthanides and Liquid Alkali Metals for “Liquid-Like” Lanthanide Transport in U-Zr Fuel
Interactions of Lanthanides and Liquid Alkali Metals for “Liquid-Like” Lanthanide Transport in U-Zr Fuel THESIS Presented in Partial Fulfillment of the Requirements for the Degree Master of Science in the Graduate School of The Ohio State University By Jeremy Payton Isler Graduate Program in Nuclear Engineering The Ohio State University 2017 Master's Examination Committee: Dr. Jinsuo Zhang, Advisor Dr. Marat Khafizov, Co-Advisor Copyrighted by Jeremy Payton Isler 2017 Abstract One of the major limitations in achieving increased burnup in metallic U-Zr nuclear fuel is Fuel-Cladding Chemical Interaction (FCCI). The migration of the fission product lanthanides from within the fuel to the peripheral is one of the major contributors to FCCI. A “liquid-like” transport mechanism proposes the lanthanide transport is aided by liquid cesium and liquid sodium in the pores of the fuel and at the fuel peripheral. The purpose of this thesis was to provide additional experimental evidence towards this proposed mechanism. This thesis investigated the interaction between the lanthanides and cesium and sodium, with a focus on the solubility of the lanthanides in these liquid alkali metals. First, a prediction of the solubility was calculated using the Miedema model. This prediction was then compared to the inversion crucible solubility experiment performed in this thesis. The solubility experiment studied the temperature and liquid-composition dependence of the lanthanides in liquid sodium, cesium and sodium-cesium mixtures. In addition, the solubility in mixtures shows the various alkali metals concentration effect on the solubility. With the results of differential scanning calorimetry (DSC) experiments, updated phase diagrams for sodium-neodymium and cesium-neodymium were obtained from the experimental data in this thesis. -
Making Bazrs3 Chalcogenide Perovskite Thin Films by Molecular Beam Epitaxy Ida Sadeghi1,2, Kevin Ye1, Michael Xu1, James M
Making BaZrS3 chalcogenide perovskite thin films by molecular beam epitaxy Ida Sadeghi1,2, Kevin Ye1, Michael Xu1, James M. LeBeau1, R. Jaramillo1† 1. Department of Materials Science and Engineering, Massachusetts Institute of Technology, Cambridge, MA, USA 2. Department of Electrical and Computer Engineering, University of Waterloo, Waterloo, ON, CA † [email protected] Abstract We demonstrate the making of BaZrS3 thin films by molecular beam epitaxy (MBE). BaZrS3 forms in the orthorhombic distorted-perovskite structure with corner-sharing ZrS6 octahedra. The single-step MBE process results in films smooth on the atomic scale, with near-perfect BaZrS3 stoichiometry and an atomically-sharp interface with the LaAlO3 substrate. The films grow epitaxially via two, competing growth modes: buffered epitaxy, with a self-assembled interface layer that relieves the epitaxial strain, and direct epitaxy, with rotated-cube-on-cube growth that accommodates the large lattice constant mismatch between the oxide and the sulfide perovskites. This work sets the stage for developing chalcogenide perovskites as a family of semiconductor alloys with properties that can be tuned with strain and composition in high-quality epitaxial thin films, as has been long-established for other systems including Si-Ge, III-Vs, and II-Vs. The methods demonstrated here also represent a revival of gas-source chalcogenide MBE. Introduction Sulfides and selenides in the perovskite and related crystal structures – chalcogenide perovskites, for brevity – may be the next family -
Download This Article PDF Format
Volume 3 Number 14 21 July 2021 Nanoscale Pages 3969–4294 Advances rsc.li/nanoscale-advances ISSN 2516-0230 PAPER Ihor Z. Hlova, Viktor P. Balema et al. Incommensurate transition-metal dichalcogenides via mechanochemical reshuffl ing of binary precursors Nanoscale Advances View Article Online PAPER View Journal | View Issue Incommensurate transition-metal dichalcogenides via mechanochemical reshuffling of binary Cite this: Nanoscale Adv.,2021,3, 4065 precursors† Ihor Z. Hlova,‡*a Prashant Singh,‡a Serhiy Z. Malynych,b Roman V. Gamernyk,c Oleksandr Dolotko,a Vitalij K. Pecharsky,ad Duane D. Johnson, ad Raymundo Arroyave,e Arjun K. Pathak f and Viktor P. Balema *a A new family of heterostructured transition-metal dichalcogenides (TMDCs) with incommensurate (“misfit”) spatial arrangements of well-defined layers was prepared from structurally dissimilar single-phase 2H-MoS2 and 1T-HfS2 materials. The experimentally observed heterostructuring is energetically favorable over the formation of homogeneous multi-principle element dichalcogenides observed in related dichalcogenide systems of Mo, W, and Ta. The resulting three-dimensional (3D) heterostructures show semiconducting Received 23rd January 2021 behavior with an indirect band gap around 1 eV, agreeing with values predicted from density functional Accepted 6th June 2021 Creative Commons Attribution-NonCommercial 3.0 Unported Licence. theory. Results of this joint experimental and theoretical study open new avenues for generating DOI: 10.1039/d1na00064k unexplored metal-dichalcogenide heteroassemblies with incommensurate structures and tunable rsc.li/nanoscale-advances physical properties. 1 Introduction Bulk TMDCs are built from layers of covalently bonded metal and chalcogen atoms held together via weak van der Waals Layered transition-metal dichalcogenides (TMDCs) with (vdW) forces (see ESI, Fig. -
LIT 8477 Consolidated Waste List, V6
UNOFFICIAL CONSOLIDATED VERSION OF ANNEXES III, IIIA, IIIB IV & IVA OF REGULATION (EC) No. 1013/2006 OF THE EUROPEAN PARLIAMENT AND OF THE COUNCIL of 14 June 2006 1 on shipments of wastes 1 Amended by COMMISSION REGULATION (EC) No 308/2009 of 15 April 2009, COMMISSION REGULATION (EC) No 413/2010 of 12 May 2010, COMMISSION REGULATION (EC) No 664/2011 of 11 July 2011 COMMISSION REGULATION (EC) No 135/2012 of 16 February 2012 & COMMISSION REGULATION (EC) No 1234/2014 of 18 November 2014. Version 6 (21/11/14) ANNEX III LIST OF WASTES SUBJECT TO THE GENERAL INFORMATION REQUIREMENTS LAID DOWN IN ARTICLE 18 (“GREEN” LISTED WASTE)2 Regardless of whether or not wastes are included on this list, they may not be subject to the general information requirements laid down in Article 18 if they are contaminated by other materials to an extent which (a) increases the risks associated with the wastes sufficiently to render them appropriate for submission to the procedure of prior written notification and consent, when taking into account the hazardous characteristics listed in Annex III to Directive 91/689/EC; or (b) prevents the recovery of the wastes in an environmentally sound manner. The following wastes will be subject to the general information requirements laid down in Article 18: For the purposes of this Regulation: Any reference to List A in Annex IX to the Basel Convention shall be understood as a reference to Annex IV to this Regulation. B1 METAL AND METAL BEARING WASTES B1010 Metal and metal-alloy wastes in metallic, non-dispersible form: -
Chemical Compatibility and High Temperature Limits for Structural
CHEMICAL COMPATIBILITY AND HIGH- TEMPERATURE LIMITS FOR STRUCTURAL MATERIALS Nasr M. Ghoniem Mechanical and Aerospace Engineering Department University of California at Los Angles (UCLA) Los Angeles, CA. 90095-1597 APEX Study Meeting SANDIA NATIONAL LABS Albuquerque, N.M. July 27-28, 1998 1 Ghoniem - UCLA COOLANT - STRUCTURAL MATERIAL SYSTEMS COOLANT STRUCTURAL MATERIAL • Liquid Lithium • Vanadium Alloys • Liquid Lithium-Lead • Silicon Carbide Composites • Molten Salts (FLiBe) • Ferritic Steels • Helium • Refractory Alloys (Ta, Nb, Mo, W) 2 Ghoniem - UCLA LIQUID METAL CHEMICAL COMPATIBILITY (Basic Mechanisms) > Dissolution in Liquid Metal dS = β()c − c dt sat bulk −∆ dS H act = Ce RT dt $ = mass transfer coefficient csat = element saturation concentration in liquid metal cbulk = actual element concentration in bulk ) Hact = activation energy for dissolution 3 Ghoniem - UCLA LIQUID METAL CHEMICAL COMPATIBILITY (Basic Mechanisms) cont. > Exchange due to non-metallic Elements For oxygen, carbon, and nitrogen, the distribution coefficient is: ∆Go ()l −∆Go ()s o a []s RT K = s e o [] as l o as are saturation activities for solid (s) and liquid (l). > For K>1, we get pick-up. > For K<1, we get loss. 4 Ghoniem - UCLA COMPATIBILITY OF VANADIUM ALLOYS WITH LIQUID LITHIUM • For V-3Ti-1Si and V-15Cr-5Ti at 550ºC in flowing lithium (Borgstedt): - weight loss: 10-3 - 3x10-3 g/m2hr - weight loss is strongly influenced by nitrogen content of the liquid metal. - Reaction is parabolic with an activation energy of 180kJ/mol (≈ nitrogen diffusion -
Tantalum (Ta73)
NANO3D SYSTEMS LLC 1110 NE Circle Blvd., ATAMI/Bldg. 11, Corvallis, Oregon 97330-4254 T 503-927-4766| F 541-758-9320| http://www.nano3dsystems.com Tantalum (Ta73) Properties Tantalum is a blue-gray, lustrous transition metal with an atomic mass of 180.95 u. Tantalum has a density of 16.69 g/cm3, a melting point of 3017 oC and a resistivity of 13.1 µOhm cm. It is hard and has a Brinell hardness of 440 – 3430 MPa. Tantalum forms compounds in oxidation states -III to +V. Most commonly encountered are oxides of Ta(V), which includes all minerals. Its standard electrode potential in respect to Ta+3 is -0.6V. Tantalum is highly corrosion-resistant. At temperatures below 150 °C tantalum is almost completely immune to attack by the normally aggressive aqua regia. It can be dissolved with hydrofluoric acid or acidic solutions containing the fluoride ion and sulfur trioxide, as well as with a solution of potassium hydroxide. Its abundance has been estimated to be ~ 2 parts per million (ppm) of the Earth’s crust. Plating Solutions The electrodeposition of reactive metals such as aluminum (Al), magnesium (Mg) and tantalum (Ta) from aqueous solutions is impossible causing hydrogen evolution to occur at the cathode, due to the narrow potential window in aqueous solutions. Electrodeposition from fused salt electrolytes is a general plating technique for the majority of electronegative refractory metals (Ta, Nb, Mo, W, Zr, Hf, Ti, V et al) [1]. It is the most practical method, which can yield thick, high purity, coherent and dense coatings. -
Oxidation Studies of Some Refractory Metals James Henry Witte Iowa State University
View metadata, citation and similar papers at core.ac.uk brought to you by CORE provided by Digital Repository @ Iowa State University Ames Laboratory Technical Reports Ames Laboratory 2-1964 Oxidation studies of some refractory metals James Henry Witte Iowa State University Harley A. Wilhelm Iowa State University Follow this and additional works at: http://lib.dr.iastate.edu/ameslab_isreports Part of the Metallurgy Commons Recommended Citation Witte, James Henry and Wilhelm, Harley A., "Oxidation studies of some refractory metals" (1964). Ames Laboratory Technical Reports. 66. http://lib.dr.iastate.edu/ameslab_isreports/66 This Report is brought to you for free and open access by the Ames Laboratory at Iowa State University Digital Repository. It has been accepted for inclusion in Ames Laboratory Technical Reports by an authorized administrator of Iowa State University Digital Repository. For more information, please contact [email protected]. Oxidation studies of some refractory metals Abstract Samples of niobium, tantalum, molybdenum and tungsten metals have been given phosphided cases by heating in a phosphorous atmosphere. The as mples were subsequently exposed to air at an elevated temperature. In tests at 800°C, the phosphided samples resisted air oxidation markedly compared to the pure untreated samples. The hospp hided cases were only a few microns thick yet oxidation resistance of all these samples extended for several hours. Phosphided samples with 90° edges did not resist oxidation at the edges as well as rounded edge samples. Disciplines Metallurgy This report is available at Iowa State University Digital Repository: http://lib.dr.iastate.edu/ameslab_isreports/66 IS-854 IOWA STATE UNIVERSITY OXIDATION STUDIES OF SOME REFRACTORY METALS by James Henry Witte and Harley A. -
What Are Refractory Metals?
What are Refractory Metals? Refractory metals are different. As a group they provide a number of unique characteristics – such as resistance to high heat, corrosion and wear – making them useful in a multitude of applications. The next time you climb into your automobile take note that you are surrounded by components which are made of refractory metals or have been cut or formed by them. Your car’s electrical or electronic systems may also make use of the metals’ electric and heat-conducting qualities. On the other hand, refractory metals were used in the tools which helped to drill the well which produces the gasoline in your tank. Piping of refractory metal alloys helped process it. And your oil may contain a refractory metal compound to increase its lubricating ability. The paradox of refractory metals is that, despite their wide and constantly growing list of applications, many people – sometimes even engineers, working with one of the metals – do not fully understand how and where each is mined, how it is processed, how it is formed, or even understand the full extent of the diversity of refractory metals’ applications. Five Metals with Unique Characteristic Tungsten W Molybdenum Mo Niobium Nb Tantalum Ta Rhenium Re Excellent strength at high temperatures. Even when heated to 1000oC (1832oF) tungsten rocket nose cones still have twice the tensile strength iron has at room temperature. Very high melting point (2468oC/4474oF to 3410oC/6170oF): High melting points of tungsten, tantalum and molybdenum make them useful in processing molten metals and minerals such as glass making. 1 Excellent wear and abrasion Exceptional resistance to resistance: Refractory metals, often corrosion. -
UWFDM-1297 Initial Engineering Assessment of Actinide Transmutation in Z-Pinch Power Plant
OLO HN GY C • Initial Engineering Assessment of Actinide E I T N • S Transmutation in Z-Pinch Power Plant T N I T O U I T S E U F • • W I N I S C O N S L. El-Guebaly, B. Cipiti, P.H. Wilson, P. Phruksarojanakun, R. Grady, I. Sviatoslavsky December 2006 (revised June 2007) UWFDM-1297 FUSION TECHNOLOGY INSTITUTE UNIVERSITY OF WISCONSIN MADISON WISCONSIN Initial Engineering Assessment of Actinide Transmutation in Z-Pinch Power Plant L. El-Guebaly, B. Cipiti, P.H. Wilson, P. Phruksarojanakun, R. Grady, I. Sviatoslavsky Fusion Technology Institute University of Wisconsin 1500 Engineering Drive Madison, WI 53706 http://fti.neep.wisc.edu December 2006 (revised June 2007) UWFDM-1297 Initial Engineering Assessment of Actinide Transmutation in Z-Pinch Power Plant L. El-Guebaly1, B. Cipiti2, P.H.Wilson1, P. Phruksarojanakun1, R. Grady1, and I. Sviatoslavsky1 1Fusion Technology Institute, University of Wisconsin, Madison, WI 2Sandia National Laboratories, Albuquerque, NM, [email protected] Abstract As part of the Advanced Energy Initiative, the U.S. Department of Energy recently announced the Global Nuclear Energy Partnership that would recycle spent fuel to expand the capacity of geological repositories. Initiation of the supporting activities is underway. These include a scoping assessment and design of the fuel reprocessing and separation systems and the transmutation of actinides using fast reactors and accelerator- driven systems. Our initial assessment indicates the Z-Pinch could be an attractive option for burning actinides (Pu, Np, Am, Cm) and/or minor actinides (Am, Cm) produced by the fission fuel reprocessing plants. A Z-transmuter would need a 200 MJ target injected every 10 seconds to transmute the actinides and deliver a net electric power of 1 GW. -
Publication Information and Contributors
Copyright © 1990 ASM International ® ASM Handbook, Volume 2: Properties and Selection: Nonferrous Alloys and All rights reserved. Special-Purpose Materials (#06182G) www.asminternational.org Contents Specific Metals and Alloys ................................... 1 Rare Earth Metals ..................................... 720 Germanium and Germanium Compounds ................. 733 Introduction to Aluminum and Aluminum Alloys ............ 3 Gallium and Gallium Compounds ........................ 739 Alloy and Temper Designation Systems for Aluminum and Indium and Bismuth .................................... 750 Aluminum Alloys ..................................... 15 Special-Purpose Materials ................................. 759 Aluminum Mill and Engineered Wrought Products .......... 29 Properties of Wrought Aluminum and Aluminum Alloys ..... 62 Magnetically Soft Materials ............................. 761 Aluminum Foundry Products ............................ 123 Permanent Magnet Materials ............................ 782 Properties of Cast Aluminum Alloys ..................... 152 Metallic Glasses ....................................... 804 Aluminum-Lithium Alloys .............................. 178 Electrical Resistance Alloys ............................. 822 High-Strength Aluminum P/M Alloys ..................... 200 Electrical Contact Materials ............................. 840 Appendix: Conventionally Pressed and Sintered Aluminum Thermocouple Materials ................................ 869 P/M Alloys .........................................