Engine Specification
Total Page:16
File Type:pdf, Size:1020Kb
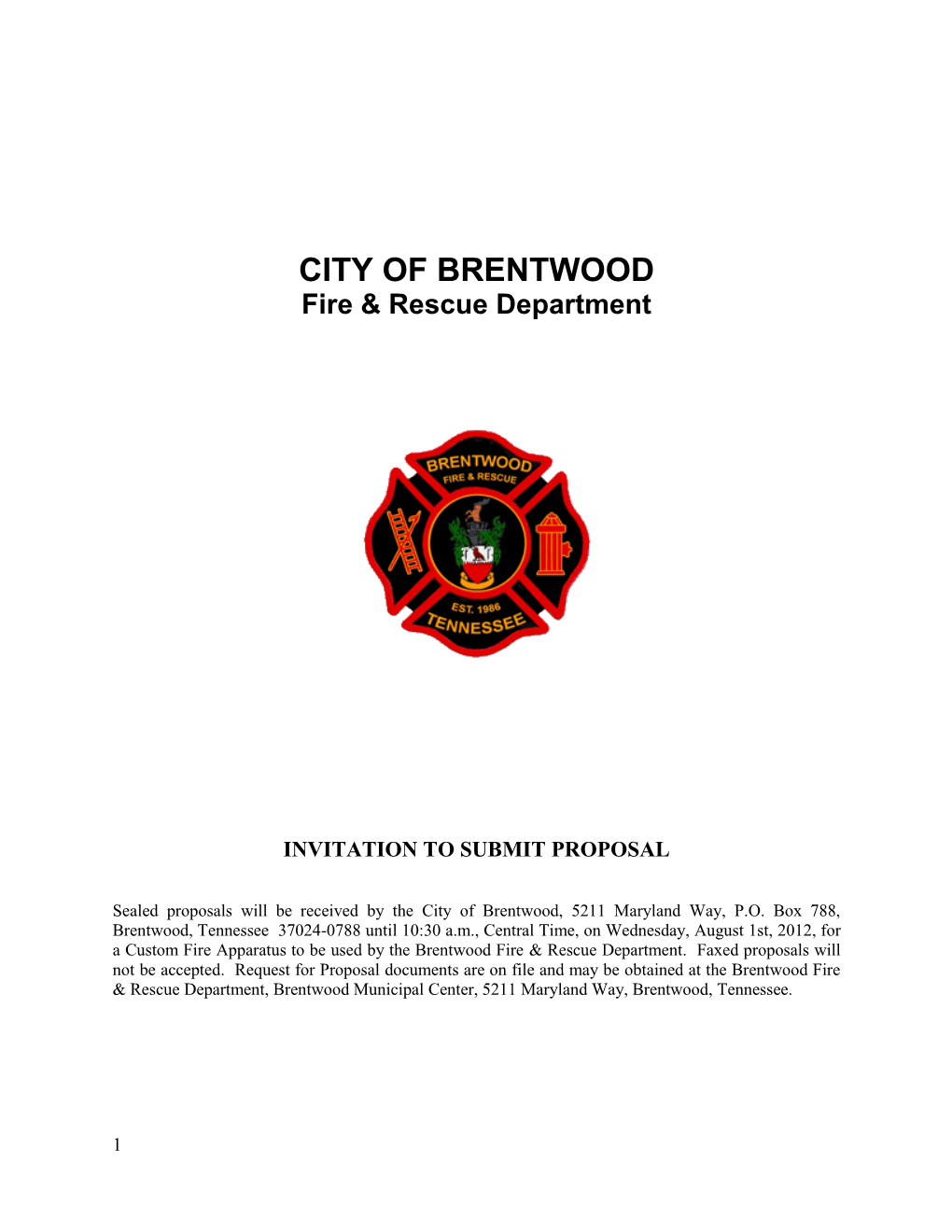
Load more
Recommended publications
-
Bid Proposal Instructions
BID PROPOSAL INSTRUCTIONS ABOUT IDOT PROPOSALS: All proposals are potential bidding proposals. Each proposal contains all certifications and affidavits, a proposal signature sheet and a proposal bid bond. PREQUALIFICATION Any contractor who desires to become pre-qualified to bid on work advertised by IDOT must submit the properly completed pre-qualification forms to the Bureau of Construction no later than 4:30 p.m. prevailing time twenty-one days prior to the letting of interest. This pre-qualification requirement applies to first time contractors, contractors renewing expired ratings, contractors maintaining continuous pre-qualification or contractors requesting revised ratings. To be eligible to bid, existing pre-qualification ratings must be effective through the date of letting. WHO CAN BID ? Bids will be accepted from only those companies that request and receive written Authorization to Bid from IDOT’s Central Bureau of Construction. REQUESTS FOR AUTHORIZATION TO BID Contractors wanting to bid on items included in a particular letting must submit the properly completed “Request for Authorization to Bid/or Not For Bid Status” (BDE 124) and the ORIGINAL “Affidavit of Availability” (BC 57) to the proper office no later than 4:30 p.m. prevailing time, three (3) days prior to the letting date. WHAT CONSTITUTES WRITTEN AUTHORIZATION TO BID? When a prospective prime bidder submits a "Request for Authorization to Bid/or Not For Bid Status”(BDE 124) he/she must indicate at that time which items are being requested For Bidding purposes. Only those items requested For Bidding will be analyzed. After the request has been analyzed, the bidder will be issued an Authorization to Bid or Not for Bid Report, approved by the Central Bureau of Construction and the Chief Procurement Officer that indicates which items have been approved For Bidding. -
Production Specifications CO#3
Production Specifications CO#3 Maui Police Department Maui Police Department Sydney Kikuchi Sydney Kikuchi 55 Mahalani Street 55 Mahalani Street Wailuku, HI 96793 Wailuku, HI 96793 808-244-6410 808-244-6410 Quote No: MPDHICM-0007 Job/Order No: SVI #603 03/27/2007 Page 1 PART NO S DESCRIPTION QTY ID PG == Boiler Plate Information - 2005.400 06/24/05 == 1 SVI 01-02-2000 Insurance ($2,000,000.00) 1 SVI 1 01-04-0110 Engineering Drawings (17" x 11" Sheet) 1 SVI 01-08-0100 General Construction and Design 1 SVI 1 01-08-A100 Internet In-Process Site 1 SVI 3 01-15-1100 Manuals - CD Format - (2) Standard 1 SVI 3 01-15-1300 |-- No Printed Copy of Manuals 1 SVI 01-18-0100 > Construction Period 365 SVI 3 01-40-0100 Warranty: Boiler Plate 1 SVI 3 01-40-1100 |-- Warranty: General - 1 Year (standard) 1 SVI 4 01-40-2100 |-- Warranty: Structural - 10 Years (standard) 25 SVI 4 01-45-0100 Testing 1 SVI 5 01-45-2000 |-- NFPA 12 Volt DC Test 1 SVI 5 01-45-3000 |-- NFPA 120/240 Volt AC Test 1 SVI 6 01-A0-1000 S > Inspection Trip (Per Person/Per Trip) 9 SVI 6 == Dealer Options - 2005.400 06/24/05 == 1 SVI 02-20-0200 S < > Delivery and Demonstration: By Dealer / Representative 200 SVI 6 Inc. $ from CO - CA port. Ocean freight $ by HT&T == Diamond - 1.005 03/25/05 == 1 SP 00-AA-0000 > Pricing as of QW Release 03-25-2005 1 SP 00-DA-4400 Diamond Flat Floor ELFD 24" Raised Roof Alum Tilt Cab 1 SP 7 17-EL-2400 |-- Flat Floor ELFD 24" Raised Roof Tilt Cab-DIA/GLAD 1 SP 7 18-05-8000 > |-- Cab Doors Full Length 20"/24" Roof-DIA/GLAD 1 SP 8 18-09-0500 |-- Door Handles -
New Pumper Specifications
Dur ham Fi r e Depar t ment 51 Col l ege Road ■ Durham, New Hampshire ■ 03824-3585 Phone 603-862-1426 ■ Fax 603-862-1513 [email protected] NEW PUMPER SPECIFICATIONS FOR DURHAM FIRE DEPARTMENT DURHAM, NEW HAMPSHIRE March 22, 2017 INSTRUCTIONS TO BIDDERS NOTICE The Town of Durham, New Hampshire, hereinafter referred to as the "town", is interested in receiving proposals from qualified individuals or companies that meet the requirements as set forth in this Request for Proposal (RFP). The town is requesting proposals for the construction and delivery of a Fire Pumper. Price provided shall include delivery to the Town of Durham. All RFP'S shall be submitted no later than 3:00 p.m. on DATE: April 24, 2017 to Chief Corey Landry, Durham Fire Department, 51 College Rd. Durham NH, 03824. SEALED bid envelopes shall be clearly labeled Bid: 2017: FD-Pumper. PURPOSE Through these specifications it is the intent of the Purchaser to secure an apparatus to withstand the duty encountered in the firefighting and rescue apparatus service. The apparatus shall be constructed with due consideration to the nature and distribution of the load to be sustained, and to the characteristics of the service. All parts not specifically mentioned herein, but which are necessary in order to furnish a complete fire apparatus, shall be furnished and shall conform to the best practices known to the emergency vehicle industry. Subletting any part of the fabrication, painting, or finishing of this apparatus will not be acceptable. The apparatus body is to be built completely by the Bidder or the bid will be excluded from consideration. -
2000W Non-Towable Light Tower W/ Wheels - 9-30 Feet - (4) 500W LED Lamps - 259,200 Lumens - 9KW Part #: WAL-ML-30-9-4X500LTL-LED-9G
Larson Electronics LLC www.LarsonElectronics.com 9419 E US HWY 175, Kemp, TX 75143 Phone: 903.498.3363 Fax: 903.498.3364 Email: [email protected] 2000W Non-Towable Light Tower w/ Wheels - 9-30 Feet - (4) 500W LED Lamps - 259,200 Lumens - 9KW Part #: WAL-ML-30-9-4X500LTL-LED-9G Page: 1 Larson Electronics LLC www.LarsonElectronics.com 9419 E US HWY 175, Kemp, TX 75143 Phone: 903.498.3363 Fax: 903.498.3364 Email: [email protected] Made in the USA The WAL-ML-30-9-4X500LTL-LED-9G 2000 Watt LED Light Tower on Non-Towable Wheeled Cart with 9000 watt Generator from Larson Electronics is an ideal solution for operators who need a fully portable, self contained, easy to operate light system capable of illuminating large areas. Adjustable from 9 to 30 feet in height above the cart deck and equipped with four 500 watt LED lamps, this unit will provide over 259,200 lumens of quality illumination. This portable light tower will run for up to 8 hours uninterrupted on a single tank of fuel. *PLEASE NOTE: ANY FREE SHIPPING OFFERS DO NOT APPLY TO LIGHT MASTS OR LIGHT TOWERS* The WAL-ML-30-9-4X500LTL-LED-9G light tower with generator is a portable lighting system designed high mobility while providing enough output to illuminate approximately 4 acres of area effectively. Equipped with four 500 watt high output LED lamps, this LED light tower provides operators with an easily deployed lighting system that can provide large scale illumination. This crank-up style light mast allows operators to extend the light mast from 9' to 30' above the deck of the pull around cart, elevating the light heads to heights up to 30' above ground level. -
ANNEXURE-1 to the TENDER ENQUIRY NO.: DPS/AMPU/ELE/354 Complete Technical Specifications of the of HIGH MAST SYSTEM
ANNEXURE-1 TO THE TENDER ENQUIRY NO.: DPS/AMPU/ELE/354 Complete technical specifications of the of HIGH MAST SYSTEM Design, manufacturing, supply and delivery at AMD,ER ,Khasmahal, Jamshedpur on FOR basis and Erection and Commissioning of High mast lighting, 20 Mtrs. height shaft with single dip hot galvanized, lantern carriage, double drum internal winch motor, trailing steel wire rope, control panel, head frame along with 08 Nos. of 200 watts LED flood light fitting complete along with aviation light on top of the high mast - 01 No. Note: Erection & Commissioning: The supplier must do the Erection, Commissioning of all the supplied High mast Lighting systems at location AMD,ER, Khasmahal, Jamshedpur ( Site will be earmarked by AMD authority) by constructing of suitable foundation considering the safe soil bearing capacity at site as 10T/sqmtr at 2 Mtrs depth with all materials and labours, including installation of mast feeder pillar by grouting stand on the concrete with all material and labours. Page 1 of 11 TECHNICAL SPECIFICATION HIGH MAST SYSTEM Height of mast : 20 Meter No. of sections : Two Material construction : S 355 grade as per BS-EN10 025 Base dia. and top diameter (A/F) : Top : 150 mm, Bottom : 460 mm Plate thickness & section Length : Top : 4 mm, Bottom : 5 mm Cross section of Mast : 20 side polygon Standard for of galvanization : As per BS EN ISO 1461 Size of opening and door at base : 1200 x 250 mm Diameter of base plate : 670 mm Thickness of base plate : 25 mm Lightning protection finial : G.I single spike of length 1200 mm Max.wind speed : 62.5 m/s Number of foundation bolts : 8 nos. -
Contract Number: A-Dems 07-2019
DISASTER AND EMERGENCY MANAGEMENT SERVICES DEPARTMENT CONTRACT NUMBER: A-DEMS 07-2019 BID DOCUMENT (IN COMPLIANCE WITH THE PREFERENTIAL PROCUREMENT REGULATIONS, 2017 PUBLISHED IN GOVERNMENT GAZETTE NO. 40553 OF 20 JANUARY 2017) THE APPOINTMENT OF SERVICE PROVIDERS TO SUPPLY, DELIVER AND COMMISSION VARIOUS TYPES OF SPECIALISED EMERGENCY SERVICES VEHICLES BY MEANS OF OUTRIGHT PURCHASE ON AN AS AND WHEN REQUIRED BASIS FROM DATE OF AWARD UNTIL 30 JUNE 2022 ISSUED BY: PREPARED BY: PREPARED FOR: Department of Finance Disaster and Emergency Management Disaster and Emergency Management Tender Office Services Department Services Department (Tender Initiation Section) 3 Hawley Road 3 Hawley Road 68 Woburn Avenue Bedfordview Bedfordview BENONI 1501 Private Bag X 65 BENONI 1500 Mr. R Van Vuuren Mr. S Sibande Tel: (011) 999-6540/6567 [email protected] [email protected] Fax: (011) 999-7511 NAME OF BIDDING ENTITY (FULL NAME, i.e. Ltd, Ltd, JV/CONSORTIUM, SOLE PROPRIETOR etc.) : __________________________________________________________________________________________________ TELEPHONE NUMBER : _______________________________________________________________________ EMAIL ADDRESS : _______________________________________________________________________ FAX NUMBER : _______________________________________________________________________ 1 CONTRACT NUMBER: A-DEMS 07-2019 THE APPOINTMENT OF SERVICE PROVIDERS TO SUPPLY, DELIVER AND COMMISSION VARIOUS TYPES OF SPECIALISED EMERGENCY SERVICES VEHICLES BY MEANS OF OUTRIGHT PURCHASE -
Price List 10/11 Innovative Traffic Technology from One Single Source
Fachbetrieb und Mitglied im Verein für Verkehrstechnik VV For purchase / rent / leasing und Verkehrssicherung e.V. V Price list 10/11 Innovative traffic technology from one single source With safety from Berghaus! www.berghaus-verkehrstechnik.de· [email protected] Fachbetrieb und Mitglied im Verein für Verkehrstechnik VVV can be upgradet for crossroads! und Verkehrssicherung e.V. MPB 3400 Mobile traffic-light system for alternating one-way traffic Can be extended for controlling T-junctions or crossroads Simple and clearly struc- tured control – all at a glance Radio, cable and quartz control for universal use All signal heads identical – any can be used as transmitters or receivers Standard radar detectors for vehicle-actuation Standard halogen lamps or with innovative LED lamps on request The new traffic-light system MPB 3400 is produced in compliance with the requirements of German regulations VDE 0832 and the RiLSA for radio, cable and quartz-controlled systems. Depending on the particular application, it corresponds to type classes A, B or C of German regulation TL-LSA97 (TechnicalDelivery Conditions Mobile Traffic Light Systems 97 The latest radio transmission technology gives the MPB 3400 a reliable digital radio path with high transmission quality. On request, the traffic light can be supplied with multi-frequency rating and up to 16 radio channels. This product can be found on page 20 Contents Pioneering light Page 2 Advance warning lamps Wired running lights systems LED-flash lights; self-synchronising running -
Pulse Template for Performance Specification
West Des Moines Fire Department Fire Engine Specification Bidder Complies Yes No SPECIFICATIONS FOR A MULTI PURPOSE RESPONSE- TRIPLE COMBINATION PUMPER The City of West Des Moines, Iowa, is specifying a cab forward (front engine, rear wheel drive) four (4) door (two (2) doors on each side), triple combination pumper to add to its front line fleet of fire apparatus. The unit shall have a rescue style body with full height and full depth compartments of adequate size to carry a full complement of rescue and firefighting tools. It shall have a 1500 gpm midship type pump, a minimum 700 gallon booster tank and seating for six (6) fully equipped firefighters. It shall be a custom fire truck chassis, cab, and body employing the latest engineering practices and the highest quality workmanship. It shall meet the current edition of NFPA 1901. The body of the apparatus shall be rescue style with body height to match that of the cab including the raised roof; no portion of the body shall be taller than the cab. Overall length of the apparatus shall not exceed 33 feet. The overall width of body shall not exceed 102 inches. The overall height shall not exceed 11 feet. The Project Team that compiled these specifications utilized three (3) utilization components to identify specific items needed in the manufacture of the vehicle, based on past and current experiences with a variety of apparatus styles and specifications: a) Safety b) Functionality c) Uniformity Sealed bids will be received by the West Des Moines Fire Department for the furnishing of all necessary labor, equipment and material for the Fire Apparatus and other equipment as outlined in the following specifications. -
IEC/ISO Database on Graphical Symbols for Use on Equipment
International Electrotechnical Commission International Organization for Standardization (requires password) Graphical Symbols for Use on Equipment The database on Graphical Symbols for Use on Equipment contains the complete set of graphical symbols included in IEC 60417 and ISO 7000. It therefore offers end-users a "one-stop" shop for all such graphical symbols. These International Standards are maintained respectively by IEC/TC 3, subcommittee SC 3C and ISO/TC 145, subcommittee SC 3. Each graphical symbol is identified by a reference number and contains a title (in English and French), a graphical representation in GIF and vectorized PDF format, and some additional data as applicable. Various search and navigation facilities allow for easy retrieval of graphical symbols. Subscriptions Customers have the possibility to subscribe to the joint IEC and ISO collection of symbols or to each respective organization's symbols only. Joint IEC 60417 and ISO 7000 collection The most cost effective solution is the combined collection which offers the IEC 60417 and ISO 7000 collections in database format, with the possibility to download IEC 60417 snapshots or the ISO 7000 standard in PDF format. In order to subscribe please contact your local IEC National Committee/approved sales outlet or local ISO member, or visit the IEC Webstore or the ISO Store. IEC 60417 collection only If you are only interested in those graphical symbols produced by the IEC, then this restricted collection offers you access to the IEC 60417 standard only, with PDF snapshots of the entire collection available for added value. In order to subscribe please contact your local IEC National Committee/approved sales outlet or visit the IEC Webstore. -
Protection, Utilization and Analysis of High Mast
ISSN: 2277-9655 [Chandra* et al., 6(5): May, 2017] Impact Factor: 4.116 IC™ Value: 3.00 CODEN: IJESS7 IJESRT INTERNATIONAL JOURNAL OF ENGINEERING SCIENCES & RESEARCH TECHNOLOGY PROTECTION, UTILIZATION AND ANALYSIS OF HIGH MAST STREET LIGHT IN RURAL AREA Bhagawati Chandra , Miss Anjali Karsh Electrical & Electronics Engineering Department with specialization in Power System Engineering of Dr. C. V. Raman Institute of Science & Technology, Kargi Road Kota, Bilaspur (C. G.). DOI: 10.5281/zenodo.573540 ABSTRACT High Mast Light gives the several cost effective advantages and cost is a major issue for rural area general services. This project illustrates the theoretical basis and the analytical development of the high mast lighting poles. In the late 1960‟s, studies were conducted to investigate the impact that high-mast lighting gives on traffic performance, driver visibility, and illumination costs. It was found that increasing the height of the lighting offered a noticeable advantage in that it provided drivers with increased uniformity of illumination and brightness while minimizing discomfort and disability glare. In this turn, it`s led to a reduced number of visibility related accidents. Also, lighting is a major requirement when we deal with working at the opencast mining. In opencast mining, the efficient lighting system is required while working during dark hours. In the present work, a new system of light mast tower is proposed & designed which increases the usability of the existing light mast towers. In this solution, each light mast is given a particular position to its vertical & horizontal axis which sets the light to focus in any particular area and direction to cover target area with minimum power and resource. -
Non-Towable Light Tower W/ Wheels - 9-30' - (4) 500W LED Lamps - 259,200 Lumens - Roll-Around Cart Part #: WAL-ML-30-9-4X500LTL-LED
Larson Electronics LLC www.LarsonElectronics.com 9419 E US HWY 175, Kemp, TX 75143 Phone: 903.498.3363 Fax: 903.498.3364 Email: [email protected] Non-Towable Light Tower w/ Wheels - 9-30' - (4) 500W LED Lamps - 259,200 Lumens - Roll-Around Cart Part #: WAL-ML-30-9-4X500LTL-LED Page: 1 Larson Electronics LLC www.LarsonElectronics.com 9419 E US HWY 175, Kemp, TX 75143 Phone: 903.498.3363 Fax: 903.498.3364 Email: [email protected] Made in the USA The WAL-ML-30-9-4X500LTL-LED 2000 Watt LED Light Tower on Non-Towable Wheeled Cart from Larson Electronics is an ideal solution for operators who need a fully portable, self contained, easy to operate light system capable of illuminating large areas. Adjustable from 9 to 30 feet in height above the cart deck and equipped with four 500 watt LED lamps, this unit will provide over 259,200 lumens of quality illumination. This portable light tower is mounted on a cart with plenty of room for a genset, toolbox or other equipment and gear and comes equipped with 50' of 12/3 SOOW chemical and abrasion resistant cord terminated in a choice of cord caps. *PLEASE NOTE: ANY FREE SHIPPING OFFERS DO NOT APPLY TO LIGHT MASTS OR LIGHT TOWERS* The WAL-ML-30-9-4X500LTL-LED light tower is a portable lighting system designed high mobility while providing enough output to illuminate approximately 4 acres of area effectively. Equipped with four 500 watt high output LED lamps, this LED light tower provides operators with an easily deployed lighting system that can provide large scale illumination.