Prehnjr Mines 0052E 11152.Pdf
Total Page:16
File Type:pdf, Size:1020Kb
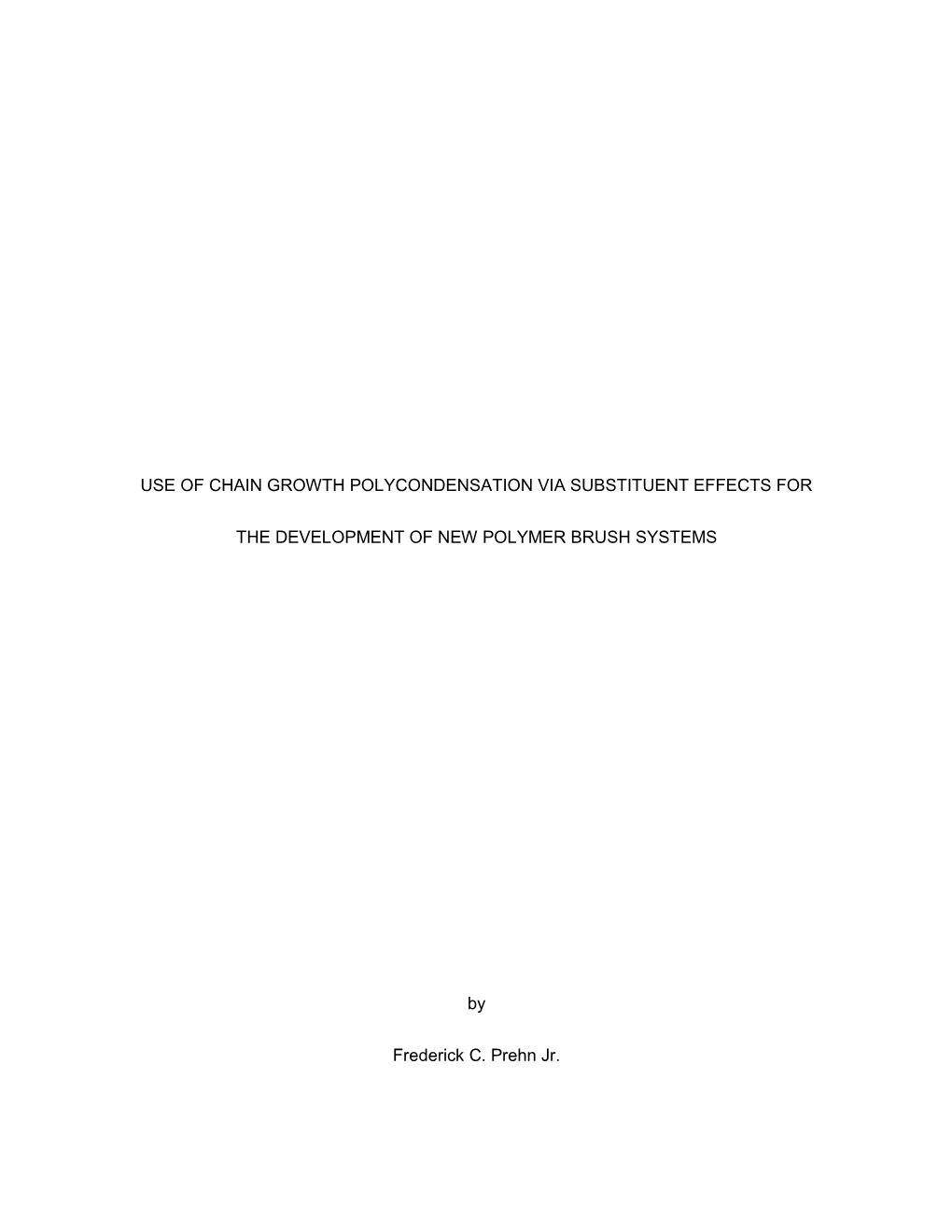
Load more
Recommended publications
-
Controlled/Living Radical Polymerization in Aqueous Media: Homogeneous and Heterogeneous Systems
Prog. Polym. Sci. 26 =2001) 2083±2134 www.elsevier.com/locate/ppolysci Controlled/living radical polymerization in aqueous media: homogeneous and heterogeneous systems Jian Qiua, Bernadette Charleuxb,*, KrzysztofMatyjaszewski a aDepartment of Chemistry, Center for Macromolecular Engineering, Carnegie Mellon University, 4400 Fifth Avenue, Pittsburgh, PA 15213, USA bLaboratoire de Chimie MacromoleÂculaire, Unite Mixte associeÂe au CNRS, UMR 7610, Universite Pierre et Marie Curie, Tour 44, 1er eÂtage, 4, Place Jussieu, 75252 Paris cedex 05, France Received 27 July 2001; accepted 30 August 2001 Abstract Controlled/living radical polymerizations carried out in the presence ofwater have been examined. These aqueous systems include both the homogeneous solutions and the various heterogeneous media, namely disper- sion, suspension, emulsion and miniemulsion. Among them, the most common methods allowing control ofthe radical polymerization, such as nitroxide-mediated polymerization, atom transfer radical polymerization and reversible transfer, are presented in detail. q 2001 Elsevier Science Ltd. All rights reserved. Keywords: Aqueous solution; Suspension; Emulsion; Miniemulsion; Nitroxide; Atom transfer radical polymerization; Reversible transfer; Reversible addition-fragmentation transfer Contents 1. Introduction ..................................................................2084 2. General aspects ofconventional radical polymerization in aqueous media .....................2089 2.1. Homogeneous polymerization .................................................2089 -
1 Fundamentals of Polymer Chemistry
1 Fundamentals of Polymer Chemistry H. Warson 1 THE CONCEPT OF A POLYMER 1.1 Historical introduction The differences between the properties of crystalline organic materials of low molecular weight and the more indefinable class of materials referred to by Graham in 1861 as ‘colloids’ has long engaged the attention of chemists. This class includes natural substances such as gum acacia, which in solution are unable to pass through a semi-permeable membrane. Rubber is also included among this class of material. The idea that the distinguishing feature of colloids was that they had a much higher molecular weight than crystalline substances came fairly slowly. Until the work of Raoult, who developed the cryoscopic method of estimating molecular weight, and Van’t Hoff, who enunciated the solution laws, it was difficult to estimate even approximately the polymeric state of materials. It also seems that in the nineteenth century there was little idea that a colloid could consist, not of a product of fixed molecular weight, but of molecules of a broad band of molecular weights with essentially the same repeat units in each. Vague ideas of partial valence unfortunately derived from inorganic chem- istry and a preoccupation with the idea of ring formation persisted until after 1920. In addition chemists did not realise that a process such as ozonisation virtually destroyed a polymer as such, and the molecular weight of the ozonide, for example of rubber, had no bearing on the original molecular weight. The theory that polymers are built up of chain formulae was vigorously advocated by Staudinger from 1920 onwards [1]. -
Cationic/Anionic/Living Polymerizationspolymerizations Objectives
Chemical Engineering 160/260 Polymer Science and Engineering LectureLecture 1919 -- Cationic/Anionic/LivingCationic/Anionic/Living PolymerizationsPolymerizations Objectives • To compare and contrast cationic and anionic mechanisms for polymerization, with reference to free radical polymerization as the most common route to high polymer. • To emphasize the importance of stabilization of the charged reactive center on the growing chain. • To develop expressions for the average degree of polymerization and molecular weight distribution for anionic polymerization. • To introduce the concept of a “living” polymerization. • To emphasize the utility of anionic and living polymerizations in the synthesis of block copolymers. Effect of Substituents on Chain Mechanism Monomer Radical Anionic Cationic Hetero. Ethylene + - + + Propylene - - - + 1-Butene - - - + Isobutene - - + - 1,3-Butadiene + + - + Isoprene + + - + Styrene + + + + Vinyl chloride + - - + Acrylonitrile + + - + Methacrylate + + - + esters • Almost all substituents allow resonance delocalization. • Electron-withdrawing substituents lead to anionic mechanism. • Electron-donating substituents lead to cationic mechanism. Overview of Ionic Polymerization: Selectivity • Ionic polymerizations are more selective than radical processes due to strict requirements for stabilization of ionic propagating species. Cationic: limited to monomers with electron- donating groups R1 | RO- _ CH =CH- CH =C 2 2 | R2 Anionic: limited to monomers with electron- withdrawing groups O O || || _ -C≡N -C-OR -C- Overview of Ionic Chain Polymerization: Counterions • A counterion is present in both anionic and cationic polymerizations, yielding ion pairs, not free ions. Cationic:~~~C+(X-) Anionic: ~~~C-(M+) • There will be similar effects of counterion and solvent on the rate, stereochemistry, and copolymerization for both cationic and anionic polymerization. • Formation of relatively stable ions is necessary in order to have reasonable lifetimes for propagation. -
LIBRARY. This Thesis Has Been Approved for the Department of Chemical Engineering and the College of Engineering and Technology
~.. STUDY OF A COUNTER-ROTATING, INTERMESHING EXTRUDER AS A POLYCONDENSATION REACTOR /" A Thesis Presented to the Faculty of The College of Engineering and Technology Ohio University In Partial Fulfilment of the Requirements for the Degree Master of Science by Edward R. Crowe November, 1992 LIBRARY. This Thesis has been approved for the Department of Chemical Engineering and the College of Engineering and Technology Associate Prof Chem1cal Engineering Dean of the College of Engineering and Technology iii Abstract An experimental study and model development have been performed to better understand the reactive extrusion of polyethylene terephthalate. A process was developed using a 34 mm counter-rotating twin screw extruder to depolymerize a commercial grade of polyethylene terephthalate into an acceptable pre-polymer for reactive extrusion experiments. Residence time d Ls'tr Ibut.Lon experiments were conducted at different screw speeds and feed rates to characterize the flow patterns of the extruder. Based on these results an idealized plug-flow model was developed to simulate this process. An experimental design using the controllable process variables of zone temperature, feed rate and nitrogen flow sweeping across the surface of the polymer melt was developed to stUdy the individual effects of each of these variables as well as any interactive effects. The results indicate that the feed rate and nitrogen flow have an effect on the degree of polymerization of the product. However, the stUdy clearly shows the dominant effect to be ,the average residence time of the polymer melt in the vent zone. The idealized plug-flow model presents a reasonable representation of this process. -
HDPE: High Density Polyethylene LDPE
Abbreviations: HDPE: high density polyethylene LDPE: low density polyethylene PET: polyethylene terephthalate PP: polypropylene PS: polystyrene PVA: polyvinyl alcohol PVC: polyvinyl chloride addition polymerization: a chemical reaction in which simple molecules are linked together to form long chain molecules. amorphous: non-crystalline polymer or non-crystalline areas in a polymer. Bakelite: a polymer produced by the condensation of phenol and formaldehyde. branched polymer: polymer having smaller chains attached to the polymer backbone. cellulose: a natmal polymer found in wood and other plant material. composite polymer: a filled or reinforced plastic. condensation polymer: one in which two or more molecules combine resulting in elimination of water or other simple molecules, with the process being repeated to form a long chain molecule. configuration: related chemical structme produced by the making and breaking ofprimary valence bonds. copolymer: a macromolecule consisting of more than one type of building unit. creep: cold flow of a polymer. cross-linking: occms when primary valence bonds are formed between separate polymer molecules. crystalline polymer: polymer with a regular order or pattern of molecular arrangement and a sharp melting point. dimer: a polymer containing two monomers. domains: sequences or regions in block copolymers. elastomer: a type of polymer that exhibits rubber-like qualities. Ekonol: a moldable, high temperatme polymer. end group: functional group at the end of a chain in polymers, e.g. carboxylic group. extrusion: a fabrication process in which a heat-softened polymer is forced continually by a screw through a die. filler: a relatively inert material used as the discontinuous phase of a polymer composite. free radical: A chemical component that contains a free electron which covalently bonds with a free electron on another molecule. -
Synthesis of Functionalized Polyamide 6 by Anionic Ring-Opening Polymerization Deniz Tunc
Synthesis of functionalized polyamide 6 by anionic ring-opening polymerization Deniz Tunc To cite this version: Deniz Tunc. Synthesis of functionalized polyamide 6 by anionic ring-opening polymerization. Poly- mers. Université de Bordeaux; Université de Liège, 2014. English. NNT : 2014BORD0178. tel- 01281327 HAL Id: tel-01281327 https://tel.archives-ouvertes.fr/tel-01281327 Submitted on 2 Mar 2016 HAL is a multi-disciplinary open access L’archive ouverte pluridisciplinaire HAL, est archive for the deposit and dissemination of sci- destinée au dépôt et à la diffusion de documents entific research documents, whether they are pub- scientifiques de niveau recherche, publiés ou non, lished or not. The documents may come from émanant des établissements d’enseignement et de teaching and research institutions in France or recherche français ou étrangers, des laboratoires abroad, or from public or private research centers. publics ou privés. Logo Université de cotutelle THÈSE PRÉSENTÉE POUR OBTENIR LE GRADE DE DOCTEUR DE L’UNIVERSITÉ DE BORDEAUX ET DE L’UNIVERSITÉ DE LIEGE ÉCOLE DOCTORALEDE SCIENCES CHIMIQUES (Université de Bordeaux) ÉCOLE DOCTORALE DE CHIMIE (Université de Liège) SPÉCIALITÉ POLYMERES Par Deniz TUNC Synthesis of functionalized polyamide 6 by anionic ring-opening polymerization Sous la direction de Stéphane CARLOTTI et Philippe LECOMTE Soutenue le 30 octobre 2014 Membres du jury: M. PERUCH, Frédéric Directeur de recherche, Université de Bordeaux Président M. HOOGENBOOM, Richard Professeur, Ghent University Rapporteur M. MONTEIL, Vincent Chargé de recherche, Université Claude Bernard Rapporteur M. YAGCI, Yusuf Professeur, Istanbul Technical University Examinateur M. AMEDURI, Bruno Directeur de recherche, Institut Charles Gerhardt Examinateur M. SERVANT, Laurent Professeur, Université de Bordeaux Invité Preamble This PhD had been performed within the framework of the IDS FunMat joint doctoral programme. -
Trade Names and Manufacturers
Appendix I Trade names and manufacturers In this appendix, some trade names of various polymeric materials are listed. The list is intended to cover the better known names but it is by no means exhaustive. It should be noted that the names given may or may not be registered. Trade name Polymer Manufacturer Abson ABS polymers B.F. Goodrich Chemical Co. Acrilan Polyacrylonitrile Chemstrand Corp. Acrylite Poly(methyl methacrylate) American Cyanamid Co. Adiprene Polyurethanes E.I. du Pont de Nemours & Co. Afcoryl ABS polymers Pechiney-Saint-Gobain Alathon Polyethylene E.I. du Pont de Nemours & Co. Alkathene Polyethylene Imperial Chemical Industries Ltd. Alloprene Chlorinated natural rubber Imperial Chemical Industries Ltd. Ameripol cis-1 ,4-Polyisoprene B.F. Goodrich Chemical Co. Araldite Epoxy resins Ciba (A.R.L.) Ltd. Arnel Cellulose triacetate Celanese Corp. Arnite Poly(ethylene terephthalate) Algemene Kunstzijde Unie N.Y. Baypren Polychloroprene Farbenfabriken Bayer AG Beetle Urea-formaldehyde resins British Industrial Plastics Ltd. Ben vic Poly(vinyl chloride) Solvay & Cie S.A. Bexphane Polypropylene Bakelite Xylonite Ltd. Butacite Poly( vinyl butyral) E.I. du Pont de Nemours & Co. Butakon Butadiene copolymers Imperial Chemical Industries Ltd. Butaprene Styrene-butadiene copolymers Firestone Tire and Rubber Co. Butvar Poly(vinyl butyral) Shawinigan Resins Corp. Cap ran Nylon 6 Allied Chemical Corp. Carbowax Poly(ethylene oxide) Union Carbide Corp. Cariflex I cis-1 ,4-Polyisoprene Shell Chemical Co. Ltd. Carina Poly(vinyl chloride) Shell Chemical Co. Ltd. TRADE NAMES AND MANUFACTURERS 457 Trade name Polymer Manufacturer Carin ex Polystyrene Shell Chemical Co. Ltd. Celcon Formaldehyde copolymer Celanese Plastics Co. Cellosize Hydroxyethylcellulose Union Carbide Corp. -
Polymer Exemption Guidance Manual POLYMER EXEMPTION GUIDANCE MANUAL
United States Office of Pollution EPA 744-B-97-001 Environmental Protection Prevention and Toxics June 1997 Agency (7406) Polymer Exemption Guidance Manual POLYMER EXEMPTION GUIDANCE MANUAL 5/22/97 A technical manual to accompany, but not supersede the "Premanufacture Notification Exemptions; Revisions of Exemptions for Polymers; Final Rule" found at 40 CFR Part 723, (60) FR 16316-16336, published Wednesday, March 29, 1995 Environmental Protection Agency Office of Pollution Prevention and Toxics 401 M St., SW., Washington, DC 20460-0001 Copies of this document are available through the TSCA Assistance Information Service at (202) 554-1404 or by faxing requests to (202) 554-5603. TABLE OF CONTENTS LIST OF EQUATIONS............................ ii LIST OF FIGURES............................. ii LIST OF TABLES ............................. ii 1. INTRODUCTION ............................ 1 2. HISTORY............................... 2 3. DEFINITIONS............................. 3 4. ELIGIBILITY REQUIREMENTS ...................... 4 4.1. MEETING THE DEFINITION OF A POLYMER AT 40 CFR §723.250(b)... 5 4.2. SUBSTANCES EXCLUDED FROM THE EXEMPTION AT 40 CFR §723.250(d) . 7 4.2.1. EXCLUSIONS FOR CATIONIC AND POTENTIALLY CATIONIC POLYMERS ....................... 8 4.2.1.1. CATIONIC POLYMERS NOT EXCLUDED FROM EXEMPTION 8 4.2.2. EXCLUSIONS FOR ELEMENTAL CRITERIA........... 9 4.2.3. EXCLUSIONS FOR DEGRADABLE OR UNSTABLE POLYMERS .... 9 4.2.4. EXCLUSIONS BY REACTANTS................ 9 4.2.5. EXCLUSIONS FOR WATER-ABSORBING POLYMERS........ 10 4.3. CATEGORIES WHICH ARE NO LONGER EXCLUDED FROM EXEMPTION .... 10 4.4. MEETING EXEMPTION CRITERIA AT 40 CFR §723.250(e) ....... 10 4.4.1. THE (e)(1) EXEMPTION CRITERIA............. 10 4.4.1.1. LOW-CONCERN FUNCTIONAL GROUPS AND THE (e)(1) EXEMPTION................. -
Chain-Growth Polymerization, Version of 1/5/05
Chapter Three, Chain-growth polymerization, Version of 1/5/05 3 Chain-growth polymerization 3.1 Introduction We indicated in Chapter 1 that the category of addition polymers is best characterized by the mechanism of the polymerization reaction, rather than by the addition reaction itself. This is known to be a chain mechanism, so in the case of addition polymers we have chain reactions producing chain molecules. One thing to bear in mind is the two uses of the word chain in this discussion. The word chain continues to offer the best description of large polymer molecules. A chain reaction, on the other hand, describes a whole series of successive events triggered by some initial occurrence. We sometimes encounter this description of highway accidents in which one traffic mishap on a fogbound highway results in a pileup of colliding vehicles that can extend for miles. In nuclear reactors a cascade of fission reactions occurs which is initiated by the capture of the first neutron. In both of these examples some initiating event is required. This is also true in chain-growth polymerization. In the above examples the size of the chain can be measured by considering the number of automobile collisions that result from the first accident, or the number of fission reactions which follow from the first neutron capture. When we think about the number of monomers that react as a result of a single initiation step, we are led directly to the degree of polymerization of the resulting molecule. In this way the chain mechanism and the properties of the polymer chains are directly related. -
Poly(Sodium Acrylate)-Based Antibacterial Nanocomposite Materials
Poly(Sodium Acrylate)-Based Antibacterial Nanocomposite Materials Samaneh Khanlari Thesis submitted to the Faculty of Graduate and Postdoctoral Studies in partial fulfillment of the requirements for the degree of Doctorate in Philosophy in Chemical Engineering Department of Chemical and Biological Engineering Faculty of Engineering UNIVERSITY OF OTTAWA © Samaneh Khanlari, Ottawa, Canada, 2015 i ii Abstract Polymer-based bioadhesives for sutureless surgery provide a promising alternative to conventional suturing. In this project, a new poly(sodium acrylate)-based nanocomposite with antibacterial properties was developed. Poly(sodium acrylate), was prepared using a redox solution polymerization at room temperature; this polymer served as a basis for a nanocomposite bioadhesive material using silver nanoparticles. In-situ polymerization was chosen as a nanocomposite synthesizing method and three methods were applied to quantify the distribution and loadings of nanofiller in the polymer matrices. These included the Voronoi Diagram, Euclidean Minimum Spanning Tree (EMST) method and pixel counting. Results showed that pixel counting combined with the EMST method would be most appropriate for nanocomposite morphology quantification. Real-time monitoring of the in-situ polymerization of poly(sodium acrylate)- based nanocomposite was investigated using in-line Attenuated Total Reflectance/Fourier Transform infrared (ATR-FTIR) technique. The ATR-FTIR spectroscopy method was shown to be valid in reaction conversion monitoring using a partial least squares (PLS) multivariate calibration method and the results were consistent with the data from off-line water removal gravimetric monitoring technique. Finally, a second, more degradable polymer (i.e., gelatin and poly(vinyl alcohol)) was used to modify the degradation rate and hydrophilicity of the nanocomposite bioadhesive. -
Synthesis and Characterization of Solution and Melt Processible Poly(Acrylonitrile-Co-Methyl Acrylate) Statistical Copolymers
SYNTHESIS AND CHARACTERIZATION OF SOLUTION AND MELT PROCESSIBLE POLY(ACRYLONITRILE-CO-METHYL ACRYLATE) STATISTICAL COPOLYMERS Padmapriya Pisipati Dissertation submitted to the faculty of the Virginia Polytechnic Institute and State University in partial fulfillment of the requirements for the degree of Doctor of Philosophy in Macromolecular Science and Engineering James E. McGrath, Chair Judy S. Riffle, Acting Chair Eugene G. Joseph Sue J. Mecham Donald G. Baird 02/20/2015 Blacksburg, VA Keywords: melt processability, polyacrylonitrile, carbon fibers, methyl acrylate, acrylic fibers, plasticizer, solution processing, high tensile modulus Copyright 2015, Padmapriya Pisipati SYNTHESIS AND CHARACTERIZATION OF SOLUTION AND MELT PROCESSIBLE POLY (ACRYLONITRILE-CO-METHYL ACRYLATE) STATISTICAL COPOLYMERS ABSTRACT Padmapriya Pisipati Polyacrylonitrile (PAN) and its copolymers are used in a wide variety of applications ranging from textiles to purification membranes, packaging material and carbon fiber precursors. High performance polyacrylonitrile copolymer fiber is the most dominant precursor for carbon fibers. Synthesis of very high molecular weight poly(acrylonitrile-co-methyl acrylate) copolymers with weight average molecular weights of at least 1.7 million g/mole were synthesized on a laboratory scale using low temperature, emulsion copolymerization in a closed pressure reactor. Single filaments were spun via hybrid dry-jet gel solution spinning. These very high molecular weight copolymers produced precursor fibers with tensile strengths averaging 954 MPa with an elastic modulus of 15.9 GPa (N = 296). The small filament diameters were approximately 5 µm. Results indicated that the low filament diameter that was achieved with a high draw ratio, combined with the hybrid dry-jet gel spinning process lead to an exponential enhancement of the tensile properties of these fibers. -
Polymer Chemistry
CLOTHWORKERS LIBRARY UNIVERSITY OF LEEDS THERMAL AND OXIDATIVE DEGRADATION OF AN AROMATIC POLYAMIDE. by «. Shojan Nanoobhai Patel 2. Submitted in accordance with the requirement for the degree of Doctor of Philosophy under the supervision of Professor I.E. McIntyre and Dr. S.A. Sills. The candidate confirms that the work submitted is his own and that appropriate credit has been given where reference has been made to work of others. Department of Textile Industries, The University of Leeds, Leeds, LS2 9JT. December 1992. CLASS MARK T:; ~S 2tC\4 -1- ABSTRACT. The thermal oxidation of an aromatic polyamide fibre, namel\' poly(m-xylylene adipamide) has been investigated. The volatile and non-volatile products of oxidation identified using T.L.C., H.P.L.C. and G.C.-M.S. include homologous series of monocarboxylic acids, dicarboxylic acids, n-alkyl amines, diamines and aldehydes. Furthermore, several aromatics, ketones and amides were also identified. Mechanisms for their derivation have been proposed which are based on oxidation reactions already established in polymer chemistry. These include a mechanism of ~ scission by an alkoxy radical thought to be responsible for the creation of the homologous series. MXD,6 fibres were also spun incorporating 100, 200 and 400ppm of a cobalt catalyst and the effect of the metal ions on the oxygen uptake of the fibres was investigated. The results show a consistent increase in the rate of oxygen uptake as the concentration of the cobalt is increased. Furthermore, T.G.A. oxidative degradation studies, conducted at isothermal temperatures in the solid state, show decreases in the activation energies associated with fibre oxidation with increased cobalt concentrations, implying the cobalt is a catalyst for oxidation.