Machining of the Gill Corporation Composite Products
Total Page:16
File Type:pdf, Size:1020Kb
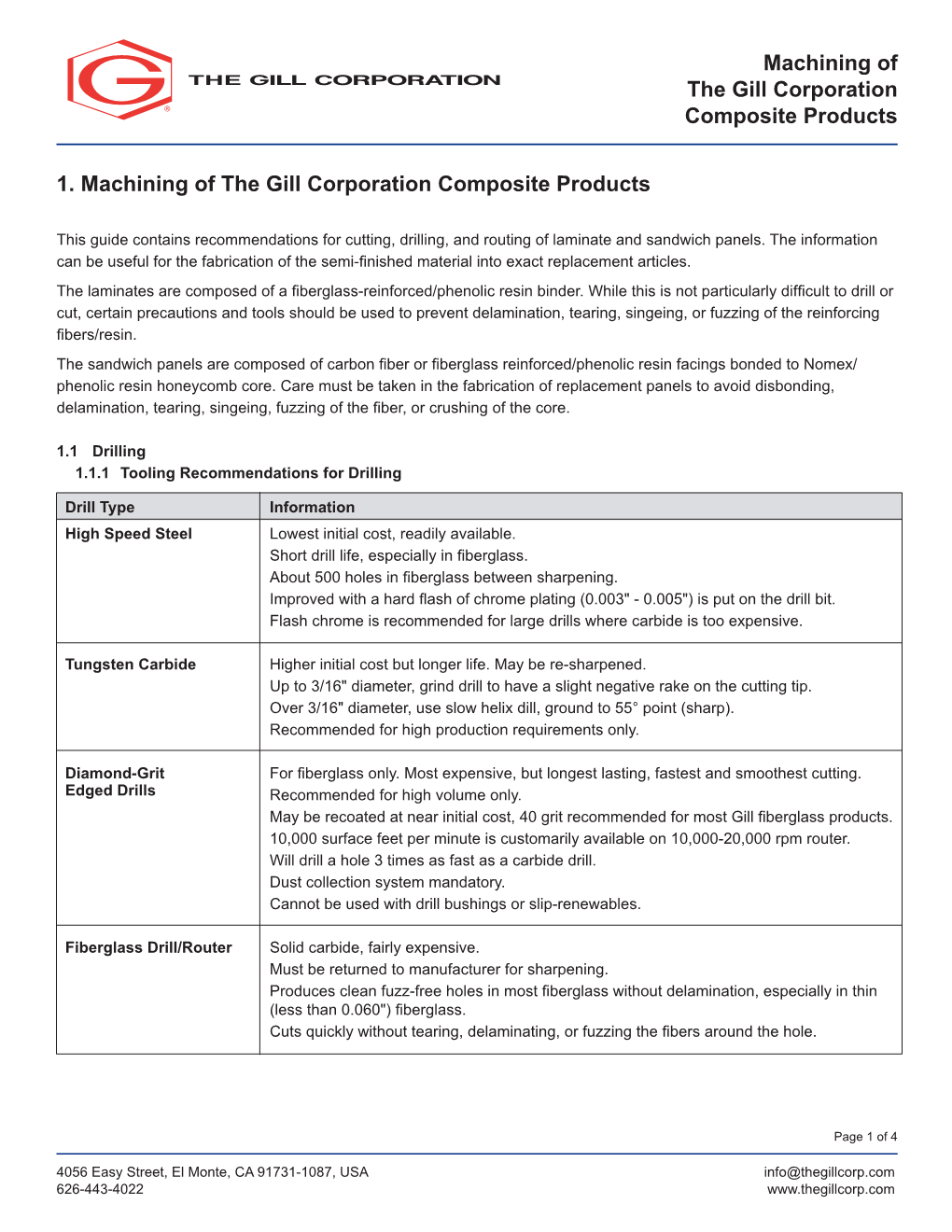
Load more
Recommended publications
-
Drill Bushing Installation Data
DRILL BUSHING INSTALLATION DATA Drill Bushing Installation Data Explained below are the basic steps to installing a drill bushing. Because there are many different situations that bushings are used in and many variables associated with the installation, no definite rules can substitute for the skill and judgment of the experienced tool-maker. If you have any questions about the proper use or installation of any of our products, please be free to contact our technical support team. Step 1 Step 2 Hole Drilling and Preparation Inserting The Bushing Drill hole using the 'jig boring data' (see next page) to determine Use an arbor press to press the bushing into the jig-plate the correct size of the hole also keeping in mind interference fits, whenever possible. If not, use some other method such as hole roundness, and alignment (see below). Always drill holes drawing the bushing into the jig-plate with two washers and a nut using a jig borer or reamer. Next lubricate the inside diameter of and bolt. A hammer should only be used if no other method is the mounting hole and the outside diameter of the bushing. possible, and never directly strike the bushing with the hammer; Lubrication is important because bushings that are installed use a block to take the blows of the hammer. Whichever method without lubrication may pick up metal and score the mounting is used be sure to maintain centerline perpendicularity, otherwise hole during installation. Lubricated bushings are also more easily inaccuracy may result in the production operation. removed with less chance of damaging the jig-plate. -
Grinding Fixture Botek
DEEP HOLE DRILLING SYSTEMS SOLID CARBIDE TOOLS Grinding machine Grinding fixture botek For regrinding single flute gundrills from Ø 0.5 mm The botek company Manufacturing deep and precise holes is a technical challenge when processing metal. Accordingly specializing on deep hole drilling technology had been the founding idea in 1974 of botek Präzisionsbohrtechnik GmbH in Riederich. botek grew to an international operating deep hole drilling tools supplier. Over 500 employees in the main company develop and manufacture single and two fluted drills, deep hole drilling tools system BTA and Ejector as well as special tools. A complete product program, regarding all deep hole drilling aspects and a team of highly qualified and dedicated cutting specialists make botek being a competent partner for the automobile industry and their suppliers, shipbuilding industry, hydraulic industry as well as motor, gear and machine building companies. • Please note our safety pointers at www.botek.de. • Our General Standard Terms and Conditions, which we assume as known, apply. • We reserve the right to make modifications in the interests of technical improvement. Such modifications cannot, in principle, be accepted as justificable reasons for complaint. • Subject to change. The manufacturer accepts no responsibility for misprints and other errors. © botekUSA 2 botek – your expert partner for deep hole drilling tools Contents P. 2 The botek company Terms and Conditions, Important information P. 3 Contents P. 4 Grinding machine MS-12 and MS 12/3 P. 5 Accessories MS-12 and MS12/3 Grinding wheels/tool holders P. 6 Grinding machine MS-01 Accessories MS-01 P. 7 Accessories MS-01 Grinding fixture type PS P. -
Feb. 15', 1927. 1,617,554
Feb. 15', 1927. 1,617,554 . e. E._ SWARTZ DRILL B'dsaI-ne Filed Dec. 16, 1925" 8 v .7 v 1 Patented‘' UNHTEEE Feb. 15, 1927. or ' 1,617,554 ' FATEWorries.~ ) GUY-E.‘ SXVARTZ, OF DETRQIT, MICHIGAN. ' ' ‘ DRILL BUSHING. .. ' Application ?led December ~1e,>1a25l Serial No. 75,683. _ _ ;In the drilling of metals considerable ‘for a drill, the said bushingibeing provided trouble is oftenv experienced from the (forma with a downwardly openingconical or ‘?ared tion of long chips or cuttings which fit is nmuth and withlupwardly extend-ing grooves often necessary to remove manually and .in the wall-of the bore thereof, the said which often results in the hands of the opera grooves being "widened at’ their lower ends tor being cut, although this danger is some to receive the extremities of chips'or cuttings timesavoided-by the use ofa hook. In any travelling upwardly-on the drill whereby the V case the necessity for such removal of the spiral. progress of thesa'id cuttings is inter ' chips presents an inconvenience and in many rupted and; they tend to travel‘ upwardly 10 cases slows up the work,,as they have ‘a through! , the said ‘grooves, f with " the v‘result tendency to wind upward ‘on the drill and “that, as the drill revolves, the said cuttings their frequent removal occupies a certain are broken'into small pieces and, fall from - amount of times and. ‘distracts the operator’s the mouth of the said bushingon to the'work attentionfrom the, work. - i or work table. ' ' , ‘ > _ it i I‘ 70 15 ' “There drill jigs are employed it is usual 4 All ofnwhich' is morejlparticularly de ' toemploy a bushing for the guidance of the V scribed and ascertained hereinafterrby way drill, and the presence ofunbroken chips or of ‘example, having reference to the¢accom~ cuttings winding upwardly on the drill fre panying drawing, wherein-é quently necessitates removing the‘bushing-or vFigure l is an elevation partlyin section. -
Aug. 13, 1968 B. HUTTON 3,396,613 JIG for USE with a MACHINE TOOL Filed Feb
Aug. 13, 1968 B. HUTTON 3,396,613 JIG FOR USE WITH A MACHINE TOOL Filed Feb. 25, 1966 2. Sheets-Sheet 1 s 424INVENTOR ray2/772-y 2,744 477/2A/A113 Aug. 13, 1968 B. HUTON 3,396,613 JIG FOR USE WITH A MACHINE TOOL Filed Feb. 25, 1966 . 2 Sheets-Sheet 2 INVENTOR. 47/4 - A72/ 24,444 a77.26%A17 3,396,613 United States Patent Office Patented Aug. 13, 1968 2 used are undersized to properly guide the undersize drill. 3,396,613 After the drilling operation, a second and larger drill JG FOR USE WITH A MACHINE TOOL bushing is used to guide the reamer in the finishing of the Billy Hutton, 1594 Paloma, Pasadena, Calif. 91104 hole. Filed Feb. 25, 1966, Ser. No. 529,996 Briefly, this invention provides a new and novel jig for 1 Claim. (C. 77-55) use with a machine tool of a class utilizing a cutting tool which rotates about its longitudinal axis above a table or platform in position to bear on and fabricate a hole in a ABSTRACT OF THE DISCLOSURE workpiece. The jig is in the form of a rigid structure hav The jig has a first and a second end rigidly connected O ing one end adapted to be fixedly and demountably at through a tapered beam. The beam converges from the tached to a stationary portion of the machine tool. The first end to the second end. The first end has a mortise for other or second end of the jig is adapted to be disposed attaching the jig to the tenon of a machine tool such that |Substantially normal to the axis of rotation of the cut the second end depends downwardly and outwardly from ting tool, proximate to the table, and above the work the first end. -
Head Press Fit Bushings
+44 (0)1204 699959 [email protected] www.hyquip.co.uk/web/index H HEAD PRESS FIT H-20-16U-.1250 Unground OD H-20-16-.1250 REAMER Reamer tolerance on ID H-20-16-.1250 NCB No counterbore on long bushings marked with * (no counterbore is standard on all other bushings) HC-20-16-.1250 Carbide bushing HM-8-12-4.50 Standard metric bushing Standard prices apply only to bushings with a standard-drill- size ID with the stated ID range. See catalog back cover for standard drill sizes and their decimal equivalents. For prices on non-standard ID sizes, including reamer-tolerance and tap- USA METRIC guide bushings, please contact factory. BODY BODY F DIA G F DIA G OD OD STANDARD ID TOLERANCES: 5/32 1/4 3/32 4mm 7mm 2mm From #80 to 1/4” +.0001/+.0004 From .35 to 3mm +.002/+.008mm 13/64 19/64 3/32 5mm 8mm 2mm Over 3 to 6mm +.004/+.012mm 1/4 23/64 3/32 6mm 9mm 2.5mm Over 1/4 to 3/4” +.0001/+.0005 Over 6 to 10mm +.005/+.014mm 5/16 27/64 1/8 7mm 10mm 2.5mm Over 10 to 18mm +.006/+.017mm 1/2 3/32 8mm 11mm 2.5mm 3/8 Over 3/4 to 1-1/2” +.0002/+.0006 Over 18 to 30mm +.007/+.020mm 13/32 1/2 5/32 10mm 13mm 3mm Over 30 to 50mm +.009/+.025mm 7/16 9/16 3/32 12mm 15mm 3mm Over 1-1/2 to 2-3/4” +.0003/+.0007 Over 50 to 80mm +.010/+.029mm 1/2 39/64 7/32 15mm 18mm 3mm 9/16 11/16 3/32 18mm 22mm 4mm Over 80 to 120mm +.012/+.034mm 5/8 51/64 7/32 22mm 26mm 4mm (G6 tolerance) 3/4 59/64 7/32 26mm 30mm 4mm 7/8 1-7/64 1/4 30mm 34mm 5mm REAMER ID TOLERANCES: 1 1-15/64 5/16 35mm 39mm 5mm From #60 a 1/4” +.0005/+.0008 From 1 to 3mm +.006/+.012mm 42mm 46mm 5mm 1-1/4 1-1/2 1/4 Over 3 to 6mm +.010/+.018mm 1-3/8 1-39/64 3/8 48mm 52mm 5mm Over 1/4 to 1” +.0006/+.0010 Over 6 to 10mm +.013/+.022mm 1-3/4 1-63/64 3/8 55mm 59mm 5mm Over 10 to 18mm +.016/+.027mm 2-1/4 2-31/6 3/8 62mm 66mm 6mm 70mm 74mm 6mm Over 1 to 1-1/2” +.0008/+.0012 Over 18 to 30mm +.020/+.033mm 78mm 82mm 6mm (F6 tolerance) 85mm 90mm 6mm ID ANSI PRICE 95mm 100mm 6mm OD LENGTH RANGE PART NO. -
While Rigid, Accurate CNC Machine Tools and Modern Drill Designs
MARCH 2005 / VOLUME 57 / NUMBER 3 special focus: holemaking ➤ BY BILL KENNEDY, CONTRIBUTING EDITOR STEADYSTEADY as it guides While rigid, accurate CNC machine tools and modern drill designs minimize the need for drill bushings, the well-proven concept remains a valuable tool for select applications. or decades, drill bush- Drill bushings ings were required for Side view F precision holemaking Jig operations. A shop would Locking screw build a fixture to lock in the Workpiece relative positions of the Top view Location pins drill and part, then use a jig Jigjig fitted with a hardened-steel bushing to guide the drill. Such setups ensured that Workpiece the drill entered the work- piece straight and produced Drill bushings an accurate hole. It also eliminated the need for B. Kennedy pilot holes; prevented drill In a classic drill bushing setup, a jig is located and wandering and chatter locked onto the workpiece to assure repeatable when drilling holes in an- positioning of the drill bushings and resultant holes. gled surfaces; provided sta- bility when drill overhang was exces- ago, automotive plants employed sive; and reduced tool breakage. transfer lines with dedicated machines Today, drill bushing use is in decline. arranged in multiple stations. “They The main reasons are the emergence of would use drill bushings at every sta- rigid, fast CNC machine tools and ad- tion where they used a drill,” he said. vanced drill designs. CNC machines Today, most automotive work is done can apply a spot drill and quickly fol- on CNC machines, where “there usu- low it with the drill that penetrates to ally isn’t space in the fixture to mount the specified depth. -
Drill and Router Guides Pressure Foot Value from UNITED! Drilling Systems
Drill and Router Guides Pressure Foot Value From UNITED! Drilling Systems PRESSURE FOOT ADATPERS Page C8 DRILL GUIDE NOSEPIECE Page C6 DRILL GUIDE TIP PRESSURE FOOT ASSEMBLY Page C7 ROUTER COLLAR GUIDES Page C24 Page C23 DG DRILL GUIDES Page C10 DRILL GUIDE TIPS Page C23 DGA DRILL GUIDES Page C11 PRESSURE FOOT NOSEPIECES Page C22 DGF DRILL GUIDES Page C13 DRILL GUIDE BUSHING ADATPERS Page C9 PRESSURE FOOT ADATPERS Page C22 DGMD DRILL GUIDES Page C19 DGI DRILL GUIDES Page C14 DGMC DRILL GUIDES Page C15 DGMK DRILL GUIDES Page C20 12200 WOODRUFF AVE. • DOWNEY, CA 90241-5608 • TELEPHONE (562) 803-1521 / (800) 421-3466 IN CA / (800) 486-3466 • FAX (562) 803-6898 / (800) 486-3465 5-26-04 EMAIL [email protected] WEBSITE www.ucc-udb.com C1 Drill Guide Bushings Pressure Foot System With Drill Guide Bushings Drill Details on the next 26 pages will increase your speed and decrease your costs. Air Mist Coolant will produce more holes at less cost than any other drill and drill motor method. Drill instant holes Rivet holes up to 1/2" with UNITED's High or other undersized Speed Pressure Foot fasteners are Drilling System. efficiently drilled. Drill speeds up to 22,000 RPM or more are all available. FASTER — BETTER Enjoy AT LOWER COST! Pressure Foot Economy! C2 UNITED Guides You on Guides For Your Job! 3-16-99 Quick— Cool Pressure Foot Drilling Application And Critical UNITED's Pressure Foot Drilling System should be APPLICATION used for all tooling applications where hand drilling operations are performed. -
Avoid Set up Delays Liners Sets in Cases
Gun Drill Master Avoid Set Up Delays Liners Sets in Cases UNITED GUN DRILL MASTER LINER SETS With a UNITED GDL MASTER GUN DRILL LINER SET you avoid set up delays and increase your gun drill guiding capacity. Each set covers minimum to maximum GDI Insert ranges. Liners store easily in a durable polyethylene case. GDL-64B CASE GDL-88B CASE GDL-112B GUN DRILL MASTER LINER CASE SETS in CASES AVAILABLE: CASES ONLY SELECT YOUR O.D. 1" O.D. 1-3/8 O.D. 1-3/4 O.D. 2-1/4 O.D. SET: GDL-64 SET: GDL-88 SET: GDL-112 SET: GDL-144 Set of FIVE 1" O.D. by 1" long Set of SIX 1-3/8 O.D. by 1-3/8 long Set of SEVEN 1-3/4 O.D. by 1-3/4 Set of FOUR 2-1/4 O.D. by 2-1/8 GDL Gun Drill Bushing Master GDL Gun Drill Bushing Master long GDL Gun Drill Bushing Mas- long GDL Gun Drill Bushing Mas- Liners. Liners. ter Liners. ter Liners. GD MASTER USE WITH 1/2" GD MASTER USE WITH 3/4" GD MASTER USE WITH 1" GD MASTER USE WITH 1-1/4" LINER LONG INSERTS LINER LONG INSERTS LINER LONG INSERTS LINER LONG INSERTS GDL-64-16-13 13/64 O.D. GDL-88-22-13 13/64 O.D. GDL-112-28-13 13/64 O.D. GDL-144-34-48 3/4 O.D. GDL-64-16-16 1/4 O.D. GDL-88-22-16 1/4 O.D. -
V TC 9-524 I
✽ TC 9-524 i Preface The purpose of this training circular is to provide a better understanding of power-driven machine tools. It also supplements technical manuals in the 9-3400-series covering power-driven machine tools. One of the main objectives is for this publication is to be clear and understandable. Illustrations throughout this publication show the step-by-step process of many machine shop operations. The tables, charts, formulas, weights, and measurements in this publication can be a ready reference for selecting the proper tooling and math formulas for machining different materials. The proponent of this publication is HQ TRADOC. Send comments and recommendations on DA Form 2028 directly to the Department of the Army, Training Directorate, ATTN: ATCL-AO, 801 Lee Avenue, Fort Lee, Virginia 23801-1713. Unless this publication states otherwise, masculine nouns and pronouns do not refer exclusively to men. TC 9-524 Preface The purpose of this training circular is to provide a better understanding of power-driven machine tools. It also supplements technical manuals in the 9-3400-series covering power-driven machine tools. One of the main objectives is for this publication is to be clear and understandable. Illustrations throughout this publication show the step-by-step process of many machine shop operations. The tables, charts, formulas, weights, and measurements in this publication can be a ready reference for selecting the proper tooling and math formulas for machining different materials. The proponent of this publication is HQ TRADOC. Send comments and recommendations on DA Form 2028 directly to the Department of the Army, Training Directorate, ATTN: ATCL-AO, 801 Lee Avenue, Fort Lee, Virginia 23801-1713. -
DRILLING OPERATIONS Chucking the Drill Drilling Holes
Drilling and Countersinking 83 DRILLING OPERATIONS Chucking the Drill WARNING Before installing or removing drill bits, countersinks, or other devices in an air motor, be sure that the air line to the motor is disconnected. Failure to observe this precaution can cause serious injury. Install proper drill in the motor and tighten with proper size chuck key. Be sure to center the drill in the chuck. Do not allow flutes to enter the chuck. Connect the air hose to the motor inlet fitting. 3. Start the drill motor and check the drill for wobble. The drill must run true, or an oversize hole will be made. Replace bent drills. Drilling Holes 1. Hold the motor firmly. Hold the drill at 90° angle to the surface, as shown in Fig. 4-7. Fig. 4-7. Square drill with work. 2. Start the hole by placing the point of the drill on the marked centerline. With the fingers, turn the chuck un- til an indentation is made. (Omit this step when drilling through a drill bushing or when a pilot hole ex- ists.) 84 Standard Aircraft Handbook Position thumb and forefinger to prevent the drill from going too far through the work, which can cause dam- age to items on the other side or result in an oversized hole. Drill the hole by starting the drill motor and exerting pressure on the centerline of the drill. Exert just enough pressure to start the drill cutting a fairly large size of chip and maintain this pressure until the drill starts to come through the work. -
Carr Lane Drill Jig Bushing Catalog
E&E SPECIAL PRODUCTS 7200 MILLER DRIVE, WARREN, MI 48092, 586-978-3377 PRECISION DRILL JIG BUSHINGS AuthorizedAuthorized Distributor: Distributor: PRINTED IN U.S.A. © COPYRIGHT 2008 CARR LANE MANUFACTURING CO. 11952-703 E&E SPECIAL PRODUCTS 7200 MILLER DRIVE, WARREN, MI 48092, 586-978-3377 E&E SPECIAL PRODUCTS 7200 MILLER DRIVE, WARREN, MI 48092, 586-978-3377 WHAT MAKES A CARR LANE DRILL BUSHING BETTER? Carr Lane drill bushings are all 1 precision honed and ground, the finest quality available. They exceed all ANSI drill-bushing TOP standards. Unlike some of our competitors, we manufacture only QUALITY first-quality drill bushings, never “economy grade.” Our nationwide network of stocking 2 distributors, plus huge inventories at two warehouse locations, guarantees same-day shipment for FAST standard bushings. In addition, our quick-response manufacturing capabilities allow us to ship almost DELIVERY all special and modified bushings in less than 10 days. Main Factory Drill Bushing Factory and Warehouse Austin, Texas St. Louis, Missouri 3 As you expect with all Carr Lane products, our drill-bushing prices are the most competitive around. Our ECONOMICAL production volumes and advanced manufacturing techniques mean PRICES $ excellent value for you. E&E SPECIAL PRODUCTS 7200 MILLER DRIVE, WARREN, MI 48092, 586-978-3377 E&E SPECIAL PRODUCTS 7200 MILLER DRIVE, WARREN, MI 48092, 586-978-3377 INDEX Bushing Selection ..............................................................................................................................................................p. 2-3 Installation and Technical Data .........................................................................................................................................p. 4-5 Counterbore Data .................................................................................................................................................................p. 6 H SP P Head Serrated Press Fit Press Fit Press Fit p. 9-13 p. 14-18 p. 19-20 SF FM Slip/Fixed Flat Milled L Liner Renewable Renewable p. -
CETS.Com 2020' Direct Line Sheet Cutting Edge Tool Supply, Inc
Cutting Edge Tool Supply, Inc. 1120-B Elkton Drive, Colorado Springs CO 80907 Phone: (800)769-3343 Fax: (800)697-3343 2020' Direct Line Sheet CETS.com 5th AXIS Carmex Evolution AB Tool Carr Lane Exsys Tool Abbott Workholding Carvesmart Falcon Abrasive Mfg. Advent Tool & Manufacturing Cedarberg Fansteel Albrecht Ceratip Federal (Mahr) Allied Tool Products Ceratizit Fette Aloris CGS Tool Fitz-Rite Amada Chemarrow Four States Industries American Carbide Tool Chick Fowler American Drill Bushing Circle Fraisa USA, Inc. American National Carbide Clausing Gator Chucks APT Cobra Gaylee Arc Abrasives Coffing Hoists Genesse MFG Arch Cutting Tools Cogsdill Glastonbury Gage Arno USA Coilhose Pneumatics Greenleaf Arrow Fasteners Collis Tool Grobet Ash Gear Continental Abrasives GTD Ashburn Craftsman Industries Gusher Pump Atom Precision Inc. Craig Tools H & R Manufacturing Award Cutter Criterion H.B. Rouse Bahco Tool Cutting Tool Technologies Hanita Balax Cyclone Hannibal Carbide Bates Abrasives Daco Jaw Hardinge Benchmark / GWS Darex Hassay Savage Berkshire Data Flute Hayden Twist Drill Best Carbide Deni Tool Hitech Usa Big Kaiser Design-Rite HPI Pioneer Bison Dillon Manufacturing HTC Bondhus Doall Saws Huot Brighton Best Dorian Tool Huron Briney Drill Master Eldorado Ideal Thread Gage Brown & Sharpe Drill-Co Ingersoll Cutting Tools Brubaker Dumont Insize Btc Chucks Dumore Internal Tool Burchette Eagle Rock International Mini-Cut Burr King East Wind Dia Abrasives J & M Diamond Tool C.H. Hanson Edward Andrews Jergens Camel Grinding Wheel Elite Abrasives Jet Abrasives Capco Abrasives Erikson J & M Diamond Tool Carbide Grinding Evencut K.O. Lee Carboloy Everede Kaiser Thin Bit Carborundum Everett Kalamazoo Cutting Edge Tool Supply, Inc.