Bersham Colliery
Total Page:16
File Type:pdf, Size:1020Kb
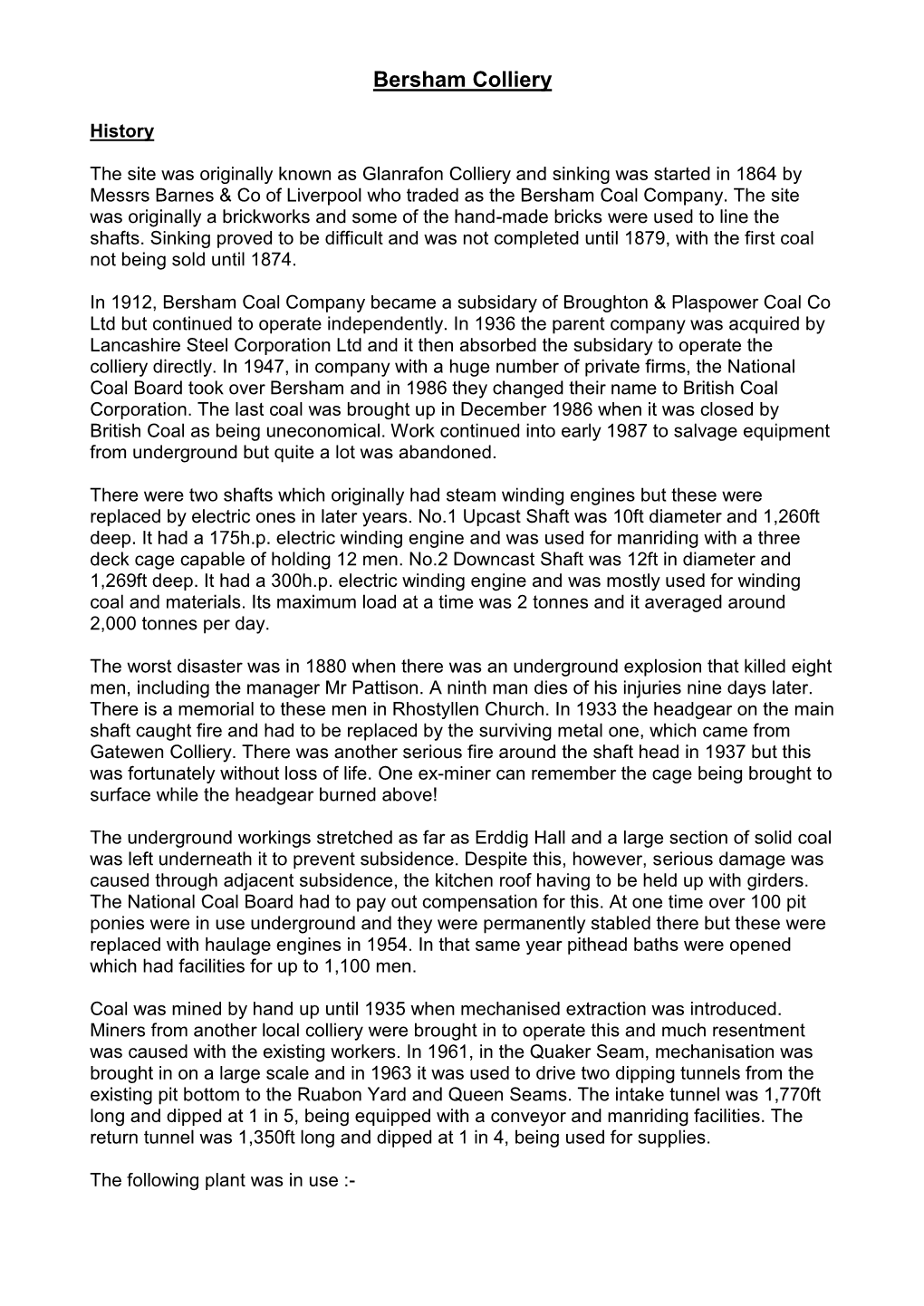
Load more
Recommended publications
-
Maelor Mission Area Magazine
Maelor Mission Area Magazine Inside this issue: • Another (mostly) Good News Edition • Re-opening and recovering July 2020 • Scams Warning 75p per issue Rev’d Canon Sue Huyton Rector of Bangor on Dee Group of Parishes & Mission Area Leader The Rectory, 8 Ludlow Road Bangor-On-Dee Wrexham. LL13 0JG. Tel 01978 780608 [email protected] Rev’d Peter Mackriell Rector of Overton and Erbistock 07795 972325 The Rectory, 4 Sundorne, Overton, Wrexham. LL13 0EB Tel. 01978 710294 [email protected] Rev’d Clive Hughes Vicar of the Hanmer Group of Parishes The Vicarage, Hanmer, Whitchurch, Shropshire. SY13 3DE. Tel 01948 830468 [email protected] MMA Lay Chair: Mr. David Williams, [email protected] Magazine Editor: David Huyton, [email protected] The Maelor Churches are part of the Maelor Mission Area. This magazine has been published by volunteers for well over a century. During that time it has served various groupings of churches. We hope you find it informative, useful, and interesting. You are welcome to respond to any item. Please hand any such contribution to your Vicar. St Dunawd, Bangor on Dee. St Deiniol, Eyton St Deiniol, Worthenbury St Deiniol and St Marcella, Marchwiel St Mary the Virgin, Overton St Hilary, Erbistock St Chad, Hanmer St John the Baptist, Bettisfield Holy Trinity, Bronington St Mary Magdalene, Penley Mission Area News Dear Friends. I am sure that many of you will already have heard about a package of measures being put together to help Mission Areas weather the present financial crisis. As a response to the help we receive, we will be expected to enter a process of review. -
September 2009
Volume 11. Issue 9 September 2009 Overton’s Free Newspaper - issued monthly DIGITAL SWITCHOVER DEADLINE! Overton is positioned right on the edge of three television regions and homes will have chosen to receive TV programmes from one of a variety of transmitters, from Wales, Granada or Central. Therefore there are different dates for the Digital Switchover according to which way your aerial points and which stations you watch. The deadline for the Digital Switchover if you receive BBC Wales, ITV Wales, & S4C is 28th October 2009, for those receiving BBC Northwest and Granada, the deadline is 4th November 2009. and for BBC Midlands and Central (from the Wrekin transmitter) the deadline is not until 2011. So what does this mean for all of us? It means that if you still have an older analogue television, when the analogue signal is switched off you won’t be able to receive any programmes. This doesn’t mean you have to throw out your old TV. There are many ways to continue viewing and some of them are quite cheap. You should have received through the post the leaflet from Digital UK telling you in detail all the options. These can be divided into those that require a one-off payment and those that require a monthly subscription. The details are as follows: - FREEVIEW Digital box from £25.00 More than 40 digital channels Digital TV from £150.00 ONE-OFF FREESAT £150 including minidish, More than 230 digital channels PAYMENT FROM SKY viewing card and standard Skybox installation FREESAT Digital boxes from £50, More than 100 digital channels Dish installation (if required) from £80 SKY From £17—£47 a month Up to 160 digital TV channels plus depending on package, more than230 free to air channels MONTHLY installation costs from £30 SUBSCRIPTION Other suppliers include VIRGIN; BT VISION; TISCALI; TOP-UP TV; WRIGHTS RADIO RELAY LTD with packages including telephone and broadband internet services. -
Date: 06/02/2019 Response/Digest EIR: 9029 Wrexham County
Date: 06/02/2019 Response/Digest EIR: 9029 Wrexham County Borough Council does hold the information requested. Request: Flytipping 1. How many incidents of flytipping were reported to the local authority in the financial year 2017-18? 2. What were the outcomes for these incidents, e.g. fines or court action and what did the local authority do about the rubbish? 3. Which wards had the highest rate of flytipping? Response: 1. 1,159 2. There was no fines or court action in 2017-18. Wrexham Council waste is processed through the MBT facility at the Recycling Centre. 3. The breakdown of incidents per ward is as follows: Ward Fly Tipping Requests Acton 20 Borras Park 8 Bronington 28 Brymbo 20 Bryn Cefn 8 Brynyffynnon 54 Cartrefle 22 Cefn 26 Ceiriog Valley 12 Chirk North 7 Chirk South 7 Coedpoeth 20 Erddig 20 Esclusham 14 Garden Village 6 Gresford East & West 8 Please note that where information is subject to copyright belonging to the Council, you will need to obtain the permission of the Council to re-use it for purposes other than private study or non-commercial research. The Council may charge for re-use. Where third party copyright material is disclosed, you must obtain permission to re-use from the copyright holders concerned. Grosvenor 55 Gwenfro 12 Gwersyllt East & South 31 Gwersyllt North 22 Gwersyllt West 27 Hermitage 6 Holt 63 Johnstown 6 Little Acton 4 Llangollen Rural 7 Llay 34 Maesydre 26 Marchwiel 26 Marford & Hoseley 37 Minera 33 New Broughton 38 Offa 68 Overton 14 Pant 19 Penycae 8 Penycae & Ruabon South 17 Plas Madoc 19 Ponciau 54 Queensway 38 Rhosnesni 7 Rossett 18 Ruabon 9 Smithfield 93 Stansty 8 Whitegate 27 Wynnstay 53 Grand Total 1159 Please note that where information is subject to copyright belonging to the Council, you will need to obtain the permission of the Council to re-use it for purposes other than private study or non-commercial research. -
GRESFORD and AFTER a FIRST-HAND ACCOUNT of THE
GRESFORD and AFTER A FIRST-HAND ACCOUNT OF THE GRESFORD DISASTER. THE GRESFORD COLLIERY EXPLOSION. SEPTEMBER, 22nd. 1934. By Mr Parry-Jones GRESFORD and AFTER A FIRST-HAND ACCOUNT OF THE GRESFORD DISASTER THE GRESFORD COLLIERY EXPLOSION SEPTEMBER, 22nd. 1934 As a Captain of one of the Rescue Teams which were employed directly after the explosion, and later in the recovery of parts of the mine which possibly could be worked, I have often been requested to put into writing my actual experiences during the time that work was being carried out. Many and varied were the reports that appeared in the Press and I wish at this juncture to pay tribute to all the Pressmen and Journalists which at that time were learning all the facts they could get hold of to enable them to place before the Great British Public, the position in which such a huge calamity had placed the little border town of Wrexham. How well they did their job, how hard they worked to do that job night and day, many of them without sleep, and very little food. My hat comes off all the time to these reports who, by their magnificent efforts, were in a very large degree responsible for the great response that was made by the Country to the Appeal made on behalf of those bereaved and destitute by the Mayor of Wrexham and the Lord Mayor of London. Often I have wondered what would have been the position if we had been left to shoulder our burden alone. No, such a thing cannot be considered or contemplated. -
Summer Cloch Maelor 3
Cloch Maelor Coedpoeth & Minera Summer Edition 2019 Welcome to our summer edition of Cloch Wales Air Ambulance: Maelor: Congratulations to Rhos Cllr Paul Pemberton, who has just successfully completed a ‘British Banger’ The weather during spring was somewhat mixed, hav- trek from Wales to Benidorm, raising funds for Wales ing had some light snow, storms with very high winds, Air Ambulance. Travelling 2020 miles, his banger of hail and a fair amount of rain, we also had a number of an old Ford Mondeo never missed a beat! Sadly at sunny and quite warm days. All in all spring passed the time of writing, this old trusty vehicle has been with a fizzle more than with a bang! I am sure we are dispatched to the scrapyard. all keeping our fingers crossed for a warm, if not hot, summer — to have two in succession would be a bo- Paul at present has raised over £3000 for the charity nus, if not a rarity. However, we have to accept what and counting, the final figure is still being calculated, comes, we can not change it, but here is hoping for a but whatever the total is, it will be gratefully received good one. by Wales Air Ambulance. There is much occurring in the village and our sur- By all accounts a good time was had by all, and all in rounding communities during the summer months, and the name of a great facility. Well done to Paul and his I would like to take the opportunity of thanking every- team. one who has made me aware of events and locations of the activities, as it makes my task very much easier. -
Historic House Eg 1
Historic House Hotels Heritage Tour | ItiNerary CLASSIC CULTURE DesigNed for those who waNt to visit aNd eNjoy BritaiN's uNique heritage of beautiful couNtry houses. HISTORIC HOUSES ExperieNce the art of quiNtesseNtial couNtry house liviNg at its best, with award- wiNNiNg restauraNts, health aNd beauty spas, all situated iN beautifully laNdscaped gardeNs. NATIONAL TRUST IN 2008 BodysgalleN Hall North Wales, Hartwell House Vale of Aylesbury aNd Middlethorpe Hall York were giveN to the NATIONAL TRUST to eNsure their loNg-term protectioN. BODYSGALLEN HALL & SPA H I S T O R I C H O U S E H O T E L S - S T A Y I N H O U S E S O F CONWY CASTLE D I S T I N C PLANNING T I They are represeNtative iN their differeNt O ways of the best of graNd domestic N YOUR TRIP architecture, from the JacobeaN aNd GeorgiaN spleNdour of Hartwell House to the crisp WWW.HISTORICHOUSEHOTELS.COM precisioN of brick aNd stoNe of Middlethorpe Hall or the Welsh verNacular charm of These sample tour itiNeraries have beeN BodysgalleN Hall set oN its wooded hill-side desigNed for the pleasure of those who eNjoy both stayiNg iN aNd visitiNg part of BritaiN's uNique heritage of beautiful TRAVEL couNtry houses. SUGGESTIONS You will stay iN the order of your choice iN three carefully restored Historic House For your jourNey betweeN our houses, we have Hotels, each aN importaNt buildiNg iN its made recommeNdatioNs for visits to properties owN right, all with a spleNdid gardeN aNd that are eN-route. -
104 Ruabon Road, Wrexham Price: £129,950
104 Ruabon Road, Wrexham Price: £129,950 • A spacious Victorian townhouse • Bathroom • Requiring internal modernisation • Upvc double glazing • Within convenient location • Gas fired central heating • Vestibule, hallway • Small garden to front • Lounge, sitting room • Yard to rear with further garden • Breakfast room, kitchen • NO CHAIN • Four good sized bedrooms • Energy Rating - E (51) Llangollen 01978 861366 Wrexham (Head Office/ Auction Gallery) 01978 353553 www.wingetts.co.uk Ruabon Road, Wrexham, LL13 7PY A spacious Victorian townhouse within a convenient location having the benefit of upvc double glazing and gas fired central heating. The accommodation requires a degree of internal modernisation and briefly comprises entrance hall with staircase to first floor landing, lounge with upvc double glazed walk-in bay window, sitting room, breakfast room and kitchen. On the first floor there are four good sized bedrooms together with a bathroom with white suite and electric shower over bath. Externally there is a small front garden whilst to the rear there is a yard with further garden area beyond which is larger than expected. This property offers an excellent opportunity to recreate a good sized family home or possible rental investment. Energy Rating - E (51) THE ACCOMMODATION WITH APPROXIMATE ROOM DIMENSIONS IS ARRANGED AS FOLLOWS ON THE FIRST FLOOR The staircase from the entrance hall rises to: LANDING Having gallery over stairwell, ceiling hatch to roof space, mains wired smoke alarm LOCATION and four panel doors off to all rooms. The property is conveniently located fronting Ruabon Road with good access into Wrexham town centre with its excellent range of shopping facilities and social amenities. -
Llinell Amser Glofa Glanrafon Fersiwn PDF 571Kb
1972 Streic y Glowyr yn dechrau — glowyr Glanrafon yn picedu British Celanese ar ystâd ddiwydiannol Rhydfudr Wrecsam i atal cyflenwadau honedig o lo cyfrinachol. Miners’ strike starts — Bersham miners picket British 1922 Celanese on Wrexham Redwither industrial estate to Slip cyflog prevent rumoured secret coal deliveries. Pay slip 1974 Glowyr Glanrafon yn pleidleisio 80% - 20% i gefnogi’r streic genedlaethol dros gyflogau. Streic yn dod i ben 1935 yn gynnar ym mis Mawrth ar ôl i lywodraeth Lafur i Lofa Glanrafon, 1984 Golygfeydd y tu allan newydd gytuno ar gytundeb cyflogau. ydd UCG, efo Arthur Scargill, arwein Mis Mawrth 1935 Bersham miners vote 80% - 20% to back national strike 1938 1950au cefnogwyr lleol Scenes outside Bersham Colliery, over pay. Strike ends in early March after new Labour Gweithlu: 550 o dan y 1950s ent, with March 1935 Arthur Scargill, NUM presid Posteri diogelwch government agrees a pay deal. Beddfaen Pattison, Eglwys ddaear a 140 ar yr wyneb. local supporters Map Arolwg Ordnans, 1872 Workforce: Safety Posters 1978 Y pwll glo yn cael ei ddefnyddio fel lleoliad ar gyfer ffilm Cerflun Y Mwynwr Olaf, y Blwyf Esclusham, Ordnance Survey map, 1872 1918 Americanaidd, The Corn is Green, yn serennu Katherine 1880 550 underground Bonc Glanrafon, 2016 1880–84 Glowyr Glanrafon yn Hepburn. Ffrwydrad ym mhwll Rhif 1 and 140 on surface. 1969 The Last Miner sculpt Pattison gravestone, cytuno i danysgrifio 2d yr ure, The colliery serves as a location for American film, The Bersham Colliery tip, 2016 — naw o ddynion yn cael Esclusham Parish Church, Yr NCB yn gwadu sïon bod wythnos i ymgyrch codi Corn is Green, starring Katherine Hepburn. -
Enforcement Register
Site Address Date Served N/000 1 Speed Six, Plas Acton Road, Pandy, Wrexham 25/03/2003 N/0002 Gates Farm, Mulsford Road, Tallarn Green, Wrexham 21/05/2003 N/0003 3 Chapel Street, Holt, Wrexham 02/10/2003 N/0004 Station House, Lightwood Green, Overton, Wrexham 19/12/2003 N/0005 Blue Bell Inn, Delph Road, Acrefair, Wrexham 30/12/2003 N/0006 Premier Mortars Depot, Vauxhall Industrial Estate, Ruabon 07/01/2004 Wrexham N/0007 14 Coed Efa Lane, New Broughton, Wrexham 03/02/2004 N/0008 101 High Street, Gwersyllt, Wrexham 04//04/2004 N/0009 Burton Buildings, 26-28 and 30 Bridge Street, Wrexham 09/08/2004 N/0010 2 Hamlington Avenue, Gwersyllt, Wrexham 21/12/2004 N/0011 Fairfield Meats, Bedwell Road, Cross Lanes, Wrexham 15/03/2005 N/0012 18 Vicarage Close, Bottom Road, Summerhill, Wrexham 09/05/2005 N/0013 53-55 Wrexham Road, Rhostyllen, Wrexham 01/06/2005 N/0014 Pwll Caddies, Long Lane, Brynteg, Wrexham 15/06/2005 N/0015 Darland Golf Course, Darland Lane, Rossett, Wrexham 29/06/2005 N/0016 101 High Street, Gwersyllt, Wrexham 04/07/2005 N/0017 Fresh Food Hall, The Cross, Holt, Wrexham 18/07/2005 N/0018 Bryn Offa, Fennant Road, Ponciau, Wrexham 24/08/2005 N/0019 Little Berse Farm, Ruthin Road, Coedpoeth, Wrexham 07/09/2005 N/0020 Alpine Windows, Old Mold Road, Gwersyllt, Wrexham 19/09/2005 N/0021 Fresh Food Hall, The Cross, Holt, Wrexham 27/09/2005 N/0022 Unit 1C, Rossett Business Park, Lavister Lane, Rossett, 14/12/2005 Wrexham N/0023 Charlbury House, off Chester Road, Gresford, Wrexham 05/01/2006 N/0024 Davy Way Office, Miners Road, Llay Industrial -
Town Tree Cover in Wrexham County Borough
1 Town Tree Cover in Wrexham County Borough Understanding canopy cover to better plan and manage our urban trees 2 Foreword Introducing a world-first for Wales is a great pleasure, particularly as it relates to greater knowledge about the hugely valuable woodland and tree resource in our towns and cities. We are the first country in the world to have undertaken a country-wide urban canopy cover survey. The resulting evidence base set out in this supplementary county specific study for Wrexham County Borough will help all of us - from community tree interest groups to urban planners and decision-makers in local authorities Emyr Roberts Diane McCrea and our national government - to understand what we need to do to safeguard this powerful and versatile natural asset. Trees are an essential component of our urban ecosystems, delivering a range of services to help sustain life, promote well-being, and support economic benefits. They make our towns and cities more attractive to live in - encouraging inward investment, improving the energy efficiency of buildings – as well as removing air borne pollutants and connecting people with nature. They can also mitigate the extremes of climate change, helping to reduce storm water run-off and the urban heat island. Natural Resources Wales is committed to working with colleagues in the Welsh Government and in public, third and private sector organisations throughout Wales, to build on this work and promote a strategic approach to managing our existing urban trees, and to planting more where they will -
Denbighshire Record Office
GB 0209 DD/BE Denbighshire Record Office This catalogue was digitised by The National Archives as part of the National Register of Archives digitisation project NRA 30556 The National Archives CLWYD RECORD OFFICE L ARO S.P.BEVON MSS. Schedule of documents deposited on indefinite loan by the County Librarian per Wrexham Area Library. 20 July 1976 (Ref: DD/BE) Clwyd Record Office 46, Clwyd Street, Ruthin, Clwyd A.N. 321 July 1987 S.P.BEVON MSS. This collection consists of material received from a Wrexham solicitor, relating to his personal and business affairs, and to some of his clients. The bulk of S.P.Bevon's personal papers consist of correspondence about properties he owned in Wrexham, and reports and prospectuses of various mining and plantation concerns abroad, in which he owned shares. There is no autobiographical material. The rest of the collection has been sorted into sequence by parish, with separate sections for court cases and election papers, as there is no large quantity of material relating to an individual client. Perhaps the most interesting item is a photograph showing the range of products made by Ewloe Potteries, Buckley, in the 1920s. Other interesting subjects include Ffos-y-go Colliery, Gwersyllt, 1901-4; the appointment of a receiver for the New Llangollen Slate and Slab Company. 1898-1903; prospectus of Broughton Hall Iron Company, c.1890; complaints about conditions at Croesnewydd Military Hospital, Wrexham, 1917; and a dispute over building costs of a new church at Brynteg, 1894-5. There are also some files of papers relating to S.P.Bevon's clients, 1920-40, in the Wrexham Library collection. -
Denbighshire Record Office
GB 0209 DD/W Denbighshire Record Office This catalogue was digitised by The National Archives as part of the National Register of Archives digitisation project NRA 30234 The National Archives CLWYD RECORD OFFICE WREXHAM SOLICITORS' MSS. (Schedule of documen^sdeposited indefinite loan bvM Bff and Wrexham. 26 November 1976, 28 September 1977, 15 February 1980). (Ref: DD/W) Clwyd Record Office, 46, Clwyd Street, A.N. 376, 471, 699 RUTHIN December 1986 WREXHAM SOLICITORS MSS. CONTENTS A.N. 471 GROVE PARK SCHOOL, WREXHAM: Governors 1-5 General 6-56 Miscellaneous 57 65 ALICE PARRY'S PAPERS 66 74 DENBIGHSHIRE EDUCATION AUTHORITY 75 80 WREXHAM EDUCATION COMMITTEE 81-84 WREXHAM AREA DIVISIONAL EXECUTIVE 85 94 WREXHAM BOROUGH COUNCIL: Treasurer 95 99 Medical Officer's records 100 101 Byelaws 102 Electricity 103 - 108 Rating and valuation 109 - 112 Borough extension 113 - 120 Miscellaneous 121 - 140 WREXHAM RURAL DISTRICT COUNCIL 140A DENBIGHSHIRE COUNTY COUNCIL 141 142 CALVINISTIC METHODIST RECORDS: SeioSeionn CM.Chapel,, RegenRegentt StreeStreett 143 - 153 CapeCapell yy M.CM.C.. Adwy'Adwy'rr ClawdClawddd 154 - 155 Henaduriaeth Dwyrain Dinbych 156 - 161 Henaduriaeth Dyffryn Clwyd 162 - 164 Henaduriaeth Dyffryn Conwy 165 Cyfarfod misol Sir Fflint 166 North Wales Association of the 167 - 171 Presbyterian Church Cymdeithasfa chwaterol 172 - 173 Miscellaneous 174 - 180 PRESBYTERIAN CHURCH OF WALES: Lancashire, Cheshire, Flintshire and 181 - 184 Denbighshire Presbyterian Church Lancashire and Cheshire Presbytery 185 - 186 Cheshire, Denbighshire