Conductive Polymer Capacitors for Automotive Applications
Total Page:16
File Type:pdf, Size:1020Kb
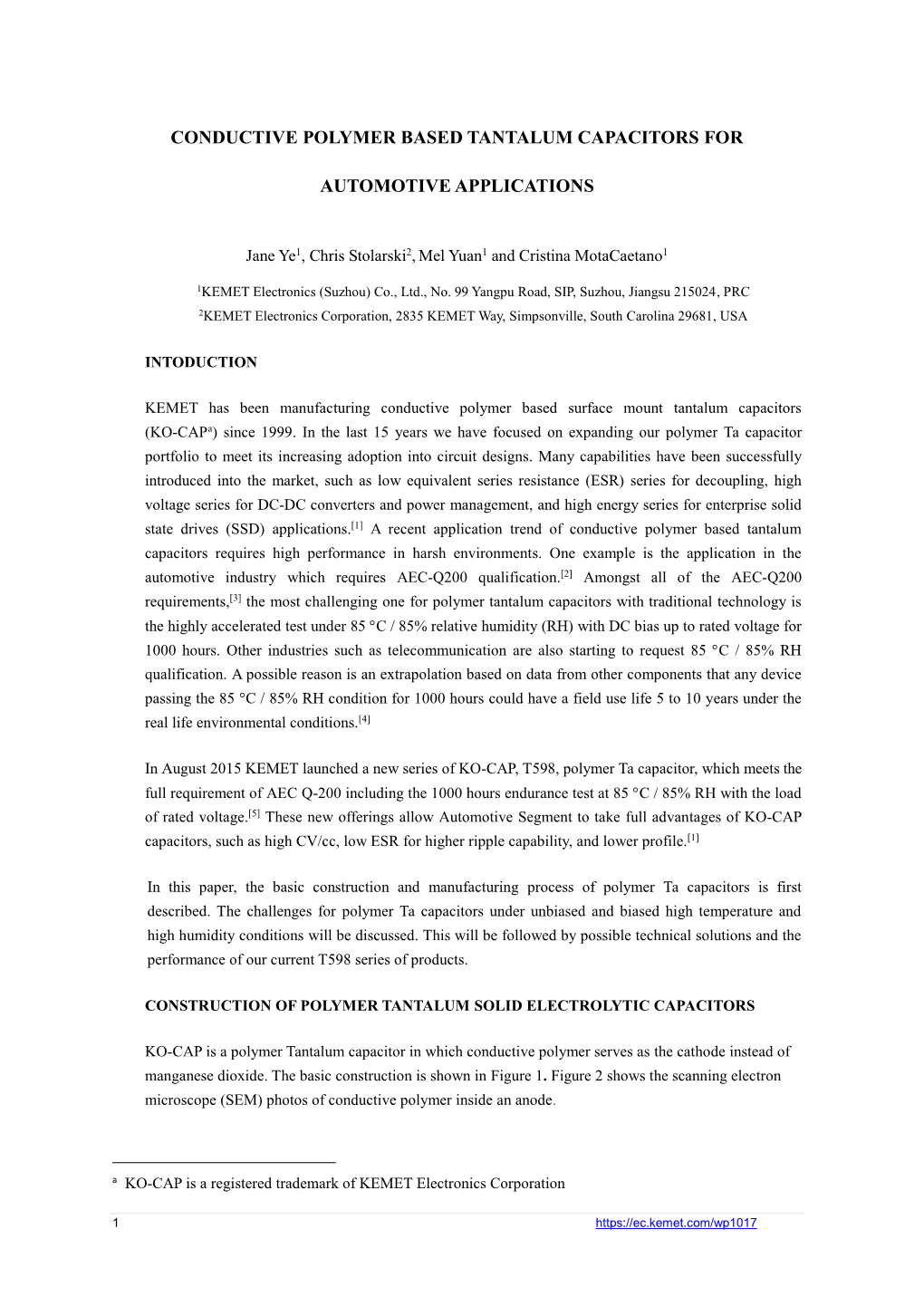
Load more
Recommended publications
-
Shape-Memory Polymeric Artificial Muscles Stress That Is Applied to the Polymer [8,70]
molecules Review Shape-Memory Polymeric Artificial Muscles: Mechanisms, Applications and Challenges 1, 1, 1, , 1 2 2 Yujie Chen y , Chi Chen y, Hafeez Ur Rehman * y, Xu Zheng , Hua Li , Hezhou Liu and Mikael S. Hedenqvist 3,* 1 State Key Laboratory of Metal Matrix Composites, School of Materials Science and Engineering, Shanghai Jiao Tong University, Shanghai 200240, China; [email protected] (Y.C.); [email protected] (C.C.); [email protected] (X.Z.) 2 Collaborative Innovation Centre for Advanced Ship and Dee-Sea Exploration, Shanghai Jiao Tong University, Shanghai 200240, China; [email protected] (H.L.); [email protected] (H.L.) 3 Department of Fibre and Polymer Technology, School of Engineering Sciences in Chemistry, Biotechnology and Health, KTH Royal Institute of Technology, SE-100 44 Stockholm, Sweden * Correspondence: [email protected] (H.U.R.); [email protected] (M.S.H.) These authors contributed equally to this work. y Academic Editor: Laura Peponi Received: 7 July 2020; Accepted: 3 September 2020; Published: 16 September 2020 Abstract: Shape-memory materials are smart materials that can remember an original shape and return to their unique state from a deformed secondary shape in the presence of an appropriate stimulus. This property allows these materials to be used as shape-memory artificial muscles, which form a subclass of artificial muscles. The shape-memory artificial muscles are fabricated from shape-memory polymers (SMPs) by twist insertion, shape fixation via Tm or Tg, or by liquid crystal elastomers (LCEs). The prepared SMP artificial muscles can be used in a wide range of applications, from biomimetic and soft robotics to actuators, because they can be operated without sophisticated linkage design and can achieve complex final shapes. -
Introduction What Is a Polymer Capacitor?
ECAS series (polymer-type aluminum electrolytic capacitor) No. C2T2CPS-063 Introduction If you take a look at the main board of an electronic device such as a personal computer, you’re likely to see some of the six types of capacitors shown below (Fig. 1). Common types of capacitors include tantalum electrolytic capacitors (MnO2 type and polymer type), aluminum electrolytic capacitors (electrolyte can type, polymer can type, and chip type), and MLCC. Figure 1. Main Types of Capacitors What Is a Polymer Capacitor? There are many other types of capacitors, such as film capacitors and niobium capacitors, but here we will describe polymer capacitors, a type of capacitor produced by Murata among others. In both tantalum electrolytic capacitors and aluminum electrolytic capacitors, a polymer capacitor is a type of electrolytic capacitor in which a conductive polymer is used as the cathode. In a polymer-type aluminum electrolytic capacitor, the anode is made of aluminum foil and the cathode is made of a conductive polymer. In a polymer-type tantalum electrolytic capacitor, the anode is made of the metal tantalum and the cathode is made of a conductive polymer. Figure 2 shows an example of this structure. Figure 2. Example of Structure of Conductive Polymer Aluminum Capacitor In conventional electrolytic capacitors, an electrolyte (electrolytic solution) or manganese dioxide (MnO2) was used as the cathode. Using a conductive polymer instead provides many advantages, making it possible to achieve a lower equivalent series resistance (ESR), more stable thermal characteristics, improved safety, and longer service life. As can be seen in Fig. 1, polymer capacitors have lower ESR than conventional electrolytic Copyright © muRata Manufacturing Co., Ltd. -
Review of Technologies and Materials Used in High-Voltage Film Capacitors
polymers Review Review of Technologies and Materials Used in High-Voltage Film Capacitors Olatoundji Georges Gnonhoue 1,*, Amanda Velazquez-Salazar 1 , Éric David 1 and Ioana Preda 2 1 Department of Mechanical Engineering, École de technologie supérieure, Montreal, QC H3C 1K3, Canada; [email protected] (A.V.-S.); [email protected] (É.D.) 2 Energy Institute—HEIA Fribourg, University of Applied Sciences of Western Switzerland, 3960 Sierre, Switzerland; [email protected] * Correspondence: [email protected] Abstract: High-voltage capacitors are key components for circuit breakers and monitoring and protection devices, and are important elements used to improve the efficiency and reliability of the grid. Different technologies are used in high-voltage capacitor manufacturing process, and at all stages of this process polymeric films must be used, along with an encapsulating material, which can be either liquid, solid or gaseous. These materials play major roles in the lifespan and reliability of components. In this paper, we present a review of the different technologies used to manufacture high-voltage capacitors, as well as the different materials used in fabricating high-voltage film capacitors, with a view to establishing a bibliographic database that will allow a comparison of the different technologies Keywords: high-voltage capacitors; resin; dielectric film Citation: Gnonhoue, O.G.; Velazquez-Salazar, A.; David, É.; Preda, I. Review of Technologies and 1. Introduction Materials Used in High-Voltage Film High-voltage films capacitors are important components for networks and various Capacitors. Polymers 2021, 13, 766. electrical devices. They are used to transport and distribute high-voltage electrical energy https://doi.org/10.3390/ either for voltage distribution, coupling or capacitive voltage dividers; in electrical sub- polym13050766 stations, circuit breakers, monitoring and protection devices; as well as to improve grid efficiency and reliability. -
Conductive Nanocomposite Fabrication by Graphene Enriched Polypropylene Master Batch
© 2015 IJEDR | Volume 3, Issue 4 | ISSN: 2321-9939 Conductive Nanocomposite fabrication by Graphene enriched Polypropylene Master Batch 1M.Naushad Ali, 2H.Alamri, 3Abdul Wahab 1 Bottom Up Technologies Corporation, Jharkhand, India 2Physics Deptt, Umm Al-Qura University, Makkah, KSA 3Engineering Grad Trainee, Jharkhand Rai UniversitSy, Ranchi, India ________________________________________________________________________________________________________ Abstract - The nanocomposites are the most attentive topic of the study currently in the material science world which is likely to bring the industrial revolution. Graphene reinforced polypropylene nanocomposite was fabricated in the balanced formulation of filler & carrier additives through melt mixing process at the trend of industrial practices. The concept of molecular arrangement was hypothesized and executed out practically. The master batch was prepared as the primary preparatory work using Twin Screw Extruder and the finished product was obtained by using the same master batch through injection molding. The percolation threshold was considered to be 5% wt. Graphene in finished product which has been proved as the innovative product line. A series of destructive and non-destructive tests and characterization techniques were conducted, analyzed and presented. First time the entire range of properties has been explored including electrical, thermal, gas barrier & mechanical properties. The resulted product has proven to be used at the industrial scale immediately and has opened the new directions in making use of other class of polymers innovatively. Key words - Nanocomposite, Electrical conductivity, Graphene, Polypropylene, Industrial applications, Nanotechnology I. Introduction Nanomaterials own the Quantum confinement which consequences the exceptional outstanding properties and lead to the enormous range of revolutionary applications. In this regard, the discovery of graphene and graphene-based polymer nanocomposites is playing a vital role in modern science and technology [1]. -
Non-Covalent Interactions on Polymer-Graphene Nanocomposites and Their Effects on the Electrical Conductivity
polymers Article Non-Covalent Interactions on Polymer-Graphene Nanocomposites and Their Effects on the Electrical Conductivity Jorge Luis Apátiga 1, Roxana Mitzayé del Castillo 1 , Luis Felipe del Castillo 2, Alipio G. Calles 1, Raúl Espejel-Morales 1, José F. Favela 3 and Vicente Compañ 4,* 1 Departamento de Física, Facultad de Ciencias, Universidad Nacional Autónoma de México, Circuito Interior s/n, Ciudad Universitaria, Mexico City 04510, Mexico; [email protected] (J.L.A.); [email protected] or [email protected] (R.M.d.C.); [email protected] (A.G.C.); [email protected] (R.E.-M.) 2 Departamento de Polímeros, Instituto de Investigaciones en Materiales, Universidad Nacional Autónoma de México, Circuito Interior s/n, Ciudad Universitaria, Mexico City 04510, Mexico; [email protected] 3 Instituto de Ciencias Nucleares, Universidad Nacional Autónoma de México, Circuito Interior s/n, Ciudad Universitaria, Mexico City 04510, Mexico; [email protected] 4 Departamento de Termodinámica Aplicada, Escuela Técnica Superior de Ingenieros Industriales (ETSII), Campus de Vera s/n, Universitat Politécnica de Valencia, 46020 Valencia, Spain * Correspondence: [email protected]; Tel.: +34-963-879-328 Abstract: It is well known that a small number of graphene nanoparticles embedded in polymers enhance the electrical conductivity; the polymer changes from being an insulator to a conductor. The Citation: Apátiga, J.L.; del Castillo, graphene nanoparticles induce several quantum effects, non-covalent interactions, so the percola- R.M.; del Castillo, L.F.; Calles, A.G.; tion threshold is accelerated. We studied five of the most widely used polymers embedded with Espejel-Morales, R.; Favela, J.F.; graphene nanoparticles: polystyrene, polyethylene-terephthalate, polyether-ketone, polypropylene, Compañ, V. -
Template-Assisted Electrochemical Synthesis of Cdse Quantum Dots—Polypyrrole Composite Nanorods
applied sciences Article Template-Assisted Electrochemical Synthesis of CdSe Quantum Dots—Polypyrrole Composite Nanorods Won-Seok Kang 1, Taegon Oh 2, Gwang-Hyeon Nam 1, Hyo-Sop Kim 1, Ki-Suk Kim 3, Sun-Hyun Park 3, Jae-Ho Kim 1,* and Jae-Hyeok Lee 3,* 1 Department of Molecular Science and Technology, Ajou University, Suwon 443-749, Korea; [email protected] (W.-S.K.); [email protected] (G.-H.N.); [email protected] (H.-S.K.) 2 Materials Architecturing Research Center, Korea Institute of Science and Technology, Seoul 02792, Korea; [email protected] 3 R&D Center for Advanced Pharmaceuticals & Evaluation, Korea Institute of Toxicology, Daejeon 34114, Korea; [email protected] (K.-S.K.); [email protected] (S.-H.P.) * Correspondence: [email protected] (J.-H.K.); [email protected] (J.-H.L.); Tel.: +82-31-219-2517 (J.-H.K.); +82-42-610-8338 (J.-H.L.) Received: 26 July 2020; Accepted: 26 August 2020; Published: 28 August 2020 Abstract: Luminescent nanoparticles have reached a high level of maturity in materials and spectral tunability for optics and optoelectronics. However, the lack of facile methodology for heterojunction formation of the nanoparticles provides many challenges for scalability. In this paper we demonstrate a simple procedure to synthesize a nanoparticle-embedded polymer nanorod hybrid structure via a template-based electrochemical method using anodic aluminum oxide membranes. This method enables the formation of interactive nanostructures wherein the interface area between the two components is maximized. As a proof of concept, semiconducting CdSe nanoparticles were embedded in polypyrrole nanorods with dimensions that can be finely tuned. -
Understanding Polymer and Hybrid Capacitors Advanced Capacitors Based on Conductive Polymers Maximize Performance and Reliability
WHITE PAPER Understanding Polymer and Hybrid Capacitors Advanced capacitors based on conductive polymers maximize performance and reliability The various polymer and hybrid capacitors have distinct sweet spots in terms of their ideal voltages, frequency characteristics, environmental conditions and other application requirements. In this paper, we’ll show you how to identify the best uses for each type of advanced capacitor. We’ll also highlight specific applications in which a polymer or hybrid capacitor will outperform traditional electrolytic or even ceramic capacitors. POLYMER CAPACITOR VARIETIES Polymer capacitors come in four main varieties, including the hybrid. Each type has different electrolytic and electrode Hybrid capacitor technology combines the performance benefits of materials, packaging and application targets: electrolytic and polymer capacitors. • Layered polymer aluminum capacitors use conductive Capacitors may seem simple enough, but specifying them has polymer as the electrolyte and have an aluminum cathode actually grown more complex in recent years. The reason why (see Figure 1). Depending on the specific model, these comes down to freedom of choice. The universe of capacitors capacitors cover a voltage range from 2-25V and offer has expanded greatly over the past few years, in large part capacitances between 2.2-560µF. The distinguishing because of capacitor designs that take advantage of advances electrical characteristic of these polymer capacitors is in conductive polymers. their extremely low equivalent series resistance (ESR). For example, some of our SP-Cap™ polymer capacitors have These advanced capacitors sometimes use conductive polymers ESR values as low as 3mΩ, which is among the lowest in to form the entire electrolyte. Or the conductive polymers can be used in conjunction with a liquid electrolyte in a design known as a hybrid capacitor. -
A STUDY of POLYMER-GRAPHENE CONDUCTING THIN FILMS and THEIR PROPERTIES by DILLI RAM DHAKAL Masters of Science in Physics Tribhu
A STUDY OF POLYMER-GRAPHENE CONDUCTING THIN FILMS AND THEIR PROPERTIES By DILLI RAM DHAKAL Masters of Science in Physics Tribhuvan University Kirtipur, Kathmandu 2012 Submitted to the Faculty of the Graduate College of the Oklahoma State University in partial fulfillment of the requirements for the Degree of MASTER OF SCIENCE May, 2018 A STUDY OF POLYMER-GRAPHENE CONDUCTING THIN FILMS AND THEIR PROPERTIES Thesis Approved: Dr. Ranji Vaidyanathan Thesis Adviser Dr. Toby Nelson Dr. Do Young Kim ii ACKNOWLEDGEMENTS I would like to offer special thanks to my advisor, Dr. Vaidyanathan, for providing the opportunity to conduct research in the field of composite material under his supervision. Without his constant support, motivation and openness for discussion, this research work would not have been possible. I am particularly grateful for the trust that he kept on me during this work. I am also grateful for the opportunity provided to me toward working in the business side of this project. I am thankful to Dr. Nelson and Dr. Kim for being a part of my thesis committee and their support. I also want to add special thanks towards Dr. Nelson and his graduate students for providing the working environment in their lab. I wish to acknowledge Dr. Frank Blum and Dr. Bhishma Sedai for providing environment to work on TGA and constant support throughout the work. I extremely thankful to all my friends (Vishanth, ShawnDea, Vishal, Muthu, Ragini, Jonathan, Santosh, Malay, Ranjan) for constant support during different aspects of my master’s degree. I am forever grateful to my parents, wife Isha and daughter Sayana, who have been backbone for my strength and passion in my life. -
Solid Polymer Aluminum SMT Capacitors Tape Specifications Reel Specifications
Application Guide, Solid Polymer Aluminum SMT Capacitors Tape Specifications Reel Specifications SPA ESRD ESRE ESRH SPA Type t2 = H + 0.3 mm ±0.2 mm W D– P A B EF P 1 P t ±0.3 + 0.1/–0.0 Ø ±0.2 2 ±0.2 ±0.2 1 A ±0.2 B Min. C ±0.5 D ±0.8 E ±0.5 W ±1.0 t 12.0 1.8 5.5 1.5 4.0 8.0 2.0 7.7 4.6 0.4 333.0 50.0 13.0 21.0 2.0 14.0 3.0 Tol.: ± mm unless otherwise specified Design Kits Design kits containing various ratings are available through the CDE web site. Typical Temperature Characteristics Capacitance Change at 120 Hz Dissipation Factor at 120 Hz 20 10 10µF/6.3V 10µF/6.3V 8 10 6 % ) 0 C ( DF ( % ) ǻ 4 -10 2 -20 0 -60 -20 20 60 100 -60 -20 20 60 100 Temperature (°C) Temperature (°C) CDE Cornell Dubilier • 1605 E. Rodney French Blvd. • New Bedford, MA 02744 • Phone: (508)996-8561 • Fax: (508)996-3830 • www.cde.com Application Guide, Solid Polymer Aluminum SMT Capacitors Typical Impedance and Equivalent Series Resistance ESRD (3.1 mm Ht.) 100.000 ESRD680M08R 68 uF/8 V Impedance/E.S.R. 10.000 ESRD121M04R 120 uF/4 V Impedance/E.S.R. 1.000 ESRD181M02R Ohms 180 uF/2 V Impedance/E.S.R. 0.100 0.010 0.001 0.1 1 10 100 1000 10000 100000 Frequency (kHz) ESRE 100.000 ESRE101M08R 100 uF/8 Vdc 10.000 Impedance/E.S.R. -
Supporting Information Sulfur Quantum Dots Wrapped by Conductive Polymer Shell with Internal Void Spaces for High-Performance Li
Electronic Supplementary Material (ESI) for Journal of Materials Chemistry A. This journal is © The Royal Society of Chemistry 2015 Supporting Information Sulfur Quantum Dots Wrapped by Conductive Polymer Shell with Internal Void Spaces for High-Performance Lithium-Sulfur Batteries Fig. S1. SEM images of S treated with CS2. Elemental sulfur was directly dissolved in CS2 and magnetic stirred at 40 °C, plenty of nanopores and nanoparticles (b) formed and precipitated on the surface of large sulfur particles (a) as the CS2 solvent vapored out. Fig. S2. TEM images of the S/PVK composites. Fig. S3. (a) XRD patterns of S/PVK nanocomposites with different S content. (b) Thermal gravimetric analysis (TGA) of S/PVK nanocomposites. (c) FT-IR spectra of S/PVK-A, B and C. The TGA measurements of S/PVK and SQD/PVK composites were measured in a two- stage heating procedure under nitrogen flow which were first heated in the range of 50-350 °C at a heating rate of 10 °C/min, and then maintained at this temperature for 20 minutes before heating to 800 °C with the same heating rate. TGA measurement of pure PVK was measured from 50-800°C at a heating rate of 10 °C/min. Fig. S4. (a) Cyclic voltammograms of sulfur and the SQD/PVK composite electrode at 0.05 mV s-1 at 1.0 to 3.0 V vs. Li/Li+. (b) Nyquist plots of the electrode for the different SQD/PVK nanocomposites, pure PVK and pure sulfur cathode before cycling from 200 kHz to 100 mHz at room temperature. -
COMPACT FORM FITTING SMALL ANTENNAS USING THREE- DIMENSIONAL RAPID PROTOTYPING by Bryan Jon Willis May 2012
View metadata, citation and similar papers at core.ac.uk brought to you by CORE provided by The University of Utah: J. Willard Marriott Digital Library COMPACT FORM FITTING SMALL ANTENNAS USING THREE- DIMENSIONAL RAPID PROTOTYPING by Bryan Jon Willis A dissertation submitted to the faculty of The University of Utah in partial fulfillment of the requirements for the degree of Doctor of Philosophy Department of Electrical and Computer Engineering The University of Utah May 2012 Copyright © Bryan Jon Willis 2012 All Rights Reserved The University of Utah Graduate School STATEMENT OF DISSERTATION APPROVAL The dissertation of Bryan Jon Willis has been approved by the following supervisory committee members: Cynthia Furse , Chair 3/27/12 Date Approved Erik Brunvand , Member 3/27/12 Date Approved Om P. Gandhi , Member 4/10/12 Date Approved Steve Blair , Member 3/27/12 Date Approved Joseph Mark Baird , Member 3/27/12 Date Approved and by Gianluca Lazzi , Chair of the Department of Electrical Engineering and by Charles A. Wight, Dean of The Graduate School. ABSTRACT Three-dimensional (3D) rapid prototyping holds significant promise for future antenna designs. Many complex designs that would be unmanufacturable or costly are realizable on a 3D printing machine. The ability to create 3D designs of virtually any configuration makes it possible to build compact antennas that can form fit to any space. These antennas build on the concept that small antennas can best reach the ideal operating limit when utilizing the entire 3D space in a sphere surrounding the antenna. Antennas require a combination of dielectric and conductive materials. -
Research Collection
Research Collection Doctoral Thesis Inhomogeneous Deformations of Thermoplastics for Physically Adaptive Soft Matter Robots Author(s): Culha, Utku Publication Date: 2016 Permanent Link: https://doi.org/10.3929/ethz-a-010735372 Rights / License: In Copyright - Non-Commercial Use Permitted This page was generated automatically upon download from the ETH Zurich Research Collection. For more information please consult the Terms of use. ETH Library DISS. ETH NO. 23592 Inhomogeneous Deformations of Thermoplastics for Physically Adaptive Soft Matter Robots A thesis submitted to attain the degree of DOCTOR OF SCIENCES of ETH ZURICH (Dr. sc. ETH Zurich) presented by UTKU CULHA M.Sc., Bilkent University born on 1 January 1988 citizen of Republic of Turkey accepted on the recommendation of Prof. Dr. Fumiya Iida, examiner Prof. Dr. Dario Floreano, co-examiner Prof. Dr. Roger Gassert, co-examiner 2016 Inhomogeneous Deformations of Thermoplastics for Physically Adaptive Soft Matter Robots Utku Culha 2016 Bio-Inspired Robotics Lab Institute of Robotics and Intelligent Systems ETH Zurich Switzerland © 2016 Utku Culha. All rights reserved. Abstract In recent years robotics researchers have started using soft materials to build robots inspired from simple organisms, plants and animals which demonstrate impressive physical and behavioural adaptations originating from their soft and deformable body structures. Unlike rigid materi- als used in conventional robots, soft materials such as polymers and gels are continuum and visco-elastic mediums which can exhibit large deformations in many directions. Usage of these materials enables robotic systems to perform adaptive interactions with uncertain and unstruc- tured environments during various tasks such as locomotion, manipulation and inspection. In biology, many important functions emerge from the formation of well-defined structures as a result of symmetry breaking in the cellular scale.