Wet Scrubber Application Guide
Total Page:16
File Type:pdf, Size:1020Kb
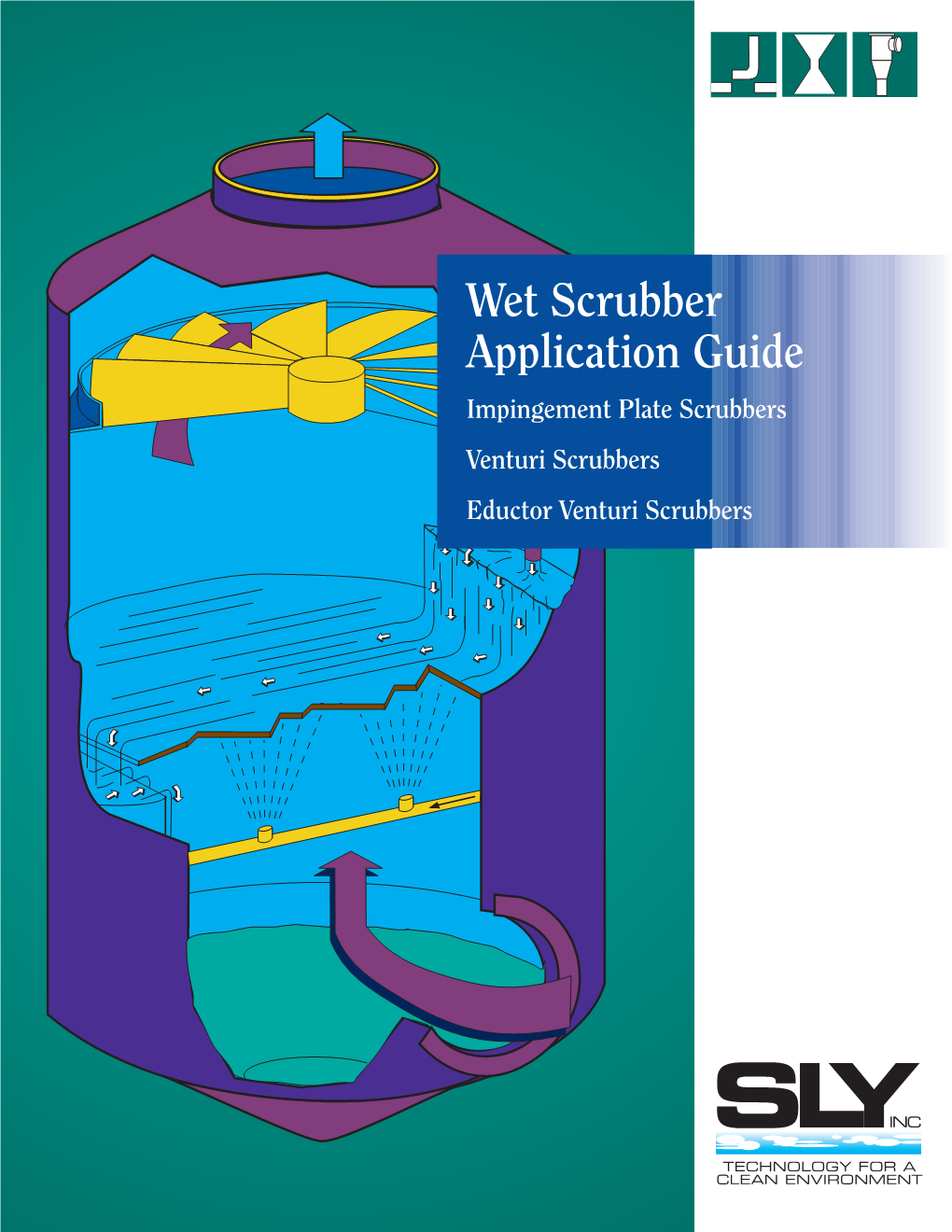
Load more
Recommended publications
-
Comparison of Chemical Wet Scrubbers and Biofiltration For
Journal of Chemical Technology and Biotechnology J Chem Technol Biotechnol 80:1170–1179 (2005) DOI: 10.1002/jctb.1308 Comparison of chemical wet scrubbers and biofiltration for control of volatile organic compounds using GC/MS techniques and kinetic analysis James R Kastner∗ and Keshav C Das Department of Biological and Agricultural Engineering, The University of Georgia, Athens, GA, 30602, USA Abstract: Increasing public concerns and EPA air regulations in non-attainment zones necessitate the remediation of volatile organic compounds (VOCs) generated in the poultry-rendering industry. Wet scrubbers using chlorine dioxide (ClO2) have low overall removal efficiencies due to lack of reactivity with aldehydes. Contrary to wet scrubbers, a biofilter system successfully treated the aldehyde fraction, based on GC/MS analysis of inlet and outlet streams. Total VOC removal efficiencies ranged from 40 to 100% for the biofilter, kinetic analysis indicated that the overall removal capacity approached 25 g m−3 h−1, and aldehyde removal efficiency was significantly higher compared with chemical wet scrubbers. Process temperatures monitored in critical unit operations upstream from the biofilter varied significantly during operation, rising as much as 30 ◦C within a few minutes. However, the outlet air temperature of a high intensity scrubber remained relatively constant at 40 ◦C, although the inlet air temperature fluctuated from 50 to 65 ◦C during monitoring. These data suggest a hybrid process combining a wet scrubber and biofilter in series could be used to improve overall VOC removal efficiencies and process stability. 2005 Society of Chemical Industry Keywords: odor; volatile organic compounds (VOC); aldehydes; wet scrubber; biofilter; gas chromatography; mass spectrometry INTRODUCTION and odor complaints have resulted in the need for low Rendering operations convert organic wastes (feathers, cost, effective treatment options. -
Application Note Wet Flue Gas Desulfurization Scrubbers Power: Environmental
Application Note Wet Flue Gas Desulfurization Scrubbers Power: Environmental Coal fi red power plant emissions are a global concern. collects in the bottom of the absorber. A paste-like calcium The burning of coal produces sulfur dioxide (SO2). When sulfi te (CaSO3) sludge forms in the liquid. CaCO3 can be released into the atmosphere SO2 combines with water very diffi cult to remove if it settles out at the bottom of the to form sulfuric acid (H2SO4). Coal fi red power plants will absorber. More recent scrubber designs will blow outside use a fl ue gas desulfurization (FGD) scrubber to remove air through liquid to convert the sulfi te to sulfate in the the SO2 before release up the stack. The scrubbing following reaction. process is pH dependent. In this paper we will explore some of the challenges in this type of pH measurement. CaSO3 + H2O + 1/2O2 ► CaSO4 + H2O The FGD scrubber uses chemical reagents sprayed into The addition of air is referred to as forced oxidation. The the fl ue gas to react with the SO2. Many different reagents resulting calcium sulfate (CaCO4) crystallizes in the liquid have been used over the years. Examples include and is easily removed through fi ltration. An added benefi t ammonia, caustic, lime, limestone, and sodium carbonate. from the process is that CaCO4 (known as gypsum) can Due to cost, the most common reagents are Lime (CaO) be sold as additive for wallboard and cement production. and Limestone (CaCO3). Since both chemicals are very similar we will limit the scope of this paper to them. -
Wet Gas Scrubbing
CHAPTER 41 WET GAS SCRUBBING Wet scrubbers use a liquid to remove solid, liquid, or gaseous contaminants from a gas stream. The scrubbing liquid performs this separation by dissolving, trap- ping, or chemically reacting with the contaminant. Scrubbers are used extensively to control air polluting emissions. So many dif- ferent scrubber configurations have been used that there is some confusion as to whether they all belong in the same category. In some references, for example, the definition of a scrubber may be restricted to certain design criteria, such as whether the units are open or packed. In this text, any device fitting the definition of the first sentence is a wet scrubber. Scrubber systems can be designed to remove entrained paniculate materials such as dust, fly ash, or metal oxides, or to remove gases, such as oxides of sulfur (SOx), from a flue gas stream to meet air emission standards. PARTICLE COLLECTION CONCEPTS In scrubbing paniculate matter from gases, the principal concern is usually removal of particles smaller than than 10 /on. Larger particles are relatively easy to separate. The successful design and operation of wet scrubbers depends on knowing the size, composition, and derivation of the particles to be collected. Figure 41.1 shows estimated size for some common pollutants. Just as fine particles in water (colloids) carry a charge of static electricity, so do colloidal par- ticles in the fumes and dust, defined as aerosols. If these particles carry no charge, they may be deliberately charged to assist removal by special separators called electrostatic precipitators. Among the particulates (term for the suspended solid materials) collected by wet scrubbers are dispersion aerosols from processes such as grinding, solid and liquid atomization, and transport of suspended powders by air currents or vibra- tion. -
2.2 Sewage Sludge Incineration
2.2 Sewage Sludge Incineration There are approximately 170 sewage sludge incineration (SSI) plants in operation in the United States. Three main types of incinerators are used: multiple hearth, fluidized bed, and electric infrared. Some sludge is co-fired with municipal solid waste in combustors based on refuse combustion technology (see Section 2.1). Refuse co-fired with sludge in combustors based on sludge incinerating technology is limited to multiple hearth incinerators only. Over 80 percent of the identified operating sludge incinerators are of the multiple hearth design. About 15 percent are fluidized bed combustors and 3 percent are electric. The remaining combustors co-fire refuse with sludge. Most sludge incinerators are located in the Eastern United States, though there are a significant number on the West Coast. New York has the largest number of facilities with 33. Pennsylvania and Michigan have the next-largest numbers of facilities with 21 and 19 sites, respectively. Sewage sludge incinerator emissions are currently regulated under 40 CFR Part 60, Subpart O and 40 CFR Part 61, Subparts C and E. Subpart O in Part 60 establishes a New Source Performance Standard for particulate matter. Subparts C and E of Part 61--National Emission Standards for Hazardous Air Pollutants (NESHAP)--establish emission limits for beryllium and mercury, respectively. In 1989, technical standards for the use and disposal of sewage sludge were proposed as 40 CFR Part 503, under authority of Section 405 of the Clean Water Act. Subpart G of this proposed Part 503 proposes to establish national emission limits for arsenic, beryllium, cadmium, chromium, lead, mercury, nickel, and total hydrocarbons from sewage sludge incinerators. -
Odor Control System
ODOR CONTROL SYSTEM What is an Odor? An odor is defined as a sensation resulting from the reception of a stimulus by the olfactory sensory system. Controlling odors is an important consideration for protecting the environment and our community amenity. Odors can be generated from a vast range of sources including sewage treatment processes and industrial effluents. Odor Control Technologies Typical odor emission control applications are the removal of odor from sewage treatment plants & sewage wet waste. Odor related complaints from communities surrounding WWTPs have been increasing for many WWTPs. Here, several emission sources need odor control equipment, e.g. such as pump stations, wet wells, sludge dewatering, manholes, air valve chambers, and sludge trans-shipment operations from silo into trucks. Sewage odor consists of mainly hydrogen sulphide & H2S is dangerous to be released to the environment. Hydrogen sulphide, the gas, also contains organic sulphur components (mercaptans, hydrocarbons) and ammonia. Odor control technologies can be grouped into three distinct categories: 1. Chemical Absorption (acid and caustic wet scrubbing) 2. Biological Oxidation (bio-filtration and bio-scrubbing / bio trinkling filtration) 3. Adsorption (activated carbon and other adsorptive medias) 4. The Combination of above systems are usually used for Biological Oxidation & Chemical Scrubbing Chemical Absorption: Chemical scrubbers achieve odor removal by mass transfer absorption via contact of air stream with aqueous solution on random packing material in a scrubbing chamber. The liquid is typically water, adjusted to the proper pH and CHEMICAL DOSING oxidation potential by chemicals. TANK CHEMICAL STORAGE TANK CHEMICAL Two parameters define the performance of any absorption SCRUBBER scrubbing system. -
Gas Scrubbers
Bulletin 7-S Gas Scrubbers INTRODUCTION The use of wet scrubbers for control of air pollution has gained wide acceptance throughout the industry. The ejector-venturi wet scrubber provides a number of advantages over many of the conventional single-purpose devices available. Particulate collectors such as cyclones and electrostatic precipitators cannot efficiently absorb gases or remove odors. Fabric filters, by design, cannot cope with gas streams having a high moisture content and are often affected by highly corrosive gases. Catalytic incinerators can be quickly poisoned by certain organic wastes. On the other hand, ejector-venturi gas scrubbers are very effective at removing noxious gases, particulates, odors, fumes and dusts from gas streams. Particulate contaminants are removed through impaction by the high velocity spray of scrubbing liquid. Gases and odors are eliminated through absorption and/or chemical reaction between the gases and scrubbing liquid. When properly matched to the application, these scrubbers, by their nature, are better able to cope with the high temperatures and corrosive conditions often encountered. Schutte & Koerting has over sixty years of experience in the control of commercial and industrial air pollution using wet scrubber technology. The ejector-venturi gas Description Page scrubbers described on the following pages have been Fig. 7010 Ejector-Venturi Scrubber 2 engineered to operate effectively in a variety of Fig. 7040 Separators 2 applications. Using the same basic design, these standard Fig. 7019 Vent Gas Scrubber System 2 scrubbers can be sized to meet volume requirements from Stock Systems 2 a few CFM to thousands of CFM. This broad applicability Fig. 7014 Scrubber-Separator System 3 permits Schutte & Koerting to stock these scrubbers in a Economical Stock Systems 3 wide range of sizes and materials. -
Lime / Limestone Wet Scrubbing System for Flue Gas Desulfurization
Application Data Sheet ADS 4900-02/rev.D Power Industry December 2014 Lime / Limestone Wet Scrubbing System for Flue Gas Desulfurization BACKGROUND will therefore add more lime when pH drops below 12 and a limestone based system will be controlled around 6. Unless Wet scrubbers are used in utilities, paper mills, and chemical one or the other is added, the SO gas will quickly drive the plants to remove sulfur dioxide (SO ) and other pollutants 2 2 pH acidic. from gas streams. Undesirable pollutants are removed by contacting the gases with an aqueous solution or slurry The calcium compounds produced in scrubbers tend to containing a sorbent. The most common sorbents are lime accumulate in recirculation loops and can cause a buildup of scale. Scale on the spray nozzles affects the atomization (Ca[OH]2) and limestone (CaCO3). Rosemount Analytical pH equipment is used to control the feed rate of these of the water droplets and reduces the scrubbing efficiency. chemicals. Scale on the return piping reduces flow rate and changes the thermal balance of the system. The tendency to scale is limited by additives such as chelating agents and phos- PROCESS phates, but these additives are generally only effective at After fly ash removal, the flue gas (seen in Figure 1) is bubbled higher pH levels. pH control is necessary to forestall the through the scrubber, and the slurry is added from start of scaling, as it is much easier to prevent scaling than above.The lime or limestone reacts with the SO2 in the flue to remove it. -
Air/Gas Cleaning & Odor Control
Air/Gas Cleaning & Odor Control Air/Gas Cleaning & Odor Control The Monroe Advantage For over forty years, Monroe Environmental has been designing and manufacturing air quality systems for industrial manufacturers, government agencies, and municipal treatment plants. Table of Complete Air Quality Solutions Contents Monroe Environmental offers a broad range of stand-alone equipment as well as complete 2 The Monroe systems to effectively manage dust, mist, odors, and Advantage fumes associated with both industrial manufactur- 4 Scrubbing ing and municipal water/wastewater treatment. Applications Monroe continues to solve challenging air 6 Packed Bed and gas cleaning problems with our skilled team of engineers, shop technicians, and knowledgeable Fume Scrubbers sales staff. The largest manufacturing companies in 8 Venturi the world routinely look to Monroe to solve their Particulate most demanding mist, dust, and fume control Scrubbers problems. 10 Carbon Monroe Systems and Services Adsorbers Packed Bed Wet Air Scrubbers 15,000 CFM Packed Bed Scrubber to remove ethylene • glycol and NMP fumes from a glass coating operation 12 Multi-Stage • Venturi Particulate Scrubbers Scrubbing • Carbon Adsorbers • Design and manufacture new air quality and odor control systems Systems • Multi-Stage Scrubbing Systems Retrofit existing systems to maximize 14 Mist and Dust Dust Collectors • • performance and removal efficiency Collection • Oil Mist Collectors • Ductwork design 16 Dry Dust • Permit assistance for EPA compliance Collectors • Industrial and municipal -
Design Guidelines for Carbon Dioxide Scrubbers I
"NCSCTECH MAN 4110-1-83 I (REVISION A) S00 TECHNICAL MANUAL tow DESIGN GUIDELINES FOR CARBON DIOXIDE SCRUBBERS I MAY 1983 REVISED JULY 1985 Prepared by M. L. NUCKOLS, A. PURER, G. A. DEASON I OF * Approved for public release; , J 1"73 distribution unlimited NAVAL COASTAL SYSTEMS CENTER PANAMA CITY, FLORIDA 32407 85. .U 15 (O SECURITY CLASSIFICATION OF TNIS PAGE (When Data Entered) R O DOCULMENTATIONkB PAGE READ INSTRUCTIONS REPORT DOCUMENTATION~ PAGE BEFORE COMPLETING FORM 1. REPORT NUMBER 2a. GOVT AQCMCSION N (.SAECIP F.NTTSChALOG NUMBER "NCSC TECHMAN 4110-1-83 (Rev A) A, -NI ' 4. TITLE (and Subtitle) S. TYPE OF REPORT & PERIOD COVERED "Design Guidelines for Carbon Dioxide Scrubbers '" 6. PERFORMING ORG. REPORT N UMBER A' 7. AUTHOR(&) 8. CONTRACT OR GRANT NUMBER(S) M. L. Nuckols, A. Purer, and G. A. Deason 9. PERFORMING ORGANIZATION NAME AND ADDRESS 10. PROGRAM ELEMENT, PROJECT. TASK AREA 6t WORK UNIT NUMBERS Naval Coastal PanaaLSystems 3407Project CenterCty, S0394, Task Area Panama City, FL 32407210,WrUnt2 22102, Work Unit 02 II. CONTROLLING OFFICE NAME AND ADDRE1S t2. REPORT 3ATE May 1983 Rev. July 1985 13, NUMBER OF PAGES 69 14- MONI TORING AGENCY NAME & ADDRESS(if different from Controtling Office) 15. SECURITY CLASS. (of this report) UNCLASSIFIED ISa. OECL ASSI FICATION/DOWNGRADING _ __N•AEOULE 16. DISTRIBUTION STATEMENT (of thia Repott) Approved for public release; distribution unlimited. 17. DISTRIBUTION STATEMENT (of the abstract entered In Block 20, If different from Report) IS. SUPPLEMENTARY NOTES II. KEY WORDS (Continue on reverse side If noceassry and Identify by block number) Carbon Dioxide; Scrubbers; Absorption; Design; Life Support; Pressure; "Swimmer Diver; Environmental Effects; Diving., 20. -
Evaluating the Effectiveness of Scrubber Installation on Sulfur Dioxide Emissions from Coal Electricity Generating Units
Evaluating the Effectiveness of Scrubber Installation on Sulfur Dioxide Emissions from Coal Electricity Generating Units Jayson Toweh Submitted in partial fulfillment of the requirements for the degree of Master of Science in Environmental Health Harvard T.H. Chan School of Public Health Boston, MA August 16, 2019 2 Abstract Background: Electricity generated by coal represents the second-largest contribution to the United States energy portfolio. Resulting emissions, such as sulfur dioxide (SO2) can lead to various adverse health impacts. Research Question: The goal of this study was to evaluate how SO2 scrubber installation affected SO2 emissions from electricity generating units (EGUs). EGU characteristics were analyzed to determine what led EGUs to install scrubbers and the types of scrubbers that were installed. Methods: EPA Air Markets Program Data was analyzed to compare emissions from EGUs that installed SO2 scrubbers between 1995-2015, to EGUs that had no scrubbers. We evaluated emissions changes from three years before to three years of post- scrubber installation. The HYSPLIT Average Dispersion metric model was used to map exposure concentration a year post scrubber installation. Results: SO2 emissions three years post-installation were 10% the levels of three years before installation. Locations in the eastern United States experienced the most significant reduction in exposure from coal EGUs. Wet Limestone scrubbers were installed most frequently contributing to the significant decrease. Discussion: The most extensive and highest emitting EGUs installed scrubbers and some of the best scrubber technology. Finding incentives to increase scrubber installation in lower generating EGUs is critical moving forward. 3 Introduction Electricity Generating Units Emissions Coal power plants are the second-largest contributor to the United States electricity supply, with 1,146 billion kWh produced equating to 27.4% of the energy generated in 2018 (EIA, 2019). -
A Review of the Scrubber As a Tool for the Control of Flue Gas Emissions in a Combustion System
EJERS, European Journal of Engineering Research and Science Vol. 4, No. 11, November 2019 A Review of the Scrubber as a Tool for the Control of flue Gas Emissions in a Combustion System N. Harry-Ngei, I. Ubong, and P. N. Ede Depending on the design, specific factors govern the Abstract—This paper focuses on the description, function application and operation of the scrubber; reference [4] and working principles of the wet gas scrubber required to listed the following vital variables to look out for in control air pollution emissions from a combustion system of a deciding the optimal scrubber for use: boiler. Important points to note in the selection and operation i. Characteristics of the particulate matter of the scrubber as well as the different types of scrubbers commonly deployed in the industries to cut down on emissions considered to be removed were addressed. A comprehensive review of the removal ii. The size categorization of the particulate matter mechanisms and schemes of the scrubber were reported for iii. Concentration of the emission in the flue gas various research on the subject. The packed tower scrubber, iv. Characteristics of the scrubber liquid, for however, was recommended because of varying advantages example, whether it is flammable or combustible and ease of operations. v. Desired removal efficiency Index Terms—Scrubber, Gas Emission, Combustion, vi. Important actual process parameters of the flue Environmental Pollution. gas as this will determine the scrubber sizing vii. Required space for the scrubber The potency and quality of separation and cleaning of I. INTRODUCTION flue gases with regards to air pollution control is depended Reference [1] described scrubbers as devices utilised to on the solvent, therefore, the characteristics, operation, remove gaseous constituents that has debilitating effects on optimum condition must be evaluated before a choice is the environment. -
Venturi Scrubbers
VENTURI PARTICULATE SCRUBBERS Monroe Venturi Scrubber and Cyclonic Separator Monroe Environmental® Venturi Scrubbers Monroe Environmental offers several venturi exhausting a lime kiln are designed to remove both heavy and light design configurations: airborne particulate matter from exhaust sys- • Circular and rectangular venturi scrubbing tems, as well as flue and process gasses. Venturi throats Venturi Scrubber Scrubbers bring particulate–laden air streams Fixed and adjustable throat designs Applications together with water at high velocities to • • Eductor, ejector, and traditional venturi • Automotive manufacturing transfer the particulate into the water stream. throat designs The water droplets and particulates are then • High, medium, and low energy pressure • Glass manufacturing removed from the air stream through centrifu- drops • Machining operations gal separation and mist elimination stages. • Dual Throat Venturi Scrubber • Buffing & deburring • Wax spraying Discharge • Flame laminating Stack • Synthetic resin fines • Grease manufacturing • Explosive dust collection • Foundry dust & fumes Venturi Scrubber Chevron • Sludge dryer exhaust Cyclonic • Incineration processes Separator • Kiln exhaust scrubbing Fan • Frack sand & proppants Venturi Scrubber with • And many others Cyclonic Separator www.mon-env.com • [email protected] • Registered ISO 9001:2015 and ISO 14001:2015 • Venturi Scrubber for frac sand/proppant dust High pressure drop 80 in. W.C. fixed Venturi Scrubber and Cyclonic Separator for PM throat Venturi removal from dryer off–gas prior to RTO. Particulate Removal Monroe Environmental specializes in wet and dry particulate collection for a wide variety Monroe Venturi Air Scrubbers are currently op- of applications. The company’s first project in erating continuously at high efficiency in many the early 1970’s was a pilot venturi scrubbing types of industrial installations throughout the system designed to remove oil and particulate United States, Mexico, and Canada.