Simple Capacitors to Supercapacitors - an Overview
Total Page:16
File Type:pdf, Size:1020Kb
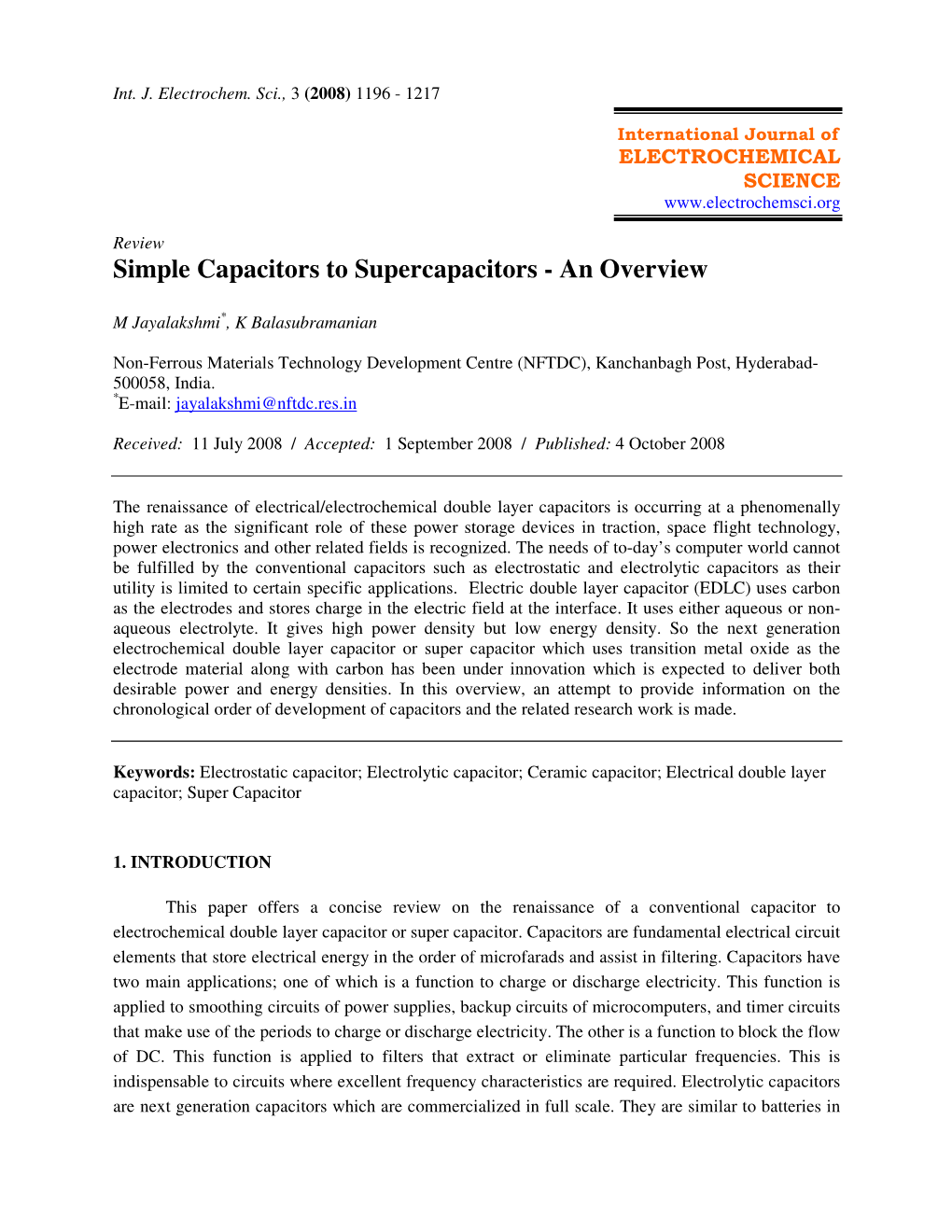
Load more
Recommended publications
-
Structural, Morphological, and Electrochemical Performance of Ceo2/Nio Nanocomposite for Supercapacitor Applications
applied sciences Article Structural, Morphological, and Electrochemical Performance of CeO2/NiO Nanocomposite for Supercapacitor Applications Naushad Ahmad 1, Abdulaziz Ali Alghamdi 1, Hessah A. AL-Abdulkarim 1, Ghulam M. Mustafa 2, Neazar Baghdadi 3 and Fahad A. Alharthi 1,* 1 Department of Chemistry, College of Science, King Saud University, Riyadh 11451, Saudi Arabia; [email protected] (N.A.); [email protected] (A.A.A.); [email protected] (H.A.A.-A.) 2 Department of Physics, The University of Lahore, Lahore 54590, Pakistan; [email protected] 3 Center of Nanotechnology, King Abdulaziz University, Jeddah 80200, Saudi Arabia; [email protected] * Correspondence: [email protected] Abstract: The composite of ceria has been widely studied as an electrode material for supercapacitors applications due to its high energy density. Herein, we synthesize CeO2/NiO nanocomposite via a hydrothermal route and explore its different aspects using various characterization techniques. The crystal structure is investigated using X-ray diffraction, Fourier transform infrared, and Ra- man spectroscopy. The formation of nanoflakes which combine to form flower-like morphology is observed from scanning electron microscope images. Selected area scans confirm the presence of all elements in accordance with their stoichiometric amount and thus authenticate the elemental purity. Polycrystalline nature with crystallite size 8–10 nm having truncated octahedron shape is confirmed from tunneling electron microscope images. Using X-ray photoelectron -
WHITE PAPER: Power Electronic Interface for an Ultracapacitor As the Power Buffer in a Hybrid Electric Energy Storage System
WHITE PAPER POWER ELECTRONIC INTERFACE FOR AN ULTRACAPACITOR AS THE POWER BUFFER IN A HYBRID ELECTRIC ENERGY STORAGE SYSTEM Dr. John Miller, PE, Michaela Prummer and Dr. Adrian Schneuwly Maxwell Technologies, Inc. Maxwell Technologies, Inc. Maxwell Technologies SA Maxwell Technologies GmbH Maxwell Technologies, Inc. - Worldwide Headquarters CH-1728 Rossens Brucker Strasse 21 Shanghai Representative Office 9244 Balboa Avenue Switzerland D-82205 Gilching Rm.2104, Suncome Liauw’s Plaza San Diego, CA 92123 Phone: +41 (0)26 411 85 00 Germany 738 Shang Cheng Road USA Fax: +41 (0)26 411 85 05 Phone: +49 (0)8105 24 16 10 Pudong New Area Phone: +1 858 503 3300 Fax: +49 (0)8105 24 16 19 Shanghai 200120, P.R. China Fax: +1 858 503 3301 Phone: +86 21 5836 5733 [email protected] – www.maxwell.com Fax: +86 21 5836 5620 MAXWELL TECHNOLOGIES WHITE PAPER: Power Electronic Interface For An Ultracapacitor as the Power Buffer in a Hybrid Electric Energy Storage System Ultracapacitor power energy storage cells have been introduced into the marketplace in relatively large volumes since 1996 and continue to experience steady growth. In recent years ultracapacitors have become more accepted as high power buffers for industrial, and transportation applications in combination with conventional lead-acid batteries, as standalone pulse power packs, or in combination with advanced chemistry batteries. The merits of ultracapacitors in such applications arise from their high power capability based on ultra-low internal resistance, wide operating temperature range of -40oC to +65oC, minimal maintenance, relatively high abuse tolerance to over charging and over temperature, high cycling capability on the order of one million charge-discharge events at 75% state-of-charge swing and reasonable price. -
Syfer Capacitor Basics
Syfer Technology Limited, Old Stoke Road, Arminghall, Norwich, Norfolk, NR14 8SQ, United Kingdom Tel: +44 (0) 1603 723300 Tel. (Sales): 01603 723310 Fax: +44 (0) 1603 723301 Email: [email protected] Web: www.knowlescapacitors.com Syfer Capacitor Basics What is a Capacitor ..................................................................................2 Electrode .............................................................................................2 Dielectric .............................................................................................2 Construction ........................................................................................2 MLCC Uses ..............................................................................................3 Limitations and Factors for Consideration ....................................................3 Dielectric Types .......................................................................................4 X7R.....................................................................................................4 X5R.....................................................................................................5 X8R.....................................................................................................5 2C1 (BZ) and 2X1 (BX) .........................................................................5 C0G ....................................................................................................5 High Q .................................................................................................5 -
High Efficiency and High Sensitivity Wireless Power Transfer and Wireless Power Harvesting Systems
High Efficiency and High Sensitivity Wireless Power Transfer and Wireless Power Harvesting Systems by Xiaoyu Wang A dissertation submitted in partial fulfillment of the requirements for the degree of Doctor of Philosophy (Electrical Engineering) in The University of Michigan 2016 Doctoral Committee: Professor Amir Mortazawi, Chair Associate Professor Anthony Grbic Associate Professor Heath Hofmann Professor Jerome P. Lynch © Xiaoyu Wang 2016 All Rights Reserved To my wife Chuan Li, and my parents ii ACKNOWLEDGEMENTS There are numerous people I would like to acknowledge for their guidance, support and friendship throughout my life as a PhD student. First of all, I would like to express my deepest gratitude to my advisor, Professor Amir Mortazawi, who is not only a great mentor, but also a precious friend. The guidance and encouragement from him have been a great treasure for me, without which the work would not have been finished. I would also like to thank my committee members Professor Anthony Grbic, Professor Heath Hofmann and Professor Jerome Lynch for their time and effort serving on my dissertation committee and providing constructive suggestions and comments. Next, I would like to thank Omar Abdelatty, with whom I have been working on the same project since summer 2015. I would also like to express my appreciation to our current and previous group members (in seniority order): Danial Ehyaie, Morteza Nick, Seyit Ahmet Sis, Victor Lee, Waleed Alomar, Seungku Lee, Fatemah (Noyan) Akbar, and Milad Zolfagharloo Koohi, for their friendship -
Flywheel Energy Storage for Automotive Applications
Energies 2015, 8, 10636-10663; doi:10.3390/en81010636 OPEN ACCESS energies ISSN 1996-1073 www.mdpi.com/journal/energies Review Flywheel Energy Storage for Automotive Applications Magnus Hedlund *, Johan Lundin, Juan de Santiago, Johan Abrahamsson and Hans Bernhoff Division for Electricity, Uppsala University, Lägerhyddsvägen 1, Uppsala 752 37, Sweden; E-Mails: [email protected] (J.L.); [email protected] (J.S.); [email protected] (J.A.); [email protected] (H.B.) * Author to whom correspondence should be addressed; E-Mail: [email protected]; Tel.: +46-18-471-5804. Academic Editor: Joeri Van Mierlo Received: 25 July 2015 / Accepted: 12 September 2015 / Published: 25 September 2015 Abstract: A review of flywheel energy storage technology was made, with a special focus on the progress in automotive applications. We found that there are at least 26 university research groups and 27 companies contributing to flywheel technology development. Flywheels are seen to excel in high-power applications, placing them closer in functionality to supercapacitors than to batteries. Examples of flywheels optimized for vehicular applications were found with a specific power of 5.5 kW/kg and a specific energy of 3.5 Wh/kg. Another flywheel system had 3.15 kW/kg and 6.4 Wh/kg, which can be compared to a state-of-the-art supercapacitor vehicular system with 1.7 kW/kg and 2.3 Wh/kg, respectively. Flywheel energy storage is reaching maturity, with 500 flywheel power buffer systems being deployed for London buses (resulting in fuel savings of over 20%), 400 flywheels in operation for grid frequency regulation and many hundreds more installed for uninterruptible power supply (UPS) applications. -
Ltc3225/Ltc3225-1
LTC3225/LTC3225-1 150mA Supercapacitor Charger FEATURES DESCRIPTION n Low Noise Constant Frequency Charging of Two The LTC®3225/LTC3225-1 are programmable supercapaci- Series Supercapacitors tor chargers designed to charge two supercapacitors in n Automatic Cell Balancing Prevents Capacitor series to a selectable fi xed output voltage (4.8V/5.3V for Overvoltage During Charging the LTC3225 and 4V/4.5V for the LTC3225-1) from input n Programmable Charge Current (Up to 150mA) supplies as low as 2.8V to 5.5V. Automatic cell balancing n Selectable 2.4V or 2.65V Regulation per Cell prevents overvoltage damage to either supercapacitor. No (LTC3225) balancing resistors are required. n Selectable 2V or 2.25V Regulation per Cell Low input noise, low quiescent current and low external (LTC3225-1) parts count (one fl ying capacitor, one bypass capacitor at n Automatic Recharge V and one programming resistor) make the LTC3225/ n I = 20μA in Standby Mode IN VIN LTC3225-1 ideally suited for small battery-powered n I < 1μA When Input Supply is Removed COUT applications. n No Inductors n Tiny Application Circuit (2mm × 3mm DFN Package, Charge current level is programmed with an external All Components <1mm High) resistor. When the input supply is removed, the LTC3225/ LTC3225-1 automatically enter a low current state, drawing APPLICATIONS less than 1μA from the supercapacitors. The LTC3225/LTC3225-1 are available in a 10-lead 2mm n Current Limited Applications with High Peak Power × 3mm DFN package. Loads (LED Flash, PCMCIA Tx Bursts, HDD Bursts, L, LT, LTC and LTM are registered trademarks and ThinSOT is a trademark of Linear GPRS/GSM Transmitter) Technology Corporation. -
Introduction What Is a Polymer Capacitor?
ECAS series (polymer-type aluminum electrolytic capacitor) No. C2T2CPS-063 Introduction If you take a look at the main board of an electronic device such as a personal computer, you’re likely to see some of the six types of capacitors shown below (Fig. 1). Common types of capacitors include tantalum electrolytic capacitors (MnO2 type and polymer type), aluminum electrolytic capacitors (electrolyte can type, polymer can type, and chip type), and MLCC. Figure 1. Main Types of Capacitors What Is a Polymer Capacitor? There are many other types of capacitors, such as film capacitors and niobium capacitors, but here we will describe polymer capacitors, a type of capacitor produced by Murata among others. In both tantalum electrolytic capacitors and aluminum electrolytic capacitors, a polymer capacitor is a type of electrolytic capacitor in which a conductive polymer is used as the cathode. In a polymer-type aluminum electrolytic capacitor, the anode is made of aluminum foil and the cathode is made of a conductive polymer. In a polymer-type tantalum electrolytic capacitor, the anode is made of the metal tantalum and the cathode is made of a conductive polymer. Figure 2 shows an example of this structure. Figure 2. Example of Structure of Conductive Polymer Aluminum Capacitor In conventional electrolytic capacitors, an electrolyte (electrolytic solution) or manganese dioxide (MnO2) was used as the cathode. Using a conductive polymer instead provides many advantages, making it possible to achieve a lower equivalent series resistance (ESR), more stable thermal characteristics, improved safety, and longer service life. As can be seen in Fig. 1, polymer capacitors have lower ESR than conventional electrolytic Copyright © muRata Manufacturing Co., Ltd. -
Synthesis of Nano-Ceramics for Supercapacitors
University of Wollongong Research Online University of Wollongong Thesis Collection 1954-2016 University of Wollongong Thesis Collections 2014 Synthesis of nano-ceramics for supercapacitors Azrin Akhter Chowdhury University of Wollongong Follow this and additional works at: https://ro.uow.edu.au/theses University of Wollongong Copyright Warning You may print or download ONE copy of this document for the purpose of your own research or study. The University does not authorise you to copy, communicate or otherwise make available electronically to any other person any copyright material contained on this site. You are reminded of the following: This work is copyright. Apart from any use permitted under the Copyright Act 1968, no part of this work may be reproduced by any process, nor may any other exclusive right be exercised, without the permission of the author. Copyright owners are entitled to take legal action against persons who infringe their copyright. A reproduction of material that is protected by copyright may be a copyright infringement. A court may impose penalties and award damages in relation to offences and infringements relating to copyright material. Higher penalties may apply, and higher damages may be awarded, for offences and infringements involving the conversion of material into digital or electronic form. Unless otherwise indicated, the views expressed in this thesis are those of the author and do not necessarily represent the views of the University of Wollongong. Recommended Citation Chowdhury, Azrin Akhter, Synthesis of nano-ceramics for supercapacitors, Doctor of Philosophy thesis, Engineering Materials Institute, University of Wollongong, 2014. https://ro.uow.edu.au/theses/4314 Research Online is the open access institutional repository for the University of Wollongong. -
Review of Technologies and Materials Used in High-Voltage Film Capacitors
polymers Review Review of Technologies and Materials Used in High-Voltage Film Capacitors Olatoundji Georges Gnonhoue 1,*, Amanda Velazquez-Salazar 1 , Éric David 1 and Ioana Preda 2 1 Department of Mechanical Engineering, École de technologie supérieure, Montreal, QC H3C 1K3, Canada; [email protected] (A.V.-S.); [email protected] (É.D.) 2 Energy Institute—HEIA Fribourg, University of Applied Sciences of Western Switzerland, 3960 Sierre, Switzerland; [email protected] * Correspondence: [email protected] Abstract: High-voltage capacitors are key components for circuit breakers and monitoring and protection devices, and are important elements used to improve the efficiency and reliability of the grid. Different technologies are used in high-voltage capacitor manufacturing process, and at all stages of this process polymeric films must be used, along with an encapsulating material, which can be either liquid, solid or gaseous. These materials play major roles in the lifespan and reliability of components. In this paper, we present a review of the different technologies used to manufacture high-voltage capacitors, as well as the different materials used in fabricating high-voltage film capacitors, with a view to establishing a bibliographic database that will allow a comparison of the different technologies Keywords: high-voltage capacitors; resin; dielectric film Citation: Gnonhoue, O.G.; Velazquez-Salazar, A.; David, É.; Preda, I. Review of Technologies and 1. Introduction Materials Used in High-Voltage Film High-voltage films capacitors are important components for networks and various Capacitors. Polymers 2021, 13, 766. electrical devices. They are used to transport and distribute high-voltage electrical energy https://doi.org/10.3390/ either for voltage distribution, coupling or capacitive voltage dividers; in electrical sub- polym13050766 stations, circuit breakers, monitoring and protection devices; as well as to improve grid efficiency and reliability. -
Suggestion of the Supercapacitor(EDLC) Application to the Electrical Characteristic Tester
Supercapacitor (EDLC) Application Note No. C2M1CXS-163A(E) Suggestion of the Supercapacitor(EDLC) Application to the Electrical Characteristic Tester 1. Summary Supercapacitor, also known as EDLC or supercap, has higher-capacity than ceramic capacitor or electrolytic capacitor. And supercapacitor is an energy storage device having longer life than a battery. In addition, Murata’s supercapacitor can handle the output power up to 50W by realizing super low ESR approximately 40mΩ (DMF series example) At the measurement environment that a high peak electric current runs through the load instantly, our supercapacitor can assist such peak current. By this effect, it is possible to downsize Fig.3 : Measurement Block Diagram with Supercapacitor and reduce power capacity of DC power supply. Besides it contributes to reduce measuring equipment cost and save the Fig.4 and Fig.5 shows each part waveform. electric power of the facilities. Top(Yellow):Load current, Middle(Green):Power line voltage, Bottom(Purple):DC power supply current. 2. Benefits Fig.4: DC power supply only. ①Downsize the DC power supply Fig.5: Supercap is added to DC power supply. Even if the power supply capacity cannot support a peak current, The effect of supercap can be confirmed because the fluctuation it does not matter because supercap can assist it. ②Supercapacitor as a power source of the input voltage is smaller and the peak current of power Because supercap can be charged quickly, it is possible to use supply decreases. supercap as power source at the time of measurement. ③Reduce the cost and Save power of measurement equipment. ④Can be mounted on limited area because of its thinner and smaller shape. -
Aluminum Electrolytic Vs. Polymer – Two Technologies – Various Opportunities
Aluminum Electrolytic vs. Polymer – Two Technologies – Various Opportunities By Pierre Lohrber BU Manager Capacitors Wurth Electronics @APEC 2017 2017 WE eiCap @ APEC PSMA 1 Agenda Electrical Parameter Technology Comparison Application 2017 WE eiCap @ APEC PSMA 2 ESR – How to Calculate? ESR – Equivalent Series Resistance ESR causes heat generation within the capacitor when AC ripple is applied to the capacitor Maximum ESR is normally specified @ 120Hz or 100kHz, @20°C ESR can be calculated like below: ͕ͨ͢ 1 1 ͍̿͌ Ɣ Ɣ ͕ͨ͢ ∗ ͒ ͒ Ɣ Ɣ 2 ∗ ∗ ͚ ∗ ̽ 2 ∗ ∗ ͚ ∗ ̽ ! ∗ ̽ 2017 WE eiCap @ APEC PSMA 3 ESR – Temperature Characteristics Electrolytic Polymer Ta Polymer Al Ceramics 2017 WE eiCap @ APEC PSMA 4 Electrolytic Conductivity Aluminum Electrolytic – Caused by the liquid electrolyte the conductance response is deeply affected – Rated up to 0.04 S/cm Aluminum Polymer – Solid Polymer pushes the conductance response to much higher limits – Rated up to 4 S/cm 2017 WE eiCap @ APEC PSMA 5 Electrical Values – Who’s Best in Class? Aluminum Electrolytic ESR approx. 85m Ω Tantalum Polymer Ripple Current rating approx. ESR approx. 200m Ω 630mA Ripple Current rating approx. 1,900mA Aluminum Polymer ESR approx. 11m Ω Ripple Current rating approx. 5,500mA 2017 WE eiCap @ APEC PSMA 6 Ripple Current >> Temperature Rise Ripple current is the AC component of an applied source (SMPS) Ripple current causes heat inside the capacitor due to the dielectric losses Caused by the changing field strength and the current flow through the capacitor 2017 WE eiCap @ APEC PSMA 7 Impedance Z ͦ 1 ͔ Ɣ ͍̿͌ ͦ + (͒ −͒ )ͦ Ɣ ͍̿͌ ͦ + 2 ∗ ∗ ͚ ∗ ͍̿͆ − 2 ∗ ∗ ͚ ∗ ̽ 2017 WE eiCap @ APEC PSMA 8 Impedance Z Impedance over frequency added with ESR ratio 2017 WE eiCap @ APEC PSMA 9 Impedance @ High Frequencies Aluminum Polymer Capacitors have excellent high frequency characteristics ESR value is ultra low compared to Electrolytic’s and Tantalum’s within 100KHz~1MHz E.g. -
Technical Notes for Electrolytic Capacitor
TECHNICAL NOTES FOR EL ECTROLYTIC CAPACITOR 2. MANUFACTURE OF ALUMINUM ELECTROLYTIC CAPACITOR Raw Aluminum Foil (1) Etching To obtain higher capacitance, surface area of aluminum foil for electrolytic capacitor increases through etching process. In etching process, aluminum foil is applied with DC or Etched Aluminum Foil AC current in a chloride solution to preferentially dissolve the surface. Surface area is increased by 60-150 times for low voltage foils and 10-30 times for high voltage foils. (2) Anodization(Formation of Dielectric Layer) Aluminum foil for electrolytic capacitor is further formed with anodic oxide film (Al2O3) on the surface as dielectric layer. Etched aluminum foil is immersed into a solution Formed Foil including ammonium salt of boric acid or phosphoric acid and applied with DC voltage so that the foil Aluminum Oxide becomes positive and the solution becomes negative. Then aluminum oxide film is formed on the surface in proportion to the applied voltage. The anodic oxide film, having the thickness of 13-15 angstrom/V (1.3-1.5 nm/V), is extremely thin, compact and highly Aluminum Substrate insulating. RUBYCON CORPORATION 2 TECHNICAL NOTES FOR EL ECTROLYTIC CAPACITOR Slitting (3) Slitting Process Etching and Forming are processed with wide roll of master foil. Then the master roll is slitted into individual rolls with specified width as per the specification. Stitching & Winding (4) Stitching and Winding Slit anode and cathode foils after slitting process are stitched with lead tabs and wound into cylindrical element together with spacer paper. Spacer paper is to contain liquid electrolyte that works as real cathode and restores damaged dielectric film, as well as maintaining the distance between anode and cathode foils constant to prevent short circuit.