Accelerating Wind Turbine Blade Circularity May 2020
Total Page:16
File Type:pdf, Size:1020Kb
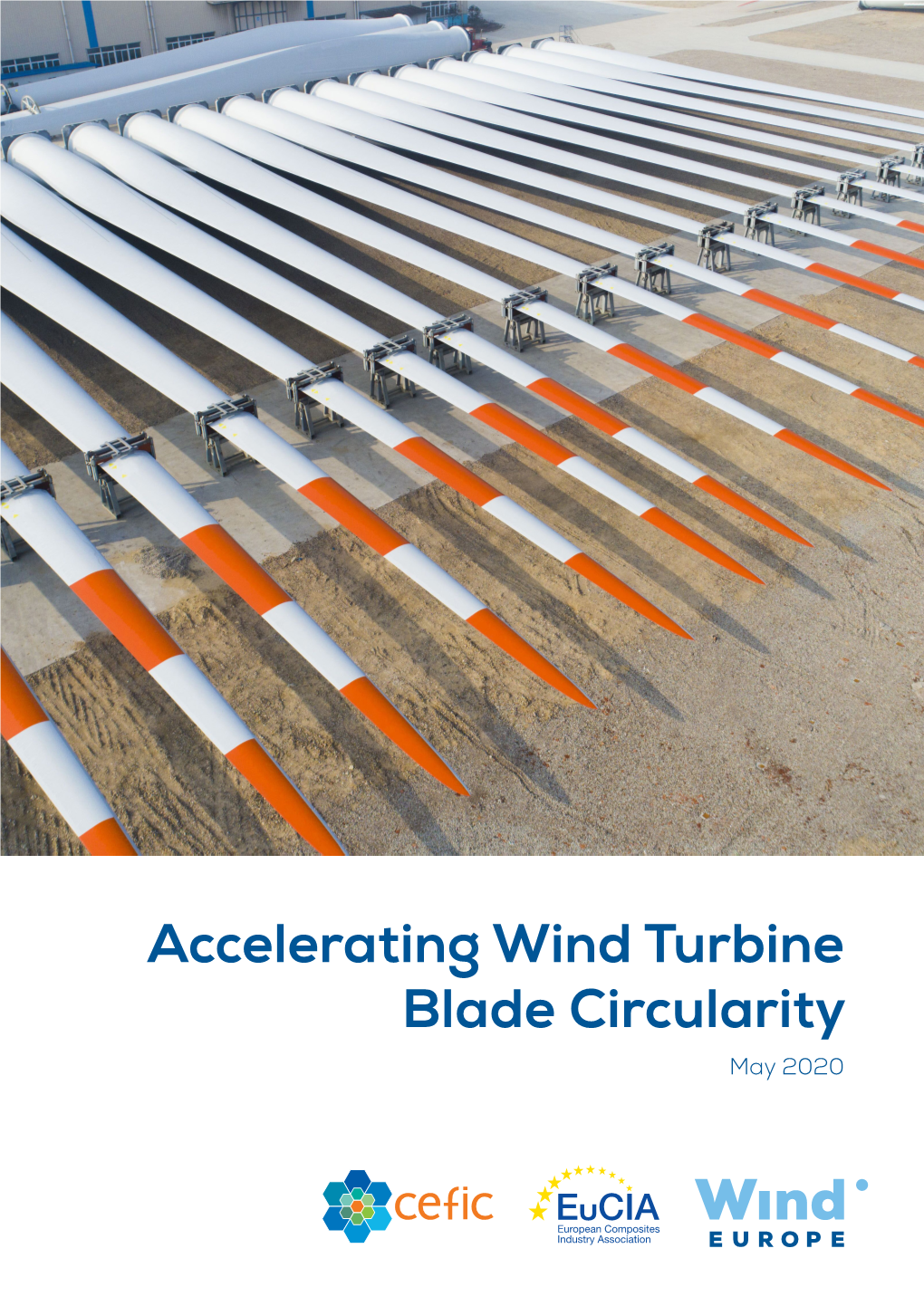
Load more
Recommended publications
-
The 4Th Wind Energy Systems Engineering Workshop
The 4th Wind Energy Systems Engineering Workshop September 13th-14th, 2017 Risø DTU National Laboratory for Sustainable Energy Roskilde, Denmark Sponsored by: DTU Wind Energy National Renewable Energy Laboratory Workshop Agenda Overview: The 4th workshop on systems engineering for wind energy will take place on the 13th and 14th of September, 2017. The first workshop in December 2010 was a success in catalyzing interest in this important topic among participants from industry, the national laboratories and academia. The second and third workshops in January 2013 and 2015, respectively, with more than 100 participants each, demonstrated the significant growth in interest from the research and industry community surrounding systems engineering for wind energy and integrated approaches to wind turbine and plant design. At this fourth workshop, DTU Wind Energy and NREL will be hosting the workshop in Europe to encourage participation from European wind energy systems engineering practitioners and interested parties. This year’s theme will be on exposing interactions in the system and exploring how different wind energy stakeholders addressing them in new, integrated and innovative ways. Short Agenda Wednesday, September 13th, 2017 8:30 a.m. – 9:00 a.m. Registration and Breakfast 8:30 a.m. ‒ 12:15 p.m. Morning sessions 12:15 p.m. ‒ 1:00 p.m. Lunch 1:30 p.m. ‒ 5:45 p.m. Afternoon sessions 5:45 p.m. ‒ 7:30 p.m. Evening reception and poster session (appetizers) Thursday, September 14th, 2017 8:00 a.m. – 8:30 a.m. Registration and Breakfast 8:30 a.m. ‒ 12:00 p.m. -
Wind Energy in Europe 2020 Statistics and the Outlook for 2021-2025
Subtittle if needed. If not MONTH 2018 Published in Month 2018 Wind energy in Europe 2020 Statistics and the outlook for 2021-2025 Wind energy in Europe 2020 Statistics and the outlook for 2021-2025 Published in February 2021 windeurope.org This report summarises new installations and financing activity in Europe’s wind farms from 1 January to 31 December 2020. It also analyses how European markets will develop in the next five years (2021 to 2025). The outlook is based on WindEurope internal analysis and consultation with its members. The data represents gross installations per site and country unless otherwise stated. Rounding of figures is at the discretion of the author. DISCLAIMER This publication contains information collected on a regular basis throughout the year and then verified with relevant members of the industry ahead of publication. Neither WindEurope, nor its members, nor their related entities are, by means of this publication, rendering professional advice or services. Neither WindEurope nor its members shall be responsible for any loss whatsoever sustained by any person who relies on this publication. TEXT AND ANALYSIS: WindEurope Business Intelligence Ivan Komusanac Guy Brindley Daniel Fraile Lizet Ramirez EDITOR: Rory O’Sullivan DESIGN: Lin Van de Velde, Drukvorm PHOTO COVER: Jacques Tarnero for Shutterstock WindEurope acknowledges the kind cooperation of the following associations and institutions: IG Windkraft (AT) – BOP, EDORA and ODE (BE) - BGWEA (BG) – HROTE, Renewable Energy Sources of Croatia (HR) - Czech Wind -
Corporate Non-Financial Reporting in Germany
Copyright © Development International e.V., 2019 ISBN: 978-3-9820398-1-7 Authors: Chris N. Bayer, PhD Gisella Vogel Sarah Kaltenhäuser Katherine Storrs Jiahua (Java) Xu, PhD Juan Ignacio Ibañez, LL.M. Title: A New Responsibility for Sustainability: Corporate Non-Financial Reporting in Germany Date published: May 6, 2019 Funded by: iPoint-systems gmbh www.ipoint-systems.com Executive Summary Germany's economy is the fourth-largest in the world (by nominal GDP), and with 28% of the euro area market, it represents the largest economy in Europe.1 Considering the supply chains leading to its economy, Germany's cumulative environmental, social and governance performance reverberates globally. The EU Non-Financial Reporting Directive (NFRD) is the impetus behind this study – a new regulation that seeks to “increase the relevance, consistency and comparability of information disclosed by certain large undertakings and groups across the Union.”2 Large undertakings in EU member states are not only required to report on their financial basics, now they are also required by Article 1 of the Directive to account for their non- financial footprint, including adverse impacts they have on the environment and supply chains. In accordance with the Directive, the German transposition stipulates that the non-financial declaration must state which reporting framework was used to create it (or explain why no framework was applied), as well as apply non-financial key performance indicators relevant to the particular business. These requirements are our point of departure: We systematically assess the degree of non-financial transparency and performance reporting for 2017 applying an ex-post assessment framework premised on the Global Reporting Initiative (GRI), the German Sustainability Code (Deutscher Nachhaltigkeitskodex, DNK) and the United Nations Global Compact (UNGC). -
Nordex Group Announces New N149/5.X Turbine
PRESS RELEASE Entering the 5 MW class: Nordex Group announces new N149/5.X turbine Powerful addition to the Delta4000 series presented in 2017 Hamburg, 26 March 2019. The Nordex Group is extending its product portfolio with a multi-megawatt machine in the 5 MW class. After the N149/4.0-4.5 and the N133/4.8, the new N149/5.X is the third turbine type in the Delta4000 series. The N149/5.X is designed for moderate and light-wind areas and can also perform optimally at sites with complex requirements. Apart from the classic core markets in Europe, the target markets for the N149/5.X also cover global growth regions such as South Africa, Australia and South America. The N149/5.X is designed for maximum flexibility and can be operated in different modes in the 5 MW range depending on site requirements and customer needs. This enables customers to individually configure the wind farm in terms of the output, capacity and lifetime of the turbine, as well as with regard to sound requirements, and thus adapt it ideally to the company's respective business model. The N149/5.X is a logical progression based on the successful approach of a flexible power range in the N149/4.0-4.5. "Thanks to the proven technological basis of the Delta4000 product series we are in a position to continuously develop highly efficient solutions for different wind regimes and different geographical regions and to ensure short lead times for product launches. We have designed the N149/5.X with its maximum flexibility and efficiency to exactly meet the needs of our customers," says José Luis Blanco, CEO Nordex Group. -
(2019), Hydrogen Production from Offshore Wind Power
HYDROGEN PRODUCTION FROM OFFSHORE WIND POWER Denis THOMAS Business Development - Renewable Hydrogen Hydrogenics Europe N.V. WindEurope Exhibition 2019 Bilbao (Spain), 2 April 2019 1 MHI VESTAS THOUGHT LEADERS FORUM| BILBAO (SP) | 02.04.2019 Hydrogen production from offshore wind power AGENDA 1. Intro: Hydrogenics, Hydrogen and Renewable Hydrogen 2. Renewable hydrogen from floating offshore wind in Japan (JIDAI) 3. Renewable hydrogen from offshore wind in the Netherlands 4. Closing remarks 2 MHI VESTAS THOUGHT LEADERS FORUM| BILBAO (SP) | 02.04.2019 Hydrogenics in Brief 4 productions sites Belgium, Canada, Germany and USA 180+ ON-SITE HYDROGEN GENERATION dedicated employees Electrolyzers Our raw materials $ 48M Industrial Hydrogen supply water & renewable power are 2017 annual sales H2O + electricity H2 + ½ O2 infinite! 2000+ 1 single focus fuel cell sites hydrogen solutions POWER SYSTEMS Fuel cells Stand-by Power Mobile Power Modules 500+ MW Power Plants Publicly Electrolysis plants traded in operation H2 + ½ O2 H2O + electricity NASDAQ (HYGS) and TSX (HYG) since 20002000 Global leader in 2 main hydrogen technologies: RENEWABLE HYDROGEN electrolysis and fuel cells 70+ years Energy Storage of experience 1,500+ Hydrogen Refueling Station Electrolysis plants Power-to-X sold since 1948 Grid balancing services 3 MHI VESTAS THOUGHT LEADERS FORUM| BILBAO (SP) | 02.04.2019 HySTAT™ 60 - alkaline electrolyser 4 MHI VESTAS THOUGHT LEADERS FORUM| BILBAO (SP) | 02.04.2019 World hydrogen market But most (96%) of the hydrogen ~1 €/kg produced today is not CO2-free (from gas, oil, coal) 2-8 €/kg If produced from renewable power via electrolysis, hydrogen is fully renewable and CO2-free. 1-2 €/kg Renewable hydrogen has the potential to decarbonize a large 20 €/MWh (power) range of applications 1 €/kg H2 (power cost in H2 cost) ~10 €/kg Production Storage / Transport / Distribution End5 -use MHI VESTAS THOUGHT LEADERS FORUM| BILBAO (SP) | 02.04.2019 Data source: The Hydrogen Economy, M. -
IBM Security Appscan Standard: User Guide Traffic Log
IBM Security AppScan Standard Version 9.0.3.11 User Guide IBM Contents Chapter 1. Introduction ........ 1 Content-Based Results view ........ 90 Product overview............. 1 Glass Box view ............ 92 Supported technologies .......... 1 Communication and Proxy view ...... 93 What's new ............... 2 HTTP Authentication view ........ 94 Contact and support information ....... 3 Test Policy view ............ 95 Test Optimization view ......... 100 Chapter 2. Installing ......... 5 Test Options view ........... 100 Privilege Escalation view ........ 103 System requirements............ 5 Malware view ............ 104 Flash Player upgrade .......... 7 Scan Expert view ........... 104 Flash Player configuration ......... 7 Advanced Configuration view....... 106 Install................. 8 Scan file structure ............ 121 Silent install .............. 8 Scan templates ............. 121 Uninstall................ 9 Predefined templates .......... 121 License ................ 9 User-Defined Scan Templates ....... 123 Load a node-locked license ........ 10 Loading scan templates ......... 123 Load a floating or token license....... 11 Editing Scan Templates ......... 123 Updates ............... 11 Changing the configuration during a scan .... 124 Temp file location ............ 12 Chapter 3. Getting started ...... 13 Chapter 5. Manual Exploring ..... 125 Using AppScan............. 125 How an automatic scan works ........ 13 Recording a Manual Explore ....... 126 Web applications vs. web services ....... 14 Exporting Manual Explore data -
Interim Financial Report, Second Quarter 2021
Company announcement No. 16/2021 Interim Financial Report Second Quarter 2021 Vestas Wind Systems A/S Hedeager 42,8200 Aarhus N, Denmark Company Reg. No.: 10403782 Wind. It means the world to us.TM Contents Summary ........................................................................................................................................ 3 Financial and operational key figures ......................................................................................... 4 Sustainability key figures ............................................................................................................. 5 Group financial performance ....................................................................................................... 6 Power Solutions ............................................................................................................................ 9 Service ......................................................................................................................................... 12 Sustainability ............................................................................................................................... 13 Strategy and financial and capital structure targets ................................................................ 14 Outlook 2021 ................................................................................................................................ 17 Consolidated financial statements 1 January - 30 June ......................................................... -
Wind Energy and Economic Recovery in Europe How Wind Energy Will Put Communities at the Heart of the Green Recovery
Wind energy and economic recovery in Europe How wind energy will put communities at the heart of the green recovery Wind energy and economic recovery in Europe How wind energy will put communities at the heart of the green recovery October 2020 windeurope.org Wind energy and economic recovery in Europe: How wind energy will put communities at the heart of the green recovery WindEurope These materials, including any updates to them, are The socio-economic impact evaluation of wind energy on published by and remain subject to the copy right of the European Union has been carried out using the SNA93 the Wood Mackenzie group ("Wood Mackenzie"), its methodology (System of National Accounts adopted in licensors and any other third party as applicable and are 1993 by the United Nations Statistical Commission) and made available to WindEurope (“Client”) and its Affiliates Deloitte’s approaches, which evaluate the effects of the under terms agreed between Wood Mackenzie and Client. renewable energy in the economy. The use of these materials is governed by the terms and conditions of the agreement under which they were Deloitte has provided WindEurope solely with the services provided. The content and conclusions contained are and estimations defined in the proposal signed by confidential and may not be disclosed to any other person WindEurope and Deloitte on March 13th, 2020. Deloitte without Wood Mackenzie's prior written permission. accepts no responsibility or liability towards any third The data and information provided by Wood Mackenzie party that would have access to the present document should not be interpreted as advice. -
Use Wind Intelligently. Live Sustain- Ability
SUSTAINABILITY REPORT USE WIND INTELLIGENTLY LIVE SUSTAINABILITY USE WIND INTELLIGENTLY. LIVE SUSTAIN- consolidated net profit 2017 in EUR million, ABILITY. 2016: EUR 141.8 million As a company that is fully aware of its responsi- bilities, through our wind energy systems we aim to contribute to climate-friendly energy gener- ation – and ensure sustainable thinking is em- bedded in all areas of our Company. installed capacity 2017 in MW, WE ARE NORDEX 2016: 2,622 MW THE NORDEX GROUP is one of the world’s lead- ing providers of high-performance wind power systems. The Group unites the two formerly in- dependent manufacturers – Acciona Windpower and Nordex – which complement each other per- fectly. Whereas Acciona Windpower generates employees 2017 at the reporting date, the majority of its revenues from major projects in growth markets, Nordex focuses its business 2016: 5,129 employees activities on Europe. By bundling these business activities, we cover around 90 percent of the markets (excluding China) for onshore systems. As both sections of our Company have different focus areas we can offer suitable wind turbines to meet very different requirements. Our manu- facturing network includes facilities in Germany, Spain, Brazil and India. In 2017 we also estab- lished a technology center in Denmark for rotor energy consumption per installed blade development. Nordex’s focus lies not only capacity 2017 in kWh / MW, on sustainable economic growth but also on 2016: 22,819 kWh / MW taking responsibility and countering the chal- lenges posed by climate change. Our Sustain- ability Strategy forms the foundation for our actions, entitled: ‘Use wind intelligently – live sustainability’. -
Drägerwerk AG & Co. Kgaa Single Entity Financial Statements for 2010
Single entity financial statements and management report of Drägerwerk AG & Co. KGaA AS OF DECEMBER 31, 2010 MANAGEMENT REPORT FINANCIAL STATEMENTS NOTES 1 CONTENTS Management report of Drägerwerk AG & Co. KGaA 2 Forward-looking statements 37 Single entity financial statements of Drägerwerk AG & Co. KGaA 39 Income statement of Drägerwerk AG & Co. KGaA from January 1 to December 31, 2010 39 Balance sheet of Drägerwerk AG & Co. KGaA as of December 31, 2010 40 Analysis of non-current assets of Drägerwerk AG & Co. KGaA 42 Notes to Drägerwerk AG & Co. KGaA single entity financial statements 2010 44 The Company’s Boards 70 Major direct and indirect shareholdings of Drägerwerk AG & Co. KGaA 76 Management compliance statement 81 2 IMPORTANT CHANGES IN FISCAL YEAR 2010 Management report of ting of Drägerwerk AG & Co. KGaA on May 8, 2009. The annual shareholders’ meeting had authorized Dräger - Drägerwerk AG & Co. KGaA werk Verwaltungs AG to increase the capital stock of the Company, with the approval of the Supervisory Board of the Company, through a single or multiple issue of new bearer common shares (no-par shares) in return for cash Important changes in fiscal year 2010 and/or deposits in kind by up to EUR 16,256,000.00 (approved capital). CAPITAL INCREASE On June 30, 2010, Drägerwerk AG & Co. KGaA increased The Company offered the new ordinary shares to the sha - its capital stock by EUR 9,753,600 to EUR 42,265,600 by reholders at a ratio of 10:3 at a subscription price of issuing 3,810,000 new bearer common shares (no-par EUR 27.50 each by way of an indirect subscription right shares) with a share of EUR 2.56 each in capital stock (Sec. -
AQR International R.C. Equity Mutual Fund June 30, 2019
AQR International R.C. Equity Mutual Fund June 30, 2019 Portfolio Exposures NAV: $28,103,726 Asset Class Security Description Exposure Quantity Equity 1&1 Drillisch Ord Shs (95,027) (2,846) Equity A P Moller Maersk Ord Shs Class B (320,512) (258) Equity A2A Ord Shs 14,344 8,254 Equity Abn Amro Bank Ord Shs 16,413 766 Equity Acs Actividades De Construccion Y Servicios Ord Shs 102,797 2,571 Equity Adecco Group Ord Shs 124,299 2,066 Equity Adidas N Ord Shs 359,272 1,162 Equity Adyen Ord Shs 222,563 288 Equity Aegon Ord Shs (8,266) (1,658) Equity Aeon Ord Shs (30,924) (1,800) Equity Ageas Ord Shs 50,285 966 Equity Aggreko Ord Shs 20,310 2,020 Equity AGL Energy Ord Shs 10,503 748 Equity Airbus Ord Shs 103,224 727 Equity Aisin Seiki Ord Shs 37,878 1,100 Equity Alfresa Holdings Ord Shs 64,143 2,600 Equity Allianz Ord Shs 659,575 2,732 Equity Alps Alpine Ord Shs 52,252 3,100 Equity Alstom Ord Shs 8,410 181 Equity Altice Europe Ord Shs (55,005) (15,290) Equity Altran Technologies Ord Shs (512,420) (32,244) Equity Amadeus It Group Ord Shs 192,293 2,424 Equity Amcor CDI (12,725) (1,120) Equity AMP Ord Shs 8,312 5,587 Equity ams Ord Shs (13,110) (334) Equity Anglo American Ord Shs 396,321 13,874 Equity Ansell Ord Shs 20,180 1,071 Equity Aristocrat Leisure Ord Shs (9,421) (437) Equity Asahi Intecc Ord Shs (9,853) (400) Equity Asics Ord Shs (15,164) (1,400) Equity ASM International Ord Shs 43,363 665 Equity Asos Ord Shs (129,296) (3,984) Equity ASR Nederland Ord Shs 283,476 6,961 Equity Assicurazioni Generali Ord Shs 47,259 2,506 Equity Astellas Pharma Ord Shs 289,219 20,300 Equity Atlas Copco Ord Shs Class B 8,815 307 Equity Atos Ord Shs 215,926 2,579 Equity Aurizon Holdings Ord Shs 125,889 33,221 rrid-3841199 AQR Capital Management, LLC | Two Greenwich Plaza | Greenwich, CT 06830 | p: +1.203.742.3600 | f: +1.203.742.3100 | w: aqr.com AQR International R.C. -
Offshore Wind in Europe – Key Trends and Statistics 2020
Offshore Wind in Europe Key trends and statistics 2020 Offshore Wind in Europe Key trends and statistics 2020 Published in February 2021 windeurope.org This report summarises construction and financing activity in European offshore wind farms from 1 January to 31 December 2020. WindEurope regularly surveys the industry to determine the level of installations of foundations and turbines, and the subsequent dispatch of first power to the grid. The data includes demonstration sites and factors in decommissioning where it has occurred. Annual installations are expressed in gross figures while cumulative capacity represents net installations per site and country. Rounding of figures is at the discretion of the author. DISCLAIMER This publication contains information collected on a regular basis throughout the year and then verified with relevant members of the industry ahead of publication. Neither WindEurope nor its members, nor their related entities are, by means of this publication, rendering professional advice or services. Neither WindEurope nor its members shall be responsible for any loss whatsoever sustained by any person who relies on this publication. TEXT AND ANALYSIS: Lizet Ramírez, WindEurope Daniel Fraile, WindEurope Guy Brindley, WindEurope EDITOR: Rory O’Sullivan, WindEurope DESIGN: Laia Miró, WindEurope Lin Van de Velde, Drukvorm FINANCE DATA: Clean Energy Pipeline and IJ Global All currency conversions made at EUR/ GBP 0.8897 and EUR/USD 1.1422. Figures include estimates for undisclosed values. PHOTO COVER: Kriegers Flak