Biaxial Testing of Fabrics - a Comparison of Various Testing Methodologies O.B
Total Page:16
File Type:pdf, Size:1020Kb
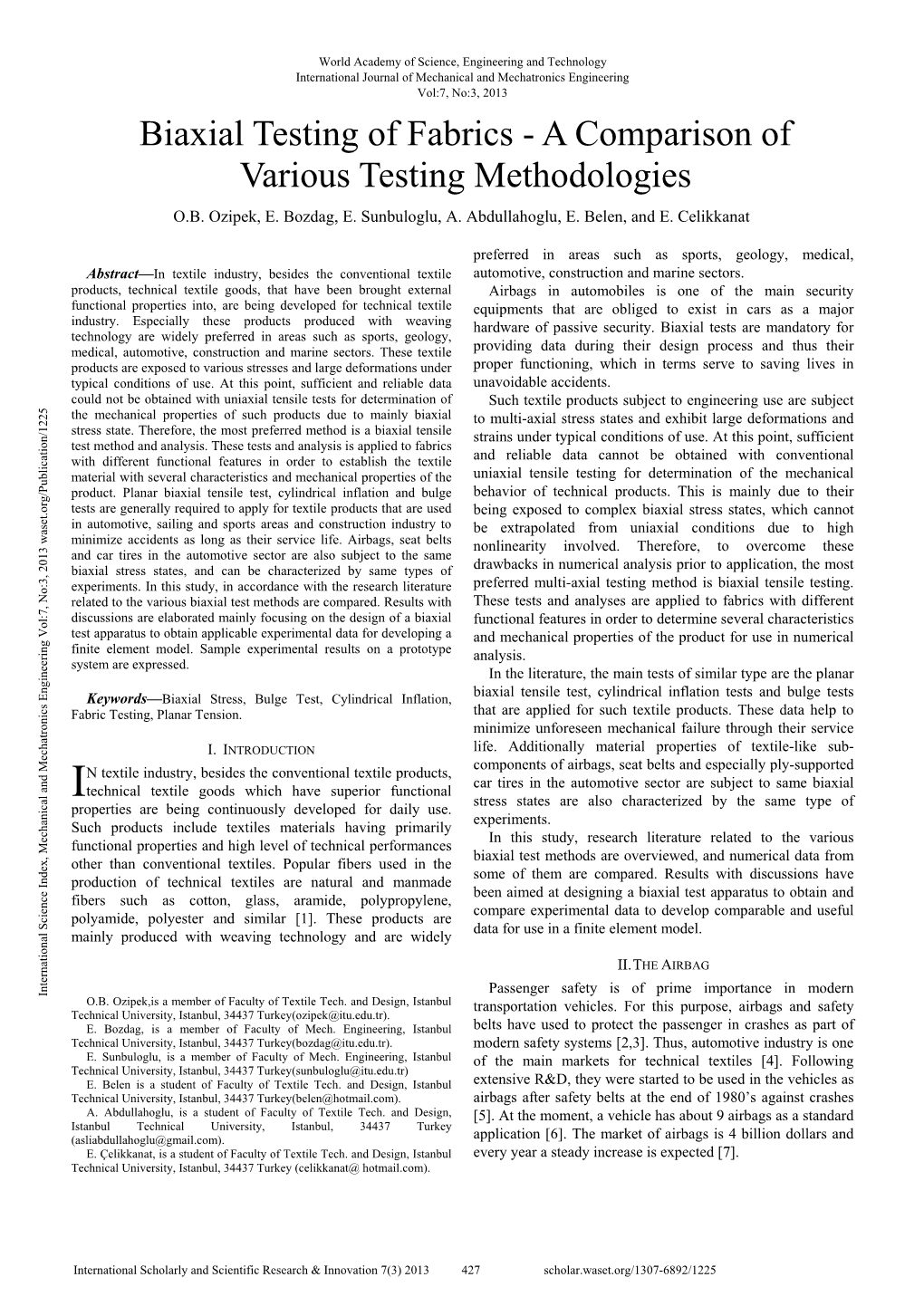
Load more
Recommended publications
-
An Experimental and Modeling Study of the Viscoelastic Behavior Of
ð þ1 t An Experimental and Modeling rðÞ¼t re þ rsðÞexp À ds (1) Study of the Viscoelastic Behavior 0 s of Collagen Gel In Eq. (1), re is the equilibrium stress, and r(s) is the relaxation time distribution function with relaxation time s. Viscoelastic biomaterials likely contain a continuous spectrum Bin Xu of relaxation time constants [5]. While Eq. (1) can be well fitted with a few exponential terms, the fitting may provide little infor- Haiyue Li mation relevant to the characterization of intrinsic material prop- erties [6]. In the present study, the time-dependent distribution spectrum r(s) of collagen gel is obtained through numerical Department of Mechanical Engineering, inverse Laplace transform. Investigating the spectrum in terms of Boston University, the number of peaks, time constants, and peak intensity was found 110 Cummington Mall, to appropriately demonstrate the main properties of viscoelastic Boston, MA 02215 behaviors [7,8]. The intensity of the peak reflects the amount of dissipated energy during relaxation. The number of peaks and time constants are often correlated with specific molecular archi- Yanhang Zhang1 tectures; as a result it can be used as an approach to understand the structural behavior of biomaterials, as well as a useful tool to Associate Professor distinguish materials [9,10]. Department of Mechanical Engineering, In this study, the relaxation time distribution spectrum is Department of Biomedical Engineering, obtained from stress relaxation data by means of inverse Laplace Boston University, transform. This spectrum is employed to understand the mecha- 110 Cummington Mall, nisms of stress relaxation in collagen network. -
Mechanical Characterisation of Hydrogels for Tissue Engineering
CHAPTER 12 Mechanical Characterisation of Hydrogels for Tissue Engineering Applications M. Ahearne*, Y. Yang and K-K Liu Summary ydrogels have been extensively investigated for use as constructs to engineer tissues in-vitro. Among the principal limitations with using hydrogels for engineering tissues are their poor mechanical H characteristics. Many techniques exist to measure the mechanical properties of hydrogels but few allow non-destructive monitoring of these propertie s under cells culture conditions. Two recently developed techniques shall be discussed in detail in the current chapter. Thin hydrogels have been clamped around their outer edge and deformed using a spherical load. The time-dependent deformation has been measured in-situ using a long focal distance microscope connected to a CCD camera and the deformation displacement has been used with a theoretical model to quantify the mechanical and viscoelastic properties of the hydrogels. For thicker hydrogels, optical coherence tomography has been used to measure the time-dependent depth of indentation caused by a spherical load on top of the hydrogel. Hertz contact theory has been applied to calculate the hydrogels mechanical properties. The mechanical and viscoelastic properties of several different hydrogel materials were examined. The principal advantages of these techniques have over conventional mechanical characterisation techniques are that the measurement can be performed on cell-seeded hydrogels and under sterile conditions while allowing non-destructive, in-situ and real-time examination of the changes in mechanical properties. KEYWORDS: Hydrogel, Mechanical characterisation, Indentation, Viscoelastic, Optical coherence tomography. *Correspondence to: Tel.: +44 (0)1782 555227. Fax: +44 (0)1782 717079. E-mail address: [email protected]. -
System for the Application of Hydrostatic Pressure and Mechanical Strain to Cell Cultures Justin Bacaoat Clemson University, [email protected]
Clemson University TigerPrints All Theses Theses 12-2018 System for the Application of Hydrostatic Pressure and Mechanical Strain to Cell Cultures Justin Bacaoat Clemson University, [email protected] Follow this and additional works at: https://tigerprints.clemson.edu/all_theses Recommended Citation Bacaoat, Justin, "System for the Application of Hydrostatic Pressure and Mechanical Strain to Cell Cultures" (2018). All Theses. 2966. https://tigerprints.clemson.edu/all_theses/2966 This Thesis is brought to you for free and open access by the Theses at TigerPrints. It has been accepted for inclusion in All Theses by an authorized administrator of TigerPrints. For more information, please contact [email protected]. SYSTEM FOR THE APPLICATION OF HYDROSTATIC PRESSURE AND MECHANICAL STRAIN TO CELL CULTURES A Thesis Presented to the Graduate School of Clemson University In Partial Fulfillment of the Requirements for the Degree Master of Science Bioengineering by Justin Bacaoat December 2018 Accepted by: Jiro Nagatomi, PhD, Committee Chair William Richardson, PhD Ken Webb, PhD ABSTRACT Pressure and stretch are two of the primary forces that result in mechanotransductory events which regulate certain aspects of human health and disease. Laboratory systems such as the commercially available Flexercell® system and a variety of custom-made setups are currently used in research to systematically apply stretch and hydrostatic pressure independently, or in conjunction to cell and tissue cultures. However, these systems do not allow for the decoupling of pressure and stretch under the same culture conditions. The present study aims to design, fabricate, and calibrate a device that can apply pressure and stretch simultaneously, as well as independently to cells in culture. -
Identification of Strain Rate-Dependent Mechanical Behaviour of DP600 Under In-Plane Biaxial Loadings Wei Liu, Dominique Guines, Lionel Leotoing, Eric Ragneau
Identification of strain rate-dependent mechanical behaviour of DP600 under in-plane biaxial loadings Wei Liu, Dominique Guines, Lionel Leotoing, Eric Ragneau To cite this version: Wei Liu, Dominique Guines, Lionel Leotoing, Eric Ragneau. Identification of strain rate-dependent mechanical behaviour of DP600 under in-plane biaxial loadings. Materials Science and Engineering: A, Elsevier, 2016, 676, pp.366 - 376. 10.1016/j.msea.2016.08.125. hal-01394743 HAL Id: hal-01394743 https://hal.archives-ouvertes.fr/hal-01394743 Submitted on 9 Nov 2016 HAL is a multi-disciplinary open access L’archive ouverte pluridisciplinaire HAL, est archive for the deposit and dissemination of sci- destinée au dépôt et à la diffusion de documents entific research documents, whether they are pub- scientifiques de niveau recherche, publiés ou non, lished or not. The documents may come from émanant des établissements d’enseignement et de teaching and research institutions in France or recherche français ou étrangers, des laboratoires abroad, or from public or private research centers. publics ou privés. Identification of strain rate-dependent mechanical behaviour of DP600 under in-plane biaxial loadings Wei LIU(1), Dominique GUINES(2), Lionel LEOTOING(2), Eric RAGNEAU(2) Corresponding author : Dominique GUINES, [email protected] (1)School of Materials Science and Engineering, Wuhan University of Technology (WHUT), China (2)Université Européenne de Bretagne, INSA-LGCGM-EA 3913, 20 Av. des Buttes de Coësmes, CS 70839, 35708 Rennes Cedex 7, France Abstract: The rate-dependent hardening behaviour of dual phase DP600 steel sheet is investigated by means of in-plane biaxial tensile tests, in an intermediate strain rate range (up to 20s-1) and for large strains (up to 30% of equivalent plastic strain) at room temperature. -
Evaluation of Formability and Determination of Flow
EVALUATION OF FORMABILITY AND DETERMINATION OF FLOW STRESS CURVE OF SHEET MATERIALS WITH DOME TEST THESIS Presented in Partial Fulfillment of the Requirements for the Degree Master of Science in the Graduate School of The Ohio State University By Ji You Yoon Graduate Program in Mechanical Engineering The Ohio State University 2012 Master's Examination Committee: Taylan Altan, Advisor Jerald Brevick Copyright by Ji You Yoon 2012 Abstract Determination of flow stress curve of sheet material is important for designing stamping process efficiently. Entering accurate flow stress curve to FE simulations is necessary to obtain reliable results from simulations. Furthermore, in most Advanced High Strength Steels (AHSS), material properties may vary from coil to coil and that can affect to product quality. The dome test is a material test to evaluate formability and determine the flow stress curve of the sheet materials. The dome test is a biaxial test which consequently achieves greater maximum true strain without localized necking compared to that of uniaxial tensile test. As a result, the flow stress curve obtained from the dome test can be determined up to larger strains than in tensile test. This reduces possible errors from extrapolation of flow stress curve obtained from tensile test. FE simulations are performed in order to understand the deformation process in the dome test and to develop database for computer program, PRODOME, (MATLAB). With PRODOME, flow stress curve is calculated (determining K and n values in Hollomon’s Law (σ=Kεn)) by inputting dome test outputs of punch force vs. stroke. It is calculated by using inverse analysis method. -
Large-Strain Hyperelastic Constitutive Model of Envelope Material Under Biaxial Tension with Different Stress Ratios
materials Article Large-Strain Hyperelastic Constitutive Model of Envelope Material under Biaxial Tension with Different Stress Ratios Zhipeng Qu 1,*, Wei He 2,3, Mingyun Lv 1 and Houdi Xiao 1 1 School of Aeronautic Science and Engineering, Beihang University, Beijing 100191, China; [email protected] (M.L.); [email protected] (H.X.) 2 AVIC Special Vehicle Research Institute, Jingmen 448035, China; [email protected] 3 College of Aerospace Engineering, Nanjing University of Aeronautics and Astronautics, Nanjing 210016, China * Correspondence: [email protected]; Tel.: +86-010-82338116 Received: 13 August 2018; Accepted: 12 September 2018; Published: 19 September 2018 Abstract: This paper reports the biaxial tensile mechanical properties of the envelope material through experimental and constitutive models. First, the biaxial tensile failure tests of the envelope material with different stress ratio in warp and weft directions are carried out. Then, based on fiber-reinforced continuum mechanics theory, an anisotropic hyperelastic constitutive model on envelope material with different stress ratio is developed. A strain energy function that characterizes the anisotropic behavior of the envelope material is decomposed into three parts: fiber, matrix and fiber–fiber interaction. The fiber–matrix interaction is eliminated in this model. A new simple model for fiber–fiber interaction with different stress ratio is developed. Finally, the results show that the constitutive model has a good agreement with the experiment results. The results can be used to provide a reference for structural design of envelope material. Keywords: envelope material; biaxial tension; constitutive model; stress ratio 1. Introduction The stress of stratospheric airship envelope material usually comes from two or more directions in practical application; thus, it is necessary to test envelope material by biaxial or multiaxial tension. -
Characterization and Sensitivity Analysis of Hyperelastic Materials in Biaxial Tension Lowell Smoger
Rochester Institute of Technology RIT Scholar Works Theses Thesis/Dissertation Collections 10-8-2010 Characterization and sensitivity analysis of hyperelastic materials in biaxial tension Lowell Smoger Follow this and additional works at: http://scholarworks.rit.edu/theses Recommended Citation Smoger, Lowell, "Characterization and sensitivity analysis of hyperelastic materials in biaxial tension" (2010). Thesis. Rochester Institute of Technology. Accessed from This Thesis is brought to you for free and open access by the Thesis/Dissertation Collections at RIT Scholar Works. It has been accepted for inclusion in Theses by an authorized administrator of RIT Scholar Works. For more information, please contact [email protected]. CHARACTERIZATION AND SENSITIVITY ANALYSIS OF HYPERELASTIC MATERIALS IN BIAXIAL TENSION By Lowell M. Smoger Submitted in partial fulfillment of the requirement for the Master of Science In Mechanical Engineering Dr. Elizabeth DeBartolo _______________________ Department of Mechanical Engineering (Thesis Advisor) Dr. Risa J. Robinson _______________________ Department of Mechanical Engineering (Committee Member) Dr. Kathleen Lamkin-Kennard _______________________ Department of Mechanical Engineering (Committee Member) Dr. Mario Gomes _______________________ Department of Mechanical Engineering (Committee Member) Dr. Wayne Walter _______________________ Department of Mechanical Engineering (Department Representative) KATE GLEASON COLLEGE OF ENGINEERING ROCHESTER INSTITUTE OF TECHNOLOGY October 8th 2010 Permission -
A New Compressible Hyperelastic Model for the Multi-Axial Deformation of Blood Clot Occlusions in Vessels
A new compressible hyperelastic model for the multi-axial deformation of blood clot occlusions in vessels Behrooz Fereidoonnezhad1, Kevin M. Moerman1, Sarah Johnson2, Ray McCarthy2, Patrick J. McGarry1,* 1 Biomedical engineering, National university of Ireland Galway, Galway, Ireland 2 Cerenovus Galway Neuro-Technology Centre, Johnson & Johnson, Galway, Ireland Abstract Mechanical thrombectomy can be significantly affected by the mechanical properties of the occluding thrombus. In this study we provide the first characterization of the volumetric behaviour of blood clots. We propose a new hyperelastic model for the volumetric and isochoric deformation of clot. We demonstrate that the proposed model provides significant improvements over established models in terms of accurate prediction of nonlinear stress-strain and volumetric behaviours of clots with low and high red blood cell compositions. We perform a rigorous investigation of the factors that govern clot occlusion of a tapered vessel. The motivation for such an analysis is two-fold: (i) the role of clot composition on the in-vivo occlusion location is an open clinical question that has significant implications for thrombectomy procedures; (ii) in- vitro measurement of occlusion location in an engineered tapered tube can be used as a quick and simple methodology to assess the mechanical properties/compositions of clots. Simulations demonstrate that both isochoric and volumetric behaviour of clots are key determinants of clot lodgement location, in addition to clot-vessel friction. The proposed formulation is shown to provide accurate predictions of in-vitro measurement of clot occlusion location in a silicone tapered vessel, in addition to accurately predicting the deformed shape of the clot. -
Assessing Biaxial Strength Characteristics of Wood-Based Structural Panels
AN ABSTRACT OF THE THESIS OF PING CHENG for the degree of Master of Science in ForestProducts presented on May 8 1996. Title: Assessing Biaxial Strength Characteristicsof Wood-Based Structural Panels. A / Signature redacted for privacy. Abstract Approved: Dr. Robert J. Leichti Biaxial strength characteristics of wood-based structural panels wereevaluated by using analytical and experimental methods. Cruciformplywood specimens were tested under biaxial tensile-tensile, compressive-compressive loadingsin a symmetrically- jointed-arm test fixture, which was mounted on a universal testingmachine. Performance of the test fixture was also evaluated during the tests. Electricalresistance strain gauges were used to measure strain values at apoint of interest, and brittle coatings were also used to analyze strain distributions over the test section. Finite-elementanalysis was employed to develop an analytical tool. The basic configurations, detail alternatives,and the influence of reinforcement orientation on the uniformity of the biaxialstress/strain distributions in the test section of the cruciform specimen wereexamined by using the finite-element method. The experimental strain values and those fromfinite-element analysis were found in close agreement. The Tsai-Wu Tensor Polynomial Strength Theory was used to construct a predicted biaxial strength envelope in stress space. Comparisons were made between the experimental data and the theoretical predictions in quadrants I and III of stress space, as well as between the finite-element results and the theoretical predictions in quadrants II and IV of stress space. Good agreements were found in quadrants I, II and IV at a load value that corresponded with audible cracking. In quadrant III of stress space, compressive-compressive stress space, the experimental failure stress condition did not agree with the analytical solution for the strength theory envelope in that quadrant. -
Mechanical Considerations of Electrospun Scaffolds For
bioengineering Review Mechanical Considerations of Electrospun Scaffolds for Myocardial Tissue and Regenerative Engineering Michael Nguyen-Truong 1 , Yan Vivian Li 1,2,3 and Zhijie Wang 1,4,* 1 School of Biomedical Engineering, Colorado State University, Fort Collins, CO 80523, USA; [email protected] 2 Department of Design and Merchandising, Colorado State University, Fort Collins, CO 80523, USA 3 School of Advanced Materials Discovery, Colorado State University, Fort Collins, CO 80523, USA 4 Department of Mechanical Engineering, Colorado State University, Fort Collins, CO 80523, USA * Correspondence: [email protected]; Tel.: +1-(970)-491-8679 Received: 1 September 2020; Accepted: 1 October 2020; Published: 3 October 2020 Abstract: Biomaterials to facilitate the restoration of cardiac tissue is of emerging importance. While there are many aspects to consider in the design of biomaterials, mechanical properties can be of particular importance in this dynamically remodeling tissue. This review focuses on one specific processing method, electrospinning, that is employed to generate materials with a fibrous microstructure that can be combined with material properties to achieve the desired mechanical behavior. Current methods used to fabricate mechanically relevant micro-/nanofibrous scaffolds, in vivo studies using these scaffolds as therapeutics, and common techniques to characterize the mechanical properties of the scaffolds are covered. We also discuss the discrepancies in the reported elastic modulus for physiological and pathological myocardium in the literature, as well as the emerging area of in vitro mechanobiology studies to investigate the mechanical regulation in cardiac tissue engineering. Lastly, future perspectives and recommendations are offered in order to enhance the understanding of cardiac mechanobiology and foster therapeutic development in myocardial regenerative medicine. -
Design of an Octo-Strain Specimen for Biaxial Tension Testing
Proceedings of the ASME 2018 13th International Manufacturing Science and Engineering Conference MSEC2018 June 18-22, 2018, College Station, TX, USA MSEC2018-6612 Downloaded from https://asmedigitalcollection.asme.org/MSEC/proceedings-pdf/MSEC2018/51364/V002T04A028/2520052/v002t04a028-msec2018-6612.pdf by NIST user on 03 September 2019 DESIGN OF AN OCTO-STRAIN SPECIMEN FOR BIAXIAL TENSION TESTING Justin L. Milner and Thomas Gnäupel-Herold National Institute of Standards and Technology, NIST Center for Neutron Research Gaithersburg, MD, USA KEYWORDS INTRODUCTION Sheet metal, Biaxial testing, Cruciform specimen, Octo-Strain Biaxial testing is a method to determine material data that specimen, Digital image correlation can be used for finite element modeling by deforming sheet metal material under complex strain paths. These methods ABSTRACT include punch tests (e.g., Marciniak and Nakazima) [1-3], bulge A custom biaxial testing fixture was designed to evaluate a pressure tests [4-6], biaxial compression tests [7], and cruciform new specimen geometry for complex loading paths. Biaxial tests [8-10] to name a few. Each of these techniques has their testing is commonly used to evaluate work-hardening behavior advantages and disadvantages; such cons include the of sheet metal in biaxial tension to study the accumulation of introduction of bending stresses and friction during the test, plastic strains to determine the anisotropic yield loci. The current sample geometry issues, and measuring the stress-strain state-of-the-art specimen geometry that is used for biaxial testing relationship. Cruciform testing eliminates the issues associated is the cruciform specimen. Cruciform specimens are machined with the introduction of bending stresses and friction as it is an into a geometry that resembles a cross with four arms arranged in-plane testing technique. -
Investigation of the Forming Limit Strains at Fracture of AA5086 Sheets
Investigation of the forming limit strains at fracture of AA5086 sheets using an in-plane biaxial tensile test Xiao Song, Lionel Leotoing, Dominique Guines, Eric Ragneau To cite this version: Xiao Song, Lionel Leotoing, Dominique Guines, Eric Ragneau. Investigation of the forming limit strains at fracture of AA5086 sheets using an in-plane biaxial tensile test. Engineering Fracture Mechanics, Elsevier, 2016, 163, pp.130-140. 10.1016/j.engfracmech.2016.07.007. hal-01359364 HAL Id: hal-01359364 https://hal.archives-ouvertes.fr/hal-01359364 Submitted on 7 Sep 2016 HAL is a multi-disciplinary open access L’archive ouverte pluridisciplinaire HAL, est archive for the deposit and dissemination of sci- destinée au dépôt et à la diffusion de documents entific research documents, whether they are pub- scientifiques de niveau recherche, publiés ou non, lished or not. The documents may come from émanant des établissements d’enseignement et de teaching and research institutions in France or recherche français ou étrangers, des laboratoires abroad, or from public or private research centers. publics ou privés. Investigation of the forming limit strains at fracture of AA5086 sheets using an in-plane biaxial tensile test X. Songa, L. Leotoinga,∗, D. Guinesa, E. Ragneaua aUniversit´eEurop´eennede Bretagne, France, INSA-LGCGM-EA 3913, 20 Av. des Buttes de Co¨esmes,CS 70839, 35708 Rennes Cedex 7, France Abstract An in-plane biaxial tensile test with a dedicated cruciform specimen is per- formed to determine the forming limit strains at fracture for aluminium alloy 5086. A method based on the evolution of strain in the central area of the specimen and the observation of the macroscopic image of specimen surface is proposed to identify the onset of fracture and the forming limit strains at this moment.