A Numerical and Experimental Investigation of Flow Induced Noise
Total Page:16
File Type:pdf, Size:1020Kb
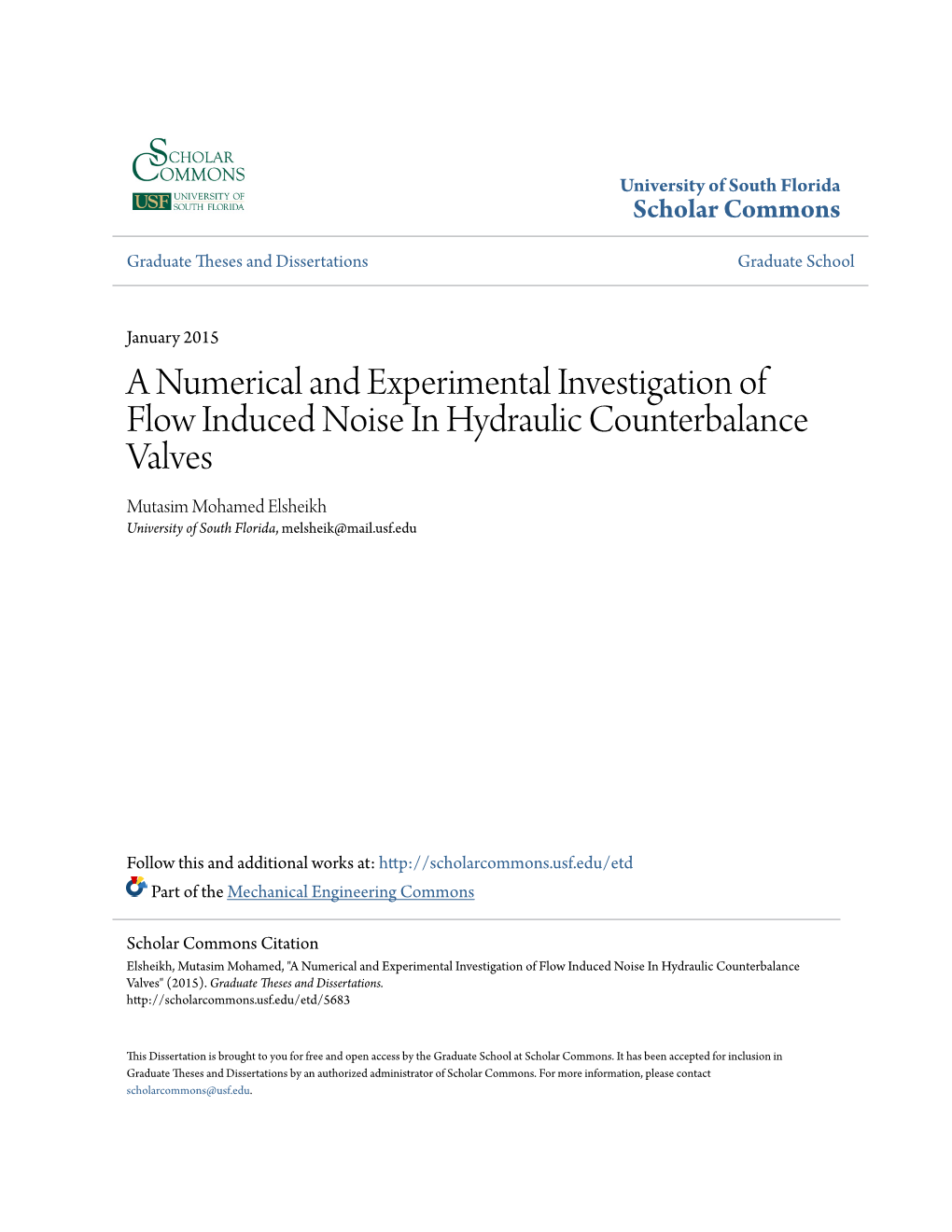
Load more
Recommended publications
-
Chapter 5 Dimensional Analysis and Similarity
Chapter 5 Dimensional Analysis and Similarity Motivation. In this chapter we discuss the planning, presentation, and interpretation of experimental data. We shall try to convince you that such data are best presented in dimensionless form. Experiments which might result in tables of output, or even mul- tiple volumes of tables, might be reduced to a single set of curves—or even a single curve—when suitably nondimensionalized. The technique for doing this is dimensional analysis. Chapter 3 presented gross control-volume balances of mass, momentum, and en- ergy which led to estimates of global parameters: mass flow, force, torque, total heat transfer. Chapter 4 presented infinitesimal balances which led to the basic partial dif- ferential equations of fluid flow and some particular solutions. These two chapters cov- ered analytical techniques, which are limited to fairly simple geometries and well- defined boundary conditions. Probably one-third of fluid-flow problems can be attacked in this analytical or theoretical manner. The other two-thirds of all fluid problems are too complex, both geometrically and physically, to be solved analytically. They must be tested by experiment. Their behav- ior is reported as experimental data. Such data are much more useful if they are ex- pressed in compact, economic form. Graphs are especially useful, since tabulated data cannot be absorbed, nor can the trends and rates of change be observed, by most en- gineering eyes. These are the motivations for dimensional analysis. The technique is traditional in fluid mechanics and is useful in all engineering and physical sciences, with notable uses also seen in the biological and social sciences. -
Cavitation Experimental Investigation of Cavitation Regimes in a Converging-Diverging Nozzle Willian Hogendoorn
Cavitation Experimental investigation of cavitation regimes in a converging-diverging nozzle Willian Hogendoorn Technische Universiteit Delft Draft Cavitation Experimental investigation of cavitation regimes in a converging-diverging nozzle by Willian Hogendoorn to obtain the degree of Master of Science at the Delft University of Technology, to be defended publicly on Wednesday May 3, 2017 at 14:00. Student number: 4223616 P&E report number: 2817 Project duration: September 6, 2016 – May 3, 2017 Thesis committee: Prof. dr. ir. C. Poelma, TU Delft, supervisor Prof. dr. ir. T. van Terwisga, MARIN Dr. R. Delfos, TU Delft MSc. S. Jahangir, TU Delft, daily supervisor An electronic version of this thesis is available at http://repository.tudelft.nl/. Contents Preface v Abstract vii Nomenclature ix 1 Introduction and outline 1 1.1 Introduction of main research themes . 1 1.2 Outline of report . 1 2 Literature study and theoretical background 3 2.1 Introduction to cavitation . 3 2.2 Relevant fluid parameters . 5 2.3 Current state of the art . 8 3 Experimental setup 13 3.1 Experimental apparatus . 13 3.2 Venturi. 15 3.3 Highspeed imaging . 16 3.4 Centrifugal pump . 17 4 Experimental procedure 19 4.1 Venturi calibration . 19 4.2 Camera settings . 21 4.3 Systematic data recording . 21 5 Data and data processing 23 5.1 Videodata . 23 5.2 LabView data . 28 6 Results and Discussion 29 6.1 Analysis of starting cloud cavitation shedding. 29 6.2 Flow blockage through cavity formation . 30 6.3 Cavity shedding frequency . 32 6.4 Cavitation dynamics . 34 6.5 Re-entrant jet dynamics . -
Article.Pdf (7.900Mb)
Journal of Wind Engineering & Industrial Aerodynamics 206 (2020) 104365 Contents lists available at ScienceDirect Journal of Wind Engineering & Industrial Aerodynamics journal homepage: www.elsevier.com/locate/jweia Aerodynamic forces on iced cylinder for dry ice accretion – A numerical study Pavlo Sokolov *, Muhammad Shakeel Virk Institute of Industrial Technology, University of Tromsø, The Arctic University of Norway, Norway ARTICLE INFO ABSTRACT Keywords: Within this paper the ISO 12494 assumption of standard of slowly rotating reference collector under ice accretion Atmospheric icing has been tested. This concept, introduced by (Makkonen, 1984), suggests that the power line cables, which are the Cylinder basis of the “reference collector” in the ISO framework, are slowly rotating under ice load, due to limited torsional CFD stiffness. For this purpose, several Computational Fluid Dynamics (CFD) simulations of the atmospheric ice ac- Numerical cretion and transient airflow conditions over iced cylinder at different angles of attack were performed. In order to Angle of attack fi Drag ascertain the similarity, several parameters were chosen, namely, drag, lift and moment coef cients, pressure and Lift viscous force. The results suggest that the benchmark cases of rotating and uniced cylinder have “similar” Transient aerodynamic loads when compared with the “averaged” results at different angles of attack (AoA), namely, the Comparison values of total pressure and viscous force. However, on individual and instantaneous basis the difference in the airflow regime between AoA cases and the benchmark cases can be noticeable. The results from the ice accretion simulation suggest that at long term the gravity force will be the dominating one, with rotating cylinder being a good approximation to the “averaged” angle of attack cases for the ice accretion. -
Flow Measurement Universitaet Erlangen-Nuember Reinhard Haak Universitaet Erlangen-Nuember 28.1 Differential Pressure Flowmeters Zaki D
Richard Thorn. "Flow." Copyright 2000 CRC Press LLC. <http://www.engnetbase.com>. Richard Thorn University of Derby Adrian Melling Universitaet Erlangen-Nuember Herbert Köchner Flow Measurement Universitaet Erlangen-Nuember Reinhard Haak Universitaet Erlangen-Nuember 28.1 Differential Pressure Flowmeters Zaki D. Husain Important Principles of Fluid Flow in Pipes • Bernoulli’s Daniel Flow Products, Inc. Equation • Common Differential Pressure Flowmeters • Donald J. Wass Other Differential Pressure Flowmeters • Performance and Applications • Installation • Differential Pressure Daniel Flow Products, Inc. Measurement • Standards • Future Developments David Wadlow 28.2 Variable Area Flowmeters Sensors Research Consulting, Inc. General Description of Variable Area Flowmeters • Measuring Principles of Variable Area Flowmeters Harold M. Miller 28.3 Positive Displacement Flowmeters Data Industrial Corporation Design and Construction • Some Commercially Available Halit Eren PD Meter Designs • Advantages and Disadvantages of PD Meters • Applications • Accessories • Price and Performance Curtin University of Technology 28.4 Turbine and Vane Flowmeters Hans-Peter Vaterlaus Axial Turbine Flowmeters • Insertion Axial Turbine Rittmeyer Ltd. Flowmeters • Angular Momentum Flowmeters • Multijet Turbine Flowmeters • Cylindrical Rotor Flowmeter • Thomas Hossle Manufacturers • Conclusion Rittmeyer Ltd. 28.5 Impeller Flowmeters Paolo Giordano Sensing Principles • Flow Ranges • Installation • Manufacturers Rittmeyer Ltd. 28.6 Electromagnetic Flowmeters Christophe -
Natural Convection Flow in a Vertical Tube Inspired by Time-Periodic Heating
Alexandria Engineering Journal (2016) xxx, xxx–xxx HOSTED BY Alexandria University Alexandria Engineering Journal www.elsevier.com/locate/aej www.sciencedirect.com ORIGINAL ARTICLE Natural convection flow in a vertical tube inspired by time-periodic heating Basant K. Jha, Michael O. Oni * Department of Mathematics, Ahmadu Bello University, Zaria, Nigeria Received 15 May 2016; revised 15 August 2016; accepted 25 August 2016 KEYWORDS Abstract This paper theoretically analyzes the flow formation and heat transfer characteristics of Natural convection; fully developed natural convection flow in a vertical tube due to time periodic heating of the surface Fully developed flow; of the tube. The mathematical model responsible for the present physical situation is presented Time-periodic heating; under relevant boundary conditions. The essential features of natural convection flow formation Vertical tube and associated heat transfer characteristics through the vertical tube are clearly highlighted by the variation in the dimensionless velocity, dimensionless temperature, skin-friction, mass flow rate and rate of heat transfer. Moreover, the effect of Prandtl number and Strouhal number on the momentum and thermal transport characteristics is discussed thoroughly. The study reveals that flow formation, rate of heat transfer and mass flow rate are appreciably influenced by Prandtl num- ber and Strouhal number. Ó 2016 Faculty of Engineering, Alexandria University. Production and hosting by Elsevier B.V. This is an open access article under the CC BY-NC-ND license (http://creativecommons.org/licenses/by-nc-nd/4.0/). 1. Introduction difference approach. From miniaturization of electrical and electronic panels, Bar-Cohen and Rohsenow [3] analyzed fully In the course of modeling a real life situation of fluid flow, developed natural convection between two periodically heated periodic heat input in a channel has captured the attention parallel plates. -
Stability and Instability of Hydromagnetic Taylor-Couette Flows
Physics reports Physics reports (2018) 1–110 DRAFT Stability and instability of hydromagnetic Taylor-Couette flows Gunther¨ Rudiger¨ a;∗, Marcus Gellerta, Rainer Hollerbachb, Manfred Schultza, Frank Stefanic aLeibniz-Institut f¨urAstrophysik Potsdam (AIP), An der Sternwarte 16, D-14482 Potsdam, Germany bDepartment of Applied Mathematics, University of Leeds, Leeds, LS2 9JT, United Kingdom cHelmholtz-Zentrum Dresden-Rossendorf, Bautzner Landstr. 400, D-01328 Dresden, Germany Abstract Decades ago S. Lundquist, S. Chandrasekhar, P. H. Roberts and R. J. Tayler first posed questions about the stability of Taylor- Couette flows of conducting material under the influence of large-scale magnetic fields. These and many new questions can now be answered numerically where the nonlinear simulations even provide the instability-induced values of several transport coefficients. The cylindrical containers are axially unbounded and penetrated by magnetic background fields with axial and/or azimuthal components. The influence of the magnetic Prandtl number Pm on the onset of the instabilities is shown to be substantial. The potential flow subject to axial fieldspbecomes unstable against axisymmetric perturbations for a certain supercritical value of the averaged Reynolds number Rm = Re · Rm (with Re the Reynolds number of rotation, Rm its magnetic Reynolds number). Rotation profiles as flat as the quasi-Keplerian rotation law scale similarly but only for Pm 1 while for Pm 1 the instability instead sets in for supercritical Rm at an optimal value of the magnetic field. Among the considered instabilities of azimuthal fields, those of the Chandrasekhar-type, where the background field and the background flow have identical radial profiles, are particularly interesting. -
Investigation of Fouling Mechanisms to Guide the Design of Diesel Engine
INVESTIGATION OF FOULING MECHANISMS TO GUIDE THE DESIGN OF DIESEL ENGINE EXHAUST DRIVEN ABSORPTION HEAT PUMPS A Thesis Presented to The Academic Faculty by Victor C. Aiello In Partial Fulfillment of the Requirements for the Degree Master of Science in the School of Mechanical Engineering Georgia Institute of Technology December 2016 COPYRIGHT © 2016 BY VICTOR AIELLO INVESTIGATION OF FOULING MECHANISMS TO GUIDE THE DESIGN OF DIESEL ENGINE EXHAUST DRIVEN ABSORPTION HEAT PUMPS Approved by: Dr. Srinivas Garimella, Advisor School of Mechanical Engineering Georgia Institute of Technology Dr. William J. Wepfer School of Mechanical Engineering Georgia Institute of Technology Dr. Peter Loutzenhiser School of Mechanical Engineering Georgia Institute of Technology Date Approved: November 21, 2016 ACKNOWLEDGEMENTS I would first like to thank my advisor, Dr. Srinivas Garimella, for providing the opportunity to work on an intriguing and challenging research project. I am grateful for being given a balance of direction and autonomy that has allowed for an invaluable learning experience. I would also like to thank the members of the Sustainable Thermal Systems Lab for their unique willingness to provide technical guidance and support. I would particularly like to thank Marcel Staedter for his mentorship and Girish Kini for his incredible dedication to this research project. It has been an honor to work with and learn from such an inspiring and hard working group of people. Lastly, I would like to thank my family, for this accomplishment would not have been possible without their unwavering support. iii TABLE OF CONTENTS ACKNOWLEDGEMENTS iii LIST OF TABLES vii LIST OF FIGURES x LIST OF SYMBOLS AND ABBREVIATIONS xvii SUMMARY xx CHAPTER 1. -
An Overview of Modeling and Experiments of Vortex-Induced Vibration of Circular Cylinders
ARTICLE IN PRESS JOURNAL OF SOUND AND VIBRATION Journal of Sound and Vibration 282 (2005) 575–616 www.elsevier.com/locate/jsvi Review An overview of modeling and experiments of vortex-induced vibration of circular cylinders R.D. Gabbai, H. Benaroyaà Department of Mechanical and Aerospace Engineering, Rutgers University, Piscataway, NJ 08854-8058, USA Received 9 October 2003; accepted 13 April 2004 Available online 11 November 2004 Abstract This paper reviews the literature on the mathematical models used to investigate vortex-induced vibration (VIV) of circular cylinders. Wake-oscillator models, single-degree-of-freedom, force–decomposi- tion models, and other approaches are discussed in detail. Brief overviews are also given of numerical methods used in solving the fully coupled fluid–structure interaction problem and of key experimental studies highlighting the nature of VIV. r 2004 Elsevier Ltd. All rights reserved. Contents 1. Introduction . 576 2. Experimental studies . 578 2.1. Fluid forces on an oscillating cylinder . 580 2.2. Three-dimensionality and free-surface effects . 581 2.3. Vortex-shedding modes and synchronization regions . 583 2.4. The frequency dependence of the added mass . 584 2.5. Dynamics of cylinders with low mass damping . 587 3. Semi-empirical models . 590 3.1. Wake–oscillator models . 590 ÃCorresponding author. Tel.: +1-732-445-4408. E-mail address: [email protected] (H. Benaroya). 0022-460X/$ - see front matter r 2004 Elsevier Ltd. All rights reserved. doi:10.1016/j.jsv.2004.04.017 ARTICLE IN PRESS 576 R.D. Gabbai, H. Benaroya / Journal of Sound and Vibration 282 (2005) 575–616 3.1.1. -
Numerical Simulation of the Wind Action on a Long-Span Bridge Deck V = W (I = 1, 2) on the Solid Boundary à (3) N+ 1 I I Vs 2 4) Calculate Vi With
A. L. Braun and A. M. Awruch Numerical Simulation of the Wind A. L. Braun Action on a Long-Span Bridge Deck PPGEC/UFRGS A numerical model to study the aerodynamic and aeroelastic bridge deck behavior is Av. Osvaldo Aranha, 99 – 3o andar presented in this paper. The flow around a rigid fixed bridge cross-section, as well as the 90035-190 Porto Alegre, RS. Brazil flow around the same cross-section with torsional motion, are investigated to obtain the www.cpgec.ufrgs.br aerodynamic coefficients, the Strouhal number and to determine the critical wind speed [email protected] originating dynamic instability due to flutter. The two-dimensional flow is analyzed employing the pseudo-compressibility approach, with an Arbitrary Lagrangean-Eulerian (ALE) formulation and an explicit two-step Taylor-Galerkin method. The finite element method (FEM) is used for spatial discretization. The structure is considered as a rigid A. M. Awruch body with elastic restrains for the cross-section rotation and displacement components. PPGEC/UFRGS & PROMEC/UFRGS The fluid-structure interaction is accomplished applying the compatibility and equilibrium Av. Sarmento Leite, 425 conditions at the fluid-solid interface. The structural dynamic analysis is performed using 90050-170 Porto Alegre, RS. Brazil the classical Newmark’s method. www.mecanica.ufrgs.br/promec Keywords: Fluid-structure interaction, Finite Element Method (FEM), Large Eddy [email protected] Simulation (LES), aeroelasticity, aerodynamics explicit two-step Taylor-Galerkin method with an Arbitrary Introduction Lagrangean-Eulerian (ALE) description. A similar Taylor-Galerkin formulation was used by Tabarrok & Su (1994) and by Rossa & Wind tunnel tests for assessment of aerodynamic and aeroelastic Awruch (2001), but with a semi-implicit scheme. -
Dimensional Analysis and Modeling
cen72367_ch07.qxd 10/29/04 2:27 PM Page 269 CHAPTER DIMENSIONAL ANALYSIS 7 AND MODELING n this chapter, we first review the concepts of dimensions and units. We then review the fundamental principle of dimensional homogeneity, and OBJECTIVES Ishow how it is applied to equations in order to nondimensionalize them When you finish reading this chapter, you and to identify dimensionless groups. We discuss the concept of similarity should be able to between a model and a prototype. We also describe a powerful tool for engi- ■ Develop a better understanding neers and scientists called dimensional analysis, in which the combination of dimensions, units, and of dimensional variables, nondimensional variables, and dimensional con- dimensional homogeneity of equations stants into nondimensional parameters reduces the number of necessary ■ Understand the numerous independent parameters in a problem. We present a step-by-step method for benefits of dimensional analysis obtaining these nondimensional parameters, called the method of repeating ■ Know how to use the method of variables, which is based solely on the dimensions of the variables and con- repeating variables to identify stants. Finally, we apply this technique to several practical problems to illus- nondimensional parameters trate both its utility and its limitations. ■ Understand the concept of dynamic similarity and how to apply it to experimental modeling 269 cen72367_ch07.qxd 10/29/04 2:27 PM Page 270 270 FLUID MECHANICS Length 7–1 ■ DIMENSIONS AND UNITS 3.2 cm A dimension is a measure of a physical quantity (without numerical val- ues), while a unit is a way to assign a number to that dimension. -
Local Models of Stellar Convection
A&A 448, 433–438 (2006) Astronomy DOI: 10.1051/0004-6361:20042245 & c ESO 2006 Astrophysics Local models of stellar convection III. The Strouhal number P. J. Käpylä 1,2,M.J.Korpi3, M. Ossendrijver2, and I. Tuominen1,3 1 Astronomy Division, Department of Physical Sciences, PO Box 3000, 90014 University of Oulu, Finland e-mail: [email protected] 2 Kiepenheuer-Institut für Sonnenphysik, Schöneckstrasse 6, 79104 Freiburg, Germany 3 Observatory, PO Box 14, 00014 University of Helsinki, Finland Received 25 October 2004 / Accepted 9 November 2005 ABSTRACT Aims. The Strouhal number (St), which is a nondimensional measure of the correlation time, is determined from numerical models of convection. The Strouhal number arises in the mean-field theories of angular momentum transport and magnetic field generation, where its value determines the validity of certain widely used approximations, such as the first order smoothing (hereafter FOSA). More specifically, the relevant transport coefficients can be calculated by means of a cumulative series expansion if St < Stcrit ≈ 1. Methods. We define the Strouhal number as the ratio of the correlation and turnover times, which we determine separately, the former from the autocorrelation of velocity, and the latter by following test particles embedded in the flow. Results. We find that the Strouhal numbers are, generally, of the order of 0.1 to 0.4 which is close to the critical value above which deviations from FOSA become significant. Increasing the rotational influence tends to shorten both timescales in such a manner that St decreases. However, we do not find a clear trend as a function of the Rayleigh number for the parameter range explored in the present study. -
1. Introduction
THE ASTROPHYSICAL JOURNAL, 549:1212È1220, 2001 March 10 ( 2001. The American Astronomical Society. All rights reserved. Printed in U.S.A. THE ZIGZAG PATH OF BUOYANT MAGNETIC TUBES AND THE GENERATION OF VORTICITY ALONG THEIR PERIPHERY T. EMONET1 High Altitude Observatory, National Center for Atmospheric Research, Boulder, CO 80307-3000; emonet=hao.ucar.edu F. MORENO-INSERTIS2 Instituto deAstrof• sica de Canarias, E38200 La Laguna, Spain; fmi=ll.iac.es AND M. P. RAST High Altitude Observatory, National Center for Atmospheric Research, Boulder, CO 80307-3000; mprast=hao.ucar.edu Received 1999 September 10; accepted 2000 October 20 ABSTRACT We study the generation of vorticity in the magnetic boundary layer of buoyant magnetic tubes and its consequences for the trajectory of magnetic structures rising in the solar convection zone. When the Reynolds number is well above 1, the wake trailing the tube sheds vortex rolls, producing a von Ka rma n vortex street, similar to the case of Ñows around rigid cylinders. The shedding of a vortex roll causes an imbalance of vorticity in the tube. The ensuing vortex force excites a transverse oscillation of the Ñux tube as a whole so that it follows a zigzag upward path instead of rising along a straight vertical line. In this paper, the physics of vorticity generation in the boundary layer is discussed and scaling laws for the relevant terms are presented. We then solve the two-dimensional magnetohydrodynamic equations numerically, measure the vorticity production, and show the formation of a vortex street and the conse- quent sinusoidal path of the magnetic Ñux tube.