Ni43-101Feasibility Study Technical Report on the Curraghinalt Gold
Total Page:16
File Type:pdf, Size:1020Kb
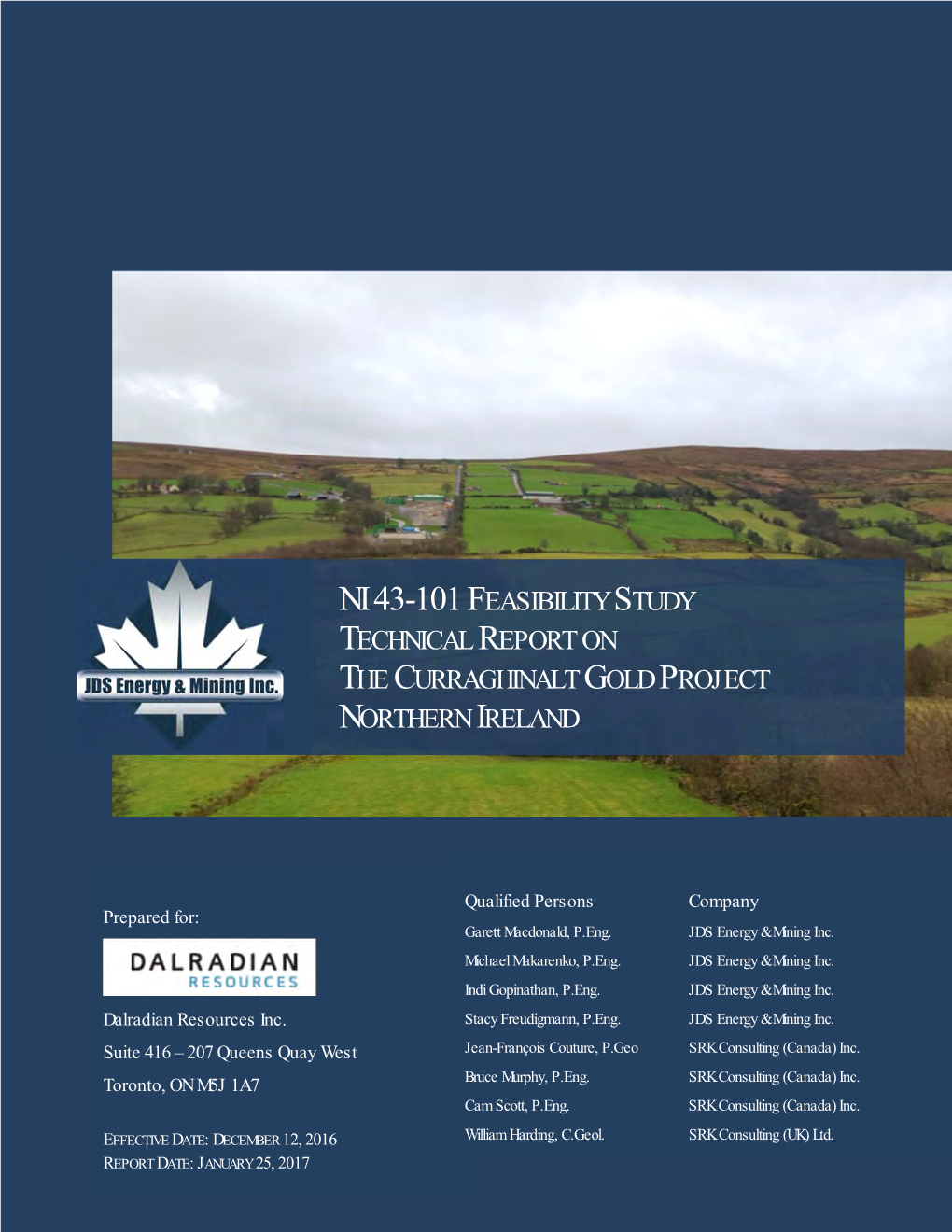
Load more
Recommended publications
-
Significance of Mineralogy in the Development of Flowsheets for Processing Uranium Ores
JfipwK LEACHING TIME REAGENTS TEMPERATURE FLOCCULANT CLARITY AREA COUNTER CURRENT DECANTATION It 21 21 J^^LJt TECHNICAL REPORTS SERIES No.19 6 Significance of Mineralogy in the Development of Flowsheets for Processing Uranium Ores \W# INTERNATIONAL ATOMIC ENERGY AGENCY, VIENNA, 1980 SIGNIFICANCE OF MINERALOGY IN THE DEVELOPMENT OF FLOWSHEETS FOR PROCESSING URANIUM ORES The following States are Members of the International Atomic Energy Agency: AFGHANISTAN HOLY SEE PHILIPPINES ALBANIA HUNGARY POLAND ALGERIA ICELAND PORTUGAL ARGENTINA INDIA QATAR AUSTRALIA INDONESIA ROMANIA AUSTRIA IRAN SAUDI ARABIA BANGLADESH IRAQ SENEGAL BELGIUM IRELAND SIERRA LEONE BOLIVIA ISRAEL SINGAPORE BRAZIL ITALY SOUTH AFRICA BULGARIA IVORY COAST SPAIN BURMA JAMAICA SRI LANKA BYELORUSSIAN SOVIET JAPAN SUDAN SOCIALIST REPUBLIC JORDAN SWEDEN CANADA KENYA SWITZERLAND CHILE KOREA, REPUBLIC OF SYRIAN ARAB REPUBLIC COLOMBIA KUWAIT THAILAND COSTA RICA LEBANON TUNISIA CUBA LIBERIA TURKEY CYPRUS LIBYAN ARAB JAMAHIRIYA UGANDA CZECHOSLOVAKIA LIECHTENSTEIN UKRAINIAN SOVIET SOCIALIST DEMOCRATIC KAMPUCHEA LUXEMBOURG REPUBLIC DEMOCRATIC PEOPLE'S MADAGASCAR UNION OF SOVIET SOCIALIST REPUBLIC OF KOREA MALAYSIA REPUBLICS DENMARK MALI UNITED ARAB EMIRATES DOMINICAN REPUBLIC MAURITIUS UNITED KINGDOM OF GREAT ECUADOR MEXICO BRITAIN AND NORTHERN EGYPT MONACO IRELAND EL SALVADOR MONGOLIA UNITED REPUBLIC OF ETHIOPIA MOROCCO CAMEROON FINLAND NETHERLANDS UNITED REPUBLIC OF FRANCE NEW ZEALAND TANZANIA GABON NICARAGUA UNITED STATES OF AMERICA GERMAN DEMOCRATIC REPUBLIC NIGER URUGUAY GERMANY, FEDERAL REPUBLIC OF NIGERIA VENEZUELA GHANA NORWAY VIET NAM GREECE PAKISTAN YUGOSLAVIA GUATEMALA PANAMA ZAIRE HAITI PARAGUAY ZAMBIA PERU The Agency's Statute was approved on 23 October 1956 by the Conference on the Statute of the IAEA held at United Nations Headquarters, New York; it entered into force on 29 July 1957. -
Curbing Illicit Mercury and Gold Flows in West Africa: Options for a Regional Approach
Curbing Illicit Mercury and Gold Flows in West Africa: Options for a Regional Approach i INCLUSIVE AND SUSTAINABLE INDUSTRIAL DEVELOPMENT ii Curbing Illicit Mercury and Gold Flows in West Africa: Options for a Regional Approach iii November 2018 iv © UNIDO 2018. All rights reserved. This document has been produced without formal United Nations editing. The designations employed and the presentation of the material in this document do not imply the expression of any opinion whatsoever on the part of the Secretariat of the United Nations Industrial Development Organization (UNIDO) concerning the legal status of any country, territory, city or area or of its authorities, or concerning the delimitation of its frontiers or boundaries, or its economic system or degree of development. Designations such as ‘developed’, ‘industrialized’ or ‘developing’ are intended for statistical convenience and do not necessarily express a judgement about the stage reached by a particular country or area in the development process. Mention of firm names or commercial products does not constitute an endorsement by UNIDO. Unless otherwise men- tioned, all references to sums of money are given in United States dollars. References to ‘tons’ are to metric tons, unless otherwise stated. All photos © UNIDO unless otherwise stated. Cover photo by Sadibou Sylla Acknowledgements This report was authored by Marcena Hunter of the Global Initiative Against Transnational Organized Crime. The report is part of the United Nations Industrial Development Organization (UNIDO) project, funded by the Government of Switzerland, to assist the Economic Community of West African States (ECOWAS) in its early implementation of the Minamata Convention. More information about the Minamata Convention and UNIDO’s work can be found on UNIDO’s website <https://www.unido.org/mercury> or by emailing Gabriela Eigenmann at [email protected]. -
S Ndlovu (PDF)
Extraction of Gold Then, Now and the Future Prof Sehliselo Ndlovu DST/NRF SARChI: Hydrometallurgy and Sustainable Development University of the Witwatersrand, Johannesburg Building a Robust Minerals Industry 3 – 4 July 2017, Cresta Lodge, Harare University of the Witwatersrand Johannesburg Founded Oct. 1896: School of Mines Approx. 37 000 Students 5 Faculties, 33 Schools, 3610 Courses >160 000 Degrees Conferred since 1922 55% Female Students 10 National Centres of Excellence Home to the Bidvest Football Club( Current PSL league Champions) Evolution in Gold Processing Past Technologies • Amalgamation • Panning Current Technologies • Cyanide leaching • Processing of Emerging and Future refractory ores Technologies • Bio-oxidation • Ionic liquids • Alternative leaching • Ultrasonic leaching reagents • Corn starch?? Past Technologies Used in Ancient Times History of gold extends back at least 6,000 years. Egypt and Mesopotamia around 4000 BC. Gravity Separation: Gold Panning Gold concentrated by washing lighter river sands with water Leaves dense gold particles Alternative- wash gold-bearing sand and gravel over a woollen fleece Traps heavier gold dust that would sink into the wool fibres. Advantages • Simplicity Disadvantages • Labour intensive Gravity Separation: Sluicing • Water is channelled to flow through a sluice-box. • Sluice-box is essentially a man-made channel with riffles (barriers) at the bottom. • Riffles create dead-zones in the water current which allows gold to drop out of suspension. Sluicing and panning results in the direct recovery of small gold nuggets and flakes. Gold Parting: Salt Cementation Process • Invented to remove Ag from Au-Ag mixtures around 6th century BC. Mix: argentiferous gold foil, common salt, brick dust or burnt clay and urine in a sealed container. -
Recovery of Gold and Iron from Cyanide Tailings with a Combined Direct Reduction Roasting and Leaching Process
metals Article Recovery of Gold and Iron from Cyanide Tailings with a Combined Direct Reduction Roasting and Leaching Process Pingfeng Fu 1,2,* ID , Zhenyu Li 1, Jie Feng 1 and Zhenzhong Bian 1 1 School of Civil and Resources Engineering, University of Science and Technology Beijing, Beijing 100083, China; [email protected] (Z.L.); [email protected] (J.F.); [email protected] (Z.B.) 2 Key Laboratory of High-Efficient Mining and Safety of Metal Mines, Ministry of Education, Beijing 100083, China * Correspondence: [email protected]; Tel.: +86-10-6233-2902 Received: 25 June 2018; Accepted: 19 July 2018; Published: 21 July 2018 Abstract: Cyanide tailings are the hazardous waste discharged after gold cyanidation leaching. The recovery of gold and iron from cyanide tailings was investigated with a combined direct reduction roasting and leaching process. The effects of reduction temperature, coal dosage and CaO dosage on gold enrichment into Au-Fe alloy (FexAu1−x) were studied in direct reduction roasting. Gold containing iron powders, i.e., Au-Fe alloy, had the gold grade of 8.23 g/t with a recovery of 97.46%. After separating gold and iron in iron powders with sulfuric acid leaching, ferrous sulfate in the leachate was crystallized to prepare FeSO4·7H2O with a yield of 222.42% to cyanide tailings. Gold enriched in acid-leaching residue with gold grade of 216.58 g/t was extracted into pregnant solution. The total gold recovery of the whole process reached as high as 94.23%. The tailings generated in the magnetic separation of roasted products, with a yield of 51.33% to cyanide tailings, had no toxic cyanide any more. -
Sion Mills to South of Omagh 113 2.4 Section 3 – South of Omagh to Aughnacloy 146
Commission Reference: 2015/D003-D006 PUBLIC INQUIRY REPORT A5 WESTERN TRANSPORT CORRIDOR ROAD SCHEME NEWBUILDINGS TO AUGHNACLOY Report by Commissioners A Beggs, D Hannon and D O’Neill Date of Report: 24 May 2017 Commission Reference: 2015/D003-D006 This page is left intentionally blank Contents Commission Reference: 2015/D003-D006 CONTENTS Page Acknowledgements iii Plan Showing the Proposed Scheme’s Sections & Phases iv Alphabetical Index of Site Specific Objections v Background to the Report 1 Part 1: General and Strategic Issues 7 1.1 The Proposed Scheme 7 1.2 Policy Context 9 1.3 Justification for the Scheme 13 1.4 Alternatives to an Offline Dual Carriageway 23 1.5 Scheme Phasing 28 1.6 Alternative Major Offline Dual Carriageway Alignments, Linkage 33 with the A4, Extent of the Scheme at New Buildings, Junction & Bridge Design 1.7 The Environmental Assessment – General Matters 38 1.8 Air Quality, Emissions & Climate Change 43 1.9 Cultural Heritage 47 1.10 Landscape 51 1.11 Ecology & Nature Conservation 55 1.12 Geology & Soils 66 1.13 Noise and Vibration 68 1.14 Effects on Travellers 70 1.15 Community and Private Assets (Including Agriculture) 71 1.16 Road Drainage & the Water Environment 74 1.17 Interactions & Cumulative Effects 79 1.18 Consultation on the Scheme 80 1.19 Conclusion on the Environmental Statement and the Impacts of 82 the Proposed Scheme i Contents Commission Reference: 2015/D003-D006 CONTENTS continued Page Part 2: Site Specific Representations 2.1 Introduction 83 2.2 Section 1 – New Buildings to Sion Mills 84 2.3 Section 2 – Sion Mills to South of Omagh 113 2.4 Section 3 – South of Omagh to Aughnacloy 146 Part 3: Conclusions 3.1 Conclusions and Recommendations on the Orders 179 Appendices Appendix 1: Acronyms & Abbreviations Used in Report 181 Appendix 2: Core Departmental Documents Before the Inquiry 183 ii Acknowledgements Commission Reference: 2015/D003-D006 Acknowledgements We wish to thank the Programme Officers, Mr Christopher McCarron and Mr Stephen Andrews, for their professionalism and hard work before, during and after the inquiry. -
Counterguerrilla Operation
FM 90-8 counterguerrilla operation/ AUGUST 1986 This publication contains technical or operational information that is for official government use only. Distribution is limited to US Government agencies Requests from outside the US Government for release of this publication under the Freedom of Information Act or the Foreign Military Sales Program must be made to: HO TR ADOC, Fort Monroe, VA 23651 ... HEADQUARTERS, DEPARTMENT OF THE ARMY DISTRIBUTION RESTRICTION- Approved for public release; distribution is unlimited. FM 90-8 CHAPTER 6. COMBAT SUPPORT Section I. General ............................................ 6-1 II. Reconnaissance and Surveillance Units ............. 6-2 Ill. Fire Support Units ................................. 6-7 CHAPTER 7. COMBAT SERVICE SUPPORT Section I. General ............................................ 7-1 II. Bases ............................................. 7-1 Ill. Use of Assets ...................................... 7-3 APPENDIX A. SUBSURFACE OPERATIONS Section I. General ............................................ A-1 II. Tunneling .......................................... A-2 Ill. Destroying Underground Facilities ................. A-12 APPENDIX B. THE URBAN GUERRILLA Section I. General ............................................ B-1 II. Techniques to Counter the Urban Guerrilla .......... B-2 APPENDIX C. AMBUSH PATROLS Section I. General ............................................ C-1 II. Attack Fundamentals .............................. C-2 Ill. Planning .......................................... -
Barite (Barium)
Barite (Barium) Chapter D of Critical Mineral Resources of the United States—Economic and Environmental Geology and Prospects for Future Supply Professional Paper 1802–D U.S. Department of the Interior U.S. Geological Survey Periodic Table of Elements 1A 8A 1 2 hydrogen helium 1.008 2A 3A 4A 5A 6A 7A 4.003 3 4 5 6 7 8 9 10 lithium beryllium boron carbon nitrogen oxygen fluorine neon 6.94 9.012 10.81 12.01 14.01 16.00 19.00 20.18 11 12 13 14 15 16 17 18 sodium magnesium aluminum silicon phosphorus sulfur chlorine argon 22.99 24.31 3B 4B 5B 6B 7B 8B 11B 12B 26.98 28.09 30.97 32.06 35.45 39.95 19 20 21 22 23 24 25 26 27 28 29 30 31 32 33 34 35 36 potassium calcium scandium titanium vanadium chromium manganese iron cobalt nickel copper zinc gallium germanium arsenic selenium bromine krypton 39.10 40.08 44.96 47.88 50.94 52.00 54.94 55.85 58.93 58.69 63.55 65.39 69.72 72.64 74.92 78.96 79.90 83.79 37 38 39 40 41 42 43 44 45 46 47 48 49 50 51 52 53 54 rubidium strontium yttrium zirconium niobium molybdenum technetium ruthenium rhodium palladium silver cadmium indium tin antimony tellurium iodine xenon 85.47 87.62 88.91 91.22 92.91 95.96 (98) 101.1 102.9 106.4 107.9 112.4 114.8 118.7 121.8 127.6 126.9 131.3 55 56 72 73 74 75 76 77 78 79 80 81 82 83 84 85 86 cesium barium hafnium tantalum tungsten rhenium osmium iridium platinum gold mercury thallium lead bismuth polonium astatine radon 132.9 137.3 178.5 180.9 183.9 186.2 190.2 192.2 195.1 197.0 200.5 204.4 207.2 209.0 (209) (210)(222) 87 88 104 105 106 107 108 109 110 111 112 113 114 115 116 -
Session 151 2008 – 09
PROCEEDINGS OF THE GEOLOGICAL SOCIETY OF GLASGOW Session 151 2008 – 09 1 SESSION 151 (2008 – 2009) Members of Council 2 Reports President 3 Membership 4 Library 4 Scottish Journal of Geology 5 Website 6 Publications 7 Strathclyde RIGS Group 7 Proceedings 10 Treasurer 10 Meetings Secretary’s report 13 Lectures 14 Members’ Night 18 Excursions Secretaries’ Reports 19 Spireslack and Garpel Burn, 25 April 20 Rouken Glen, 7 May 23 Bathgate Hills, 16 May 24 Highland Border Slate Quarries, 6 June 26 Ballantrae – Metamorphics, 11 July 28 Isle of Bute, east coast, 15 Aug 32 Isle of Gigha, 18 – 21 Sept 34 General Information 40 Intimations 40 2 SESSION 151 (2008– 2009) Members of Council President Dr Alan W. Owen Vice Presidents Dr Chris J. Burton Mr Mervyn H. Aiken vacancy Honorary Secretary Dr Iain Allison Treasurer Mr Michael J. Pell Membership Secretary Dr Robin A. Painter Minutes Secretary Mrs Margaret L. Greene Meetings Secretary Dr Jim Morrison Publications Miss Muriel Alexander Librarian Dr Chris J. Burton Asst Librarian & Hon Archivist Mrs Seonaid Leishman Proceedings Editor Miss Margaret Donnelly Publicity Dr Neil D.L.Clark (web) Dr R. A. Painter (meetings etc) Excursion Secretaries Mr Jim Martin (Saturdays) Mr David McCulloch (Residential) Strathclyde RIGS Chairperson Mr Stuart Fairley Rockwatch Representative Ms Katerina Braun Junior Member Mr. Robert Jamieson Journal Editors Dr Colin J.R. Braithwaite Dr Brian Bell Ordinary Members Mrs Barbara Balfour Dr Simon Cuthbert Dr Tim Dempster Mr Charles M. Leslie Mr Robert McNicol Mrs Margaret Rollo Independent Examiner Mrs Beth Diamond 3 PRESIDENT Membership of the Society has shown an encouraging rise to 390, reversing the trend of recent years. -
The Dalradian Rocks of the North-East Grampian Highlands of Scotland
Revised Manuscript 8/7/12 Click here to view linked References 1 2 3 4 5 The Dalradian rocks of the north-east Grampian 6 7 Highlands of Scotland 8 9 D. Stephenson, J.R. Mendum, D.J. Fettes, C.G. Smith, D. Gould, 10 11 P.W.G. Tanner and R.A. Smith 12 13 * David Stephenson British Geological Survey, Murchison House, 14 West Mains Road, Edinburgh EH9 3LA. 15 [email protected] 16 0131 650 0323 17 John R. Mendum British Geological Survey, Murchison House, West 18 Mains Road, Edinburgh EH9 3LA. 19 Douglas J. Fettes British Geological Survey, Murchison House, West 20 Mains Road, Edinburgh EH9 3LA. 21 C. Graham Smith Border Geo-Science, 1 Caplaw Way, Penicuik, 22 Midlothian EH26 9JE; formerly British Geological Survey, Edinburgh. 23 David Gould formerly British Geological Survey, Edinburgh. 24 P.W. Geoff Tanner Department of Geographical and Earth Sciences, 25 University of Glasgow, Gregory Building, Lilybank Gardens, Glasgow 26 27 G12 8QQ. 28 Richard A. Smith formerly British Geological Survey, Edinburgh. 29 30 * Corresponding author 31 32 Keywords: 33 Geological Conservation Review 34 North-east Grampian Highlands 35 Dalradian Supergroup 36 Lithostratigraphy 37 Structural geology 38 Metamorphism 39 40 41 ABSTRACT 42 43 The North-east Grampian Highlands, as described here, are bounded 44 to the north-west by the Grampian Group outcrop of the Northern 45 Grampian Highlands and to the south by the Southern Highland Group 46 outcrop in the Highland Border region. The Dalradian succession 47 therefore encompasses the whole of the Appin and Argyll groups, but 48 also includes an extensive outlier of Southern Highland Group 49 strata in the north of the region. -
Petrography of Metalimestones and Metadolostones from the Dalradian of Northern Ireland Natural Environment Research Council
Petrography of metalimestones and metadolostones from the Dalradian of Northern Ireland Natural Environment Research Council British Geological Survey Onshore Geology Series TECHNICAL REPORT WA/00/72 Petrography of metalimestones and metadolostones from the Argyll and Southern Highland groups, Dalradian, Northern Ireland Christopher W Thomas December 2000 Contributors: M R Cooper and T P Johnston (Geological Survey of Northern Ireland) Geographical Index Northern Ireland Subject Index Petrography, Dalradian geology, metacarbonate rocks Bibliographic reference Thomas, C W. 2000 Petrography of metalimestones and metadolostones from the Argyll and Southern Highland groups, Dalradian, Northern Ireland. British Geological Survey Technical Report WA/00/72 © NERC copyright 2000 British Geological Survey, Edinburgh 2000 BGS Technical Report WA/00/72 Status: 16 January 2001 The full range of Survey publications is available Parent Body through the Sales Desks at Keyworth and at Natural Environment Research Council Murchison House, Edinburgh, and in the BGS London Polaris House, North Star Avenue, Information Office in the Natural History Museum Swindon, Wiltshire, SN2 I EU. Earth Galleries. The adjacent bookshop stocks the Telephone 01793 411500 more popular books for sale over the counter. Most Fax 01793 411501 BGS books and reports are listed in HMSO's Sectional List 45, and can be bought from HMSO and through HMSO agents and retailers. Maps are listed in the Kingsley Dunham Centre BGS Map Catalogue, and can be bought from Keyworth, Nottingham, NG 12 5GG. Ordnance Survey agents as well as from BGS. Telephone 0115 936 3100 Fax 0115 936 3200 The British Geological Survey carries out the geological survey of Great Britain and Northern Ireland (the latter as an agency service for the Murchison House, West Mains Road, government of Northern Ireland), and of the Edinburgh, EH9 3LA. -
History of the Church of Jesus Christ of Latter-Day Saints in Ireland Since 1840
Brigham Young University BYU ScholarsArchive Theses and Dissertations 1968 History of The Church of Jesus Christ of Latter-Day Saints in Ireland Since 1840 Brent A. Barlow Brigham Young University - Provo Follow this and additional works at: https://scholarsarchive.byu.edu/etd Part of the European History Commons, History of Christianity Commons, and the Mormon Studies Commons BYU ScholarsArchive Citation Barlow, Brent A., "History of The Church of Jesus Christ of Latter-Day Saints in Ireland Since 1840" (1968). Theses and Dissertations. 4503. https://scholarsarchive.byu.edu/etd/4503 This Thesis is brought to you for free and open access by BYU ScholarsArchive. It has been accepted for inclusion in Theses and Dissertations by an authorized administrator of BYU ScholarsArchive. For more information, please contact [email protected], [email protected]. 4119 HISTORY OF THE CHURCH OF JESUS CHRIST OF UTTERUTTERDAYLATTERDAYLATTER DAY SAINTS IN IRELANDD SINCE 18101840 A thesis presented to the department of graduate studies in religious instruction brigham young university provo utah in partial fulfillment of the requirements for the degree master of arts by brent aaAa& barlow may 1968 acknowledgments I1 would like to express ravmyraysincere appreciation to the following people for thetheirir valuable assistance and help dr richard 0 cofanocowanocowan chairman of the advisory colitcomitcommitteetee fforroror his many timely suggestions and genuine interest in this research pro- ject dr rodney turner member of the advisory committee -
Table of Contents
EirGrid and SONI Joint Environmental Report Table of Contents Non-Technical Summary .......................................................................................................... i Introduction i The Joint Environmental Report ii Project Need iv Overall Project Description iv Alternatives vii Location and Routeing Alternatives viii JER Appraisal of the Proposed Interconnector x 1. Introduction .................................................................................................................... 1 1.1 The Proposed Interconnector 1 1.2 Guidance and Legislation on Transboundary Projects 2 1.3 This Report 5 2. Project Description and Purpose ............................................................................... 10 2.1 Project Need 10 2.2 Overall Project Description 10 3. Alternatives .................................................................................................................. 15 3.1 Introduction 15 3.2 Technological Alternatives 16 3.3 Location and Routeing Alternatives 17 4. Population – Socio-Economic .................................................................................... 20 4.1 Introduction 20 4.2 Methodology 20 4.3 The Receiving Environment 21 4.4 Mitigation Measures 22 4.5 Residual Impacts 23 4.6 Transboundary Effects 24 4.7 Conclusions 24 5. Population – Tourism .................................................................................................. 25 5.1 Introduction 25 5.2 Methodology 25 5.3 The Receiving Environment 26 EirGrid and SONI Joint Environmental