High-Speed Train Derailments - Minimizing Consequences Through Innovative Design
Total Page:16
File Type:pdf, Size:1020Kb
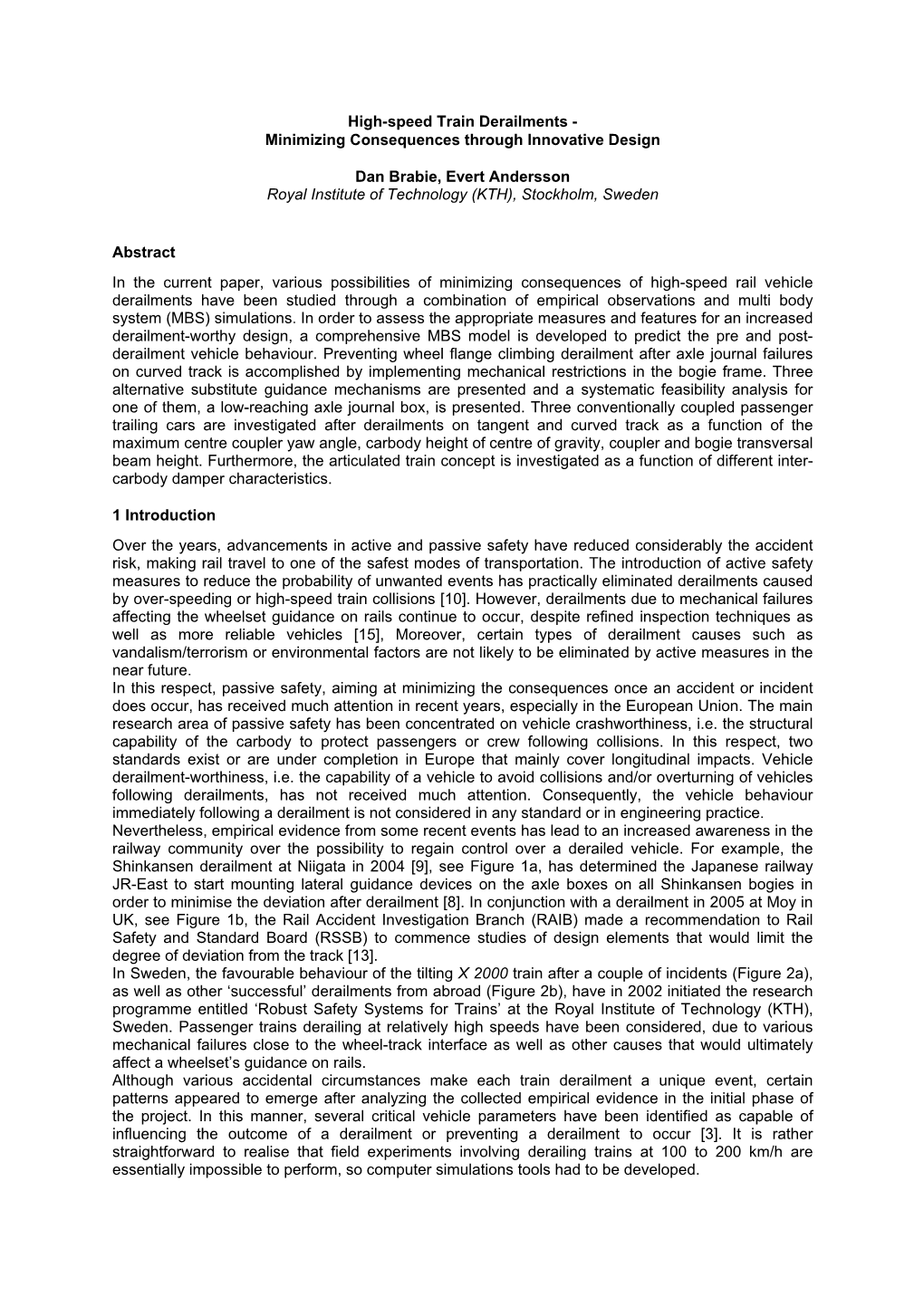
Load more
Recommended publications
-
Rail Accident Report
Rail Accident Report Derailment of a passenger train near Cummersdale, Cumbria 1 June 2009 Report 06/2010 March 2010 This investigation was carried out in accordance with: l the Railway Safety Directive 2004/49/EC; l the Railways and Transport Safety Act 2003; and l the Railways (Accident Investigation and Reporting) Regulations 2005. © Crown copyright 2010 You may re-use this document/publication (not including departmental or agency logos) free of charge in any format or medium. You must re-use it accurately and not in a misleading context. The material must be acknowledged as Crown copyright and you must give the title of the source publication. Where we have identified any third party copyright material you will need to obtain permission from the copyright holders concerned. This document/publication is also available at www.raib.gov.uk. Any enquiries about this publication should be sent to: RAIB Email: [email protected] The Wharf Telephone: 01332 253300 Stores Road Fax: 01332 253301 Derby UK Website: www.raib.gov.uk DE21 4BA This report is published by the Rail Accident Investigation Branch, Department for Transport. * Cover photo courtesy of Network Rail Derailment of a passenger train near Cummersdale, Cumbria, 1 June 2009 Contents Preface 5 Key Definitions 5 The Accident 6 Summary of the accident 6 The parties involved 7 Location 8 External circumstances 8 The trains involved 10 Events preceding the accident 10 Events during the accident 10 Consequences of the accident 11 Events following the accident 11 The Investigation -
JR East Technical Review No.27-AUTUMN.2013
Interpretive article Clarification of Mechanism of Shinkansen Derailment in the 2011 Great East Japan Earthquake and Countermeasures Against Earthquakes Kenji Horioka Director, Safety Research Laboratory, Research and Development Center of JR East Group The Great East Japan Earthquake of March 11, 2011 resulted in tremendous damage to JR East railway facilitates due to seismic vibration and the ensuing tsunami. One incident was the derailment of a Tohoku Shinkansen train making a test run near Sendai Station. This marked the second time a JR East Shinkansen train had derailed, following that in the 2004 Mid Niigata Prefecture Earthquake. This article will cover the derailment accident investigation and its findings along with issues and lessons discovered in the process of that investigation. It will also cover past countermeasures against earthquakes and future issues in R&D. 1 Introduction of the process of clarifying derailment accident phenomena, lessons learned through that, and new issues that came up in Broad-ranging damage was suffered in the JR East area due to light the recent earthquake. seismic vibration and the ensuing tsunami of the Great East In clarifying derailment accident phenomena, we received Japan Earthquake of March 11, 2011. The earthquake was huge, much technical guidance from the Railway Technical Research measuring a magnitude (MW) of 9.0 (approx. 1,000 times the Institute (RTRI) related to issues such as analyzing response of energy of the 1995 Great Hanshin-Awagi Earthquake), but we structures affected by seismic motion and analyzing rolling stock were fortunate in that there were no major injuries to passengers. behavior. I would like to take this opportunity to express our JR East did, however, suffer unprecedented damage including gratitude for their assistance. -
Railwayoccurrencerepo Rt
RAILWAY OCCURRENCE REPORT 05-109 tourist Trains Linx and Snake, derailments, Driving 20 February 2005 - Creek Railway, Coromandel 3 March 2005 TRANSPORT ACCIDENT INVESTIGATION COMMISSION NEW ZEALAND The Transport Accident Investigation Commission is an independent Crown entity established to determine the circumstances and causes of accidents and incidents with a view to avoiding similar occurrences in the future. Accordingly it is inappropriate that reports should be used to assign fault or blame or determine liability, since neither the investigation nor the reporting process has been undertaken for that purpose. The Commission may make recommendations to improve transport safety. The cost of implementing any recommendation must always be balanced against its benefits. Such analysis is a matter for the regulator and the industry. These reports may be reprinted in whole or in part without charge, providing acknowledgement is made to the Transport Accident Investigation Commission. Report 05-109 tourist Trains Linx and Snake derailments Driving Creek Railway Coromandel 20 February 2005 - 3 March 2005 Abstract On Sunday 20 February 2005 at about 1300, the Driving Creek Train Linx derailed at Peg 1660. The rear bogie of the last passenger set derailed and was dragged about 15 m before one of the derailment bars hit a rail joint fishplate, causing the rear bogie to jump further to the left-hand side of the track. One passenger received moderate injuries. In the afternoon of Sunday 27 February 2005, the rear bogie of the last passenger set of the Train Linx derailed to the inside of a tight right-hand curve at Peg 1270 on the Driving Creek Railway. -
Report 99-115 Vintage Train Derailment Kawakawa 26 June
Report 99-115 vintage train derailment Kawakawa 26 June 1999 Abstract At about 1345 hours on Saturday, 26 June 1999, a vintage steam train operated by the Bay of Islands Vintage Railway was on a scheduled passenger trip from Opua to Kawakawa when the track spread and the locomotive and the following two carriages derailed at low speed. No injuries to the crew or passengers resulted. Safety issues identified included the standard of track maintenance and the adequacy of the track inspection. Two safety recommendations were made to the operator, and two to the Director of the Land Transport Safety Authority to address the safety issues. The Transport Accident Investigation Commission is an independent Crown entity established to determine the circumstances and causes of accidents and incidents with a view to avoiding similar occurrences in the future. Accordingly it is inappropriate that reports should be used to assign fault or blame or determine liability, since neither the investigation nor the reporting process has been undertaken for that purpose. The Commission may make recommendations to improve transport safety. The cost of implementing any recommendation must always be balanced against its benefits. Such analysis is a matter for the regulator and the industry. These reports may be reprinted in whole or in part without charge, providing acknowledgement is made to the Transport Accident Investigation Commission. Transport Accident Investigation Commission P O Box 10-323, Wellington, New Zealand Phone +64 4 473 3112 Fax +64 4 499 1510 E-mail: [email protected] Web site: www.taic.org.nz Contents List of Abbreviations.............................................................................................................................. -
Commission of Railway Safety)
GOVERNMENT OF INDIA MINISTRY OF CIVIL AVIATION (COMMISSION OF RAILWAY SAFETY) Office of the Commissioner of Railway Safety, Eastern Circle, 14, Strand Road (12th Floor), Kolkata - 700001. No. Dated: 17.08.2011 To The Chief Commissioner of Railway Safety, Ashok Marg, Lucknow - 226 001. Sir, Sub: Preliminary narrative report on derailment of 12510 Dn Guwahati – Bangalore Express between Km 279/10– 279/7 in Gour Malda – Jamirghata Double line non electrified section of MLDT division of E.Rly and its subsequent collision by 53027 Up Azimganj – Malda Town Passenger train at about 19.05 hrs on 31.07.2011. INTRODUCTION 1.1 Preamble In accordance with Rule 3 of the 'Statutory Investigation into Railway Accidents Rules, 1998, issued by the Ministry of Civil Aviation, Government of India, I hereby submit a brief Preliminary narrative Report of my Statutory Inquiry in respect of the Derailment of 12510 Dn Guwahati – Bangalore Express between Km 279/10 – 279/7 in Gour Malda – Jamirghata Double line non electrified section of MLDT division of E.Rly and its subsequent collision by 53027 Up Azimganj – Malda Town Passenger train at about19.05 hours on 31.07.2011 1.2 Inspection and Inquiry - 1.2.1 On 31.07.2011, I received a call on my mobile phone from CSO/E.Rly at 19.35 hrs. On seeing the call log at 20.00 hrs, I immediately rang him. He responded stating that there was an accident of the Bangalore – Guwahati Express over Malda division in MLDT-AZ section in which a passenger train is also involved. -
On the Influence of Rail Vehicle Parameters on the Derailment Process and Its Consequences
DAN BRABIE on the Derailment Parameters Vehicle On the Influence of Rail and its Consequences Process TRITA AVE 2005:17 ISSN 1651-7660 ISBN 91-7283-806-X On the Influence of Rail Vehicle Parameters on the Derailment Process and its Consequences DAN BRABIE Licentiate Thesis in Railway Technology KTH 2005 KTH Stockholm, Sweden 2005 www.kth.se On the Influence of Rail Vehicle Parameters on the Derailment Process and its Consequences by Dan Brabie Licentiate Thesis TRITA AVE 2005:17 ISSN 1651-7660 ISBN 91-7283-806-X Postal Address Visiting address Telephone E-mail Royal Institute of Technology Teknikringen 8 +46 8 790 84 76 [email protected] Aeronautical and Vehicle Engineering Stockholm Fax Railway Technology +46 8 790 76 29 SE-100 44 Stockholm . Contents Contents.............................................................................................................................i Preface and acknowledgements.................................................................................... iii Abstract ............................................................................................................................v 1 Introduction.................................................................................................................1 1.1 Background information......................................................................................1 1.2 Previous research.................................................................................................1 1.3 Scope, structure and contribution of this thesis...................................................3 -
Summary of Accidents Investigated by the Federal Railroad Administration (FRA) Includes 238 Railroad Accidents
© Summary of Accidents U.S. Department Investigated By The of Transportation Federal Railroad Administration Federal Railroad Administration Calendar Year 1 9 8 7 <T5 Office of Safety June 1989 Washington, D.C. 20590 TABLE OF CONTENTS P a g e INTRODUCTION .................. i ACCIDENT SUMMARY . .............................. iii ACCIDENT SUMMARY BY TRACK CLASS, DAMAGES, TYPE AND CAUSE................................................ iv INVOLVEMENT OF TRAIN ACCIDENTS BY RAILROAD, TYPE, AND CAUSE (Total figures varing due to duplicate reporting). v ACCIDENT LOCATION...................................... vi ACCIDENT INVESTIGATION REPORTS ........................ 1 / INTRODUCTION The 1987 Summary of Accidents Investigated by the Federal Railroad Administration (FRA) includes 238 railroad accidents. This summary provides the following information: o the railroad(s) involved o the location and the time of the accident o the type of railroad accident o the method of operation and movements involved o the speed involved o the type and class of track o the number of casualties o the estimated cost of railroad damages o the probable cause and any contributing factor(s). The railroad codes used in this summary can be found in the FRA Guide for Preparing Accident/Incident Reports Appendix A. Estimated railroad damage includes labor cost, and all other costs to repair or replace damaged on-track equipment, signals, track, track structures, or roadbed. The cost of lading and clearing the wreck, as well as the cost to society, is not included. y* The data were edited and summarized by FRA personnel. The United States Government assumes no liability for its contents or use. 9 Federal Railroad Administration Office of Safety, RRS-22 400 Seventh Street, S.W. -
~A .. &O -22...MAJOR RAILROAD ACCIDENTS INVOLVING
~A .. &o -22.... REPORT NO. FRA-RRS-80-04 MAJOR RAILROAD ACCIDENTS INVOLVING HAZARDOUS MATERIALS RELEASE COMPOS I TE SUMMAR I ES 1969-1978 U.S. DEPARTMENT OF TRANSPORTATION RESEARCH AND SPECIAL PROGRAMS ADMINISTRATION Transportation Systems Center Cambridge MA 02142 JULY 1980 FINAL REPORT DOCUMENT IS AVAILABLE TO THE PUBLIC THROUGH THE NATIONAL TECHNICAL INFORMATION SERVICE, SPRINGFIELD, VIRGINIA 22161 Prepared for U.S. DEPARTMENT OF TRANSPORTATION FEDERAL RAILROAD ADMINISTRATION Office of Safety Washington DC 20590 NOTICE This document is disseminated under the sponsorship of the Department of Transportation in the interest of information exchange. The United States· Govern- ment assumes no liability for its contents or use thereof. NOTICE The United States Government does not P.ndorse pro- ducts or manufacturers. Trade or manufacturers' names appear herein solely because they are con- sidered essential to the object of this report. Technical ~eport Documentation Page 1. Report No. 2 . Government Accession No. 3. Recipient" s Cotalog No. FRA-RRS-80-04 4. Title and Subtitle 5. Reoort DotR July 1980 MAJOR RAILROAD ACCIDENTS INVOLVING HAZARDOUS MATERIALS RELEASE, COMPOSITE SUMMARIES 1969-1978 6. Performing Organization Code DTS-223 1-::---,--,-,-------------------------------! 8. Performing Orgoni zation Report No . 7. Author' s) Theodore S. Glickman, Technical Monitor DOT-TSC-FRA-80-22 9. Performing Orgoni zation Name and Address 10 . Work Un it No. (TRAIS} U.S . Department of Transportation RR042/R0332 Research and Special Programs Administration 11. Contract or Grant No. Transportation Systems Center Cambridge, MA 02142 t-- --- ---- - - - ------------ - ---------,1 13. Type of Report and Period Covered 12. Sponsoring Agency Name and Address Final Report U.S. -
Derailment of a Rail Head Treatment Train Near Dunkeld & Birnam, 29
Derailment of a rail head treatment train near Dunkeld & Birnam, 29 October 2018 Important safety messages This accident demonstrates that the formation of large wheel flats on rail vehicles can lead to derailment. It is therefore important that: • operators and maintainers of Rail Head Treatment Trains (RHTTs) closely monitor the condition of wheels and braking systems when operating in low adhesion conditions, due to the increased likelihood of the formation of large wheel flats. • operators of freight trains, and other specialist trains derived from freight wagons (including RHTTs), undertake suitable roll-by examinations on departure from yards, to detect non-rotating wheels. • maintainers of freight wagons have a process in place to control the isolation of handbrake interlocks on freight wagons. • staff preparing freight trains for departure, check that handbrakes are fully released and do not place sole reliance on handbrake interlocks. Summary of the accident At around 22:15 hrs on 29 October 2018, a rail head treatment train (RHTT) comprising a Class 67 locomotive and two specialised wagons, operated by DB Cargo and travelling between Inverness and Perth, derailed just after passing Dunkeld and Birnam station. Both wheelsets of the 4th bogie in the train derailed at a set of trailing points, ran for around 100 metres causing significant track damage, and then rerailed at the next set of trailing points. The train then continued a further 15 miles to Perth. Rail Accident Investigation Branch Safety digest 01/2019: Dunkeld & Birnam Simplified diagram of the track layout at Dunkeld and Birnam station Cause of the accident The RHTT was crewed by a driver, and an operative who operated the rail head treatment equipment in accordance with a pre-defined plan. -
Full-Scale Train Derailment Testing and Analysis of Post-Derailment Behavior of Casting Bogie
applied sciences Article Full-Scale Train Derailment Testing and Analysis of Post-Derailment Behavior of Casting Bogie Hyun-Ung Bae 1 , Jiho Moon 2 , Seung-Jae Lim 3, Jong-Chan Park 4 and Nam-Hyoung Lim 4,* 1 R&D Lab., Road Kinematics co., Ltd., Cheonan 31094, Korea; [email protected] 2 Department of Civil Engineering, Kangwon National University, Chuncheon 24341, Korea; [email protected] 3 Chungnam Railway Research Institute, Chungnam National University, Daejeon 34134, Korea; [email protected] 4 Department of Civil Engineering, Chungnam National University, Daejeon 34134, Korea; [email protected] * Correspondence: [email protected]; Tel.: +82-42-821-8867 Received: 10 November 2019; Accepted: 18 December 2019; Published: 19 December 2019 Abstract: In this study, a full-scale train bogie derailment test was conducted. For this, test methodologies to describe the wheel-climbing derailment of the train bogie and to obtain accurate test data were proposed. The derailment test was performed with the casting bogie for a freight train and a Rheda 2000 concrete track. Two different derailment velocities (28.08 km/h and 55.05 km/h) were considered. From the test, it was found that humps in the concrete track affected the post-derailment behavior of the bogie when the derailment velocity was 28.08 km/h. For a higher derailment velocity (55.05 km/h), significant lateral movement of the derailed bogie was observed. This lateral movement was first controlled by wheel–rail contact, followed by contact with the containment wall. Finally, the train was returned to the track center. -
Railway Investigation Report R04t0008 Main-Track
RAILWAY INVESTIGATION REPORT R04T0008 MAIN-TRACK DERAILMENT CANADIAN PACIFIC RAILWAY TRAIN NO. 239-13 MILE 178.20, BELLEVILLE SUBDIVISION WHITBY, ONTARIO 14 JANUARY 2004 The Transportation Safety Board of Canada (TSB) investigated this occurrence for the purpose of advancing transportation safety. It is not the function of the Board to assign fault or determine civil or criminal liability. Railway Investigation Report Main-Track Derailment Canadian Pacific Railway Train No. 239-13 Mile 178.20, Belleville Subdivision Whitby, Ontario 14 January 2004 Report Number R04T0008 Synopsis On 14 January 2004, at approximately 1942 eastern standard time, Canadian Pacific Railway intermodal train 239-13, travelling westward, derailed 11 car platforms transporting 18 containers at Mile 178.20 of the Belleville Subdivision. The derailment occurred just east of the overpass at Garden Street in Whitby, Ontario. Some of the rail car platforms and containers fell onto the roadway below, striking a southbound vehicle and fatally injuring the two occupants. Ce rapport est également disponible en français. © Minister of Public Works and Government Services 2006 Cat. No. TU3-6/04-1E ISBN 0-662-42997-4 TABLE OF CONTENTS 1.0 Factual Information ............................................................................1 1.1 The Accident ................................................................................................................ 1 1.2 Site Examination......................................................................................................... -
Considerations on the Derailment Causes Over the Years on the Romanian Railway Network
MATEC Web of Conferences 178, 08010 (2018) https://doi.org/10.1051/matecconf/201817808010 IManE&E 2018 Considerations on the derailment causes over the years on the Romanian railway network Mircea Nicolescu* Romanian Railway Investigating Agency AGIFER, Calea Griviței 393, București, România Abstract. This paper has analysed a series of railway accidents produced by derailment in two different time periods: 1938-1945 and 2010-2011, in attempting to compare direct causes typologies. The comparison serves as purpose to establish the way in which technological development produced several changes and the conclusions can be surprising. In spite of the technical evolutions in the railroads industry during 70 years, a lot of the causes remain the same. 1 Introduction The railway accident is defined in the national legislation [1], as well as in the European legislation [2] as an “unforeseen event, unwanted and unintended or a specific chain of events which had harmful consequences”. The derailment is one of the distinct categories of the accidents according to the same legislation. The study of the derailment and the avoid in occurring a such event had always an utmost importance due to safety but also economic reasons. The train derailments are the result of the contact loss between the wheel and the track or the rolling of the wheels outside the track (either on the exterior of the tracks either between them). The railway track sustains the wheels but it also guiding them. In consequence, any situation in which this capacity is reduced, it results in a derailment. In the specialized papers that analyses the phenomenon [3], the mechanisms that determine a derailment are classified in the following categories: derailments as a result of wheel flange climb, derailments caused by wheel lift, derailments caused by gauge spread, derailments determined by rail failure, derailments due to incorrect switch rail position and condition, derailments caused by suspension failure.