Impact of Different Binders on the Roughness, Adhesion Strength, and Other Properties of Mortars with Expanded Cork
Total Page:16
File Type:pdf, Size:1020Kb
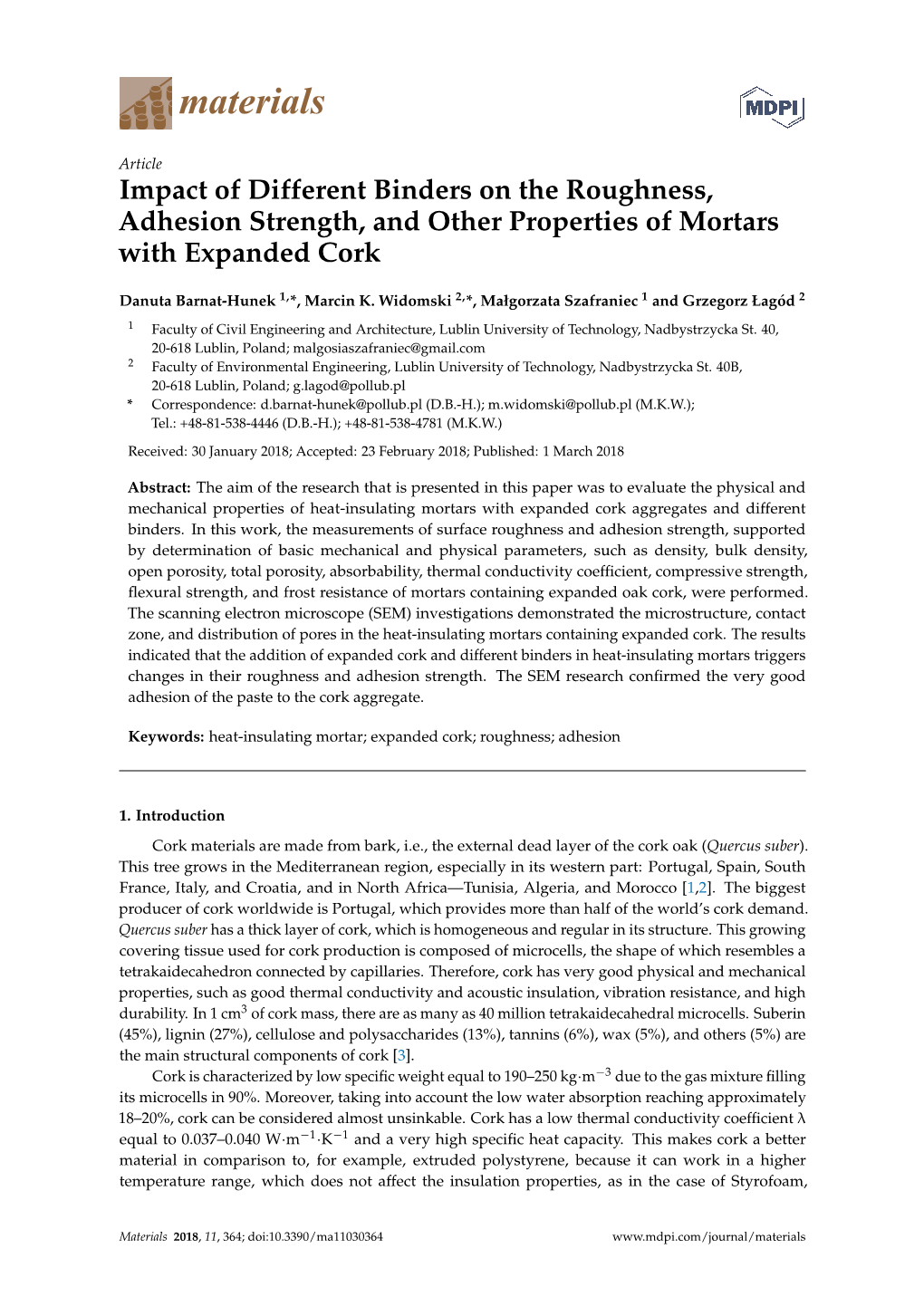
Load more
Recommended publications
-
Project MKULTRA, the CIA's Program of Research in Behavioral Modification JOINT HEARING
1977 Senate Hearing on MKULTRA: Cover Page Project MKULTRA, The CIA's Program Of Research In Behavioral Modification JOINT HEARING BEFORE THE SELECT COMMITTEE ON INTELLIGENCE AND THE SUBCOMMITTEE ON HEALTH AND SCIENTIFIC RESEARCH OF THE COMMITTEE ON HUMAN RESOURCES UNITED STATES SENATE NINETY-FIFTH CONGRESS FIRST SESSION ____________ AUGUST 3, 1977 Printed for the use of the Select Committee on Intelligence and Committee on Human Resources 1 1977 Senate Hearing on MKULTRA: Cover Page U.S. GOVERNMENT PRINTING OFFICE WASHINGTON: 1977 For sale by the Superintendent of Documents, U.S. Government Printing Office Washington, D.C. 20402 Stock No. 052-070-04357-1 2 1977 Senate Hearing on MKULTRA: Staff Page SENATE SELECT COMMITTEE ON INTELLIGENCE (Established by S. Res. 400, 94th Cong., 2d sess.) DANIEL K. INOUYE, Hawaii, Chairman BARRY GOLDWATER, Arizona, Vice Chairman BIRCH BAYH, Indiana ADLAI E. STEVENSON, Illinois WILLIAM D. HATHAWAY, Maine WALTER D. HUDDLESTON, Kentucky JOSEPH R. BIDEN, JR., Delaware ROBERT MORGAN, North Carolina GARY HART, Colorado DANIEL PATRICK MOYNIHAN, New York CLIFFORD P. CASE, New Jersey JAKE GARN, Utah CHARLES McC. MATHIAS, JR., Maryland JAMES B. PEARSON, Kansas JOHN H. CHAFE, Rhode Island RICHARD G. LUGAR, Indiana MALCOLM WALLOP, Wyoming ROBERT C. BYRD, West Virginia, Ex Officio Member HOWARD H. BAKER, JR., Tennessee, Ex Officio Member WILLIAM G. MILLER, Staff Director EARL D. EISENHOWER, Minority Staff Director AUDREY H. HATRY, Chief Clerk COMMITTEE ON HUMAN RESOURCES HARRISON A. WILLIAMS, JR., New Jersey, Chairman JENNINGS RANDOLPH, West Virginia CLAIBORNE PELL, Rhode Island EDWARD M. KENNEDY, Massachusetts GAYLORD NELSON, Wisconsin 3 1977 Senate Hearing on MKULTRA: Staff Page THOMAS F. -
Twilight 2000
TWILIGHT 2000 Twilight 2000 is a Role playing game set in a fictional future, one where World war 3 began in the late 1990's and eventually slipped into a nuclear exchange changing society as we know it. The players assume the roles of survivors trying to live through the aftermath of the war. Twilight 2000 was published in the mid 1980's by Game Designers Workshop who unfortunately closed their doors in the early 1990's. The copyright was purchased by Tantalus, Inc but there are no stated plans to revive the game. Despite the lack of any new material from a publisher the game continues to expand through the players on websites such as this. This is my contribution to the game, this site will be in a constant state of change, I plan to add material as I get it finished. This will include new equipment, optional rules, alternate game backgrounds and other material as it accumulates, currently I am working on source material for a World war 2 background, but I also have been completing some optional rules of my own as well as modern equipment. For other perspectives on Twilight 2000 visit the links listed at the bottom of this page. Twilight 2000 World war 2 material World war 2 source book Twilight 2000 Modern equipment Modern equipment Optional rules for Twilight 2000 Fire Links to other Twilight 2000 pages Antennas T2K Page: Focusing on Sweden's forces, equipment and background, also includes archives of discontinued sites and web discussions. The Dark place: Includes material for several RPG's including Twilight 2000 and Behind Enemy Lines. -
Roman Mortars Used in the Archaeological Sites In
UNIVERSIDAD POLITÉCNICA DE MADRID ESCUELA TÉCNICA SUPERIOR DE ARQUITECTURA ROMAN MORTARS USED IN THE ARCHAEOLOGICAL SITES IN SPAIN AND TURKEY A COMPARATIVE STUDY AND THE DESIGN OF REPAIR MORTARS TESIS DOCTORAL DUYGU ERGENÇ Ingeniera Geológica y Máster en Restauración Junio 2017 CONSERVACIÓN Y RESTAURACIÓN DEL PATRIMONIO ARQUITECTÓNICO ESCUELA T ÉCNICA SUPERIOR DE ARQUITECTURA DE MADRID ROMAN MORTARS USED IN THE ARCHAEOLOGICAL SITES IN SPAIN AND TURKEY A COMPARATIVE STUDY AND THE DESIGN OF REPAIR MORTARS Autor: DUYGU ERGENÇ Ingeniera Geológica y Máster en Restauración Directores: Dr. Fco. David Sanz Arauz Doctor en Arquitectura por ETSAM, UPM Dr. Rafael Fort González Doctor en Geología Económica por UCM, Senior científico en Instituto de Geociencias (CSIC-UCM) 2017 TRIBUNAL Tribunal nombrado por el Mgfco. Y Excmo. Sr. Rector de la Universidad Politécnica de Madrid, el día de de 2017 Presidente: Vocales: Secretario: Suplentes: Realizado el acto de lectura y defensa de la Tesis Doctoral el día de de 2017 en la Escuela Técnica Superior de Arquitectura de la Universidad Politécnica de Madrid EL PRESIDENTE LOS VOCALES EL SECRETARIO I hereby declare that all information in this document has been obtained and presented in accordance with academic rules and ethical conduct. I also declare that, as required by these rules and conduct I have fully cited and referenced all material and results that are not original to this work. To my family Acknowledgements This thesis would not have been possible without the support and expertise of many people. First of all, I would like to express my sincere gratitude to my advisors, Dr. Fco. -
Foreign Military Weapons and Equipment
DEPARTMENT OF THE ARMY PAMPHLET NO. 30-7-4 FOREIGN MILITARY WEAPONS AND EQUIPMENT Vol. III INFANTRY WEAPONS DEPARTMENT OF THE ARMY DT WASHINGTON 25, D. C. FOREWORD The object in publishing the essential recognition features of weapons of Austrian, German, and Japanese origin as advance sections of DA Pam 30-7-4 is to present technical information on these weapons as they are used or held in significant quantities by the Soviet satellite nations (see DA Pam 30-7-2). The publication is in looseleaf form to facilitate inclusion of additional material when the remaining sections of DA Pam 30-7-4 are published. Items are presented according to country of manufacture. It should be noted that, although they may be in use or held in reserve by a satellite country, they may be regarded as obsolete in the country of manufacture. DA Pam 30-7-4 PAMPHLET DEPARTMENT OF THE ARMY No. 30-7-4 WASHINGTON 25, D. C., 24 November 1954 FOREIGN MILITARY WEAPONS AND EQUIPMENT VOL. III INFANTRY WEAPONS SECTION IV. OTHER COUNTRIES AUSTRIA: Page Glossary of Austrian terms--------------------------------------------------------- 4 A. Pistols: 9-mm Pistol M12 (Steyr) ---------------------------------------------------- 5 B. Submachine Guns: 9-mm Submachine Gun MP 34 (Steyr-Solothurn) ------------------------------- .7 C. Rifles and Carbines: 8-mm M1895 Mannlicher Rifle- - ____________________________________- - - - - - -- 9 GERMANY: Glossary of German terms___________________________________---------------------------------------------------------11 A. Pistols: 9-mm Walther Pistol M1938-- _______________________-- - --- -- -- 13 9-mm Luger Pistol M1908--------------------------------------------------15 7.65-mm Sauer Pistol M1938---------------------------------_ 17 7.65-mm Walther Pistol Model PP and PPK ---------------------------------- 19 7.63-mm Mauser Pistol M1932----------------------------------------------21 7.65-mm Mauser Pistol Model HSc ------------------------------------------ 23 B. -
Structural Use of Unreinforced Masonry
Document No. :: IITK-GSDMA-EQ12-V4.0 :: IITK-GSDMA-EQ19-V2.0 ::IITK-GSDMA-EQ25-V2.0 Final Report :: A - Earthquake Codes IITK-GSDMA Project on Building Codes Structural Use of Unreinforced Masonry by Dr. Durgesh C. Rai Department of Civil Engineering Indian Institute of Technology Kanpur Kanpur With assistance from Mr. Sandeep Pal Ms. Ami Patwa Mr. Samaresh Paikara Mr. Ashish Narayan Department of Civil Engineering Indian Institute of Technology Kanpur Kanpur Code &Commentary IS:1905 • This document has been made available as a “Draft for Comment” and is not ready for use. It is still in development stage as a part of ongoing project on Building Codes sponsored by Gujarat State Disaster Management Authority, Gandhinagar at Indian Institute of Technology Kanpur. • The views and opinions expressed are those of the authors and not necessarily of the GSDMA, the World Bank, IIT Kanpur, or the Bureau of Indian Standards. • Comments and feedbacks may please be forwarded to: Prof. Sudhir K Jain, Dept. of Civil Engineering, IIT Kanpur, Kanpur 208016, email: [email protected]; [email protected] Page ii Code &Commentary IS:1905 CONTENTS PART 1: CODE AND COMMENTARY 0. – FOREWORD .........................................1 5.6 – Permissible Stresses 59 5.6.1 – Basic Compressive stress 59 1. – SCOPE ..................................................5 5.6.2 – Permissible Compressive 1.1 – ..........................................................5 Stress……………………………….60 1.2 – ..........................................................5 5.7 – Combined Permissible -
The Cavalry Group
World War II US Cavalry Groups European Theater GORDON L. ROTTMAN ILLUSTRATED BY PETER DENNIS © Osprey Publishing • www.ospreypublishing.com Elite • 129 World War II US Cavalry Groups European Theater GORDON L. ROTTMAN ILLUSTRATED BY PETER DENNIS Series editor Martin Windrow © Osprey Publishing • www.ospreypublishing.com CONTENTS INTRODUCTION 4 THE PRE-WAR CAVALRY REGIMENTS 5 Regiments, squadrons, and troops THE CAVALRY GROUP (MECHANIZED) 7 Organization: Headquarters and Headquarters Troop – Cavalry Reconnaissance Squadrons (Mechanized) – Troops Cavalry Group armament and vehicles CAVALRY GROUP MISSIONS 16 Doctrine and practice Group and squadron tactics Task-organization for combat CAVALRY GROUP DEPLOYMENTS 32 THE TEST OF BATTLE 42 Representative examples of cavalry groups in action: 113th Cavalry Group reconnaissance mission – 4th Cavalry Group screening mission – 113th Cavalry Group in the defense – 6th Cavalry Group in the offensive – 2nd Cavalry Group in defense of a river – 2nd Cavalry Reconnaissance Squadron in a river assault – 316th Cavalry Brigade in the offensive – 101st Cavalry Group, miscellaneous missions – 3rd Cavalry Group in the pursuit CONCLUSIONS 58 Assessments The post-World War II mechanized cavalry SELECT BIBLIOGRAPHY 63 INDEX 64 © Osprey Publishing • www.ospreypublishing.com WORLD WAR II US CAVALRY GROUPS EUROPEAN THEATER INTRODUCTION The World War II battlefield accomplishments of the mechanized cavalry groups go largely unreported. These predecessors of the armored cavalry regiments of the late 1940s to early 2000s carried the lineages of pre-war cavalry regiments. Supporting field armies, corps, and divisions, the lightly armed, fast-moving cavalry groups performed not only their primary roles of reconnaissance and security missions, but also both offensive and defensive operations, as well as a variety of unforeseen special missions. -
RAO BULLETIN 1 December 2017
RAO BULLETIN 1 December 2017 PDF Edition THIS RETIREE ACTIVITIES OFFICE BULLETIN CONTAINS THE FOLLOWING ARTICLES Pg Article Subject . * DOD * . 05 == NDAA 2018 [17] ---- (Impact on Defense Spending) 07 == DoD Blended Retirement System ---- (Bonus Lowest Allowed By Law) 07 == Transgender Troops [11] ---- (Sex Assignment Surgery Ban Halted) 09 == Transgender Troops [12] ---- (Third Court Injunction Issued) 09 == AFRH [08] ---- (New CEO Named) 10 == N-Zero [01] ---- (Battery Might Not Need A Charge for 10 Years). 11 == DoD Children Schools ---- (47 Under Consideration for Divestiture) 12 == GI Bill Transferability [03] ---- (Policy Change Under Consideration) 13 == GTMO Detainees [01] ---- (Artwork Barred From Further Release) 14 == DoD Fraud, Waste, & Abuse ---- (Reported 16 thru 30 NOV 2017) 15 == POW/MIA Recoveries ---- (Reported 16 thru 30 NOV 2017 | Eleven) . * VA * . 17 == White House VA Hotline [01] ---- (Now Fully Staffed 7/24) 1 17 == VA Privatization [12] ---- (H.R.4457 Breaks Nation’s Promise To Vets) 18 == VA Benefits Reform ---- (Shulkin Calls for Overhaul & Realignment) 19 == VA Benefits Reform [01] ---- (Choice & Tricare Merger Proposal) 22 == VA Benefits Reform [02] ---- (VFW Criticizes Veterans Empowerment Act) 22== VA ID Card [13] ---- (Vets Can Now Apply) 23 == VA Unpaid Obligations ---- ($226M to Settle 23 Claims) 24 == VA Women Vet Programs [32] ---- (Depression & Heart Disease) 25 == VA Physician Qualifications [03] ---- (Poor Performers Not Reported | 90%) 25 == PTSD [235] ---- (HBOT Treatment Option) 26 == VA Suicide -
Technical Specifications for Reconstruction of Development
TECHNICAL SPECIFICATIONS FOR RECONSTRUCTION OF DEVELOPMENT CENTER IN VLORA 1 PRESENTATION This technical specification is the contractual document, drawn up especially for works of reconstruction of “DEVELOPMENT CENTER” in Vlora. Items listed in this specification, corresponding to the voices of BoQ, based on project design and in "Technical Manual construction price and technical analysis" approved by Council of Ministers nr. 629, date 15.7.2015. Quality standards materials used are, those of the Albanian state for materials manufacturing country and the countries of the European Union to import materials. In these cases the administrator already kontratres origin certificate may request and certificates of quality and technical performance data of the items to be supplied. Standards used in this technical specification are not reliant on project drawings or technical requirements for design and implementation, but also in legal manuals and other books. Subject involved in drafting this reconstruction, in case the problem may make suggestions, improvements and amendments to those specifications, if required by the potential changes to the categories of works or the lack of details and materials. 2 GENERAL The paragraph in this section are complementary to the details in the contract and contractor serving for bid preparation phase and implementation phase supervisor. Contractor and supervision should note that: Materials replacment specified in the contract document shall be made only with the approval of the supervisor if the material proposed to be replaced is the same or better than specified or if the materials of specified materials can not be brought on the construction site in time to complete the work of the Contract, due to conditions beyond the control of the Contractor. -
1940 FRENCH ARMAMENT by David Lehmann April 19, 2006
1 1939-1940 FRENCH ARMAMENT by David Lehmann April 19, 2006 NOTES ABOUT INFANTRY / CAVALRY UNITS INFANTRY There are many different types of infantry troops : ! Infantry ! Light infantry ! Light infantry, type Overseas ! Motorized infantry ! Mechanized infantry ! Mountain infantry ! Light mountain infantry ! North African infantry ! Colonial infantry And different types of infantry units : ! Infantry Brigade ! Metropolitan Infantry Regiment type "North-East" ! Metropolitan Infantry Regiment type "Overseas" ! Half-Brigade and Battalions of Chasseurs ! Zouave Infantry Regiment ! North African Tirailleurs Regiments ! Mountain Infantry Regiment ! Half-Brigade and Battalions of Alpine Chasseurs ! Pyrenean Half-Brigade and Battalions ! Motorized Infantry Regiment ! Mechanized Infantry Battalion ! Foreign Legion Regiment, Battalion, Half-Brigade, Brigade ! Half-Brigade and Battalions of Light Infantry ! Fortress Infantry Regiments ! Alpine Fortress Half-Brigades and Battalions ! Machine-gun Battalions Dragons portés "Dragons Portés" (Portés means roughly carried by a vehicle) is a motorized infantry kind of unit. The Dragons Portés were professional units of better morale, though few personnel had any combat experience (senior officers were often WW1, Poland and/or Rif war veterans though). They were the motorized infantry in the Division Légère Mécanique (DLM) and Division Légère de Cavalerie (DLC). The firepower of the squads was high since each was armed with two LMGs instead of only one for a typical infantry squad. The Dragons Portés squad was designed to cover a large ground area and as such during initial planning for these units (in the early 30's), each squad received 2 LMGs. At the beginning, all squads were equipped with 2 vehicles (Citroën-Kégresse P19) carrying each 1 LMG and 7 men : in fact 1 half-squad of 6 men + 1 driver. -
Durability of Fabric-Reinforced Cementitious Matrix (FRCM) Composites: a Review
applied sciences Review Durability of Fabric-Reinforced Cementitious Matrix (FRCM) Composites: A Review Karrar Al-Lami 1,2 , Tommaso D’Antino 1 and Pierluigi Colombi 1,* 1 ABC Department of Architecture, Built Environment and Construction Engineering, Politecnico di Milano, 20133 Milan, Italy; [email protected] (K.A.-L.); [email protected] (T.D.) 2 Civil Engineering Department, University of Wasit, Al-Rabee st, Wasit 00964, Iraq * Correspondence: [email protected]; Tel.: +39-02-2399-4280 Received: 15 January 2020; Accepted: 27 February 2020; Published: 2 March 2020 Abstract: Strengthening and rehabilitation of masonry and concrete structures by means of externally bonded fabric-reinforced cementitious matrix (FRCM) (also referred to as textile reinforced mortar (TRM)) composites was proposed as an alternative to the use of fiber-reinforced polymer (FRP) composites due to their good mechanical properties and compatibility with the substrate. However, quite limited studies are available in the literature regarding the long-term behavior of FRCM composites with respect to different environmental conditions. This paper presents a thorough review of the available researches on the long-term behavior of FRCM composites. Namely, (i) test set-ups employed to study the FRCM durability, (ii) conditioning environments adopted, and (iii) long-term performance of FRCM and its component materials (mortar and fiber textile) subjected to direct tensile and bond tests, are presented and discussed. Based on the available results, some open issues that need to be covered in future studies are pointed out. Keywords: fabric-reinforced cementitious matrix (FRCM); textile reinforced concrete (TRC); textile reinforced mortar (TRM); inorganic-matrix; open-mesh textile; long-term behavior 1. -
Redalyc.Analysis of the Properties of Masonry Mortars Made With
Revista de la Construcción ISSN: 0717-7925 [email protected] Pontificia Universidad Católica de Chile Chile Martínez, Iván; Etxeberria, Miren; Pavón, Elier; Díaz, Nelson Analysis of the properties of masonry mortars made with recycled fine aggregates for use as a new building material in Cuba Revista de la Construcción, vol. 15, núm. 1, abril, 2016, pp. 9-21 Pontificia Universidad Católica de Chile Santiago, Chile Available in: http://www.redalyc.org/articulo.oa?id=127646309001 How to cite Complete issue Scientific Information System More information about this article Network of Scientific Journals from Latin America, the Caribbean, Spain and Portugal Journal's homepage in redalyc.org Non-profit academic project, developed under the open access initiative Analysis of the properties of masonry mortars made with recycled fine aggregates for use as a new building material in Cuba Análisis de las propiedades de morteros de albañilería fabricados con áridos finos reciclados como un nuevo material de construcción en Cuba Iván Martínez (Main author) Instituto de Ingeniería, Universidad Nacional Autónoma de México, México DF, México. [email protected] Miren Etxeberria (Contact author) Departamento de Ingeniería Civil y Ambiental. Universidad Politécnica de Cataluña, Barcelona, España. C. Jordi Girona, 1-3, Módulo C1, CP: 08034, Barcelona, España. [email protected] Elier Pavón Centro de las Ciencias Exactas y de las Tecnologías, Universidad Federal del Oeste de Bahía, Brasil. [email protected] Nelson Díaz Departamento de Ingeniería Civil, Instituto Superior Politécnico José Antonio Echeverría, La Habana, Cuba. [email protected] Abstract This paper details the research work carried out on masonry mortars produced employing recycled aggregates in 100% substitution for natural sand aggregates. -
A Top Secret Program Hidden in Plain Sight
Follow the links – read the articles, pdf’s. Find out what’s really happening in your world… Why Microwave Auditory Effect Crowd-Control Gun Won't Work By Monica Heger First Published July 2008 Experts say you'd fry before you heard anything PHOTO: FRANCO VOGT/CORBIS 22 July 2008—New Scientist magazine recently reported that Sierra Nevada Corp., based in Sparks, Nevada, plans to build what it calls a nonlethal microwave ray gun with the ability to beam irritating sounds into people’s heads. But experts in the underlying biophysics say it cannot work: the device would kill you well before you were bothered by the noise. The gun, which is being built by Lev Sadovnik at Sierra Nevada, would take advantage of a phenomenon known as the microwave auditory effect. When microwaves are delivered in short pulses, the cochlear tissue in the ear expands. That expansion is heard as an audible click to anyone receiving the radiation, a sound much like that of two rocks being hit together underwater. The company says that the device, called MEDUSA (for “mob excess deterrent using silent audio”), could be used for crowd control. However, experts say the gun wouldn’t work as advertised. There is no way the ray gun could deliver sound loud enough to be annoying at nonfatal power levels, says Kenneth Foster, a bioengineering professor at the University of Pennsylvania who first published research on the microwave auditory effect in 1974. “Any kind of exposure you could give to someone that wouldn’t burn them to a crisp would produce a sound too weak to have any effect,” Foster says.