Reduction Kinetics of Uranium Trioxide to Uranium Dioxide Using Hydrogen
Total Page:16
File Type:pdf, Size:1020Kb
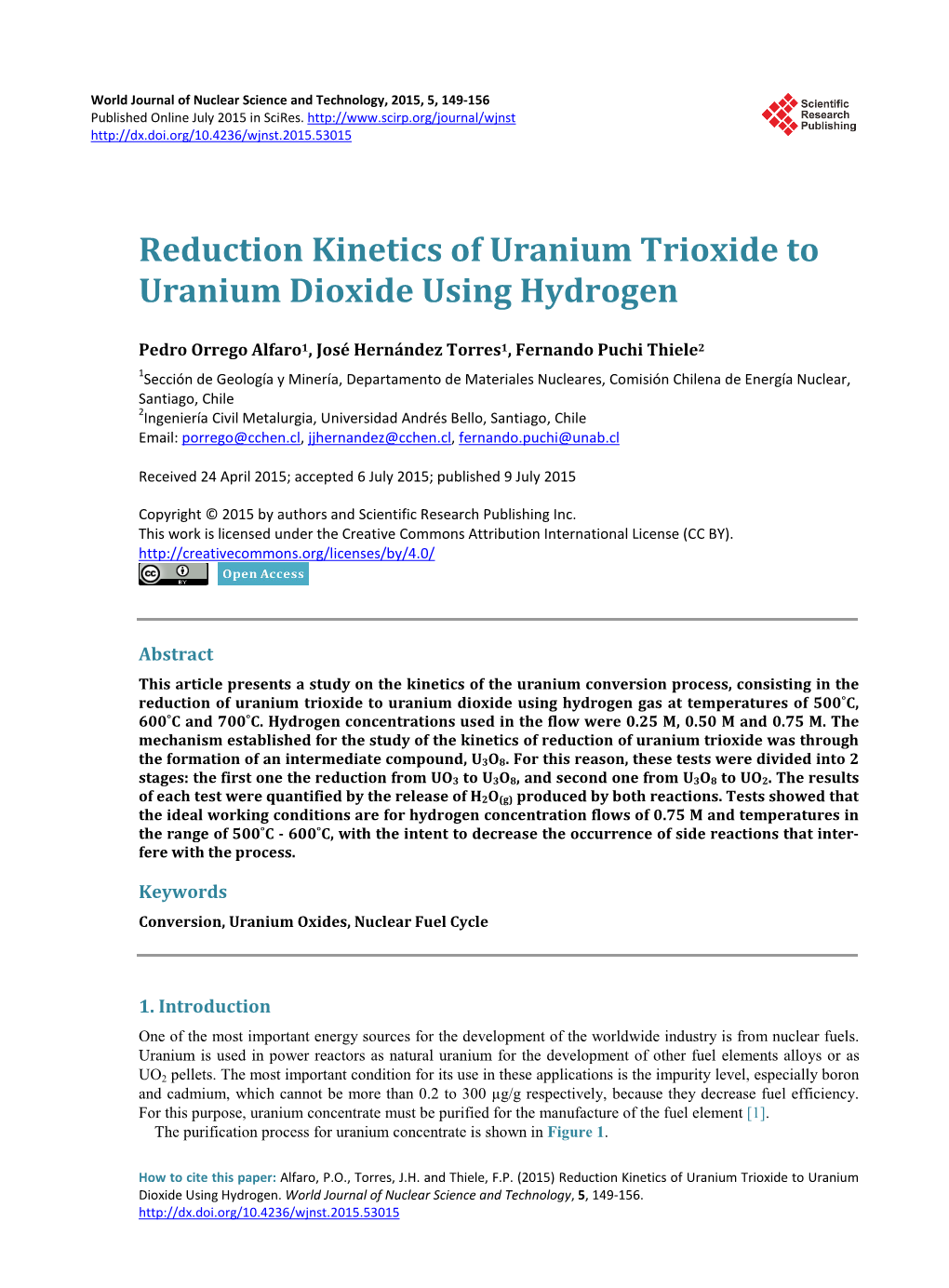
Load more
Recommended publications
-
Gas Phase Chemical Evolution of Uranium, Aluminum, and Iron Oxides Received: 22 January 2018 Batikan Koroglu1, Scott Wagnon 1, Zurong Dai1, Jonathan C
www.nature.com/scientificreports OPEN Gas Phase Chemical Evolution of Uranium, Aluminum, and Iron Oxides Received: 22 January 2018 Batikan Koroglu1, Scott Wagnon 1, Zurong Dai1, Jonathan C. Crowhurst1, Accepted: 19 June 2018 Michael R. Armstrong1, David Weisz1, Marco Mehl1,2, Joseph M. Zaug1, Harry B. Radousky1 & Published: xx xx xxxx Timothy P. Rose1 We use a recently developed plasma-fow reactor to experimentally investigate the formation of oxide nanoparticles from gas phase metal atoms during oxidation, homogeneous nucleation, condensation, and agglomeration processes. Gas phase uranium, aluminum, and iron atoms were cooled from 5000 K to 1000 K over short-time scales (∆t < 30 ms) at atmospheric pressures in the presence of excess oxygen. In-situ emission spectroscopy is used to measure the variation in monoxide/atomic emission intensity ratios as a function of temperature and oxygen fugacity. Condensed oxide nanoparticles are collected inside the reactor for ex-situ analyses using scanning and transmission electron microscopy (SEM, TEM) to determine their structural compositions and sizes. A chemical kinetics model is also developed to describe the gas phase reactions of iron and aluminum metals. The resulting sizes and forms of the crystalline nanoparticles (FeO-wustite, eta-Al2O3, UO2, and alpha-UO3) depend on the thermodynamic properties, kinetically-limited gas phase chemical reactions, and local redox conditions. This work shows the nucleation and growth of metal oxide particles in rapidly-cooling gas is closely coupled to the kinetically-controlled chemical pathways for vapor-phase oxide formation. Gas phase nucleation and growth of metal oxide nanoparticles is an important topic for many areas of chemistry, physics, material science, and engineering1–6. -
The Role of Pe, Ph, and Carbonate on the Solubility of UO2 and Uraninite Under Nominally Reducing Conditions
Geochimica et Cosmochimica Acta, Vol. 62, No. 13, pp. 2223–2231, 1998 Copyright © 1998 Elsevier Science Ltd Pergamon Printed in the USA. All rights reserved 0016-7037/98 $19.00 1 .00 PII S0016-7037(98)00140-9 The role of pe, pH, and carbonate on the solubility of UO2 and uraninite under nominally reducing conditions 1 1 1 1 2 2 3, IGNASI CASAS, JOAN DE PABLO, JAVIER GIMENEZ´ , M. ELENA TORRERO, JORDI BRUNO, ESTHER CERA, ROBERT J. FINCH, * and 3,† RODNEY C. EWING 1Department of Chemical Engineering, Polytechnic University of Catalunya, Barcelona 08028, Spain 2QuantiSci SL, Parc Tecnolo`gic del Valle`s, Cerdanyola 08290, Spain 3Department of Earth and Planetary Sciences, University of New Mexico, Albuquerque, New Mexico 87131, USA (Received August 14, 1997; accepted in revised form March 26, 1998) Abstract—Experimental data obtained from uranium dioxide solubility studies as a function of pH and under nominally reducing conditions in a 0.008 mol dm23 perchlorate medium and in a 1 mol dm23 chloride solution are presented. The solubility of extensively characterized uraninite samples from Cigar Lake (Canada), Jachymov (Czech Republic), and Oklo (Gabon) was determined in a solution matching the composition of a groundwater associated with granitic terrain. The redox potential of the test solution was monitored throughout the experimental period. The results obtained were modeled using aqueous formation constants compiled by the NEA, using stability constants corrected to appropriate ionic strengths. The solubility curves have been adjusted by calculating the 1 N value of Ks4 (UO2(s) 2H2O U(OH)4(aq)) that gave the best fit with the experimental data. -
Depleted Uranium Hexafluoride: Waste Or Resource?
UCRGJC-120397 PREPRINT Depleted Uranium Hexafluoride: Waste or Resource? N. Schwertz J. Zoller R Rosen S. Patton C. Bradley A. Murray This paper was prepared for submittal to the Global ‘95 International Conference on Evaluation of Emerging Nuclear Fuel Cycle Systems Versailles, France September 11-14,1995 July 1995 This isa preprint of apaper intended for publication in a jaurnal orproceedings. Since changes may be made before publication, this preprint is made available with the understanding that it will not be cited or reproduced without the permiasion of the anthor. DISCLAIMER This document was prepared as an account of work sponsored by an agency of the United Stat= Government. Neither theunited States Governmentmor theuniversity of California nor any oftheir employees, makes any warranty, express or implied, or assumesanylegalliabilityorrespomibility forthe accuracy,completeness,orusefuin~ of any information, apparatus, pduct, or process disdosed, or represents that its use wouldnotinfringe privatelyowned rights. Referencehemin to anyspe&c commercial prodocis, proms, or service by trade name, trademark, manufacturer, or otherwise, does not necessarily constituteor imply its endorsement, reconunendation, or favoring by the United States Government or the University of California. The views and opinions of authors expressed herein do not necessady state or reflect those of the United States Government or the University of California, and shall not be used for adveltising or product endorsement purposes. DISCLAIMER Portions of this document may be illegible in electronic image products. Images are produced from the best available original document . DEPLETED URANIUM HEXAFLUORIDE: WASTE OR RESOURCE? N. Schwertz, J. Zoller, R. Rosen, S. Patton LAWRENCE LIVERMORE NATIONAL LABORATORY P. -
Measurement of Uranium Dioxide Thermophysical Properties by the Laser Flash Method
2009 International Nuclear Atlantic Conference - INAC 2009 Rio de Janeiro,RJ, Brazil, September27 to October 2, 2009 ASSOCIAÇÃO BRASILEIRA DE ENERGIA NUCLEAR - ABEN ISBN: 978-85-99141-03-8 MEASUREMENT OF URANIUM DIOXIDE THERMOPHYSICAL PROPERTIES BY THE LASER FLASH METHOD Pablo Andrade Grossi 1, Ricardo Alberto Neto Ferreira 2, Denise das Mercês Camarano 3, Roberto Márcio de Andrade 4 1,2,3 Centro de Desenvolvimento da Tecnologia Nuclear-CDTN Comissão Nacional de Energia Nuclear-CNEN Av. Presidente Antônio Carlos 6627 Cidade Universitária-Pampulha-Caixa Postal 941 CEP: 31.161-970 Belo Horizonte, MG 1 [email protected] 2 [email protected] 3 [email protected] 4 Departamento de Engenharia Mecânica Escola de Engenharia da Universidade Federal de Minas Gerais Av. Presidente Antônio Carlos 6627-Cidade Universitária-Pampulha CEP: 31.270-901 - Belo Horizonte – MG - Brasil 4 [email protected] ABSTRACT The evaluation of the thermophysical properties of uranium dioxide (UO 2), including a reliable uncertainty assessment, are required by the nuclear reactor design. These important informations are used by thermohydraulic codes to define operational aspects and to assure the safety, when analyzing various potential situations of accident. The Laser Flash Method had become the most popular method to measure the thermophysical properties of materials. Despite its several advantages, some experimental obstacles have been found due to the difficulty to obtain experimentally the ideals initial and boundary conditions required by the original method. An experimental apparatus and a methodology for estimating uncertainties of thermal diffusivity, thermal conductivity and specific heat measurements based on the Laser Flash Method are presented. A stochastic thermal diffusion modeling has been developed and validated by Standard Samples. -
Molecular Characterization of Uranium(VI) Sorption Complexes on Iron(III)-Rich Acid Mine Water Colloids
Geochimica et Cosmochimica Acta 70 (2006) 5469–5487 www.elsevier.com/locate/gca Molecular characterization of uranium(VI) sorption complexes on iron(III)-rich acid mine water colloids Kai-Uwe Ulrich a,*, Andre´ Rossberg a,b, Harald Foerstendorf a, Harald Za¨nker a, Andreas C. Scheinost a,b a Institute of Radiochemistry, FZ Rossendorf e.V., P.O. Box 510119, D-01314 Dresden, Germany b Rossendorf Beamline at ESRF, B.P. 220, F-38043 Grenoble, France Received 7 November 2005; accepted in revised form 21 August 2006 Abstract A mixing of metal-loaded acid mine drainage with shallow groundwater or surface waters usually initiates oxidation and/or hydrolysis of dissolved metals such as iron (Fe) and aluminum (Al). Colloidal particles may appear and agglomerate with increasing pH. Likewise chemical conditions may occur while flooding abandoned uranium mines. Here, the risk assessment of hazards requires reliable knowl- edge on the mobility of uranium (U). A flooding process was simulated at mesocosm scale by mixing U-contaminated acid mine water with near-neutral groundwater under oxic conditions. The mechanism of U-uptake by fresh precipitates and the molecular structure of U bonding were determined to estimate the mobility of U(VI). Analytical and spectroscopic methods such as Extended X-ray Absorption Fine-Structure (EXAFS) spectroscopy at the Fe K-edge and the U LIII-edge, and Attenuated Total Reflectance Fourier Transform Infra- red (ATR-FTIR) spectroscopy were employed. The freshly formed precipitate was identified as colloidal two-line ferrihydrite. It removed U(VI) from solution by sorption processes, while surface precipitation or structural incorporation of U was not observed. -
Depleted Uranium Technical Brief
Disclaimer - For assistance accessing this document or additional information,please contact [email protected]. Depleted Uranium Technical Brief United States Office of Air and Radiation EPA-402-R-06-011 Environmental Protection Agency Washington, DC 20460 December 2006 Depleted Uranium Technical Brief EPA 402-R-06-011 December 2006 Project Officer Brian Littleton U.S. Environmental Protection Agency Office of Radiation and Indoor Air Radiation Protection Division ii iii FOREWARD The Depleted Uranium Technical Brief is designed to convey available information and knowledge about depleted uranium to EPA Remedial Project Managers, On-Scene Coordinators, contractors, and other Agency managers involved with the remediation of sites contaminated with this material. It addresses relative questions regarding the chemical and radiological health concerns involved with depleted uranium in the environment. This technical brief was developed to address the common misconception that depleted uranium represents only a radiological health hazard. It provides accepted data and references to additional sources for both the radiological and chemical characteristics, health risk as well as references for both the monitoring and measurement and applicable treatment techniques for depleted uranium. Please Note: This document has been changed from the original publication dated December 2006. This version corrects references in Appendix 1 that improperly identified the content of Appendix 3 and Appendix 4. The document also clarifies the content of Appendix 4. iv Acknowledgments This technical bulletin is based, in part, on an engineering bulletin that was prepared by the U.S. Environmental Protection Agency, Office of Radiation and Indoor Air (ORIA), with the assistance of Trinity Engineering Associates, Inc. -
Final Report
BNL-52661 Formal Report MECHANISMS OF RADIONUCLIDE-HYROXYCARBOXYLIC ACID INTERACTIONS FOR DECONTAMINATION OF METALLIC SURFACES A.J. FRANCIS, C.J. DODGE, AND J.B. GILLOW Brookhaven National Laboratory, Upton, NY 11973 G.P. HALADA AND C.R. CLAYTON Department of Materials Science, SUNY at Stony Brook, NY 11794 FINAL REPORT PROJECT PERIOD: 10/1/98 TO 9/30/01 PROJECT NUMBER: 64946 DISCLAIMER This report was prepared as an account of work sponsored by an agency of the United States Government. Neither the United State Government nor any agency thereof, nor any of their employees, not any of their contractors, subcontractors, or their employees, makes any warranty, express or implied, or assumes any legal liability or responsibility for the accuracy, completeness, or usefulness of any information, apparatus, product, or process disclosed, or represents that its use would not infringe privately owned rights. Reference herein to any specific commercial product, process, or service by trade name, trademark, manufacturer, or otherwise, does not necessarily constitute or imply its endorsement, recommendation, or favoring by the United States Government or any agency, contractor, or subcontractor thereof. The views and opinions of authors expressed herein do not necessarily state or reflect those of the United States Government or any agency, contractor or subcontractor thereof. MECHANISMS OF RADIONUCLIDE-HYROXYCARBOXYLIC ACID INTERACTIONS FOR DECONTAMINATION OF METALLIC SURFACES* A.J. FRANCIS, C.J. DODGE, AND J.B. GILLOW Brookhaven National Laboratory, Upton, NY 11973 G.P. HALADA AND C.R. CLAYTON Department of Materials Science, SUNY at Stony Brook, NY 11794 FINAL REPORT PROJECT PERIOD: 10/1/98 TO 9/30/01 PROJECT NUMBER: 64946 *This work was performed under the auspices of the U.S. -
High-Density Concrete with Ceramic Aggregate Based on Depleted Uranium Dioxide
HIGH-DENSITY CONCRETE WITH CERAMIC AGGREGATE BASED ON DEPLETED URANIUM DIOXIDE S.G. Ermichev, V.I. Shapovalov, N.V.Sviridov (RFNC-VNIIEF, Sarov, Russia) V.K. Orlov, V.M. Sergeev, A. G. Semyenov, A.M. Visik, A.A. Maslov, A. V. Demin, D.D. Petrov, V.V. Noskov, V. I. Sorokin, O. I. Uferov (VNIINM, Moscow, Russia) L. Dole (ORNL, Oak Ridge, USA) Abstract - Russia is researching the production and testing of concretes with ceramic aggregate based on depleted uranium dioxide (UO2). These DU concretes are to be used as structural and radiation-shielded material for casks for A-plant spent nuclear fuel transportation and storage. This paper presents the results of studies aimed at selection of ceramics and concrete composition, justification of their production technology, investigation of mechanical properties, and chemical stability. This Project is being carried out at the A.A. Bochvar All-Russian Scientific-Research Institute of inorganic materials (VNIINM, Russia) and Russian Federal Nuclear Center – All-Russia Scientific Research Institute of Experimental Physics (RFNC-VNIIEF, Russia). This Project #2691 is financed by the International Science and Technology Center (ISTC) under collaboration of the Oak- Ridge National Laboratory (USA) I. INTRODUCTION The current practice of ensuring the required gamma conduction, thermo-, radiation and corrosion resistance, shielding and strength of metal-concrete casks is based on service life and water resistance. concrete density. For this purpose high-density rocks Specific characteristics of UO2’s chemical activity (magnetite, iron glance, barium sulfate, etc.) as well as because of its small size of particles and thus great specific scrap, scale, broken metal chips and others are introduced surface area prevent the use of traditional methods of UO2 into concrete as coarse aggregates. -
I -F??TI O08'w –Gçanooog –Ggan
Feb. 27, 1962 L. BURRIS, JR., ETA 3,023,097 REPROCESSING URANIUM DIOXDE FUES Filed Nov. 23, 1959 2 Sheets-Sheet I-F??TI OOOG–ggan O08’w–gçan no?opa8 (g?20%OG) INVENTOR. Les lie 8urris, Jr. Af r e di S c h n e i der Attorney Feb. 27, 1962 L. BURRIS, JR., ETA 3,023,097 REPROCESSING URANIUM DIOXDE FUELS Filed Nov. 23, 1959 2 Sheets-Sheet 2 - 4O - 5 ? - 6 O - 8O - 9 O - OO - , ? - 2 O - 3 O Nd 2O Gnd Sm2O3 - 4 O - 150 Pr2O3 and Ce2O3 O 3OO 5OO IOOO 5OO 2OOO 25 OO Temperature (K) F I Leslie Burris,INVENTOR. Jr. Alfred Schneid er BY ????? C???-e Attorney - 3,023,097 United States Patent Office Patented Feb. 27, 1962 2 of the dioxide fuel and its commingled substances in prep 3,323,097 aration for the next step about to be described; this size REPROCESSING GUARNUM DIXE FUELS Lesie Burris, Jr., and Alfred Schneider, Naperville, H., reduction is best carried out by successive oxidations and aSsigi nors to the United States of America as rere reductions which cause crumbling by reason of the suc sented by the United States Atomic Energy Cons cessive changes in crystal structure. After the particle ?$$??? size has been reduced sufficiently, a molten reducing i Fied Nov. 23, 1959, Ser. No. 854,989 metal of the group consisting of zinc and cadmium is 4 Claims. (C. 75-84.) introduced to the crumbled mixture, and this causes quite a number of metals to go into the metallic state, where The invention relates to a novel pyrometalurgical O upon they alloy with the reducing metal and the molten method of reprocessing uranium dioxide fuels after they metal phase may then be separated from the solid oxide have become contaminated by ª fission products in i nu phase consisting of the oxides of metals such as uranium, clear reactors, and more particularly, to a novel method rare earths and plutonium which are still not reduced. -
Dissolution of Uranium Dioxide in Nitric Acid Media: What Do We Know?
EPJ Nuclear Sci. Technol. 3, 13 (2017) Nuclear © Sciences P. Marc et al., published by EDP Sciences, 2017 & Technologies DOI: 10.1051/epjn/2017005 Available online at: http://www.epj-n.org REGULAR ARTICLE Dissolution of uranium dioxide in nitric acid media: what do we know? Philippe Marc1, Alastair Magnaldo1,*, Aimé Vaudano1, Thibaud Delahaye2, and Éric Schaer3 1 CEA, Nuclear Energy Division, Research Department of Mining and Fuel Recycling Processes, Service of Dissolution and Separation Processes, Laboratory of Dissolution Studies, 30207 Bagnols-sur-Cèze, France 2 CEA, Nuclear Energy Division, Research Department of Mining and Fuel Recycling Processes, Service of Actinides Materials Fabrication, Laboratory of Actinide Conversion Processes, 30207 Bagnols-sur-Cèze, France 3 Laboratoire Réactions et Génie des Procédés, UMR CNRS 7274, University of Lorraine, 54001 Nancy, France Received: 16 March 2016 / Received in final form: 15 November 2016 / Accepted: 14 February 2017 Abstract. This article draws a state of knowledge of the dissolution of uranium dioxide in nitric acid media. The chemistry of the reaction is first investigated, and two reactions appear as most suitable to describe the mechanism, leading to the formation of monoxide and dioxide nitrogen as reaction by-products, while the oxidation mechanism is shown to happen before solubilization. The solid aspect of the reaction is also investigated: manufacturing conditions have an impact on dissolution kinetics, and the non-uniform attack at the surface of the solid results in the appearing of pits and cracks. Last, the existence of an autocatalytic mechanism is questionned. The second part of this article presents a compilation of the impacts of several physico-chemical parameters on the dissolution rates. -
Inis: Terminology Charts
IAEA-INIS-13A(Rev.0) XA0400071 INIS: TERMINOLOGY CHARTS agree INTERNATIONAL ATOMIC ENERGY AGENCY, VIENNA, AUGUST 1970 INISs TERMINOLOGY CHARTS TABLE OF CONTENTS FOREWORD ... ......... *.* 1 PREFACE 2 INTRODUCTION ... .... *a ... oo 3 LIST OF SUBJECT FIELDS REPRESENTED BY THE CHARTS ........ 5 GENERAL DESCRIPTOR INDEX ................ 9*999.9o.ooo .... 7 FOREWORD This document is one in a series of publications known as the INIS Reference Series. It is to be used in conjunction with the indexing manual 1) and the thesaurus 2) for the preparation of INIS input by national and regional centrea. The thesaurus and terminology charts in their first edition (Rev.0) were produced as the result of an agreement between the International Atomic Energy Agency (IAEA) and the European Atomic Energy Community (Euratom). Except for minor changesq the terminology and the interrela- tionships btween rms are those of the December 1969 edition of the Euratom Thesaurus 3) In all matters of subject indexing and ontrol, the IAEA followed the recommendations of Euratom for these charts. Credit and responsibility for the present version of these charts must go to Euratom. Suggestions for improvement from all interested parties. particularly those that are contributing to or utilizing the INIS magnetic-tape services are welcomed. These should be addressed to: The Thesaurus Speoialist/INIS Section Division of Scientific and Tohnioal Information International Atomic Energy Agency P.O. Box 590 A-1011 Vienna, Austria International Atomic Energy Agency Division of Sientific and Technical Information INIS Section June 1970 1) IAEA-INIS-12 (INIS: Manual for Indexing) 2) IAEA-INIS-13 (INIS: Thesaurus) 3) EURATOM Thesaurusq, Euratom Nuclear Documentation System. -
Experimental Studies of Neutron Irradiated Uranium Dioxide at High Temperatures
NL90C1051 lNIS-mi— 12739 Experimental studies of neutron irradiated uranium dioxide at high temperatures R.H.J. Tanke EXPERIMENTAL STUDIES OF NEUTRON IRRADIATED URANIUM DIOXIDE AT HIGH TEMPERATURES EXPERIMENTELE STUDIES VAN MET NEUTRONEN BESTRAALD URANIUMDIOXIDE BIJ HOGE TEMPERATUREN (met een samenvatting in het Nederlands) PROEFSCHRIFT TER VERKRIJGING VAN DE GRAAD VAN DOCTOR AAN DE RIJKSUNIVERSITEIT TE UTRECHT, OP GEZAG VAN DE RECTOR MAGNIFICUS PROF.DR. J.A. VAN GÏNKEL, VOLGENS BESLUIT VAN HET COLLEGE VAN DEKANEN IN HET OPENBAAR TE VERDEDIGEN OP WOENSDAG 20 JUNI 1990 DES NAMIDDAGS TE 4.15 UUR. door Richardus Hendrikus Johannes Tanke geboren op 19 april 1957 te Hengelo (O) Promotor: Prof.Dr. CD. Andriesse Aan Pien CIP-GEGEVENS KONINKLIJKE BIBLIOTHEEK DEN HAAG Tanke, Richardus Hend. ^kus Johannes Experimental studies of neutron irradiated uranium dioxide at high temperatures / Richardus Hendrikus Johannes Tanke. - Arnhem : KEMA. - 111. Thesis Utrecht. - With index, ref. - With summary in Dutch. ISBN 90-353-1023-3 pbk. ISBN 90-353-1024-1 geb. SISO 538 UDC [539.125.06:546.791-31:536.45](043.3) Subject headings: uranium dioxide / gamma tomography. Contents Summary and outline 7 Outline of this thesis 9 Chapter 1: Introduction 11 The safety issue during the development of nuclear power 11 Experimental programmes on the release of fission products 15 from overheated fuel The KEMA source term experiment 17 References 18 Chapter 2: Experimental equipment and laboratory facilities 21 The hot cell 23 Measurement equipment for the evaporation experiment