Industrial Waste Heat Recovery: Potential Applications, Available Technologies and Crosscutting R&D Opportunities
Total Page:16
File Type:pdf, Size:1020Kb
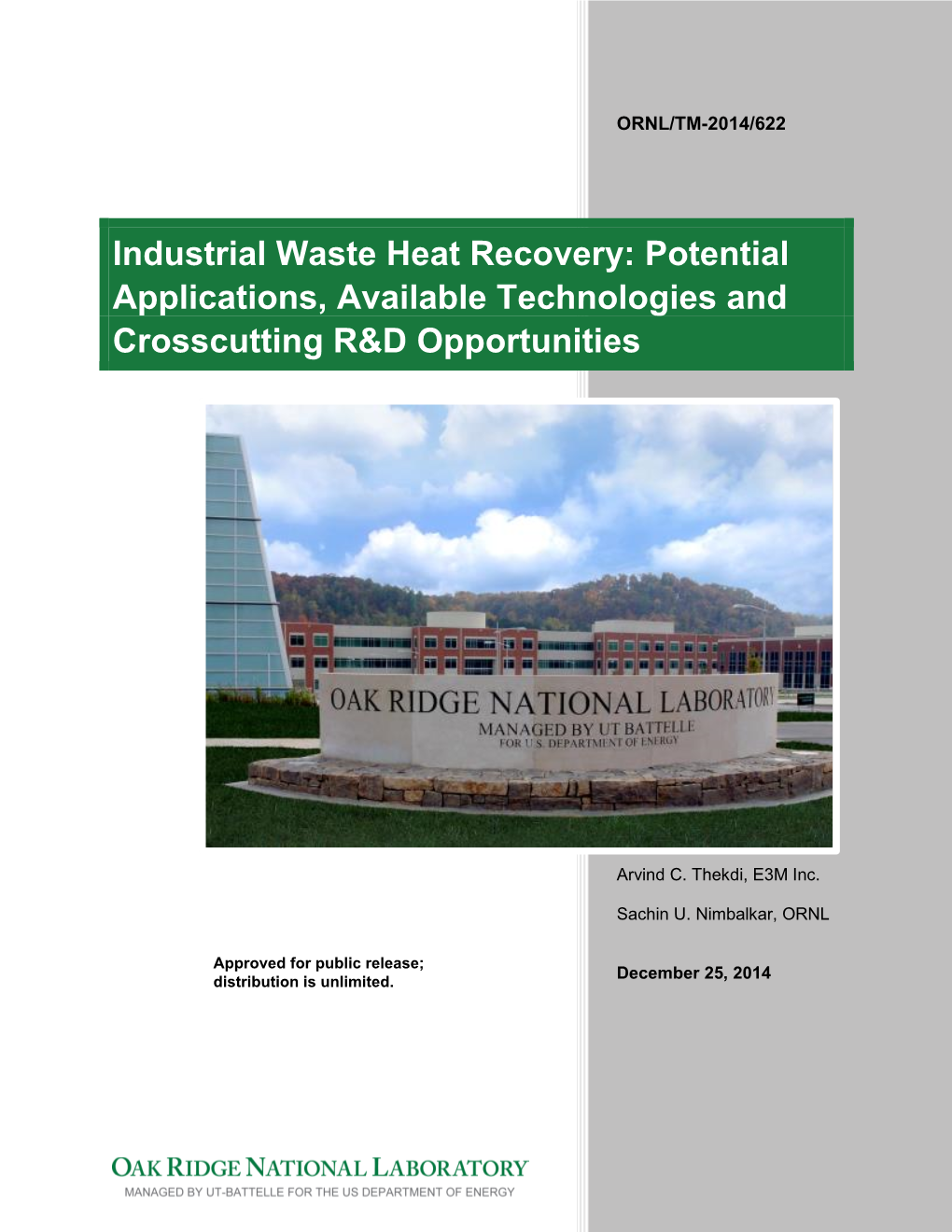
Load more
Recommended publications
-
Advanced Heat Pump Systems Using Urban Waste Heat “Sewage Heat”
Mitsubishi Heavy Industries Technical Review Vol. 52 No. 4 (December 2015) 80 Advanced Heat Pump Systems Using Urban Waste Heat “Sewage Heat” YOSHIE TOGANO*1 KENJI UEDA*2 YASUSHI HASEGAWA*3 JUN MIYAMOTO*1 TORU YAMAGUCHI*4 SEIJI SHIBUTANI*5 The application of heat pumps for hot water supply and heating systems is expected. Through this, the energy consumption of hot water supply and heating, which account for a substantial proportion of the total energy consumption in a building, will be reduced. The level of reduction can be dramatically increased by use of "sewage heat," which is part of waste heat in an urban area. So far, however, it has been difficult to determine whether sufficient technical or basic data available to widely use sewage heat exists. Therefore, demonstrations on the evaluation method for the potential of sewage heat in an urban area and the actual- equipment scale of verification using untreated sewage were conducted to understand the characteristics of sewage heat, and major technologies for use of sewage heat were developed. The technologies were applied to the system using sewage heat, and the system achieved a 29% reduction in the annual energy consumption and a 69% reduction in the running cost in the hot water system in lodging facilities compared to the conventional system using a boiler. The depreciation timespan of the difference in the initial cost between the conventional system and the heat pump system is about four years, and this system has an economically large advantage. In this report, the results obtained through the development and the demonstrations are systematically organized and the technical information needed for introduction of use of sewage heat is provided. -
Energy Recovery from Waste Incineration—The Importance of Technology Data and System Boundaries on CO2 Emissions
energies Article Energy Recovery from Waste Incineration—The Importance of Technology Data and System Boundaries on CO2 Emissions Ola Eriksson 1,* and Göran Finnveden 2 1 Faculty of Engineering and Sustainable Development, Department of Building, Energy and Environmental Engineering, University of Gävle, SE 801 76 Gävle, Sweden 2 Division of Environmental Strategies Research–fms, Department of Sustainable Development, Environmental Sciences and Engineering (SEED), School of Architecture and the Built Environment, KTH Royal Institute of Technology, SE 100 44 Stockholm, Sweden; goran.fi[email protected] * Correspondence: [email protected]; Tel.: +46-26-648145 Academic Editor: George Kosmadakis Received: 19 October 2016; Accepted: 12 April 2017; Published: 15 April 2017 Abstract: Previous studies on waste incineration as part of the energy system show that waste management and energy supply are highly dependent on each other, and that the preconditions for the energy system setup affects the avoided emissions and thereby even sometimes the total outcome of an environmental assessment. However, it has not been previously shown explicitly which key parameters are most crucial, how much each parameter affects results and conclusions and how different aspects depend on each other. The interconnection between waste incineration and the energy system is elaborated by testing parameters potentially crucial to the result: design of the incineration plant, avoided energy generation, degree of efficiency, electricity efficiency in combined heat and power plants (CHP), avoided fuel, emission level of the avoided electricity generation and avoided waste management. CO2 emissions have been calculated for incineration of 1 kWh mixed combustible waste. The results indicate that one of the most important factors is the electricity efficiency in CHP plants in combination with the emission level of the avoided electricity generation. -
A Brief Research Review on the Anaerobic Digestion of Food Waste
March 20, 2019 A brief research review on the anaerobic digestion of food waste Setting the ground work for pilot testing Bryan Berdeen OREGON STATE UNIVERSITY – AEC 406 Table of Contents ABSTRACT .................................................................................................................................... 1 INTRODUCTION ........................................................................................................................... 3 PROJECT STATEMENT & APPROACH ........................................................................................... 6 LITERATURE REVIEW ................................................................................................................... 7 SIGNIFICANCE and POLICY/BUSINESS IMPLICATIONS ............................................................... 10 CONCLUSIONS ........................................................................................................................... 11 BIBLIOGRAPHY .......................................................................................................................... 12 I ABSTRACT The increase in regulations in certain state and local governments is requiring landfills to divert organic material to other more environmentally sustainable options is creating markets for the reuse of this organic material before it can enter local landfills. According to the EPA the anaerobic digestion of food waste (ADFW) is the only carbon negative process when dealing with the post-consumer use of food waste. Other landfill -
Waste Heat Recovery in Diesel Engines Using the Organic Rankine
DF Waste Heat Recovery in Diesel Engines using the Organic Rankine Cycle Potential of Heat Recovery in the Volvo D13 Engine for Marine and Standby Power Generation Applications ANIL GOPINATH BHARADWAJ WAEL AL HAJI Department of Mechanics and Maritime Sciences, CHALMERS UNIVERSITY OF TECHNOLOGY Gothenburg, Sweden 2020 Master’s thesis in Automotive Engineering Waste Heat Recovery in Diesel Engines using the Organic Rankine Cycle Anil Gopinath Bharadwaj Wael Al Haji DF Department of Mechanics and Maritime Sciences Division of Combustion and Propulsion Systems Chalmers University of Technology Gothenburg, Sweden 2020 Waste Heat Recovery in Diesel Engines using the Organic Rankine Cycle ANIL GOPINATH BHARADWAJ WAEL AL HAJI © ANIL GOPINATH BHARADWAJ, WAEL AL HAJI, 2020 Examiner: Sven B Andersson, Prof. Division of Combustion and Propulsion Sys- tems, Chalmers University of Technology Supervisors: Jelmer Rijpkema, Chalmers University of Technology; Patrik Land- berg, Volvo Penta AB; Björn Wessman, Volvo Penta AB; Master’s Thesis in Automotive Engineering Department of Mechanics and Maritime Sciences Division of Combustion and Propulsion Systems Chalmers University of Technology SE-412 96 Gothenburg Telephone +46 31 772 1000 Cover: Pictures showcasing the engine which WHR system is used for, operating points of interest and a T-s diagram of cyclopentane. Printed by Department of Mechanics and Maritime Sciences Gothenburg, Sweden 2020 iv Waste Heat Recovery in Diesel Engines using the Organic Rankine Cycle Potential of Heat Recovery in the Volvo D13 Engine for Marine and Standby Power Generation Applications Thesis for the degree of Masters in Automotive Engineering/Marine Engineering ANIL GOPINATH BHARADWAJ, WAEL AL HAJI Department of Mechanics and Maritime Sciences, Division of Combustion and Propulsion Systems Chalmers University of Technology Abstract The current global warming situation and various other environmental challenges call for innovative and easy-to-implement technologies to help counter the effect. -
2017-Smith-Aber-Applied-Energy
Applied Energy 211 (2018) 194–199 Contents lists available at ScienceDirect Applied Energy journal homepage: www.elsevier.com/locate/apenergy Energy recovery from commercial-scale composting as a novel waste MARK management strategy ⁎ Matthew M. Smitha, , John D. Aberb a University of New Hampshire Department of Natural Resources, 105 Main Street (Nesmith Hall 222), Durham, NH 03824, USA b University of New Hampshire Department of Natural Resources, 105 Main Street (Nesmith Hall 126), Durham, NH 03824, USA HIGHLIGHTS GRAPHICAL ABSTRACT • Energy recovery rates from a com- mercial-scale composting facility are presented. • Compost vapor between 51 and 66 °C resulted in recovery rates of 17,700–32,940 kJ/h. • Energy recovery was directly related to compost vapor and heat sink tem- peratures. • Temperature lag times between in- itiation of aeration and system equili- brium existed. • Temperature lag times warrant unique aeration schedules to maximize en- ergy recovery. ARTICLE INFO ABSTRACT Keywords: This study reports operational information from a commercial-scale Aerated Static Pile (ASP) composting system Compost energy recovery with energy recovery, one of the few currently in operation globally. A description of this innovative system is Aerated static pile composting followed by operational data on energy capture efficiency for 17 experimental trials with variable compost vapor Compost heat recovery and heat sink temperatures. Energy capture was directly and predictably related to the differential between Alternative energy compost vapor and heat sink temperatures, with energy capture ranging from 17,700 to 32,940 kJ/h with a Waste to energy compost vapor temperature range of 51–66 °C. A 5-day temperature lag time existed between compost pile formation, and when compost vapor temperatures were sufficiently high for energy recovery (≥50 °C). -
A Customer Guide to Combined Heat and Power
A Customer Guide to Combined Heat and Power A product of the Energy Solutions Center Inc. 400 North Capitol St. NW Commercial Buildings Consortium Washington, DC 20001 Energy Solutions Center Inc. www.ESCenter.org Table of Contents Available Resources www.understandingCHP.com What is Combined Heat & Power 1 www.GasAirConditioning.com Prime Movers 3 Reciprocating Engines 4 U.S. Department of Energy and FEMP https://www.energy.gov/eere/amo/combined-heat- Combustion Turbines 5 and-power-basics https://www.energy.gov/eere/femp/federal-energy- Micro Turbines 6 management-program CHP Installation database: Steam Turbines 7 https://doe.icfwebservices.com/chpdb/ Fuel Cells 8 U.S. Environmental Protection Agency (EPA) https://www.epa.gov/chp Micro CHP 9 Policies & Incentives Database: https://www.epa.gov/chp/dchpp-chp-policies-and- Waste Heat Recovery 10 incentives-database Site vs. Source 12 Environmental Benefits 13 Economics 15 Available Resources 18 What is Combined Heat & Power Combined Heat and Power (CHP) by definition is the generation of two forms of energy from one common source of fuel also known as Cogeneration. Waste Heat Heat & Hot Water Recovered Fuel Prime Mover Electricity & Generator The CHP system is typically located at or near your building and generates electricity or mechanical power with the added benefit of recovering the waste heat in the form of hot water, steam, or warm Spark spread is the relative difference between the price of fuel and air to meet thermal needs. This high quality and very reliable power the price of power. Spark spread is highly dependent on the system provides a secure energy source along with the ability to efficiency of conversion. -
Waste Heat Recovery Technology Assessment
Quadrennial Technology Review 2015 Chapter 6: Innovating Clean Energy Technologies in Advanced Manufacturing Technology Assessments Additive Manufacturing Advanced Materials Manufacturing Advanced Sensors, Controls, Platforms and Modeling for Manufacturing Combined Heat and Power Systems Composite Materials Critical Materials Direct Thermal Energy Conversion Materials, Devices, and Systems Materials for Harsh Service Conditions Process Heating Process Intensification Roll-to-Roll Processing Sustainable Manufacturing - Flow of Materials through Industry Waste Heat Recovery Systems Wide Bandgap Semiconductors for Power Electronics U.S. DEPARTMENT OF ENERGY Quadrennial Technology Review 2015 Waste Heat Recovery Systems Chapter 6: Technology Assessments NOTE: This technology assessment is available as an appendix to the 2015 Quadrennial Technology Review (QTR). Waste Heat Recovery Systems is one of fourteen manufacturing-focused technology assessments prepared in support of Chapter 6: Innovating Clean Energy Technologies in Advanced Manufacturing. For context within the 2015 QTR, key connections between this technology assessment, other QTR technology chapters, and other Chapter 6 technology assessments are illustrated below. Representative Intra-Chapter Connections Representative Extra-Chapter Connections CHP: heat recovery in CHP systems Sustainable Manufacturing: optimization of heat flows to maximize production intensity and minimize waste heat losses Electric Power: waste heat recovery Direct Thermal Energy Conversion: novel energy -
A Waste Heat Recovery Strategy for an Integrated Steelworks
A Waste Heat Recovery Strategy for An Integrated Steelworks By Christopher Lloyd Williams Thesis submitted to the Cardiff University in fulfilment of the requirements for the degree of Doctor of Philosophy. School of Engineering Cardiff University December 2015 Summary UK energy prices have doubled over the last decade, which has driven the UK Iron and Steel Industry to invest in energy efficient technologies. However, even with these relatively high prices the industry still finds it difficult to build a business case to justify waste heat recovery projects. The Steel Industry has large quantities of waste heat and there are technologies readily available for its capture, but often the issue has been finding a cost effective ‘end use’. Individual schemes incorporating both capturing and an ‘end use’ for the waste heat often incur high capital costs with resulting long payback times. This thesis defines the development and modelling of a strategy and methodology for the utilisation of waste heat recovery in a UK based Steelworks. The methodology involves the utilisation of the existing steam distribution circuit to link the possible waste heat schemes together with a single ‘end user’ thus limiting the capital requirement for each subsequent project. The thesis defines the development of a numerical model that is initially verified through extensive comparison to actual plant data from a series of pre-defined operational scenarios. The model is used to predict the pressure and temperature effects on the steam distribution system as the waste heat recovery boilers from various areas of the case study steelworks are connected up to it. -
Landfill Gas (LFG) Electricity Project with Waste Heat Recovery and Utilization Project Organization
Gundersen Health System & La Crosse County, Wisconsin Landfill Gas (LFG) Electricity Project with Waste Heat Recovery and Utilization Project Organization LFG Conditioning, LFG Electricity, Waste Heat Recovery, and Compression, Utilization & Pipeline General Contractor: Engineer-Procure-Construct Contractor: McHugh Excavating & Plumbing, Inc. Gundersen Health System • Mission: We distinguish ourselves through excellence in patient care, education, research, and improved health in the communities we serve • GL Health System – Currently have 41 clinic facilities – 325 bed tertiary care hospital – Physician-led Integrated delivery system • ~700 providers and ~6,500 employees – Residency and medical education programs – Multiple Top 100 Hospital & Service Line recognition – Health Plan – A variety of affiliate organizations including EMS ambulance service, rural hospitals, nursing homes, hospice, etc. Primary Objective • Energy Independence by 2014 - Produce more power than Gundersen consumes from fossil fuel sources – Makes our healthcare delivery more affordable to patients – Benefits human health – Strengthens our regional economy – Improves our environment 4 Why Health Care Providers Should Care • Pollutants from the burning of fossil fuels cause: – Cancer, liver disease, kidney disease, reproductive issues – Cardiovascular deaths and stroke1 • According to the Department of Energy, hospitals are 2.5 times more energy intensive than other commercial buildings2 – This is inconsistent with our mission… we are responsible for contributing -
Design and Experimental Study of HTSG for Waste to Energy: Analysis of Pressure Difference
energies Article Design and Experimental Study of HTSG for Waste to Energy: Analysis of Pressure Difference Jeachul Jang ID , Sunhee Oh, Chongpyo Cho and Seong-Ryong Park * ID Energy Efficiency and Materials Research Division, Korea Institute of Energy Research (KIER), Daejeon 34129, Korea; [email protected] (J.J.); [email protected] (S.O.); [email protected] (C.C.) * Correspondence: [email protected]; Tel.: +82-42-860-3224 Received: 18 June 2018; Accepted: 5 July 2018; Published: 11 July 2018 Abstract: The purpose of the present study is to analyze pressure difference changes inside a high-temperature steam generator (HTSG), which produces steam using the heat generated by waste incineration and decreases the pressure of the produced steam while increasing its temperature. The high-temperature, low-pressure steam produced by a HTSG is used for hydrogen production. Therefore, the steam temperature must be at least 700 ◦C, and the pressure must be lower than 300 kPa; hence, a device is needed to increase the steam temperature in the boiler and decrease the steam pressure. The physical behavior of the device was modeled and experimentally validated. The modeling and experimental results demonstrated good agreement when the steam was not preheated; however, an additional pressure drop required consideration of the opposite case. Keywords: high-temperature steam generator (HTSG); superheater; waste to energy (WtE); sudden effect; pressure difference 1. Introduction Waste to energy (WtE) has the advantages of reducing waste and transforming the energy obtained during incineration to a new form of useful energy [1]. In addition, the waste heat that is dissipated during incineration can be used to generate steam in a waste heat boiler, which can then be used directly or supplied to a turbine for power generation [2,3]. -
(WTE) Options and Solid Waste Export Considerations
Waste-to-Energy (WTE) Options and Solid Waste Export Considerations Prepared for King County Solid Waste Division 201 S. Jackson Street, Suite 701 Seattle, WA 98104 Prepared by Normandeau Associates, Inc. 1904 Third Avenue, Suite 1010 Seattle, WA 98101 www.normandeau.com in conjunction with CDM Smith Inc. and 14432 SE Eastgate Way, Suite 100 Neomer Resources LLC Bellevue, WA 98007 12623 SE 83rd Court Newcastle, WA 98056 September 28, 2017 Waste-to-Energy (WTE) Options and Solid Waste Export Considerations Contents List of Figures .......................................................................................................... iv List of Tables ............................................................................................................. v Acronyms and Abbreviations ................................................................................... vi Executive Summary .............................................................................................. viii 1 Introduction ........................................................................................................1 1.1 Modern WTE Trends and Advancements .......................................................................1 1.2 WTE Evaluation Criteria ...............................................................................................2 1.3 Preliminary WTE Sizing and Plant Configuration for King County’s Waste Projection .......................................................................................................................2 -
Waste to Energy in the Age of the Circular Economy Best Practice Handbook
WASTE TO ENERGY IN THE AGE OF THE CIRCULAR ECONOMY BEST PRACTICE HANDBOOK NOVEMBER 2020 ASIAN DEVELOPMENT BANK WASTE TO ENERGY IN THE AGE OF THE CIRCULAR ECONOMY BEST PRACTICE HANDBOOK NOVEMBER 2020 ASIAN DEVELOPMENT BANK Creative Commons Attribution 3.0 IGO license (CC BY 3.0 IGO) © 2020 Asian Development Bank 6 ADB Avenue, Mandaluyong City, 1550 Metro Manila, Philippines Tel +63 2 8632 4444; Fax +63 2 8636 2444 www.adb.org Some rights reserved. Published in 2020. ISBN: 978-92-9262-480-4 (print); 978-92-9262-481-1 (electronic); 978-92-9262-482-8 (ebook) Publication Stock No. TIM200330-2 DOI: http://dx.doi.org/10.22617/TIM200330-2 The views expressed in this publication are those of the authors and do not necessarily reflect the views and policies of the Asian Development Bank (ADB) or its Board of Governors or the governments they represent. ADB does not guarantee the accuracy of the data included in this publication and accepts no responsibility for any consequence of their use. The mention of specific companies or products of manufacturers does not imply that they are endorsed or recommended by ADB in preference to others of a similar nature that are not mentioned. By making any designation of or reference to a particular territory or geographic area, or by using the term “country” in this document, ADB does not intend to make any judgments as to the legal or other status of any territory or area. This work is available under the Creative Commons Attribution 3.0 IGO license (CC BY 3.0 IGO) https://creativecommons.org/licenses/by/3.0/igo/.