Estimation of Scour Depth at Bridge Abutments Nchrp 24-20
Total Page:16
File Type:pdf, Size:1020Kb
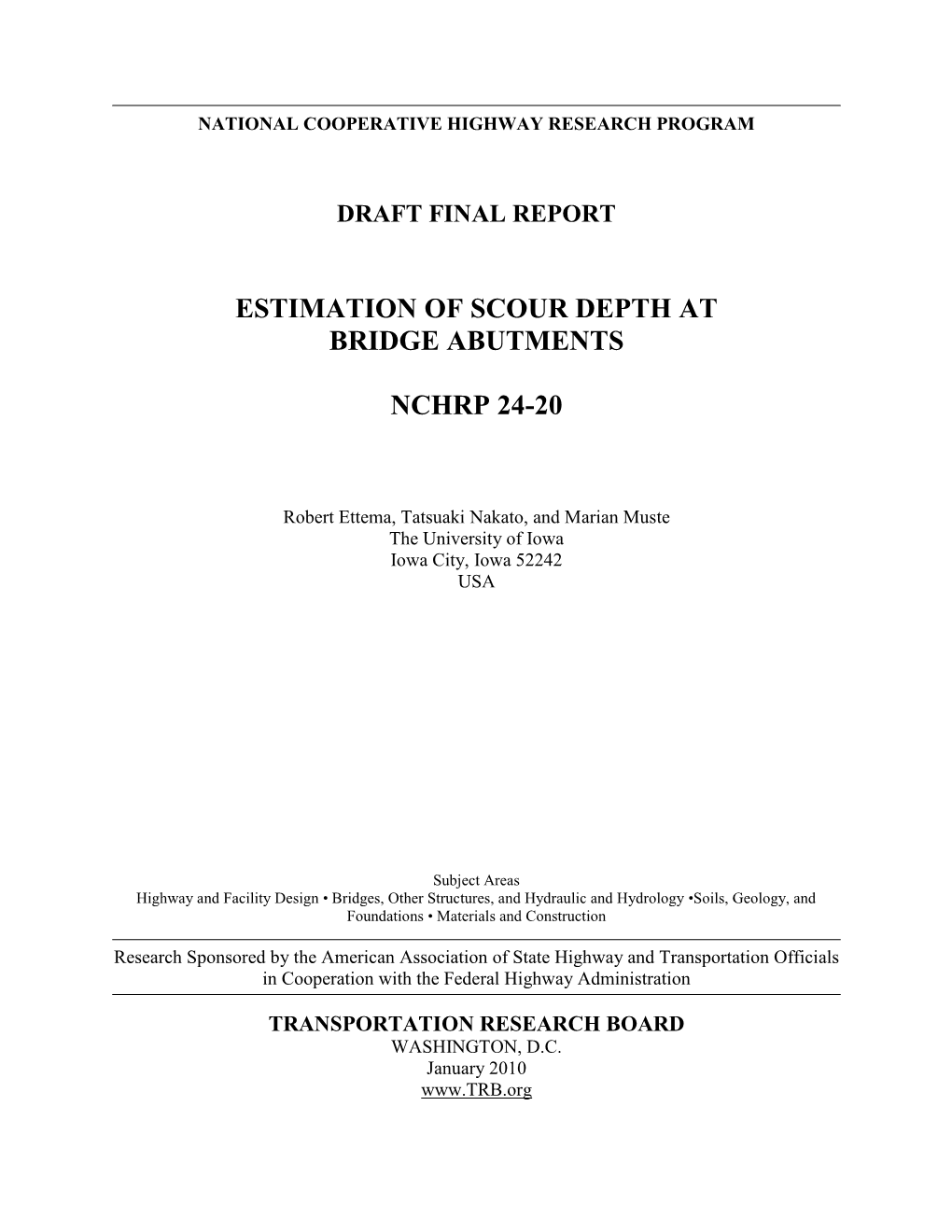
Load more
Recommended publications
-
The Science Behind Scour at Bridge Foundations: a Review
water Review The Science behind Scour at Bridge Foundations: A Review Alonso Pizarro 1,* , Salvatore Manfreda 1,2 and Enrico Tubaldi 3 1 Department of European and Mediterranean Cultures, University of Basilicata, 75100 Matera, Italy; [email protected] 2 Department of Civil, Architectural and Environmental Engineering, University of Naples Federico II, via Claudio 21, 80125 Napoli, Italy 3 Department of Civil and Environmental Engineering, University of Strathclyde, 75 Montrose Street, Glasgow G1 1XJ, UK; [email protected] * Correspondence: [email protected]; Tel.: +44-7517-865-662 Received: 14 December 2019; Accepted: 22 January 2020; Published: 30 January 2020 Abstract: Foundation scour is among the main causes of bridge collapse worldwide, resulting in significant direct and indirect losses. A vast amount of research has been carried out during the last decades on the physics and modelling of this phenomenon. The purpose of this paper is, therefore, to provide an up-to-date, comprehensive, and holistic literature review of the problem of scour at bridge foundations, with a focus on the following topics: (i) sediment particle motion; (ii) physical modelling and controlling dimensionless scour parameters; (iii) scour estimates encompassing empirical models, numerical frameworks, data-driven methods, and non-deterministic approaches; (iv) bridge scour monitoring including successful examples of case studies; (v) current approach for assessment and design of bridges against scour; and, (vi) research needs and future avenues. Keywords: scour; bridge foundations; Natural Hazards; floods 1. Introduction “If a builder builds a house for a man and does not make its construction firm, and the house which he has built collapses and causes the death of the owner of the house, that builder shall be put to death. -
Chapter 15 – Table of Contents
Bridge Maintenance Course Series Reference Manual Chapter 15 – Table of Contents Chapter 15 - Channel and Waterway ....................................................................................... 15-1 15.1 Identifying Scour and Erosion – Waterway Mechanics ..................................................... 15-1 15.2 Preventive and Basic Maintenance for Channels and Waterway ..................................... 15-5 15.2.1 Debris Removal ............................................................................................................... 15-5 15.2.2 Vegetation Removal ........................................................................................................ 15-8 15.3 Repair and Rehabilitation of Channel and Waterway ....................................................... 15-8 15.3.1 Placement of Riprap and Gabions ................................................................................ 15-11 15.2.2 Tremie Concrete ........................................................................................................... 15-19 15.2.3 Grout Bag Placement .................................................................................................... 15-20 15.2.4 Sheet Piling.................................................................................................................... 15-24 15.2.5 Articulated Block ........................................................................................................... 15-25 15.3 Chapter 15 Reference List ............................................................................................... -
Arizona State Government Bridge Scour Program – a Practitioner’S Perspective
ARIZONA STATE GOVERNMENT BRIDGE SCOUR PROGRAM – A PRACTITIONER’S PERSPECTIVE ITTY P. ITTY Bridge Group, Arizona Department of Transportation, Phoenix, AZ 85007, USA JEFF BLAU Parsons Brinckerhoff Quade & Douglas Inc., 177 North Church Avenue, Suite 500 Tucson, AZ 85701, USA The waterway bridges in the state of Arizona, an arid region, experience infrequent flash floods. Not considering culverts, there are approximately two thousand waterway bridges, half of them owned by State and the other half by local and Federal agencies. Following the guidelines from the Federal Highway Administration, Arizona and the other states have evaluated the waterway bridges for possible scour vulnerability. The results of these scour assessments are already reported. In Arizona, more than forty percent of the bridges were vulnerable to scour based on the calculated scour. Since then, the Arizona Department of Transportation has been installing various scour countermeasures under these bridges as a part of the States’ Plan of Action. The current scour status of the bridges within the state is presented. This paper will feature the scour countermeasures installed at three typical sites around the State. One such site encounters severe long term degradation. For this site, the countermeasure, comprising a concrete floor and an energy dissipater, under super critical flow conditions is discussed. Keywords: Arizona; Scour; Countermeasure 1. INTRODUCTION 1.1. Background A scour evaluation program for the Arizona Department of Transportation (ADOT) was triggered by the floods that prevailed during the period of 1977 through 1983. These events caused considerable damage to highways, with bridges lost during the flood of 1978, 1980 and 1983. -
Bridge Scour Prediction and Prevention Workshop
Countermeasure Calculations and Design . Summarized from “Bridge Scour and Stream Instability Countermeasures, Experience, Selection, and Design Guidance”, Second Edition, Publication No. FHWA NHI 01-003, Hydraulic Engineering Circular No. 23, FHA . Author’s experience Selecting a Countermeasure . depends on Erosion Mechanism, Stream Characteristics, Construction and Maintenance Requirements, Vandalism, and Costs Countermeasures for Meander Migration . bank revetments, . spurs, . retardance structures, . longitudinal dikes, . vane dikes, . bulkheads, . channel relocations, and . a carefully planned cutoff River Out-Flanking Bridge Opening . Some rivers continue to meander and migrate in plan view. River may go around (out-flank) the bridge opening, or attack abutment. Example of River Meander FHA (1978) “Countermeasures for Hydraulic Problems at Bridges” Countermeasures For Channel Braiding And Anabranching . dikes constructed from the margins of the braided zone to the channel over which the bridge is constructed, . guide banks at bridge abutments (Design Guideline 10) in combination with revetment on highway fill slopes (Design Guideline 12), . riprap on highway fill slopes only, and . spurs (Design Guideline 9) arranged in the stream channels to constrict flow. Countermeasures For Degradation . Check-dams or drop structures, . Combinations of bulkheads and riprap revetment, . deeper foundations at piers and pile bents, . Jacketing piers with steel casings or sheet piles, . adequate setback of abutments from slumping banks, . Rock -and-wire mattresses, . Longitudinal stone dikes placed at the toe of channel banks, . tiebacks to the banks to prevent outflanking. Riverbed Degradation . Some rivers have beds that are naturally degrading due to conditions upstream or downstream. Any bridge piers or abutments built will need to have a deeper foundation. Degradation Failure,Ariz. -
Bridge Scour in Nonuniform Sediment Mixtures and in Cohesive Materials: Synthesis Report
U.S. Department Publication No. FHWA-RD-03-083 of Transportation June 2003 Federal Highway Administration BRIDGE SCOUR IN NONUNIFORM SEDIMENT MIXTURES AND IN COHESIVE MATERIALS: SYNTHESIS REPORT Federal Highway Administration Office of Infrastructure Research and Development Turner-Fairbank Highway Research Center 6300 Georgetown Pike McLean, Virginia 22101 FOREWORD This report is a summary of a six-volume series describing detailed laboratory experiments conducted at Colorado State University for the Federal Highway Administration as part of a study entitled “Effects of Sediment Gradation and Cohesion on Bridge Scour.” This report will be of interest to hydraulic engineers and bridge engineers involved in bridge scour evaluations. It will be of special interest to other researchers conducting studies of the very complex problem of estimating scour in cohesive bed materials and to those involved in preparing guidelines for bridge scour evaluations. The six-volume series has been distributed to National Technical Information Service (NTIS) and to the National Transportation Library, but it will not be printed by FHWA. This summary report, which describes the key results from the six-volume series, will be published by FHWA. T. Paul Teng, P.E. Director, Office of Infrastructure Research and Development NOTICE This document is disseminated under the sponsorship of the U.S. Department of Transportation in the interest of information exchange. The U.S. Government assumes no liability for the contents or use thereof. This report does not constitute a standard, specification, or regulation. The U.S. Government does not endorse products or manufacturers. Trade and manufacturers’ names appear in this report only because they are considered essential to the object of the document. -
Coastal and Offshore Scour / Erosion Issues – Recent Advances
K-6 Fourth International Conference on Scour and Erosion 2008 COASTAL AND OFFSHORE SCOUR / EROSION ISSUES – RECENT ADVANCES B. Mutlu SUMER1 1Professor, Technical University of Denmark, DTU Mekanik, Section of Coastal, Maritime and Structural Engineering (Nils Koppels Allé, Building 403, DK-2800, Kgs. Lyngby, Denmark) E-mail: [email protected] A review is presented of recent advances in scour/erosion in the marine environment. The review is organized in five sections: Numerical modeling of scour; Seabed and wind farm interaction; Coastal defense structures; Scour protection; and Impact of liquefaction. Over eighty references are included in the paper. Key Words : coastal and offshore structures, erosion, liquefaction, marine structures, numerical modeling, scour, scour protection; wind farms 1. INTRODUCTION probably biased with the author’s own current research interest. Nonetheless, the paper aims at The topic scour and erosion has been covered by giving the current state of the art on coastal and several text books, Breusers and Raudkivi1), offshore scour/erosion issues with reference to the Hoffmans and Verheij2), Melville and Coleman3) cited topics. mainly for scour processes around hydraulic structures, and Herbich4), Herbich et al.5), Whitehouse6) and Sumer and Fredsøe7) mainly for 2. NUMERICAL MODELLING OF SCOUR marine structures. The topic has also been covered partially by recent review articles, Sumer et al.8), Flow and the resulting scour processes may be Sumer9-10), and several keynote-lecture articles investigated in the laboratory, the physical modeling; presented in the Proceedings of the previous or they may be studied theoretically, using Conferences on Scour and Erosion11-13). analytical/theoretical or numerical methods, the The present paper gives a partial coverage of the mathematical modeling. -
Combined Acoustic and Geotechnical Scour Measurements at Bridge Piles in the New River, Virginia
Combined Acoustic and Geotechnical Scour Measurements at Bridge Piles in the New River, Virginia Nina Stark, Dennis Kiptoo, Reem Jaber, Julie Paprocki and Samuel Consolvo Charles E. Via, Jr., Department of Civil and Environmental Engineering, Virginia Tech, 750 Drillfield Drive, Blacksburg, VA 24061, USA; e-mail: [email protected]. Corresponding author. ABSTRACT Scour assessment and monitoring can be time- and cost-intensive. In this preliminary study, the combined use of acoustic and geotechnical in-situ instruments was demonstrated through a graduate class field experiment at the Vietnam Veterans’ Memorial Bridge crossing of the New River in Fairlawn, Virginia. Acoustic Doppler current profiling was conducted for flow velocity measurements, chirp sonar was deployed for acoustic sub-bottom scanning, and rotary side scan sonar was used for acoustic river bed imaging. A portable free fall penetrometer was deployed to estimate geotechnical properties of the river bed surface sediments, and sediment samples were retrieved. A scour hole was clearly detected and measured in depth. Differences in surficial river bed stiffness were mapped, and boulders and riprap were detected. Through the combined use of acoustic and geotechnical method, some key information relevant for scour assessment were determined within few hours and without larger support infrastructure or divers. INTRODUCTION Scour focused site investigations at bridge piers represents a time- and cost-intensive task for bridge managers, owners, and surveyors. About 84% of all bridges within the United States stretch over waterways, and thus, require scour assessment and mitigation (FHWA 1989). The quality and reliability of scour prediction and risk assessment highly depends on the availability of high quality scour observations (Melville 2000; Briaud et al. -
Riprap Countermeasures
U.S. Department of Transportation Federal Highway Administration Strategies to Mitigate Scour Critical Structures Dan Ghere Hydraulics Engineer (708) 283-3557 [email protected] Support Material HEC 23, Bridge Scour and Stream Instability Countermeasures, Volumes 1 & 2 NCHRP 135048, Countermeasure Design for Bridge Scour and Stream Instability NCHRP Report 568, Riprap Design Criteria, Recommended Specifications, and Quality Control NCHRP Report 593, Countermeasures to Protect Bridge Piers from Scour HEC 18, Evaluating Scour at Bridges Design Frequency Risk Based Design HEC 18 Tables 2.1 & 2.3 combined Probability of Exceedance Example Bridge Design Life – 75 Years .Hydraulic Design Flood Frequency – Q50 .Probability of Exceedance – 78% .Scour Design Flood Frequency – Q100 .Probability of Exceedance – 59.2% .Scour Check Flood Frequency – Q200 . Probability of Exceedance - 31.3% Flood Exceedance Probability HEC 18, Appendix B Hydraulic Countermeasure Types • Riprap • Partially Grouted Riprap • Articulated Concrete Blocks • Gabions & Gabion Mattresses • Concrete Armor Units (Toskanes, A-Jacks, etc.) • Spurs • Bendway Weirs • Guide Banks • Longitudinal Peaked Stone Toe Protection Riprap Countermeasures • Riprap Revetment – channel bank • Riprap Embankment Overtopping • Riprap at Bridge Piers • Riprap at Abutments • Riprap for Bottomless Culverts Similarities • Stone quality specification • Gradation specifications • Filter requirements Differences • Equations for sizing • Layer thickness • Toe detail • Lateral extent • Filter extent HEC 23 Riprap Equations Revetment (DG 4) 퐕 2.5 D = 퐲 (퐒퐟퐂퐬퐂퐯퐂퐓)[ / ] 30 퐊 퐒퐠 −ퟏ 퐠퐲 ퟏ ퟐ Bridge Piers (DG 11) ퟐ D = ퟎ.ퟔퟗퟐ 푽 50 푺품 −ퟏ ퟐ품 Abutments (DG 14) 풌풚 푽ퟐ 푫 x for F ≤ 0.8 ퟓퟎ = (푺품 −ퟏ) 품풚 R 풌풚 푽ퟐ 푫 = x [ ] 0.14 for F > 0.8 ퟓퟎ (푺품 −ퟏ) 품풚 R Riprap Calculator • Revetment • Pier • Abutment/Guide Bank • Spur • Embankment Overtopping • Culvert Outlet • Open Bottom Culvert • Wave Attack Layer Thickness • Abutments: Not less than 1.5 D50 or D100 • Channel Lining: Not less than 1.5 D50 or D100 • Piers: 3D50 or depth of contraction scour. -
SCOUR: EVALUATION and RIPRAP John G
SCOUR: EVALUATION AND RIPRAP John G. Delphia, P.E. TxDOT Bridge Division Geotechnical Branch 2017 BRIDGE WEBINAR JULY 2017 IMPORTANCE OF SCOUR • The most common cause of bridge failures is from floods scouring bed material from around bridge foundations (from pg 1-1, Evaluating Scour at Bridges- 5th Edition, FHWA 2012) • There is a need to ensure public safety and minimize the adverse effects resulting from bridge failures/closures 2017 BRIDGE WEBINAR JULY 2017 2 IMPORTANCE OF SCOUR Scour Program • 1991 – The FHWA initiated a Scour Evaluation Program. • The program required state DOT’s to http://www.timesunion.com/local/article/30-years-ago- Bridge-collapse-kills-10-11045976.php#photo- evaluate all existing structures for scour 12655627 vulnerability. • All subsequent new bridge designs are required to include a scour evaluation. https://dspace.library.colostate.edu/bitstream/handle/10 217/86173/Lesson02.pdf?sequence=11&isAllowed=y 2017 BRIDGE WEBINAR JULY 2017 3 IMPORTANCE OF SCOUR PURPOSE OF PERFORMING A SCOUR ANALYSIS To ensure that a bridge can withstand the effects of scour without failing. PURPOSE OF CODING A BRIDGE FOR SCOUR To identify the current status of the bridge regarding its vulnerability to scour PURPOSE OF DOCUMENTATION OF SCOUR FOR BRIDGES To document the current status of the bridge regarding its vulnerability to scour and to indicate what to do during /after flooding events 2017 BRIDGE WEBINAR JULY 2017 4 BRIDGE SCOUR EVALUATION PROCEDURES SCOUR EVALUATION PROCEDURES 2017 BRIDGE WEBINAR JULY 2017 5 BRIDGE SCOUR EVALUATION -
Countermeasures to Protect Bridge Piers from Scour Reference
COUNTERMEASURES TO PROTECT BRIDGE PIERS FROM SCOUR REFERENCE DOCUMENT Prepared for National Cooperative Highway Research Program Transportation Research Board National Research Council TRANSPORTATION RESEARCH BOARD NAS-NRC PRIVILEGED DOCUMENT This report, not released for publication, is furnished only for review to members of or participants in the work of the National Cooperative Highway Research Program (NCHRP). It is to be regarded as fully privileged, and dissemination of the information included herein must be approved by the NCHRP. P.F. Lagasse, P.E. Clopper, L.W. Zevenbergen, and L.G. Girard Ayres Associates Inc 3665 John F. Kennedy Parkway Building 2, Suite 200 Fort Collins, Colorado 80525 December 2006 COUNTERMEASURES TO PROTECT BRIDGE PIERS FROM SCOUR REFERENCE DOCUMENT Prepared for National Cooperative Highway Research Program Transportation Research Board National Research Council P.O. Box 270460 Fort Collins, Colorado 80527 (970) 223-5556, FAX (970) 223-5578 Ayres Project No. 32-0430.00 2407-REF.DOC December 2006 TABLE OF CONTENTS PART 1 DETAILED DESCRIPTION OF THE NCHRP 24-07(2) LABORATORY TESTING PROGRAM 1. Introduction ...................................................................................................................1.1 1.1 Background............................................................................................................1.1 1.2 Testing Program Summary ....................................................................................1.1 2. Testing Facilities and Protocols ....................................................................................2.1 -
Riprap As a Permanent Scour Protection Around Bridge Piers
View metadata, citation and similar papers at core.ac.uk brought to you by CORE provided by Hydraulic Engineering Repository Conference Paper, Published Version Anglin, C. D.; Itamunoala, F.; Millen, G. Riprap as a Permanent Scour Protection Around Bridge Piers Verfügbar unter/Available at: https://hdl.handle.net/20.500.11970/100365 Vorgeschlagene Zitierweise/Suggested citation: Anglin, C. D.; Itamunoala, F.; Millen, G. (2002): Riprap as a Permanent Scour Protection Around Bridge Piers. In: Chen, Hamn-Ching; Briaud, Jean-Louis (Hg.): First International Conference on Scour of Foundations. November 17-20, 2002, College Station, USA. College Station, Texas: Texas Transportation Inst., Publications Dept.. S. 582-596. Standardnutzungsbedingungen/Terms of Use: Die Dokumente in HENRY stehen unter der Creative Commons Lizenz CC BY 4.0, sofern keine abweichenden Nutzungsbedingungen getroffen wurden. Damit ist sowohl die kommerzielle Nutzung als auch das Teilen, die Weiterbearbeitung und Speicherung erlaubt. Das Verwenden und das Bearbeiten stehen unter der Bedingung der Namensnennung. Im Einzelfall kann eine restriktivere Lizenz gelten; dann gelten abweichend von den obigen Nutzungsbedingungen die in der dort genannten Lizenz gewährten Nutzungsrechte. Documents in HENRY are made available under the Creative Commons License CC BY 4.0, if no other license is applicable. Under CC BY 4.0 commercial use and sharing, remixing, transforming, and building upon the material of the work is permitted. In some cases a different, more restrictive license may apply; if applicable the terms of the restrictive license will be binding. First International Conference on Scour of Foundations, ICSF-1 Texas A&M University, College Station, Texas, USA November 17-20, 2002 Riprap as a Permanent Scour Protection Around Bridge Piers RIPRAP AS PERMANENT SCOUR PROTECTION AROUND BRIDGE PIERS D. -
Alternatives to Riprap As a Scour Countermeasure
Alternatives to Riprap as a Scour Countermeasure J. Sterling Jones, Federal Highway Administration David Bertoldi and Stuart Stein, GKY & Associates, Inc. Riprap is the most common and best documented method tate highway agencies are conducting a nation• of protection against local scour at bridge piers. Alterna• wide evaluation of existing bridges for vulner• tives to riprap vary in size, shape, and mass as well as S ability to failure due to scour. Of the 483,000 flexibility of design. The overall performance of alterna• bridges over water, roughly 39 percent either are sus• tives such as grout mats and grout bags, extended footings, ceptible to scour or have unknown foundations. Of the tetrapods, cable-tied blocks, anchors (used in connection scour-susceptible bridges that have been evaluated, with countermeasures) and high-density particles is evalu• about 17 percent have been identified as scour critical. ated. In general, alternatives are used when riprap is hard These require monitoring, repair, or scour protection. to obtain, the size required for high-velocity streams is un• FHWA has dedicated much of the research activity reasonable, or riprap is difficult to place, among other rea• in the Turner-Fairbank Highway Research Center hy• sons. Various tests were performed on all previously men• draulics laboratory in support of the nationwide scour tioned countermeasures with and without a pier on a fixed evaluation program. In particular, this laboratory has bed. An obstructed movable-bed condition was also tested been a focal point for investigating the feasibility of var• to obtain qualitative data for each countermeasure. Rec• ious techniques for protecting bridge piers from local ommendations for implementing these alternatives are scour.